单级蜗杆减速器机械设计毕业课程设计.docx
《单级蜗杆减速器机械设计毕业课程设计.docx》由会员分享,可在线阅读,更多相关《单级蜗杆减速器机械设计毕业课程设计.docx(29页珍藏版)》请在冰豆网上搜索。
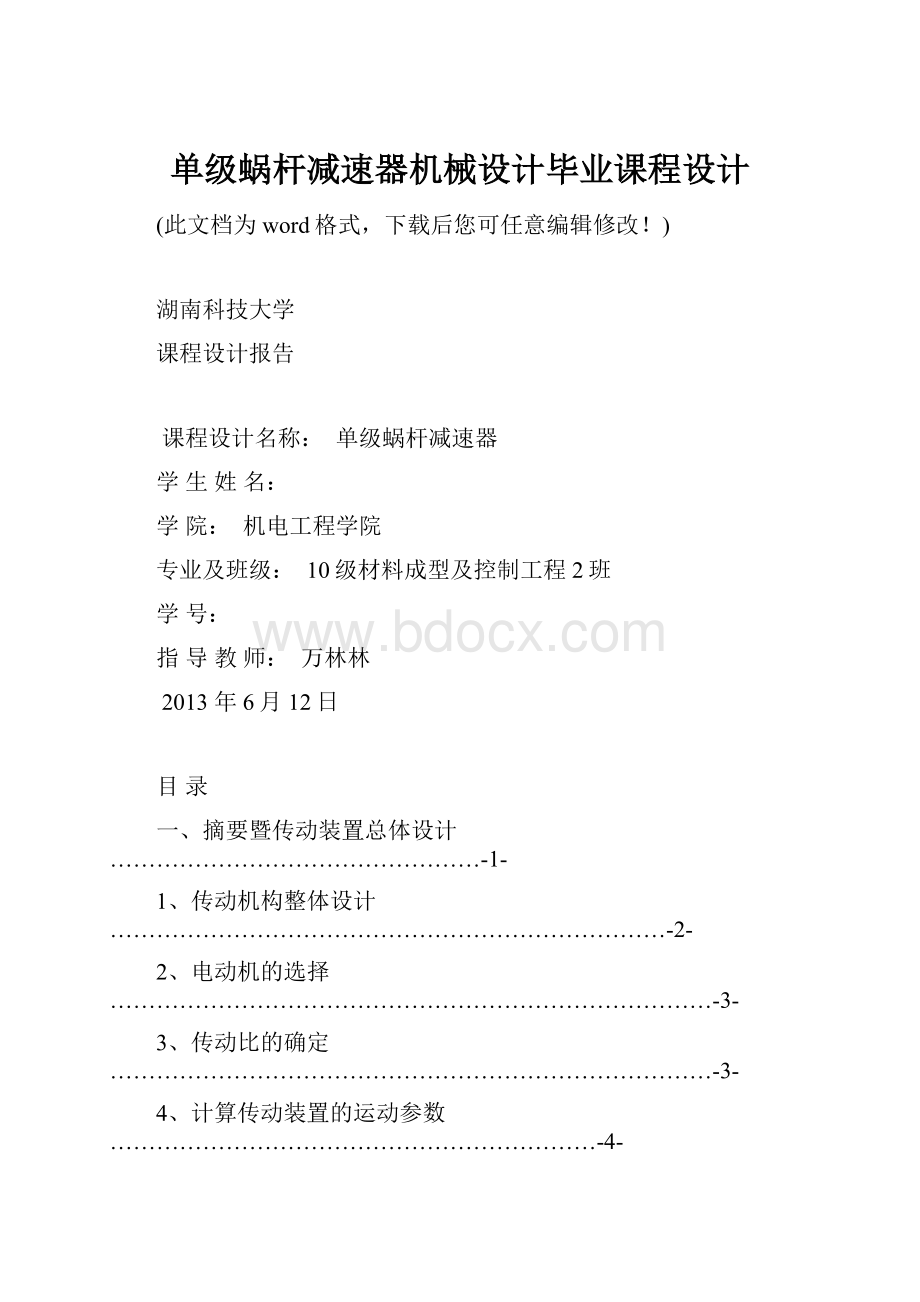
单级蜗杆减速器机械设计毕业课程设计
(此文档为word格式,下载后您可任意编辑修改!
)
湖南科技大学
课程设计报告
课程设计名称:
单级蜗杆减速器
学生姓名:
学院:
机电工程学院
专业及班级:
10级材料成型及控制工程2班
学号:
指导教师:
万林林
2013年6月12日
目录
一、摘要暨传动装置总体设计…………………………………………-1-
1、传动机构整体设计………………………………………………………………-2-
2、电动机的选择……………………………………………………………………-3-
3、传动比的确定……………………………………………………………………-3-
4、计算传动装置的运动参数………………………………………………………-4-
二、传动零件的设计………………………………………………………-4-
1、减速器传动设计计算……………………………………………………………-4-
(1)蜗杆的设计………………………………………………………………-4-
(2)蜗轮的设计………………………………………………………………-6-
2、验算效率…………………………………………………………………………-7-
3、热平衡计算………………………………………………………………………-7-
4、精度等级公差和表面粗糙度的确定……………………………………………-8-
三、轴及轴承装置设计……………………………………………………-8-
1、蜗杆轴的设计…………………………………………………………………-8-
2、蜗轮轴的设计…………………………………………………………………-12-
3、滚动轴承的选择………………………………………………………………-16-
4、键连接及联轴器的选择………………………………………………………-17-
四、机座箱体结构尺寸及附件………………………………………-19-
1、箱体的结构尺寸………………………………………………………………-19-
2、减速器的附件…………………………………………………………………-21-
五、蜗杆减速器的润滑…………………………………………………-24-
1、蜗杆的润滑……………………………………………………………………-24-
2、滚动轴承的润滑………………………………………………………………-24-
六、设计体会…………………………………………………………………-24-
七、参考文献…………………………………………………………………-25-
1、摘要
—传动装置总体设计
1、传动机构整体设计
根据要求设计单级蜗杆减速器,传动路线为:
电机——联轴器——减速器——联轴器——带式运输机。
(如图右图所示)根据生产设计要求可知,该蜗杆的圆周速度V≤4——5ms,所以该蜗杆减速器采用蜗杆下置式见(如图下图所示),采用此布置结构,由于蜗杆在蜗轮的下边,啮合处的冷却和润滑均较好。
蜗轮及蜗轮轴利用平键作轴向固定。
蜗杆及蜗轮轴均采用圆锥滚子轴承,承受径向载荷和轴向载荷的复合作用,为防止轴外伸段箱内润滑油漏失以及外界灰尘,异物侵入箱内,在轴承盖中装有密封元件。
该减速器的结构包括电动机、蜗轮蜗杆传动装置、蜗轮轴、箱体、滚动轴承、检查孔与定位销等附件、以及其他标准件等。
总传动比:
i=35Z1=1Z2=31
为了确定传动方案先初选卷筒直径:
D=300mm运输带速度:
V=1.3ms
卷筒转速=60×1000v(D)=60×1000×1(×300)rmin=82.80rmin
而i=35,并且=,
所以有=i=35.02×82.80=2899.656rmin选择同步转速为1500r,满载转速为2900rmin的电动机。
===82.80rmin
由=60×1000v(D)可得D≈300mm
2、选择电动机
(1)选择电动机类型
按已知工作要求和条件选用Y系列一般用途的全封闭自扇冷鼠笼型三相异步电动机.
(2)选择电动机容量
工作机要求的电动机输出功率为:
其中
则
由电动机至运输带的传动总效率为:
式中,查机械设计手册可得
联轴器效率=0.99
滚动轴承效率=0.98
单头蜗杆效率=0.72
转油润滑效率=0.96
卷筒效率=0.96
则
61.2%
初选运输带有效拉力:
F=5000N
从而可得:
=6.5kw
电动机型号表一
方案
电动机型号
额定功率
Pedkw
电动机转速rmin
额定转矩
同步转速
满载转速
1
Y132S2-2
7.5
3000
2900
2.0
2
Y132S2-4
7.5
1500
1440
2.2
3
Y160M-6
7.5
1000
960
2.0
4
Y160L-8
7.5
750
720
2.0
(3)确定电动机转速
有前面可知电机的满载转速为2899rmin
从而可以选取Y132S2-2以下是其详细参数
Y132S2-2的主要性能参数
额定功率
kw
同步转速
n(r)
满载转速
n(r)
电动机总重N
启动转矩
额定转矩
最大转矩
额定转矩
7.5
3000
2900
2.0
2.3
3、传动比的确定
由前面可知总传动比i总=i=35
4、计算传动装置的运动和动力参数
(1)各轴转速
蜗杆轴n1=2900min
齿轮轴n2=290035=82.81rmin
卷筒轴n3=n2=82.81rmin
(2)各轴的输入功率
蜗杆轴p1==6.3063kw
齿轮轴p2=p1=4.2717kw
卷筒轴p3=p2=3.0449kw
(3)各轴的转矩
电机输出转矩=9550=(9550×6.5)2900N·m=21.41N·m
蜗杆输入转矩==21.41×0.99×0.98N·m=20.77N·m
蜗轮输入转矩=i=20.77×35×0.98×0.72×0.96N·m=14.06N·m
卷筒输入转矩==492.1×0.99×0.98N·m=477.43542N·m
将以上算得的运动和动力参数列于表2-2
表2-2
类型
功率P(kw)
转速n(rmin)
转矩T(N·m)
传动比i
效率η
电动机轴
6.5
2900
21.41
蜗杆轴
6.3063
2900
20.77
0.61
蜗轮轴
4.2717
82.81
492.1
35
传动滚筒轴
3.0449
82.81
477.43542
二、传动零件的设计
1、减速器传动设计计算
蜗杆的设计
(1)选择蜗杆传动类型
根据GBT的推存,采用渐开线蜗杆(ZI)。
(2)选择材料
蜗杆:
根据库存材料的情况,并考虑到蜗杆传动传递的功率不大,速度只是中等,故蜗杆用45钢;因希望效率高些,耐磨性好些,故蜗杆螺旋齿面要求淬火,硬度为45~55HRC。
因而蜗轮用铸锡磷青铜ZCuSn10P1,金属模铸造。
为了节约贵重的有色金属,仅齿圈用青铜制造,而轮芯用45号或者铸铁HT100钢制造。
(3)按齿面接触疲劳强度进行设计
根据闭式蜗杆传动的设计准则,先按齿面接触疲劳强度进行设计,再校核齿根弯曲疲劳强度。
由手册知传动中心距
≥
①确定作用在蜗轮上的转距
由前面可知=492.1N·m
②确定载荷系数K
因工作载荷较稳定,故取载荷分布不均系数=1;
由机械设计手册取使用系数=1.15
由转速不高,冲击不大,可取动载荷系数=1.05;
K==1.21
③确定弹性影响系数
因用铸锡磷青铜蜗轮和钢蜗杆相配,故=160
④确定接触系数
假设蜗杆分度圆直径d和传动中心距a的比值da=0.35,从而可查得=2.9
⑤确定许用接触应力
根据蜗轮材料为铸锡磷青铜ZCuSn10P1,金属模铸造,蜗杆螺旋齿面硬度>45HRC,可从手册中查得蜗轮的基本许用应力=268
应力循环次数N=60j=60×1×123×8×365×16=3.4×
寿命系数==0.61
则==0.61×268=163.48
⑥计算中心距
≥
mm=104.55mm
取中心距a=125mm,i=35,完全满足要求,取模数m=5,蜗杆分度圆直径d1=50mm。
这时d1a=0.4,根据机械设计可查接触系数=2.75,由于,因此以上计算结果可用。
⑷蜗杆与蜗轮主要几何参数
①蜗杆
轴向齿距pa=zm=15.7mm
直径系数q=d1m=10
齿顶圆直径da1=d1+2m=50+2×1×5mm=60mm
齿根圆直径df1=d1-=d1-2m(+)=50-2×(1×5+0.2×5)mm=38mm
导程角γ=18’36’’
蜗杆轴向齿厚Sa=0.5m=7.85mm
蜗杆尺宽b1=91mm
蜗轮的设计
蜗轮的齿数Z2=31;变位系数X2=-0.5;
验算传动比
这时传动比误差为,是允许的。
蜗轮齿数=31
变位系数=-6587
分度圆直径=m=5×31=155mm
齿顶圆直径da2=+2ha2=155+2×5(1-0.6581)=158.419mm
齿根圆直径df2=-=155-2×(1×5+0.2×5)mm=143mm
蜗轮咽喉母圆半径Yg2=a-0.5da2=.419mm=45.7905mm
⑸校核齿根弯曲疲劳强度
当量齿数
由=-0.6587,=32.88,查机械设计手册可得齿形系数=3.35
螺旋角系数=1-=1-=0.9192
许用弯曲应力=
从手册中查得由ZCuSn10P1制造的蜗轮的基本许用弯曲应力=56
寿命系数
==0.487×56=14.67
弯曲强度是满足的。
计算中心距
2、验算效率
已知γ=18’31’’=,;与相对滑动速度有关
==3.845ms
查表可得=0.0236,
代入式中可得87%大于原估计值,因此不用重算。
3、热平衡计算
散热面积A
取传热系数,取,从而可以计算出箱体工作温度
因为,所以符合要求。
4、精度等级公差和表面粗糙度的确定
考虑到所设计的蜗杆传动是动力传动,属于通用机械减速器,从GBT圆柱蜗杆、蜗轮精度中选择7级精度,侧隙种类为c,标注为7cGBT。
然后由有关手册查得要求的公差项目及表面粗糙度,详见图纸。
三、轴及轴承装置的设计
1、蜗杆轴的设计
(1)最小直径的确定
由于蜗杆的直径很小,可以将蜗杆和蜗杆轴做成一体,即做蜗杆轴。
蜗杆的转矩。
蜗轮的转矩N·m
则作用于齿轮上的圆周力:
轴向力:
径向力:
初步确定轴的最小直径
先按参考文献1式15-2初步估算轴的最小直径。
选取轴的材料为45钢,调质处理。
根据表15-3,取,于是得
输出轴的最小直径显然是安装联轴器处轴的直径。
为了使所选的轴的直径与联轴器的孔径相适应,故需同时选取联轴器型号。
(2)联轴器的选择
联轴器的计算转矩,查文献1表14-1,考虑到转矩变化很小,故取,则:
按照计算转矩应小于联轴器公称转矩的条件,查参考文献2表14-4,选用LX2型弹性柱销联轴器,其公称转矩为560000N·mm。
半联轴器的孔径d1=25mm,故取d12=25mm,半联轴器长度L=62mm,半联轴器与轴配合的毂孔长度L1=44mm。
(3)轴上零件的装配方案
蜗杆是直接和轴做成一体的,左轴承及轴承端盖从左面装,右轴承及右端盖从右面装。
(4)轴向定位及轴各段直径和长度
1)为了满足半联轴器的轴向定位要求,1-2轴段右段需制出一轴肩,故取2-3段直径d23=28mm;左端用轴端挡圈定位,按轴端直径取挡圈直径D=30mm。
半联轴器与轴配合的毂孔长度L1=44mm,为了保证轴端挡圈只压在半联轴器上而不压在轴的端面上,故1-2段的长度应比L1短一些,现取L12=42mm。
2)初步选择滚动轴承。
因轴承同时受有径向力和轴向力的作用,故选用单列圆锥滚子轴承。
参照工作要求并根据mm,由轴承产品目录中初步选取0基本游隙组、标准精度级的单列圆锥滚子轴承30206,其基本尺寸
,故,则。
3)由于蜗杆的齿根圆为38mm,故取轴段mm。
蜗杆的轴承内侧采用轴环定位,轴肩高度h>0.07d,故取h=5mm,则轴环处的直径,轴环宽度,取。
4)轴承端盖的总宽度为20mm,根据轴承端盖的装拆以及便于对轴承添加润滑脂的要求,取端盖的外端面与半联轴器右端面间的距离,故取。
5)由于箱体由蜗轮决定,轴承采用脂润滑,蜗杆齿宽,滚动轴承宽度,
则
(5)轴上零件的周向定位
半联轴器与轴的周向定位均采用平键连接。
按=25mm,由文献一表6-1查得平键截面,键槽用键槽铣刀加工,长为36mm,同时为了保证齿轮半联轴器与轴的配合为。
滚动轴承与轴的周向定位是由过度配合来保证的,此处选用轴的直径尺寸公差为m6。
(6)确定轴上圆角和倒角尺寸
参考文献一表15-2,取轴端倒角为,各处轴肩的圆角半径如下:
,,,
,,
蜗杆轴的校核
蜗杆轴校核
设蜗杆齿宽的法向中心线的有侧长为,左侧的长度为,则:
水平面的支承反力(图a)
垂直面的支承反力(图b)
绘水平面的弯矩图
绘垂直面的弯矩图
绘合成弯矩图
该轴所受扭矩为:
10.21N·m=10210N·mm
按弯扭合成应力校核轴的强度
由图可知轴承上截面C为危险截面,根据文献1式(15-5)及以上数据,以及轴单向旋转,扭转切应力为脉动循环变应力,取α=0.6,轴的计算应力
前已选定轴的材料为45钢,调质处理,由文献1表15-1查得。
因此<,故安全。
由于轴的最小直径是按扭转强度很宽裕地确定的,由蜗杆轴受力情况知截面C处应力最大,但其轴径也较大,且应力集中不大,各处应力集中都不大,故蜗杆轴的其它截面的疲劳强度不必校核。
2、蜗轮轴的设计
(1)最小直径的确定
蜗轮上的转矩。
则作用于齿轮上的
圆周力:
轴向力:
径向力:
初步确定轴的最小直径
先按文献1式15-2初步估算轴的最小直径。
选取轴的材料为45钢,调质处理。
根据表15-3,取,于是得
输出轴的最小直径显然是安装联轴器处轴的直径。
为了使所选的轴的直径与联轴器的孔径相适应,故需同时选取联轴器型号。
(2)联轴器的选择
联轴器的计算转矩,查文献1表14-1,考虑到转矩变化很小,故取,则:
按照计算转矩应小于联轴器公称转矩的条件,查参考文献2表14-4,
选用LX3型弹性柱销联轴器,其公称转矩为1250N·m。
半联轴器的孔径d1=35mm,故取d12=35mm,半联轴器长度L=82mm,半联轴器与轴配合的毂孔长度L1=60mm。
(3)根据轴向定位的要求确定轴的各段直径和长度
根据蜗轮结构尺寸,取=45mm。
为了满足半联轴器的轴向定位要求,1-2轴段右段需制出一轴肩,故取2-3段直径=38mm;左端用轴端挡圈定位,按轴端直径取挡圈直径D=40mm。
半联轴器与轴配合的毂孔长度L1=60mm,为了保证轴端挡圈只压在半联轴器上而不压在轴的端面上,故1-2段的长度应比L1短一些,现取L12=58mm。
初步选择滚动轴承。
因轴承同时受有径向力和轴向力的作用,故选用单列圆锥滚子轴承。
参照工作要求并根据,由轴承产品目录中初步选取0基本游隙组、标准精度级的单列圆锥滚子轴承30208,其基本尺寸
,故,而。
右端滚动轴承采用轴肩进行轴向定位。
取轴肩高度h=5mm,因此,取=50mm。
蜗轮的右端采用轴肩定位,轴肩高度h>0.07d,故取h=5mm,则轴环直径=55mm。
轴环宽度,则取=10mm。
轴承端盖的总宽度为20mm,根据轴承端盖的装拆以及便于对轴承添加润滑脂的要求,取端盖的外端面与半联轴器右端面间的距离,故取。
轴承宽度为19.75mm,取挡圈宽度为15mm,所以=20+15+2=37mm。
=(1.2~1.8),则取=60mm;取=16mm。
所选轴承的外形如前面所选轴承图所示。
(4)蜗轮轴的校核
设蜗杆齿宽的法向中心线的有侧长为,左侧的长度为,则:
水平面的支承反力(图a)
垂直面的支承反力(图b)
绘水平面的弯矩图
绘垂直面的弯矩图
绘合成弯矩图
该轴所受扭矩为
按弯扭合成应力校核轴的强度
由图可知轴承上截面C为危险截面,根据文献1式(15-5)及以上数据,以及轴单向旋转,扭转切应力为脉动循环变应力,取α=0.6,轴的计算应力
前已选定轴的材料为45钢,调质处理,由文献1表15-1查得。
因此<,故安全。
由于轴的最小直径是按扭转强度很宽裕地确定的,由蜗轮轴受力情况知截面C处应力最大,但其轴径也较大,且应力集中不大,各处应力集中都不大,故蜗轮轴疲劳强度不必校核。
3、滚动轴承的选择
蜗杆轴上轴承的校核
1)蜗杆轴滚动轴承校核
蜗杆上的轴承代号为:
30206
2)蜗杆受力
蜗杆的转矩。
则作用于齿轮上的圆周力:
轴向力:
径向力:
3)当量动载荷
由已知条件知道工作时间为8年,每年按365天计算,且每天二班制工作,则大概总的工作时间为:
当量动载荷P=,查表13-5得:
X=0.4,Y=1.5;查表13-6得:
;故P===4917N
由参考文献1式13-6a知基本额定动载荷
查表13-4得;对于滚子轴承ε=
故=83380N
4)校核轴承的寿命
查文献2表13-1得C=43.2KNε=103n=2900rmin
故,此轴承的寿命满足要求
蜗轮轴上轴承的校核
1)蜗轮轴上轴承的校核
蜗轮上的轴承代号为:
30208
2)蜗轮受力
蜗轮上的转矩。
则作用于齿轮上的
圆周力:
轴向力:
径向力:
3)求当量动载荷
由已知条件知道工作时间8年,每年按365天计算,且每天二班制工作,则大概总的工作时间为:
当量动载荷P=,查表13-5得:
X=0.4,Y=1.7;查表13-6得:
;
故P==1.2x(0.4x66.03+1.7x83.08=1726.526N
由参考文献1式13-6a知基本额定动载荷
查表13-4得;对于滚子轴承ε=
故=10074.97N
5)校核轴承的寿命
查文献2表13-1得C=63KNε=103n=1440rmin
故,此轴承的寿命满足要求
5、键联接和联轴器的选择
(1)选择键联接的类型和尺寸
本设计中有三处要求使用键联接,一处为减速器输入轴(蜗杆)的联轴器处,设置在蜗杆上的键标此处为键1此处轴的直径d1=25mm。
一处是减速器输出轴(蜗轮轴)的联轴器处,设置在蜗轮轴上的键标此处为键2此处轴的直径d2=35mm。
另一处是蜗轮与蜗轮轴的联接,标记此处的键为键3此处轴的直径d3=45mm。
一般8级以上的精度要有定心精度的要求,所以选择用平键联接,由于只是联接的是两根轴,故选用圆头普通平键(A)型。
而键3的蜗轮在轴的中间,所以也选择圆头普通平键(A)型。
根据以上的数据,从文献1表6-1中查得键1的截面尺寸为:
B(mm)
H(mm)
L(mm)
键Ⅰ
14
9
70
键Ⅱ
14
9
70
键Ⅲ
18
11
70
(2)校核键联接的强度
键Ⅰ处键、轴和联轴器的材料是钢和铸铁,且属于静联接由文献1的表6-2查得许用挤压应力为[]=120~150MPa,取其平均值,[]=135MPa。
键的工作长度为l=L-b=36mm-8mm=28mm,键与轮毂的键槽的接触高度为k=0.5h=0.5×7mm=3.5mm。
由文献1的式6-1可得
可见联接的挤压强度满足,即该键可以正常工作。
键Ⅱ处键、轴和蜗轮的材料是钢和铸铁,且属于静联接由文献1的表6-2查得许用挤压应力为[]=MPa,取其平均值,[]=135MPa。
键的工作长度为l=L-b=50mm-10mm=40mm,键与轮毂的键槽的接触高度为k=0.5h=0.5×8mm=4mm。
由文献1的式6-1可得
可见联接的挤压强度满足,即该键可以正常工作。
键Ⅲ处键、轴和联轴器的材料是钢和铸铁,且属于静联接由文献1的表6-2查得许用挤压应力为[]=MPa,取其平均值,[]=135MPa。
键的工作长度为l=L-b=32mm-14mm=18mm,键与轮毂的键槽的接触高度为k=0.5h=0.5×9mm=4.5mm。
由文献1的式6-1可得
可见联接的挤压强度满足,即该键可以正常工作。
自此减速器中的所有的键均以校核完毕,所有的键均满足使用要求。
键的外型图和键槽的安装图:
四、机座箱体结构尺寸及其附件
1、箱体的结构尺寸
(1)箱座高度
齿高为:
则齿轮浸油深度符合条件齿轮浸油深度大于10mm的要求。
总的油深
箱体内储油宽度大约为160mm
箱体内储油长度大约为350mm
则储藏的油量
单级减速器每传递1kw的功率所需的油量:
符合要求。
(2)箱体的刚度设计
⑴箱体结构形式的选择
选择本蜗杆减速器的箱体形式为剖分式.由于蜗杆圆周速度小于10ms,故采用蜗杆下置式
⑵箱体材料的选择与毛坯种类的确定
根据蜗杆减速器的工作环境,可选箱体材料为灰铸铁HT200.由于铸造箱体刚性好,易得到美观的外形,灰铸铁铸造的箱体还易于切削、吸收振动和消除噪音等优点,可采用铸造工艺获得毛坯.
从参考文献2表4-1,表4-2可得下表:
名称
符号
蜗轮蜗杆减速器尺寸
选用
箱座壁厚
8
箱盖壁厚
8
箱盖凸缘厚度
12
箱座凸缘厚度
12
箱座底凸缘厚度
20
地脚螺钉直径
地脚螺钉数目
4
轴承旁联结螺栓直径
盖与座联结螺栓直径
联结螺栓间距
175
轴承端盖螺钉直径
视孔盖螺钉直径
定位销直径
至外箱壁距离
26、22、18、16
至凸源边缘距离
20、16、14
轴承旁凸台半径
16
凸台高度
45
外箱壁至轴承座端面距离
42
蜗轮顶圆与内壁的距离
10
蜗轮轮毂端面与内壁距离
9
箱盖、箱座肋厚
轴承端盖外径
120
轴承旁联结螺栓距离
120
2、减速器的附件
(1)窥视孔及视孔盖
图8
参考文献2表4-3得:
表8
直径
孔数
90
75
60
-
70
55
40
7
4
4
5
(2)通气器
由已知选型号
外型安装图:
图9
查参考文献2表4-5可得:
表9
8
3
16
40
40
12
7
16
18
40
25.4
22
6
2
2
(3)油标尺
由条件可选M16型的。
安装图:
图10