喷气织机可靠性评价文件模板.docx
《喷气织机可靠性评价文件模板.docx》由会员分享,可在线阅读,更多相关《喷气织机可靠性评价文件模板.docx(38页珍藏版)》请在冰豆网上搜索。
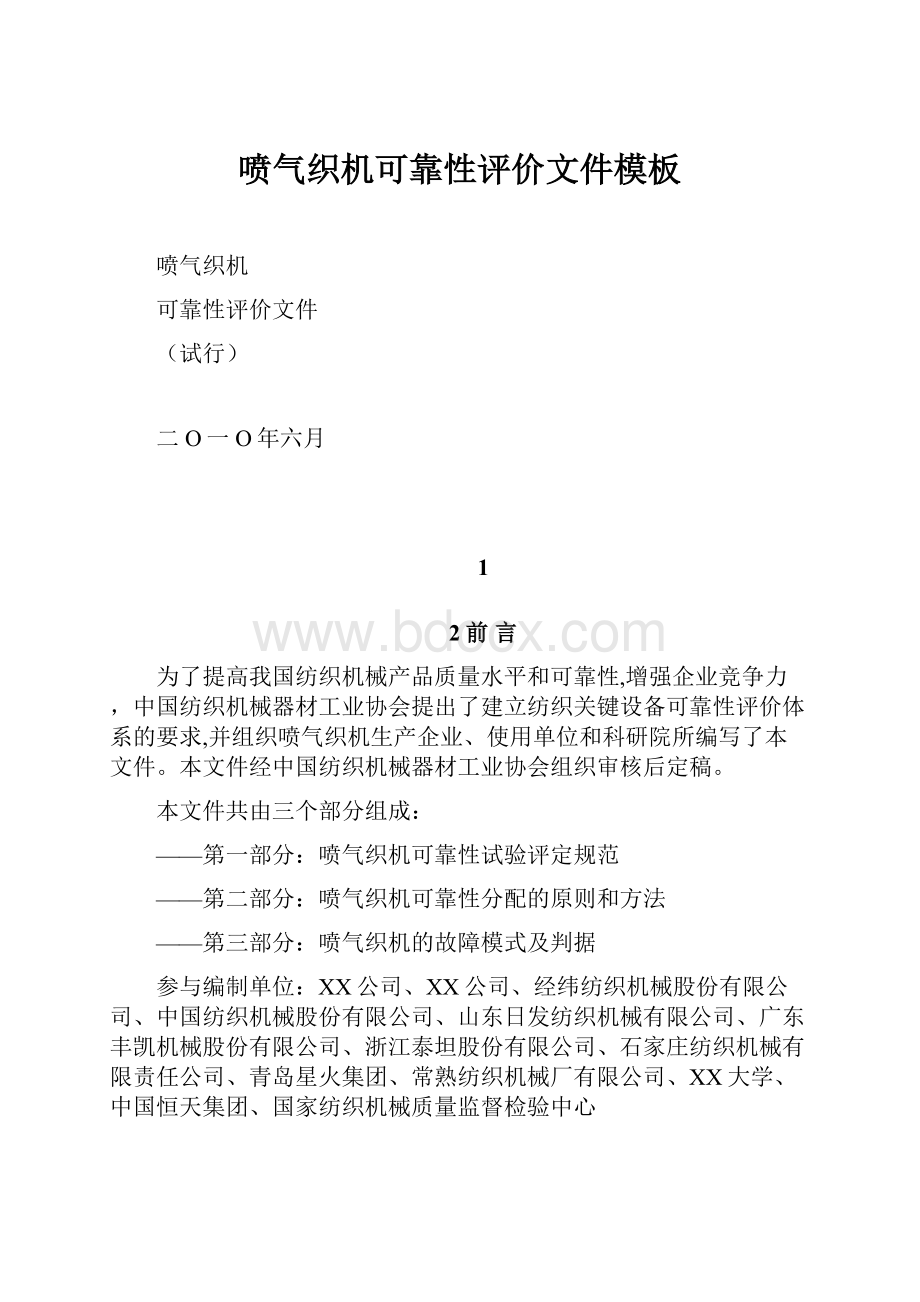
喷气织机可靠性评价文件模板
喷气织机
可靠性评价文件
(试行)
二O一O年六月
1
2前言
为了提高我国纺织机械产品质量水平和可靠性,增强企业竞争力,中国纺织机械器材工业协会提出了建立纺织关键设备可靠性评价体系的要求,并组织喷气织机生产企业、使用单位和科研院所编写了本文件。
本文件经中国纺织机械器材工业协会组织审核后定稿。
本文件共由三个部分组成:
——第一部分:
喷气织机可靠性试验评定规范
——第二部分:
喷气织机可靠性分配的原则和方法
——第三部分:
喷气织机的故障模式及判据
参与编制单位:
XX公司、XX公司、经纬纺织机械股份有限公司、中国纺织机械股份有限公司、山东日发纺织机械有限公司、广东丰凯机械股份有限公司、浙江泰坦股份有限公司、石家庄纺织机械有限责任公司、青岛星火集团、常熟纺织机械厂有限公司、XX大学、中国恒天集团、国家纺织机械质量监督检验中心
喷气织机可靠性试验评定规范
1范围
本文件规定了喷气织机(以下简称织机)可靠性测定试验方法及其评价指标的计算方法。
本文件适用于对批量生产的织机进行可靠性测定试验及评定,织机上的器材(喷嘴、钢筘、综框、综丝、停经片等)、电气装置(电控箱、储纬器、电磁离合器、经停装置、纬停装置等)和微机控制系统,也可以同主机同时进行测定试验。
2引用文件
GB/T3187—1994可靠性、维修性术语
GB/T5080.1—1986设备可靠性试验总要求
GB/T5080.4—1985设备可靠性试验可靠性测定试验的点估计和区间估计方法(指数分布)
GJB899—1990可靠性鉴定和验收试验
FZ/T9400×喷气织机
3试验的目的
3.1通过可靠性试验,了解喷气织机现有的可靠性水平,找出产品薄弱环节,为企业提高产品可靠性提供依据,不断满足用户对设备的可靠性要求。
3.2通过测定喷气织机可靠性的指标值,验证产品的可靠性水平,提高生产企业的知名度和影响力。
4测定试验指标及计算方法
4.1早期失效期
早期失效期主要反映产品因环境、设计、工艺、安装等方面不良引起的故障。
4.2早期失效期考核要求
4.2.1对于新产品设计,企业应进行产品的分阶段的可靠性设计和评审。
4.2.2零部件加工和整机安装,应具备相应的过程控制和工艺流程规范。
4.2.3整机出厂前,经检测合格后,应按相关试验条件进行运转试验。
4.3早期失效期的平均无故障工作时间MTBF
………………
(1)
式中:
r—在试验时间内织机累计故障次数
n—织机抽样试验台数
ti—在评定周期内第i台织机的实际工作时间
注:
试验中若r=0,则延长试验时间,直到出现故障为止。
4.4偶然失效率期的平均无故障工作时间MTBF
4.4.1点估计(定时截尾)
………………
(2)
式中:
tc—定时截尾时间
4.4.2区间估计
4.4.2.1置信度为(1-α)的平均无故障工作时间的单侧置信下限为:
………………(3)
式中:
α—风险度
l—置信下限
T—总试验时间
4.4.2.2置信度为(1-α)的平均无故障工作时间的双侧置信区间的下限和上限分别为:
……………………(4)
……………………(5)
式中:
μ—置信上限
注:
1)若试验结果r=0时,按90%置信度的单侧置信下限计算。
2)X2(1-a)(2r+2)、X2α/2(2r+2)、X2(1-α/2)(2r)是X2分布的分位数,可查X2分布分位数表(见附录A)。
4.5平均恢复前时间MTTR
……………………(6)
式中:
tmi—在试验时间内第i台织机故障修复时间
4.6稳态可用度A(指稳态条件下,规定时间区间内的瞬时可用度的均值)
……………………(7)
式中:
MUT—平均可用时间
MDT—平均不可用时间
注:
在可靠性测定试验中,一般只测定平均无故障工作时间MTBF值,企业可根据自身条件进行测定早期失效期的平均无故障工作时间MTBF值及平均恢复前时间MTTR。
5试验样机的要求
5.1对于新产品设计,企业应进行产品的分阶段的可靠性设计和评审。
5.2零部件加工和整机安装,应具备相应的过程控制和工艺流程规范。
5.3正常批量生产出厂的合格品。
5.4由试验组织单位按纺织行业标准检验合格后,并经调试能正常运转的产品。
5.5对测定早期故障的样机,应在安装完成后,进行1个月的早期故障的测定。
对测定偶然故障期的平均无故障工作时间的样机,一般是调试使用1个月后,已排除早期故障,但使用不超过2年的机台。
6试验条件
6.1工作环境:
织纯棉布:
温度22~30℃;相对湿度75~80%
织涤棉布:
温度20~30℃;相对湿度70~75%
织化纤长丝:
温度15~30℃;相对湿度70~85%
织精毛纺:
温度20~30℃;相对湿度75~80%
6.2织造品种:
按使用厂实际织造品种。
6.3织机工艺转速:
按企业实际生产的织物品种决定。
一般不低于最高设计转速的75%。
6.4试验机台应由经培训合格的挡车工操作,并由专职保全工调试。
6.5要有专人负责记录、维修和故障分析。
注:
在可靠性试验期间,如无法满足上述试验条件要求,经试验组织单位同意,可继续试验,但应对现场试验条件进行详细记录。
7抽样方式
按简单随机抽样法,在用户单位从使用现场中随机抽取本质上相同的产品作为样本(样本数n=10~12台)。
8试验方案
8.1采用现场试验的方法,按企业实际生产的情况进行。
8.2本文件假定产品寿命服从指数分布。
8.3本文件采用有替换定时截尾方式。
8.4规定置信度为90%。
8.5平均无故障工作时间,MTBF=2000小时。
8.6试验方案:
按照GJB899—90试验方案13,在α=10%、β=20%、d=2的情况下,试验总时间:
T=12.4MTBF=24800小时。
截尾故障数:
γ=10次。
8.7测定喷气织机可靠性特征量的试验总时间定为24800小时(每台运转时间应不低于T/n小时,如n=10台时,每台运转时间不低于2480小时)。
9故障模式及判据
按《喷气织机故障模式及判据》规定。
10数据处理
10.1测定试验时间是指全部受试机台正常运转生产时间的总和(包括故障修复时间),此外任何原因的停机时间都不应计算在内。
10.2非故障停机时间,如停电、节假日等人为因素的停机时间和按工厂规定的维修如调整、清洗、更换等停机时间都不计入故障修复时间。
10.3试验产品在试验期间可按说明书规定进行正常维护和保养,但在整个试验期间不得进行大修。
10.4采用点估计和区间估计同时计算的办法。
11试验结果和总结报告
11.1所有现场试验数据,应全部如实填写,记录和审核人要签名,记录数据不得自行更改。
11.2试验结束后,所有现场测试数据和故障分析报告交试验组织单位,由该单位进行汇总、统计、整理。
12可靠性评定
12.1同台织机累计当量故障次数
r′=
式中:
—第
次故障等级的加权系数。
n—累计故障次数
12.2累计当量故障总次数
r=
式中:
—第
台织机的累计当量故障次数
N—抽样试验样机总台数
12.3当量平均无故障工作时间MTBF
当量平均无故障工作时间的点估计值和区间估计值,按公式
(2)和(3)、(4)、(5)计算,若各项指标值均大于或等于《喷气织机可靠性的分配原则和方法》中规定的可靠性目标值,且不出现致命故障,则认定该批产品达到了本文件规定的可靠性指标要求。
附录A
(资料性附录)
X2分布分位数表
自由度V
(V)
(V)
(V)
2
0.103
4.605
5.991
4
0.711
7.779
9.488
6
1.635
10.65
12.59
8
2.773
13.36
15.51
10
3.940
15.98
18.31
12
5.226
18.55
21.03
14
6.571
21.06
23.69
16
7.962
23.54
26.30
18
9.390
25.99
28.87
20
10.85
28.41
31.41
22
12.34
30.81
33.92
24
13.85
33.20
36.42
26
15.38
35.56
38.89
28
16.92
37.92
41.34
30
18.49
40.26
43.77
32
20.09
42.57
46.17
34
21.70
44.80
48.57
36
23.30
47.19
50.96
38
24.91
49.50
53.36
40
26.51
51.81
55.76
42
28.16
54.08
58.11
50
34.76
63.17
67.51
52
36.45
65.42
69.82
60
43.19
74.40
79.08
62
44.90
76.63
81.37
70
51.74
85.53
90.53
72
53.47
87.74
92.80
80
60.39
96.58
101.88
82
62.14
98.78
104.13
90
69.13
107.57
113.15
3注:
1.自由度在可靠性试验中,用于表明可靠性试验或测量数据的可靠程度。
2.在定时截尾试验中,MTBF双侧置信区间下限的自由度v=2r+2,MTBF双侧置信区间上限的自由度v=2r;MTBF单侧置信下限的自由度v=2r+2。
以此,在表中查取相对应的X2分布分位数值。
喷气织机可靠性分配的原则和方法
1范围
本文件规定了喷气织机(以下简称织机)可靠性分配的原则、方法和可靠性目标值。
本文件适用于各类织机,包括自制件、器材、外协件、配套件的可靠性分配。
2引用文件
GB/T3187—1994可靠性、维修性术语
GB/T5080.4-1985设备可靠性试验可靠性测定试验的点估计和区间估计方法(指数分布)
FZ/T9400×喷气织机
喷气织机可靠性试验评定规范
3分配的目的
整机的可靠性是由组成整机的各系统、部件、零件、器材、配套件等的可靠性来保证的,只有组成整机的各系统、部件的可靠性得到保证了,才能保证整机的可靠性。
4分配原则
4.1可靠性分配应以整机的可靠性目标值来进行分配,目标值由各织机生产企业协商确定。
4.2在进行整机可靠性分配时,应对自制件、器材、外协件等一并进行分配,其分配值可从第一次分配得到,也可从系统、部件再分配时得到。
4.3整机、器材(包括喷嘴、综框、综丝、停经片、钢筘、边撑刺)的失效率分配比例为1∶0.1。
4.4整机(除器材外)的其余部分系统、部件的可靠性目标值,按整机剔除上述部件的目标值的80%进行分配。
4.5分配的方法采用专家评分的方法。
4.6假设产品寿命服从指数分布。
5分配程序
5.1确定需要分配的目标值
5.1.1确定整机的可靠性目标值,即整机的平均无故障工作时间:
MTBF=2000h
5.1.2整机的失效率目标值:
=1/MTBT=1/2000=0.0005(次/h)=5次/104h
5.1.3器材的失效率目标值:
λ1=0.1×λ=0.1×0.0005=0.00005(次/h)=5次/105h
5.1.4器材的平均无故障工作时间:
MTBF=1/λ1=20000h
5.1.5整机(除器材外)的其余系统、部件的失效率目标值:
=(λ-λ1)×0.8=0.00036(次/h)=3.6次/104h
5.1.6整机(除器材外)的其余系统、部件的平均无故障工作时间:
MTBFs=1/
=1/0.00036=2778h
5.2确定评分要素和评分原则
5.2.1整机根据五种要素,即复杂程度、技术难度、工作时间、维修性、故障致命度,对各系统、部件进行打分的。
5.2.2器材根据四种要素,即工艺条件、工作时间、维修性和故障致命度,对器材各部件进行打分的。
5.2.3评分原则
整机按五种因素即复杂程度(ei1)、技术难度(ei2)、工作时间(ei3)、维修性(ei4)、故障致命度(ei5)进行评分,评分原则见表1复杂程度评分准则(ei1)、表2技术难度评分准则(ei2)、表3工作时间评分准则(ei3)、表4维修性评分准则(ei4)、表5故障致命度评分准则(ei5)。
5.2.3.1复杂程度---是指与织机功能有关的各系统或部件的复杂程度,根据各系统或部件为完成整机功能而设置的零部件数量,加工工艺的复杂性及组装的难易程度来进行评分。
最简单的为1分,最复杂的为10分。
见表1。
表1复杂程度评分准则(ei1)
分数
评分准则
9~10
系统或部件结构很复杂,影响整机功能大,组成零件较多,加工与装配困难,要精细反复调整。
7~8
系统或部件结构复杂,对整机功能影响较大,装配要稍加调整,组成中采用部分标准零件。
5~6
系统或部件结构不复杂,对整机功能影响一般,装配无困难,组成零件居中。
3~4
系统或部件结构简单,影响整机功能很小,加工及装配方便,组成零件不多。
1~2
对整机功能无影响,系统或部件为少量的简单零件组成。
5.2.3.2技术难度——是考虑系统或部件目前的技术水平和成熟程度、改进提高的可能性来进行评分的。
技术水平低,对目前设计、加工工艺进行改进的可能性大的为1分;技术水平和成熟度较高,改进可能性小的为10分。
见表2。
表2技术难度评分准则(ei2)
分数
评分准则
9~10
系统或部件的技术水平和成熟度很高,进行改进、提高很困难。
7~8
系统或部件的技术水平和成熟度较高,改进设计、加工工艺有一定困难,把握不大。
5~6
系统或部件有一定的技术水平和成熟度,设计可以进行改进、提高,加工工艺改进亦有一定把握。
3~4
系统或部件的技术水平和成熟度一般,可以改进设计,加工工艺上很成熟。
1~2
系统或部件的技术水平和成熟度很差,改进设计,提高加工工艺均无困难。
5.2.3.3工艺条件---主要从材料和工艺两方面考虑,根据目前国内材料和工艺的成熟程度来进行评分。
目前材料和工艺成熟、改进可能性大的,评低分;材料和工艺还不能过关的、改进可能性小的,则评高分,评分在1~10分之间。
见表2A。
表2A工艺条件评分准则
分数
准则
9~10
材料、工艺方面尚不成熟,改进提高该零部件的质量非常困难。
7~8
材料、工艺方面不太成熟,改进提高该零部件的质量把握不大。
5~6
材料、工艺方面比较成熟,或已有新材料、新工艺,改进提高该零部件的质量把握较大。
3~4
材料、工艺方面很成熟,改进提高该零部件的质量技术上基本可行。
1~2
非常成熟的材料和工艺,改进提高该零部件的质量技术上已无困难。
5.2.3.4工作时间——根据系统或部件在完成整机功能中的工作时间(循环次数或任务时间的百分数)来进行评分,系统或部件一直处于工作状态的为10分,工作时间最短的为1分。
见表3
表3工作时间评分准则(ei3)
分数
评分准则
9~10
系统或部件在完成整机功能中,一直处于工作状态。
7~8
系统或部件在完成整机功能中,基本上处于工作状态,稍有间歇、停顿。
5~6
系统或部件在完成整机功能中,作间歇运动,有40~50%停顿时间。
3~4
系统或部件在完成整机功能中,大部分时间处于停顿状态。
1~2
系统或部件在完成整机功能中,基本上处于停顿或不工作状态。
5.2.3.5维修性---根据部件或零件、器材等所处的位置以及使用、维修的难易程度及所需维修水平的高低来进行评分。
容易维修的,评高分;不容易维修的,评低分,评分在1~10分之间。
见表4、表4A。
表4维修性评分准则
分数
准则
9~10
需要普通工具在机台表面即可维修,维修非常容易。
7~8
需要随机工具,维修人员不需要拆卸其它零件即可维修,维修很容易。
5~6
需要专用工具,维修人员需要拆卸一些其它零件方可维修,维修比较容易。
3~4
需要完成比较复杂的解体方可维修。
维修较困难,维修水平要求较高。
1~2
需要完成很复杂的解体方可维修。
维修很困难,维修水平要求很高。
表4A器材维修性评分准则(ei4)
分数
准则
7~8
能在短时间内找出故障,维修方便,所需费用小。
5~6
维修较方便,更换下来的器材能进行维修。
3~4
一次性更换的零件。
5.2.3.6故障致命度---根据部件和零件故障对安全、使用和经济的影响来进行评分。
故障后果严重的评低分;故障后果轻微的评高分,评分在1~10分之间。
见表5。
表5故障致命度评分准则(ei5)
分数
准则
9~10
未造成整机或系统的性能显著下降的轻微故障。
7~8
引起系统或整机性能下降的故障,所需维修费用较少,例如无故停车等。
5~6
引起系统或整机性能下降的故障,所需维修费用中等。
3~4
引起系统或整机性能明显下降的严重故障;或系统、部件需要高价修理或修理时间较长的故障。
1~2
机器严重损坏,造成很大经济损失甚至危害人员安全的故障。
6评分程序
6.1聘请专家
所聘请的专家必须对织机的性能、使用相当熟悉,有较全面的了解和掌握;聘请的专家面要广,要有制造厂、使用厂、器材、配套件厂等各方面的代表,也可有大专院校、科研所以及从事管理工作的人员参加,专家人数一般不少于5人。
6.2专家打分
将表6所列的评分项目表发给聘请的专家,他们根据自己的经验,按照上述评分要素,参考表1~表5的评分准则,对织机的各系统、部件进行打分。
表6织机可靠性分配表
机型:
日期:
年月日
评分人:
单位:
序号
系统及部件名称
复杂程度
ei1
技术难度
(工艺条件)
ei2
工作时间
ei3
维修性
ei4
故障致命度
ei5
1
2
3
4
6.3评分结果汇总和计算
6.3.1将各位专家的评分表汇总后,计算各系统、部件的分配结果,若进一步需要知道某部件中的某关键零件的分配目标值,则可用该系统或部件分配到的目标值按上述方法再进一步进行分配,如此深入,直到获得所需要的零件、器材等的可靠性目标分配值。
6.3.2计算系统或部件各要素的评分均值ei1、ei2、ei3、ei4、ei5,即所有专家在对各系统、部件五种要素的评分结果相对稳定后,分别取其各要素的评分均值。
6.3.3计算各系统、部件的评分数
式中:
——第
个系统或部件的评分数
6.3.4整机(除器材外)的其余系统、部件的评分数
Ws=
式中:
——系统或部件个数
6.3.5计算各系统、部件的评分系数
=
/Ws
式中:
——第
个系统或部件的评分系数
7织机可靠性指标的置信区间及对各系统、部件的可靠性分配计算
根据喷气织机近几年的质量水平,规定其平均无故障工作时间(MTBF)为2000h。
以此目标值作为分配计算基础。
7.1整机故障数
r=10次
7.2织机在置信度为90%时的平均无故障时间的置信区间
7.2.1单侧置信下限为
MTBFl=2T/
(2r+2)=2×24800/X20.9(2×10+2)=49600/30.81=1609.9h
7.2.2双侧置信区间的下限和上限分别为
MTBFl=2T/
(2r+2)=2×24800/X20.05(2×10+2)=49600/12.34=4019h
MTBFu=2T/
(2r)=2×24800/X20.95(2×10)=49600/31.41=1579h
以上估计值说明MTBF真值落在这个区间的概率至少为90%。
7.3各系统或部件的失效率
式中:
——第
个系统或部件的失效率
7.4各系统或部件的平均无故障工作时间
MTBF
=
式中:
MTBFI——第
个系统或部件的平均无故障工作时间
7.5各系统或部件的故障次数
ri=24800/MTBFi
式中:
ri——第
个系统或部件的故障次数
7.6织机各系统、部件的可靠性目标值的分配计算结果见表7。
8几点说明
8.1可靠性分配所进行的专家评分和取值按德尔菲(Delphi)法的步骤进行。
在评分过程中,各位专家独立地进行评分,若第一轮评分意见比较一致,则可一次评分结束;若评分意见不一致,则取专家评分意见的中位值作为专家的集体意见反馈给各位专家,并请他们根据这个结果,在考虑其他专家的意见后修改自己的意见。
如果某位专家对评分要素的评分明显偏高或偏低,则请该专家陈述其评分依据,并反馈给其他专家参考,在此基础上进行第二轮打分,如此反复迭替,直到评分结果相对稳定。
8.2在各项计算结束后,要进行验算,以保证各系统、部件分配的失效率之和小于或等于整机的失效率目标值。
表7喷气织机整机可靠性分配结果汇总表
序号
系统及部件
名称
复杂程度
ei1
技术
难度
ei2
工作
时间
ei3
维修性
ei4
故障
后果
ei5
评分数
wi
评分系数
ai
失效率分配值
λi
(次/
h)
平均无故障工作时间分配值MTBFi
(h)
故障次数
分配值
ri
1
主传动部分
7
8
10
6
5
16800
0.*********
3.1246
32004
0.7749
5970.21798
2
送经部分
7
7
10
6
6
17640
0.*********
3.2808
30480
0.8136
3
引纬部分
8
7
9
6
7
21168
0.*********
*********
3.9370
25400
0.9763
4
开口部分
7
7
10
6
4
11760
0.*********
2.1872
45720
0.5424
5
打纬部分
7
7
10
6
4
11760
0.*********
2.1872
45720
0.5424
6
卷曲部分
7
6
10
6
6
15120
0.*********
2.8121
35560
0.6974
7
剪刀部分
5
6
8
8
8
15360
0.*********
2.8568
35004
0.7084
8
绞边部分
5
6
10
8
6
14400
0.*********
2.6782
37338
0.6642
9
润滑部分
5
7
8
6
6
10080
0.