注塑产品成型缺陷及其对策.docx
《注塑产品成型缺陷及其对策.docx》由会员分享,可在线阅读,更多相关《注塑产品成型缺陷及其对策.docx(14页珍藏版)》请在冰豆网上搜索。
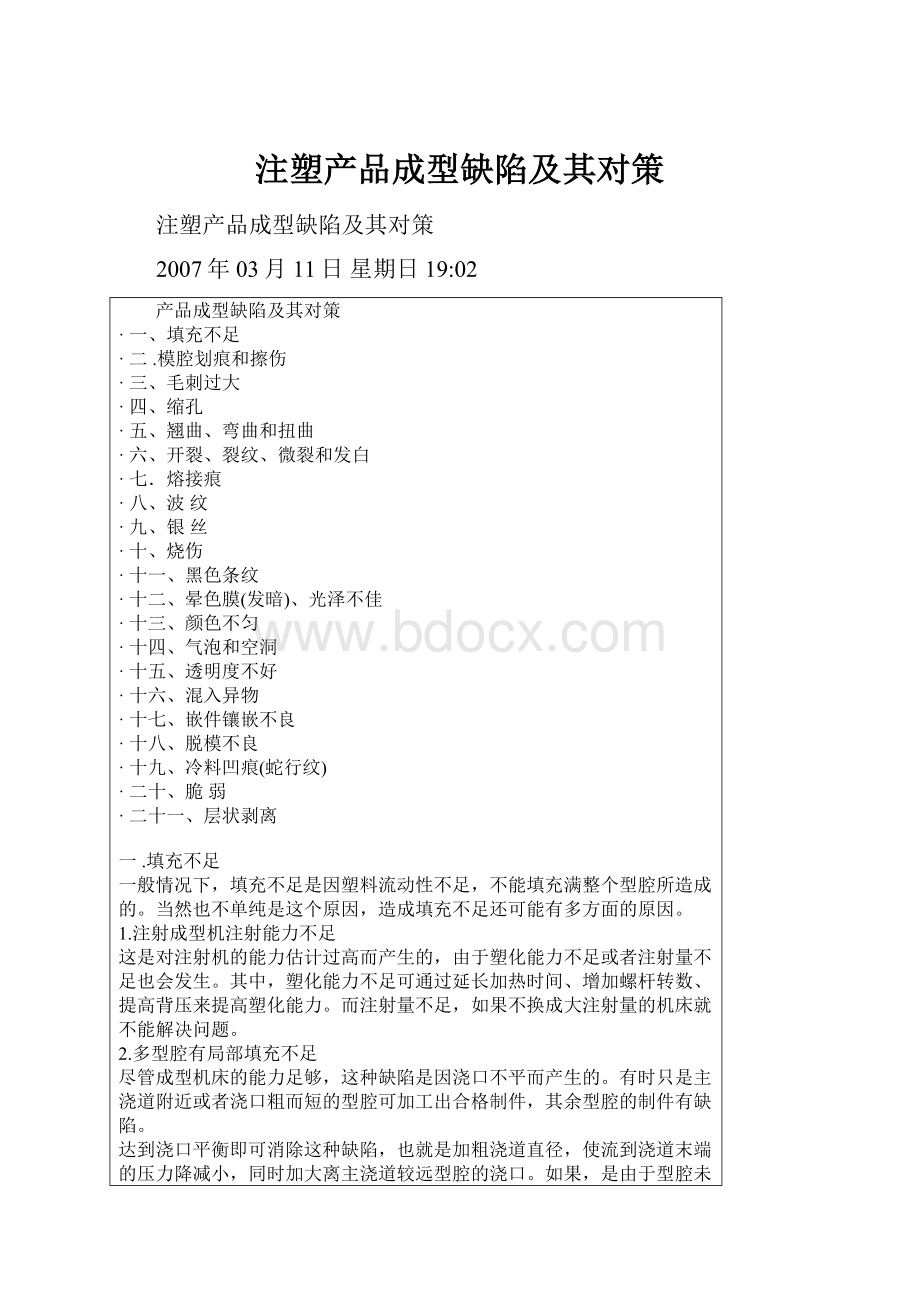
注塑产品成型缺陷及其对策
注塑产品成型缺陷及其对策
2007年03月11日星期日19:
02
产品成型缺陷及其对策
·一、填充不足
·二.模腔划痕和擦伤
·三、毛刺过大
·四、缩孔
·五、翘曲、弯曲和扭曲
·六、开裂、裂纹、微裂和发白
·七.熔接痕
·八、波纹
·九、银丝
·十、烧伤
·十一、黑色条纹
·十二、晕色膜(发暗)、光泽不佳
·十三、颜色不匀
·十四、气泡和空洞
·十五、透明度不好
·十六、混入异物
·十七、嵌件镶嵌不良
·十八、脱模不良
·十九、冷料凹痕(蛇行纹)
·二十、脆弱
·二十一、层状剥离
一.填充不足
一般情况下,填充不足是因塑料流动性不足,不能填充满整个型腔所造成的。
当然也不单纯是这个原因,造成填充不足还可能有多方面的原因。
1.注射成型机注射能力不足
这是对注射机的能力估计过高而产生的,由于塑化能力不足或者注射量不足也会发生。
其中,塑化能力不足可通过延长加热时间、增加螺杆转数、提高背压来提高塑化能力。
而注射量不足,如果不换成大注射量的机床就不能解决问题。
2.多型腔有局部填充不足
尽管成型机床的能力足够,这种缺陷是因浇口不平而产生的。
有时只是主浇道附近或者浇口粗而短的型腔可加工出合格制件,其余型腔的制件有缺陷。
达到浇口平衡即可消除这种缺陷,也就是加粗浇道直径,使流到浇道末端的压力降减小,同时加大离主浇道较远型腔的浇口。
如果,是由于型腔未完全闭合所致,这时就必须减少每次注射成型的数目。
3.塑料流动性不佳
如果塑料流动性不佳,未等流到型腔末端或者未流到溢料槽就已冷凝,因而往往造成填充不足。
为了消除这种缺陷可提高溶料温度,并在熔料冷凝前使熔料流到型腔末端,也可加快注射速度。
也就是说提高料筒温度、提高注射压力,加快注射速度,也可提高模具温度。
在这种场合,塑料良好的流动性特别重要,所以更换流动性好的塑料也是一种解决方法。
4.流动阻力过大
阻碍熔料流动的部位有喷嘴、主浇道、浇道、浇口和制件的薄壁处等。
采用如下方法可减小喷嘴流动阻力:
加大喷嘴直径,提高喷嘴温度,使用流动阻力较小的喷嘴。
对于主浇道可增大其直径:
对于浇道应避免采用流动阻力大的半圆形浇道,而采用圆形或梯形浇道,若增大直径则更好。
同时必须使其长度为最短。
至于壁厚太薄造成的填充不足,可增加整个壁厚或增加局部壁厚,亦可在填充不足处的附近,设置辅助浇道或浇口来解决。
特别是被喷嘴最先注射出的熔料因被主浇道和浇道冷却,导致流动阻力变大,在这种情况下应开设大的冷料穴。
若因模具温度低而使流动阻力增大,提高模具温度也就可以了。
根据模具具体情况改变冷嘲热讽却水出入口位置,或者变更冷却水的流径路线,也会取得良好效果。
5.型腔内排气不良
由于这种原因而造成的填充不足屡屡发生。
当熔料被注入型腔时,往往是一开始熔料就把型腔封闭,在局部未填充处残留有空气。
还因填充过快,空气有时来不及从分型面溢出而被压缩,造成局部未填充塑料,成型制件填充不足。
这种缺陷特别容易出现在模腔的转角处,深凹陷处和被厚壁部分包围着的薄壁部分。
即大多发生在用侧浇口成型时薄底的壳形件及长凸台的头部。
这样被封闭的空气受绝热压缩而达高温,有时会烧焦制件的局部(参照烧伤和黑色条纹部分)。
消除这种缺陷的措施是降低注射速度,给予一定的排气时间,若将模腔内的空气用真空泵排除,一般情况下很有效。
最好的方法是设置排气孔道,选择浇口位置使空气易于先排出,或从模具结构上考虑排气方式。
即把模腔局部制成镶件,使用空气从镶件缝隙溢出,或者在分型面上开设浅槽,还可以利用顶杆的缝隙来排气。
例如采用多浇口等形式成型时,将模具的一部分制成镶件,可利用其缝隙作排气孔道。
6.锁模力不足
虽然也可认为锁模力与填充不足没有关系,但有时这也是造成填充不足的原因。
即使使用注射量相同的成型机床,有时也会出现锁模力不足的现象。
如果锁模力不足,在注射压力作用下动模稍微后退,将产生飞边毛刺而使制件注射量当中足,因而引起注射量不足,这与上面说过的机床能力不足一样,也会产生填充不足的现象。
7.塑料供应不足
尽管注射机能力足够,而从喷泉嘴注射出的熔料达不到所需数量,也可产生填充不足。
其原因有两个,一是料斗的塑料粘边落不到料筒中;另一个是使用螺杆式注射成型机时,塑料在料筒内滑移,不能前进。
前者是因塑料在料斗干燥器内局部熔化结块,使粉料或不规则颗粒料无法进入料斗。
后者是因塑料等级选择不当,颗粒料的润滑剂过多造成的,如改为配比正确的原料就可解决。
8.塑料供给过剩
对于柱塞式注射机,如果进入料筒的塑料过多,注射压力因压缩颗粒粒而消耗掉一部分,因此降低了注射成型所必需的从喷嘴射出熔料的压力,从而造成注射压力不足。
其解决方法是调整供料数量,使之恰好适合成型所需的塑料量。
二.模腔划痕和擦伤
模腔划痕是指模腔表面狎痕被原封不动地复制在成型制件表面上,因此除了修理模具之外没有其它办法。
相反,擦伤是因模具拔模斜度相反或不足,而出现在制件与模腔相对滑动面上的擦伤现象。
如果这样继续成型,极有可能磨损模具本身,必须及时修正模具。
也有因抛光不充分或模具局部有毛刺而造成造成擦伤,稍加修理即可。
有的模具采用中心一根顶杆的顶出方式,实际顶出时顶板倾斜,因之制件也倾斜而产生顶出擦伤。
这是被顶出制件相对型腔中习不平衡所造成的缺陷,需注意顶出方式的设计。
另外,拔模斜度不足也会产生擦伤。
所以设计制件时必须充分考虑拔模斜度。
特别是有蚀刻加工图案时,蚀刻的细小凸凹是造成反拔模斜度的原因,就取足够大的拔模斜度。
同时,也必须反拔模斜面上的蚀诶花纹深度考虑进去。
三、毛刺过大
毛刺过大多发生在分合面上,即动模与静模之间、滑块的滑配部位、镶件的缝隙、顶杆孔隙等处流入熔料,在制件上形成多余的飞边毛刺,这样的飞边毛边毛刺,在乘型时起杠杆作用、会使飞边毛刺进一步增大,从而造成模具局部的凹陷,形成时飞边毛刺进一增大的恶性循环。
所以,如果一开始发现产生了飞边毛刺,就必须尽早修整模具。
毛刺的产生有下面几种原因。
1.锁模力不足
与成型制件的投影面积相比,如果锁模力较小,由于注射压力的作用使动、静模之间将出现缝隙,这样势必就会出现飞边毛刺。
特别是把侧浇口置于制件中央附近的孔上时,因为这种成型浇口需要较大的注射压力,所以极易出现毛刺。
降低注射压力或者提高锁模力都可消除这种缺陷,若根据具体情况改用流动性好的塑料采用低压成型,有[时也是很有成效的。
2.模具局部配合不严密
首先讨论动、静模合模不严的问题,尽管棋具本身合模严密,当采用肘杆式锁模机构的注射机成型时,往往因模具平行度不佳或者锁模装置调整的不良,产生诸如左右两边锁模不。
均衡的现象,即左右两侧只有—边被锁紧,另—‘边不密贴,此时必须调整拉杆(二根或四根拉扦)使之均衡仲展,其次,也有因模具本身研配不佳造成密贴不严。
特别是制件中心有成型孔时,由于这部分的支承作用,当锁模力不充足时也容易出现毛刺。
另外是滑动型芯,因沿动型芯是动作机构,往往产生毛刺,所以滑动型芯的配合很重要。
尤其是对左右分型的哈夫模,其侧面的投影面积也受成型压力作用,如果设计很不能完全承受这个压力也常会出现毛刺。
关于镶件缝隙和顶杆孔隙,不仅会产生毛刺恶性循环增大的现象,而且还会增大顶出阻力。
3.模具挠曲引起
如果模具原度不足,受注射压力作用将产生挠曲,这时若中心附近有孔,孔的周边就会产生毛刺;还有利用中心孔开侧浇口时,孔和浇道周边也会产生毛刺。
这种原因产生的毛刺,是由模具制作不良造成的,所以较难修理。
采取补强模具,可使毛刺减小。
4.塑料流动性过好
单纯是由于塑料流动性过好,在理论上并不是产生毛刺的原因。
可是,当塑料流动性过好时,那怕是微细的缝隙塑料也能钻进去,所以极易出现毛刺。
要消除这种毛刺,可降低熔料温度或注射压力,也可降低模具温度或注射速度,
5.注入熔料过多
这也不是产生毛刺的直接原因。
为了防止缩孔而注入过多熔料的作法是错误的,应采取增加注射时间或保压时间来成型(参照缩孔)。
6.模具表面有异物
模具合模面上有异物,必然会产生毛刺。
解决这个问题,显然应清扫于净模具表面,使合模面密贴即可。
四、缩孔
成型制件表面出现的凹陷叫缩孔。
这是成型时常产生的缺陷,是由于塑料成型时收缩所造成的,所以大多数难以消除。
加之注射成型的过程中,是把熔融塑料注入凉的棋腔内,又因塑料导热性很差,所以冷却甚为复杂。
特别是厚壁部分比薄壁部分冷却较缓慢,因而厚壁部分易出现缩孔。
另外榄具温度稍高部位冲凝缓慢,因而形成棋具局部温差,若加上模具本身热传导的差异,那水温度偏高成热传导较差的部位就会出现缩孔。
因而,设计时应考减采用难以出现缩孔的成型制件及模具结构。
1。
压缩不足
在主侥道、浇道和浇口比成型制件壁厚和容积过小的模具中,因注射压力不能充分作用到模腔内的熔料上,使收缩量增大,从而出现较大的缩孔。
·特别是浇口过小时,即使保压时间充足,但浇口已经硬化,使压力传递不到模腔内的熔料上。
尤其是对固熔点不一致的结品性塑料,就更容易产生这种现象,还有易出毛刺的模具,因闭合不严而加不上足够的成型压力,也易出现缩孔。
螺杆式注射机设置有逆止环,以防止熔料沿螺杆回流,但比柱塞式注射机易出缩孔。
在这一点上,可以说柱塞式注射机比螺扦式注射机好。
如上所述,当熔料乃至型腔末端的熔料尚未冷凝硬化之前,加上足够的保持压力即可防止压缩不足所造成的缩孔。
所以,增大主浇道、浇道、浇门,尤其是增大浇口直径是很有效的。
另外增大注射压力,或加上足够的保持压力也很重要。
而熔料不足也助长缩孔。
塑料流动性好,如果增加压力,因产生毛刺也会引起缩孔,必要时降低料简温度或改用流动性差的塑料能防止缩孔。
在离浇口较远、流动熔料的末端也容易出现地孔,这是出十流到末端的流路阻力引起压力损失所造成的,所以在易山缩孔的附近开没浇口、或者增加该部位的厚度也是有效的。
因此,根据情况增加点浇口数目。
或变更浇口位置更为有效。
2.注射量调整不当
螺杆式注射成型机注射终了时,必须在螺杆头部与喷嘴之间留有适当数量的熔融塑料,用它来缓冲。
若这个缓冲量为零,又把注射量调整到终了时,螺杆同时也顶到底,这样在保压时螺杆就无法前进,因而不能进行保压。
这样在保压过程中,塑料收缩就成为缩孔而表现出来。
这类浇口部位的缩孔和制件表面深浅不均的缩孔,很容易与其他原因缩孔相区别。
解决的办法是留有一定的缓冲量,使注射结柬时螺扦仍能前进数毫米乃至十几毫米。
缓冲量为零,即把注射量调整到注射结束螺杆顶到底时,这样将会缩短注射机本身的寿命,因此必须十分注意这一点。
3.缩孔出现在制件工作面上
有些成型制件即使内部出现缩孔,有时也没有妨碍。
这种情形如开头叙述的那样,模具温度高的一面易出缩孔,而温度低的—面很匠难出缩孔。
所以,应把不允许出缩孔的面充分冷却,或者相反将允许出缩孔的(即不允许出缩孔的相对面)高温成型也很有效。
4.冷却不均匀
成型制件壁厚极不均匀时,厚壁部分比薄壁部分冷却的缓慢,因而厚壁部分产生缩孔。
要消除由于壁厚不均匀产生的缩孔,从理论上来说也是困难的,所以设计制件时应使壁厚均匀。
也就是说,重点是缩小壁厚的变化。
例如设计凸台时,如果对外径尺寸有要求,就应在中心设置消除缩孔的工艺孔;当要求凸台强度时,不应加粗凸台本身,而应采取利用加强筋增加强度的方式。
平缓凹下的缩孔要比急剧凹陷下去的缩孔不那么显眼,所以不要求精度的制件,应在外层已冷凝硬化,月.中心部分尚柔软能够顶出的状态下出模,然后在空气中或温水中缓冷,这样可使缩孔不明显,不影响使用.
5.收缩量过大
成型塑料本身的热膨胀系数较大时,当然易出现绍孔。
因此,低温成型这种塑料就不易出现缩孔。
若提高注射压力可使更多的塑料注入模腔,所以压力越高缩孔也就相应减小。
可是,温度降到塑料所需最低温度以下,即使提高注射压力,也很难防止结品性塑料的缩孔。
例如聚丙烯、高密度聚乙烯、聚甲醛等,其结晶固体与熔融状态的密度显著不问,所以防止缩孔很困难。
这时如果允许用非结品性共聚体代替,就能减少缩孔。
另外,如果填充无机填充剂,如玻璃纤维、石棉等也可使缩孔变小。
五、翘曲、弯曲和扭曲
注射成型时塑料的成型收缩率随流动方向的不同而不问,就是说流动方向的收缩卒远比垂立方向大。
结品性塑料的收缩率本来就大,而,收缩率在方问上的差值与大的收缩率相迭加,就比非结品性塑料更大。
有时收缩率在方向上的差值达1%以上。
尤其是成型收缩率还·受成型制件壁厚的彤响。
由于收缩率的不同,致使制件产生变形。
注射成型足把粘流态的高聚物挤压到模腔中成型的一种方法,所以小可避免在成型制件内部残留有内部应力。
此应力也将引起制件的变形。
此外还有一些原因也往往引起变形。
如制件未完全硬化就顶出的变形。
还有顶杆推力造成的变形。
由于上述原因,将成型制件从模腔顶出后,就达不到内部应变最小的理想形状,而出现翘曲、弯曲和扭曲等现象。
可采用辅助工具来娇正冷却变形。
即把从模腔内顶出的,且内部尚柔软的成型制件放在辅助工具中,随着辅助工具一起冷却,从原始状态限定变形。
根据冷却方式来确定冷却时间,一般需冷却10min以上。
引起制件翘曲、弯曲和扭曲的具体原因及防止办法如下。
1.冷却不充分或不均匀
在未完全冷却时顶出,顶杆的顶推力往往使成型制件变形,所以未充分冷却就勉强出模也会产生变形。
;对策是在模腔内克分冷却,持完全硬化后方可顶出。
也可以降低棋具温度、延长冷却时间。
然而,有的棋具的局部,例如浇口对侧冷却不充分,在通常成型条件下还有时不能防止'变形。
这种情况应考虑变更冷却水的路径、冷却水道的位置或追加冷却梢孔,尤其应考虑不用水冷,采用空气冷却等方式。
2.顶扦造成
有的制件的脱模性不良,采用顶杆强行脱棋而造成变形。
对不易变形的塑料如甲其丙烯酸甲酯制件,这时不是产生变形而是产生裂纹。
对于ABS和聚苯乙烯制件,这种变形是以被推项部位的发白表现出来(参照开裂、裂纹、微裂和发白)。
其消除方法是改善模具的抛光、使其易于脱模,问时使用脱模剂也可改善脱模。
最根本的改进方法是珩磨型芯、减小脱模阻力,或增大拔棋斜度,在不易顶出部位增设顶扦等,而变更顶出方式则更重要。
3.由成型应变引起
成型应变造成的变形主要是由成型收缩在方向上的差异、壁厚的变化所产生的。
因此,提高模具温度、提高熔料温度、降低注射压力、改善浇注系统的流动条件等均可减小收缩率在方向上的差值。
可是,只变更成型条件大多难以矫正过来,这时就需改变浇口的位置和数目例如成型长杆件时要从—端注入等。
有时必需改变冷却水道的配置;较长薄片类制件更、容易变形,有时需变更制件的励部设计在其上翘一侧的背面设置加强胁等.利用辅助工具冷却来矫正这种变形大多是有效的。
不能矫正时,有的需修正模具尺寸。
4。
结晶性塑料
结晶性塑料的成型iDC缩率1Jb非结晶性塑料大很多,由于融点温度范困狭窄多数产生变形,并且往往是难以修正的。
:
结晶性塑料的结品度随冷却速度的不同而变化,即急剧冷却结晶度降低、成型收缩率减小,而缓慢冷却结晶度升高、成型收缩率增大。
结晶性塑料变形的特殊矫正法就是利用这—性质。
灾际上使用的矫正法是使动、静模有—定的温差。
就是采取使翘曲的另一面产生应变的温度,即可矫正变形。
有时这个温差高达20。
C以上,但必须十分均匀地分布。
必须指出,在设计结晶性塑料成型制件及模具时,如不预先采取特别的防止变形的手段,制件会因变形而无法使用,仅使成型条件达到上述各项要求,大多数情况仍然不能娇正变形。
六、开裂、裂纹、微裂和发白
有的成型制件并没有局部破碎,只是表面产生微细的开裂,根据其程度和外观上的差别,把较严重的叫开裂或裂缝,较轻微的叫做微裂或龟裂。
其中微裂不仅则成型后产生;放置后或与溶剂蒸气等接触时也会发生。
而ABS和耐冲击聚苯乙烯根本不产生这种现象,却以顶杆推顶部位发白的形式表现出来,采用热风加温则可消除这种发白现象。
1、产生上述现象的原因有下两几点。
1.脱模不畅、成型时模的拔模斜度不足,成为例拔模斜度,或抛光极差,因此制件脱模困难,往拄造成制件破损或发白。
由于主浇道抛光不好使制件粘在静模、或者动模上,有侧壁凸凹并采用硬性脱模时,更容易产生这种现象。
总之发生这种缺陷时,首先应注意模具的抛光,并在增大拔模斜度的同时在成型制件开裂处附近增设顶杆,使制件不弯曲、合理地脱模。
对于聚甲基丙烯酸甲酯成型制件,因塑料本身较脆、表面要求有光泽,大多采用镀铬模具成型。
然而电镀具有平面不易镀覆的性质,却易放覆到转角处;因而成为倒拔模斜度,所以必须予以特别注意。
2.过填充
由于过分担心成型缩孔,结果注入棋腔的熔料过多,使成型制件内部产生极大的应变。
这时收缩变得很小,不但容易开裂,并且放置一段时间后内部应变更容易造成微裂。
要消除过填充的开裂可提高熔料温度、降低注射压力、提高模具温度,但只要保证熔料易于注入模腔即可。
根据成型制件外观等有关原因,必须以过填充的方式成型时,为使制件不发生微裂,成型后应进行塑化处理,这对消除内部应变是有效的。
3.冷却不充分
在末完全硬化时就将制件顶出,有时顶仟周困开裂或发白。
‘通过充分冷却或改变模具本身的冷却方式等,可消除这利,缺陷。
4.嵌件周围开裂
置入嵌件成型时由于塑料的收缩,应力显著地集中在嵌件周围。
这个力虽然能牢固地保持住嵌件,但是应力过大时嵌件周围塑料往往开裂。
要减少嵌件周围的开裂,有效的是预热嵌件或尽量缩小收缩差,进行塑化处理效果更明显。
七.熔接痕
成型时熔料汇合处产生的细线被称做熔接痕,这是低温熔料相汇合因不能完全熔合而产生的。
这种熔接痕只发生在熔料汇合部位,就是说,只发生在带孔成型制件、或多个浇口成型的制件,该处的强度低于其它部分。
栅格等制件的熔接痕出现在中心,对强度和外观有影响。
熔接痕的详细情况叙述如下。
1、熔接痕位置不当
熔接痕产生的部位与浇口,制件形状有关,当不能消除时应把它移到不影响外观质量的位置。
为此,需要考虑移动浇口位置,改变浇口尺寸并保持平衡;、改变制件壁厚等方法。
2、熔料流动性不足,如果熔料流动性不足,熔接处的熔料温度将更低,并且压力损失也大,势必使熔接痕明显、强度下降;因此下降使熔接痕仍在原来的位置上,也应使之不明显,以减少对外观及强度的影响。
措施是使熔料以高温、高压流到汇合处;'若能降低流动阻力就更好了。
:
所以,应采取升高熔料温度来提高流动性;加快注射速度使熔料不降温就达到汇合处,s升高模具温度减少熔料降温;扩大浇口或加厚到达汇合处路径上的制件壁厚,以减少流动阻力。
改用流动性良好的塑料有利于减轻熔接痕。
采用多个浇口成型时肯定会产生熔接痕,而用单浇口能够成型时,就可能不产生熔接痕。
3.存在空气或挥发成分
熔接痕虽然如上所述是难免的,但在熔料流动时首先应把空气或挥发成分排除掉‘如果排气不畅,熔接痕当然变得明显。
这种情形严重时还会引起填充不足或烧伤(参照填充不足、烧伤);考虑到有这种可能时,有必要利用镶件的缝隙排气或设置排气孔道,对于空气造成的熔接痕恰好与通常的消除熔接痕方法相反。
有时甚至要降低注射速度才能使熔接痕不明显。
4。
脱模剂造成
当模腔表面涂有脱模剂时,一旦被熔料运送到熔接处,因脱模剂与熔料相互不熔合而产生熔接痕。
当使用含硅脱模剂时,这种现象更严重。
如果这种熔接痕粗重,往往使制件变得脆弱,并且易开裂(参照脆弱)。
5。
着色剂造成
如果加入铝箔或微粒状着色剂成型圆片制件,熔接痕明显地随着色剂的性质变化。
消除这种熔接痕是困难的(参照颜色不匀)。
八、波纹
所谓波纹,是指熔料流入模腔后出现的以浇口为中心的条纹。
这是由于模腔各面熔料冷凝硬化不均匀所产生的。
详细说明如下。
1.塑料粘度过大。
熔料粘度过大时一接触到模腔表面很快就冷凝,后面流来的熔料迫使冷凝料继续流动,,从而产生条纹。
:
条纹产生的原因多数是模具温度不适当。
可用改变成型条件,即提高熔料温度和模具温度来消除。
2.熔料温度不均匀
滞留在注射机喷咀头部的熔料,应与成型制件脱模时一起除掉。
如有残余部分或有主浇道及浇道冷却了的冷料,被注入模腔,也同样产生波纹。
一开始就注入热的熔料即可消陈波绞。
注重抛光注射机喷嘴、升高喷嘴温度、模具上设计足够大的冷料穴等也可消除波纹。
3、模具温度不适宜
模具温度过低,处于低温部位的熔料就立即冷凝,因而产生波纹。
虽然提高模具温度能够消除这种缺陷,但是这样必将延长成型周期。
九、银丝
这是出现在制件表面熔料流动方向上的银白色纹理;这种现象的原因虽然很多,但主要是原料干燥不彻底,由水分或挥发成分造成的。
当产生银丝时,首先要用彻底干燥的颗粒料进行成型实验,若这样尚不能消除,可检查其他原因。
:
银丝产生的具体原因分述如下;
1.由水分或挥发成分引起的
如果用未经充分干燥的塑料成型,水分或挥发成分在料筒内被气化,并随熔料一起从喷嘴注入模腔。
这种加杂着气体的熔料一接触到模腔就冷凝硬化,气体妨碍熔料与型腔表面的密贴,并沿着流动方向形成白色纹理,这就是出现在制件上的银丝。
进行充分干燥,完全除掉水分或吸附水分即可防止银丝,然而梅雨季节空气湿度极高,有时干燥料在料斗内吸潮也会产生银丝。
对于壁厚变化大的制件由于排气不畅及注射量不足,,也容易产生银丝。
螺杆的形式也是产生银丝的有关因素,即使在相同条件下,因螺杆的形式不同产生银丝的状态也不相同。
2.由塑料分解引起
塑料本身分解,或者添加的稳定剂、防止带电剂等分解,结果产生气体,这与未完全干操的情形相同,往往也产生银丝。
这时为使塑料不分解,应降低熔料温度成型,同时还应缩短熔料在料筒内的停留时间。
3.卷入空气引起
随着颗粒料一起从料斗进入料筒的空气,经过螺秆和料筒之间的缝隙,或者校塞和料筒之间被排向后方;螺杆式注射机把卷入的空气一直运送到喷嘴。
从喷嘴注射出夹杂着气体的熔料,因与型腔表面不密贴而产生根丝。
如果将料筒下部充分冷却;或使料筒后部温度偏低些,就可解决这个问题。
变更既定成型条件如降低螺杆转数、提高背压,就可以避免出现银丝。
4,熔料温度偏低引起.
如果注入模腔的熔料温度偏低,;一般表现为波纹,有的模具往往出现银丝。
这种情形与波纹中的2.相同,因而采取的措施也相同,提高熔料温度、加大模具的冷料穴等都可以消除银丝。
5.模腔表面的水分或挥发成分引起
如果模腔表面沾染有水分;被熔料气化之后往往造成银丝缺陷。
这时制件表面发暗(,晕包膜),如果消除了发暗这一缺陷,同时也就消除了银丝缺陷(参照晕:
色膜;光泽不佳部分)。
6,由塑料粉造成
不使用颗粒料、而直接使用粉料成型时,或者往颗料中掺入大量粉料成型时,很容易卷入空气。
这与上述3.相同,因此应遵循3.的要求解决银丝缺陷。
,要采用粉料成型,应采用压缩比大,不卷入空气的特殊螺杆.
7.混入异种塑料引起
把相互不易熔合的两种塑料混合成型,虽然会引起层状剥离(参照剥离),但是有时也会出现银丝缺陷。
彻底清洗料简.使用未被污染的原料即可解决这个问题。
十、烧伤
烧伤现象是熔接痕部分与型腔末端的局部塑料被烧焦变黑。
这如在填充不足的5。
中及熔接痕的3.中说到的一样,因型腔内部的空气排不出去,被绝热压缩达高温,使塑料焦化而产生烧伤。
因而解决办法与前面说到的相同。
降低注射速度,留出空气从分型面排出的时间,或者改变模具结构,使空气能从镶件的缝隙、顶秆的孔隙、开设在分型面上的浅楷等处排出。
十一、黑色条纹
成型制件上形成的照线叫黑色条纹,其原因主要有下面几点。
1.塑料过热分解引起;
塑料或添加的紫外线吸收剂、防止带电添加剂等在料筒内过热分解,或者在料筒内停留时间过长而分解,变成黑色。
如果将变黑的塑料注入型腔,则变成成型制件的黑色条纹。
只