注塑件通用技术条件.docx
《注塑件通用技术条件.docx》由会员分享,可在线阅读,更多相关《注塑件通用技术条件.docx(17页珍藏版)》请在冰豆网上搜索。
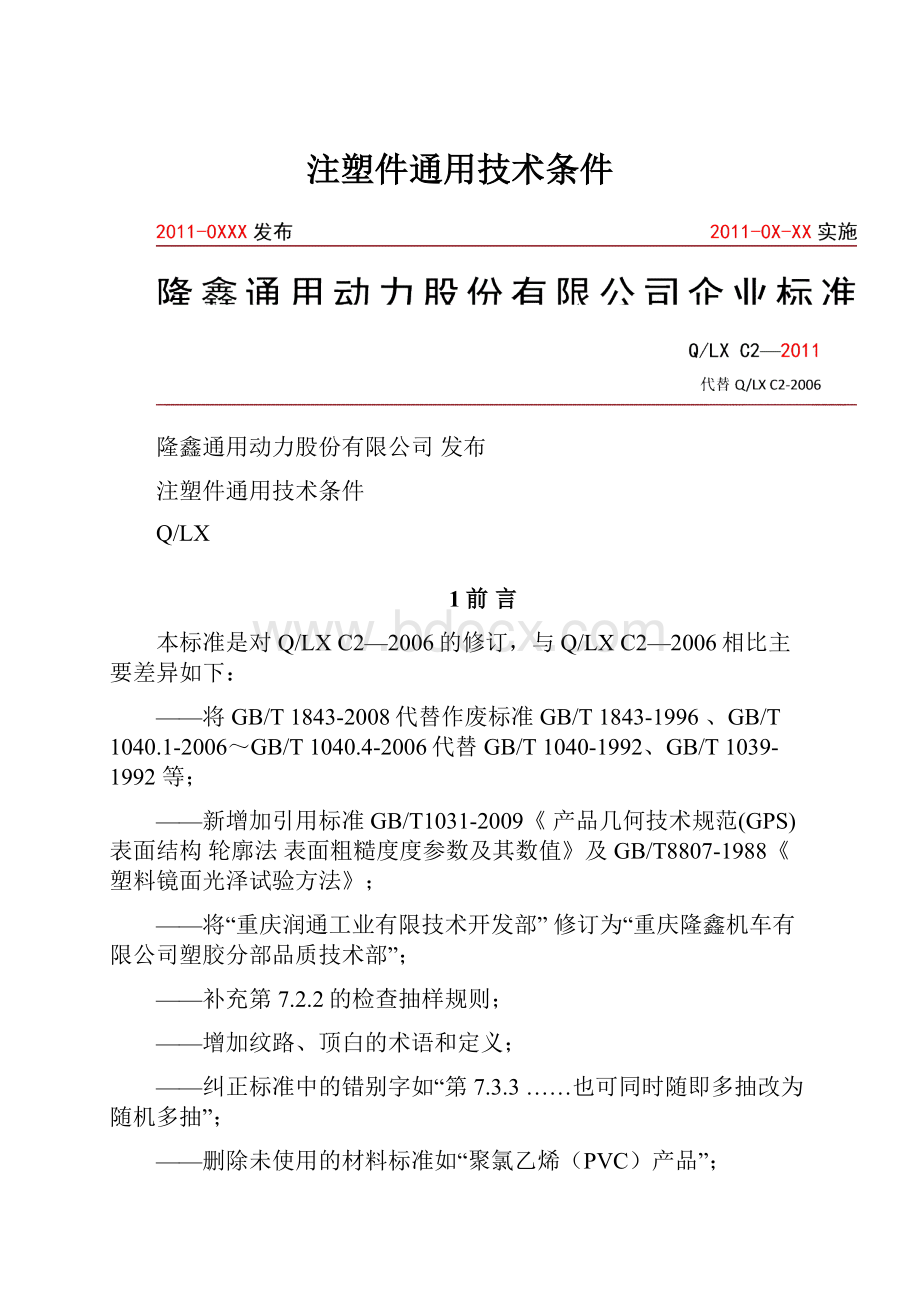
注塑件通用技术条件
隆鑫通用动力股份有限公司发布
注塑件通用技术条件
Q/LX
1前言
本标准是对Q/LXC2—2006的修订,与Q/LXC2—2006相比主要差异如下:
——将GB/T1843-2008代替作废标准GB/T1843-1996、GB/T1040.1-2006~GB/T1040.4-2006代替GB/T1040-1992、GB/T1039-1992等;
——新增加引用标准GB/T1031-2009《产品几何技术规范(GPS)表面结构轮廓法表面粗糙度度参数及其数值》及GB/T8807-1988《塑料镜面光泽试验方法》;
——将“重庆润通工业有限技术开发部”修订为“重庆隆鑫机车有限公司塑胶分部品质技术部”;
——补充第7.2.2的检查抽样规则;
——增加纹路、顶白的术语和定义;
——纠正标准中的错别字如“第7.3.3……也可同时随即多抽改为随机多抽”;
——删除未使用的材料标准如“聚氯乙烯(PVC)产品”;
——删除标准内光亮度要求,因白坯制件的光泽度都是烤漆后作要求;
——删除制件应具有光泽,同批产品色泽应一致不允许有色差,因为喷砂、皮纹处理的目的是用亚光或隐去光泽,该条要求是矛盾的。
本标准实施的过渡要求:
对于本标准实施前已经做完实验的注塑产品,对照本标准相应规定如有不符,给予6个月的过渡期。
本标准由隆鑫通用动力股份有限公司提出。
本标准由隆鑫通用动力股份有限公司技术中心管理部规格管理室归口。
本标准由重庆隆鑫机车有限公司塑胶分部品质技术部起草。
本标准主要起草人:
刘琼
本标准审核人:
程光敏
本标准批准人:
何军
本标准所代替标准版本的历次发布情况为:
——Q/LXC2—2006
注塑件通用技术条件
11 范围
本标准规定了摩托车注塑产品的术语和定义、要求、试验方法、检验规则、标志、包装、运输、贮存等。
本标准适用于重庆隆鑫机车有限公司塑胶分部生产的摩托车注塑产品。
12 规范性引用文件
下列文件对于本文件的应用是必不可少的。
凡是注日期的引用文件,仅注日期有版本适用于本文件。
凡是不注日期的引用文件其最新版本(包括所有的修改单)适用于本标准。
GB/T191-2008包装储存运图示标志
GB/T1033-1986塑料密度和相对密度试验方法塑料非泡沫塑料密度的测定第1部分:
浸渍法、液体比重瓶法和滴定法塑料非泡沫塑料密度的测定第1部分:
浸渍法、液体比重瓶法和滴定法
GB/T1040.1-2006~GB/T1040.4-2006塑料拉伸性能的测定
GB/T1634-2004塑料弯曲负载热变形温度(简称热变形温度)试验方法
GB/T1634.1~1634.3-2004《塑料负荷变形温度的测定》
GB/T1843-2008塑料悬臂梁冲击试验方法
GB/T2408-2008塑料燃烧性能试验方法水平法和垂直法
GB/T2411-2008塑料和硬橡胶 使用硬度计测定压痕硬度(邵氏硬度)
GB/T2828.1-2003计数抽样检验程序第1部分:
按接收质量限(AQL)检索的逐批检验抽样计划
GB/T9341-2008塑料弯曲性能试验方法
GB/T8807-1988塑料镜面光泽试验方法
GB/T3398.2-2008塑料硬度测定第2部分洛氏硬度
GB131-2006产品几何技术规范(GPS)技术产品文件中表面结构的表示法
Q/LXC1-2011覆盖件注塑材料
13 术语和定义
下列术语和定义适用于本标准。
13.1 缺料
由于注塑量填充不足,造成制件局部不完整或不饱满。
13.2 尺寸不稳定
主要由于模具强度不良,精度不高,注塑机工作液压、温度控制不稳定和塑料成形条件不稳定等原因,使制件密度变化引起的尺寸变化。
13.3 气泡
由于熔料充气过多或排气不良而导致塑件内残留气体,并呈现体积较小或成片的空穴。
注:
塑料收缩、材料分解或抗静电等添加剂分解产生气体,预料背压过低,流道不畅流等原因易产生气泡。
13.4 缩痕
由于保压补缩不良,塑件冷却不匀,壁厚不匀及塑料收缩率大,容易在远离浇口,且壁厚的地方出现,如加强筋、支柱等地方常易发生;收缩性较大的结晶性塑料更易发生。
13.5 飞边
由于合模锁模力过低,注塑压力过大,模具配合间隙过大,模具强度不好,料温过高,塑料流动性好,加料过多使塑件沿边缘出现多余薄翅。
13.6 熔接缝
由于熔料分流汇合时料温下降,树脂与附合物不相溶等原因,使熔料汇合处熔接不良,沿塑件表面及内部产生明显的细接缝线。
注:
如熔融塑料在型腔中由于遇到嵌件、孔洞(包括栅格)等流动不连贯的区域,充模料流停顿而以多股形式汇合的区域;此外在发生浇口喷射充模时也会生成熔接缝,喷射时,熔体直接射入模腔直到撞到对面的模壁,随后而来的熔料产生压缩使料流折迭,于是在折合相遇的地方形成熔接终缝。
13.7 银丝斑纹
由于料内水分或充气,挥发物过多,预塑背压力不足,空气混入,熔料受剪切作用过大,熔料与模具表面密合不良,或急速冷却或混入异料或分解变质,而使塑料表面沿料流方向出现银白色光泽的针状条纹或云母状斑纹。
13.8 翘曲变形
由于成形时残余应力,壁厚不均造成收缩应力,如剪切应力,冷却应力等。
脱模不良,冷却定形时间不足,塑件强度不足,模具变形等原因,均会使塑件发生畸变,翘曲不平和型孔偏移等现象。
13.9 黑点、黑条
由于塑料分解或料中可燃性挥发物、空气等在高温、高压下分解燃烧,燃烧物随熔料注入型腔,或原料型腔排气不良、清洁度差、杂物混入,在塑件表面呈炭状烧伤现象。
13.10 喷射痕
在制品上浇口附近出现如蚯蚓状的流线,只有在模具为侧式浇口(边缘浇口)时出现。
13.11 剥离
不同种类的材料和杂物混入,制品象云母那样发生层状剥离现象,其原因是勉强地把不相容的材料混炼在一起等。
13.12 龟裂
由于成型温度过低,塑化不良,注射压力过大,分子链在应力作用下沿受力的方向上排列不好产生裂纹,经过退火可以恢复。
注:
如当脱模顶出力不平衡时,或脱模腔造成很大真空吸力会引起龟裂;或制品涂漆时,由于涂料中溶剂的作用对具有残余应力的制品表面也会引起龟裂。
可采用提高熔体温度和模具温度使熔体处于较好的流动状态以降低注射压力,使分子链处于自然排列整齐状态的工艺方法消除内应力。
13.13 冷斑
射嘴的冷料或模具上夹的冷料,注射时在产品中产生的不相熔斑块。
13.14 气痕
由于模具厚薄不均,排气不良(注射成型时,厚的地方流速快,薄的地方流速慢,于是在薄的地方形成空穴使气体无法排除)在制件的表面形成的流纹。
13.15 纹路
物体上面的皱痕或花纹
13.16 顶白
顶出时所需脱模力较大,顶针不够力,使产品局部被顶坏,从产品正面看,有明显的白色或胶位高出的现象称为顶白,也可称之为顶高水口。
14 产品分类
注塑产品按采用材料分为:
1——聚丙稀(PP)产品;
2——丙烯腈一丁二烯一苯乙烯(ABS)产品;
3——尼龙(PA6)产品;
4——聚碳酸脂(PC)产品等。
15 要求
15.1 原材料要求
原料要求应符合Q/LXC1的规定。
15.2 塑料白坯的要求
完整性要求
a)参照样件,制件应完整、饱满,有无缺料现象;
b)定位支撑,定位柱、装配支耳、加强筋等细长件应无断裂;
c)应无因压力过大或其它原因而导致的装配孔、装配槽的封闭;
d)制件应无因脱模而拉伤破裂、破损,无顶白、顶冒现象,无因模具损伤而出现多料现象。
表观质量要求
制件的表观质量主要指制件主视面、侧面、背面的质量。
主视面
主视面即制件装于摩托车上,用阳光或灯光随意照射,直接着光的表面;或者肉眼随意观察,直接观察到的表面。
主视面不允许有气泡、银丝、斑纹、黑点、拉丝、冷斑、流痕、划痕、凹凸小圆点(即砂眼),缩水和熔接痕应尽量减到最低限度。
熔接痕允许存在的范围:
a)熔接缝的宽度d<(0.04~0.06)mm,长度L按以下几种情况确定:
5——物料遇两阻碍物后的汇合处:
熔接缝与阻碍物的大小,离浇口的远近和原材料的流动性有关。
考虑以上因素,距浇口距离大于100mm,每增加10mm,熔接缝L可增加1mm~2mm。
即:
L<50mm。
6——物料遇一阻碍物后的合熔处,距浇口距离大于100mm每增加10mm,熔接缝L可增加1mm~2mm。
即:
L<50mm。
7——物料由两浇口注射后的合熔的熔接缝与两进浇口的距离有关,两浇口距离大于100mm,每增加10mm,熔接缝L可增加1~2mm。
即:
L<50mm。
b)其余的熔接缝应小于30mm~50mm。
所有情况的熔接缝都应通过工艺调整和模具整改达到最低限度,由于客观原因确实无法消除时,长度不得超过50mm。
主视面缩水处的最低点与整个制件圆滑平面或弧面的距离应小于0.3mm,表面粗糙度Ra0.2um(按GB/T131-2006的默认规则,下同)。
纹路d<(0.04~0.06)mm,长度L<(30~50)mm,且整个平面分布在1~2条之内。
表面不得有油污,轻微的表面污染须用棉纱擦试干净,必要时用乙醇等有机溶剂进行清洗。
侧面
制件外观面,制件装于摩托车上,用阳光或灯光随意照射,不能直接着光的面,也称阴面。
有的制件表面在摩托车上整体处于该状态,其表观质量均按侧面的要求考核。
侧表面不允许有气泡、冷斑,色斑杂质面积小于0.5mm2,
分散度不大于2个/100mm2,每件制品不多于3个;
整个表面不多于5点的细小针状银丝,须用800号以上的水砂砂去并保持制件的光亮平滑。
缩水处最低点与整个圆滑平面或弧面的距离不大于0.5mm。
熔接缝的宽度d<(0.06~0.08)mm,长度按以下几种情况确定:
8——物料遇两阻碍物后的汇合处:
熔接缝与阻碍物的大小、离浇口的远近和原材料的流动性有关。
考虑以上因素,距浇口距离大于100mm,每增加10mm,熔接缝L可增加2mm~3mm。
即:
L<50mm;
9——物料遇一阻碍物后的合熔处,距浇口距离大于100mm每增加10mm,熔接缝L可增加2mm~3mm。
即:
L<50mm;
10——物料由两浇口注射后的合熔处与两进浇口的距离有关,两浇口距离大于100mm,每增加10mm熔接缝L可增加2mm~3mm。
即:
L<50mm;
11——非上述原因的熔接缝小于(40~60)mm。
12——所有情况的熔接缝都应通过工艺调整和模具整改达到最低限度,确实无法消除或限制时长度不得超过60mm。
整个表面粗糙度Ra0.4um以下。
纹路d<(0.06~0.08)mm,L<(40~60)mm,且整个平面分布在2~3条之内;
表面不得有油污,轻微的污染须用棉纱擦试干净;
浇口处有细小的拉丝须用800号以上水砂砂掉,无明显的流痕、冷斑,细小的凹凸小圆点也必须砂掉。
允许存在轻微顶白,但顶白处不高于制件表面。
背面
背面即制件装于摩托车上,无论用什么方式均不能被观察到的表面,有的制件,整体处于不能被观察到的状态,其表观质量均按背面的要求考核。
a)不允许有气泡、冷斑;
b)其缩水处最低点与整个圆滑平面或弧面的距离应不超过0.8mm,熔接痕的长度不能超过制件宽度的三分之一;
c)细小的银丝须用800号以上水砂砂掉,不允许存在成片的银丝;
d)表面粗糙度Ra1.6μm以下。
1注:
5.2条中“d”表示宽度,“L”表示长度。
15.3 塑料有色坯的要求
有色坯即在本色塑料原料中按要求加入一定的色母料,经注射成型,但表面仍需喷漆的坯子。
其目的是使制件喷漆后不透明,制件表面所喷涂漆的颜色一般与色母料的颜色相同或相近。
制件完整性要求
a)制件外形尺寸和装配尺寸应与样件相符;
b)制件应完整、饱满、无翘曲、变形、缺料现象;
c)定位支撑、定位柱、装配支耳、加强筋等细长件应无断裂;
d)应无因压力过大或其它原因而导致的装配孔、槽封闭;
e)应无因脱模而拉伤破裂、破损,无顶白、顶冒现象,无因模具损伤而出现多料现象。
制件外观质量的要求
主视面
a)表面不允许有气泡、银丝、拉丝、冷斑;
b)产品允许存在色差,但制件表面色差分布总体均匀,色类相同,不能深浅不一;
c)允许存在的斑点须与制件色母料的颜色一致或相仿,且斑点面积在0.5mm2以下;
d)缩水处的最低点与整个饱满制件的圆滑平面或弧面的距离应不超过0.3mm;
e)熔接缝宽度d<(0.04~0.06)mm,并应通过工艺调整和模具整改达到最低限度,确实无法消除或限制时,长度L<(30~50)mm;
f)表面不得有油污,轻微的污染须用棉纱擦试干净;
g)表面粗糙度Ra0.2μm以下。
侧面
a)表面不允许有气泡、冷斑;
b)细小的针状银丝,在制件整个表面不应多于5点,可用800#以上的水砂砂去并保持制件的光亮平滑;
c)色斑杂质表面积小于1.0mm2,分散度不大于2个/100mm2,且每件制品不超过3个;
d)缩水处最低点与整个圆滑平面或弧面的距离应不超过0.5mm,熔接缝的宽度d<(0.06~0.08)mm,长度小于(40~60)mm;
e)纹路宽度d<(0.06~0.08)mm,L<(40~60)mm,且整个平面分布在2~3条之内;
f)表面不得有油污,轻微的污染须用棉纱擦试干净,浇口处有细小的拉丝须用800号以上的水砂砂掉,允许存在轻微顶白,但顶白处不高于制件表面;
g)表面粗糙度Ra0.4μm以下。
背面
a)其表面不允许存在气泡、冷斑、成片的银丝,细小的银丝须用800号以上的水砂砂去;
b)其缩水处最低点与整个圆滑平面或弧面的距离应不超过1mm,熔接缝长度不超过制件总长的三分之一;
c)表面粗糙度Ra1.6μm以下。
15.4 其它注塑件(包括不需喷漆,直接使用的注塑件)的要求
完整性要求
a)参照样件,制件的外形尺寸和装配尺寸应与样件相符;
b)制件应完整、饱满、无翘曲、变形、缺料现象;
c)定位支撑、定位柱、装配支耳、加强筋处等细长件应无断裂;
d)装配孔、槽应无封闭,制件应无因脱模而拉伤破裂、破损,无顶白、顶冒现象,无因模具损伤而出现的多料现象。
表观质量要求
不需喷漆、直接使用于表面的注塑件
a)主视面
13——主视面表面不允许有气泡、流痕、花纹、银丝、划痕;
14——缩水处最低点与整个圆滑平面或弧面的距离应不超过0.5mm;
15——熔接缝宽度d<(0.04~0.06)mm,长度L<(20~40)mm;
16——制件表面粗糙度Ra0.2μm以下;
17——制件应具有一定的光泽,表面油污、脱模剂等痕迹必须擦拭干净;
18——同批产品色泽应一致,主视面不许有色差,制件不得有起层,剥离现象。
b)非主视面
19——不允许有气泡、流痕、花纹,色斑杂质应控制在面积小于0.5mm2,每制件不多于3个;
20——缩水处最低点与整个圆滑平面或弧面的距离应不超过0.8mm;
21——熔接缝宽度d<(0.06~0.08)mm,长度L<(60~80)mm;
22——制件表面粗糙度Ra0.4μm以下;
23——同批产品色泽应一致,不允许有明显色差,制件不得有起层,剥离现象。
不需喷漆,直接使用于摩托车内部的注塑件
a)主视面
24——其主视面表面应无银丝、气泡;
25——缩水处最低点与整个平面或弧面的距离应不超过0.6mm;
26——熔接缝宽度d<(0.04~0.06)mm,长度L<(40~60)mm;
27——同批产品色泽一致不允许有色差,制件不得有起层,剥离现象,
28——制件的表面粗糙度Ra0.8μm以下。
b)非主视面
29——表面应无1/5面积以上的花纹、流痕;
30——制件表面粗糙度Ra1.6μm以下;
31——熔接缝长度不超过制件宽度的三分之一;
32——制件不得有起层、剥离之现象。
喷砂件、皮纹件
33——表面应无花纹、流痕、气泡;
34——表面砂粒皮纹均匀,深浅度一致,拐角处、形状变化部份花纹疏密度一致;
35——缩水深度小于0.4mm,制件不得有起层、剥离、泛白等现象。
翘曲变形
所有制件冷却完全定型后,发生的翘曲变形不得超过5mm。
15.5 注塑产品毛刺、飞边的要求
毛刺、飞边的总体确认
毛刺、飞边的存在主要是模具动定模、分型面、滑块、抽芯配合间隙不好,两碰面接触不好,或锁模力不够,或注射压力过大超过塑料产品的溢边值而产生的细薄的边,必须去除掉,但不伤及制件尺寸的本身,是尖角的边必须去除锐角,一般保持R0.5mm的弧度,整个边缘应圆滑、自然、流畅,手指感觉不能有凹凸、刺手现象,不得有残留毛边,修边不平,跳刀等。
但有特殊要求的除外,如两塑料制件紧密的配合处,塑料件与灯具、仪表装配的边缘,视具体情况可保持制件的棱角,只允许用500号水砂轻砂其毛刺,特注意制件的装配孔、槽的毛刺、飞边一定要去除干净。
制件的浇口确认
对浇口的去除,浇口较厚有可能伤及制件本身的尺寸,影响配合和外观要求,须用专用镊子剪掉,剪掉后必须保持曲面的连贯自然。
15.6 注塑产品的尺寸要求
注塑产品的结构尺寸及允许偏差按图样的规定执行。
15.7 注塑产品的性能要求
注塑产品的各项性能要求,如:
燃烧速度、密度、拉伸强度、断裂伸长率、冲击强度、硬度、热变形温度、弯曲模量等应符合产品图样的规定。
16 试验方法
注塑产品外观用目测及手感,当外观目测有分歧时,粗糙度度可用测量仪检测,光泽度可按GB/T8807-1988的规定检测;表面色斑杂质大小用游标卡尺测试;分散度用100mm×100mm的检框测试。
注塑产品结构尺寸允许偏差及未注尺寸公差用通用量具测试。
注塑产品燃烧速度按GB/T2408-2008中规定的方法测试。
密度按GB/T1033的规定测试。
拉伸强度按GB/T1040的规定测试。
断裂伸长率按GB/T1040.1中4.3的规定测试。
冲击强度按GB/T1843的规定测试。
硬度按GB/T9342的规定测试。
热变形温度按GB/T1634-的规定测试。
弯曲模量按GB/T9341的规定测试。
邵氏硬度按GB/T2411的规定测试。
17 检验规则
17.1 检验分类
检验分类分为出厂检验和型式试验。
检验批由同一原料,同一配方,同一工艺条件,同一色泽的注塑产品组成,其最大批量为10000只。
17.2 出厂检验
每批注塑产品应经品质部检验合格,并附产品合格证后,方能出厂。
出厂检验抽样项目的样本,按GB/T2828.1-2003正常检查二次抽样方案从提交检查批中随机抽取,检查抽样规则见下表1。
其检查水平(L),合格质量水平(AC)及判定数组(AC、Re)。
表1
抽样数:
n
批量
样本大小n
合格判定数Ac
1-100
3
0
101-500
5
0
501-1200
8
0
1201-3200
12
0
3200以上
15
0
检验项目为5.2~5.5规定的内容。
出厂检验时,提交检查批的各检验项目经检验均合格后,该批方为合格。
出厂检验时,经检验不合格的检查批,经加工处理后,允许重新组批提交检验。
17.3 型式试验
有下列情况之一时,应进行型式试验。
(1)新产品定型或老产品改型时。
(2)当材料、工艺有较大改变,可能影响产品质量时。
(3)正常生产情况下,每年一次。
(4)出厂检验结果与上次型式检验有较大差异时。
(5)国家质量技术监督机构提出型式试验要求时。
型式试验的内容为第5章全部内容。
型式检验的样本应从出厂检验的同一批合格品中随机抽取3件,也可同时随机多抽6件备用。
型式检验时,如有一件不合格,允许加倍抽样复检,复检时,如仍有一件不合格,则该批产品不合格。
18 标志、包装、运输、贮存
18.1 标志
注塑产品应在规定位置打上企业专用的永久性标志,或由供需双方商定。
外包装上应标明下列内容或由供需双方商定。
36——产品代号、名称;
37——企业名称、地址;
38——执行标准代号;
39——按GB/T191-2008规定的“向上”、“怕雨”、“易碎”、“禁止翻滚”、“防摔打”、“防碰撞”、“小心轻放”及“堆码极限”等图示标志;
40——颜色;
41——出厂日期;
42——数量、重量、体积。
18.2 包装
注塑产品内包装用薄膜,外包装用瓦楞纸箱。
纸箱材料、尺寸和结构应保证产品在运输、贮存中不受损坏。
注塑产品外包装应严密、牢实。
18.3 运输
注塑产品装卸、运输时,应防雨、防潮、防止碰撞,挤压、摔打、抛掷及包装损坏。
18.4 贮存
注塑产品应贮存在清洁、通风、干燥的库房内,不应与腐蚀性物质共存。
注塑产品从出厂之日起,贮存期限为1年,超过1年的须通知品质部门重新对该批产品进行确认。