中心轴零件机械加工工艺课程设计.docx
《中心轴零件机械加工工艺课程设计.docx》由会员分享,可在线阅读,更多相关《中心轴零件机械加工工艺课程设计.docx(14页珍藏版)》请在冰豆网上搜索。
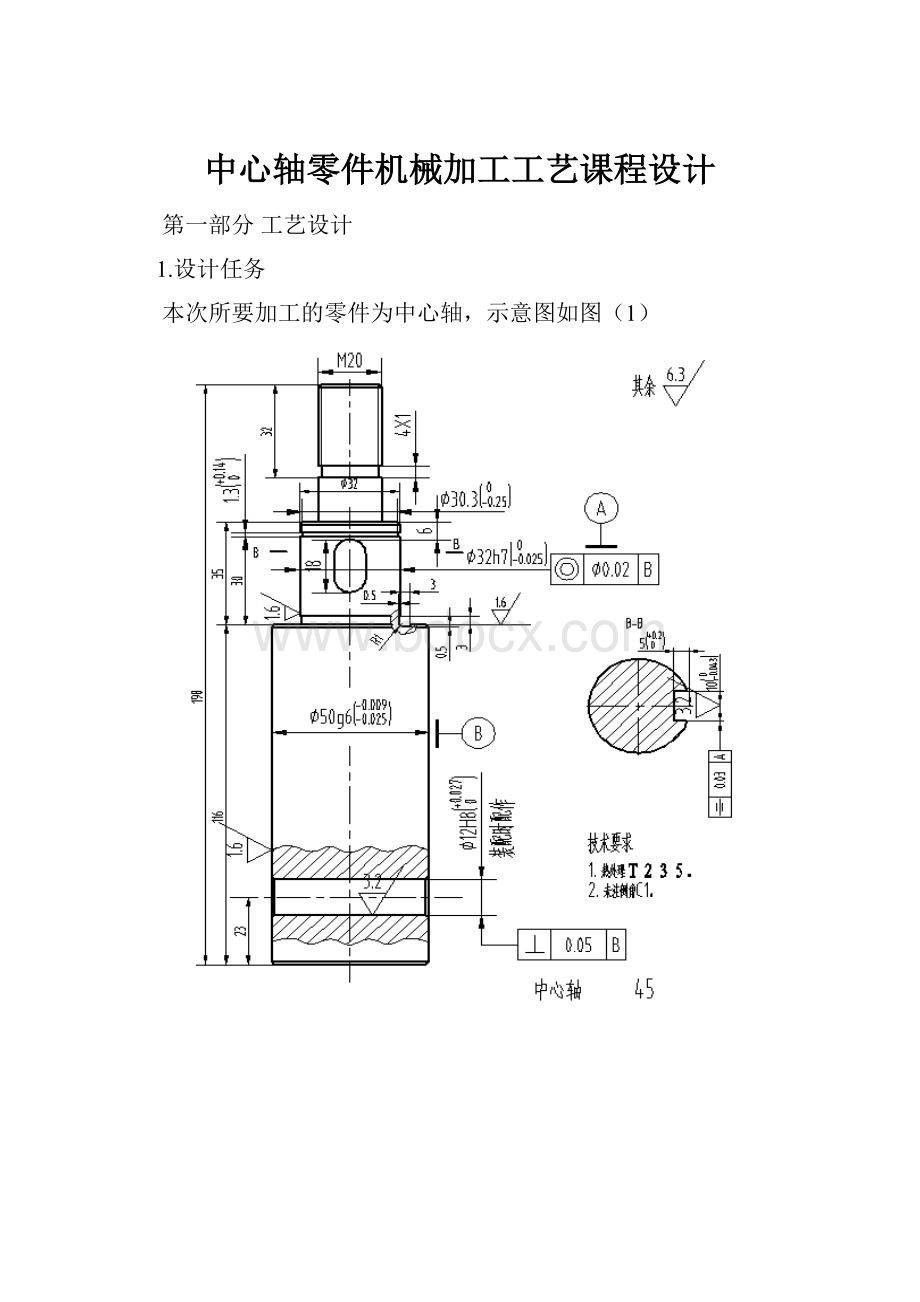
中心轴零件机械加工工艺课程设计
第一部分工艺设计
1.设计任务
本次所要加工的零件为中心轴,示意图如图
(1)
图
(1)
材料:
45
零件生产类型:
中批量生产
2.零件工艺性分析
中心轴零件图的视图正确、完整;尺寸、公差齐全,但技术要求未注明淬火层深度,该零件的结构较为典型,其中,Φ50g6的直径尺寸要求较高,公差为IT6,表面粗糙度为Ra1.6.为主要表面,但加工并不成问题。
零件的另一端面的表面粗糙度度要求并不高为Ra6.3,但在零件的加工过程中均要利用这两个端面来定位,所以也为主要表面。
整个零件中最复杂也是最难加工的地方就是键槽,可使用专门的夹具在普通铣床上加工
此轴为细长轴,考虑到轴的刚性,在加工各轴段外圆表面的过程中特别是是磨削加工的过程中使用三爪卡盘和顶尖定位装夹
3.毛坯的选择
该轴零件加工中,刀具与工件之间的切削力较大。
工件材料的可切削性能。
强度、硬度、塑性、提供冷切削加工、机械性能都跟工件的材料有关。
所以选择45钢为该轴类零件的材料。
45钢相对切削性硬质合金刀具1.0,高速钢刀具1.0,45钢经济合理对加工刀具的要求也合理,45钢用途广泛,主要是用来制造汽轮机、压缩机,泵的运动零件制造齿轮、轴活塞销等零件。
根据以上数据适合该轴的加工。
轴类零件的毛坯有棒料、锻件和铸件三种。
锻件:
适用与零件强度较高,形状较简单的零件。
尺寸大的零件因受设备限制,故一般用自由锻;中、小型零件可选模锻;形状复杂的刚质零件不宜用自由锻。
铸件:
适用于形状复杂的毛坯。
钢质零件的锻造毛坯,其力学性能高于钢质棒料和铸钢件。
根据该轴零件的结构形状和外轮廓尺寸,所以采用棒料。
毛坯的尺寸通过确定加工余量最后可确定尺寸为Φ53*204mm,毛坏示意图如图
(2)
图
(2)
4.工艺过程设计
4.1定位基准的选择
对于中心轴的外圆表面的加工均利用外圆表面定位,对于轴向定位则使用被加工一端的相对端的端面来定位以遵循“基准重合”原则,当掉头装夹的时候使用相反的那端来定位
加工键槽、平面使用起所在轴端的轴线以及与之最靠近的端面来定位,这也符合“基准重合”原则。
4.2零件表面加工方法的选择
本零件的加工表面有外圆、平面、键槽、螺纹、端面、槽等,这里只列举其中较为典型的三个表面来说明其加工方法
(1)Φ50g6外圆表面
精度等级:
IT6表面粗糙度:
Ra61.6µm
加工路线有为
粗车→半精车→粗磨→精磨
(2)键槽侧面
精度等级:
IT9表面粗糙度:
Ra3.2µm
加工路线为
粗铣→半精铣
(3)螺纹M20
精度等级:
表面粗糙度:
Ra6.3µm
加工路线为
在粗磨外圆表面后可车螺纹
4.3制定工艺路线
方案一:
工序10:
下料
工序15:
粗车外圆Φ51.66mm,车中心孔
工序20:
粗车外圆Φ21mm,车台阶面,车外圆Φ33.66mm,车中心孔
工序25:
半精车外圆Φ50.66mm,车倒角C1
工序30:
半精车外圆Φ20mm,车Φ32.66mm,车倒角、沟槽、螺纹
工序35:
调质处理235HBS
工序40:
修研中心孔
工序45:
中检
工序50:
钻Φ12H8的孔
工序55:
铣键槽
工序60:
粗磨外圆至尺寸为Φ50.06h8mm,Φ32.06h8mm
工序65:
精磨外圆至尺寸为Φ50g6mm,Φ32h7mm
工序70:
终检
工序75:
油封入库
方案二:
工序10:
下料
工序15:
粗车外圆Φ51.66mm,车中心孔
工序20:
粗车外圆Φ21mm,车台阶面,车外圆Φ33.66mm,车中心孔
工序25:
半精车外圆Φ50.66mm,车倒角C1
工序30:
半精车外圆Φ20mm,车Φ32.66mm,车倒角、沟槽、螺纹
工序35:
粗磨外圆至尺寸为Φ50.06h8mm,Φ32.06h8mm
工序40:
调质处理235HBS
工序45:
修研中心孔
工序50:
钻Φ12H8的孔
工序55:
铣键槽
工序60:
精磨外圆至尺寸为Φ50g6mm,Φ32h7mm
工序65:
终检
工序70:
油封入库
方案比较:
方案二中将粗磨放在铣削加工之前,其理由是为其后的铣削加工键槽准备较好的辅助基础,但这样会使工件在两台机床之间来回移动,浪费工时,降低生产效率,而且这样做对提高键槽的加工精度的意义并不大,因为在键槽的加工过程中是以其所在轴段的轴线为定位基准。
在淬火前进行磨削加工,由于材料较软,对磨削加工不利,且会在零件的表面产生很大的残余应力。
方案二中还缺少必要的中检工序。
在其精磨后无去应力处理,会使表面有较大的残余应力。
综上所述,选择方案一为此零件的加工路线。
5确定毛坯尺寸、机械加工余量及工序尺寸
5.1确定毛坯的尺寸
零件的最大轴径处为Φ50mm,此外圆表面的路线为:
粗车→半精车
精车的余量为1mm
半精车的余量为2mm
选择直径为Φ50+1+2=Φ53的棒料
端面的加工路线为:
粗车→半精车
余量同上
所以棒料的长度为:
198+(1+2)*2=204mm
所以选择棒料尺寸为:
Φ53X204mm
5.2确定加工余量、工序尺寸以及表面粗糙度
这里选择二个比较典型表面来说明计算其工序尺寸
(1)Φ50g6
mm外圆表面Φ
表1
工序双边余量
工序尺寸及公差
表面粗糙度
精磨
0.06mm
Φ50g6
mm
Ra1.0µm
粗磨
0.6mm
Φ50h8
mm
Ra1.6µm
半精车
1mm
Φ50.66h10
mm
Ra6.3µm
粗车
2mm
Φ51.66
Ra12.5µm
(2)Φ32h7轴段上的键槽和平面工序尺寸的计算。
图(3}
铣削加工键槽的工序是在粗磨工序之前,因此需要考虑铣削加工工序完成之后工序尺寸的精度
6.刀具的选择及切削参数
6.1进给量f的确定
进给量是刀具在进给运动方向上相对于工件的位移量.粗加工时进给量的选择主要受切削力的限制。
根据加工材料、刀杆尺寸、工件直径及已确定的背吃刀量来选取较大的进给量。
在半精加工和精加工时,则按表面粗糙度要求,根据工件材料、刀尖圆弧半径、切削速度来选择合理的进给量。
当切削速度提高,刀尖圆弧半径增大或刀具磨有修光刃时可以选择较大的进给量以提高生产率。
粗铣时高速钢铣刀每齿进给量f=0.10~0.15mm/z
硬质合金钢铣刀每齿进给量f=0.10~0.25mm/z
精铣时高速钢铣刀每齿进给量f=0.02~0.05mm/z
硬质合金钢铣刀每齿进给量f=0.10~0.15mm/z
钻孔时钻头每齿进给量f=0.1~0.2mm/r
扩孔时钻头每齿进给量f=0.2mm/r
粗铰时铰刀每齿进给量f=0.4mm/r
精铰时铰刀每齿进给量f=0.15mm/r
6.2切削深度αp的确定
切削深度是指在垂直于进给方向上待加工表面与已加工表面间的距离。
对于工艺系统刚性允许时,可以选取较大的切削深度,以减少走刀次数,提高生产效率。
对于零件的精度要求较高时,考虑适当留出半精加工和精加工的切削余量。
然而对于数控加工所留的精加工余量一般情况下比普通加工时所留余量小。
铣削时,精加工余量通常为0.2~0.8mm。
和镗削加根据加工余量确定。
粗加工(Ra10~80µm)时一次进给应尽可能切除全部余量。
在中等功率机床上背吃刀量可达8~10mm。
半精加工(Ra1.25~10µm)时,背吃刀量取为0.5~2mm。
精加工(Ra0.32~1.25µm)时,背吃刀量取为0.1~0.4mm。
在工艺系统刚性不足或毛坯余量很大或余量不均匀时,粗加工要分几次进给一般第一次走刀为总加工余量的2/3~3/4。
当工件表面粗糙度值要求为Ra0.8~3.2μm时,铣削分为粗铣、半精铣、精铣三个阶段进行。
精铣时面铣刀的背吃刀量取0.5~1.0mm。
总结本图的背吃刀量选取如下
粗加工时αp=3mm
精加工时αp=0.5mm
粗铰通孔时αp=0.05mm
精铰通孔时αp=0.02mm
6.3切削速度Vc的确定
切削速度是在进行切削加工时,刀具切削刃的某一点相对于待加工表面在主运动方向上的瞬时速度。
Vc主要根据工件材料、刀具材料和机床功率来选择。
⑴刀具材料好,Vc可选得高些。
⑵Ra要求小的,要避开积屑瘤、鳞刺产生的Vc,高速钢Vc刀取小于5m/min,硬质合金钢刀Vc取较高的Vc130~160m/min。
⑶表面有硬皮或断续切削时,应适当降低Vc。
⑷工艺系统刚性差的,Vc应减小。
当主运动为旋转运动时,Vc可按下式计算Vc=лDn/1000D为工件待加工表面或刀具的最大直径(mm)n为主运动的转速。
6.4主轴转速n的确定
在确定主轴转速时,要根据所选择的工件材料、刀具材料、机床功率和加工性质。
如粗、精加工等条件下来确定其允许的切削速度。
切削速度确定之后,再根据n=1000c/лD就可以计算出主轴转速了。
刀具选择的结果如下:
图(4)
刀具切削参数主轴转速
序号
加工内容
刀具规格
n/r.min
进给速度
v
/mm.min
类型
材料
1
粗加工外轮廓
(T01)93°外圆偏刀
硬质合金
180
54
2
精加工外轮廓
(T02)93°外圆偏刀
50
5
3
切螺纹退刀槽
(T03)切槽刀
50
10
4
车M20螺纹
(T04)60°普通螺纹车刀
50
5
表1刀具的切削参数
第二部分夹具设计
1设计任务
设计加工中心轴Φ50g6轴段上钻削Φ12H8孔的钻床夹具
2确定定位方案、选择定位元件
孔的加工需要限制6个自由度,由于此零件为轴类零件,可以以轴套定位,或者以外圆表面用V型块定位限制其中4个自由度,V型块的定心精度比轴套高,且对此零件使用V型块夹紧之后更为方便。
对于V型块也可以选择两个短V型块或一个长V型块,若选择两个短V型块定位,工件的夹紧会很不方便,且对定位精度有一定影响。
长V型块限制x轴和y轴的移动和转动。
对于z轴的转动与移动可以用压板来限制,这样就可实行对孔的加工。
3夹紧机构的选择及设计
夹紧机构有斜楔夹紧机构、螺旋夹紧机构、偏心夹紧机构、铰链夹紧机构、联动夹紧机构等。
该孔的加工为钻削加工,钻削加工的切削力较大,且为间歇切削,震动较大,所以不适合选用偏心夹紧机构,斜楔夹紧机构的效率低,联动夹紧机构的结构较复杂,这里可以选择螺旋夹紧机构或者铰链夹紧机构。
选用螺旋夹紧机构使用压板压紧的优点是压板较宽,使工件的夹紧更稳定,所以选用螺旋夹紧机构。
4定位误差的计算
这里只计算V型块的定位精度是否满足
图(5)
图(6)
工序尺寸:
Φ12H8
mm
工序基准与定位基准不重合且互相垂直,所以基准位置误差△dw=△jw=0.027mm<0.05mm
所以能够满足精度要求
5导向装置
在加工中要确定麻花钻的工作部分处于被加工孔的位置,且最好能保证钻头相对与工件的轴线是垂直的,在钻床夹具中,需要选择钻套,引导刀具进入正确的加工的位置,并防止刀具在加工过程中发生倾斜,提高刀具的刚性。
6夹具在机床上的定位和夹紧
钻床专用夹具在钻床上的定位及夹紧,用紧固螺钉、支撑钉联接夹具及机床。
小结
本次课程设计是综合运用所学知识进行设计实践的环节,为对我们在生产实际中进行调查研究的能力、观察问题、分析问题能力的培养至关重要。
通过课程设计的锻炼,我们运用所学知识的能力、解决问题的能力、创新设计的能力都得到了很好的锻炼和加强。
从方案的论证到具体的设计,查阅了很多的资料,丰富了自己的知识面。
同时通过课程设计使我掌握做好一个设备的流程和所需考虑的主要问题,为以后的工作奠定了基础。
在那上面。
课程设计让我从传统的被动性学习,转变为主动性学习;从闭门读书、死记硬背模式学习,转变为研究性、合作性学习;使工作、学习、生活步入系统化流程等,我认为这种改变是质的飞跃。
经过三个星期的磨练和奋斗,感觉自己进步很大,发现了自己的能力和未被挖掘的潜力。
课程设计不仅使我完善和复习了以前所学知识,同时从老师和同学那里学到了在课本上学不到的知识。
它们将对我以后的工作、学习和生活产生深远影响。
总之,一句话,课程设计使我受益匪浅!
本次设计是在老师耐心指导和悉心关怀下完成的,她对我们的高度责任心,给我的学习、生活和工作有很大的影响,并将激励我永远奋发向上。
参考书目
1.李益民主编机械制造工艺设计简明手册北京:
机械工艺出版社,1993.6
2.徐圣群主编简明机械加工工艺手册上海:
上海科学技术出版社。
3.倪森寿主编机械制造工艺与装备习题集和课程设计指导书北京:
化学工业出版社2003
4.孙本绪熊万武主编机械加工余量手册北京:
国防工业出版社
5.王少俊主编机械制造工艺手册北京:
机械工业出版社1984
6.孟少农主编机械加工工艺设计手册北京:
机械工业设计出版社1982
7.赵家齐主编机械制造工艺学课程指导书北京:
机械工业出版社1993
8.张龙勋主编机械制造工艺学课程设计和课程习题集北京:
机械工业出版社1994
9.马智贤主编机械加工余量手册北京:
中国标准出版社1994
10.赵如福主编金属加工工艺手册上海:
上海科学工艺出版社1992
11.张进生主编机械制造工艺与夹具设计指导北京:
机械工业出版社1995