04柴油加氢装置学生版xch.docx
《04柴油加氢装置学生版xch.docx》由会员分享,可在线阅读,更多相关《04柴油加氢装置学生版xch.docx(16页珍藏版)》请在冰豆网上搜索。
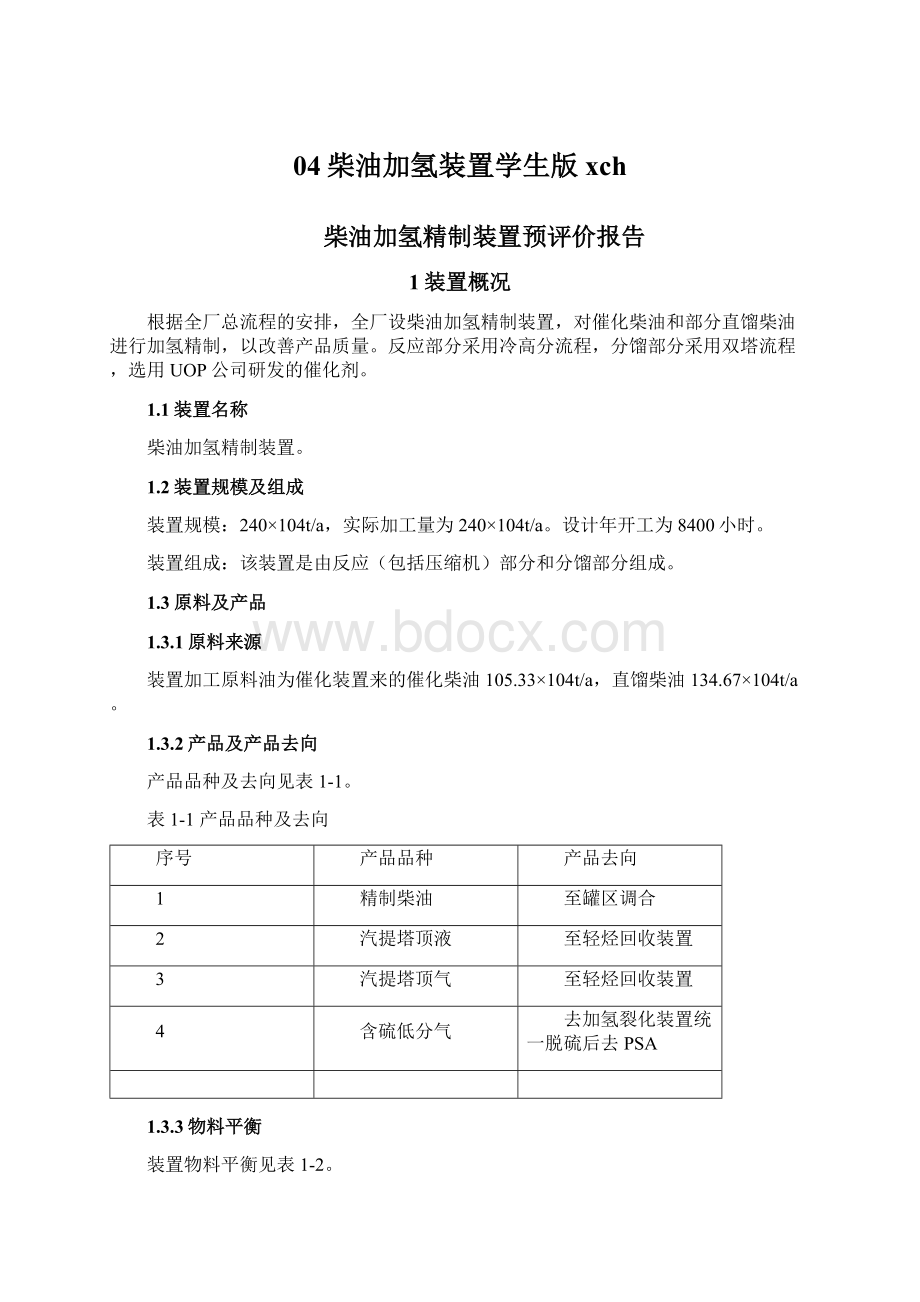
04柴油加氢装置学生版xch
柴油加氢精制装置预评价报告
1装置概况
根据全厂总流程的安排,全厂设柴油加氢精制装置,对催化柴油和部分直馏柴油进行加氢精制,以改善产品质量。
反应部分采用冷高分流程,分馏部分采用双塔流程,选用UOP公司研发的催化剂。
1.1装置名称
柴油加氢精制装置。
1.2装置规模及组成
装置规模:
240×104t/a,实际加工量为240×104t/a。
设计年开工为8400小时。
装置组成:
该装置是由反应(包括压缩机)部分和分馏部分组成。
1.3原料及产品
1.3.1原料来源
装置加工原料油为催化装置来的催化柴油105.33×104t/a,直馏柴油134.67×104t/a。
1.3.2产品及产品去向
产品品种及去向见表1-1。
表1-1产品品种及去向
序号
产品品种
产品去向
1
精制柴油
至罐区调合
2
汽提塔顶液
至轻烃回收装置
3
汽提塔顶气
至轻烃回收装置
4
含硫低分气
去加氢裂化装置统一脱硫后去PSA
1.3.3物料平衡
装置物料平衡见表1-2。
表1-2装置物料平衡
序号
物料名称
数值
备注
w%
kg/h
104t/a
一
原料
1
直馏柴油
56.11
160321
134.67
2
催化柴油
43.89
125393
105.33
3
氢气
0.58
1655
1.39
合计
100.58
287369
241.39
二
产品
1
石脑油
0.50
1429
1.20
2
轻柴油
99.00
282858
237.60
3
气体+H2S
0.98
2794
2.35
4
损失
0.10
288
0.24
合计
100.58
287369
241.39
1.4公用工程消耗
1.4.1给排水量
给排水量见表1-3。
表1-3给排水量
用水地点
给水(t/h)
排水(t/h)
新鲜水
除氧水
除盐水
净化水
循环水
含油
污水
含盐
污水
含硫污水
循环
热水
生活
污水
水冷却器
943
943
机泵冷却
7
1
6
配制药剂
1
1
注水
9.5
9
18.5
1.0MPa蒸汽
12
间断用水
2
2
合计
2
10.5
9
950
1
31.5
949
2
1.4.2电用量
装置电用量见表1-4。
表1-4电用量
序号
电压V
轴功率(kW)
备注
1
6000
2440
2
380
320
3
220
100
合计
2860
1.4.3蒸汽用量
装置蒸汽用量见表1-5。
表1-5蒸汽用量
蒸汽用量,t/h
自产汽,t/h
0.4MPa
1.0MPa
3.5MPa
0.4MPa
1.0MPa
正常
最大
正常
最大
正常
最大
正常
最大
正常
最大
12
22
22
1.4.4燃料用量
装置燃料用量见表1-6。
表1-6燃料用量
燃料油,kg/h
燃料气,kg/h
备注
780
(热值10000kcal/kg)
1.4.5压缩空气用量
装置压缩空气用量见表1-7。
表1-7压缩空气用量
序号
项目
压力
连续Nm3/min
间断Nm3/min
正常
最大
正常
最大
1
净化压缩空气
0.6
2.5
3.0
2
非净化压缩空气
0.6
20
合计
2.5
3.0
20
1.4.6氮气用量
装置氮气用量见表1-8。
表1-8氮气用量
用汽参数
连续,Nm3/min
间断,Nm3/次
压力MPa
温度℃
正常
最大
正常
最大
0.6
40
3.0
40000
1.5平面布置
占地面积:
100×75=7500m2。
界区不设控制室,各装置共用中心控制室。
反应构架上设有电动葫芦,大型泵的上方设置有检修用手动葫芦或检修吊梁,方便检修与维护。
压缩机厂房采用敞开式结构且分两层布置,厂房内设置桥式吊车
装置布置充分考虑了工艺系统要求的设备标高差和泵净吸入头(NPSH)的需要以及过程控制对设备布置的要求。
此外,为防止堵塞、结焦,控制压降、温降等有工艺要求的相关设备尽量靠近布置。
管桥成组合式布置,仪表电缆、电气电缆拟以槽盒的形式布置在管桥最上层,便于检修和维护,管桥下布置泵。
2工艺流程、设备
2.1工艺流程
2.1.1技术方案的选择
(1)工艺技术方案的选择
本可研柴油加氢精制装置的反应部分拟采用冷高分流程,分馏部分采用双塔流程,精制催化剂选用UOP公司研发的Graded/UF-210Stars催化剂。
(2)工艺流程方案的选择
原料油过滤
原料油进装置后,首先经自动反冲洗过滤器,除去大于25微米的颗粒状杂质,以防止反应器因进料中固体颗粒堵塞导致压力过大而造成的非正常停工。
原料油惰性气体保护
装置内原料油缓冲罐采用惰性气体保护,避免原料油与空气接触,以减轻原料油在换热器、加热炉管及反应器中的结焦程度。
分馏部分采用双塔汽提流程。
低温部位采用注水措施,以防止铵盐结晶
加氢过程中生成的H2S、NH3和HCL,在一定温度下会生成NH4CL和NH4HS结晶,沉积在空冷器管束中,堵塞管路,引起系统压力降增大,因此在反应产物进入空冷器前注入脱氧水来溶解铵盐,避免铵盐结晶析出。
反应部分采用冷高分分离流程
采用炉前混氢,提高换热器效率和减缓结焦程度。
设置高分到低分间液力回收透平
由于装置规模较大,高分到低分流量大,压差高,设置高分到低分间液力回收透平用于驱动反应进料泵,可以回收较多的能量(约335kw)。
2.1.2工艺流程
(1)反应部分
自罐区来的原料油先经自动反冲洗过滤器、脱水罐后进入原料油缓冲罐,原料油缓冲罐中的原料经反应进料泵升压后,与来自新氢压缩机和循环氢压缩机的混合氢混合。
混合原料油经混氢原料油(Ⅰ)/反应产物换热器、混氢原料油(Ⅱ)/反应产物换热器换热后进入反应加热炉,加热至适宜温度进入到加氢反应器中,该反应器装有保护剂与精制催化剂,设置三段催化剂床层,床层间设有注急冷氢设施。
自加氢反应器来的反应产物经反应产物/混氢原料油(II)换热器、低分油/反应产物换热器、反应产物/混氢原料油(I)换热器换热,然后依次经反应产物空冷器、反应产物水冷器冷却至40℃,进入高压分离器。
为了防止反应产物中的铵盐在低温部分结晶,通过脱氧水泵将脱氧水注入到反应产物空冷器或反应产物/混氢原料油(I)换热器上游的管道中。
冷却后的反应产物在高压分离器中进行油、气、水三相分离。
高分气经循环氢压缩机入口分液罐分液后进入循环氢压缩机。
循环氢升压后分三路:
两路作为急冷氢进入反应器,一路与来自新氢压缩机的新氢混合,混合氢与原料油混合作为反应进料。
含硫、含氨污水自高压分离器底排出,至酸性水汽提装置统一处理。
高压分离器油相经减压调节阀进入低压分离器,低压分离器富氢气体送至加氢裂化装置统一脱硫后去PSA装置。
低分油经低分油/分馏塔底油换热器和低分油/反应产物换热器换热后进硫化氢汽提塔,含硫、含氨污水自低压分离器底排出,送至酸性水汽提装置统一处理。
新氢经新氢压缩机入口分液罐分液后进入新氢压缩机升压后,再与循环氢压缩机出口的循环氢混合。
反应部分工艺流程图见附图5-1。
(2)分馏部分
从反应部分来的低分油进入硫化氢汽提塔,塔顶油气经冷凝冷却至40℃,进入硫化氢汽提塔顶回流罐进行气、油、水三相分离。
含硫气体至加氢裂化装置统一脱硫。
含硫污水至酸性水汽提装置,油相经硫化氢汽提塔顶回流泵升压后作为塔顶回流,塔底油经分馏塔进料加热炉加热至适宜温度后进分馏塔。
塔顶油气经冷凝冷却至40℃,进入分馏塔顶回流罐进行油、水分离。
含油污水送出装置。
油相经分馏塔顶回流泵升压后一部分作为塔顶回流,一部分作为石脑油出装置。
塔底油经分馏塔底产品泵增压经换热后进入精制柴油空冷器冷却至50℃后出装置。
分馏部分工艺流程图见附图5-2。
(3)催化剂预硫化部分
为了使催化剂具有良好的活性,新鲜的或再生后的催化剂在使用前都必须进行预硫化。
采用湿法硫化,以DMDS为硫化剂。
2.1.3主要操作条件
反应操作条件见表2-1,高、低压分离器及分馏塔操作条件见表2-2。
表2-1反应器主要操作条件
入口氢分压,MPa(G)
6.4*
入口氢油比,Nm3/m3
400*
总体积空速,h-1
1.34
催化剂
Graded/UF-210Stars
平均反应温度,℃(初期/末期)
328/359
注:
*为参考国内同类装置的估计值。
表2-2高、低压分离器及分馏塔操作条件
单位
数值
高压分离器
温度
℃
40
压力
MPa(G)
7.0
低压分离器
温度
℃
40
压力
MPa(G)
1.2
硫化氢
汽提塔
入塔温度
℃
200
塔顶温度
℃
183
塔底温度
℃
179
塔顶压力
MPa(G)
0.8
分馏塔
入塔温度
℃
250
塔顶温度
℃
179
塔底温度
℃
231
塔顶压力
MPa(G)
0.25
2.2工艺设备
2.2.1重要设备选择
(1)塔
装置共设有两个塔,硫化氢汽提塔和分馏塔,其中硫化氢汽提塔塔径为Φ2200/Φ2600×21000,塔内设20层塔板,设备材质选用20R+0Cr13Al,塔内件材质为0Cr13;分馏塔塔径为Φ2600/Φ3200×28000,塔内设32层塔板,设备材质选用20R,塔内件材质为0Cr13。
(2)反应器
本装置反应部分采用单系列,设有加氢精制反应器一台,反应器内设三个床层,采用热壁板焊结构。
根据Nelson曲线,在目前的操作条件下,选用2¼Cr-1Mo钢可满足抗氢腐蚀要求,为防止高温H2S+H2腐蚀,反应器内壁堆焊309L+347L。
反应器内部设有入口扩散器、顶部分配盘、冷氢箱、再分配盘和出口收集器,内部构件材质全部采用0Cr18Ni10Ti。
(3)反应进料加热炉
反应进料加热炉管内介质为含硫原料油和富氢混合气的混合物,柴油加氢单元操作温度为388℃,操作压力为8.1MPa。
在此条件下,TP321H可满足抗氢腐蚀的要求。
同时TP321H具有一定的抗晶间腐蚀能力。
解决了由于原料中硫腐蚀及其腐蚀产物在装置开停工期间对奥氏体不锈钢的晶间腐蚀,该台炉炉管采用TP321H。
采用单排双面辐射横管立式炉采用Φ219×14炉管。
反应进料加热炉采用的是单排双面辐射,辐射排管形式选用2排、每排1管程辐射炉管表面设有管壁热电偶,以检测炉管壁温的变化。
对流管采用翅片管以强化传热,提高对流传热系数。
为提高加热炉效率,在对流顶设置了空气预热器
燃烧器为专烧气型燃烧器,辐射衬里为耐火纤维结构,对流衬里为轻质浇注料结构。
反应进料加热炉设计热效率为88%。
(4)分馏塔进料加热炉
分馏塔进料加热