天然气制氢装置操作规程.docx
《天然气制氢装置操作规程.docx》由会员分享,可在线阅读,更多相关《天然气制氢装置操作规程.docx(27页珍藏版)》请在冰豆网上搜索。
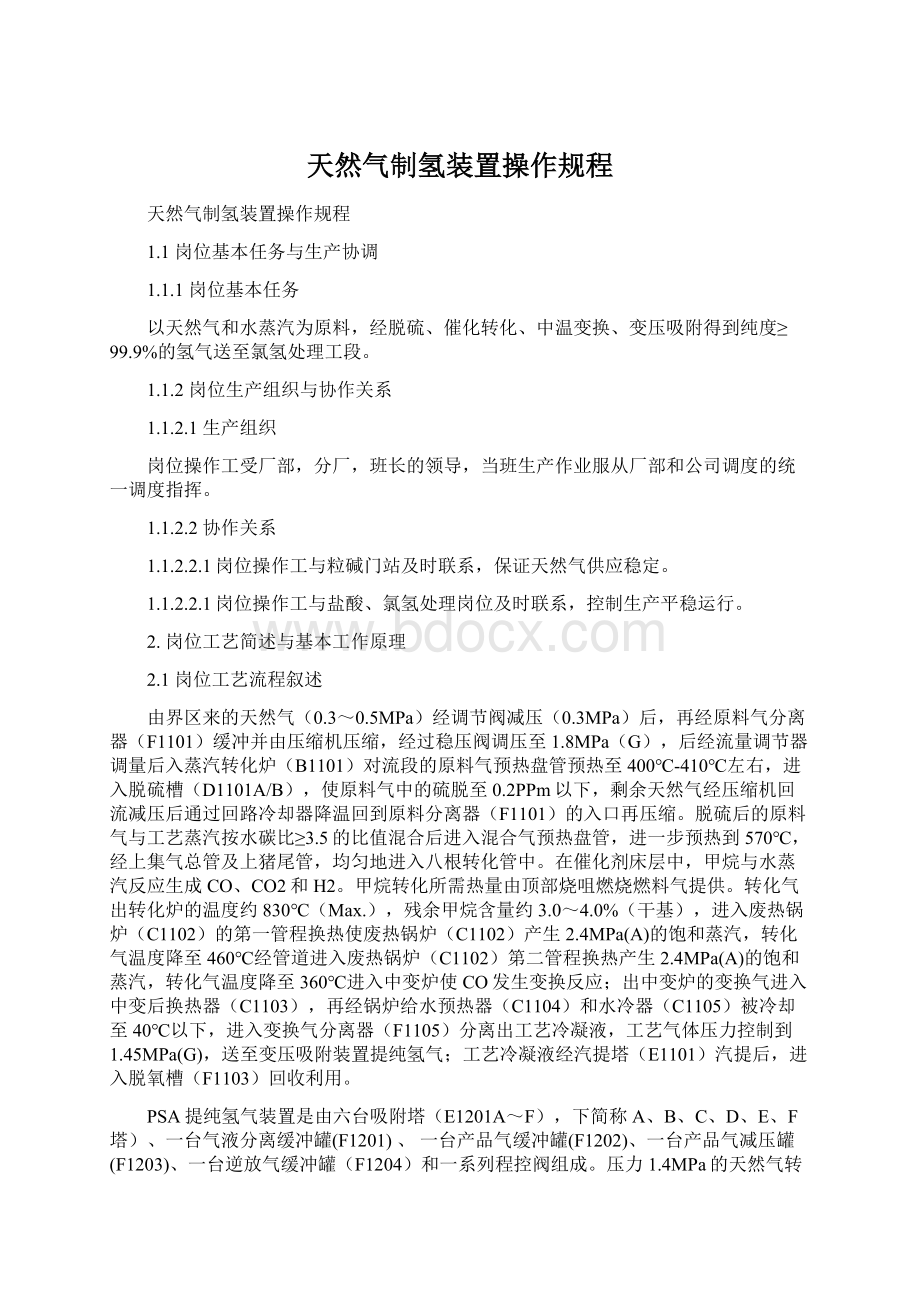
天然气制氢装置操作规程
天然气制氢装置操作规程
1.1岗位基本任务与生产协调
1.1.1岗位基本任务
以天然气和水蒸汽为原料,经脱硫、催化转化、中温变换、变压吸附得到纯度≥99.9%的氢气送至氯氢处理工段。
1.1.2岗位生产组织与协作关系
1.1.2.1生产组织
岗位操作工受厂部,分厂,班长的领导,当班生产作业服从厂部和公司调度的统一调度指挥。
1.1.2.2协作关系
1.1.2.2.1岗位操作工与粒碱门站及时联系,保证天然气供应稳定。
1.1.2.2.1岗位操作工与盐酸、氯氢处理岗位及时联系,控制生产平稳运行。
2.岗位工艺简述与基本工作原理
2.1岗位工艺流程叙述
由界区来的天然气(0.3~0.5MPa)经调节阀减压(0.3MPa)后,再经原料气分离器(F1101)缓冲并由压缩机压缩,经过稳压阀调压至1.8MPa(G),后经流量调节器调量后入蒸汽转化炉(B1101)对流段的原料气预热盘管预热至400℃-410℃左右,进入脱硫槽(D1101A/B),使原料气中的硫脱至0.2PPm以下,剩余天然气经压缩机回流减压后通过回路冷却器降温回到原料分离器(F1101)的入口再压缩。
脱硫后的原料气与工艺蒸汽按水碳比≥3.5的比值混合后进入混合气预热盘管,进一步预热到570℃,经上集气总管及上猪尾管,均匀地进入八根转化管中。
在催化剂床层中,甲烷与水蒸汽反应生成CO、CO2和H2。
甲烷转化所需热量由顶部烧咀燃烧燃料气提供。
转化气出转化炉的温度约830℃(Max.),残余甲烷含量约3.0~4.0%(干基),进入废热锅炉(C1102)的第一管程换热使废热锅炉(C1102)产生2.4MPa(A)的饱和蒸汽,转化气温度降至460℃经管道进入废热锅炉(C1102)第二管程换热产生2.4MPa(A)的饱和蒸汽,转化气温度降至360℃进入中变炉使CO发生变换反应;出中变炉的变换气进入中变后换热器(C1103),再经锅炉给水预热器(C1104)和水冷器(C1105)被冷却至40℃以下,进入变换气分离器(F1105)分离出工艺冷凝液,工艺气体压力控制到1.45MPa(G),送至变压吸附装置提纯氢气;工艺冷凝液经汽提塔(E1101)汽提后,进入脱氧槽(F1103)回收利用。
PSA提纯氢气装置是由六台吸附塔(E1201A~F),下简称A、B、C、D、E、F塔)、一台气液分离缓冲罐(F1201)、一台产品气缓冲罐(F1202)、一台产品气减压罐(F1203)、一台逆放气缓冲罐(F1204)和一系列程控阀组成。
压力1.4MPa的天然气转化气进入吸附塔(E1201A、B、C、D、E、F)进行吸附,得到的产品气在产品气缓冲罐(F1202)缓冲之后经过计量、减压在产品气减压罐(F1203)缓冲后去用户。
解吸气经逆放气缓冲罐(F1204)缓冲去转化炉(B1101)燃烧.。
燃料天然气和变压吸附装置来的解吸尾气进入转化炉的顶部烧嘴燃烧,向转化炉提供热量,助燃空气由鼓风机加压后经空气预热器(C1106)预热后进烧咀。
燃烧生成的烟气经对流段换热后约195℃-205℃由用户回收利用于生产碳酸钠或由烟囱高空放空。
为回收烟气热量,在转化炉对流段内设有四组换热盘管:
(由高温段至低温段)
2.1.1蒸汽-原料混合气预热盘管;
2.1.2原料气预热盘管(高温段);
2.1.3锅炉给水预热盘管(烟气废锅);
2.1.4空气预热器(C1106)。
2.2基本反应原理
2.2.1天然气脱硫
在一定的温度、压力下,原料气通过氧化锰及氧化锌脱硫剂,将原料气中的有机硫、H2S脱至0.2PPm以下,以满足蒸汽转化催化剂对硫的要求,其主要反应为:
COS+MnO→MnS+CO2
H2S+MnO→MnS+H2O
H2S+ZnO→ZnS+H2O
2.2.2烃类的蒸汽转化
烃类的蒸汽转化是以水蒸汽为氧化剂,在镍催化剂的作用下将烃类物质转化,制取氢气。
这一过程为吸热过程故需外供热量,转化所需的热量由转化炉辐射段燃烧燃料气提供。
此反应是强吸热的反应,增加蒸汽量和提高温度有利于反应平衡向生成物一侧移动;同时此反应前后物质的量有变化,是体积增大的反应,所以随压力的增大能提高剩余蒸汽热效率,使生产成本降低,并提高催化剂的利用率。
在镍催化剂作用下其主要反应:
CH4+H2OCO+3H2-Q
CO+H2OCO2+H2+Q
2.2.3中温变换
转化炉送来的转化气,含12.5%-13.5%左右的CO,变换的作用是使CO在催化剂作用下,与水蒸汽反应而生成CO2和H2。
这样,增加了需要的氢气量。
中温变换反应的方程式:
CO+H2OCO2+H2+Q
这是一个可逆的放热反应,选择中温反应兼顾了变换反应的速度和深度。
增加过量的水蒸汽,有利于反应向右侧进行。
2.2.4气体组分表一览表
2.2.5原料天然气组份表
表2-1原料天然气组份表
组份
CO2
CH4
C2H6
C3H8
C4H10
C5H12
C6H14
N2
H2S
含量(V%)
0.03
94.48
3.38
0.59
0.25
0.09
0.04
1.14
微量
PSA尾气组份表
表2-2PSA尾气组份表
组份
H2
CO
CO2
CH4
N2
含量(V%)
38.86
6.51
44.51
9.49
0.64
压力(MPa)
0.02~0.04
3.3正常开停车
3.3.1开车准备工作
3.3.1.1现场清理、检查
首先要清理现场,清除一切与安装无关的杂物,要保证进出口道路及安全通道的畅通。
要特别注意检查与安全有关的设施是否齐备完好,如消防栓、灭火器、安全阀、阻火器、放空管、电气防爆设施等。
3.1.1.2仪表的检查和校验
在系统进行化工试车之前,应由专业人员及操作工人配合对整个仪表系统进行全面检查及调试,看是否符合工艺设计的要求。
进行各仪表报警值的试验,看是否准确可靠,同时查看报警指示灯和声响是否正确。
3.1.1.3系统正常开车(三剂均处于还原态)
3.1.1.3.1启动引风机,鼓风机,调整炉膛上部负压20-80Pa。
3.1.1.3.2先建立除氧器液位,启动锅炉给水泵,建立汽包液位1.7米处,启动锅炉给水循环泵,用外界常压蒸汽升温汽包,启动压缩机通氮气在废锅后放空。
3.1.1.3.3置换燃料气管线,做炉内可燃性气体分析,合格后点燃烧嘴。
3.1.1.3.4脱硫槽与转化管用氮气升温(以转化管出口温度为准),升温速度控制在50℃/h,在废锅后放空,(若转化管出口温度在300℃以上可直接用蒸汽升温)升温至300℃-310℃左右,脱硫槽从系统断开,继续通氮气/天然气从脱硫槽出口放空。
转化管改用外界蒸汽继续升温,在废锅后放空。
可根据自产蒸汽情况切换自产蒸汽。
3.1.1.3.5TI1107升至650℃时,关闭氮气改通天然气,分析脱硫后天然气的硫含量,合格后将脱硫槽并入系统,注意控制水碳比,将中变炉并入系统,在汽液分离器缓冲罐后放空。
分析转化气、中变气中的N2、CH4、CO、CO2含量,合格后并入PSA工段,逐渐增加天然气和蒸汽量。
解析气通入尾气烧嘴燃烧,为转化炉提供热量。
产品气分析合格后减压稳压后压力控制在0.11Mpa送至盐酸。
3.3.1.4系统正常停车
3.3.1.4.1当后工段减负荷时,转化工段也应将负荷相应降低,当负荷降至350m³/h时停变压吸附。
在汽液分离器缓冲罐后放空。
3.3.1.4.2系统降温时负荷也相应的降低,注意控制减量的速率,减量顺序依次分别为燃料气、原料气、蒸汽。
在减负荷过程中注意控制好触媒床层的温度,注意控制水碳比,在500m³/h以上保持水碳比大于4.0,在500m³/h以下保持水碳比大于5.0。
降温速率为60℃/h,当转化管出口温度在600℃左右时断中变炉、在废锅后放空。
3.3.1.4.3当转化管出口温度降到550℃切换原料天然气为氮气进预热盘管,在脱硫槽后放空。
转化管改通蒸汽降温,在中变后放空。
当转化管出口温度降到400℃时,停天然气压缩机,断脱硫槽、中变并保温保压。
中控关闭(HV1102)和PV1112。
3.3.1.4.4根据情况决定是否停锅炉给水泵和循环泵;
3.3.1.4.5引风机需半小时后才能停,之后全开炉膛自然通气。
3.3.1.4.6冬季停车应放掉废锅和除氧器的水,防止冻坏设备。
3.3.1.4.7停转化蒸汽后应将汽包压力通过PV1110或现场放空降低,避免废锅单层受压引起封头泄漏。
3.1.1.5短期停车和再正常开车
当系统某一部分发生故障,需作临时短期停车。
其做法是:
3.1.1.5.1中控人员关HV1102,勿使转化管出口气体超温。
以每小时60℃的速率降低转化管出口温度,并逐渐切断燃料气,现场关烧嘴根部阀。
3.1.1.5.2逐步减少工艺气至1/3设计负荷,然后一次切除。
3.1.1.5.3当转化管出口温度降到400℃时,系统保温保压。
3.1.1.5.4在封闭保温时,可停锅炉给水泵和锅炉给水循环泵,注意保持汽包有1.5米的液位,并停止排污。
若汽包有水位时,再开车比较简单,先开启锅炉给水泵、锅炉给水循环泵,再开引风机和鼓风机。
当炉温(TI1107)还在260℃以上时,可直接通入蒸汽升温,这时可迅速点燃烧嘴,控制升温速度在50℃/h。
其它步骤同正常开车。
若汽包无水位时要恢复送水,建立液位,但要加大排放量清除因干锅形成的沉垢。
然后开引风机和鼓风机,系统开始正常开车。
3.1.1.6系统紧急停车(具体见异常情况的处理)
本装置在正常生产中由于内部故障或因外部条件恶化或控制回路动作,为确保装置和操作人员的安全而采取的非计划性的快速停车称为紧急停车。
当发生紧急停车时可按以下原则进行工作。
(1)值班负责人确认停车原因及停车情况
(2)各岗位检查停车控制回路动作,自动阀的开闭以及转动设备的停车动作是否正确。
(3)向调度室汇报停车情况及联系处理要求。
总之,要尽可能将事故影响限制在局部范围防止扩大,严防产生造成更大的损失。
在装置运转过程中,导致生产用的各种介质中断的原因是很多的,除了后系统的影响造成转化系统需紧急停车外,当发生下述的情况亦需要紧急停车,并采取相应措施:
(1)原料气突然中断。
(2)除氧器(F1103)的水位低而又无法补水。
(3)给水泵跳停汽包给水中断,而备用泵又不能启动使供水立即恢复。
(4)燃料气中断。
(5)炉膛负压维持不住,引风机跳车,而备机又不能启动。
(6)冷却水中断。
(7)突然断电。
(8)仪表空气压力低于0.4MPa工艺指标。
(9)蒸汽管线破裂。
(10)转化管破裂。
(11)工艺蒸汽中断。
(12)其它重大设备事故。
出现以上的情况时,原则上均应采取以下措施:
(1)迅速切断原料气及燃料气;现场关烧嘴根部阀。
(2)全开尾气燃料气放空;
(3)继续通蒸汽,注意蒸汽压力及温度,当转化炉出口温度降到~400℃时,系统保温保压。
若自产蒸汽不够,引外界蒸汽,但一定要注意多排放冷凝水。
(4)此停车过程可暂不装脱硫槽、中变炉进出口盲板。
如果非引风机故障,则在停车过程中保持引风机运行,以维持炉膛负压。
3.4变压吸附工段运行说明
3.4.1PSA工艺过程叙述
PSA提纯氢气装置是由六台吸附塔(E1201A~F),下简称A、B、C、D、E、F塔)、一台气液分离缓冲罐(F1201)、一台产品气缓冲罐(F1202)、一台产品气减压罐(F1203)、一台逆放气缓冲罐(F1204)和一系列程控阀组成。
压力~1.4MPa的