矩形上壳罩注射模具的设计.docx
《矩形上壳罩注射模具的设计.docx》由会员分享,可在线阅读,更多相关《矩形上壳罩注射模具的设计.docx(23页珍藏版)》请在冰豆网上搜索。
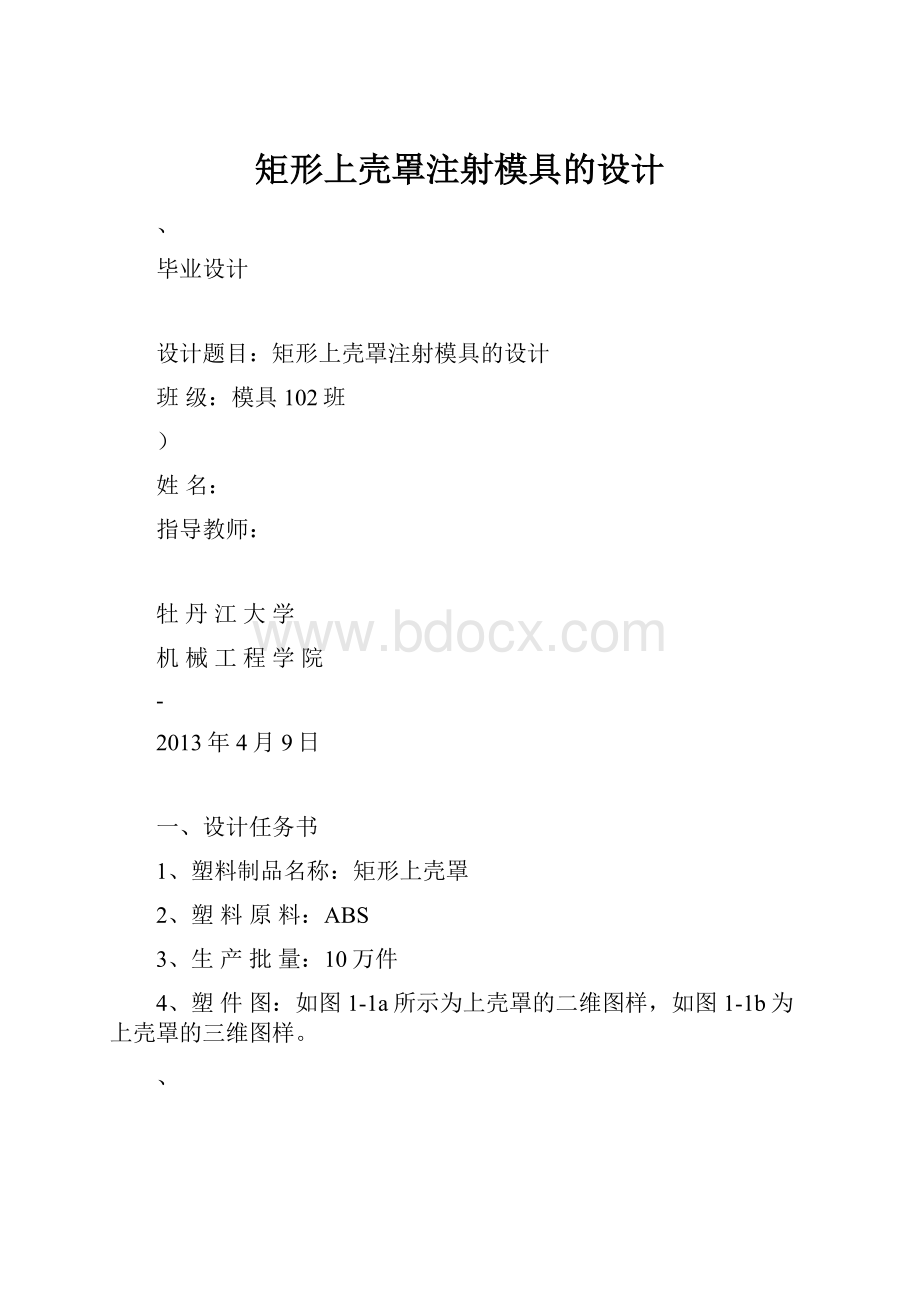
矩形上壳罩注射模具的设计
、
毕业设计
设计题目:
矩形上壳罩注射模具的设计
班级:
模具102班
)
姓名:
指导教师:
牡丹江大学
机械工程学院
-
2013年4月9日
一、设计任务书
1、塑料制品名称:
矩形上壳罩
2、塑料原料:
ABS
3、生产批量:
10万件
4、塑件图:
如图1-1a所示为上壳罩的二维图样,如图1-1b为上壳罩的三维图样。
、
图1-1a上壳罩的二维图样
,
图1-1b上壳罩的三维图样
二、塑件的结构工艺性分析:
1.塑件的成型特性:
ABS是聚苯乙烯的改性产品,是不透明非结晶型聚合物,无毒、无味,密度为-1.05gcm2。
ABS具有突出的力学性能,坚固、坚韧、坚硬;具有一定的化学稳定性和良好的介电性能;具有较好的尺寸稳定性,易于成型和机械加工,成型塑件表面有较好的光泽,经过调色可配成任何颜色,表面可镀铬。
其缺点是耐热性差,连续工作温度为70℃左右,热变形温度为93℃左右,但热变形比聚苯乙烯、聚氯乙烯、尼龙等都高;耐候性差,在紫外线作用下易变硬发脆。
ABS可采用注射、挤出、可延、吹塑、真空成型、电镀、焊接及表面涂饰等多种成型加工方法。
ABS成型性能如下:
(1)易吸水,成型加工前应进行干燥处理,表面光泽要求高的塑件应长时间预热干燥。
(2)流动性中等,溢边值为0.04mm左右。
(3)、
(4)壁厚和熔料温度对收缩率影响极小,塑件尺寸精度高。
(5)比热容低,塑化效率高,凝固也快,固成型周期短。
(6)表面粘度对剪切速率的依赖性很强,因此模具设计中大都采用点浇口形式。
(7)顶出力过大或机械加工时塑件表面会留下白色痕迹,脱模斜度易取2°以上。
(8)易产生熔接痕,模具设计时应注意尽量减少浇注系统对料流的阻力。
(9)易采用高料温、高模温、高注射压力成型。
在要求塑件精度高时模具温度可控制在50-60℃;而在强调塑件光泽和耐热性时,模具温度应控制在60-80℃。
2.塑件的结构工艺性分析:
(1)塑件的尺寸精度分析:
!
该需标注公差的尺寸有ø18±、2xø12+、30±,属于一般精度要求,其他尺寸均为未标注公差的自由尺寸,可按MT5查取公差。
表1-2所列为塑件主要尺寸的公差要求。
塑件主要尺寸的公差要求
表1-2
部位
尺寸
尺寸公差
部位
尺寸
~
尺寸公差
外形尺寸
120
孔尺寸
ø18
±
%
80
ø12
+
40
ø
+
20
孔间距尺寸
10
"
±
6
22
±
《
2
30
±
内形尺寸
38
+
48
±
76
+
84
…
±
116
+
,
(2)塑件的表面质量分析:
该塑件要求外观光洁、色彩艳丽,不允许有成型斑点和熔接痕,Ra为μm,而内表面无特殊要求。
(3)塑件的结构工艺性分析
1)从图纸上看,该塑件外形为四方壳罩,圆角过渡且无尖角存在,壁厚均匀,且符合最小壁厚要求。
2)塑件型腔较大,有尺寸不等的孔,如ø18、ø12、ø,它们均符合最小孔径要求。
3)内部有四个均布的加强肋,可增强塑件的强度,减小塑件的变形。
肋的侧壁设有1°左右的斜度,底部等处有的圆角过渡。
4)在塑件一侧有两个ø12的孔,另一侧内部有内凸,要考虑侧向分型抽芯装置。
5)为使塑件顺利脱模,可在塑件内部及加强肋处增设1°-2°的拔模斜度。
`
综上所述,该塑件可采用注射成型加工。
3.塑件的生产批量
该塑件产量达10万件,生产类型属于中等批量生产,可以考虑采用一模多腔、快速脱模以及成型周期不易太长的模具,同时模具造价要适当控制。
4.初选注射机
(1)计算塑件体积或重量
通过三维造型可获得矩形上壳罩的体积V=45.9cm3。
塑件的质量ω=ρV=47.3g。
ρ-ABS的密度
。
(2)确定型腔数量
由于该塑件两侧面分别有侧孔和内凸,加上塑件尺寸有一般精度要求,外表面有高光洁要求,不易采用太多型腔数目,所以考虑采用一模两腔,型腔平衡布置在型腔板两侧,以方便侧抽实现、浇口排列和模具的平衡。
(3)确定注射成型的工艺参数
根据该塑件的结构特点和ABS的成型性能,查有关资料初步确定塑件的注射成型工艺参数见表1-3
表1-3塑件的注射成型工艺参数
工艺参数
内容
工艺参数
"
内容
预热和干燥
温度80-90/℃
成型时间/s
注射时间
3-5
时间2h
保压时间
15-30
料筒温度/℃
后段
180-200
冷却时间
;
15-30
中段
210-230
总周期
40-70
%
前段
200-210
螺杆转速r/min
30-60
喷嘴温度/℃
180-190
后处理
方法
?
红外线灯烘箱
模具温度/℃
60-80
温度
104.06g
,
?
|
{
表1-5
【
塑件注射成型工艺卡
塑件注射成型工艺卡
资料编号
共页
】
第页
塑件名称
矩形上壳体
材料牌号
ABS
设备型号
SZY-300
装配图号
$
材料定额
每模件数
2件
零件图号
单件质量/g
/
工装号
材料干燥
设备
温度
80-90℃
时间
2h
?
料筒温度/℃
后段
180-200
中段
210-230
前段
200-210
喷嘴
180-190
~
模具温度/℃
60-80
时间/s
注射
3-5
—
保压
15-30
冷却
15-30
压力/Mpa
》
注射压力
70-90
背压
后处理
温度
}
红外线灯烘箱70℃
时间定额/min
辅助
时间
2-4h
、
单件
检验
编程
校对
审核
组长
[
车间主任
检验组长
主管工程师
.
三、分型面及浇注系统的设计
1、分型面的选择
为保证塑件能顺利分型,主分型面应首先考虑选择在塑件外形的最大轮廓处。
如图1-6所示,在满足该原则的三个方案中,方案A的塑件开模后留在定模一侧,塑件不易取出,顶出机构设计复杂;方案B的侧向抽芯滑块可安放在动模,实现侧抽机构简单,但会产生影响塑件外观的飞边,且飞边不易清除;方案C不但保证了塑件取出方便,且毛刺飞边的清除也较容易,因此选择方案C。
表1-6
;
2、浇注系统的设计
综合分析浇口易采用方便加工整修、凝料去除容易且不会在塑件外壁留下痕迹的侧浇口,模具采用单分型面结构两板模,模具制造成本比较容易控制在合理的范围内。
浇口系统的设计如图1-7所示.
图1-7
(1)主流道和定位圈的设计
由于主流道与注射机的高温喷嘴反复接触碰撞,所以要设计独立可拆卸更换的浇口套,且采用优质钢材制作,并经热处理提高硬度,定位圈与浇口套分开设计.如图1-8
图1-8
查资料得到SYZ-300型注射机与喷嘴的有关尺寸:
喷嘴前端球面半径SR0=12mm,喷嘴孔直径d0=4mm,定位圈直径为¢125mm。
为保证模具主流道与喷嘴的紧密接触,避免溢料,主流道与喷嘴的关系为:
SR=SR0+(1-2),d=d0+。
因此,取主流道球面半径SR=14mm,主流道的小端直径d=4.5mm。
$
为了便于将凝料从主流道中拔出,所以将主流道设计成圆锥形,其斜度为2°-4°,计算其大端直径约为¢10mm,为避免模内的高压塑料产生过大的反压力,配合段直径D不宜过大,取D=25mm;同时为了使熔料顺利进入分流道,在主流道出料端设计R2的圆弧过渡;为补偿在注射机喷嘴冲击力作用下浇口套的变形,将浇口套的长度设计的比模板厚度短0.02mm;浇口套外圆盘轴肩转角半径R宜大一些,取R=3mm,以免淬火开裂和应力集中。
查资料得SYZ-300型螺杆式注射机的定位圈直径为¢125mm,一般定位圈高出定模座板表面5-10mm。
(2)分流道的设计
该模具采用U形断面分流道,在一块模板上,切削加工容易实现,且比表面积不大,热量损失和阻力损失不太大,查有关经验表格得ABS上午分流道直径为¢-9.5mm,取¢8mm,据此,该模具的分流道设计如图1-9所示。
图1-9
(3)浇口的设计
图1-10
根据塑件的外观要求及型腔分布情况,选用如图1-10所示的侧浇口。
从塑件的底侧中部进料,去除凝料时不会在塑件的外壁留下浇口痕迹,不影响塑件的外观。
】
(4)冷料穴的设计
采用带Z形头拉料杆的冷料穴,如图1-11所示,将其设置在主流道的末端,既起到冷料穴的作用,又兼起开模分型时将凝料从主流道中拉出留在动模一侧,稍做侧向移动便可取出凝料的作用。
图1-11
四、模具设计方案论证
1、型腔设计
对于一模多件的模具型腔布置,在保证浇注系统分流道的流程短、模具结构紧凑、模具能正常工作的前提下,尽可能使模具型腔对称、均衡、取件方便。
本案例的模具采用一模两腔,型腔平衡布置在型腔板两侧。
2、成型零件的结构确定
该塑件的材料为ABS工程塑料,对表面粗糙度和精度的要求较高,因此要求成型零件有足够的强度、刚度、硬度和耐磨性,应选用优质模具钢制作,还应进行热处理以使其具备50-55HRC的硬度。
{
(1)凹模的设计
采用整体嵌入式凹模,放在定模板的一侧,主要是从节省优质模具钢材料、方便热处理,方便日后的更换维修等方面考虑的。
(2)凸模(型芯)设计
型芯结构设计也应采用组合式,可节省贵重模具钢,减少加工工作量。
成型塑件内壁的大型芯装在动模板上,成型24x¢、¢12孔的小型芯装在定模板上,方便型芯的制作安装、塑件的飞边去除以及塑件内部冷却水道的排布。
3、导向定位机构设计
由于塑件基本对称且无单向侧压力,所以采用直导柱导向便可满足合模导向及闭模后的定位。
4、推出机构设计
根据矩形上壳罩的形状特点,其推出机构可采用推件板推出或推杆推出。
其中推件板推出结构可靠、顶出力均匀,不影响塑件的外观质量,但制造困难,成本高;推杆推出结构简单,推出平稳可靠,虽然推出时会在塑件内部型腔上留下顶出痕迹,但不影响塑件外观,所以采用推杆推出机构。
—
5、抽芯机构的确定
塑件一侧还有两个侧孔,采用应用最为广泛的斜导柱侧向抽芯机构,结构简单、制造方便、动作可靠。
塑件另一侧的内凸所需抽拔力不大,抽芯距短,采用制造安装方便的圆柱形推杆内侧抽芯。
6、冷却系统设计
采用冷却水冷却,凹模冷却水道采用环绕型腔布置的两层式冷却回路,水道开设时注意避开安装在定模上的小型芯及侧向抽芯滑块;大型芯冷却采用隔板式管道冷却,在型芯上开设两个孔,孔内插上纵向隔板,与开在动模支撑板上的横向管路形成循环冷却回路,冷却通路的设计如图1-12.
冷却通路的设计
'
五、主要零部件的设计计算
1、成型零件的成型尺寸
该塑件的成型零件尺寸均按平均值法计算,查有关手册得ABS的收缩率为%%,故平均收缩率Scp=(+)%/2=%=,根据塑件尺寸公差要求,模具制造公差取δz=△/3,成型零件尺寸计算见表1-13。
(1)型腔侧壁厚度S的
成型零件尺寸计算
》
类别
模具零件名称
塑件尺寸
计算公式
工作尺寸
型腔计算
定模镶件
。
Lm=[(1+Scp)△]+δz0
+
+
Lm=[(1+Scp)△]+δz0
+
内镶块
Lm=[(1+Scp)△]+δz0
)
+
Lm=[(1+Scp)△]+δz0
+
。
20
+
型芯计算
大型芯
38+
Lm=[(1+Scp)Ls+△]0-δz
小型芯Ⅰ
¢+
Lm=[(1+Scp)Ls+△]0-δz
¢
)
侧型芯
¢12+
¢
小型芯Ⅱ
¢18±
&
¢
中心距计算
滑块
30±
Cm=(1+Scp)Cs±δz/2
±
)
22±
±
定模镶件
10±
±
48±
±
84±
±
2、模具型腔壁厚的确定
本模具的凹模采用的是整体嵌入式,因此可用整体式矩形型腔壁厚计算公式来确定型腔侧壁厚度S和型腔底板厚度T,如图1-14
l—型腔长度,取值120mm;b—型腔宽度,取值80mm;h—型腔深度,取值为40mm;T—型腔底板厚度,mm;S—型腔侧壁厚度,mm;L—模板长度,mm;B—模板宽度,mm。
(2)计算
1)按刚度条件计算
—
C----由h/L决定的系数查表9-22可得C=;
P----型腔内最大熔体压力,可取注射成型压力的25%-50%,P取30MPa;
h----型腔深度,h=40mm;
E----模具钢的弹性模量,一般中碳钢E=,预硬化塑料模具钢E=x105MPa;
[δ]-模具刚度计算许用变形量,查《机械零件设计手册》得[δ]=25i2=25xL1/5+
=25x1/5+=.
2)按强度条件计算
'
P---型腔内最大熔体压力,取P=30MPa;
h---型腔深度,h=40mm;
W---抗弯截面系数,由h/L决定,查《塑料成型工艺与模具设计》表的W=;
α---型腔的边长比,α=b/L=80/120=;
[σ]---模具强度计算许用应力,一般中碳钢[σ]=160MPa,预硬化塑料模具钢[σ]=300MPa。
(2)型腔底板厚度T的计算
1)按刚度条件计算
>
C′---由型腔边长比L/b决定的系数,查表的C′=;
P---型腔内最大熔体压力,可取注射成型压力的25%-50%,P取30MPa;
b---型腔宽度,b=80mm;
E---模具钢的弹性模量,一般中碳钢E=MPa,预硬化塑料模具钢E=MPa;
[δ]---模具刚度计算许用变形量,一般可通过查表得[δ]=25i2=25x5+=。
2)按强度条件计算
…
α′---由型腔长度与型腔宽度之比L/b所决定的系数,查本教材《塑料成型工艺与模具设计》表得α′=;
P---型腔内最大熔体压力,可取注射成型压力的25%-50%,P取30MPa;
b---型腔宽度,b=80mm;
[σ]---模具强度计算许用应力,一般中碳钢[σ]=160MPa,预硬化塑料模具钢[σ]=300MPa。
根据以上刚度、强度的计算,得出型腔的壁厚要求为:
型腔侧壁厚度S≥;型腔底板厚度T≥。
3、抽芯机构的设计计算
(1)抽芯距S的计算
S=h+(2-3)=2+3=5m
;
h----侧型芯成型部分高度,h=2mm
(2)抽芯力的计算
Fc=chp(μcos-sin)=°-sin0°)=
c---侧型芯成型部分截面平均周长,C=()d==37.68mm;
h---侧型芯成型部分高度,h为2mm;
p---塑件对型芯单位面积上的包紧力,一般模内冷却的塑件p为8-12Mpa,取10Mpa;
μ—塑料对模具钢的摩擦系数,μ为取;
---侧型芯的脱模斜度和倾斜角,该塑件为0°.
}
(3)确定斜导柱的倾斜角
该处的侧向抽芯距小,抽芯力不大,斜导柱的倾斜角取12°.
(4)确定斜导柱的直径
根据抽芯力Fc和斜导柱的倾斜角可查表得最大弯曲力Fw=1KN,然后根据Fw、和Hw(侧型芯滑块所受的脱模力作用线与斜导柱中心线的交点到斜导柱固定板的距离,该塑件为22mm),查表得斜导柱的直径d=10mm.
(5)斜导柱总长度计算
Lz=L1+L2+L3+L4+L5
=(d2/2)tan+h/cos+(d/2)tan+S/sin+(5-10)
=14/2tan12°+50/cos12°+10/2tan12°+5/sin12°+(5-10)
=++++(5-10)
=-87.72mm取Lz=85mm
Lz---斜导柱总长度;
d2---斜导柱固定部分大端直径;
h---斜导柱固定板的厚度;
d---斜导柱工作部分的直径;
S---抽芯距。
(6)确定楔紧块的′
由于滑块移动方向与合模方向垂直,故′=+(2°-3°)=14°-15°。
(7)确定滑块装置的定位距离
由于滑块移动方向与合模方向垂直,故滑块装置的定位距离S应等于实际抽芯距。
S=Lscos=(Lz-L1-L2-L3-L5)sin12°=6
Ls---斜导柱有效抽芯长度;
---斜导柱的倾斜角。
4、推出机构的设计
采用推杆推出机构,由于该塑件的脱模力不是太大,推杆的布置空间足够,所以无需用繁琐的计算方法确定推杆的尺寸大小,可以根据经验选取d=8mm的国标推杆,保证推出距离略大于型芯的突出长度2-3mm,即推出距离大于40mm。
5、标准模架的确定
综合考虑本塑件采用一模两腔平衡布置、侧浇口一次分型结构、型腔的壁厚要求、塑件尺寸大小、侧向抽芯机构、冷却水道的布置等多项因素,估计型腔模板的概略尺寸,查表选取标准模板的尺寸为315mmx400mmx63mm,选用A2型标准模架,标记为:
A2-315400-32-Z1(GB/T12555-2006)。
六、成型设备的校核计算
1、注射量的校核
在一个注射成型周期内,注射模具内所需的塑料熔体总量mi与模具浇注系统的容积和型腔容积有关,其值用下式计算:
mi=Nms+mj
N---型腔数量
ms—单个制品的质量或体积
mj---浇注系统和飞边所需的塑料质量或体积
已知N=2,ms=,经估算mj≈20cm3,则mi≈。
SZY-300型注射机的额定注射量为mI=320cm3,为使注射成型过程稳定可靠,应有
mi=()mI=32-256cm3
因此,该注射机的注射量满足模具的要求。
2、锁模力的校核
注射机锁模力的校核关系式为
F≧kpA
F---注射机锁模力,由表1-4可得SZY-300型螺杆式注射机的锁模力为1400kN;
k---压力损耗系数,一般取;
p---型腔内熔体的压力,本塑料p=30MPa;
A---塑件及浇注系统在分型面上的投影面积之和,本模具A=。
计算得:
F=故注射机的锁模力足够,满足锁模要求。
3、安装尺寸的校核
本模具采用的是A2-315400-30-ZI(GB/T12555-2006)的标准模架,模具的外形尺寸为400mmx400mm,模具闭合高度为H=100+A+B+C=100+63+50+100=313mm,查资料得SZY-300型注射机动、定模模板最大安装尺寸为520mmx620mm,允许模具的最小厚度Hmin=265mm,最大厚度Hmax=355mm,即模具的外形尺寸不超过注射机动、定模模板最大安装尺寸,模具闭合高度满足Hmin≦H≦Hmax的安装条件,故该模具满足SZY-300型螺杆式注射机的安装要求。
4、推出机构的校核
SZY-300型螺杆式注射机的推出形式为中心及上、下两侧设有推杆。
由于该模具推力不太大,在SZY-300型螺杆式注射机上采用中心¢50mm顶杆推出,在动模座板预留与之匹配的¢52mm顶出孔;塑件实际推出距离为55mm>(40+10)mm,满足推出距离要求。
5、开模行程的校核
注射机的开模行程是有限的,取出制品所需的开模距离必须小于注射机的最大开模距离,本模具为单分型面注射模具,SZY-300型螺杆式注射机的最大开模行程与模厚无关,校核关系式为
S>H1+H2+(5-10)
S---注射机的最大开模行程,由表1-4的SZY-300型螺杆式注射机的最大行程S=340mm;
H1---塑件脱模所需的推出距离,该塑件的脱模推出距离为55mm;
H2---塑件的高度(不包括浇注系统高度),该塑件的高度为40mm。
计算得
H1+H2+(5-10)=55+40+10=105mm
此外,由于侧抽芯距较短,无须通过增加开模距离来加大侧抽芯距,SZY-300型螺杆式注射机的开模行程足够。
以上分析证明,SZY-300型螺杆式注射机能满足要求,故可采用。
根据校核结论,将SZY-300型螺杆式注射机填入塑件的成型工艺卡中。
七、绘制模具装配图
模具装配图
总结:
在这次的毕业设计过程中,虽然遇到了很多问题,但通过多次的请教,动手实际操作,问题被一一解决,使自己的实际操作能力和知识的运用能力都得到了很大的进步,所以非常感谢我的指导教师和企业师傅。
通过这次设计使我认识到了cad软件运用和识图能力的重要性。
在今后的学习中我会不断加强软件与实际操作的综合运用,把知识与实践相结合,提高自己的创新能力和思维方向。
即将毕业的我,在今后的工作中难免还会再遇到一些意想不到的问题和麻烦,这时就要让自己学会运用以前所学的知识和积累的经验去解决它。
随着科学技术的高度发达,一些质量优、性能好、效率高、能耗低、价格低的产品将被开发出来,因此要求我们必须树立良好的设计思想,重视对自己进行机械设计能力的培养,增强设计方面的知识和努力。
综合运用好所学课程知识,加之我们平时的知识积累和老师的极大帮助和指导,为这次的毕业设计提供了有力的保障。
饮水平有限,设计中必然存在许多不足之处,还望老师批评指导。