BH型钢结构加工制作指导书修王森要点.docx
《BH型钢结构加工制作指导书修王森要点.docx》由会员分享,可在线阅读,更多相关《BH型钢结构加工制作指导书修王森要点.docx(52页珍藏版)》请在冰豆网上搜索。
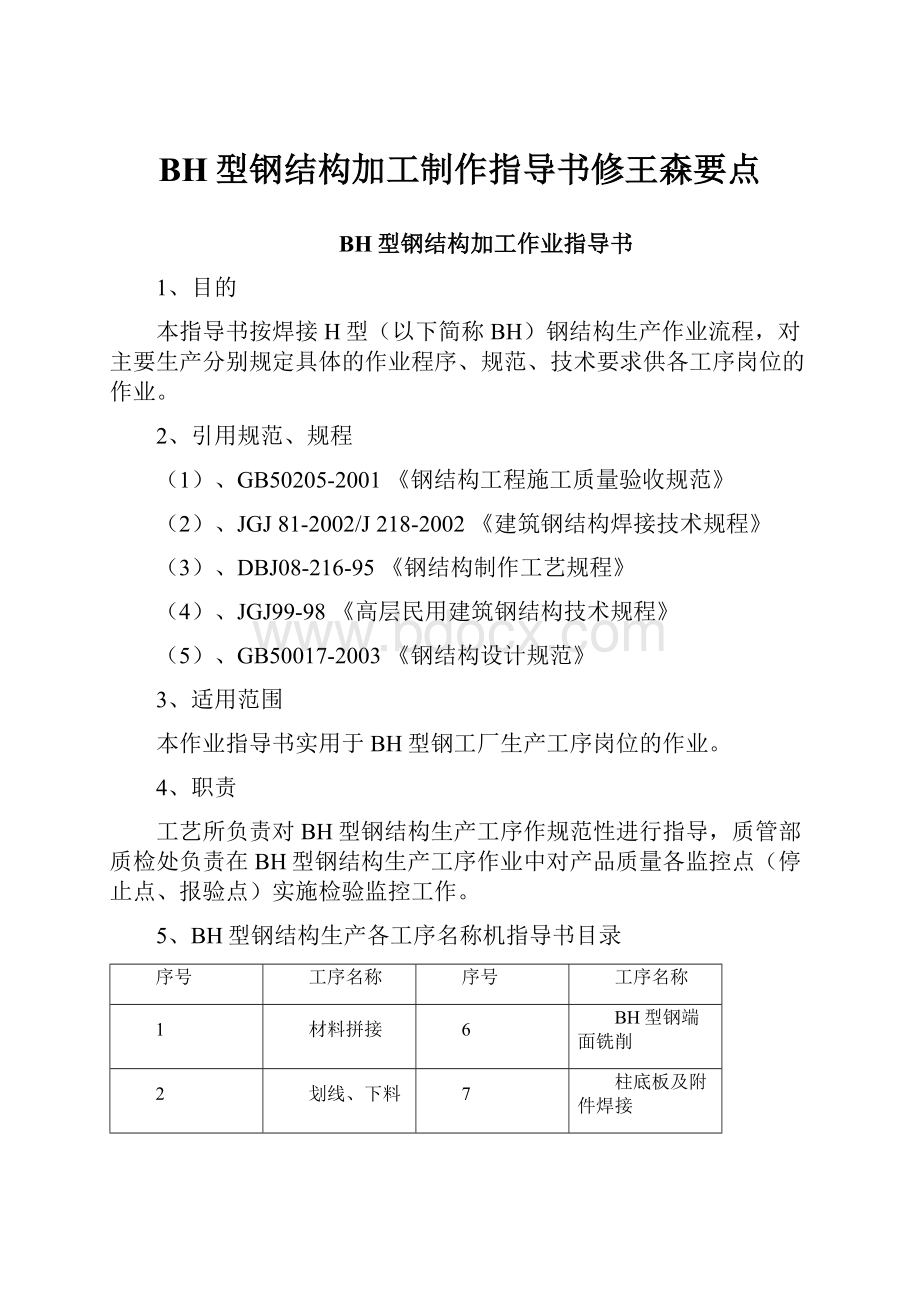
BH型钢结构加工制作指导书修王森要点
BH型钢结构加工作业指导书
1、目的
本指导书按焊接H型(以下简称BH)钢结构生产作业流程,对主要生产分别规定具体的作业程序、规范、技术要求供各工序岗位的作业。
2、引用规范、规程
(1)、GB50205-2001《钢结构工程施工质量验收规范》
(2)、JGJ81-2002/J218-2002《建筑钢结构焊接技术规程》
(3)、DBJ08-216-95《钢结构制作工艺规程》
(4)、JGJ99-98《高层民用建筑钢结构技术规程》
(5)、GB50017-2003《钢结构设计规范》
3、适用范围
本作业指导书实用于BH型钢工厂生产工序岗位的作业。
4、职责
工艺所负责对BH型钢结构生产工序作规范性进行指导,质管部质检处负责在BH型钢结构生产工序作业中对产品质量各监控点(停止点、报验点)实施检验监控工作。
5、BH型钢结构生产各工序名称机指导书目录
序号
工序名称
序号
工序名称
1
材料拼接
6
BH型钢端面铣削
2
划线、下料
7
柱底板及附件焊接
3
BH型钢装配
8
表面处理和涂装
4
BH型钢焊接、矫正及加强板的组装焊接
9
包装和发运
5
焊接矫正
10
附:
栓钉焊接,连接板、牛腿、表面处理和涂装、包装检验、发运
6、本指导书由工艺所制定、管理和解释(焊接参数由焊试室认可)
编制/日期
会签/日期
审查/日期
会签/日期
批准/日期
生效/日期
BH型钢构件生产流程
1、板材拼接
1.1、拼接前的准备工作
1.1.1、钢板拼接、对接应在平台上进行,拼接之前需要对平台进行清理;将有碍拼接的杂物、余料、码脚等清除干净。
1.1.2、钢板拼接之前需要对其进行检测检验(当PL≥30mm时,要做UT),合格后方可进行拼接;若钢板在拼接之前有平面度超差过大时,需要在钢板矫正机上进行矫正;直至合格后才允进入拼接。
1.1.3、按拼板排料图领取要求的钢板,进行拼接前需要对钢板进行核对;核对的主要内容包括:
拼接钢板材质、牌号、厚度、尺寸、数量,对外观表面锈蚀程度等(当钢板厚度≥40时要求进行Z向性能检测);合格后划出切割线。
1.1.4、焊接H型钢翼缘板拼接长度不应小于2倍板宽;腹板拼接宽度不应小于300mm,长度不应小于600mm;腹板下料拼接时拼接焊缝与翼缘板任一拼接焊缝不在同一截面上,相互之间错开尺寸L>200mm。
拼接焊缝还应避开柱节点位置,同时与劲板之间错开尺寸L>200mm;拼接后构件长度方向余量需满足设计要求。
拼接图示:
1.1.5、拼接焊接坡口可采用半自动切割机、NC切割机、刨边机等进行坡口加工;火焰切割坡口后应打磨焊缝坡口,打磨两侧各20mm~30mm。
1.1.6、自动、半自动气割工艺参数
序号
钢板厚度mm
氧气压力(Mpa)
乙炔压力(Mpa)
气割速度mm/min
1
6~10
0.2~0.25
≥0.03
650~450
2
10~20
0.25~0.30
≥0.035
500~350
3
20~30
0.30~0.40
≥0.04
450~300
4
40~60
0.50~0.60
≥0.050
400~300
5
60~80
0.60~0.70
≥0.050
350~250
6
80~100
0.80~0.90
≥0.060
300~200
1.1.7、零件切割与号料的允许偏差
1、精密切割±0.50mm
2、自动、半自动切割±1.0mm
3、手工切割±1.5mm
1.1.8、一般切割面与钢材表面不垂直度不大于钢材厚度5%,且不大于1.5mm;切割表面粗糙度为100~200um,切割缺棱大于2.0mm时,应焊补打磨;局部深度大于1.0mm时,应打磨圆顺。
1.1.9、若为重要构件厚板切割时,应作适当预热,或按工艺技术要求执行。
1.1.9、气割表面质量要求
表面割纹深度
(G值)
平面度(用B值表示)
上边缘融化程度(S值)
≤100um~200um
板厚t>25
≤1.0%t
上缘有圆角咬边宽度≤1.0mm
板厚t≤25
≤2.0%t
注:
(1)、表面割纹深度G表示:
指切割面波纹的峰与谷之间距离,(取任意点的平均值)
(2)、平面度以B值表示:
指沿切割面方向垂直于切割面上的凹凸程度,按照切割面钢板厚度t计算。
(3)、上边缘融化程度以S表示,指气割过程中烧塌情况,表明是否产生塌角及形成间断后;连续性的熔滴及熔化条状物。
1.1.10、若为重要构件厚板切割时,应作适当预热,或按工艺技术要求执行。
1.2、钢板拼接焊接参数
1.2.1、钢板拼接自动焊接参数(Ø4.8mm焊丝)
钢板
厚度(mm)
接头形式
焊接
层数
正面
反面
焊接根部
处理
电流
A
电压
V
速度
cm/min
电流
A
电压
V
速度
cm/min
6
1
540~580
29~31
42~48
580~620
28~32
42~48
反面
清根
打磨
8
1
560~600
31~33
47~53
600~640
32~34
47~53
10
1
560~600
31~33
47~53
600~640
32~34
47~53
12
1
630~670
31~33
42~48
630~670
32~34
42~48
14
1
630~670
34~36
32~38
680~720
34~36
32~38
同上
16
1
680~720
34~36
32~38
700~740
35~37
32~38
19
1
730~770
35~37
32~38
730~770
35~37
27~33
22
1
680~720
34~36
37~43
730~770
34~36
27~33
同上
2
660~700
37~39
22~28
680~720
35~37
22~28
25
1
680~720
34~36
32~38
730~770
34~36
32~38
2
660~700
37~39
22~28
680~720
35~37
22~28
28
1
730~770
34~36
33~38
730~770
34~36
32~38
2
660~700
34~36
22~28
680~720
35~37
22~28
30
1
730~770
34~36
32~38
730~770
34~36
27~33
2
680~720
34~36
27~33
680~720
36~38
22~28
32
1
730~770
34~36
32~38
730~770
34~36
27~33
2
710~750
34~36
28~32
680~720
37~39
22~28
钢板
厚度(mm)
接头形式
焊接
层数
正面
反面
焊接根部
处理
电流
A
电压
V
速度
cm/min
电流
A
电压
V
速度
cm/min
34
1
730~770
34~36
32~38
730~770
34~36
32~38
反面
清根
打磨
2
700~740
34~36
27~33
730~770
34~36
27~33
3
/
/
/
680~720
37~39
22~28
36
1
730~770
34~36
32~38
730~770
34~36
27~33
2
710~750
34~36
27~33
730~770
34~36
27~33
3
/
/
/
680~720
37~39
22~28
38
1
730~770
34~36
32~38
730~770
34~36
27~33
同上
2
730~770
34~36
27~33
730~770
35~37
27~33
3
730~770
37~39
22~28
680~720
37~39
22~28
40
1
730~770
34~36
32~38
730~770
34~36
27~33
同上
2
730~770
34~36
28~32
730~770
35~37
27~33
3
730~770
34~36
28~32
730~770
35~37
27~33
4
730~770
37~39
22~28
730~770
37~39
22~28
钢板
厚度(mm)
接头形式
焊接
层数
正面
反面
焊接根部
处理
电流
A
电压
V
速度
cm/min
电流
A
电压
V
速度
cm/min
45
1
730~770
34~36
32~38
730~770
34~36
27~33
反面
清根
打磨
2
730~770
34~36
27~33
760~800
35~37
27~33
3
780~820
37~39
27~33
760~800
35~37
27~33
4
730~770
37~39
22~28
680~720
35~37
32~38
5
/
/
/
680~720
35~37
32~38
50
1
730~770
34~36
32~38
730~770
34~36
27~33
同上
2
730~770
35~37
27~33
760~800
35~37
27~33
3
780~820
37~39
27~33
780~820
37~39
27~33
4
730~770
35~37
32~38
680~720
35~37
27~33
5
730~770
35~37
32~38
680~720
35~37
27~33
1.2.2、钢板拼接自动焊接参数(Ø4.0mm焊丝)
钢板厚度(mm)
接头形式
焊接顺序
电流(A)
电压(V)
速度cm/min
焊接根部
处理
8
正
440~480
30~32
47~53
或反面清根
打磨
反
480~530
10
正
530~570
30~32
44~48
反
590~640
32~34
12
正
620~680
33~35
40~44
反面清根
打磨
反
680~720
33~35
38~44
14
正
650~680
34~36
42~48
同上
反
680~720
35~37
36~40
16
正1,2
620~650
33~35
42~48
同上
反3
680~720
34~36
39~45
18
正1,2
620~650
33~35
37~43
反3
680~720
34~36
39~45
20
正1,2
620~650
33~35
37~43
同上
反3,4
680~720
34~36
39~45
22
正1,2
620~650
33~35
42~48
反3,4
680~720
34~36
39~45
钢板厚度(mm)
接头形式
焊接顺序
电流(A)
电压(V)
速度cm/min
焊接根部
处理
24
正1,2
620~650
33~35
39~45
同上
反3,4
640~670
33~35
37~43
28
正1,2
620~650
33~35
37~43
反3,4
640~670
33~35
35~41
30
正1,2
620~650
33~35
35~41
反3,4
640~670
33~35
35~41
32
正1,2
640~670
33~35
35~41
反3,4
660~690
33~35
35~41
1.2.3钢板拼接CO2气体保护焊参数
钢板厚度(mm)
坡口形状
焊丝直径
道数
电流A
电压V
速度cm/min
CO2流量L/min
备注
10
Ø1.2
2
300~320
37~39
60~70
20
反面
清根
打磨
16
Ø1.2
4
140~160
24~26
20~30
20
同上
260~280
31~33
35~40
270~290
34~36
50~60
270~290
34~36
40~50
19
Ø1.2
4
140~160
24~26
26~30
20
260~280
31~33
35~45
300~320
35~37
40~50
300~320
35~37
35~40
16
Ø1.6
4
400~430
36~38
50~60
25
同上
400~430
36~38
50~60
19
Ø1.6
4
400~430
36~38
35~45
25
400~430
36~38
35~45
钢板厚度(mm)
坡口形状
焊丝直径
道数
电流A
电压V
速度cm/min
CO2流量L/min
备注
8
Ø1.2
2
120~130
26~27
30~50
20
250~260
28~30
40~50
10
2
130~140
26~27
30~50
20
280~300
30~33
25~30
16
Ø1.2
3
120~140
25~27
40~50
20
300~320
33~35
30~40
300~320
35~37
20~30
19
Ø1.2
4
120~140
25~27
40~50
25
300~320
33~35
30~40
300~320
33~35
30~40
300~320
35~37
20~25
1.3、焊条、焊丝、焊剂的选用
1.3.1、拼板焊前领取定位焊需要的焊条(焊条应按产品说明书规定烘焙)、焊丝和已烘焙的焊剂,焊条和焊剂的领用量应控制在每班的用量内,其由钢板的材料和厚度决定。
1.3.1.1、焊条、焊丝牌号规格。
(见下表)
钢板
手工电弧焊焊条
CO2气体保护焊焊丝
牌号
规格(mm)
牌号
规格(mm)
牌号
规格(mm)
Q235
全部
E4303(J422)
Ø3.2,Ø4,Ø5
ER49-1
(或ER50-6)
Ø1.2,Ø1.4,Ø1.6
Q345B
pL≤20
pL>20
E5003(J502)
E5016(J506)
Ø3.2,Ø4,Ø5
ER50-6
Ø1.2,Ø1.4,Ø1.6
Q345C
pL>20
E5015(J507)
Ø4,Ø5
ER50-6
Ø1.2,Ø1.4,Ø1.6
Q345D
pL>20
E5015(J507)
Ø4,Ø5
ER50-6
Ø1.2,Ø1.4,Ø1.6
Q390
pL>20
E5515-D3;-G
Ø4,Ø5
ER50-G
Ø1.2,Ø1.4,Ø1.6
Q420
pL>20
E5515-D3;-G
Ø4,Ø5
ER55-G
(或ER55-D2)
Ø1.2,Ø1.4,Ø1.6
1.3.1.2、埋弧自动焊丝的牌号、规格、焊剂,由钢材材质和厚度,构件安全度相匹配,
埋弧自动焊丝的牌号和规格:
表1.2.1-2
钢板
埋弧焊丝
埋弧焊剂
牌号
规格(mm)
牌号
规格(mm)
型号
Q235
全部
H08A
Ø3.2
Ø4.0
Ø5.0
HJ431(F4A0)
Q345B
PL≤14
PL>14
H08A
(或H08MnA)
HJ431(F4A0)
SJ101(F48A2)
Q345C
Q345D
PL>14
H08MnA
(或H10Mn2)
Ø3.2
Ø4.0
Ø5.0
Ø6.4
Q390
PL>14
H08MnA
(或H10Mn2)
SJ101(F48A2),F5011
F5021,F5031
Q420
PL>14
H10Mn2
(或H08MnMoA)
F6011,F6021-(F62A2-H8),F6031
1.3.1.3、埋弧焊用焊丝除门型焊机大盘外,单机自动埋弧焊机用丝还需要配专用焊丝盘,盘丝过程中应进行去油处理;注意焊丝轧印不能太深。
盘好丝的盘上应有粘贴标签(标签应注明焊材牌号、规格和检验号内容)。
1.3.1.4、焊材烘培参数
1、焊剂(HJ431):
250 ℃/2hSJ101:
350℃/2h
2、焊条(Exx03):
150℃/1~1.5h
3、焊条(Exx15、Exx16):
350℃/2h
1.4、钢板拼接的装配
1.4.1、对需要拼接的钢板,吊运至拼接焊接平台上。
1.4.2、拼板错边量及间隙按表1.3-1规定
表1.4-1
钢板厚度t(mm)
允许错边(mm)Δ
间隙(a)
4~8
≤1.0
0~+1.0
8~20
≤2.0
20~40
≤2.5
>40
≤3.0
1.4.3、钢板拼接两端应装焊引熄弧板,其材质厚度和坡口应与拼板相同;宽度应大于80mm,长度宜为2t,且不小于100mm,厚度应不小于10mm。
起熄弧应在板的1/2以外处。
1.4.4、定位焊焊丝按相关规定,点焊间距300~500mm,焊缝长度宜大于40mm;焊缝厚度不宜超过设计焊缝2/3,且不超过6mm。
1.4.5、引熄弧板定位焊应在焊接坡口和垫板上,不应在焊缝以外母材上,如下图示:
1.4.6、拼板装配时应考虑二板的预反变形量及正反面焊接量,尽可能减少接头的焊接角变形。
1.4.7、装配完成,操作者应自检合格后,须经检验检查合格方可进入正式焊接。
1.5、拼板焊接
1.5.1、正面焊缝焊接,将焊接小车置于拼板缝一侧,焊丝处于焊缝中心为准,且与焊道保持平行。
1.5.2、将焊接小车置于轨道上,焊丝下送至焊缝处,调整焊丝处于校直状态,并作一试行走来回。
1.5.3、焊接工艺参数见表1.2,并随时关注电流、电压、焊接速度无异常,厚板焊接时,还应注意焊道布置为多层多道焊。
1.5.4、焊到端头熄弧板大于1/2处才能停止施焊。
1.5.5、待焊渣稍冷后才敲去焊渣,将多余焊剂收集筛选待后回用。
1.5.6、检查焊道表面质量,进行目测检查,如无异常;再进行背面焊接,如厚板拼焊,以1/2焊满翻身为宜,不应一次焊满,以免变形量过大。
1.5.7、背面焊时,应先清根,打磨焊道,再进行焊接;重复1.5.1-1.5.5直至焊满;厚板应再次反身直至焊满。
1.5.8、焊缝增强量(余高)0~3mm,特殊要求按设计或合同技术要求条件为准。
1.5.9、普通碳素结构钢在冷却到工作环境程度,低合金钢在焊后24小时方可进行外观检查。
1.5.10、焊接工件外观检查:
用目测、5倍放大镜、焊接卡尺、必要时辅以磁粉检查表面微裂缝。
1.5.11、焊缝应均匀,不得有裂纹,未融合、夹渣、焊瘤、咬边、弧坑、针状气孔等缺陷、焊接应无飞溅残留物;对接焊缝一般以一级焊缝技术要求,特殊情况为二级焊缝为准。
对接焊缝外形尺寸允许偏差:
项目
示意图
一级焊缝
二级焊缝
焊缝余高c
b<20
0.5~2.0
0.5~2.5
b≥20
1.0~3.0
0.5~3.5
焊缝错边d
PL≤20
PL>20
d<0.10t且<2.0
<3.0
D<0.10t且<2.0
<3.0
1.5.12、焊接完成后应用火焰切割去除引熄弧板并修磨平整,不得用锤击落引熄弧板。
1.5.13、按规定要求清根时,进行碳弧气刨的焊缝,对背面待焊焊缝进行清根,刨后必须清磨(清除渗碳层)。
(1)、碳弧气刨应采用直流反接(工件接电源负极)。
(2)、圆碳棒直径为Ø7或Ø8mm,扁碳棒宽度为12mm或14mm。
(3)、为避免产生“夹碳”或“粘渣”,除采用合适的刨削速度外,还应使碳棒与工件间有合适的倾斜角度;推荐角度如下表:
刨槽深度(mm)
2.5
3.0
4.0
5.0
6.0
7~8
碳棒倾角(度)
25º
30º
35º
40º
45º
50º
气刨工艺参数
碳棒直径
(宽度)
电弧长度(mm)
压缩空气压力(Mpa)
极性
电流(A)
气刨速度(mm/min)
Ø7
1-2
0.39~0.59
直流反接
280~300
0.5~1.0
Ø8
1-2
0.40~0.60
直流反接
350~400
1.0~1.2
12
1-2
0.39~0.59
直流反接
260~280
0.6~1.0
14
1-2
0.40~0.60
直流反接
280~300
1.0~1.2
1.6、无损检测
1.6.1、检验员在对焊缝外观质量检查合格基础上,应对需要探伤部位进行打磨,直至符合探伤表面要求。
1.6.2、检验员填写无损探伤检测委托书,按相关规定进行UT探伤。
等级
探伤比例
合格标准
一级焊缝
100%
GB11345B级检验;评定II级或以上
二级焊缝
20%
GB11345B级检验;评定II级或以上
三级全焊透焊缝可不进行UT
1.6.3、探伤人员必须在焊缝完全冷却后方能进行UT,并出具探伤报告;明确记录构件相关部位。
1.6.4、当UT发现焊缝缺陷:
气孔、夹渣、未熔合等必须返工,直至重探合格为止。
1.6.5、探伤人员必须对不合格部件划出深度和长度,出具焊缝返工通知书。
1.6.6、焊接返修应上报技术部备案;一次返修可采用常规工艺,二次返修应查明原因;并制定相应返修工艺。
对重大复杂构件,还应抄报工艺工程师。
1.6.7、探伤人员对返修焊缝进行再探时,还应出具探伤报告。
1.6.8、Q345、Q420钢厚板40mm以上焊缝反修采用碳刨前,应作60℃预热处理。
1.6.9、补焊时务必在坡口内引弧,熄弧时应填满弧坑,多层焊时应错开接头不小于100mm。
1.7、钢板拼接切割后,应进行矫正达到平整度要求。
1.8、钢板拼接切割后,应进行矫正达到平整度要求如下
项目
允许偏差
图例
钢板的局部
平整度
t≤14
1.5
t>14
1.0
2、放样、下料
2.1、放样、下料前的准备
2.1.1、放样前,放样人员必