基于串级技术和PLC控制器的双容水箱液位控制系统.docx
《基于串级技术和PLC控制器的双容水箱液位控制系统.docx》由会员分享,可在线阅读,更多相关《基于串级技术和PLC控制器的双容水箱液位控制系统.docx(66页珍藏版)》请在冰豆网上搜索。
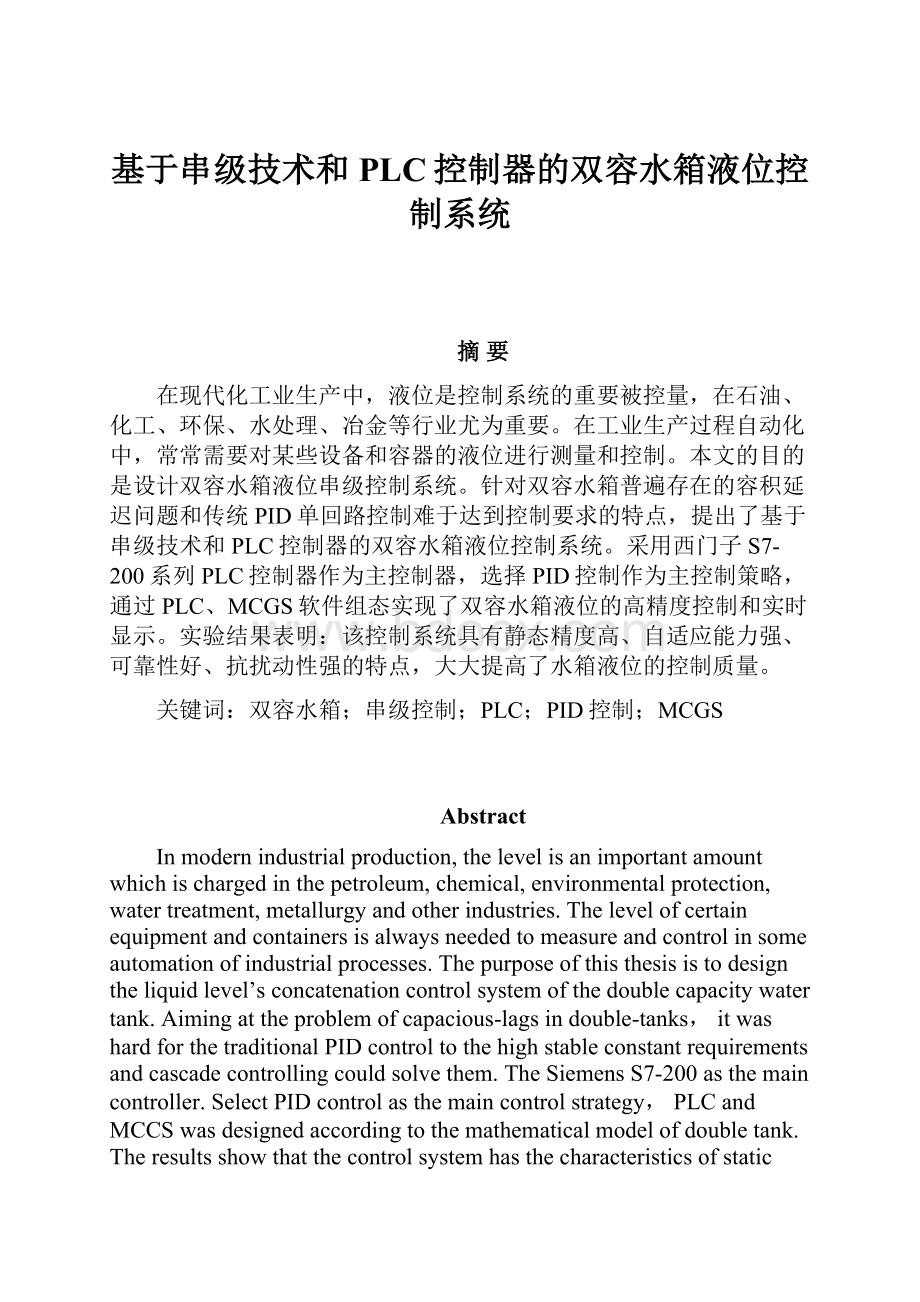
基于串级技术和PLC控制器的双容水箱液位控制系统
摘要
在现代化工业生产中,液位是控制系统的重要被控量,在石油、化工、环保、水处理、冶金等行业尤为重要。
在工业生产过程自动化中,常常需要对某些设备和容器的液位进行测量和控制。
本文的目的是设计双容水箱液位串级控制系统。
针对双容水箱普遍存在的容积延迟问题和传统PID单回路控制难于达到控制要求的特点,提出了基于串级技术和PLC控制器的双容水箱液位控制系统。
采用西门子S7-200系列PLC控制器作为主控制器,选择PID控制作为主控制策略,通过PLC、MCGS软件组态实现了双容水箱液位的高精度控制和实时显示。
实验结果表明:
该控制系统具有静态精度高、自适应能力强、可靠性好、抗扰动性强的特点,大大提高了水箱液位的控制质量。
关键词:
双容水箱;串级控制;PLC;PID控制;MCGS
Abstract
Inmodernindustrialproduction,thelevelisanimportantamountwhichischargedinthepetroleum,chemical,environmentalprotection,watertreatment,metallurgyandotherindustries.Thelevelofcertainequipmentandcontainersisalwaysneededtomeasureandcontrolinsomeautomationofindustrialprocesses.Thepurposeofthisthesisistodesigntheliquidlevel’sconcatenationcontrolsystemofthedoublecapacitywatertank.Aimingattheproblemofcapacious-lagsindouble-tanks,itwashardforthetraditionalPIDcontroltothehighstableconstantrequirementsandcascadecontrollingcouldsolvethem.TheSiemensS7-200asthemaincontroller.SelectPIDcontrolasthemaincontrolstrategy,PLCandMCCSwasdesignedaccordingtothemathematicalmodelofdoubletank.Theresultsshowthatthecontrolsystemhasthecharacteristicsofstaticaccuracy,adaptability,reliability,andantinterference,andgoodeffectsareachievedbythiscontrollerinthedouble-tanks.
Keywords:
double-tanks;cascadecontrol;PLC;PIDcontrol;MCGS
目录
1绪论
1.1选题的目的与意义
生产与生活的自动化是人类长久以来所梦寐以求的目标,在18世纪自动控制系统在蒸汽机运行中得到成功的应用以后,自动化技术时代开始了。
随着工业技术的更新,特别是半导体技术、微电子技术、计算机技术和网络技术的发展,自动化仪表已经进入了计算机控制装置时代。
大力发展工业自动化技术既可以促进信息化的发展又可以武装传统产业,带动工业化的实现。
因此把工业自动化作为一个行业重点发展,应作为我国实现工业化和信息化的战略方针。
用工业自动化技术武装传统产业,使设备控制自动化、工艺流程自动化,从而实现我国的工业化建设。
事实上,由于信息化和管理自动化的核心技术是相同的,都基于计算机技术、网络技术、软件技术和信息技术,所以管自动化是信息化的重要组成部分。
因此,发展工业自动化技术可以促进工业化的实现,带动信息化的发展,这就是工业自动化的特殊地位及重要性。
随着计算机控制装置在控制仪表基础上发展起来以后,自动化控制手段也越来越丰富。
在现代化工业生产中,液位是控制系统的重要被控量,在石油、化工、环保、水处理、冶金等行业尤为重要。
在工业生产过程自动化中,常常需要对某些设备和容器的液位进行测量和控制。
通过液位的检测与控制,了解容器中的原料、半成品或成品的数量,以便调节容器内的输入输出物料的平衡,保证生产过程中各环节物料搭配得当。
通过控制计算机可以不断监控生产的运行过程,即时地监视或控制容器液位,保证产品的质量和数量。
如果控制系统设计欠妥,会造成生产中对液位控制的不合理,导致原料的浪费、产品的不合格,甚至造成事故,所以设计一个良好的液位控制系统在工业生产中有着重要的实际意义。
本课题是以液位作为控制对象,设计双容水箱液位串级控制系统,充分利用自动化仪表技术,自动控制技术等以实现对水箱液位的串级控制。
1.2过程控制系统的发展
过程控制系统的发展随着工业生产要求的提高和生产技术的进步经历了很长一段发展过程,大致可分为几个方面:
1仪表化与局部自动化系统
这一阶段的主要特点是:
采用的过程检测控制仪表为基地式仪表和部分单元组合式仪表,而且多数是气动式仪表,其结构方案大多数是单输入-单输出的单回路定值系统。
过程控制的主要工艺参数是温度、压力、流量、液位等热工参数的定值控制。
控制的主要目的是保持工业生产的连续性和稳定性减少扰动。
单元组合式仪表以采样模拟技术和经典控制理论,实现了对生产过程的集中控制。
以单回路PID(比例、积分、微分)策略为主,同时针对不同的对象与要求,创造了一些专门的控制系统,如按物件,例配置的比值控制,克服大滞后的Smith预估器,克服干扰的前馈控制和串级控制等。
仪表化与局部自动化系统运行设计分析的理论基础是以频域法和根轨迹法为主体的经典控制理论,它在控制性能上一般只能实现简单参数的PID调节和简单的串级、前馈控制,主要任务是稳定系统,实现定值控制。
无法实现如自适应控制,最优化控制等复杂的控制形式。
2计算机集中式数字控制系统
由于生产过程的强化,控制对象的复杂,即高维、大时滞、严重非线性、耦合及严重不确定性对象,上述简单的控制系统已经无能为力。
随着计算机技术的发展,人们试图用计算机控制系统,替代全部模拟控制仪表,即模拟技术由数字技术来替代。
计算机集中式数字控制系统主要经历了2个阶段:
(1)直接数字控制系统DDC(DirectDigitalControl)
DDC系统是用1台计算机配以模数、数模转换器等输入输出设备,从生产中获得信息,按照预先规定的控制算法算出控制量,并通过输出通道,直接作用在执行机构上,实现对生产过程的闭环控制。
DDC系统不仅可以对一个回路进行控制,而且通过采样,可以实现对多个回路的控制。
在DDC系统中的计算机参加闭环控制过程,它不仅能完全取代模拟调节器,实现多回路的PID调节,而且不需改变硬件,只需通过改变程序就能实现多种较复杂的控制规律,如串级控制、前馈控制、非线性控制、自适应控制、最优控制等。
(2)计算机集中监督控制系统SCC(Supervisory ComputerControlSystem)
在DDC系统中,其给定值是预先设定的,并存入微机内存中,它不能随生产负荷,操作条件和工艺信息变化而及时修正。
因此,不能使生产处于最优工况。
SCC系统是将操作指导和DDC综合起来的一种较高形式的控制系统。
在SCC系统中计算机对生产过程中的参数进行巡检,按照所设计的控制算法进行计算,计算出最佳设定值直接传递给DDC计算机,进而由DDC计算机控制生产过程。
它实现了分级控制。
SCC系统改进了DDC系统在实时控制时采用周期不能太长的缺点,能完成较为复杂的计算,可实时实现最优化控制。
计算机集中式数字控制系统所采用的主要理论基础是现代控制理论。
各种改进或复合PID算法,大大提高了传统PID控制的性能与效果。
对多输入多输出的多变量控制理论,克服对象特性时变和环境干扰等不确定影响的自适应控制,消除因模型失配而产生不良影响的预测控制,保证系统稳定的鲁棒控制等。
新理论与策略的应用为计算机集中控制奠定了坚定的理论基础。
3集散式控制系统DCS(DistributedControlSystem)
集中式计算机控制系统在将控制集中的同时,也将危险集中,因此可靠性不高,抗干扰能力较差,随着现代工业生产的迅速发展,不仅要求完成生产过程的在线控制任务,而且还要求实现现代化集中式管理。
它的主导思想是将复杂的对象化分为几个子对象,然后用局部控制器(现场控制站)作为一级,直接作用于被控对象,即所谓水平分散。
第2级是操纵各现场控制站的协调控制器(操作监视站),它使各子系统协调配合,共同完成系统的总任务。
DCS既有计算机控制系统控制算式先进,精度高、响应速度快的优点,又有仪表控制系统安全可靠、维护方便的特点。
集散式控制系统的数据通信网络是连接分级递阶结构的纽带,是典型的局域网。
它传递的信息以引起物质、能量的运动为最终目的。
因而,它强调的是可靠性、安全性、实时性和广泛的实用性。
对于那些工艺复杂,建模困难的过程控制对象,传统控制理论难以解决。
而对于知识、仿人脑推理、学习、记忆能力的智能控制系统,可不需要建立对象模型,而通过获取有关信息,模仿人智能直接进行决策与控制。
此外,还可利用智能技术的特征提取,模式分类和聚类分析,建立较精确的对象模型,再用传统的控制方法实施控制。
智能控制方法有以下几种:
分级递阶智能控制、专家控制、人工神经网络控制、拟人智能控制理论等。
4现场总线控制系统FCS(FieldControlSystem)
集散系统大多采用网络通信体系结构,采用本公司专用的标准和协议,加之受到现场仪表在数字化、智能化方面的限制,它没能将控制功能彻底地分散到现场。
现场总线控制系统是计算机技术、通信技术、控制技术的综合与集成。
通过现场总线,将工业现场具有通信特点的智能化仪器仪表、控制器、执行机构等现场设备和通信设备连接成网络系统。
连接在总线上的设备之间可直接进行数据传输和信息交换。
同时,现场设备和远程监控计算机也可实现信息传输。
这样,将现场控制站中的控制功能下移到网络的现场智能设备中,从而构成虚拟控制站,通过现场仪表就可构成控制回路,实现了分散控制。
FCS系统较好地解决了过程控制的两大基本问题,即现场设备的实时控制和现场信号的网络通信。
它不仅实现了智能下移数据传输从点到点发展到采用总线方式。
而且用大系统的概念来看整个过程控制系统,即整个控制系统可看作是一台巨大的计算机按总线方式运行。
故全数字化、全分散式、全开放、可互操作和开放式互连网络是其主要特点和发展方向。
基于人工神经网络、模式识别、模糊理论基础而开发的软测量技术,为FCS系统提供了强大的信息检测功能。
过程优化即稳态优化和最优控制等各种先进控制理论以及多学科和技术的交叉和融合,为FCS系统提供了坚实的理论基础。
而计算机网络技术的发展和成熟又为FCS系统的实现提供了技术。
5计算机集成过程系统CIPS(ComputerIntegratedProcessSystem)
尽管各种先进的控制系统能明显提高控制质量和经济效益,但是它们仍然只是相互孤立的控制系统。
从过程控制系统发展的必要性和可能性来看,过程控制系统必将朝综合化、智能化的方向发展。
因此,以智能控制理论为基础,以计算机及网络为主要手段对企业的经营计划、调度、管理和控制全面综合,实现从原料进库到产品出厂的自动化、整个生产系统信息管理的最优化。
整个系统由生产管理层,高级控制与优化层,基础控制层3部分组成。
这种集控制、优化、调度、管理等于一体并将信号处理技术、数据库技术、通讯技术以及计算机网络技术进行有机结合而发展起来的所谓综合自动化系统称为计算机集成过程系统CIPS(ComputerIntegratedProcossSystem)。
作为一种全集成自动化系统,既是对设备的集成,也是对信息的集成。
CIPS覆盖操作层、管理层、决策层,涉及企业生产全过程的计算机优化。
它的最大特点是多种技术的综合与全企业信息的集成。
它表现的最大特征是仿人脑功能,这一点在某种程度上是回复到初级阶段的人工控制,但更多是在人工控制基础上的进步和飞跃。
1.3可编程控制器产生及现状
可编程程序控制器(ProgrammableController)通常也称为可编程控制器。
它是以微处理器为基础,综合了计算机技术、自动控制技术而发展起来的一种通用的工业自动控制装置;具有体积小、功能强、程序设计简单、灵活通用、维护方便等优点。
本设计课题采用在工业领域有着广泛应用的西门子S7200系列PLC作为主控制器。
S7-200系列小型PLC可以应用于各种自动化系统。
系统组成如图1.1:
图1.1:
S7200-PLC系统组成
S7200PLC由主机、输入/输出接口、电源、模块扩展接口和外部设备接口、计算机编程软件等几个主要部分组成。
世界上公认的第一台PLC是1969年美国数字设备公司(DEC)研制的。
限于当时的元器件条件及计算机发展水平,早期的PLC主要由分立元件和中小规模集成电路组成,可以完成简单的逻辑控制及定时、计数功能。
20世纪70年代初出现了微处理器。
人们很快将其引入可编程控制器,使PLC增加了运算、数据传送及处理等功能,完成了真正具有计算机特征的工业控制装置。
为了方便工程技术人员使用,可编程控制器采用和继电器电路图类似的梯形图作为主要编程语言,并将参加运算及处理的计算机存储元件都以继电器命名。
此时的PLC为微机技术和继电器常规控制概念相结合的产物。
20世纪70年代中末期,可编程控制器进入实用化发展阶段,计算机技术已全面引入可编程控制器中,使其功能发生了飞跃。
更高的运算速度、超小型体积、更可靠的工业抗干扰设计、模拟量运算、PID功能及极高的性价比奠定了它在现代工业中的地位。
20世纪80年代初,可编程控制器在先进工业国家中已获得广泛应用。
这个时期可编程控制器发展的特点是大规模、高速度、高性能、产品系列化。
这个阶段的另一个特点是世界上生产可编程控制器的国家日益增多,产量日益上升。
这标志着可编程控制器已步入成熟阶段。
20世纪末期,可编程控制器的发展特点是更加适应于现代工业的需要。
从控制规模上来说,这个时期发展了大型机和超小型机;从控制能力上来说,诞生了各种各样的特殊功能单元,用于压力、温度、转速、位移等各式各样的控制场合;从产品的配套能力来说,生产了各种人机界面单元、通信单元,使应用可编程控制器的工业控制设备的配套更加容易。
目前,可编程控制器在机械制造、石油化工、冶金钢铁、汽车、轻工业等领域的应用都得到了长足的发展。
我国可编程控制器的引进、应用、研制、生产是伴随着改革开放开始的。
最初是在引进设备中大量使用了可编程控制器。
接下来在各种企业的生产设备及产品中不断扩大了PLC的应用。
目前,我国自己已可以生产中小型可编程控制器。
上海东屋电气有限公司生产的CF系列、杭州机床电器厂生产的DKK及D系列、大连组合机床研究所生产的S系列、苏州电子计算机厂生产的YZ系列等多种产品已具备了一定的规模并在工业产品中获得了应用。
此外,无锡华光公司、上海乡岛公司等中外合资企业也是我国比较著名的PLC生产厂家。
21世纪,PLC会有更大的发展。
从技术上看,计算机技术的新成果会更多地应用于可编程控制器的设计和制造上,会有运算速度更快、存储容量更大、智能更强的品种出现;从产品规模上看,会进一步向超小型及超大型方向发展;从产品的配套性上看,产品的品种会更丰富、规格更齐全,完美的人机界面、完备的通信设备会更好地适应各种工业控制场合的需求;从市场上看,各国各自生产多品种产品的情况会随着国际竞争的加剧而打破,会出现少数几个品牌垄断国际市场的局面,会出现国际通用的编程语言;从网络的发展情况来看,可编程控制器和其它工业控制计算机组网构成大型的控制系统是可编程控制器技术的发展方向。
目前的计算机集散控制系统DCS(Distributed Control System)中已有大量的可编程控制器应用。
伴随着计算机网络的发展,可编程控制器作为自动化控制网络和国际通用网络的重要组成部分,将在工业及工业以外的众多领域发挥越来越大的作用。
2系统控制方案设计
2.1PID控制器
2.1.1PID控制的原理和特点
工程实际中,应用最为广泛的调节器控制规律为比例、积分、微分控制,简称PID控制,又称PID调节。
PID控制器问世至今已有近70年历史,它以其结构简单、稳定性好、工作可靠、调整方便而成为工业控制的主要技术之一。
当被控对象的结构和参数不能完全掌握,或得不到精确的数学模型时,控制理论的其它技术难以采用时,系统控制器的结构和参数必须依靠经验和现场调试来确定,这时应用PID控制技术最为方便。
即当我们不完全了解一个系统和被控对象﹐或不能通过有效的测量手段来获得系统参数时,最适合用PID控制技术。
PID控制,实际中也有PI和PD控制。
PID控制器就是根据系统的误差,利用比例、积分、微分计算出控制量进行控制的。
(1)比例(P)控制
比例控制是一种最简单的控制方式。
其控制器的输出与输入误差信号成比例关系。
当仅有比例控制时系统输出存在稳态误差。
(2)积分(I)控制
在积分控制中,控制器的输出与输入误差信号的积分成正比关系。
对一个自动控制系统,如果在进入稳态后存在稳态误差,则称这个控制系统是有稳态误差的或简称有差系统。
为了消除稳态误差,在控制器中必须引入“积分项”。
积分项对误差取决于时间的积分,随着时间的增加,积分项会增大。
这样,即便误差很小,积分项也会随着时间的增加而加大,它推动控制器的输出增大使稳态误差进一步减小,直到等于零。
因此,比例+积分(PI)控制器,可以使系统在进入稳态后无稳态误差。
(3)微分(D)控制
在微分控制中,控制器的输出与输入误差信号的微分(即误差的变化率)成正比关系。
自动控制系统在克服误差的调节过程中可能会出现振荡甚至失稳。
其原因是由于存在有较大惯性组件(环节)或有滞后组件,具有抑制误差的作用,其变化总是落后于误差的变化。
解决的办法是使抑制误差的作用的变化“超前”,即在误差接近零时,抑制误差的作用就应该是零。
这就是说,在控制器中仅引入“比例”项往往是不够的,比例项的作用仅是放大误差的幅值,而目前需要增加的是“微分项”,它能预测误差变化的趋势,这样,具有比例+微分的控制器,就能够提前使抑制误差的控制作用等于零,甚至为负值,从而避免了被控量的严重超调。
所以对有较大惯性或滞后的被控对象,比例+微分(PD)控制器能改善系统的动态特性。
2.1.2比例调节
在人工调节的实践中,如果能使阀门的开度与被调参数偏差成比例的话,就有可能使输出量等于输入量,从而使被调参数趋于稳定,达到平衡状态。
这种阀门开度与被调参数的偏差成比例的调节规律,称为比例调节。
比例调节作用,一般用字母P来表示。
比例调节器实际上是一个放大倍数可调的放大器。
比例调节作用虽然及时、作用强,但是有余差存在,被调参数不能完全回复到给定值,调节精度不高,所以比例调节为“粗调”。
纯比例调节只能用于干扰较小、滞后较小,而时间常数又不太小的对象。
2.1.3比例积分调节
对于工艺条件要求较高并且余差不允许存在的情况下,比例作用调节器不能满足要求了,克服余差的办法是引入积分调节。
因为单纯的积分作用使过程缓慢,并带来一定程度的振荡,所以积分调节很少单独使用,一般都和比例作用组合在一起,构成比例积分调节器,简称PI调节器。
表示PI调节作用的参数有两个:
比例度P和积分时间Ti。
而且比例度不仅影响比例部分,也影响积分部分,使总的输出既具有调节及时、克服偏差有力的特点,又具有克服余差的性能。
由于它是在比例调节(粗调)的基础上,有加上一个积分调节(细调),所以又称再调调节或重定调节。
但是,积分时间太小,积分作用就太强,过程振荡剧烈,稳定程度低;积分时间太大,积分作用不明显,余差消除就很慢。
如果把积分时间放到最大,PI调节器就丧失了积分作用,成了一个纯比例调节器。
2.1.4比例积分微分调节
微分调节的作用主要是用来克服被调参数的容量滞后。
在生产实际中,有经验的工人总是既根据偏差的大小来改变阀门的开度大小(比例作用),同时又根据偏差变化速度的大小进行调节。
比如当看到偏差变化很大时,就估计到即将出现很大的偏差而过量地打开(关闭)调节阀,以克服这个预计的偏差,这种根据偏差变化速度提前采取的行动,意味着有“超前”作用,因而能比较有效地改善容量滞后比较大的调节对象的调节质量。
微分调节是指调节器的输出变化与偏差变化速度成正比,偏差变化的速度越大,微分时间越长,则调节器的输出变化就越大。
对于一个固定不变的偏差,不管其有多大,微分做用的输出总是零,这是微分作用的特点。
由于实际微分器的比例度不能改变,固定为100%,微分作用也只在参数变化时才出现,所以实际微分器也不能单独使用。
一般都是和其它调节作用相配合,构成比例微分或比例积分微分调节器。
比例积分微分调节又称PID调节,PID调节中,有三个调节参数,就是比例度P、积分时间IT、微分时间DT。
适当选取这三个参数值,就可以获得良好的调节质量。
由分析可知,PID作用调节质量最好,PI调节第二,PD调节有余差。
纯比例调节虽然动偏差比PI调节小,但余差大,而纯积分调节质量最差,所以一般不单独使用。
2.2系统设计
2.2.1双容水箱数学模型的建立
双容水箱液位系统的结构图如图2.1所示。
设Q0、Q1为上水箱的进水流量和出水流量,Q2为下水箱的出水流量;h1、h2分别为上水箱、下水箱的液位;R1、R1分别为上水箱、下水箱的线性化水阻,A1、A2分别为上水箱、下水箱的横截面积。
根据动态物料平衡关系有:
图2.1双容水箱示意图
A1=
=
-
=
-
(1)
A
=
-
=
-
(2)
(1)
(2)经拉氏变化,得
(3)
(4)
令
,
,
,有双容过程传递函数
2.2.2方案设计
单回路控制系统解决了工艺生产过程自动化中大量的参数定值问题。
但是,随着现代工业生产的迅速发展,工艺操作条件的要求更加严格,对安全运行和经济性及对控制质量的要求也更高。
此时单回路控制系统满足不了要求,需要开发和运用新的控制系统,进一步提高控制质量。
双容水箱是作为一种常用的液位控制设备,由于水箱本身普遍存在着容积延迟,系统惯性比较大,液位变化缓慢,系统一般呈非线性。
系统的下水箱液位受上水箱液位的影响很大,当系统中出现扰动时,尽管阀门开度作了相应的变化,但只通过上水箱的控制通道,难以迅速控制下水箱的液位。
实践证明,单回路控制效果不理想,系统的调节时间过长。
串级控制是改善调节过程动态性能的有效方法,由于其超前的控制作用,可以大大克服系统的容积延迟。
针对双容水箱对象的特点,设计双容水箱液位串级控制系统。
串级控制系统结构如图2.2所示。
串级控制系统采用两套检测变送器和两个调节器,前一个调节器的输出作为后一个调节器的设定,后一个调节器的输出送往调节阀。
前一个调节器称为主调节器,后一个调节器称为副调节器。
在串级控制系统中,由于引入了一个副回路,不仅能及早克服进入副回路的扰动,而且又能改善过程特性。
副调节器具有“粗调”的作用,主调节器具有“细调”的作用,从而使其控制品质得到进一步提高。
串级控制回路系统增加了副回路,使性能得到改善,表现在以下几个方面:
(1)改善了过程的动态特性
串级控制系统比单回路控制系统在结构上多了一个副回路。
它的容量滞后减少了,过程的动态特性得到改善,使系统的响应加快,控制更为及时。
(2