淬火工艺.docx
《淬火工艺.docx》由会员分享,可在线阅读,更多相关《淬火工艺.docx(12页珍藏版)》请在冰豆网上搜索。
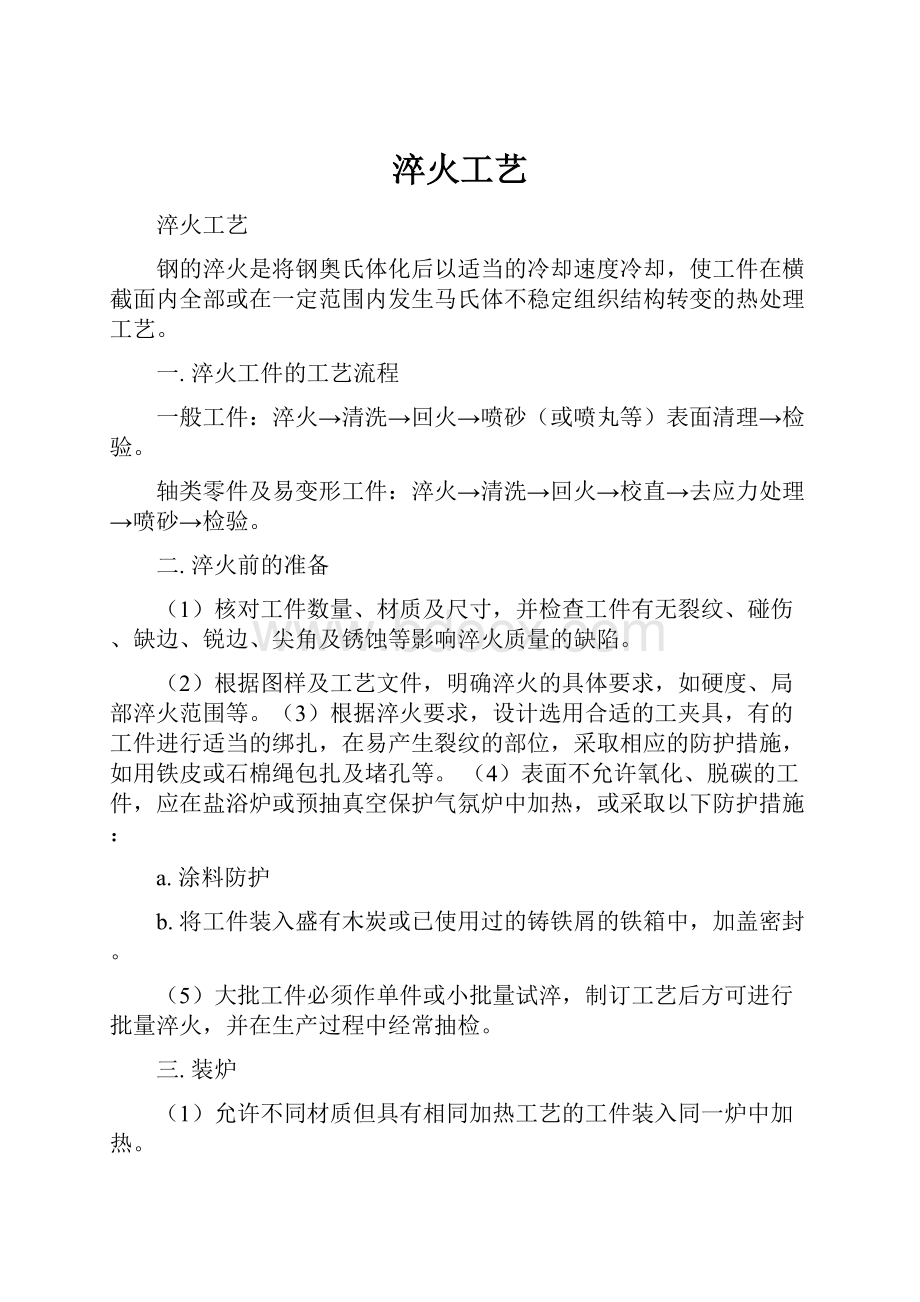
淬火工艺
淬火工艺
钢的淬火是将钢奥氏体化后以适当的冷却速度冷却,使工件在横截面内全部或在一定范围内发生马氏体不稳定组织结构转变的热处理工艺。
一.淬火工件的工艺流程
一般工件:
淬火→清洗→回火→喷砂(或喷丸等)表面清理→检验。
轴类零件及易变形工件:
淬火→清洗→回火→校直→去应力处理→喷砂→检验。
二.淬火前的准备
(1)核对工件数量、材质及尺寸,并检查工件有无裂纹、碰伤、缺边、锐边、尖角及锈蚀等影响淬火质量的缺陷。
(2)根据图样及工艺文件,明确淬火的具体要求,如硬度、局部淬火范围等。
(3)根据淬火要求,设计选用合适的工夹具,有的工件进行适当的绑扎,在易产生裂纹的部位,采取相应的防护措施,如用铁皮或石棉绳包扎及堵孔等。
(4)表面不允许氧化、脱碳的工件,应在盐浴炉或预抽真空保护气氛炉中加热,或采取以下防护措施:
a.涂料防护
b.将工件装入盛有木炭或已使用过的铸铁屑的铁箱中,加盖密封。
(5)大批工件必须作单件或小批量试淬,制订工艺后方可进行批量淬火,并在生产过程中经常抽检。
三.装炉
(1)允许不同材质但具有相同加热工艺的工件装入同一炉中加热。
(2)装炉工件均应干燥、不得有油污及其他脏物。
(3)截面大小不同的工件装入同一炉时,大件应放在炉膛后部,大、小工件分别计算保温时间。
(4)装炉时必须将工件有规律摆放在装炉架或炉底板上,用钩子、钳子或专用工具堆放,不得将工件直接抛入炉内,以免碰伤工件或损坏炉衬。
(5)细长工件必须在井式炉或盐炉中垂直吊挂加热,以减少变形。
(6)在箱式炉中装工件加热时,一般为单层排列,工件间隙10~30mm。
小件允许适当堆放,但保温时间应适当增加。
四.加热
1.加热方式
(1)碳钢及合金钢工件,一般可直接装入比规定的淬火温度高20~30℃的炉中加热。
(2)高碳高合金钢及形状复杂的工件应先预热。
2.加热温度选择。
3.工件加热时间的计算:
炉中的工件应在规定的加热温度范围内保持适当的时间,保证必要的组织转变和扩散。
加热时间是指从工件装入炉,通电加热起至出炉的整个加热过程保持的时间。
加热时间与工件的有效厚度、钢种、装炉方式、装炉量、装炉温度、炉的性能及密封程度等因素有关。
4.有效厚度的选择(同时适用于退火和正火工艺)
(1)圆棒形工件以直径计算。
(2)扁平工件以厚度计算(保温系数选取上限)。
(3)实心圆锥体按离大端1/3高度处的直径计算。
正火工艺
一.目的及应用
正火是将钢材或各种金属机械零件加热到临界点Ac3或Accm以上的适当温度,保温一定时间后在空气中冷却,得到珠光体基体组织的热处理工艺。
二.工艺规范
(1)常用钢号的正火加热温度及硬度值。
(2)正火保温时间的计算,可参照淬火工艺规程。
(3)正火工件的冷却一般为空冷,大件正火也可采用风机冷却、喷雾冷却等,以获得理想的效果。
三.操作要点
(1)正火温度工艺规范相近的工件,允许同炉处理。
(2)对表面质量要求高的工件加热应采取防止氧化或脱碳的气体保护措施。
(3)工件一般采用工作温度或稍高于工作温度装炉。
若互相重叠装料,应相应延长保温时间1/4。
(4)工件应均匀放置在炉膛有效工作区里。
(5)工件出炉后,应散开放置在干燥处空冷,不得将工件堆积,不得放在潮湿处。
回火工艺
退火工艺
退火是将钢材或各种金属机械零件加热到适当温度,保温一段时间,然后缓慢冷却,可以获得接近平衡状态组织的热处理工艺。
在机械制造行业,退火通常作为工件制造加工过程中的预备热处理工序。
一.完全退火
完全退火是将钢件或各种机械零件加热到临界点Ac3以上的适当温度、在炉内保温缓慢逐渐冷却的工艺方法。
其目的是为了细化组织、降低硬度、改善机械切削加工性能及去除内应力。
完全退火适用于中碳钢和中碳合金钢的铸钢件、焊接件、轧制件等。
完全退火工艺曲线见图。
3.工件装炉:
一般中、小件均可直接装入退火温度的炉内,亦可低温装炉,随炉升温。
4.保温时间:
保温时间是指从炉子仪表到达规定退火加热温度开始计算至工件在炉内停止
加热开始降温时的全部时间。
工件堆装时,主要根据装炉情况估定,一般取2~3h。
5.工件冷却:
保温完成后,一般停电(火),停止加热,关闭炉门逐渐缓冷至500℃即可出炉空冷。
对某些合金元素含量较高、按上述方式冷却后硬度仍然偏高的工件,可采用等温冷却方法,即在650℃附近保温2~4h后再炉冷至500℃。
二.去应力退火
去应力退火是将工件加热到Ac1以下的适当温度,保温一定时间后逐渐缓慢冷却的工艺方法。
其目的是为了去除由于机械加工、变形加工、铸造、锻造、热处理以及焊接后等产生的残余应力。
1.去应力退火工艺曲线见图1-3。
2.不同的工件去应力退火工艺参数见表C。
3.去应力退火的温度,一般应比最后一次回火温度低20~30℃,以免降低硬度及力学性能。
4.对薄壁工件、易变形的焊接件,退火温度应低于下限。
5.低温时效用于工件的半加工之后(如粗加工或第一次精加工之后),一般采用较低的温度。
表C去应力退火工艺及低温时效工艺
类别
加热速度
加热温度
保温时间/h
冷却速度
焊接件
≤300℃装炉
≤100~150℃/h
500-550
2-4
炉冷至300℃出炉空冷
消除加工应力
到温装炉
400-550
2-4
炉冷或空冷
高精轴套、镗杆(38CrMoAlA)
≤200℃装炉≤80℃/h
600-650
10-12
炉冷至200℃出炉(在350℃以上冷速≤50℃/h)
精密丝杠(T10)
≤200℃装炉≤80℃/h
550-600
10-12
炉冷至200℃出炉(在350℃以上冷速≤50℃/h)
主轴、一般丝杠
(45、40Cr)
随炉升温
550-600
6-8
炉冷至200℃出炉
量检具、精密丝杠(T8、T10、CrMn、GCr15)
随炉升温
130-180
12-16
空冷(时效最好在油浴中进行)
化学热处理工艺
渗碳、渗氮、碳氮共渗
渗碳是为了增加钢件表层的含碳量和一定的碳浓度梯度,将钢件在渗碳介质中加热并保温使碳原子渗入钢件表层的化学热处理工艺称为渗碳,渗碳钢一般采用普通碳钢、优质碳素结构钢和低碳合金结构钢,也可采用Q235钢。
开炉前的准备:
(1)渗碳工件表面不应有锈蚀、污垢、裂纹及伤痕等缺陷。
(2)工件表面不需渗碳部分可采用表面镀铜或涂防渗碳涂料防止渗碳,也可在渗碳后,对不需要渗碳的部分切削去渗碳层。
镀铜层的厚度一般应大于0.03mm;防渗碳涂料的厚度一般应大于0.3mm,要求涂层致密。
(3)采用滴注式渗碳时,渗碳剂一般是甲醇(形成载气);煤油或丙酮、醋酸乙酯(形成富化气),有条件时也可以采用其他方式的可控气氛渗碳。
为取得高质量渗碳,减少碳黑,最好选用航空煤油滴注。
(4)准备好试样和中间试样。
试样宜取自同批零件,试样表面不允许有锈蚀、油污。
中间试样一般为Φ10mm×10钢试棒。
渗碳操作:
①开炉前检查设备(参照井式气体渗碳炉操作规程)
②根据停炉时间和炉罐情况,按工艺文件规定,进行炉罐渗碳。
炉罐渗碳时间,对于新炉罐一般为6-12h,对于旧炉罐一般为2-4h左右。
③装炉:
a.将材质相同、渗碳层技术要求相同、渗碳后热处理方式相同的工件,放在同一炉生产。
试样放在料筐的有代表性的位置。
每炉装载量和装料高度应小于设备规定的最大装载量和装料高度。
b.为保证炉内渗碳气氛的循环畅通,使渗碳层均匀,工件间应留有纵横大于5mm的间隙。
c.料筐装入炉内时,要垂直摆放,各层料筐应齐整,不得有间隙,同时悬吊放入中间试样棒。
d.工件入炉后,将炉盖盖紧,不允许有漏气现象,滴入渗碳剂后,应保持炉内压力为196-490Pa。
将废气点燃,火苗高度为200-300mm。
④渗碳
a.渗碳工艺曲线:
根据材质及渗碳层显微组织的要求,由有关工艺文件规定渗碳工艺曲线,一般对于要求严格控制碳化物的低合钢钢工件,可参考工艺曲线图;对于不要求严格控制碳化物的低碳钢、低合金钢工件,可参考工艺曲线图
关于渗碳工艺曲线说明如下:
赶气:
其目的是赶走炉内空气,使炉内空气恢复到工艺规定的碳势气氛。
保温:
其目的是使炉内工件温度均匀。
保温时间一般是40min到1h。
渗碳温度和渗碳时间:
渗碳温度一般为900~940℃,渗碳时间应根据要求的渗碳层深度确定,它与渗碳温度、炉内气氛的碳势及工件特征等因素有关。
渗碳剂的选择及应用:
采用滴注式渗碳时,可根据生产厂条件选择渗碳剂。
选用普通煤油作渗碳剂,炉内碳黑较多。
选用航空煤油,不易产生碳黑,甲醇作载气,煤油作富化气,炉内碳黑较少。
用甲醇作载气,丙酮或醋酸乙醋作富化气,炉内碳黑则更少,可进行气氛的碳势控制。
渗碳剂用量根据工件装载量和表面积大小等因素进行调整。
渗氮
渗氮的常见缺陷
一、硬度偏低
生产实践中,工件渗氮(软氮化)后其表面硬度有时达不到工艺规定的要求,轻者可以返工,重者则造成报废。
造成硬度偏低的原因是多方面的:
设备方面:
如系统漏气造成氧化;
材料:
如材料选择欠佳;
前期热处理:
如基体硬度太低,表面脱碳严重等;
预先处理:
如进炉前的清洁方式及清洁度。
工艺方面:
如渗氮(软氮化)温度过高或过低,时间短或氮势不足等等。
所以具体情况要具体分析,找准原因,解决问题。
二、硬度和渗层不均匀
装炉方式不当;
气压调节不当;
温度不均;
炉内气流不合理。
三、变形过大
变形是难以杜绝的,对易变形件,采取以下措施,有利于减小变形:
渗氮(软氮化)前应进行稳定化处理;
渗氮(软氮化)过程中的升、降温速度应缓慢;
保温阶段尽量使工件各处的温度均匀一致。
对变形要求严格的工件,如果工艺许可,尽可能采用较低的氮化(软氮化)温度。
四、处观质量差
渗氮(软氮化)件出炉后首先用肉眼检查外观质量,钢件经渗氮(软氮化)处理后表面通常呈银灰(蓝黑色)色或暗灰色(蓝黑色),不同材质的工件,氮化(软氮化)后其表面颜色略有区别,钛及钛合金件表面应呈金黄色。
五、脉状氮化物
氮化(特别是离子氮化)易出现脉状氮化物,即扩散层与表面平行走向呈白色波纹状的氮化物。
其形成机理尚无定论,一般认为与合金元素在晶界偏聚及氮原子的扩散有关。
因此,控制合金元素偏聚的措施均有利于减轻脉状氮化物的形成。
工艺参数方面,渗氮温度越高,保温时间越长,越易促进脉状组织的形成,如工件的棱角处,因渗氮温度相对较高,脉状组织比其它部位严重得多。
感应加热工艺
高频感应加热原理
用交流电流流向被卷曲成环状的导体(通常为铜管),由此产生磁束,将金属放置其中,磁束就会贯通金属体,在与磁束自缴的方向产生窝电流(旋转电流)……感应作用此时,由于金属内的电阻产生焦耳热(1平方R),使温度上升,这就是感应加热。
由此,对金属等被加热物体,在非接触的状态下就能加热。
(发热有焦耳热及磁滞损失产生的热,但主要有焦耳热引起的。
)
中频感应加热原理
应用电磁感应原理,置工件于交流磁场中,产生涡流损耗而发热,达到熔炼、透热、淬火等加热的要求。
这种加热方式,具有加热快、烧损少、劳动强度低,能保证产品质量和易于组织自动生产线等优点
热处理工艺模拟
加热炉炉壁温度模拟(使用MARC软件模拟)
工件冷却过程模拟(使用ANSYS软件模拟)
大型井式渗碳炉炉气模拟(物理模拟装置)
典型工件热处理工艺举例
铝合金轮毂热处理炉加工工艺曲线图:
常用齿轮钢材的调质热处理工艺
钢号
淬火温度
(℃)
硬度要求(HR)
有无回火脆性
回火温度(℃)
180~220
220~260
260~300
35
850~870水淬
550~570
540~560
-
无
40
840~860水淬
560~580
550~570
-
无
45
830~850水淬
570~590
560~580
-
无
50
820~840水淬
600~620
570~590
510~530
无
55
810~830水淬
-
590~610
530~550
无
40Cr
840~860水淬
-
590~610
560~580
有
50Cr
830~850油淬
-
580~600
550~570
有
55Cr
820~840油淬
-
590~610
560~580
有
35CrMo
850~870油淬
-
580~600
540~560
无
35SiMn
860~880油淬
-
580~600
540~560
无
34CrMoA
850~870油淬
-
610~630
570~590
无
42CrMo
840~860油淬
-
590~610
550~570
无
42SiMn
840~860油淬
-
590~610
550~570
有
40CrSi
850~870油淬
-
670~690
620~640
有
40CrNi
850~870油淬
-
590~610
560~580
有
38CrMnMo
850~870油淬
-
670~690
650~670
有
38CrSiMnMo
850~870油淬
-
680~700
660~680
有
35Cr2MnMo
860~880油淬
-
620~640
600~620
有
37SiMn2MoV
860~880油淬
-
670~690
650~670
稍有