无损检测的概述.docx
《无损检测的概述.docx》由会员分享,可在线阅读,更多相关《无损检测的概述.docx(12页珍藏版)》请在冰豆网上搜索。
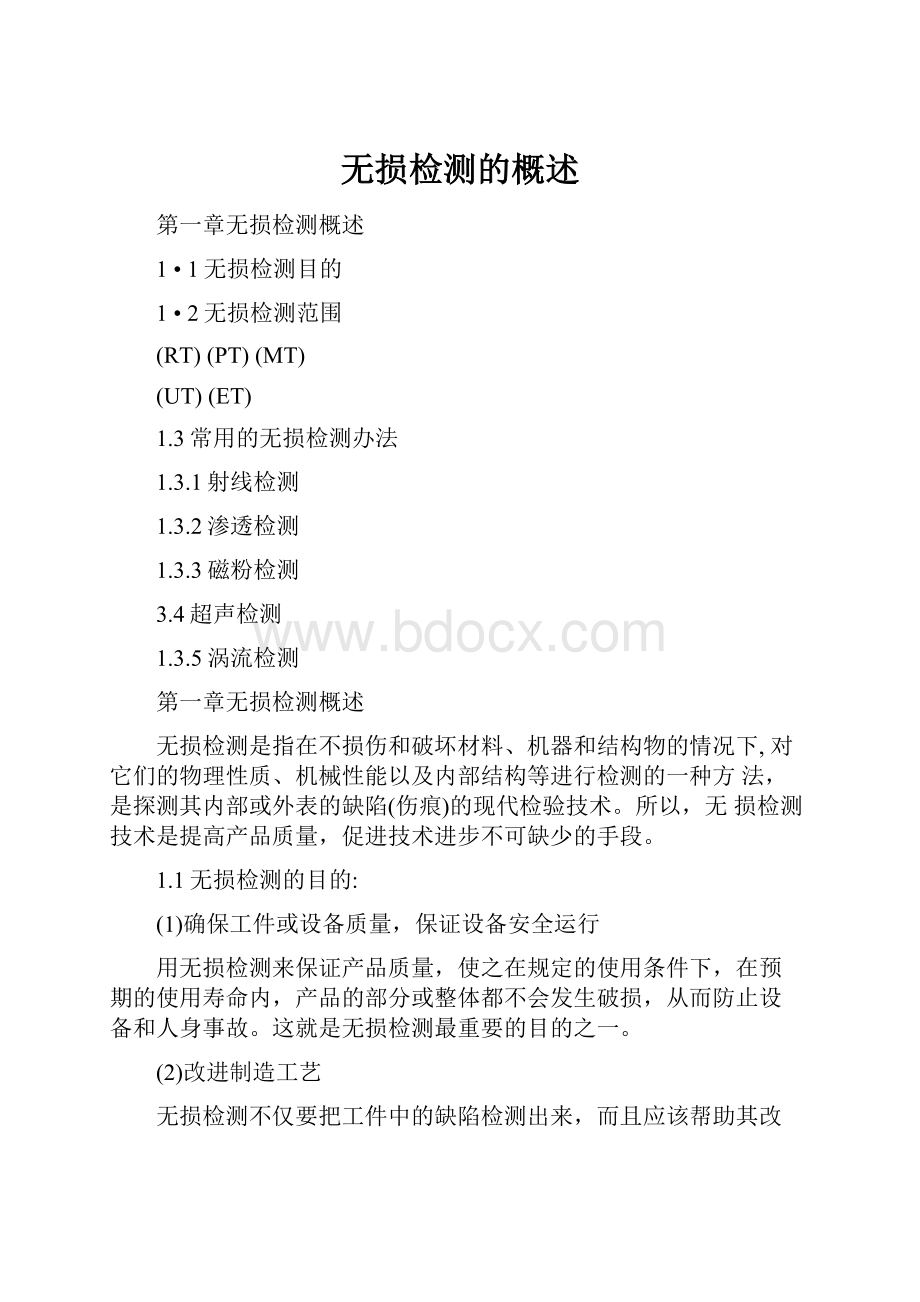
无损检测的概述
第一章无损检测概述
1•1无损检测目的
1•2无损检测范围
(RT)(PT)(MT)
(UT)(ET)
1.3常用的无损检测办法
1.3.1射线检测
1.3.2渗透检测
1.3.3磁粉检测
3.4超声检测
1.3.5涡流检测
第一章无损检测概述
无损检测是指在不损伤和破坏材料、机器和结构物的情况下,对它们的物理性质、机械性能以及内部结构等进行检测的一种方法,是探测其内部或外表的缺陷(伤痕)的现代检验技术。
所以,无损检测技术是提高产品质量,促进技术进步不可缺少的手段。
1.1无损检测的目的:
(1)确保工件或设备质量,保证设备安全运行
用无损检测来保证产品质量,使之在规定的使用条件下,在预期的使用寿命内,产品的部分或整体都不会发生破损,从而防止设备和人身事故。
这就是无损检测最重要的目的之一。
(2)改进制造工艺
无损检测不仅要把工件中的缺陷检测出来,而且应该帮助其改
进制造工艺。
例如,焊接某种压力容器,为了确定焊接规范,可以根据预定的焊接规范制成试样,然后用射线照相检查试样焊缝,随后根据检测结果,修正焊接规范,最后确定能够达到质量要求的焊接规范。
(3)降低制造成木
通过无损检测可以达到降低制造成本的目的。
例如,焊接某容器,不是把整个容器焊完后才无损检测,而是在焊接完工前的中间工序先进行无损检测,提前发现不合格的缺陷,及时进行修补。
这样就可以避免在容器焊完后,由于出现缺陷而整个容器不合格,从而节约了原材料和工时费,达到降低制造成本的目的。
1.2无损检测的范围
(1)组合件的内部结构或内部组成情况的检查
(2)材料.铸锻件和焊中缺陷缝的检查
a、质量评定
bs寿命评定
(3)材料和机器的计量检测
通过定量的测定材料和机器的变形量或腐蚀量来确定能不能继续使用。
例如,用超声波测厚仪来测定容器的腐蚀量,通过射线照相来测定原子反应堆用过的燃料棒的变形量、喷气发动机叶片的变形量等。
(4)材质的无损检测
无损检测可以用来验证材料品种是否正确,是否按规定进行处
理,例如,可采用电磁感应法来进行材质混料的分选和材料热处理状态的判别。
(5)表面处理层的厚度测定
确定各种表而层的深度和厚度。
例如,用电磁感应检测法可以测定渗碳淬火层的深度和镀层的厚度。
(6)应变测试1.3常用的无损检测办法1.3.1射线检测(RT)
射线检测(探伤)有X射线、Y射线和中子射线等检测方法。
它是利用各种射线源对材料的透射性能及不同材料的射线的衰减程度的不同,使底片感光成黑度不同的图像来观察的。
射线检测用来检测产品的气孔、夹渣、铸造孔洞等立体缺陷。
当裂纹方向与射线平行时就能被检查岀来。
1、基本原理
利用射线通过物质时的衰减规律,即当射线通过物质时,由于射线与物质的相互作用发生吸收和散射而衰减。
其衰减程度,则根据其被通过部位的材质.厚度和存在缺陷的性质不同而异。
2、应用
优点是检测结果可作为档案资料长期保存,检测图像较直观,对缺陷尺寸和性质判断比较容易。
缺点是当裂纹而与射线近于垂直时就很难检查出来,对工件中平而型缺陷(裂纹未熔合等缺陷)也具有一定的检测灵敏度,但与其
它常用的无损检测技术相比,对微小裂纹的检测灵敏度较低,并且射线源
生产成
术长,
3、主q
照才
试件
铅玻璃
反射镜
荧光屏
I
机械传动装置
荧光屏
观察者
图1.5荧光屏观察法检测示意图
1。
3
4
W
d
I一一被透照试件诃——射线感光胶片;
3气孔(缺陷)川一-夹渣(缺陷)
试件
胶片位置①
胶片位置②
图1.3投影式放大照相原理
图L2射线照相原理示意图
1.3.2渗透检测(PT)
液体渗透检测是一种检查工件或材料表而缺陷的一种方法,它不受材料磁性的限制,比磁粉探伤的应用范围更加广泛。
应用于各种金属.非金属.磁性.非磁性材料及零件的表面缺陷的检查。
可以说,除表面多孔性材料以外,几乎一切材料的表而开口缺陷都可以应用此方法获得满意的检测结果。
1、基木原理
利用黄绿色的荧光渗透液或红色的着色渗透液对窄狭缝隙良好的渗透性,经过渗透清洗.显示处理以后显示放大了的探伤显示痕迹,用目视法来观察,对缺陷的性质和尺寸做出适当的评价。
2s应用
优点是应用广泛,原理简明易懂,检查经济,设备简单,显示缺陷直观,并可以同时显示各个不同方向的各类缺陷。
对大型工件和不规则零件的检查以及现场机件的抢修检查,更能显示其特殊的优点。
但渗透探伤对埋藏于表皮层以下的缺陷是无能为力的。
缺点是只能检查开口暴露于表面的缺陷,另外还有操作工序繁杂等。
3s步骤
第一步:
将被探工件浸涂具有高度渗透能力的渗透液,由于液
紫外灯
紫外灯
⑸
r荧光法滞诲紫外光源
I着色法眼看
1.3.3磁粉检测(MT)1、基木原理
当材料或工件被磁化后,若在工件表面或近表而存在裂纹、冷隔等缺陷,便会在该处形成一漏磁场。
此漏磁场将吸引、聚集检测过程中施加的磁粉,而形成缺陷显示。
因此,磁粉检测首先是对被检丄件加外磁场进行磁化.
外加磁场的获得一般有两种方法:
一种是由可以产生大电流(几百安培至上万安培)的磁力探伤机直接给被检工件通大电流而产生磁场;
另一种是把被检工件放在螺旋管线圈产生的磁场中,或是放在电磁铁产生的磁场中使工件磁化。
工件被磁化后,在工件表面上均匀喷洒微颗粒的磁粉(磁粉平均粒度为5〜lOum),—般用四氧化三铁或三氧化二铁作为磁粉。
如果被检工件没有缺陷,则磁粉在工件表面均匀分布。
当工件上有缺陷时,由于缺陷(如裂纹.气孔、非金属夹杂物等)内含有空气或非金属,其磁导率远远小于工件的磁导率;由于磁阻的变化,位于工件表而或近表而的缺陷处产生漏磁场,形成一个小磁极,如图3.1所示。
磁粉将被小磁极所吸引,缺陷处由于堆积比较多的磁粉而被显示出来,形成肉眼可以看到的缺陷图像。
为了使磁粉图像便于观察,可以采用与被检工件表面有较大反衬颜色的磁粉。
常用的磁粉有黑色、红色和口色。
为了提高检测灵
敏度,还可以采用荧光磁粉,在紫外线照射下使之更容易观察到工件中缺陷的存在。
2、应用
用于检测铁磁性材料和丄件(包括铁.線.钻等)表而上或近表而的裂纹以及其它缺陷。
对表而缺陷最灵敏,对表而以下的缺陷随埋藏深度的增加检测
灵敏度迅速下降。
它被广泛用于磁性材料表ffi和近表面缺陷的检测。
能采用磁粉检测方法。
但当铁磁性材料上的非磁性涂层厚度不超过
50Um时,对磁粉检测的灵敏度影响很小。
3s方法a、湿法
磁悬液应采用软管浇淋或浸渍法施加于试件,使整个被检表面被完全覆盖。
采用连续法时,磁化电流应在施加磁悬液之前或从磁悬液中取出之前接通(如果检测采用浸渍法),并保持1/5〜1/2S,直至试件
被磁悬液覆盖,磁悬液覆盖膜足以产生良好的磁痕。
采用剩磁法时,试件应通过施加电流至少1/5S的方法来磁化。
此后,切断磁化电流,采用软管浇淋或浸渍法施加磁悬液。
对于浸渍法,试件应仔细地从磁悬液中取出,以免冲掉磁痕。
对于剩磁荧光磁粉检验法,如觉得有必要保证缺陷的磁痕有效,则试件可放在用于制备磁悬液的载液中仔细清洗。
b、干法
磁粉应直接喷撒在被检区域,并除去过量的磁粉。
轻轻地振动试件,使其获得较为均匀的磁粉分布。
应注意避免使用过量的磁粉,不然会影响缺陷的有效显示。
对于连续法,磁化电流应恰好在施加磁粉前接通,并应在其后的吹风、轻敲或振动中,保持接通。
对于剩磁法,试件应先磁化,在切断磁化电流之后,再按上述方法施加磁粉。
1.3,4超声检测(UT)1.原理和类型
超声波探伤主要是通过测量信号往返于缺陷的渡越时间,来确定缺陷和表而间的距离;测量回波信号的幅度和发射换能器的位
来确定缺陷的大小和方位。
这就是通常所说的脉冲反射法或A扫描法。
此外,还有B扫描和C扫描等方法。
B扫描可以显示工件内部缺陷的纵截面图形。
C扫描可以显示工件内部缺陷的横剖面图形。
1、应用
超声波检测是工业无损检测中应用最为广泛的一种方法。
就无损探伤而言,超声波法适用于各种尺寸的锻件、轧制件、
煌鑼和某些铸件-于论皋儆铁.有仔■金属和韭®制可以采fflK
探头
发射波事F—缺陥波;B—--j底波
图4.18接触法探伤
T—发射波;S—界面波;F—缺陷波;B—底波
1.3.5涡流检测(ET)
涡流检测
工业上无损检测的方法之一。
给一个线圈通入交流电,在一定条件下通过的电流是不
变的。
如果把线圈靠近被测工件,像船在水中那样,工件内会感应出涡流•受涡流影响,线圈电流会发生变化。
由于涡流的大小随工件内有没有缺陷而不同,所以线圈电流变化的大小能反映有无缺陷》原理:
将通有交流电的线圈置于待测的金属板上或套在待测的金属管外(见图)。
这时线圈内及其附近将产生交变磁场,使试件中产生呈旋涡状的感应交变电流,称为涡流。
涡流的分布和大小,除与线圈的形状和尺寸、交流电流的大小和频率等有关外,还取决于试件的电导率、磁导率、形状和尺寸、与线圈的距离以及表面有无裂纹缺陷等。
因而,在保持其他因素相对不变的条件下,用一探测线圈测虽涡流所引起的磁场变化,可推知试件中涡流的大小和相位变化,进而获得有关电导率、缺陷、材质状况和其他物理量妆口形状、尺寸等)的变化或缺陷存在等信息。
但由于涡流是交变电流,具有集肤效应,所检测到的信息仅能反映试件表面或近表面处的情况。
特点:
仁对于金属皆、棒、线材的检测,不需要接触,也无需要耦合介质。
所以检测速度高,易于实现自动化检测,特别适合在线普检。
2、对于表而缺陷的探测灵敏度很高,且在一世范围内具有良好的线性指示,可对大小不同缺陷进行评价,所以可以用作质量管理与控制。
3、影响涡流的因素很多,如裂纹、材质、尺寸、形状及电导率和磁导率等。
采用特泄脾电路进行处理,可筛选出某一因素而抑制其他因素,由此有可能对上述某单独影响因素进行有效的检测。
4、由于检査时不需接触工件又不用耦合介质,所以可进行高温下的检测。
由于探头町伸入到远处作业,所以可对工件的狭窄区域及深孔壁(包姑管壁)等进行检测。
5、由于采用电信号显示,所以可存储、再现及进行数据比较和处理。
6、涡流探伤的对彖必须是导电材料,且由于电磁感应的原因,只适用于检测金属表而缺陷,不适用检测金属材料深层的内部缺陷。
7、金属表而感应的涡流的渗透深度随频率而异,激励频率高时金属表而涡流密度大,随着激励频率的降低,涡流渗透深度增加,但表面涡流密度下降,所以探伤深度与表而伤检测灵敏度是相互矛盾的,很难两全。
当对一种材料进行涡流探伤时,须要根据材质、表而状态、检测标准作综合考虑,然后再确定无损检测方案与技术参数。
8、采用穿过式线圈进行涡流探伤时,线圈覆盖的是管、棒或线材上一段长度的岡周,获得的信息是整个圆环上影响因素的累积结果,对缺陷所处圆周上的具体位置无法判泄。
9、旋转探头式涡流探伤方法可准确探出缺陷位置,灵敏度和分辨率也很高,但检测区域狭小,在检验材料需作全而扫查时,检验速度较慢。
10、涡流探伤至今还是处于当量比较检测阶段,对缺陷做出准确的左性立S判断尚待开发。