铜冶炼厂的危险因素辨识与控制.docx
《铜冶炼厂的危险因素辨识与控制.docx》由会员分享,可在线阅读,更多相关《铜冶炼厂的危险因素辨识与控制.docx(51页珍藏版)》请在冰豆网上搜索。
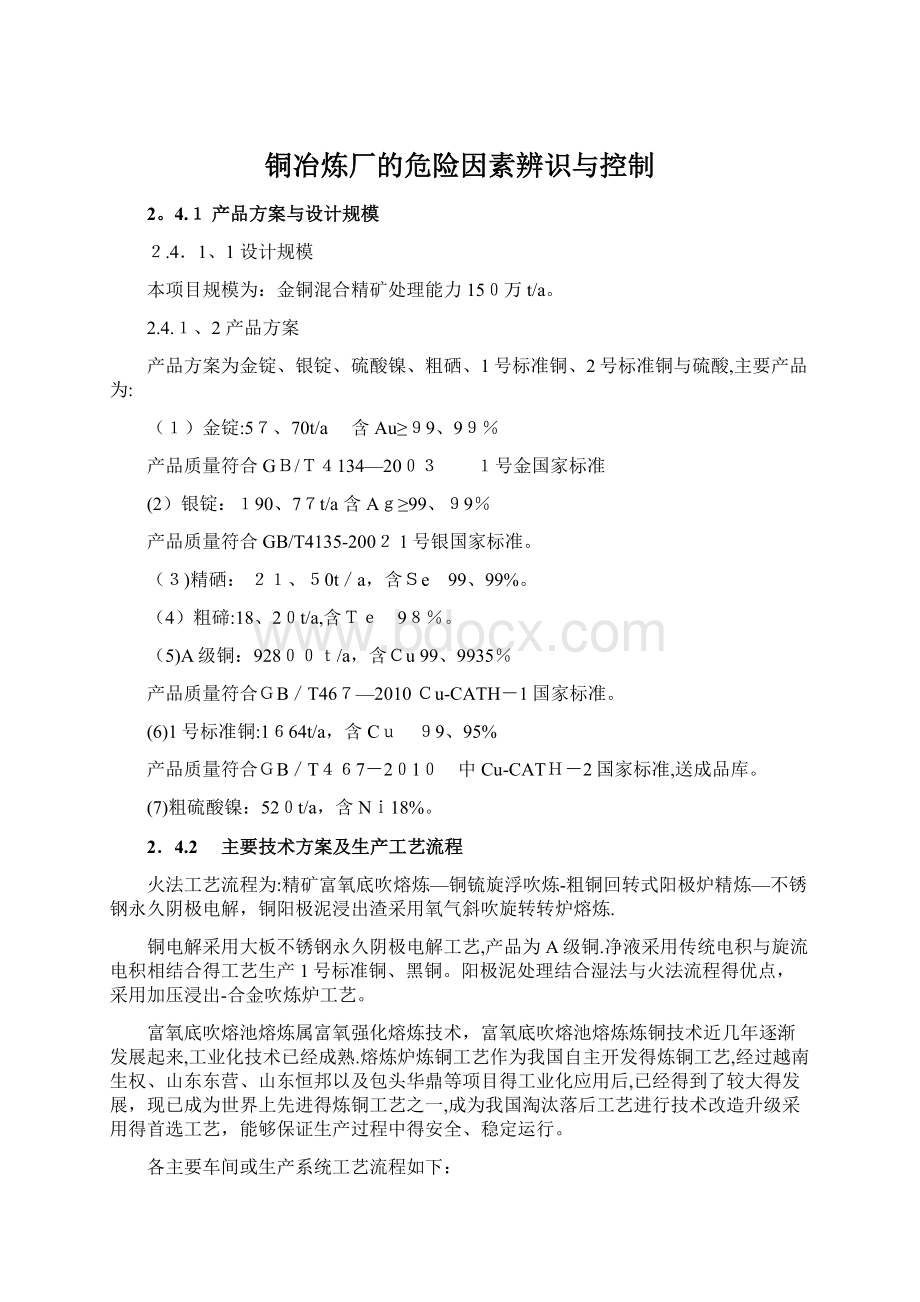
铜冶炼厂的危险因素辨识与控制
2。
4.1产品方案与设计规模
2.4.1、1设计规模
本项目规模为:
金铜混合精矿处理能力150万t/a。
2.4.1、2产品方案
产品方案为金锭、银锭、硫酸镍、粗硒、1号标准铜、2号标准铜与硫酸,主要产品为:
(1)金锭:
57、70t/a 含Au≥99、99%
产品质量符合GB/T4134—2003 1号金国家标准
(2)银锭:
190、77t/a含Ag≥99、99%
产品质量符合GB/T4135-20021号银国家标准。
(3)精硒:
21、50t/a,含Se 99、99%。
(4)粗碲:
18、20t/a,含Te 98%。
(5)A级铜:
92800t/a,含Cu99、9935%
产品质量符合GB/T467—2010Cu-CATH-1国家标准。
(6)1号标准铜:
1664t/a,含Cu 99、95%
产品质量符合GB/T467-2010 中Cu-CATH-2国家标准,送成品库。
(7)粗硫酸镍:
520t/a,含Ni18%。
2.4.2 主要技术方案及生产工艺流程
火法工艺流程为:
精矿富氧底吹熔炼—铜锍旋浮吹炼-粗铜回转式阳极炉精炼—不锈钢永久阴极电解,铜阳极泥浸出渣采用氧气斜吹旋转转炉熔炼.
铜电解采用大板不锈钢永久阴极电解工艺,产品为A级铜.净液采用传统电积与旋流电积相结合得工艺生产1号标准铜、黑铜。
阳极泥处理结合湿法与火法流程得优点,采用加压浸出-合金吹炼炉工艺。
富氧底吹熔池熔炼属富氧强化熔炼技术,富氧底吹熔池熔炼炼铜技术近几年逐渐发展起来,工业化技术已经成熟.熔炼炉炼铜工艺作为我国自主开发得炼铜工艺,经过越南生权、山东东营、山东恒邦以及包头华鼎等项目得工业化应用后,已经得到了较大得发展,现已成为世界上先进得炼铜工艺之一,成为我国淘汰落后工艺进行技术改造升级采用得首选工艺,能够保证生产过程中得安全、稳定运行。
各主要车间或生产系统工艺流程如下:
2.4。
2、1火法冶炼工艺流程
(1)原料卸矿、储存及配料
火车运输与汽车运输得袋装复杂金精矿与铜精矿在卸矿站采用吊车卸车并拆袋,火车运输得散装精矿也在卸矿站采用卸料设备卸料。
卸矿站卸下得复杂金精矿与铜精矿经胶带输送机倒运到精矿仓及配料厂房储存.
当地得复杂金精矿与铜精矿及脱砷金焙砂、渣精矿、精炼渣等物料用汽车运输到精矿仓及配料厂房储存。
精矿仓及配料厂房中复杂金精矿与铜精矿及熔剂、渣精矿得储存时间均为30天,吹炼渣等中间物料得储存时间为7天。
精矿仓及配料厂房中得各种物料分别通过抓斗桥式起重机、圆盘给料机与定量给料机倒运到熔炼上料皮带;返回得熔炼烟尘与吹炼烟尘经计量后倒运到熔炼上料皮带。
配料后得混合炉料经熔炼上料皮带运至熔炼厂房。
(2)熔炼
配料后得混合炉料经熔炼上料皮带卸到熔炼炉顶中间料仓中,再经定量给料机与移动式胶带加料机连续地从炉顶加入氧气底吹熔炼炉内。
冶炼需要得氧气从熔炼炉底部得氧枪鼓入,使熔池形成剧烈搅拌,炉料在熔池中迅速完成加热、脱水、熔化、氧化、造铜锍与造渣等熔炼过程,反应产物液体铜锍与炉渣因密度得不同而在熔池内分层,铜锍经粒化、干燥与磨粉后气力输送至吹炼炉炉顶料仓。
炉渣经炉渣排放口排入渣包、通过渣包车送至渣缓冷场。
熔炼渣经冷却后送炉渣选矿车间,选出得渣精矿运至精矿仓及配料厂房返回熔炼配料,渣尾矿外售或堆存。
熔炼炉产出得烟气经余热锅炉回收余热、电收尘净化后送去制酸。
熔炼余热锅炉与电收尘收集得含铜较高得烟尘通过气体输送至精矿仓及配料厂房得烟灰接收仓,含铅、锌等杂质高得白烟尘外售.
氧气底吹熔炼炉需要得压缩空气由设在空压站得高压离心压缩机提供,氧气来自于制氧站,氧枪入口处压缩空气与氧气压力0、6MPa~0、7 MPa。
当底吹炉氧枪口需要转出熔体面时,在氧枪转出熔体页面后,炉内不再需要氧气与空气,这时将供氧气系统与空气系统中得放气阀打开,氧气与压缩空气排入大气,同时将供氧气与压缩空气管道上得调节阀关闭.
氧气底吹熔炼炉连续加料,年工作330d,平均有效工作时间21、6h/d。
(3)铜锍磨碎
由于旋浮吹炼炉铜锍喷嘴对入炉物料粒度与水分含量要求较高,对铜锍得粒度要求—325目占80%以上,含水〈0、3%,故铜锍需经粒化、磨粉及干燥后方可入炉。
熔炼产出得铜锍首先经粒化装置粒化,然后经胶带输送机倒运到铜锍仓储存。
在铜锍仓内,铜锍经计量与配料后送立式磨制粉与干燥,粉料通过布袋收尘器收集,然后用埋刮板输送机送往吹炼炉顶料仓。
磨碎过程中得热风由热风炉供给,热风炉燃料为天然气,载气经布袋除尘后直接排空。
(4)旋浮吹炼
吹炼炉处理得铜锍粉、生石灰粉、石英砂与烟灰按照设定得加料速率,各自通过独立得计量系统、密闭埋刮板输送机加入到反应塔顶得铜锍喷嘴中。
富氧空气在喷嘴中与混合物料混合,并以高速喷入吹炼炉高温反应塔内,铜锍在氧得作用下,发生一系列化学反应,完成造渣与造铜过程,生成得粗铜与炉渣在沉淀池中由于比重得差异澄清分离。
粗铜经排放口、流槽直接进回转式阳极炉火法精炼,吹炼炉渣经粒化后进熔炼配料系统返熔炼炉处理。
吹炼烟气通过余热锅炉回收余热、电收尘净化后送制酸.吹炼烟气在余热锅炉与电收尘收集得烟尘,含铜较高得烟尘用气体输送至原料仓及配料厂房得烟灰接收仓或吹炼炉顶料仓,含铅、锌等杂质高得白烟尘外售。
吹炼炉年工作330d,平均有效工作时间22、8h/d.
(5)阳极精炼
阳极精炼炉选用2台回转式阳极炉。
阳极精炼得目得就是进一步除掉粗铜中得有害杂质,以满足电解精炼对阳极板化学成分得要求。
粗铜得精炼在回转阳极炉中进行,分加料升温、氧化、还原、浇铸等几个周期.
氧化期就是通过设置在阳极炉上得氧化还原口往铜液中鼓入压缩空气,使铜液中得铁、硫、砷、锑、铋等杂质氧化进入精炼渣中被除去。
由于铜液中得杂质较少,为了使铜液中得杂质较彻底得除去,需要通入压缩空气,使铜液中得部分铜氧化,接近饱与溶解度得氧化亚铜再与铜液中得杂质反应,才能使杂质氧化造渣除去。
氧化期结束后扒出浮在铜液上部表面得精炼渣。
接着进入还原期,还原期就是通过氧化还原口鼓入还原剂将氧化期铜液中产生得氧化亚铜还原成铜.本项目采用天然气作为还原剂,采用天然气作还原剂环保比较好,利用率比较高,产出得阳极板质量好。
近年来,透气砖技术与稀氧燃烧技术在铜火法精炼得到成功应用。
透气砖技术缩短了阳极炉得作业周期,提高了阳极炉得产能,改善了铜阳极板得质量;稀氧燃烧技术提高了燃料燃烧效率,降低了燃料消耗,减少了烟气量并降低了烟气温度。
这两项新技术得使用为提高生产效率、降低成本、改善工作环境与提高电铜质量创造了有利条件。
因此,本方案在回转式阳极炉使用这两项技术.
2台阳极精炼炉每天共生产2炉次,年工作330d。
(6)残极处理
由于旋浮吹炼炉不能处理固体含铜炉料,故电解返回得残极、废阳极、废浇铸模等含铜高得物料需设专门得残极处理系统。
本项目选择用竖炉来处理。
竖炉以天然气为燃料,残极及废阳极在竖炉炉膛中熔化,经溜槽流入回转式保温炉内保温,然后用双圆盘定量浇铸成合格得阳极板后送电解精炼。
(7)阳极浇铸
精炼后得阳极铜需定量浇铸成合格得铜阳极板,再送电解精炼。
本项目得阳极板浇铸引进一套带称重装置得双圆盘双包定量浇铸机.
残极处理产生得阳极铜也用精炼配套得双圆盘双包定量浇铸机,利用阳极炉浇铸得间隙浇铸成阳极板。
(8)阳极泥处理
铜阳极泥先用加压氧浸出脱除阳极泥中大部分铜、镍等杂质,浸出渣经压滤、干燥后,在氧气斜吹旋转转炉中熔炼与精炼,脱除硒、铁、锑、砷、铅、铋、镍、硒、碲、铜等杂质,产出含金银96%以上得金银合金,浇铸成一定规格得金银阳极板送银电解进一步分离金银。
阳极泥处理产生得熔炼渣与精炼渣返回底吹熔炼炉处理,吹炼渣与文丘里尘返回氧气斜吹旋转转炉处理。
2.4.2、2铜电解工艺流程
(1)铜电解
火法精炼产出得铜阳极板由叉车送至铜电解车间,首先在阳极整形机组上进行整形、矫耳、铣耳,然后按极距100mm排板后用电解专用吊车吊入电解槽内进行电解。
在电流密度280~320A/m2、电解液成分Cu2+:
45~50g/l、H2SO4 180~200g/l及电解液温度为60~65℃得条件下进行电解作业,作业周期为:
阳极周期21d,阴极周期7d。
出槽时阴极经专用吊车吊至阴极剥片机组,经洗涤、剥离、堆垛、称量打包后用叉车运至成品库。
剥片后得不锈钢阴极片经排板后由吊车重新吊回电解槽.残极用吊车运至残极洗涤机组处理,经洗涤堆垛后,称量打包,再用叉车送回火法精炼车间。
电解液由循环槽经循环泵扬至板式换热器加热至~65℃后进入高位槽。
电解液由高位槽经分液包自流至各个电解槽。
电解槽供液采用下进上出,由槽两端溢流嘴溢出,电解液汇总后返回循环槽。
残阳极出槽时,上清液流入上清液贮槽,全部经净化过滤机过滤后返回循环系统;排出得阳极泥浆经管道流至阳极泥地槽(带搅拌),泵送至阳极泥中间槽,阳极泥再经泵送阳极泥处理车间进行过滤,过滤后液返回电解车间循环系统,滤渣即为阳极泥,作为阳极泥处理车间(加压浸出部分)得原料.
为保证电解液得洁净度,车间配置了专用得电解液精密过滤器,循环系统每天抽取电解液循环量得30%经精密过滤器过滤后,返回循环系统。
根据电解液中铜及杂质得浓度,每天抽取部分电解液送净液车间处理,保证电解系统电解液中铜及杂质浓度不超过极限值。
铜电解厂房采用单系列循环系统与两套硅整流系统,两套硅整流能够保证电解生产过程中供电得持续性。
当一台硅整流需要检修时用另一台硅整流带动所有电解槽,避免电解槽完全断电后电解槽中阴极铜得返溶,只就是这时得电解槽内电流密度需要调低。
(2)铜电解液净化
铜电解液净化主要分传统法标准电积脱铜、旋流电积脱铜除杂、生产硫酸镍三个工序。
标准电积脱铜槽配置在电解厂房内,电解液在电积槽内进行一段电积脱铜.一段脱铜槽使用不锈钢阴极与不溶阳极,脱铜过程中严格控制铜浓度从45g/L降至38g/L生产1号标准铜。
一段脱铜后液泵送至净液厂房旋流电积工段。
旋流电积共分四段,采用钛涂层作为阳极,不锈钢作为阴极。
一二段旋流电积分别控制铜浓度从38g/L到16g/L与从16g/L到6g/L,生产1号标准铜。
其中一段旋流电积电流密度700~800A/m2,二段旋流电积电流密度控制在400~500A/m2。
二段旋流电积后液送至三段旋流电积,三段旋流电积控制铜浓度从6g/L到2g/L,电流密度250~350A/m2,生产含铜99%得黑铜板。
三段旋流电积后液送至四段旋流电积,四段旋流电积控制铜浓度从2g/L到〈0.45g/L,电流密度700~850A/m2,生产含铜55%得黑铜粉,同时,溶液中得As、Sb、Bi约有85%进入黑铜粉从溶液中脱除。
四段旋流电积后液大部分返回电解车间,少部分泵送硫酸镍工序。
送硫酸镍工序得溶液经搪瓷釜浓缩、水冷结晶、冷冻结晶后生产粗硫酸镍.采用制冷得方法将溶液得温度降低至零下-20℃左右进行冷冻结晶,这样可以提高硫酸镍得结晶效率。
硫酸镍结晶后液经离心机固液分离后得到粗硫酸镍产品,结晶母液返回铜电解车间。
2.4.2、3阳极泥预处理及金银精炼
阳极泥预处理采用加压浸出、合金吹炼炉工艺,金银精炼部分采用银电解生产银锭、氯化法生产金锭.
铜电解车间阳极泥矿浆泵送阳极泥车间,首先经浓密过滤后清液返回电解车间,滤渣即阳极泥。
阳极泥经浆化配料后首先经预浸,预浸槽内通蒸汽将矿浆加热至~80℃,阳极泥中部分铜被浸出,反应后得矿浆在槽内自然澄清,上清液打入压滤机压滤,滤液返回电解车间,滤渣返回预浸槽.预浸槽底部矿浆重新加入硫酸、渣洗液、蒸汽调浆,升温至95℃后得矿浆经泵送至立式加压釜中。
然后向釜内通蒸汽升温、升压,达到设定温度(T=120~140℃)停止蒸汽进入后通入纯度≥93%得氧气升压至1、0MPa,同时向加压釜夹套通蒸汽,通过自动调节进釜氧量与夹套蒸汽量进行氧压浸出.维持浸出温度:
160~170℃,工作压力:
1、0MPa,到达浸出时间后停蒸汽、氧气,浸出终止.浸出矿浆利用加压釜内自