合成氨生产工艺合成岗位2.docx
《合成氨生产工艺合成岗位2.docx》由会员分享,可在线阅读,更多相关《合成氨生产工艺合成岗位2.docx(24页珍藏版)》请在冰豆网上搜索。
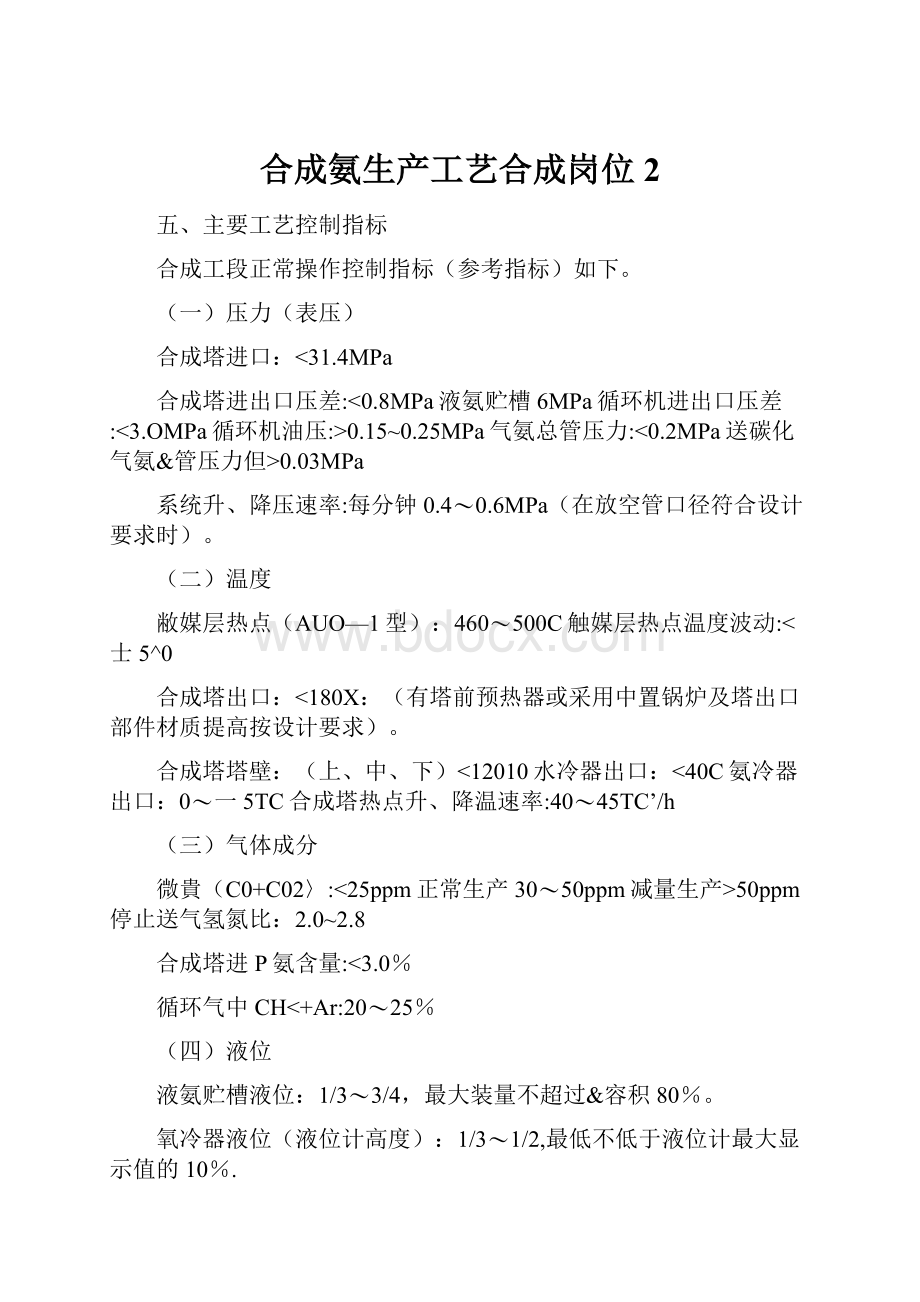
合成氨生产工艺合成岗位2
五、主要工艺控制指标
合成工段正常操作控制指标(参考指标)如下。
(一)压力(表压)
合成塔进口:
<31.4MPa
合成塔进出口压差:
<0.8MPa液氨贮槽6MPa循环机进出口压差:
<3.OMPa循环机油压:
>0.15~0.25MPa气氨总管压力:
<0.2MPa送碳化气氨&管压力但>0.03MPa
系统升、降压速率:
每分钟0.4〜0.6MPa(在放空管口径符合设计要求时)。
(二)温度
敝媒层热点(AUO—1型):
460〜500C触媒层热点温度波动:
<士5^0
合成塔出口:
<180X:
(有塔前预热器或采用中置锅炉及塔出口部件材质提高按设计要求)。
合成塔塔壁:
(上、中、下)<12010水冷器出口:
<40C氨冷器出口:
0〜一5TC合成塔热点升、降温速率:
40〜45TC’/h
(三)气体成分
微貴(C0+C02〉:
<25ppm正常生产30〜50ppm减量生产>50ppm停止送气氢氮比:
2.0~2.8
合成塔进P氨含量:
<3.0%
循环气中CH<+Ar:
20〜25%
(四)液位
液氨贮槽液位:
1/3〜3/4,最大装量不超过&容积80%。
氧冷器液位(液位计高度):
1/3〜1/2,最低不低于液位计最大显示值的10%.
氨分离器、冷交换器液位:
以不带液、不跑气为准。
(五)电加热器对地绝缘电阻值>0.2MQ。
(六)循环机电机电流及温升按铭牌规定。
冰机岗位正常操作控制指标如下(参考指标)。
(一)压力(表压)
进口气氨压力:
0.08〜0.2MPa出口气氨压力:
<1.6MPa油泵出口油压:
>0.15〜0.25MPa
(二)温度
冰机出口气氨温度:
C150X:
循环油温度:
<50-C
(三)液位(液位计高度)
曲轴箱油位:
1/2〜2/3
(四电机电流及温度按铭牌规定值。
第二节本工段生产特点、常见事故及预防
一、生产特点
在小氮肥工业生产过程中是以合成氨为中心的。
在氨合成工段以前的工序,所有的生产过程诸如原料气的制造、气体的净化和压缩等都是为了满足氨的合成对原料气的要求而采取的措沲。
可以说小合成氨工业中所有的其它工序都要根据氨合成工序的要求来进行调节和操作。
因此,如何安全、合理、有效地对本工段进行控制,是关系到全广的安全生产和经济效益的重要环节。
下面从安全生产的角度来分析本工段的特点。
(一)高压高温
氨的合成反应是在髙压、高温下进行的。
由于氨合成反应是体积缩小的反应。
操作压力高对反应的化学平衡和反应速度都是有利的,因此压力愈高愈有利于合成反应。
但压力过高又受到设备的限制,所以目前小合成氨采用中压法生产,操作压力为31.4MPa和20MPa。
此压力虽然就合成氨而言属中压法制氨的范围内,但其压力数值已属名符其实的高压。
又由于氨合成反应为放热反应,温度降低有利于提高氨净值。
但为了加快反应速度,又必须控制在一定的操作温度下进行。
从使用的触媒要求来看,温度过低,轻则使催化剂活性下降,氨合成率降低,消耗增加;重则达不到催化剂的活性温度使反应不能进行。
温度过高又会使触媒烧结,铁微晶增大而失去活性。
所以氨的合成反应是控制在480〜500X:
左右的高温下进行的。
由此可见,高压高温是合成氨的生产能够进行的基本条件、也是合成工段生产的首要特点。
虽然高压髙温能加速化学反应,高压还能提高设备生产能力,减少占地,节省投资,但是高压高温给本工段的安全生产带来了许多不利因素。
第一,在高压高温下,氢氮气对钢材的腐蚀作用加剧。
主要是氢气在高压高温下对碳钢有较强的渗透能力,形成氢腐蚀,使钢材脱碳而变脆,产生所谓的“氢脆”。
氮气也会对设备发生渗氮作用从而减弱其机械性能。
氢脆区最易产生裂纹,从而使设备强度降低而破坏。
第二,材料自身在高压高温下也会发生持续的塑性变形积累,改变其金相组织从而引起材质强度、延伸率等机械性能下降,使材料产生拉伸、鼓泡、变形和裂纹而破坏。
第三:
高压髙温能使可燃气体的爆炸极限扩大,髙压更对上限影响较大。
如氨在常温下的爆炸极限为15.5〜27%而在100X:
时则变为14.5〜29.5%,常压下CH,的爆炸上限为15%,而在12.3MPa时则扩大为45.7%,由于爆炸界限加宽使其危险性增加。
第四:
高压高温时设备维护不利,会增加设备管道泄漏因素,因此对设备(备件)的设计、材质、制造、维修和管理提出了比常压常温设备更严格的要求。
(二)高压、低压并存相通
高压、低压同时存在,并互相连通是本工段的第二个特点。
两种不同的压力系统并存
本工段有两种操作压力,一种是高压31.4MPa的压力系统即氨合成操作部分;另一种是中压1.6MPa的氨分离操作部分。
两种不同而又相差甚大的压力系统同时存在又彼此紧密相连。
对操作上提出了高要求。
在氨分离器和冷交换器下部的氨分离器内,高压气体通过液氨及输送液氨的管道和中压贮槽部分相通;并通过放氨液位加以控制。
如果放氨操作失误或其它设备方面原因,氨分离器的液位控制过低,就易造成高压气窜入贮槽系统,引起贮槽超压爆炸。
其结果是大量液氨外泄,使人中毒窒息,危害极大。
小氮肥厂因此原因而造成这类事故已多次发生。
高、低压设备并存
合成工段高压部分均为高压设备,但在高压设备内套有低压设备。
主要有合成塔里的内套和冷交换器上部的换热器内芯。
以合成塔为例。
合成塔被称为合成氨工业的心脏,内件结构复杂,里面装有触媒筐、换热器、电加热器等部件,在高温高压下工作。
理论上要求合成塔各部件应既能承受高压、又能承受高温。
但是目前金属材料的性能不能同时达到这个要求,所以在设计合成塔时就要求各部件承受高压的不承受高温,承受高温的不承受高压。
因此合成塔有内套和外壳。
合成塔的外筒承受高压但不承受高温,内套承受高温但不承受髙压,而内外套之间的环隙中不断通过的冷气带走高温内套辐射的热量使塔壁温度升高不多。
这样合成塔的外筒,能承受31.4MPa的压力,是高压设备。
而内套只能承受0.8MPa的压力,是低压设备。
另外还有一类是低压部分套在高压部分外面的设备。
在高压氨冷器中,通髙压气的蛇形盘管为高压区,外壳包含的氨冷器液氨蒸发部分为低压区。
在软水加热器中,内管为高压气管,属高压;套管里的软水部分为低压区。
由于高低压设备并存,也给安全生产带来了难度。
常发生由于操作不当造成合成塔压差增大,而使内套损坏,导致生产不能进行的事故。
或者发生由于系统压差增大使冷交内芯漏气损坏的事故。
冷交漏气后,气体走近路管内压力高的气体跑至管外,不仅造成进口氨含量增高,合成反应不好,影响氧产量外,更重要的是气体不经氨冷器直接进入合成塔,使补充气中含有的几百ppm蒸汽进入触媒而引起触媒中毒失效。
如果在触媒还原过程中漏气,则危害更大,会使还原后触媒活性大大降低。
在氨冷器和软水加热器中,如果高压蛇管和高压管泄漏或破裂,(因为包在里面往往不易被发现),会使高压气体进入低压部分引起氨冷器壳体爆炸和软水加热器套管爆炸,或高乐气进入套管软水系统造成锅炉泵抽空,或变换精炼等用软水岗位的故障。
事故统计表明这类事故也屡有发生。
高低压设备并存对本工段的设备管理和操作也提出高的要求。
(三)有催化剂存在
氨的合成反应必须在有催化剂(又称触媒)存在条件"F才能进行,这是本工段生产的第三个特点。
由于氮分子的高度稳定性,欲断裂氮-氮键需要巨大的能量。
因此H2和Nz合成NH3的反应,在常温常压下几乎是不可能的,即使是在很高的温度下其反应速度仍然非常慢。
而催化剂的作用主要是改变反应的途径,从而降低了反应过程的阻力。
它能使由比和乂合成为氨的反应在不太高的温度下具有较高的反应速度。
从而使氨的合成有了工业化的可能。
因此有催化剂存在是工业化制氨的必要前提。
目前小合成氨厂使用的为A系氨合成催化剂,其主要原料是天然磁铁矿,化学成分为Fe300真正起触媒作用的是多孔的(X型海绵状的纯铁。
触媒经过一段时间的使用后会因毒物入侵(氧和含氧化合物,如蒸汽、co、co2、o2和硫、磷、砷及其化合物)使其中毒和衰老,活性降低而需要更换。
在高温、高压下如果触媒保护使用不当,带油、带铜液、带液氨、过氧、微量高、温度、压力波动频繁、超指标等,都会增加毒物对触媒的毒害,并易造成触媒的破碎、活性下降并缩短使用周期。
由于触媒的更换过程比较复杂,耗时多、费用高、需全厂停车,常安排在大修中进行。
因此在生产中创造条件,满足催化剂的使用需求,精心维护、保养触媒,防止触媒中毒和老化,做到催化剂活性高,使用寿命长是保证稳产高产,安全生产的重要措施。
(四)易燃易爆
易燃易爆是合成工段第四个特点。
从设备上来看,无论是高压的合成部分设备,还是氨分离贮存系统都属于压力容器。
当压力容器由于设备本身缺陷、或外界压力超过其承受压力时,便会发生物理性爆炸。
如液氨贮槽由于高压气倒入超压而发生爆炸事故。
另一方面由于所承受的介质属于易燃易爆物质,一旦发生事故伤亡损失严重,破环力大。
如小氮肥厂贮槽容积在5〜50m3,一旦贮槽爆炸,瞬间几吨乃至几十吨液氨泄出,立即挥发为气氨。
气氨是可燃物-,和空气混合后遇火源发生二次爆炸,爆炸力大,还会损坏其它设备;加之氨有毒性,挥发后能造成大面积污染和人员大量伤亡。
资料表明一吨液氨可使28万立方米的空间受到致命污染。
因而漳成设备损坏厂毁人亡,后果不堪设想。
进入合成工段补充气体中含H2大约70〜74%,含Nz约:
20〜25%,含CH4约1〜2%,循环气中含有H2、N2、NH3、CH4、Ar等。
它们之中除了N2和Ar外,H2、NH3、CH4气体均为易燃易爆物质,当与空气混合到一定比例,在遇火源或高温的影响下,就会发生着火与化学性爆炸。
而氢的爆炸界限为4.0〜74.2%,下限较低,爆炸浓度范围较宽,因此其爆炸的危险性最大。
如果高压气体从设备中泄漏出来,即使数量不多,也极易于空气混合而达到爆炸范围,在遇火源或放空过快和泄漏严重时,由于气体流速大,与设备摩擦产生高温和静电即能引起爆炸。
本工段常见的有合成塔顶着火和循环机泄漏高压气体冲出造成的爆炸事故。
可燃性气体NH3、H2、CH4在空气中的爆炸范围见本汇编防爆部分。
此外,合成塔内中心管里有电加热器,在电炉使用过程中如绝缘不好、漏气等都易使可燃气体着火和爆炸。
还有,当被还原的触媒粉末暴露在空气里时,能和氧发生剧烈的氧化反应,也能发生爆炸,常见的有合成塔拆小盖的爆炸事故。
因此在生产过程中无论是设备或管道里的气体泄漏到空气中、或者是空气渗入设备管路中,都能形成易燃易爆的环境,而触发爆炸,因而都是不能允许的。
从本工段设备发生爆炸事故的频率和危险性来看,合成塔和液氨贮槽事故发生率最高,危害性最大。
因而这两个设备是全工段也是全厂重点防爆设备。
循环机故障引起的爆炸事故也占相当比例,应予以足够重视。
本工段第五个特点是低温有毒。
这是由于本工段是全厂产氨和贮氨的集中地而决定的。
在常温常压下,氨是有刺激性臭味的无色气体,极易溶于水,一升水大约可溶解600升氨。
氨的这一特性可在“跑氨”时,利用水来冲洗吸收,可迅速而大量降低环境的氨的浓度,而使人们可以靠近处理。
气氨是一种有毒气体,它能使人窒息中毒。
液氨是无色液体,极易挥发成气氨,在常压下,一33.4‘C时即变成气体,液氨除具有气氨的毒性外,因其温度低(在零度以下),溅落在皮肤上会造成化学烧伤。
气氨和液氨对人的毒害及车间允许浓度见第十六章防毒部分。
本工段是合成氨产生之源,贮氨之地,既有气氨、也有液氨。
如不注意防护,既能使人中毒窒息,空气中氨含量达到7g/m3时可危及人的生命,又能使人受到低温化学烧伤。
综上所述,本工段具有高温高压、高低压并存、易燃易爆、低温有毒、有催化剂存在等生产特点,也可以说它们是小氮肥厂生产特点的集中反映。
这些特点对本工段的设备管理和生产操作提出了一系列的安全要求。
要做好本工段的安全工作,就要从这些特点和要求出发制定和落实相应的安全措施,以确保安全生产。
二、安全操作要点
(一)正确使用内套和触媒,保护合成塔
合成塔是合成工段的关键设备。
合成塔的设备状况、操作水平关系到合成工段的安全运行,高产、低耗直接影响企业的经济效益。
由于内套是合成塔的重要部件,如果说合成塔是合成系统的心脏,则合成塔内套是心脏的心脏,内套如发生问题,合成系统乃至全厂的生产将无法进行。
由于内套是高压系统内的低压设备,又处于触媒的高温区,是冷热气体交换的场所,设备工况比较复杂,因此较易损坏。
另外触媒如使用不当,就会增加毒物对触媒的毒害,加速触媒的中毒和衰老。
内套和触媒又相互联系相互影响,内套损坏会影响触媒层温度的控制,触媒温度控制不稳定,又会缩短内套使用寿命。
因此,睪正确使用内套和触媒,稳定合成塔操作,保护合成塔以延长其&用寿命。
稳定控制热点温度,严禁超温
触媒层温度的控制是合成操作的中心,要根据合成塔进口气体成分及生产负荷等外界条件影响温度因素的变化,及时调节循环机近路、系统近路、合成塔冷副阀,稳定控制触媒层的热点温度,并做到勤调、细调、预先调。
一般情况下主阀不作为温度调控手段,但在其它手段无法控制时,可辅以主阀调节。
但要注意主阀开启度不能过小,以保证有足够的流量。
热点温度波动范围应控制在±5C以内,并根据不同的触媒型号和触媒使用的不同阶段确定热点温度控制指标。
在触媒的活性温度范围内,前期控制略低一些,中后期可控制略高一些。
要使整个触媒层的温度都维持在触媒活性范围内,要求反应温度达到热点温度后,气体温度随催化床深度而降低,以兼顾反应速度和平衡。
不允许超温操作,以防结晶粘聚烧坏触媒而失去活性。
对于A110-1型触媒,应控制在460〜500€之间,瞬间超温不能超过510℃。
当发现触媒层温度猛升或猛降时,应立即判明原因,采取相应措施。
触媒升、降温应控制升降温速率40〜50℃/h,防止猛升猛降(原始开车另有要求),还应注意缩小触媒同一平面温差(小于15℃)和顶点和底部的温差,以避免由于温度波动频繁和温差过大而加速触媒老化。
稳定控制压力,减少压差,严禁超压
合成操作中既要保证有足够的新鲜气量使合成系统维持在较髙压力下操作,又不能超压,操作力求减少压力波动。
要根据合成塔内反应情况,进口氨、惰性气体含量以及外工段条件、氢氮比的波动等影响压力因素的变化及时用放空阀进行调节,稳定控制系统压力严禁超压运行。
调节压力时应缓慢,不允许猛升猛降。
升降压速率在放空管口径符合设计要求时为每分钟0.4〜0.5MPa,以防形成过大压差而损坏内套和冷交换器内芯,或因超过安全流速将铜液带至合成塔或循环机。
应控制塔进出口压差不能超过内套所能承受的0.BMPa和冷交换器内外管压差<0.8MPa(如设计有特殊规定,则应按设计值)。
卸压时尽量开塔后放空进行,如塔前、塔后同时进行则要求保持塔前压力大于塔后压力,以防气体倒流触媒粉末粘连而烧坏电炉丝。
同时,放空速度不能过快以防产生静电而着火、爆炸。
把好精炼气质量关,防止触媒中毒
触媒中毒分为暂时中毒和永久中毒。
凡是由CO、co2、HzO等含氧化合物引起,经过处理,活性可以得到恢复的触媒中毒称为暂时中毒。
凡是由碳、硫、砷及其化合物引起的中毒,因其与触媒作用生成比氧化物更稳定的表面化合物而使触媒活性不能再得到恢复,称为永久中毒。
精心维护保养触媒,把好合成塔入口的精炼气质量关,减少暂时中毒,杜绝永久中毒。
要严格控制合成塔入塔补充气微量指标C0+C02<25ppm,超过指标时及时减量生产,超过50ppm时切气放空。
精心操作,防止进合成塔气带油、带水、带液氨,杜绝带铜液,发现精炼带铜液立即切气并排放氨分、油分,同时经常注意油分离器的分离效率,定期进行清理。
保护外筒、注意塔壁温度和塔出口温度的控制
由于外筒由16MnR制成,又系高压设备,制造复杂,价格昂贵,本身不能经常修理和更换,为保证安全,并延长其使用寿命,要保护好外筒。
注意控制好塔壳温度和塔出口温度,以避免合成塔主要部件同时承受高压和高温负荷,造成塔壁温度过髙,使钢材强度下降,不能承受高压,酿成破坏事故;同时还会加速氢氮气对塔壳的腐蚀,引起钢材脱碳和渗氮,使其结构疏松,强度降低,轻则缩短使用寿命,重则造成重大爆炸事故。
塔外壳温度一般应控制小于120亡。
塔出口温度过高也会加剧氢氮气对钢材的腐蚀,降低其机械强度。
要严格根据管道材质控制塔出口温度在规定指标范®内。
对优质铬钼钢管温度可控制在200℃以下,(当温度达到230℃以上时,便开始脱碳渗氮,而且速度较快)对普通钢材,温度可控制在150℃以下。
对优质合金钢材,温度要控制在设计规定范围以内。
发现塔壁温度和塔出口温度过高要通过关小塔副阀、加大循环量来进行调节,并查找内套设备的原因,及时进行处理。
具体防止办法见事故分析。
另外,值得提出的是,为防止因为突然停电,合成塔环隙间气体不流动而造成塔壁温度升高,应在停电后,继续监视塔壁温度,间断地适当开启塔后放空,放掉部分气体,以带去热量。
(二)防止跑气和漏气,防止高压气体窜入低压部分
防止高压气体倒入液氨贮槽必须十分重视放氨操作,控制好一、二级氨分离器(冷交下氨分)的液位,确保液面稳定、防止液位过低,高压气窜到贮槽超压发生爆炸。
有条件的厂应采用自动放氨装置放氨以保证氣分液位稳定。
防止氨冷器高压气体进入低压部分
由于氨冷器高压蛇管泄漏不易觉察,要注意控制氮冷器出口气氨总管压力不得超过0.2MPa,如气氨压力超高,说明高压蛇形盘管泄漏,髙压气由此进入低压部分,应立即停车处理,以防高压气进入冰机进口引起爆炸。
应当注意的是氨冷器在检修后(被油污堵塞进行淸洗后)必须把连接方块拆开,逐根吹净积水,以防加氨后把管子胀裂,高压气漏入而爆炸,
防止软水加热器高压气体窜入低压部位
要加强水质处理,对全厂的循环软水进行降氧,控制循环软水中氧含量不大于0.05mg/l,以减少和防止高压管被水中溶解氧腐蚀击穿,发现有泄漏,应及时处理,以防髙压气窜入低压部位引起爆炸。
防止冷交漏气
要注意控制好气体成份、(氢氮比不能过低)循环气量和控制好升降压速度来减少系统阻力,以防止冷交换器的压差增大而发生损坏漏气,使气体不经氨冷器而直接进入合成塔。
如合成系统阻力大时应及时进行系统检查,以降低系统压差。
防止合成塔漏气
要经常检査合成塔顶大盖与外筒螺栓,小盖与电极杆,大盖与小盖等连接处容易发生漏气的地方,要及时卸压进行处理,以避免漏气遇热发生着火和爆炸。
如发现着火,宜用干粉、氮气等绝缘性能好的灭火剂灭火。
(三)严格控制系统内的氧含量
合成系统循环气是易燃易爆气体,又在高温高压下工作,如果氧含量超高,就会发生爆炸,要求严格控制系统内的氧含量。
生产中特别要注意防止压缩机操作工误操作,半水煤气在压缩机岗位通过2〜3或5〜6直通阀走近路到合成工段引起氧含量高,在系统检修结束开车试压之前,一定要先用精炼气或惰性气置换,分析氧含量合格(02<0.2%)才能进行升压(详见开停车置换部分)。
(四)氨冷、氨分的操作
1.氨冷器温度和压力的控制
氨冷器工作状态的好坏不仅影响合成塔的正常操作,也关系着冰机的安全运行,要及时调节氨冷器液位和液氨蒸发压力,控制好氨冷温度,以降低进口氨含量。
氨冷器液位不能控制过高以防液氨带入冰机引起爆炸,送碳化气氨总管压力不能过低,应大于0.03MPa(但应小于0.2MPa),以防碳化吸收岗位的氨水倒入冰机引起爆炸。
另外在氨冷器中应保证气体经氨冷后有液氨分离下来,这样才能保证补充气中水分被除去,从而保护触媒,因此要求水冷与氨冷保持一定水温差,特别是冬季气温低更要注意这一点。
一般温差维持在10〜15℃。
2.氨分液位的控制
必须控制好一、二级氨分离器液位,确保液位稳定,防止过高,液氨带入循环机或合成塔,过低无液面,高压气体冲入贮槽,引起超压爆炸。
(五)贮槽安全保护
贮槽是本工段重点防爆防毒设备,必须注意加强安全保护。
贮槽压力不得超过1.6MPa,以防止超压而发生爆炸。
贮装液氨量最高不得超过贮槽容积的80%,以防止液氨装得过多,当环境温度升高时,液氨膨胀,液体不可压缩,使容器压力升高而爆炸。
计算表明,满嫌液氨温度由2CTC升高到25"C时,压力升高到84个大气压,贮槽必然爆炸。
最低不得低于贮槽容积的
注意保证贮槽和氨用阀门、管道、液位计、安全阀、压力表等受压设备、备件的制造质量,材质要符合要求,做到使用灵活、安全可靠,严禁以次充好,以保证液氨系统的密闭性和安全性。
安全阀、压力表必须定期校验,并有铅封。
贮槽应有符合规定的接地装置和良好的绝热保冷措施,或设有凉棚。
附近应有喷洒吸收和排水等防止液氨大量外泄的防范措施。
(4)加强个人防护,岗位(车间)应备有氧气呼吸器、防毒面具、(防氨)胶皮衣和靴等必要防护器具。
当进入髙浓度氨气场所作业或检修时,要采取身体防护措施。
如发生跑氨事故时,要立即带上防氨面具和氧气呼吸器处理,当身边无防氨面具时,可用湿的毛巾、手帕及衣服堵住嘴和鼻子向迎风方向跑,迅速撤离毒区。
(六)正确使用电加热器
开用电加热器之前应先测量电加热器对地绝缘电阻,要求大于0.2MQ。
先开循环机并运转正常后再启动电炉。
在电炉运行时,若要停循环机,必须先停电炉,后停循环机。
(七)有关检修安全
必须十分重视检修安全,数年来,小氮肥事故统计分析表明,检修是事故的髙发期。
有关检修安全主要参见第十五章“检修部分”,需特别注意的是以下几点。
检修时不能带压紧螺栓。
拧紧法兰垫时一定要卸压以防高压气冲出爆炸。
髙压设备按有关压力容器规定定期进行检测,高压材料、备件不能串规、串级使用,禁止用低压备件、材料代替高压备件、材料。
液氨和冰机系统检修时要注意卸净压力和采取防氨措施。
严格动火制度,本工段为一级防火区,禁止烟火,如需动火,则要办理动火手续,并做好相应的安全措施,如盲板隔离,惰性气置换(或氮气吹扫),水或蒸汽热冼和分析合格等。
合成塔拆小盖时,必须按照规定采取降温、卸压、置换、保正压、打开放空阀等措施,具体详见“事故处理及预
防”部分,以防拆小盖时发生爆炸事故。
(6)设备气密试验应按规定用空气进行,禁止用氧气代替空气对设备管道充压、保压、试压置换或吹扫,不能用精炼气试压。
(八)循环机、冰机的操作
经常检查循环机和冰机传动部件运转和密封情况,如发现敲击等异常响声时,应立即查明原因、及时处理,以避免高压气体冲出循环机发生爆炸。
经常检查曲轴箱的润滑油质量、油位高度及油泵出口油压,应符合工艺指标,保证良好润滑。
经常检査冰机进出口压力和温度,必须控制在工艺指标范围内,防止超温和超压,并随时注意气氨进口结霜,防止液氨带入冰机,防止氨水带入冰机。
(九)巡回检查
根据操作记录表,按时检查及记录。
每十五分钟检查一次系统各点压力和温度。
每半小时检查一次氨冷器液位。
每半小时检查一次循环机、冰机运转情况。
油分离器(氨油分离器)每四小时排油一次。
每班检查一次合成、冰机水冷器冷却水淋洒情况。
每班检查一次系统设备管道泄漏情况。
每天(日班)检查一次合成塔顶盖情况。
每周(日班)氨冷器、液氨贮槽排污一次。
每月检査一次贮槽安全阀起跳情况。
(十)开、停车注意事项
必须十分重视开、停车操作安全,数年来小氮肥事故统计分析表明,开、停车和检修一样也是事故的高发期。
根据生产和检修的不同要求,采用不同的开、停车方式,以保安全。
①开车操作分为正常开车和原始开车。
正常开车又分为系统未经检修处于保压保温状况下的开车和系统检修后的开车。
对于前者不须进行置换,对于后者则须先吹净,再置换,试压查漏其方法和原始开车步骤同。
②停车操作分为短期停车,紧急停车和长期停车。
其中短期停车又分为系统保压保温状况下的停车和系统需检修的停车。
对于前者无需进行置换,对于后者须进行置换等步骤,和长期停车步骤相同。
③原始开车需经开车前准备,单体试车,系统吹净,空气气密试验,装填触媒,吹触媒灰及系统置换,二次气密试验、氨冷器气氨管阀真空试验及系统充氨,升温还原等步骤。
④长期停车需经停止加氨,循环降温系统卸压,合成塔隔离保正压,系统置换等步骤,具体开停车步骤,见化工部小氮肥工艺操作规程。
开停车按方案进行,有关工段要加强联系。
在开、停车过程中,开、停车步骤要正确。
有关的阀门开