邢钢TRT自动化控制功能规格书.docx
《邢钢TRT自动化控制功能规格书.docx》由会员分享,可在线阅读,更多相关《邢钢TRT自动化控制功能规格书.docx(45页珍藏版)》请在冰豆网上搜索。
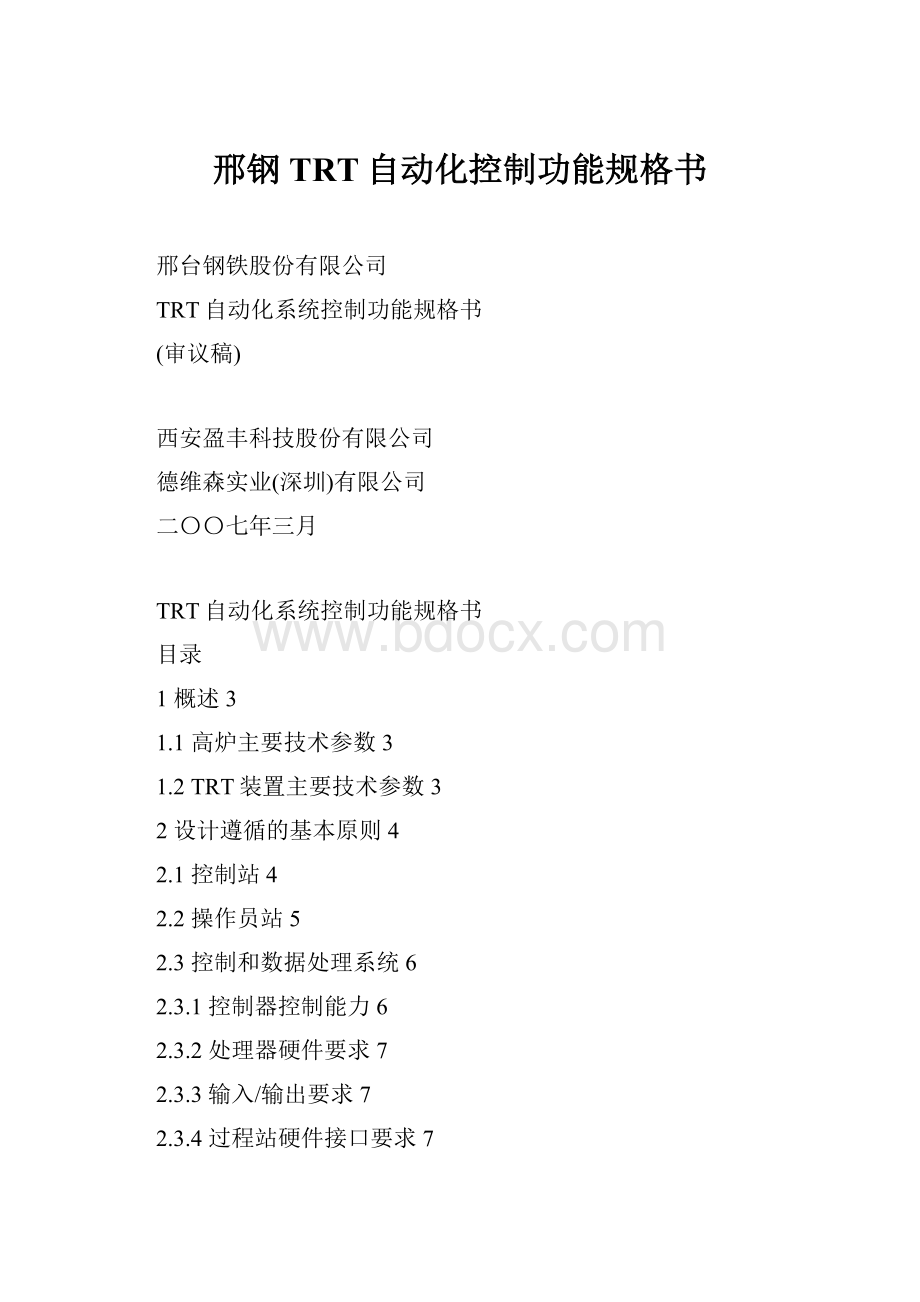
邢钢TRT自动化控制功能规格书
邢台钢铁股份有限公司
TRT自动化系统控制功能规格书
(审议稿)
西安盈丰科技股份有限公司
德维森实业(深圳)有限公司
二〇〇七年三月
TRT自动化系统控制功能规格书
目录
1概述3
1.1高炉主要技术参数3
1.2TRT装置主要技术参数3
2设计遵循的基本原则4
2.1控制站4
2.2操作员站5
2.3控制和数据处理系统6
2.3.1控制器控制能力6
2.3.2处理器硬件要求7
2.3.3输入/输出要求7
2.3.4过程站硬件接口要求7
2.3.5控制室机柜7
2.4系统主要技术要求7
2.4.1平均无故障时间及平均故障维修时间7
2.4.2自控系统的自诊断及容错8
2.4.3系统可靠性裕量8
2.4.4电源系统8
2.4.5电子机柜和接线9
3工艺流程及系统硬件构成9
3.1工艺流程简介9
3.2控制系统构成及选型10
3.2.1ControlLog系统控制平台11
3.2.2控制系统选型15
3.3现场仪表构成及选型16
3.3.1TRT现场仪表构成16
3.3.2现场仪表选型18
4TRT控制要求与控制系统功能实现20
4.1反馈控制系统20
4.1.1转速调节系统20
4.1.2功率调节系统21
4.1.3高炉顶压调节系统22
4.1.4超驰控制系统22
4.1.5氮气密封压差调节系统23
4.2顺序逻辑控制系统23
4.2.1启动(停机)联锁控制23
4.2.2重故障自动紧急停机联锁控制24
4.2.3大型阀门开关指令系统和电气联锁控制24
5TRT过程监控系统的实现——操作员站24
5.1设计要求的主要画面25
5.1.1主要流程图画面25
5.1.2机组启、停和运行过程监视画面25
2.5监控系统主要功能阐述29
5.2.1启动前的准备工作:
29
5.2.2启动操作29
5.2.3停机操作:
29
6结束语30
1概述
现代高炉炉顶压力高达0.15-0.25MPa,炉顶煤气中存有大量势能。
高炉煤气余压能量回收透平发电装置(Blast-FurnaceTopPressureRecoveryTurbineUnit),简称TRT,就是利用高炉炉顶的余压余热,将高炉煤气导入透平膨胀机作功,驱动发电机发电的一种能量回收装置。
邢钢在建的高炉TRT发电装置,其装机容量为5000KW,自动控制系统采用基于PC的过程控制系统——PPC,用以完成机组的反馈控制、顺序/逻辑控制和过程监视等功能。
1.1高炉主要技术参数
项目
单位
参考值
备注
1
高炉容量
M3
450
2
年产炼钢生铁
X106t
3
综合利用系数
t/M3d
4
热风温度
℃
5
炉顶压力
KPa
135
6
平均煤气发生量
X104M3/h
132300Nm3/h
MAX144500Nm3/h
7
除尘器出口煤气温度
℃
180-210℃
1.2TRT装置主要技术参数
项目
单位
参考值
备注
1
炉顶压力设定值
KPa
2
透平入口煤气容积流量
Nm3/h
3
透平入口煤气压力
MPa
4
透平入口煤气温度
℃
5
透平入口煤气相对湿度
%
6
透平出口煤气压力
MPa
7
透平入口煤气含尘量
Mg/m3
8
透平输出功率
kW
9
转数
rpm
10
前端轴瓦温度
11
后端轴瓦温度
12
13
14
发电机额定功率
kW
15
发电机额定电压
kV
16
发电机额定转速
r/min
17
发电机功率因数
18
前端轴承温度
19
后端轴承温度
20
21
22
循环水进水压力
MPa
23
循环水进水温度
℃
24
循环水回水压力
MPa
25
循环水回水温度
℃
26
氮气温度
℃
27
氮气压力
MPa
28
氮气流量
L/min
29
润滑油油站油箱容积
L
30
润滑油油站供流量
L/min
31
润滑油冷却器出口油温
℃
32
润滑油供油压力
MPa
33
动力油站油箱容积
L
34
动力油油泵输出油压力
MPa
35
动力油油泵流量
L/min
36
2设计遵循的基本原则
2.1控制站
1)自控系统是由以DCS/PLC为基础的,分布式的多台系统组件所组成,这些系统组件分布在具有开放式结构的通讯网络上,包括:
操作员站、控制和数据采集系统、外设及有关的硬件和软件。
2)自控系统应在严格的工业环境下长期、稳定地运行。
系统组件的设计应符合真正的工业等级,满足国内、国际的安全标准。
并且易配置、易接线、易维护、隔离性好,结构坚固,抗腐蚀,适应较宽的温度变化范围。
系统应具备良好的电磁兼容性,支持I/O模块在系统运行过程中进行带电热插拔、交换。
能够承受工业环境的严格要求。
3)自控系统是经过现场实验的,并且是出厂前最新的硬件和软件版本。
4)通讯系统是可靠的,即单台硬件设备出现故障(包括通讯系统硬件故障)都不会影响其它系统组件之间的通讯。
通讯波特率≥1Mbps,通讯距离≥1KM,网络要求使用可直埋的电缆,在出现故障时,在线增加或删除任意一个节点,都不会影响到其他设备的运行和通讯。
5)系统中的任何组件通电或掉电都不会影响其他组件的运行。
6)系统允许在线修改软件,也就是除被修改的组件外,不会影响其它系统组件,数据点的修改仅仅影响被修改的回路,回路的输出将保持在修改前最后时刻的数值。
7)联锁系统故障检出元件动作时,在操作员站的显示屏上应进行声光报警,同时报警打印机立即打印出来,并存储在历史模件中,报警的确认和消声由键盘和按钮来实现,联锁系统通常采用手动紧急切断按钮和联锁复位按钮。
对某些联锁的输入应设旁路开关。
2.2操作员站
操作员站包括用于操作员远程操作和工程师站工程维护的人机接口(HMI)和高性能工业级计算机。
操作员站是操作员了解各装置全部信息的接口单元,操作员可在正常或异常情况下对各装置进行控制和监视。
⏹操作员站的功能
1)显示全部的过程变量及有关参数
2)操作所有控制回路的参数,如改变设定点、工作方式、回路输出、调整PID参数等
3)报警显示
4)过程流程图显示
5)趋势显示(实时的和历史的)
6)报告和报表
7)系统诊断报告
8)操作受权限制
⏹操作员站支持功能
操作员站应能支持通用的编程软件,以帮助用户维护和修改数据库,编制应用程序。
支持功能包括在线和离线的数据库定义(即组态、下载等)、备份文件程序管理等。
9)操作员站的实际处理能力不能超过满负荷的30%。
10)每台操作员站具有独立的CPU,操作员站之间应具有内部切换的能力。
11)操作员站的画面刷新时间≤1s。
⏹打印机
打印机应能自动、连续地打印报表、报警、系统维护记录等,也能按命令要求打印报表、屏幕画面和组态记录等。
2.3控制和数据处理系统
控制和数据处理系统包括完成控制功能和I/O监视功能的全部硬件和软件,系统通常是由控制处理器、I/O模件所组成,他们都安装在标准的机柜内,控制处理器执行控制功能,I/O接口模块处理现场输入/输出信号。
供货商应按各种组件的10%提供备用量,同时在机柜中提供20%的备用空间以备扩展。
2.3.1控制器控制能力
12)控制和数据处理系统接受过程变量的输入信号,然后按照组态数据的要求,对输入信号进行处理,存放到相应的数据库中显示或计算,传送输出信号至最终控制元件。
13)在I/O信号处理方面,系统对模拟量提供线性化、补偿、累积、开方和报警功能;系统对开关量提供报警和状态变化的检测。
14)在控制方面,系统能够完成调节控制、联锁逻辑、手动操作、由标准算法或用户程序组合而成的自动顺序。
15)调节控制功能至少包括各种PID算法(反馈、前馈、开关、比率、超前/滞后等)、标准计算(加、减、乘、除、复合运算等)、基本的控制功能(开关、限幅、高/低选择等)、自适应控制功能。
16)联锁控制功能包括用于开关控制的梯形逻辑。
17)系统必须提供控制回路的自整定调节软件。
18)现场控制站通信能力:
现场控制站能够插入较多的通信卡,至少能方便支持ControlNet、ProfiBUS、ModBUS等最常用的标准通信方式。
2.3.2处理器硬件要求
1)CPU为高性能32位RISC中央处理器,时钟频率不小于50MHz。
2)控制器整体应具有抗化工厂经常出现的电磁干扰和抗振的能力。
3)控制器可提供Ethernet通讯或通过安装在机架上的通讯接口卡提供。
2.3.3输入/输出要求
1)控制和数据处理系统可以支持来自现场设备的各种输入和输出信号。
2)所有信号在进出自控系统时都必须采取隔离措施,以防信号过载、瞬变和浪涌冲击。
3)模拟量的扫描周期≤1s,数字量的扫描周期≤10ms。
4)输入/输出数据的分辨率不低于12位。
5)驱动接口应能保证驱动600m范围以内的二线制24VDC变送器。
2.3.4过程站硬件接口要求
1)I/O的隔离要能做到回路级间电气隔离;
2)I/O信号分辨,应在有关资料中说明;
3)输入接口应能保证在使用安全栅的情况下驱动600米范围内的EJA二线制VDC变送器。
2.3.5控制室机柜
要求供方提供的机柜为前后开门,接线端子采用优质进口产品,机柜中端子排将有不少于10%的备用量。
220VAC端子应与信号隔离,机内配线在小汇线槽内敷设。
经过UPS后机柜内的系统所需电源配电工作由供方完成。
为了保持机柜内温度低于各元件允许的最高温度,要提供强制的通风。
供方提供端子柜的接地方式及要求。
2.4系统主要技术要求
2.4.1平均无故障时间及平均故障维修时间
⏹平均无故障时间(MTBF)
供方应给出其系统的MTBF,并能解释其计算方式。
⏹平均故障维修时间(MTTR)
供方应给出其系统的MTTR,并给出其计算方法,以及列举两个以上的控制回路所使用部件的MTTR。
⏹模块化要求
供方应保证自控系统具备较高程度的模块化水平。
2.4.2自控系统的自诊断及容错
自控系统应具有完整的自诊断系统,应为软件级及硬件级的自诊断报警,并且定时自动或人工启动诊断系统,并在操作员站CRT上显示自诊断状态和结果。
自诊断系统包括全面的离线和在线诊断软件,诊断程序能对系统设备故障的检查和对外部设备运行状态的检查。
自控系统应具有一定程度的容错能力,即当某些模块发生故障后,不影响整个系统的有效工作。
2.4.3系统可靠性裕量
系统应按下列原则考虑备用容量:
⏹CPU负荷率控制器≤60%
操作员站≤40%
⏹存储器占有容量内存≤50%
⏹每个机柜内的各种类型I/O点裕量>15%
⏹每个机柜内I/O插件槽裕量>15%-
⏹电源负荷裕量>40%
⏹通讯总线负荷率ETHNET<20%
⏹操作员站允许的最大标签量至少应为系统过程I/O点数的150~200%
⏹系统可用率99.9%(试验时间-累计故障停用时间)/试验时间X100%
2.4.4电源系统
⏹双回路供电
系统支持两路彼此独立220V交流电源输入并具备双回路自动切换功能。
⏹UPS系统的要求
1)输入电源为200VAC或380VAC50Hz。
2)输出电源为220VAC50Hz。
3)UPS的容量为:
6KVA。
4)续电能力不小于30分钟。
5)具有自诊断及报警、工作状态显示。
⏹自控系统对供电质量要求
供电电源等级及其偏差、供电频率及其偏差、纹波系数、最大幅值等符合系统要求。
2.4.5电子机柜和接线
6)电子设备柜的外壳防护等级,控制室内应为IP30,主厂房内应用IP54,露天现场应用IP65。
7)机柜门应有导电门封垫条,以提高抗射频干扰(RFI)能力。
柜门上不应装设任何系统部件。
8)机柜的设计应满足电缆由柜底引入的要求,特殊要求时应满足电缆由机柜侧面引入的要求。
9)对需散热的电源装置,应提供易于更换的排气风扇和内部循环风扇。
10)机柜内应装设温度检测开关,当温度过高时进行报警。
11)装有风扇的机柜均应提供易于更换的空气过滤器。
12)机柜内的端子排应布置在易于安装接线的地方,即为离柜底300mm以上和距柜顶150mm以下。
机柜端子应至少能接入1~2.5mm2截面的电缆。
每个机柜的I/O点的数量不应过多,不宜大于250~300点(机柜电缆不宜多于180根),机柜内应留有充足的备用端子,备用裕度为50%。
13)机柜内的每个端子排和端子都应有清晰的标志,并与图纸和接线表相符。
端子号采用端子打号机制作。
14)端子排、电缆夹头、电缆走线槽及接线槽均应由“非燃烧”型材料制造。
15)提供机柜、控制台以及其他设备之间互联的电缆(包括两端的接触件),这些电缆应符合IEEE防火标准。
16)电源模件、处理器模件或I/O模件之间的连接应避免手工接线。
17)机柜内应预留充足的空间,能方便地接线、汇线和布线。
3工艺流程及系统硬件构成
3.1工艺流程简介
高炉TRT发电装置由透平主机系统、高低压发配电系统、润滑油系统、动力油系统、电液伺服控制系统、给排水系统、大型阀门系统、氮气密封系统、自动控制系统等部分组成。
TRT主工艺流程如下图所示。
高炉煤气经过重力除尘器、布袋除尘器,再经入口电动碟阀、入口插板阀、快速切断阀进入透平机入口,通过导流器使气体转成轴向进入叶栅,气体在静叶和动叶栅组成的流道中不断膨胀做功,压力和温度逐级降低,并转化为动能作用于转子,使之旋转,转子通过联轴器带动励磁发电机发电,做功后的煤气从透平机出口进入工艺管网供用户使用。
在入口插板阀之前,透平出口之后并联有旁通快开阀组,旁通阀组在正常停机和紧急停机时,进行高炉顶压控制。
3.2控制系统构成及选型
自动控制系统设置了二台操作员站(其中一台具有工程师站的功能),这二台操作员站是相互兼容的,即都具有相同的功能并且都能完成所有的操作任务。
控制系统拓扑结构如下图所示:
控制器通过智能型I/O模块,连接端子及必要的信号处理,完成连续的,离散的,顺序的控制及数据采集功能。
系统组件(控制站、操作员站和I/O模块)之间是通过高速数据公路进行通讯,系统中全部变量的更新周期≥10次/秒。
3.2.1ControlLog系统控制平台
为保证TRT机组长期安全、稳定地运行,自动控制系统采用ROCKWELL-AB公司生产的ControlLog系统控制平台。
代表自动化发展新趋势的新一代ControlLogix控制系统,从传统单纯的PLC和DCS控制转为PLC和DCS融合发展的方式,是罗克韦尔自动化顺应这种发展潮流推出的新一代的控制平台,Logix控制器平台是将高速离散控制、过程控制、协调传动控制、运动控制、批次控制和安全控制融于一体的一个控制平台。
允许混合使用多个处理器、多种网络和I/O。
系统灵活性强、易于集成、模块化设计、开放式结构,特有的升级固件,使得系统在应用中功能强大、安全可靠,而且极大地节省培训费用和工程实施费用。
ControlLogix在TRT过程控制中的选型和应用,基于下述特点:
3.2.1.1控制器:
ControlLogix处理器为适合顺序、过程、传动和运动控制的模块化、高性能控制平台:
每个处理器可以执行多个控制任务,减少所需要的控制器个数,这样,排错更快。
可以分别触发多个周期任务以便达到更高的性能水平。
每台Logix5555控制器最大寻址量128000点DI/O,4000点AI/O及回路。
ControlLogix平台通过背板提供了高速数据传输。
各控制器能产生(广播)和使用(接收)系统标签,这种技术使得多个控制器共享输入信息和输出状态,非常实用。
可选用户内存(1.5Mb)。
用户根据需要进行灵活的标签定义方式,用户甚至可以定义自己的数据结构,用自己定义的数据结构,可定义成类似BF.system1.hopper1.motor1.state这样的标签名称,非常直观,有些类似于高级语言中的数据结构定义
模块可进行固件升级(CPU、SRM、CNB(R)),固件升级就是运行效能和可靠性的升级,用户可以从ROCKWELL网站下载新的Flash版本。
3.2.1.21756系列智能I/O模块:
所有模板均为智能型设计,根据模板类型不同,每个模板的每个通道都可依用户需要进行设置,而且由于网络的灵活性及模板的智能化,可组态成OWNER工作方式,多个CPU可读取同一个模板的数据。
I/O模块种类繁多,可拆卸端子,具有带电拔插、分变则报(COS)、自诊断、时间标记、模块标识、闪存升级、电子保险、单独隔离等功能。
模块广播数据的速率可设定。
1756-HSC高速计数模块(4通道)每2ms就能更新数据,效率高。
3.2.1.3网络设置:
NetLinx体系是ControlNet、DeviceNet和Ethernet/IP三个开放式网络的基础,网络分层、分工明确、安全可靠。
通过在系统中插入不同类型的通讯模板,系统可组成CONTROLNET网、以太网,可连接DEVICENET设备,可进行串行通讯以及DHRIO通讯,网络结构可以是总线型、树型等,非常方便、灵活。
——EtherNet
EtherNet/IP是开放的工业联网标准支持实时I/O控制和消息传递功能。
这种融合是基于将以太网应用于工业控制应用日益明显的需求;
生产者/消费者(Producer/Consumer)网络服务支持您在同一链路上完整实现设备组态(configure)、实时控制(control)、信息采集(collect)等全部网络功能。
——ControlNet
控制网ControlNet冗余、开放、高速、实时、对等传送数据信息,ControlNet能够可靠预测数据何时发送,具有高度的确定性。
ControlNet网络除了为关键任务提供确定的、可重复的控制数据传输,还支持非关键数据的传送。
I/O的刷新和控制器到控制器的互锁永远比程序的上载/下载、消息传送(Messaging)等占有更高的优先级。
——DevicelNet
设备网DevicelNet,是一种开放式的底层通用网络,基于标准的CAN技术,具有互操作性。
成本及维护费用低。
3.2.1.4操作员站:
操作员站包括专业的工业计算机和基于WINDOWS平台的罗克韦尔软件包。
是罗克韦尔自动化公司自行开发推出的产品,具有世界工业界领先的水平。
RSLogix5000梯形图编程软件包,有灵活易用的编辑功能、通用的操作画面、诊断和纠错工具。
RSView是高度集成、基于组件的人机界面,发挥微软领先技术优势的监控软件,其开放性与第三方程序有高度兼容性。
RSLinx为现场设备连接罗克韦尔自动化产品的通讯软件,界面友好、功能强大,支持不同网络上的设备通讯。
工业计算机
工控机为VERSAVIEWINTEGRATEDDISPLAYCOMPUTER15-INCHTFT,15吋TFT具触摸功能的高性能工业计算机。
HMI
RSViewSupervisoryEdition,通常称为:
RSViewSE,是一个强大的管理级的监控软件。
它具有多服务器集群和多客户端的分布式结构,和强大的可伸缩性。
利用RSViewEnterprise系列的共用开发环境-RSViewStudio进行开发。
应用组态存在于各个RSViewSE服务器当中,而客户端可以任意的调用显示各服务器中的应用。
RSViewSupervisoryEdition同时也是罗克韦尔自动化ViewAnyWare产品战略的核心组成部分。
作为人机监控软件-HMI,RSView第一个采用了:
1)全面支持ActiveX™的技术,使得用户可以在显示画面中任意简单地插入ActiveX控件,来丰富应用。
2)开发了RSViewSE的对象模型-ObjectModel,使得用户可以简单的将RSView32和其他的基于组件的应用软件互操作或者集成应用。
3)集成微软的VisualBasic®forApplications(VBA)作为内建的脚本语言编辑器。
可以随意定制开发后台应用程序。
4)同时支持OPC的服务器和客户端模式。
亦即既可以通过OPC和硬件通讯,又可以向其他软件提供OPC的服务。
5)第一个支持附加件结构-AOA。
使得用户可以将其他的功能模块直接挂接到RSViewSE的核心上去,生成一体的应用。
RSViewSupervisoryEdition的主要特点描述如下:
⏹基于网络的分布式监控
RSViewSE的多服务器多客户端结构可以很容易的建立分布式应用的方案。
这种具有高度伸缩性的结构可以应用在小到一台服务器一个客户端的小系统,也可以应用在多服务器多客户端的大系统上。
⏹共用的开发环境-RSViewStudio
利用组态工具RSViewStudio进行应用开发,可以显著减少开发时间和节省开发成本。
RSViewStudio支持RSViewME和RSViewSE组态内容的互相再利用,这样你可以直接将基于嵌入式系统开发的组态内容,如在RSViewME上开发的画面,直接拷贝或者引导到分布式的RSViewSE中去,反过来也一样,前后互相兼容。
⏹增强的罗克韦尔自动化优选连接方案
由于采用了最新的罗克韦尔产品的FactoryTalk底层通讯和数据服务架构,RSViewSE可以广泛的、高性能的和众多不同网络中的众多不同的PLC,如ControlLogix和其它Allen-BradleyPLC进行通讯。
同样的,还可以利用高性能的网络接口和OPC技术同时挂接众多第三方的PLC和网络进行通讯。
⏹直接I/O数据关联
在推荐应用中,RSViewSE不需要建立任何的Tag-标签来定义和PLC的通讯关系。
RSViewSE可以直接关联控制器处理器中的所有I/O信息。
在组态的时候,只需要将所需的点直接拖放到画面等需要的地方去。
避免了再次定义Tag的重复劳动,同时减少了开发的出错机会。
当修改程序或者I/O的时候,RSViewSE可以自动直接继承这一改变。
⏹透明的数据集成
在RSViewSE的应用中,您不必担心您的数据是从哪个地方哪个PLC中采集来的。
因为所有的PLC-包括不同品牌的PLC对于服务器,开发员,客户端来说都是透明的。
FactoryTalk中采用了数据命名映射的技术。
数据并不用某一特定PLC的特定物理内存格式来描述,而是更为容易理解,并且可以智能映射的符号描述法。
当一个I/O点发生接线或者其他物理变化时,FactoryTalk可以智能映射,RSViewSE无需做任何组态修