乳化液基础知识.docx
《乳化液基础知识.docx》由会员分享,可在线阅读,更多相关《乳化液基础知识.docx(8页珍藏版)》请在冰豆网上搜索。
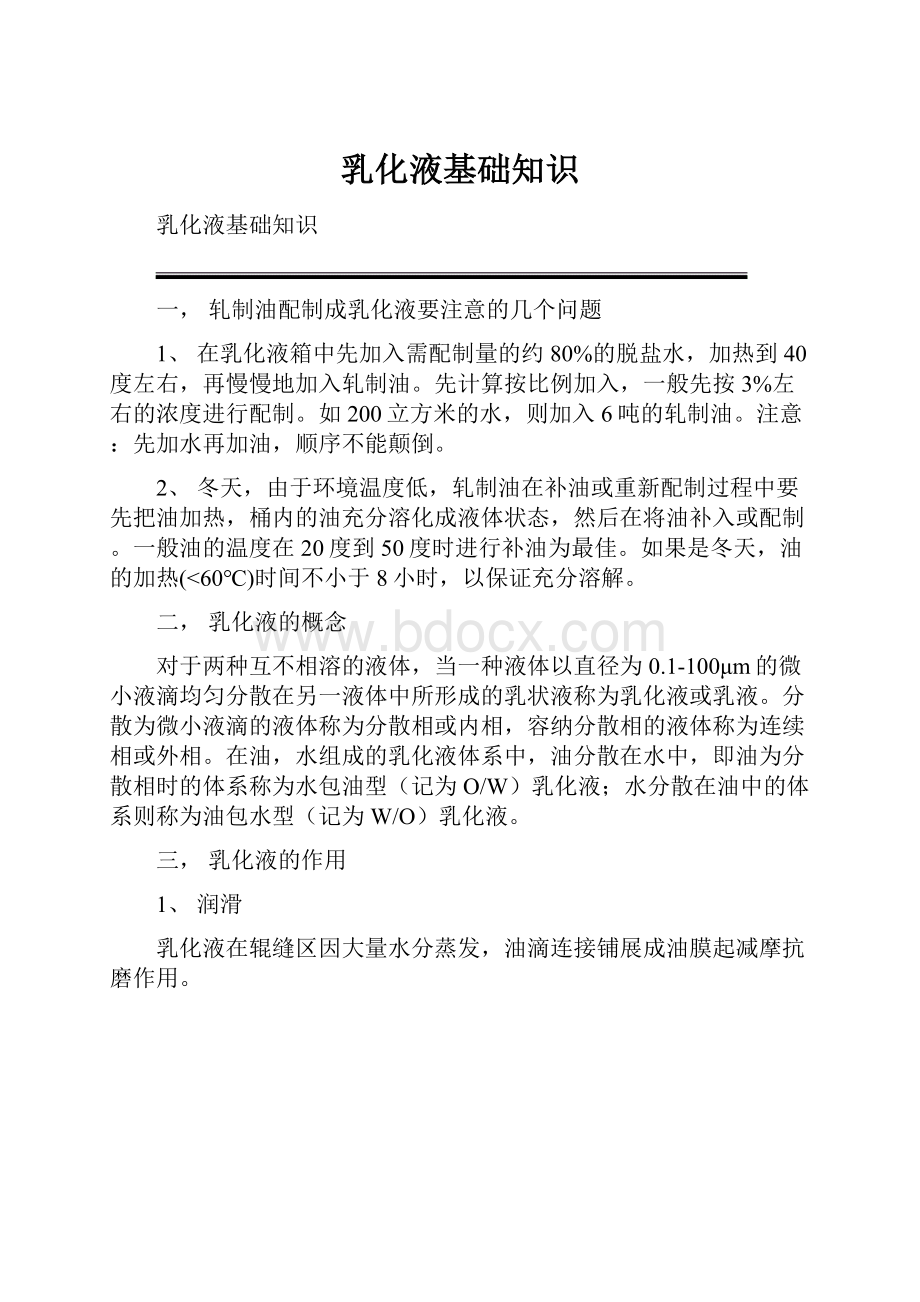
乳化液基础知识
乳化液基础知识
一,轧制油配制成乳化液要注意的几个问题
1、在乳化液箱中先加入需配制量的约80%的脱盐水,加热到40度左右,再慢慢地加入轧制油。
先计算按比例加入,一般先按3%左右的浓度进行配制。
如200立方米的水,则加入6吨的轧制油。
注意:
先加水再加油,顺序不能颠倒。
2、冬天,由于环境温度低,轧制油在补油或重新配制过程中要先把油加热,桶内的油充分溶化成液体状态,然后在将油补入或配制。
一般油的温度在20度到50度时进行补油为最佳。
如果是冬天,油的加热(<60℃)时间不小于8小时,以保证充分溶解。
二,乳化液的概念
对于两种互不相溶的液体,当一种液体以直径为0.1-100μm的微小液滴均匀分散在另一液体中所形成的乳状液称为乳化液或乳液。
分散为微小液滴的液体称为分散相或内相,容纳分散相的液体称为连续相或外相。
在油,水组成的乳化液体系中,油分散在水中,即油为分散相时的体系称为水包油型(记为O/W)乳化液;水分散在油中的体系则称为油包水型(记为W/O)乳化液。
三,乳化液的作用
1、润滑
乳化液在辊缝区因大量水分蒸发,油滴连接铺展成油膜起减摩抗磨作用。
2、冷却
变形和摩擦热一方面通过水分蒸发,另一方面通过乳化液的喷淋带走,从而保证轧件和轧辊的温度不至于过高。
冷却和润滑随浓度的关系如下图所示,浓度增加,冷却效果稍有下降。
冷却
润滑
浓度%
012345678
3、清洗
乳化液具有清洗能力,从而保证轧件,轧机和乳化系统清净。
4、防锈
轧后钢板表面附有乳化液,水分蒸发后均匀分布一层油膜,油中又含有防锈添加剂,从而保证钢板轧后的短期防锈。
四,轧制油的组成
轧制油由矿物油,脂类,抗氧剂,乳化剂,极压剂,防锈剂和其他添加剂组成。
矿物油从石油炼制中来,起部分润滑的作用;脂类包括天然脂和合成酯,主要起润滑的作用;抗氧剂能延长乳化液使用寿命;乳化剂能将油和水拉到一起形成乳化液,乳化剂的种类和添加量决定了体系的稳定程度和颗粒分布;防锈剂在轧后钢板上吸附起防锈作用。
五,轧机和乳化液箱系统环境在进行清洁卫生时要注意方面
1、不能使用任何化学清洗剂对轧机和乳化液箱系统进行清洗。
2、如果使用工业水进行清洗轧机,清洗后收集槽内的水最好排放掉。
六,轧机检修后或较长时间的停机(二天以上),在开机前注意方面
1、安装工作辊前先试喷一下乳化液,检查是否有喷嘴堵塞或部分堵塞,如果发现有喷嘴堵塞或部分堵塞,必须要把喷嘴卸下,疏通后再安装上去。
2、在开机前要测试乳化液浓度,由于停机时磁性过滤器常常还在工作,一般停机时间较长会使浓度有所下降,如果浓度过低则需补充新油到目标浓度。
3、如果在检修过程中有液压油等其它油大量泄漏到乳化液系统,则开机前必须进行撇油。
七,撇杂油时要注意的方面
1、先关掉搅拌(包括机械搅拌和空气搅拌),让杂油充分地浮起来,然后再撇去杂油。
2、如果有可能尽量在轧机停机时撇杂油,这样乳化液的流动性较低,杂油也较容易浮起来。
3、每周测定一次撇出杂油的皂化值,以便了解撇出的油中轧制油含量后采取相应措施。
八,乳化液温度的控制
1、正常生产情况下,乳化液温度控制在52-58℃,过高会使乳化液添加剂析出,使乳化液的稳定性变差,过低会使润滑性能不能有效发挥。
2、停机情况下,乳化液温度控制在45-50℃,过高浪费热能,过低会滋生细菌。
九,乳化液的维护
1.皂化值—皂化值是指皂化1克油品所需氢氧化钾的毫克数。
被皂化的物质主要是油脂和合成酯等脂类化合物。
皂化值在轧制油中具有重要意义,它的高低代表了轧制油润滑性能的好坏,一般来讲,皂化值越高,润滑性能越好,但轧后退火的清净性也随之变差。
乳化液的皂化值会随着杂油的泄漏而随之降低,一般,杂油的含量不能大于在乳化液中油含量的20%,否则会因润滑性能下降而影响轧制。
杂油含量%=100%*(原油皂化值—乳化液实测皂化值)/原油皂化值
2.酸值—酸值是表示油品中有机酸的含量多少的指标。
中和1g油品中的有机酸所需氢氧化钾的毫克数。
乳化液如果发生细菌生长,酸值会提高,如果受杂油等外界其它因素干扰,酸值也会发生变化。
酸值最好控制在:
原油酸值±2mgKOH/g
3.铁含量—乳化液中的铁粉含量,用PPM表示。
一般控制在小于500ppm,过高会影响乳化液的清净性,从而影响钢板表面的清净性,但适量的铁含量对润滑起一定的帮助。
4.PH值—表征乳化液的酸碱度。
一般乳化液的PH值的控制范围为4.5—6.5,过高则可能有碱性物质侵入乳化液系统,如清洗剂、工业水等。
过低则可能酸性的物质侵入乳化液系统,如酸洗钢板表面残留酸过多、乳化液中有大量细菌、ESI过低造成乳化液酸败等。
5.电导率—表征乳化液中各离子含量程度。
电导率一般在500us/cm以下,过高则说明有外界离子的侵入。
如酸洗钢板表面残留酸过多,清洗剂的侵入、脱盐水的质量、有工业水侵入、ESI过低等。
6.ESI—乳化液稳定性指数。
一般在0.4—0.8,过高会影响润滑性,过低会增加油耗,维护也困难,甚至也会影响润滑性。
7.氯含量—乳化液中氯含量主要来自酸洗后钢板表面的夹带,乳化液中氯含量一般要小于50ppm,过高会引起钢板发生点蚀。
十,乳化液电导率和PH值几种变化的分析
1.PH下降,电导率不变
原因:
细菌
有机酸
后果:
气味
防锈
乳化液稳定性降低
解决:
添加杀菌剂
对乳化液充气
提高水质
切换乳化液
2.PH下降,电导率上升
原因:
酸洗线氯离子,硫酸离子,盐酸或硫酸的挟带。
后果:
降低乳化液稳定性
生锈
解决:
加强酸洗线漂洗,更换挤干辊,控制酸洗漂洗槽中的漂洗水电导率
3.PH不变,电导率上升
原因:
由于水的挥发,残留中性盐增加
酸洗线盐份挟带
冷却水泄漏
后果:
降低了乳化液的稳定性
乳化液灰分提高
锈蚀
解决:
补充去离子水或蒸馏水
加强酸洗线漂洗
防止冷却器泄漏
4.PH上升,电导率上升
原因:
酸洗线中和剂挟带
碱性清洗剂污染乳化液
后果:
乳化液稳定性上升(ESI升高),有些时间可能使乳化液不稳定,提高乳化液灰份,锈蚀
解决:
加强酸洗线漂洗
控制酸洗线电导率
避免碱性清洗剂倒入乳化液中
系统的清洗和准备
乳化液系统的清洗
一般情况下,新建轧机过程中的残渣、焊渣等如残留在乳化液系统,对轧机喷嘴的畅通是非常不利的。
所以整个乳化液系统的清洗是非常必要的。
乳化液系统的清洗过程如下:
Ø卸除轧机喷管上的喷嘴,进行清洗,保证喷嘴畅通无异物;
Ø进行机架、收集槽和乳化液箱的清理;
Ø清理完毕后,在乳化液箱中注入足够循环的普通水或配制水;
Ø升温至35~45℃,配置0.5%浓度的乳化液,循环1至2小时,清洗所有管道和附属设备(开启磁性过滤器);
Ø全部排放;
Ø安装轧机喷嘴,并调整好角度;
Ø准备进行乳化液配制;
乳化液的配制
在完成必要的清洗工作后,可以进行乳化液的配制。
配制工作如下:
Ø记录每一步工作及测试结果;
Ø从配制水箱中取样,检查配制水水质,保证水质达到应用要求;
Ø检查轧制油的名称、批号,确保使用所需轧制油;
Ø在系统中注入配制水,其总量约为正常用量的70-80%;
Ø从乳化液系统中取水样检测,确保水质已经达到要求;
Ø循环并加热升温;控制温度为40℃;
Ø加油,开始配制乳化液;目标浓度为3.0%,先加入达到2.5%乳化液浓度所需油量,然后逐步达到目标浓度;
Ø乳化液取样测定浓度,同时将系统温度升至所需温度50℃;
Ø如果所测浓度高于目标浓度,向系统中补水,直至达到或低于设定浓度;
Ø根据测定浓度,配制余下轧制油,达到所需浓度;
Ø取样测试浓度,浓度不合格,重复前述步骤;
Ø乳化液试喷,检查喷嘴及喷射角度;
Ø开始准备轧制,并逐步补水、补油至正常应用液位;
Ø上述部骤可根据实际情况和现场服务工程师的建议作相应调整。