公铁两用桥钢梁制造工艺方案.docx
《公铁两用桥钢梁制造工艺方案.docx》由会员分享,可在线阅读,更多相关《公铁两用桥钢梁制造工艺方案.docx(28页珍藏版)》请在冰豆网上搜索。
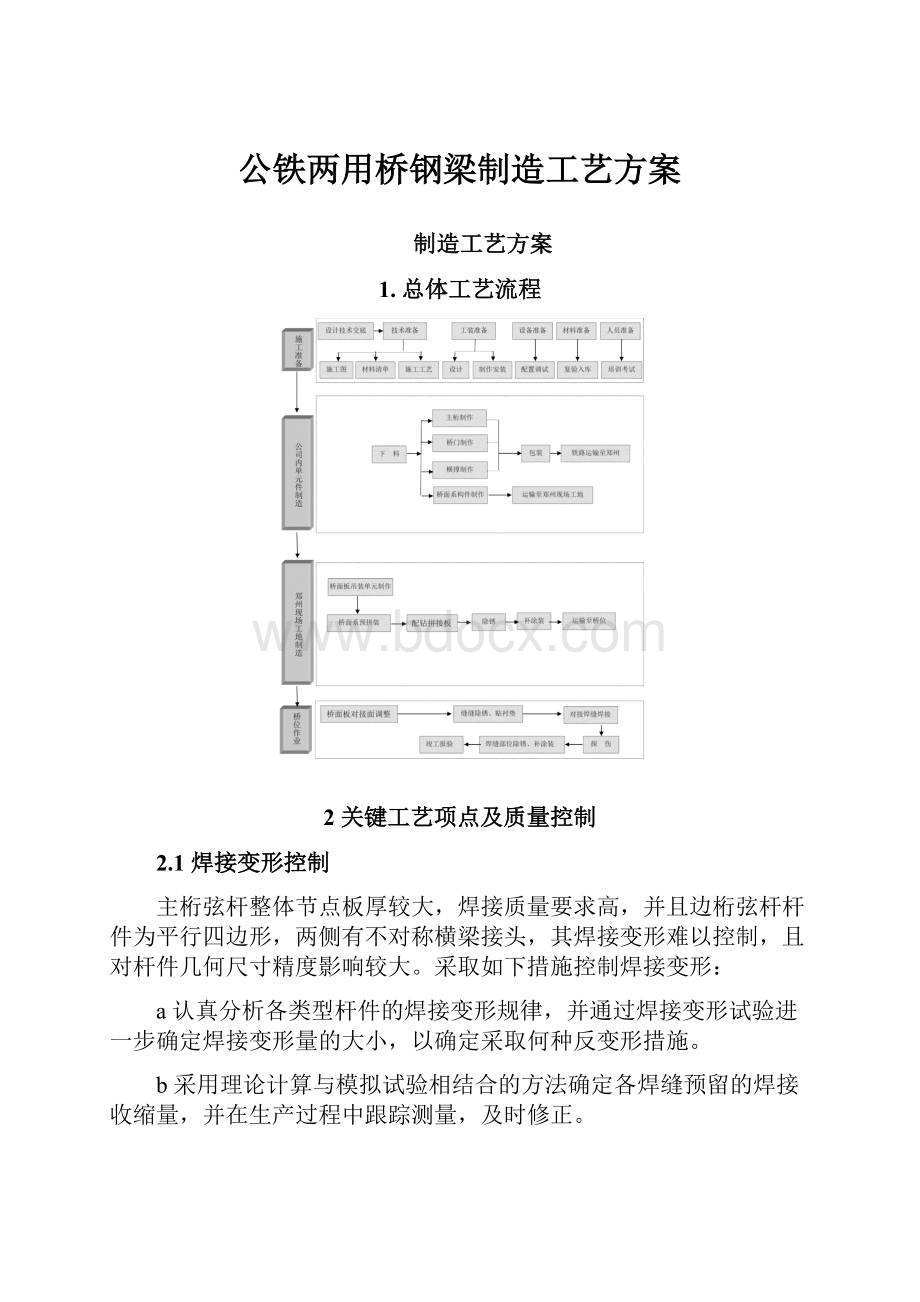
公铁两用桥钢梁制造工艺方案
制造工艺方案
1.总体工艺流程
2关键工艺项点及质量控制
2.1焊接变形控制
主桁弦杆整体节点板厚较大,焊接质量要求高,并且边桁弦杆杆件为平行四边形,两侧有不对称横梁接头,其焊接变形难以控制,且对杆件几何尺寸精度影响较大。
采取如下措施控制焊接变形:
a认真分析各类型杆件的焊接变形规律,并通过焊接变形试验进一步确定焊接变形量的大小,以确定采取何种反变形措施。
b采用理论计算与模拟试验相结合的方法确定各焊缝预留的焊接收缩量,并在生产过程中跟踪测量,及时修正。
c对零件下料、坡口加工、杆件整体组装等生产过程严格把关,并采用合理的焊接方法、优化焊接顺序、在专用胎型上焊接等措施,控制焊接变形。
2.2对接焊缝、熔透焊缝的焊接质量控制
对接焊缝和熔透焊缝是构件传力的关键焊缝,特别是整体节点板的对接和下弦杆整体节点板与上水平板的焊接,是该桥的重点和难点。
对该类焊缝焊接质量的控制是焊接工艺的重中之重。
采取如下措施:
a根据接头形式,分类进行焊接工艺试验,确定焊接方法、焊接设备、焊接材料、焊接工艺参数、焊接顺序、坡口形式等。
b根据焊接试验结果编制合理可行的焊接工艺。
c设计保证焊接质量和便于控制焊接变形的工艺装备,确保焊接工艺的有效实现和焊接变形的有效控制。
d编制关键焊缝的质量控制计划,从原材料的复验、下料、拼装、焊接和探伤等生产过程严格把关。
2.3箱形杆件精度控制
该桥边桁箱形杆件为平行四边形,中下弦杆件为上盖板伸出整体节点结构形式,箱形杆件结构新颖,整体组装精度较难控制。
采取如下控制措施:
a针对平行四边形杆件设计专用箱形组装胎型,胎型底面设置成14.036°角度,确保两腹板单元的垂直安装,同时调整板块单元的组装顺序。
b箱形杆件隔板作为杆件组装的内胎,是控制杆件组装精度的关键。
因此对隔板周边全部机加工,根据焊接收缩情况确定工艺留量,并先根据平行四边形机加工角度之后再开坡口。
c对影响杆件箱口尺寸的腹板板块测厚,配刨水平板宽度,确保杆件组装精度。
d在箱口部位设置临时支撑,控制箱口尺寸。
2.4制孔精度控制
弦杆、整体节点、拼接板等杆件的孔群较多,连接关系复杂。
其精度将直接影响桥位安装进度及质量。
因此对连接孔群的制孔精度要求很高。
采取如下措施:
a以后孔法工艺为主,先孔法为辅的制孔工艺,避免焊接变形的影响,提高制孔精度。
b设计高精度的精密划线工艺和精密制孔工艺。
c设计高精度的制孔工艺装备。
2.5试拼装质量控制
试拼装工艺是制造精度和桥位架设精度的联系纽带,是必不可少的一道重点工艺。
将采取如下措施:
a试拼装在专用的胎架上进行,胎架有足够的强度,确保试拼装过程中不产生变形;试拼装前对胎架测平,确保试拼装平面度的精度要求。
b各试拼装杆件处于自由状态进行,确保试拼装检测结果的准确性和可靠性,达到试拼装的目的。
c每次定位下一节间杆件时,均检测平面度、对角线差、节间长度、桁高等项点,确保整体试拼装精度。
2.6涂装质量控制
涂装是保证桥梁钢结构耐久性的重要措施之一,防腐涂装质量能否得到保障直接关系到钢桥梁的使用寿命长短。
通过对以往桥梁防腐涂装质量控制薄弱环节的总结分析,重点从以下几个方面对防腐涂装质量加以控制:
a严格控制涂装原材料质量,所有油漆及铝材等涂装材料进厂均必须在具有资格的涂料检测中心复验合格后方可投入使用。
b对除锈磨料的材质、大小、形状、配比、硬度等进行优选,通过工艺试验确定合理的喷砂工艺参数,确保除锈质量满足要求。
c除锈前将构件自由边倒圆弧R=2mm,保证边角部位涂层厚度要求。
d在施工全过程中,对环境温度、相对湿度、露点温度、钢板温度等环境因素进行检测,以满足涂装各工序的施工要求。
e在油漆施工过程中,对高压空气质量、油漆混合、油漆搅拌、油漆熟化、油漆粘度、稀释剂比例、喷嘴压力、枪嘴到工件距离、喷漆角度、预涂以及湿膜厚度等进行巡检,保证每一项都符合要求。
f涂装前对两种涂层过渡区域进行预涂,保证两种涂层体系过渡区域接缝整齐,涂层厚度达到要求。
g涂装时采取遮盖等有效方法对现场预留焊缝部位进行保护,避免油漆污染,影响桥位现场焊接质量。
3主要构件制造工艺
3.1零件的下料加工
钢板在下料前,进行钢板表面质量检查,对其表面缺陷按照《桥梁用结构钢》(GB/T714-2000)及《铁路钢桥制造规范》(TB10212-98)的要求进行修补及处理。
合格后的钢板在滚板机上进行滚平,使其满足平面度的要求。
根据零件的具体形状和大小确定下料方法,对较长矩形板件采用多嘴头门式切割机精切下料,对形状复杂的板件采用数控切割机精切下料,对较规则的薄板次要零件采用剪切下料;型钢采用剪切机或焰切下料;钢板对接坡口采用火焰精密切割、刨边机或铣边机加工。
3.2U形肋的制作
U形肋是桥面系的基本组成构件,每个断面U形肋数量为14根,本合同段共计1540根不同长度的U形肋。
断面尺寸为U400×300×10mm。
采用如下工艺制作:
a采用门式切割机对称切割下料,两长边预留机加工量;
b用双面铣加工两长边;
c划纵横基准线及钻孔对向线,用样板在摇臂钻床钻孔;
d在滚剪机上加工坡口;
e在数控折弯机上两边对胎折弯成型,使其满足技术标准要求。
注意:
零件下料时应对称切割,以减小切割变形。
当下料后零件旁弯影响机加工时,应对旁弯采用顶弯机进行冷矫正。
3.3中下弦杆件的制作
中下弦杆件由上盖板、下盖板、节点板、腹板、隔板、纵向加劲肋及横向接头板等零件组成(图3-1),断面尺寸为宽(2090/3080)×高(2820/3400)。
杆件最大重量43.7t,最大长度14080mm。
杆件两端及整体节点为φ33高强螺栓孔群,桥面板横梁接头盖、腹板为φ26高强螺栓孔群。
图3-1中下弦杆件示意图
3.3.1中下弦杆制作工艺流程总图
加劲板
腹板
上盖板
加劲板
隔板
下盖板
加劲板
腹板单元
槽形单元
箱形单元
中下弦杆
加劲板
上盖板单元
节点板
下盖板单元
接头板
零件的下料及加工
图3-2中下弦杆制作工艺流程总图
3.3.2中下弦制造采用的工艺
具体过程如下:
a零件采用数控火焰切割机精切下料。
下料时纵肋、盖板及腹板长度方向预留焊接收缩量;
b机加工隔板周边;机加工上盖板过渡斜坡、腹板、接头板及纵肋一端部焊接坡口;
c测量上下盖板厚度方向轧制偏差,配差机加工腹板及节点板两长边及坡口;
d在平台上组装上下盖板单元(盖板+纵肋)、腹板单元(腹板+节点板+纵肋),焊接并修整变形。
在平台上划出各单元件的横竖基准线,作为杆件整体组装的基准,并划出隔板组装位置线;
e在组装胎型上进行杆件整体组装。
首先将上盖板单元置于胎型上,按线组装隔板及腹板单元;
f采用CO2气体保护半自动焊焊接隔板与上盖板、腹板的连接焊缝;
g按基准线组装上盖板单元,采用埋弧自动焊焊接四条主焊缝,焊接时对称、同向施焊,焊后修整焊接变形;
h在划线平台上划出杆件纵横基准线、横梁腹板组装位置线和纵肋二组装位置线;
i在划线平台上修正纵横基准线,划出杆件及横梁下盖板钻孔对向线,采用钻孔样板用摇臂钻床钻制杆件两端及整体节点孔群,采用磁力钻钻制下盖板横梁位置孔群,并利用该孔定位横梁腹板采用磁力钻钻制孔群;
j组装横梁腹板及纵肋二(已钻孔),采用CO2气体保护半自动焊焊接,焊后修整焊接变形;
k参与试拼装(不试装时直接进入下道工序);
l进行杆件整体除锈、涂装,完成成品杆件制造。
3.4边下弦杆件的制作
边下弦杆件由上盖板、下盖板、节点板、腹板、隔板、纵向加劲肋及横向接头板等零件组成(图4-3),断面尺寸为宽(2630/3000)×高(2010/3100)。
杆件最大重量42.6t,最大长度14080mm。
杆件两端及整体节点为φ33高强螺栓孔群,桥面板横梁接头盖、腹板为φ26高强螺栓孔群。
节点板
隔板
上盖板
纵肋二
纵肋一
横梁腹板板
内侧腹板
下盖板
图3-3边下弦杆件示意图
3.4.1边下弦杆制作工艺流程总图同中下弦杆制作工艺流程总图
3.4.2边下弦制造采用的工艺
具体过程如下:
a零件采用数控火焰切割机精切下料。
下料时纵肋、盖板及腹板长度方向预留焊接收缩量;
b机加工隔板周边;机加工上盖板过渡斜坡、腹板、接头板及纵肋一端部焊接坡口;
c测量上下盖板厚度方向轧制偏差,配差机加工腹板及节点板两长边及坡口;
d在平台上组装上下盖板单元(盖板+纵肋,上盖板纵肋二暂不组装)、腹板单元(腹板+节点板+纵肋),焊接并修整变形。
在平台上划出各单元件的横竖基准线,作为杆件整体组装的基准,并划出隔板组装位置线;
e内侧腹板单元在划线平台上划纵横基准线及部分孔的钻孔对向线,用样板在摇臂钻床上钻两端部分孔群;
f在组装胎型上进行杆件整体组装。
首先将上盖板单元置于胎型上,按线组装内腹板单元及隔板(垂直组装腹板单元,内腹板两端孔群为先钻孔),再组装外侧腹板;
g采用CO2气体保护半自动焊焊接隔板与上盖板、腹板的连接焊缝;
h按基准线组装上盖板单元,采用埋弧自动焊焊接四条主焊缝,焊接时对称、同向施焊,焊后修整焊接变形;
i在划线平台上划出杆件纵横基准线、横梁腹板组装位置线及纵肋二组装位置线;
j在划线平台上修正纵横基准线并划出杆件端部、横梁下盖板及整体节点板钻孔对向线,采用钻孔样板摇臂钻床钻制两端及节点板孔群,用钻孔样板磁力钻钻制下盖板横梁位置孔群,并利用该孔定位横梁腹板采用磁力钻钻制孔群;
k组装横梁腹板及上盖板纵肋二,采用CO2气体保护半自动焊焊接,焊后修整焊接变形(纵肋二两端孔群已钻出);
l对内侧腹板拼接板试装配钻孔;
m参与试拼装(不试装时直接进入下道工序);
n进行杆件整体除锈、涂装,完成成品杆件制造。
3.5箱形边腹杆杆件的制作
箱形腹杆杆件由上下水平板、腹板、隔板等零件组成(图4-1),断面尺寸为宽(940/969mm)×高(800~1000mm)。
杆件两端为φ33高强螺栓孔群。
水平板
竖板
隔板
图3-4腹杆箱形杆件示意图
3.5.1腹杆箱形杆件制作工艺流程总图
竖板
隔板
槽形单元
箱形杆件
零件的下料及加工
下水平板
上水平板
图3-5腹杆箱形杆件制作工艺流程总图
3.5.2腹杆箱形杆件制造采用的工艺
具体过程如下:
a零件采用数控火焰切割机精切下料。
下料时水平板及竖板长度方向预留焊接收缩量;
b机加工隔板周边;
c测量竖板厚度方向轧制偏差,配差机加工水平板两长边及坡口;
d在组装胎型上进行杆件整体组装。
首先将下水平板单元置于胎型上,按线组装隔板;
e按基准线组装两竖板单元,采用CO2气体保护半自动焊焊接隔板与下水平板、两竖板的连接焊缝;
f按基准线组装上水平板,采用埋弧自动焊焊接四条主焊缝,焊接时对称、同向施焊,焊后修整焊接变形;
g在划线平台上划出杆件纵横基准线及钻孔对向线,采用覆盖式样板用摇臂钻床钻出两端孔群;
h参与试拼装后,进行杆件整体除锈、涂装,完成成品杆件制造。
3.6腹杆工形杆件制作
盖板
腹板
主桁腹杆工形杆件由盖板、腹板、纵向加劲肋等零件组成(图4-2),断面尺寸为宽(700~1700mm)×高(1200/1600mm)。
图3-6工形杆件示意图
采用如下工艺制作:
a门式火焰切割机精切下料,长度方向预留焊接收缩量;腹板两长边预留加工量;
b测量上下盖板厚度偏差,根据测量结果机加工腹板两焊接边及坡口,以消除板厚偏差对杆件高度的影响;
c在划线平台上划出各上下盖板及腹板基准线,作为整体组装的基准;
d在组装胎型上组装盖板及腹板;
e采用埋弧自动焊焊接,焊后修整焊接变形;
f在整体划线平台上划出杆件横竖基准线,采用覆盖式钻孔样板用摇臂钻床钻制杆件两端孔群;
g参与试拼装后,进行杆件整体除锈、涂装,完成成品杆件制造。
3.7桥面板吊装单元的制作
3.7.1桥面板块划分
郑州黄河桥铁路桥面为正交异性整体钢桥面板。
即由纵、横肋加劲的正交异性钢桥面板和主桁的下弦杆用焊接连接在一起,成为桥面结构直接参与弦杆受力的板桁组合结构。
桥面板板厚16mm,采用U形闭口肋和板式加劲肋。
标准节段横向宽6.1m,纵向12m长,在混凝土道砟槽底面的铁路桥面板上焊接剪力钉。
纵向设置4道倒T型横梁,桥面板顶板连接采用焊接,横梁腹板和底板与下弦杆连接采用M24螺栓连接。
桥面板纵肋连接采用M22螺栓连接。
桥面板吊装单元由桥面板、U形肋、横梁组成。
桥面板吊装单元制作时,先将桥面板划分为宽度2.45m~3.25m的两个板单元制作,然后将两个板单元组焊为一个吊装单元,吊装单元的最大重量约为26t。
本合同段桥面板吊装单元共计110块。
桥面板单元划分见图4-7。
图4-7桥面板吊装单元划分示意图
3.7.2桥面板块各单元部件的制作工艺
3.7.2.1桥面板单元制作工艺
桥面板单元由U形肋和面板组成,U形肋两端采用高强螺栓连接,面板与下弦杆上水平板及相邻面板采用焊接连接。
桥面板单元的制作工艺流程如下:
U肋
桥面板单元
⑴.U形肋边缘机加工后卡样板钻两端孔群,加工两长边坡口后在折弯机上压型。
在与面板组装前组焊U肋封头板;
⑵.桥面板划纵横基准线及U肋组装位置线,并将纵横基准线返到桥面板另一侧,打样冲眼;
⑶.在组装平台上按线组装U肋;
⑷.板单元焊接在反变形胎架上进行,控制焊接变形;
⑸.修整变形并划剪力钉组装位置线,按线组焊剪力钉;
⑹.修整变形后火焰切割板单元周边坡口。
⑺.桥面板单元打砂除锈、涂装后交成品。
3.7.2.2横梁制作工艺
横梁为T形结构,盖、腹板两端有高强螺栓孔,与边桁和中桁弦杆的横梁接头板栓接,其制作工艺流程为:
腹板
下盖板
1.横梁腹板采用数控切割下料,并保证外形尺寸,底边机加工,确保腹板高度;
2.横梁组装成T形,焊接并修整;
3.划线钻制盖腹板孔群;
4.组焊两侧加劲肋;
5.横梁打砂除锈、涂装后交成品。
3.7.2.3桥面板块拼装工艺
板单元先接宽再参与整体组装
在桥位现场布置两个板块接宽胎型,工厂制作完成的板块单元元运至现场后,先在胎型上接宽。
另外在现场布置桥面板预拼装组装胎架,每一轮按3个节间布置。
胎架为模拟弦杆设置定位装置,用以控制横梁位置。
为控制桥面板块的装配位置,在胎架上设置纵横基准线和基准点,同时胎架外设置独立的基线、基点,对胎架进行监控。
U肋拼接板采用配钻工艺。
其制作工艺流程为:
桥面板单元接宽
修整
定位桥面系横梁
整体组装
纵向用U肋定位样板
横向对正纵基线
焊接
修整
补涂装
留一块参与下次预拼
3.7.2.4精度管理系统
鉴于该桥桥面系连接的特殊性,建立下弦杆和桥面系的制作精度管理。
下弦杆横梁接头板在厂内钻孔后,应有专人全面测量各横梁接头孔至弦杆中心的距离、横梁接头至弦杆节点距离及各横梁接头之间距离,并做详细记录,待杆件发运时一并发往现场,作为是否配钻个别拼接板及调整模拟接头间距的依据;
4试拼装
为验证工艺方案的合理性,图纸及工艺文件的正确性,工艺装备及设备精度的可靠性,确保桥位架设顺利进行,按《铁路钢桥制作规范》要求对主桁杆件进行平面辗转试拼装,每次试拼装5个节间,长度为60m。
进行试拼装的结构包括:
边主桁、中主桁及桥门。
为了顺利完成桥门整体的试装,需要制作临时连接杆件,使杆件在自由状态下试拼装。
4.1试拼装目的
为了确保钢桁梁杆件的批量化生产,验证各杆件之间的相对组装关系,选择有代表性的构件进行试拼装,以确保批量杆件的整体精度满足架设的需要,减少现场高空作业难度和加快安装进度,使全桥钢桁梁和正交异性钢桥面顺利架设。
4.2试拼装操作程序
主桁杆件及桥门的试拼装在公司钢结构车间北跨完成。
具体操作程序如下:
a将试拼装台凳摆放到位,并进行全面检测;
b将首节间弦杆摆放在胎架上,调整上下弦杆中心距、对角线及平面度,满足规范要求;
c安装竖杆及斜杆,用安装螺栓及冲钉定位,检测上下弦杆中心距、对角线及平面度,调整至满足规范要求;
d重复以上程序完成全部杆件的试拼装;
e检测桁高、节间长度、旁弯、试拼装全长、拱度、平面度、对角线、主桁中心距、栓孔通过率等项点,合格后向监理工程师报验。
5焊接工艺方案
5.1典型焊缝的焊接工艺
5.1.1厂内对接焊缝的焊接
钢板的厂内对接均采用埋弧自动焊焊接,用MZ-1-1000埋弧自动焊机进行焊接,为了防止第一道焊漏,施焊前在对接焊缝的背面垫紫铜衬垫或焊剂垫,焊接过程中反面采用碳弧气刨清根,确保焊缝熔透;同时,在焊接过程中采用两面交替焊接,以减少焊后变形及焊残余应力。
5.1.2工型杆件的盖、腹的四条主焊缝的焊接
采用埋弧自动焊进行焊接,焊机采用瑞典伊萨公司产的埋弧自动焊焊接中心或MZ1-1000、MZ-1-1000焊机进行焊接。
严格控制四条焊缝的焊接方向一致,以防工件产生焊接扭曲变形。
为保证杆件焊后的直线度,对杆件焊接顺序如图6-1所示,对未开坡口焊缝,在船型位置进行焊接,以保证焊缝的外观尺寸和表面质量;对开坡口焊缝,在平角位置进行焊接,以保证焊缝的熔深。
图5-1工型杆件焊接顺序
5.1.3箱型杆件盖、腹板与纵肋的焊接
采用瑞典伊萨公司产的埋弧自动焊焊接中心或MZ1-1000焊机在船型位置先焊接端部坡口焊缝,待坡口基本填满后,通长进行纵肋贴角焊缝的焊接。
在焊接中严格控制两侧焊缝的焊接方向一致,以防纵肋产生焊接扭曲变形。
5.1.4箱型杆件的盖、腹板四条棱角焊缝的焊接
采用瑞典伊萨公司产的埋弧自动焊焊接中心或MZ-1-1000焊机施焊,焊接在平角位置进行,在焊接过程中随时调整焊丝的对正,以免焊偏。
当同一条焊缝中存在深浅不同的坡口时,将多道焊焊道的起、落弧部位留在焊缝表面,即在浅坡口填满后,焊深坡口时在浅坡口的焊缝上起、落弧,并超出不等厚对接焊缝交叉处100mm以上,多道焊缝焊完后将多焊焊道的起、落弧处的余高用砂轮磨去,使焊缝匀顺过渡,在焊接中严格控制四条焊缝的焊接方向一致。
5.1.5箱型杆件隔板焊缝的焊接
采用实芯焊丝CO2气体保护焊进行焊接。
箱型杆件隔板焊缝为隐蔽工程,为确保隔板的焊接质量,在封焊最后一块水平板组成箱体前,对已焊的其它箱型杆件隔板焊缝进行严格检查和修补,消除缺陷,修磨焊缝端部成平顺过渡。
5.1.6T型熔透角焊缝的焊接
接头板、节点板等处的T型熔透焊缝采用药芯焊丝CO2气体保护焊或焊条电弧焊进行焊接。
焊缝开双面K型坡口,施焊时先对坡口的一侧进行封底焊,用碳弧气刨清根、砂轮打磨后进行两面对成交替焊接,减少焊接变形,上弦节点板与平联节点板焊连的两端部位应打磨匀顺并加以锤击,提高结构的抗疲劳承载能力。
。
5.1.7T形横梁(T形节间横梁)的焊接
用埋弧自动焊MZ1-1000焊机施焊施焊,两条焊缝的焊接方向应一致,防止产生扭曲变形,对焊缝端部进行包头处理。
焊接完成后用型钢矫正机对T形肋进行矫正,保证T形肋的直线度、翼板和腹板的垂直度。
5.1.8桥面板块焊接
⑴U形肋焊接工艺。
用药芯焊丝CO2气体保护自动焊,焊接设备采用电源KR500型CO2半自动焊机配合CS-5型智能小车,为了控制焊接变形,板块的焊接制作专用的焊接反变形胎架,根据不同的板块宽度、厚度,横向设置反变形量,板块置于胎架上后周边用丝杠压紧后焊接。
焊接时端部采用手工电弧焊焊接,并且端部不断弧包角焊,焊后将包角部位用铣销工具打磨成半径不小于12mm的圆弧,减小应力集中,避免缺陷的产生。
⑵铁路T横肋与U形肋、面板焊接。
为了提高焊缝的抗疲劳能力,横位焊接T横肋与U形肋、面板处的焊缝时,在U肋拐角处不允许断弧,一次将切角焊封,对U肋与T横肋角焊缝的端部进行包角处理,并对成形不匀顺的地方进行修磨,提高结构的抗疲劳能力。
5.1.9主桁下弦杆顶板槽口焊缝焊接
对于主桁下弦杆节点板和桥面板焊连的开槽两端部位,下弦杆上水平板应按设计要求开槽,并且两侧均需开焊接坡口,能使节点板插入。
制造时熔透焊缝采用双面K型坡口,采用药芯焊丝CO2气体保护焊接进行焊接,在节点板插入槽口后,先焊平位熔透焊缝,在槽口端部用碳弧气刨将箱内侧槽口端部气刨坡口,使其焊缝由平位熔透焊缝过渡到横位熔透坡口,坡口过渡要匀顺,气刨后用砂轮或电铣修磨并将夹碳层去除,斜度不大于1:
5,然后焊接横位熔透焊缝。
如图6-2所示。
图5-2下弦杆顶板槽口坡口示意
5.2典型杆件的焊接
5.2.1中桁上弦杆的焊接
⑴焊接节点板与腹板不等厚对接焊缝,焊接时开不对称带钝边双U形或V形坡口,用埋弧自动焊进行焊接,焊后应按要求对余高进行修磨。
⑵焊接顶(底)板、腹板上的纵肋,采用瑞典伊萨公司产的埋弧自动焊焊接中心或MZ1-1000焊机在船型位置进行焊接,在焊接中两侧焊缝的焊接方向一致,以防纵肋产生焊接扭曲变形。
⑶在组装胎型上组装顶板单元、两腹板单元和隔板形成槽形,定位焊后用实芯焊丝CO2气体保护焊焊接隔板与顶板、腹板的角焊缝。
⑷组装弦杆底板单元,焊接箱形四条棱角焊缝,采用埋弧自动焊焊接中心在平位置进行焊接。
用实芯焊丝CO2气体保护焊焊接端隔板外侧焊缝和杆件两端1m范围内四条棱角焊缝内侧的贴角焊缝,在贴角焊缝与隔板相交的位置使焊缝匀顺过渡。
5.2.2中桁下弦杆的焊接
⑴焊接节点板与腹板不等厚对接焊缝,焊接时开不对称带钝边双U形或V形坡口,用埋弧自动焊进行焊接,焊后应按要求对余高进行修磨。
⑵焊接顶(底)板、腹板上的纵肋,采用埋弧自动焊焊接中心在船型位置进行焊接,在焊接中两侧焊缝的焊接方向一致,以防纵肋产生焊接扭曲变形。
⑶在主桁顶板上开孔(带双面K形坡口),将带节点板的腹板插入顶板开孔并定位,组装隔板。
采用实芯焊丝CO2气体保护焊焊接隔板焊缝,形成槽形。
采用药芯焊丝CO2气体保护焊平位焊接节点板与顶板熔透焊缝,先焊接箱内侧焊缝,并处理好平位熔透与横位熔透交接部位的焊缝。
⑷组装底板形成箱形,采用埋弧自动焊焊接四条棱角焊缝,在顶板开孔端部交界处焊缝坡口由腹板过渡到顶板,焊接操作时焊工手动调整焊丝位置,确保焊缝过渡匀顺和焊缝质量。
⑸横梁腹板焊接。
用药芯焊丝CO2气体保护焊横位焊接,焊接时先焊接大坡口侧,反面清根后在焊接小坡口侧确保熔透,焊接完成后对焊缝进行锤击以提高焊缝的抗疲劳承载能力。
5.2.3边桁上、下弦杆的焊接
该桥边桁为采用斜桁形式,是本桥的技术特点和制造难点,边桁弦杆杆件为平行四边形截面,平行四边形箱形杆件的水平板、竖板及节点板板端与板件斜交成75.9°,制造时模拟实桥空间位置,在保证斜交的板件端面加工成与连接面平行后再开坡口焊接,并严格控制组装的偏差。
⑴焊接节点板与腹板不等厚对接焊缝,焊接时开不对称带钝边双U形或V形坡口,用埋弧自动焊进行焊接,焊后应按要求对余高进行修磨。
⑵焊接顶(底)板、腹板的纵肋,均采用埋弧自动焊焊接中心在船位进行焊接,在焊接中两侧焊缝的焊接方向一致,以防纵肋产生焊接扭曲变形,值得注意的是焊接腹板上的纵肋时,因纵肋与腹板之间斜交关系,组装时预先给定反变形,先焊钝角侧前要将锐角侧码固,以控制焊接变形。
⑶在模拟节点板与顶底板之间斜交关系,然后在顶板槽口开双面K形坡口,将带节点板的腹板插入顶板开孔并定位,组装隔板。
采用实芯焊丝CO2气体保护焊焊接隔板焊缝,形成槽形。
采用药芯焊丝CO2气体保护焊平位焊接节点板与顶板熔透焊缝,先焊接箱内侧焊缝,并处理好平位熔透与横位熔透交接部位的焊缝。
⑷组装底板形成箱形,采用埋弧自