典型铣削零件加工的工艺分析及编程.docx
《典型铣削零件加工的工艺分析及编程.docx》由会员分享,可在线阅读,更多相关《典型铣削零件加工的工艺分析及编程.docx(12页珍藏版)》请在冰豆网上搜索。
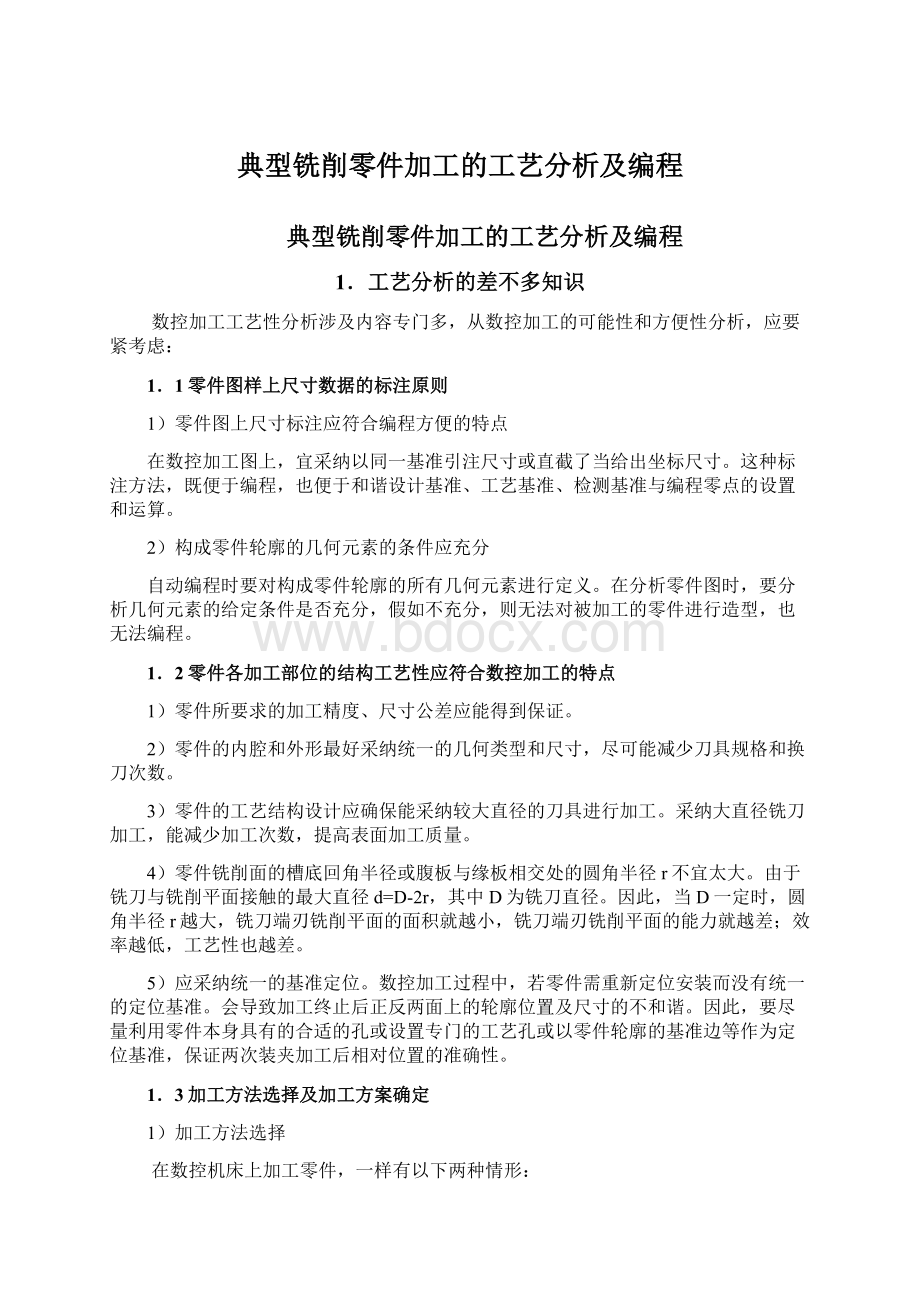
典型铣削零件加工的工艺分析及编程
典型铣削零件加工的工艺分析及编程
1.工艺分析的差不多知识
数控加工工艺性分析涉及内容专门多,从数控加工的可能性和方便性分析,应要紧考虑:
1.1零件图样上尺寸数据的标注原则
1)零件图上尺寸标注应符合编程方便的特点
在数控加工图上,宜采纳以同一基准引注尺寸或直截了当给出坐标尺寸。
这种标注方法,既便于编程,也便于和谐设计基准、工艺基准、检测基准与编程零点的设置和运算。
2)构成零件轮廓的几何元素的条件应充分
自动编程时要对构成零件轮廓的所有几何元素进行定义。
在分析零件图时,要分析几何元素的给定条件是否充分,假如不充分,则无法对被加工的零件进行造型,也无法编程。
1.2零件各加工部位的结构工艺性应符合数控加工的特点
1)零件所要求的加工精度、尺寸公差应能得到保证。
2)零件的内腔和外形最好采纳统一的几何类型和尺寸,尽可能减少刀具规格和换刀次数。
3)零件的工艺结构设计应确保能采纳较大直径的刀具进行加工。
采纳大直径铣刀加工,能减少加工次数,提高表面加工质量。
4)零件铣削面的槽底回角半径或腹板与缘板相交处的圆角半径r不宜太大。
由于铣刀与铣削平面接触的最大直径d=D-2r,其中D为铣刀直径。
因此,当D一定时,圆角半径r越大,铣刀端刃铣削平面的面积就越小,铣刀端刃铣削平面的能力就越差;效率越低,工艺性也越差。
5)应采纳统一的基准定位。
数控加工过程中,若零件需重新定位安装而没有统一的定位基准。
会导致加工终止后正反两面上的轮廓位置及尺寸的不和谐。
因此,要尽量利用零件本身具有的合适的孔或设置专门的工艺孔或以零件轮廓的基准边等作为定位基准,保证两次装夹加工后相对位置的准确性。
1.3加工方法选择及加工方案确定
1)加工方法选择
在数控机床上加工零件,一样有以下两种情形:
一是有零件图样和毛坯,要选择适合加工该零件的数控机床;
二是己经有了数控机床,要选择适合该机床加工的零件。
不管哪种情形,都应依照零件的种类和加工内容选择合适的数控机床和加工方法。
平面轮廓零件的轮廓多由直线、圆弧和曲线组成,一样在两坐标联动的数控铣床上加工;
具有三维曲面轮廓的零件,多采纳三坐标或三坐标以上联动的数控铣床或加工中心加工。
经粗铣的平面,尺寸精度可达IT12~IT14级(指两平面之间的尺寸),表面粗糙度(或Ra值)可达12.5μm~50μm。
经粗、精铣的平面,尺寸精度可达IT7~IT9级,表面粗糙度Ra值可达1.6μm~3.2μm。
孔加工的方法比较多,有钻削、扩削、铰削和镗削等。
大直径孔还可采纳圆弧插补方式进行铣削加工。
关于直径大于φ30mm己铸出或锻出毛坯孔的孔加工,一样采纳粗镗→半精镗→孔口倒角一精镗加工方案。
孔径较大的可采纳立铣刀粗铣一精铣加工方案。
有空刀槽时可用锯片铣刀在半精镗之后、精镗之前铣削完成,也可用镗刀进行单刃螳削,但单刃模削效率低。
关于直径小于φ30mm的无毛坯孔的孔加工,通常采纳饶平端面→打中心孔→钻→扩→孔口倒角→铰加工方案。
有同轴度要求的小孔,须采纳饶平端面→打中心孔→钻→半精螳→孔口倒角→精镗(或铰)加工方案。
为提高孔的位置精度,在钻孔工步前须安排锪平端面和打中心孔工步。
孔口倒角安排在半精加工之后、精加工之前,以防孔内产生毛刺。
螺纹的加工依照孔径大小而定,一样情形下,直径在M5mm~M20mm之间的螺纹,通常采纳攻螺纹的方法加工。
直径在M6mm以下的螺纹,在加工中心上完成底孔加工后,通过其他手段攻螺纹。
因为在加工中心上攻螺纹不能随机操纵加工状态,小直径丝锥容易拆断。
直径在M25mm以上的螺纹,可采纳镗刀片螳削加工。
加上方法的选择原则:
是保证加工表面的精度和表面粗糙度的要求。
由于获得同一级精度及表面粗糙度的加工方法一样有许多,因而在实际选择时,要结合零件的形状、尺寸和热处理要求全面考虑。
例如,关于IT7级精度的孔采纳镗削、铰削、磨削等方法加工可达到精度要求,但箱体上的孔一样采纳镗削或铰削;而不采纳磨削。
一样小尺寸的箱体孔选择铰削,当孔径较大时则应选择镗削。
此外,还应考虑生产率和经济性的要求,以及工厂的生产设备等实际情形。
2)加工方案确定
确定加工方案时,第一应依照要紧表面的尺寸精度和表面粗糙度的要求,初步确定为达到这些要求所需要的加工方法,即精加工的方法,再确定从毛坯到最终成形的加工方案。
在加工过程中,工件按表面轮廓可分为平面类和曲面类零件,其中平面类零件中的斜面轮廓又分为有固定斜角和变斜角的外形轮廓面。
外形轮廓面的加工,若单纯从技术上考虑,最好的加工方案是采纳多坐标联动的数控机床,如此不但生产效率高,而且加工质量好。
但由于一样中小企业无力购买这种价格昂贵、生产费用高的机床,因此应考虑采纳2.5轴操纵和3轴操纵机床加工。
2.5轴操纵和3轴操纵机床上加工外形轮廓面,通常采纳球头铣刀,轮廓面的加工精度要紧通过操纵走刀步长和加工带宽度来保证。
加工精度越高,走刀步长和加工带宽度越小,编程效率和加工效率越低。
如图1所示,球头刀半径为R,零件曲面上曲率半径为ρ,行距为S,加工后曲面表面残留高度为H。
则有:
式中,当被加工零件的曲面在ab段内是凸的时候取“+”号,是凹的时候取“一”号。
图1行距的运算图
1.4工艺设计
1)工序和工步的划分
在数控机床上加工零件,工序应尽量集中,一次装夹应尽可能完成大部分工序。
数控加工工序的划分有下列方法:
(1)按加工内容划分工序
关于加工内容较多的零件,按零件结构特点将加工内容分成若干部分,每一部分可用典型刀具加工。
例如加工内脏、外型、干面或曲面等、加工内腔时,以外形夹紧:
加工外腔时,以内腔的孔夹紧。
(2)按所用刀具划分工序
如此能够减少换刀次数,压缩空行程和减少换刀时刻,减少换刀误差。
(3)按粗、精加工划分工序
关于容易发生加工变形的零件,通常粗加工后需要进行矫形,这时粗加工、精加工作为两道工序,即先粗加工再精加工,可用不同的机床或不同的刀具进行加工。
为了便于分析和描述较复杂的工序,在工序内又分为工步,工步的划分要紧从加工精度和效率两方面考虑。
如零件在加工中心上加工,关于同一表面按粗加工、半精加工、精加工依次完成,整个加工表面按先粗后精加工分开进行:
关于既有铣面又有镗孔的零件,可先铣面后镗孔,以减少因铣削切削力大,造成零件可能发生变形而对孔的精度造成阻碍:
关于具有回转工作台的加工中心,若回转时刻比换刀时刻短,可采纳按刀具划分工步,以减少换刀次数,提高加工效率。
但数控加工按工步划分后,三检制度(自检、互检、专检)不行执行,为了幸免零件发生批次性质量咨询题,应采纳分工步交检,而不是加工完整个工序之后再交检。
2)加工余量的选择
加工余量指毛坯实体尺寸与零件(图纸)尺寸之差。
加工余量的大小对零件的加工质量和制造的经济性有较大的阻碍。
余量过大会白费原材料及机械加工工时,增加机床、刀具及能源的消耗;余量过小则不能排除上道工序留下的各种误差、表面缺陷和本工序的装夹误差,容易造成废品。
因此,应依照阻碍余量的因素合理地确定加工余量。
零件加工通常要通过粗加工、半精加工、精加工才能达到最终要求。
因此,零件总的加工余量等于中间工序加工余量之和。
(1)工序间加工余量的选择原则
采纳最小加工余量原则,以求缩短加工时刻,降低零件的加工费用。
应有充分的加工余量,专门是最后的工序。
(2)在选择加工余量时,还应考虑的情形
由于零件的大小不同,切削力、内应力引起的变形也会有差异,工件大,变形增加,加工余量相应地应大一些。
零件热处理时引起变形,应适当增大加工余量。
加工方法、装夹方式和工艺装备的刚性可能引起的零件变形,过大的加工余量会由于切削力增大引起零件的变形。
(3)确定加工余量的方法
查表法:
这种方法是依照各工厂的生产实践和实验研究积存的数据,先制成各种表格,再聚拢成手册。
确定加工余量时查阅这些手册,再结合工厂的实际情形进行适当修改后确定。
目前我国各工厂普遍采纳查表法。
体会估算法:
这种方法是依照工艺编制人员的实际体会确定加工余量。
一样情形下,为了防止因余量过小而产生废品,体会估算法的数值总是偏大。
体会估算法常用于单件小批量生产。
分析运算法:
这种方法是依照一定的试验资料数据和加工余量运算公式,分析阻碍加工余量的各项因素,并运算确定加工余量。
这种方法比较合理,但必须有比较全面和可靠的试验资料数据。
目前,只在材料十分贵重,以及少数大量生产的工厂采纳。
3)加工路线的确定
在数控加工中,刀具刀位点相关于工件运动的轨迹称为加工路线,它是编程的依据,直截了当阻碍加工质量和效率。
在确定加工路线时要考虑下面几点:
(1)保证零件的加工精度和表面质量,且效率要高。
(2)减少编程时刻和程序容量:
(3)减少空刀时刻和在轮廓面上的停刀,以免划伤零件:
(4)减少零件的变形;
(5)位置精度要求高的孔系零件的加工应幸免机床反向间隙的带入而阻碍孔的位置精度;
(6)复杂曲面零件的加工应依照零件的实际形状、精度要求、加工效率等多种因素来确定是行切依旧环切,是等距切削依旧等高切削的加工路线等。
1.5刀具的选择。
数控加工刀具从结构上可分为:
①整体式;②镶嵌式,它能够分为焊接式和机夹式。
机夹式依照刀体结构不同,又分为可转位和不转位两种;③减振式,当刀具的工作臂长与直径之比较大时,为了减少刀具的振动,提高加工精度,多采纳此类刀具;④内冷式,切削液通过刀体内部由喷孔喷射到刀具的切削刃部;⑤专门型式,如复合刀具、可逆攻螺纹刀具等。
数控加工刀具从制造所采纳的材料上可分为:
①高速钢刀具;②硬质合金刀具:
③陶瓷刀具;④立方氮化硼刀具;⑤金刚石刀具:
③涂层刀具。
数控铣床和加工中心上用到的刀具有:
①钻削刀具,分小孔、短孔、深孔、攻螺纹、铰孔等;②镗削刀具,分粗镗、精镗等刀具:
③铣削刀具,分面铣、立铣、三面刃铣等刀具。
1.6切削用量的确定
切削用量包括切削速度、进给出速度、背吃刀量和侧吃刀量。
背吃刀量和侧吃刀量在数控加工中通常称为切削深度和切削宽度。
如图2所示。
图2铣削切削用量
选择切削用量的原则是:
粗加工时,一样以提高生产率为主,但也应考虑经济性和加工成本;半精加和精加时,应在保证加工质量的前提下,兼顾切削效率、经济性和加工成本。
具体数值应依照机床讲明书、切削用量手册,并结合体会而定。
从刀具的耐用度动身,切削用量的选择方法是:
先确定切削深度或切削宽度,其次确定进给出量,最后确定切削速度。
1)切削深度aP
①在工件表面粗糙度值要求为Ra12.5μm~25μm时,假如圆周铣削的加工余量小于5mm,端铣的加工余量小于6mm,粗铣一次进给就能够达到要求。
但在余量较大,工艺系统刚性较差或机床动力不足时,可分多次进给完成。
②在工件表面粗糙度值要求为Ra3.2μm~12.5μm时,可分粗铣和半精铣两步进行。
粗铣时切削深度或切削宽度选取同前。
粗铣后留0.5mm~1.0mm余量,在半精铣时切除。
③在工件表面粗糙度值要求为Ra0.8μm~3.2μm时,可分粗铣、半精铣、精铣3步进行。
半精铣时切削深度或切削宽度取1.5mm~2mm:
精铣时圆周铣侧吃刀量取0.3mm~0.5mm,面铣刀背吃刀量取0.5mm~lmm。
2)进给量
进给量有进给速度Vf、每转进给量f和每齿进给量fZ3种表示方法。
进给速度Vf是单位时刻内工件与铣刀沿进给方向的相对位移,单位为mm/min,在数控程序中的代码为F。
每转进给量f是铣刀每转一转,工件与铣刀的相对位移,单位为mm/r。
每齿进给量fZ是铣刀每转过一齿时,工件与铣刀的相对位移,单位为mm/z。
3种进给量的关系为:
Vf=f·n=fZ·z·n
铣刀转速为n,铣刀齿数为z。
每齿进给量fZ的选取要紧取决于工件材料的力学性能、刀具材料、工件表面粗糙度等因素。
工件材料的强度和硬度越高,fZ越小;反之则越大。
硬