液压系统设计.docx
《液压系统设计.docx》由会员分享,可在线阅读,更多相关《液压系统设计.docx(12页珍藏版)》请在冰豆网上搜索。
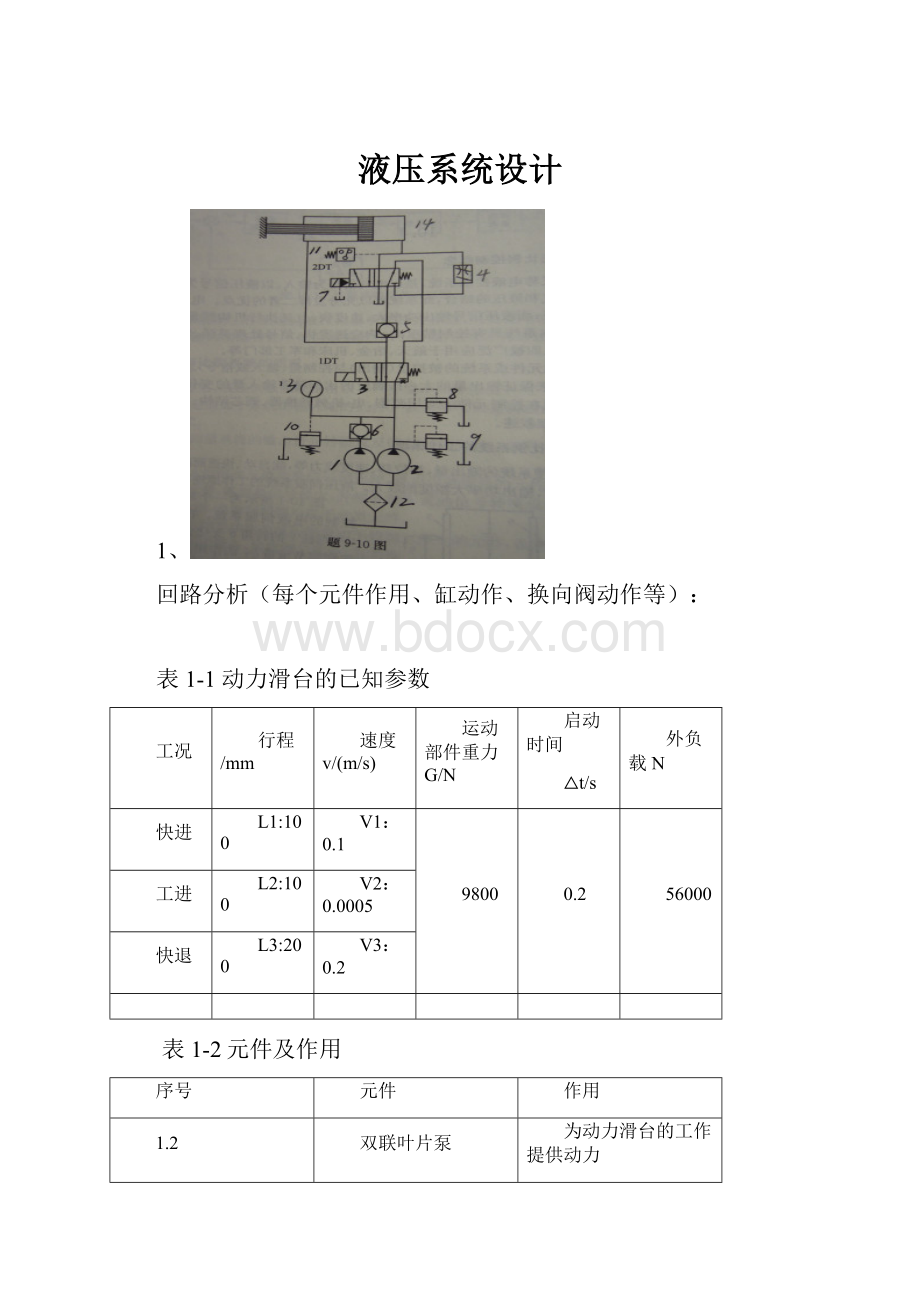
液压系统设计
1、
回路分析(每个元件作用、缸动作、换向阀动作等):
表1-1动力滑台的已知参数
工况
行程/mm
速度v/(m/s)
运动部件重力G/N
启动时间
△t/s
外负载N
快进
L1:
100
V1:
0.1
9800
0.2
56000
工进
L2:
100
V2:
0.0005
快退
L3:
200
V3:
0.2
表1-2元件及作用
序号
元件
作用
1.2
双联叶片泵
为动力滑台的工作提供动力
3
两位五通电液换向阀
开始阶段得电与2DT得电执行快进工况,然后当无杆腔压力增大,压力开关动作,使得1DT失电,2DT依然得电执行工进工况,工进结束,2DT失电,1DT得电执行快退工况。
4
两位四通电磁换向阀
5
调速阀
调节工进速度
6、7
单向阀
上:
工进时阻止小流量高压力泵的液压油通过溢流阀泄油
下:
阻止小流量高压力泵的液压油通过左下路溢流阀泄油
8
滤油器
过滤液压油
9、10、11
溢流阀
上:
工进时为有杆腔泄油
左下:
当执行工进工况时为大流量低压力泵泄油
右下:
为小流量低压力泵提供过载保护
12
压力表
观测系统压力
13
压力开关
按预设压力控制开断
14
液压缸
拖动执行元件工作
表1-3电磁阀-工况真值表
1DT
2DT
工况
失电
失电
空转
得电
得电
快进
失电
得电
工进
得电
失电
快退
表1-4动作时间计算表
工况
时间计算表达式
动作时间
快进
T1=L1/V1
1s
工进
T2=L2/V2
200s
快退
T3=L3/V3
1s
表1-5液压缸动作周期图表
原位
1
液压缸快进
2
液压缸工进
3
液压缸快退
01201
202
表1-6液压缸外负载计算结果
工况
计算公式
外负载/N
符号意义
启动
1690
静摩擦负载
动摩擦负载
惯性负载
加速
1480
快进
1980
工进
56980
反向启动
1960
加速
1980
快退
980
确定液压缸参数,编制工况图
参教材p198页表9-3初选液压缸的设计压力p1=6MPa。
为了满足工作台快退速度是快进的2倍,并减小液压泵的流量,今将液压缸的无杆腔作为主工作腔,并在快进时差动连接,则液压缸无杆腔与有杆腔的有效面积A1与A2应满足A1=3A2。
为防止工进结束时发生前冲,液压缸需保持一定回油背压。
参考表9-4暂取背压0.6MPa,并取液压缸机械效率ηcm=0.90则可计算出液压缸无杆腔的有效面积
由
A1=3A2P1=6,P2=0.6
F=56980
得
A1=109
D=118mm
按GB/T2348-1993,取标准值D=120mm;A1=3A2,故
活塞杆直径为
按GB/T2348-1993,取标准值D=120mm
同理,d=97.98mm,选d=100mm
所以A1=113平方厘米
A2=34.5平方厘米
A=A1-A2=78.5平方厘米
差动连接快进时,液压缸有杆腔压力p2必须大于无杆腔压力p1,其差值估取△p=p2-p1=0.5MPa,并注意到启动瞬间液压缸尚未移动,此时△p=0;另外,取快退时的回油压力损失为0.7MPa。
根据上述假定条件经计算得到液压缸工作循环中各阶段的压力、流量和功率(见表1-7),并可给出其工况图。
表1-7液压缸工作循环中各阶段压力及流量和功率
工作阶段
计算公式
负载F/N
回油腔压力p2/MPa
工作腔压力p1/MPa
输入流
q/(m3/s)
输入功率
P/kW
快进
启动
;
1960
---
0.50
---
---
加速
1480
0.93
0.43
---
---
恒速
980
0.86
0.36
0.785×10-5
290
工进
56980
0.6
5.60
0.56×10-6
31.4
快退
启动
1960
---
0.50
---
---
加速
1980
0.7
2.93
---
---
恒速
980
0.7
2.60
0.69×10-6
450
选择液压元、辅件1.液压泵及其驱动电机 首先确定液压泵的最高工作压力:
由液压缸的表1-7可以查得液压缸最高工作压力出现在工进阶段,p1=5.60MPa。
此时缸的输人流量较小,且进油路元件较少,故泵至缸间的进油路压力损失估取为∑△p=0.8MPa根据式(9-5)算得小流量泵的最高工作压力为Pp1=P1+∑△p=6.40MPa
大流量泵仅在快速进退时向液压缸供油,由图可知快退时液压缸的工作压力比快进时大,取进油路压力损失为∑△p=0.4MPa,则大流量泵最高工作压力为Pp2=2.93+0.4=3.33(MPa)然后确定液压泵的流量:
液压泵的最大供油量qp按液压缸的最大输入流量(0.785×10--3m3/s)进行估算。
根据式(9-6)取泄漏系数K=1.1,则qp=1.1×0.785×10-3=51.81L/min考虑到溢流阀的最小稳定流量为2L/min,工进时的流量为0.56×10-2m3/s(0.336L/min),则小流量泵的流量至少应为2.5L/min。
最后确定液压泵及其驱动电机的规格,根据以上计算结果查阅产品样本,选用规格相近的YB1-2.5/50型双联叶片泵。
由表1-7知,最大功率出现在快退阶段,取泵的总效率为ηP=0.8,则所需电机功率为
Pp=(pp×qp)/ηp=3.77(kW)
选用电动机型号:
查相关手册或电动机产品样本,选用规格相近的Y2-112M-4型封闭式三相异步电动机,其额定功率4kW。
表1-8液压缸在各阶段的实际进出流量、运动速度和持续时间
工作阶段
流量/(L/min)
速度/(m/s)
时间/s
无杆腔
有杆腔
快进
Q进=A1(qp1+qp2)/A
=75.6
q出=q进A2/A1
=23.1
v1=(qp1+qp2)/A
=0.111
T1=L1/v1
=0.90
工进
Q进=0.5
q出=q进A2/A1
=0.15
V2=q进/A1
=0.74×10-3
T2=L2/v2
=135.1
快退
Q进=(qp1+qp2)=52.5
q出=q进A1/A2
=172
V3=q进/A2
=0.254
T3=L3/v3
=0.787
管件尺寸与选定的标准元件油口尺寸相同。
油箱容量按式(9-11)计算,
V=ɑ×qp=6×52.5=315(L)
表1-9控制阀部件及辅助元件型号规格
序号
名称
通过流量(L/min)
额定流量
(L/min)
额定压力
/MPa
额定降压
/MPa
型号
1.2
双联叶片泵
——
2.5/50
6.3
——
YB1-2.5/50
3
两位五通电液换向阀
172
4
两位四通电磁换向阀
172
5
调速阀
<1
6
21
——
2FRM5
6
单向阀
75.6
115
31.5
0.2
S20A
7
单向阀
50
65
31.5
0.2
S15A
8
过滤器
52.5
9
溢流阀
<1
50
31.5
——
DBD6HP
10
溢流阀
2.5
250
31.5
——
DB10
11
溢流阀
2.5
250
31.5
——
DB10
12
压力表
——
——
——
——
K-6B
13
压力开关
按选定的液压元件接口尺寸确定管道直径d=18mm,进、回油管道长度均取为l=2m;取油液运动黏度v=1×10-4m2/s,油液密度ρ=0.9174×103kg/m3。
由表1-8查得工作循环中进、回油管道中通过的最大流量q=172L/min发生在快退阶段,由此计算得雷诺数。
得Re=2028<2300
故可推论出:
各工况下的进回油路中的液流均为层流。
将适用于层流的沿程阻力系数λ=75/Re=75πdv/(4q)和管道中液体流速v=4q/(πd2)代入沿程压力损失计算公式。
在管道具体结构尚未确定情况下,管道局部压力损失常按以下经验公式计算。
各工况下的阀类元件的局部压力损失按式(9-13)计算,即设
根据以上三式计算出的各工况下的进回油管道的沿程、局部和阀类元件的压力损失数值见表9-13。
表1-10压力损失数值
管路
各工况下的压力损失/(×105Pa)
快进
工进
快退
进油
1.051
0.00696
0.730
1.0051
0.000696
0.0730
1.775
5
0.317
3.8311
≈5
1.12
回油
0.321
0.00209
2.391
0.0321
0.000209
0.2391
0.406
6
2.38
0.727
≈6
5.0101
将回油路上的压力损失折算到进油路上,可求得总的压力损失,例如经折算得到的快进工况下的总的压力损失为
3.8311×105+0.727×105×(34.5/113)=4.053×105(Pa)
根据上述计算可知:
液压泵也即溢流阀的调整压力应为小流量泵工进阶段的液压缸工作腔压力和进油路压力损失之和,即
Pp1≥5.60+0.5=6.10(MPa)
大流量泵在快退时的工作压力Pp2最高,它是溢流阀9调压值的主要参考数据,即
Pp2≥2.93+0.11=3.04(MPa)
由表1-8的数据可看到,本液压系统在整个工作循环持续时间中,快速进退仅占1%,而工作进给达99%,所以系统效率、发热和温升可概略用工进时的数值来代表。
根据式(9-16)可算出工进阶段的回路效率
0.076
其中,大流量泵的工作压力Pp2就是此泵通过顺序阀卸荷时所产生的压力损失,因此它的数值为pp2=0.3×106×(50/65)2=0.178(MPa)
前己取双联液压泵的总效率ηp=0.80,现取液压缸的总效率ηcm=ηm=0.90,则按式(9-15)即可算得本液压系统的效率
0.8×0.076×0.90=0.054
足见工进时液压系统效率很低,这主要是由于溢流损失和节流损失造成的。
工进工况液压泵的输入功率为
518.2(W)
根据系统的发热量计算式(9-18)可算得工进阶段的发热功率
518.2×(1-0.08)=476.72(W)
按式(9-20),取散热系数(m•℃)算得系统温升为
10.56(℃)
设机床工作环境温度t=25℃,加上此温升后有t=25+
10.56=35.56℃,对照表9-6,在正常工作温度内,符合要求。
由于系统压力较低,执行元件速度不高,系统液压冲击不大,可不考虑。
表9-6各种液压系统允许油温