IF钢冶炼关键技术.ppt
《IF钢冶炼关键技术.ppt》由会员分享,可在线阅读,更多相关《IF钢冶炼关键技术.ppt(95页珍藏版)》请在冰豆网上搜索。
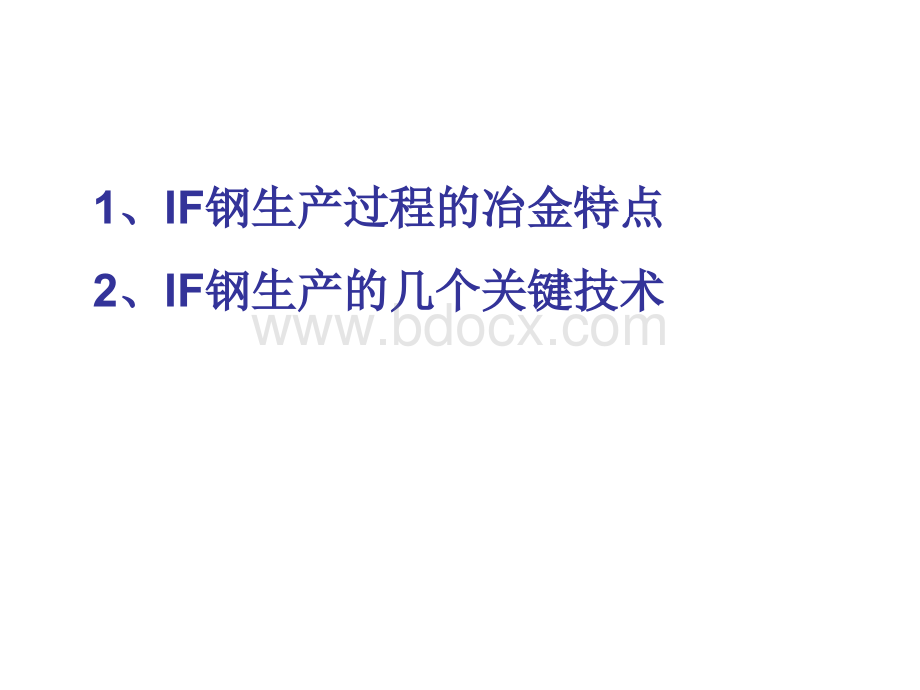
1、IF钢生产过程的冶金特点钢生产过程的冶金特点2、IF钢生产的几个关键技术钢生产的几个关键技术RHRH高效脱碳高效脱碳脱碳反应:
CCOOCOCO日本钢管技报,1986,No.114,1RH处理脱碳速度式为:
(1)v:
RH真空室内钢液体积,m3;ak:
脱碳反应速度系数,m3/min;CV:
真空室内钢水碳含量,;Ce:
与CO分压平衡的钢液碳含量,。
式中:
提高脱碳速度:
增加ak;增强混合,加快C向反应界面的传递速度。
减少Ce;提高真空程度,降低PCO。
1、强真空系统抽气能力和高真空度是获得超低碳的必要条件神户制钢加古川厂2RH的有关参数1990SteelmakingConferenceProceedings,p.79新日铁名古屋厂2RH的有关参数2001SteelmakingConferenceProceedings,p.625加古川厂不同RH真空度对脱碳反应的影响1990SteelmakingConferenceProceedings,p.792、IF钢生产工序的发展及技术特点钢生产工序的发展及技术特点国内外国内外IF钢的生产工艺流程一般为:
钢的生产工艺流程一般为:
铁水预处理转炉冶炼一铁水预处理转炉冶炼一RH真空精炼一连铸热真空精炼一连铸热轧一冷轧一退火一平整。
轧一冷轧一退火一平整。
每一个工序均在不同程度上影响每一个工序均在不同程度上影响IF钢的最终产品钢的最终产品性能。
性能。
2.1铁水预处理工序铁水预处理工序在进行在进行IF钢生产时,必须进行铁水预处理,其目钢生产时,必须进行铁水预处理,其目的是:
的是:
减少转炉冶炼过程中的渣量,从而减少出钢过减少转炉冶炼过程中的渣量,从而减少出钢过程中的下渣量;程中的下渣量;降低转炉冶炼终点钢液和炉渣的氧化性;降低转炉冶炼终点钢液和炉渣的氧化性;提高转炉冶炼终点炉渣的碱度和提高转炉冶炼终点炉渣的碱度和MgO含量。
含量。
采用喷吹金属镁和活性石灰对铁水进行脱硫,可采用喷吹金属镁和活性石灰对铁水进行脱硫,可使入炉铁水中的硫含量控制在使入炉铁水中的硫含量控制在0.003以下。
而通以下。
而通过喷吹含镁和过喷吹含镁和CaC2,可使入炉铁水中的硫含量降,可使入炉铁水中的硫含量降至至0.010以下。
以下。
2.2转炉冶炼工序转炉冶炼工序总结国内外关于总结国内外关于IF钢转炉冶炼的研究成果,可归钢转炉冶炼的研究成果,可归纳为:
纳为:
采用顶底复吹转炉进行冶炼,降低转炉冶炼终采用顶底复吹转炉进行冶炼,降低转炉冶炼终点钢液氧含量;点钢液氧含量;实现转炉冶炼动态模型控制,提高转炉冶炼终实现转炉冶炼动态模型控制,提高转炉冶炼终点钢液碳含量和温度的双命中率;点钢液碳含量和温度的双命中率;提高铁水比,入炉铁水的硫含量小于提高铁水比,入炉铁水的硫含量小于0.003;控制矿石投入量;控制矿石投入量;提高氧气纯度,控制炉内保持正压;提高氧气纯度,控制炉内保持正压;转炉冶炼后期增大底部惰性气体流量,加强溶转炉冶炼后期增大底部惰性气体流量,加强溶池搅拌;池搅拌;转炉冶炼后期采用低枪位操作;转炉冶炼后期采用低枪位操作;将转炉冶炼终点钢液的碳含量由将转炉冶炼终点钢液的碳含量由0.020.03提高至提高至0.030.04;采用出钢挡渣技术;采用出钢挡渣技术;出钢过程中不脱氧,只进行锰合金化处理;出钢过程中不脱氧,只进行锰合金化处理;采用钢包渣改质技术。
采用钢包渣改质技术。
2.3RH真空精炼工序真空精炼工序总结国内外关于总结国内外关于IP钢钢RH真空精炼的研究成果,可真空精炼的研究成果,可归纳为:
归纳为:
严格控制严格控制RH真空精炼之前钢液中的碳含量、氧含量和真空精炼之前钢液中的碳含量、氧含量和温度;温度;采取采取RH真空精炼前期吹氧强制脱碳方法:
真空精炼前期吹氧强制脱碳方法:
增大增大RH真空脱碳后期的驱动气体流量,增加反应界面。
真空脱碳后期的驱动气体流量,增加反应界面。
减少减少RH真空槽冷钢;真空槽冷钢;采用海绵钛替代钛铁合金;采用海绵钛替代钛铁合金;建立合理的建立合理的RH真空精炼过程控制模型;真空精炼过程控制模型;进行进行RH炉气在线分析、动态控制;炉气在线分析、动态控制;采用钙处理技术。
采用钙处理技术。
2.4连铸工序连铸工序总结国内外关于总结国内外关于IP钢连铸生产的研究成果,可归纳为:
钢连铸生产的研究成果,可归纳为:
采用钢包下渣自动检测技术;采用钢包下渣自动检测技术;加强大包一长水口之间的密封;加强大包一长水口之间的密封;连铸中间包使用之前采用氩气清扫;连铸中间包使用之前采用氩气清扫;提高大包滑动水口开启成功率;提高大包滑动水口开启成功率;采用连铸浸入式长水口;采用连铸浸入式长水口;采用大容量连铸中间包,并进行钢液流场优化;采用大容量连铸中间包,并进行钢液流场优化;保证连铸中间包内钢液面相对稳定,且高于临界高度;保证连铸中间包内钢液面相对稳定,且高于临界高度;采用低碳碱性连铸中间包包衬和覆盖剂;采用低碳碱性连铸中间包包衬和覆盖剂;采用低碳高粘度连铸结晶器保护渣:
采用低碳高粘度连铸结晶器保护渣:
采用连铸结晶器液面自动控制技术,确保液面波动小于采用连铸结晶器液面自动控制技术,确保液面波动小于3mm。
2.5IF钢中碳含量的控制钢中碳含量的控制IF钢中碳含量的控制技术主要包括以下三个钢中碳含量的控制技术主要包括以下三个方面:
方面:
(1)转炉冶炼终点碳的控制;)转炉冶炼终点碳的控制;在在IF钢生产时,日本川崎制钢公司、美国钢生产时,日本川崎制钢公司、美国Inland钢铁公司和宝钢将转炉炼终点钢液中的碳含量控钢铁公司和宝钢将转炉炼终点钢液中的碳含量控制为制为0.030.04,氧含量控制为,氧含量控制为0.050.065;德国德国Thyssen钢铁公司认为转炉冶炼终点钢液的钢铁公司认为转炉冶炼终点钢液的最佳碳含量为最佳碳含量为0.03,最佳氧含量为,最佳氧含量为0.06。
(2)RH真空脱碳真空脱碳美国美国Inland钢铁公司采用钢铁公司采用RH-OB进行深脱碳处理。
进行深脱碳处理。
RH-OB的真空脱碳过程主要分为以下两个阶段:
的真空脱碳过程主要分为以下两个阶段:
强制脱碳阶段强制脱碳阶段从开始到第从开始到第8min,RH-OB采取吹氧强制真空脱碳方法,采取吹氧强制真空脱碳方法,真空度为真空度为4kPa8kPa。
在此阶段,钢液中的碳含量可从。
在此阶段,钢液中的碳含量可从0.030.04降低至降低至810-6左右。
左右。
自然脱碳阶段自然脱碳阶段从第从第8min至第至第12min,RH-OB停止吹氧,进行自然真空停止吹氧,进行自然真空脱碳方法,真空度小于脱碳方法,真空度小于266Pa。
在此阶段,钢液中的碳含。
在此阶段,钢液中的碳含量可从量可从80106降低至降低至2010-6以下。
以下。
宝钢为了满足钢种和多炉连浇的要求,采取提高脱碳速度宝钢为了满足钢种和多炉连浇的要求,采取提高脱碳速度的方法:
的方法:
在在RH脱碳初期采用硬脱碳方式,真空室压力快速下降,脱碳初期采用硬脱碳方式,真空室压力快速下降,加速脱碳;加速脱碳;在在RH脱碳后期通过脱碳后期通过OB喷嘴的环缝吹入较大量的氩气,喷嘴的环缝吹入较大量的氩气,增加反应界面。
增加反应界面。
武钢针对武钢针对RH真空设备存在的抽气能力过小的问题,开发真空设备存在的抽气能力过小的问题,开发出如下的出如下的RH真空脱碳技术:
真空脱碳技术:
提高浸渍管的寿命,尤其是延长大直径的使用时段;提高浸渍管的寿命,尤其是延长大直径的使用时段;加大驱动氩气流量,并实现石英浸渍管内径扩大的动态加大驱动氩气流量,并实现石英浸渍管内径扩大的动态调整;调整;真空室快速减压。
真空室快速减压。
采用以上技术后,在采用以上技术后,在RHRH真空脱碳过程中,可在真空脱碳过程中,可在15152020分钟分钟内将内将IFIF钢中碳含量降低到钢中碳含量降低到0.0015%0.0015%左右。
左右。
(3)防止)防止RH后钢液增碳后钢液增碳在在RH真空处理后,必须严格控制真空处理后,必须严格控制IF钢的增碳,可钢的增碳,可能导致能导致IF钢增碳的因素如下:
钢增碳的因素如下:
RH真空室内的合金及冷钢增碳;真空室内的合金及冷钢增碳;钢包覆盖剂增碳;钢包覆盖剂增碳;包衬、长水口、滑板等钢包耐火材料增碳;包衬、长水口、滑板等钢包耐火材料增碳;连铸中间包覆盖剂增碳;连铸中间包覆盖剂增碳;包衬、塞棒、浸入式水口、滑板等中间包耐火材包衬、塞棒、浸入式水口、滑板等中间包耐火材料增碳;料增碳;连铸结晶器保护渣增碳。
连铸结晶器保护渣增碳。
日本新日铁在生产日本新日铁在生产IF钢时,采用超低碳多孔钢时,采用超低碳多孔镁质钢包覆盖剂。
超低碳中间包覆盖剂和低镁质钢包覆盖剂。
超低碳中间包覆盖剂和低碳空心结晶器保护渣、低碳长水口和浸入式碳空心结晶器保护渣、低碳长水口和浸入式水口、结晶器液面控制仪等措施,水口、结晶器液面控制仪等措施,IF增碳量增碳量可稳定控制在可稳定控制在89ppm,甚至达到,甚至达到2.6ppm。
宝钢在宝钢在IF钢生产中,采用低碳高碱度中间包钢生产中,采用低碳高碱度中间包覆盖剂和低碳高粘度结晶器保护渣,同时减覆盖剂和低碳高粘度结晶器保护渣,同时减少少RH真空槽冷钢,控制从真空槽冷钢,控制从RH真空脱碳后的真空脱碳后的钢液增碳,增碳量可稳定控制在钢液增碳,增碳量可稳定控制在7ppm。
2.6IF钢中氮含量的控制钢中氮含量的控制IF钢的降氮问题主要在转炉内解决,当钢的降氮问题主要在转炉内解决,当IF钢中氮含量小于钢中氮含量小于20ppm时,时,RH真空精炼真空精炼过程中降氮非常困难,有时若密封不好还过程中降氮非常困难,有时若密封不好还导致增氮。
因此在导致增氮。
因此在IF钢生产过程中,减少转钢生产过程中,减少转炉冶炼终点的氮含量和避免钢液增氮是获炉冶炼终点的氮含量和避免钢液增氮是获得超低氮得超低氮IF钢的主要途经。
钢的主要途经。
宝钢采用的主要技术措施为:
宝钢采用的主要技术措施为:
高铁水比,控制矿石投入量;高铁水比,控制矿石投入量;提高氧气纯度,控制炉内为正压;提高氧气纯度,控制炉内为正压;转炉冶炼后期采用低枪位操作;转炉冶炼后期采用低枪位操作;提高转炉冶炼终点控制的命中率和精度,提高转炉冶炼终点控制的命中率和精度,不允许再吹;不允许再吹;钢包水口和长水口连接处采用氩气和纤维钢包水口和长水口连接处采用氩气和纤维体密封。
体密封。
采用以上措施后,采用以上措施后,RH精炼终点氮含量控制精炼终点氮含量控制在在20ppm以下,平均以下,平均13ppm。
台湾中钢公司采用以下技术:
台湾中钢公司采用以下技术:
转炉冶炼过程增加铁水比和溶剂量,形成较后的转炉冶炼过程增加铁水比和溶剂量,形成较后的渣层,增加渣层,增加CO在渣层中停留时间,隔离大气。
转在渣层中停留时间,隔离大气。
转炉冶炼结束前,向炉内加白云石,产生大量的炉冶炼结束前,向炉内加白云石,产生大量的CO气体形成正压层,阻止钢液从大气中吸氮;气体形成正压层,阻止钢液从大气中吸氮;RH精炼过程中,采用海绵钛代替钛铁合金,减少精炼过程中,采用海绵钛代替钛铁合金,减少铁合金增氮;铁合金增氮;连铸过程采用长水口、氩气密封和纤维体密封等连铸过程采用长水口、氩气密封和纤维体密封等技术进行保护浇注。
技术进行保护浇注。
采用以上技术后,采用以上技术后,IF钢中氮含量可以控制在钢中氮含量可以控制在30ppm以下。
以下。
2.7IF钢中氧含量的控制钢中氧含量的控制IF钢中氧含量的控制技术涉及转炉冶炼、钢中氧含量的控制技术涉及转炉冶炼、RH真空精炼和连铸等工艺环节。
真空精炼和连铸等工艺环节。
武钢采用了以下技术:
武钢采用了以下技术:
用顶底复吹转炉进行冶炼,降低转炉冶炼终点钢液氧含量;用顶底复吹转炉进行冶炼,降低转炉冶炼终点钢液氧含量;实现转炉冶炼动态模型控制,提高转炉冶炼终点钢液碳含量和温度实现转炉冶炼动态模型控制,提高转炉冶炼终点钢液碳含量和温度的双命中率;的双命中率;采用挡渣出钢;采用挡渣出钢;进行钢包渣改质;进行钢包渣改质;采用钢包下渣自动检测技术;采用钢包下渣自动检测技术;采用大容量连铸中间包,并进行钢液流场优化;