多用角架搁板注塑模具设计.docx
《多用角架搁板注塑模具设计.docx》由会员分享,可在线阅读,更多相关《多用角架搁板注塑模具设计.docx(61页珍藏版)》请在冰豆网上搜索。
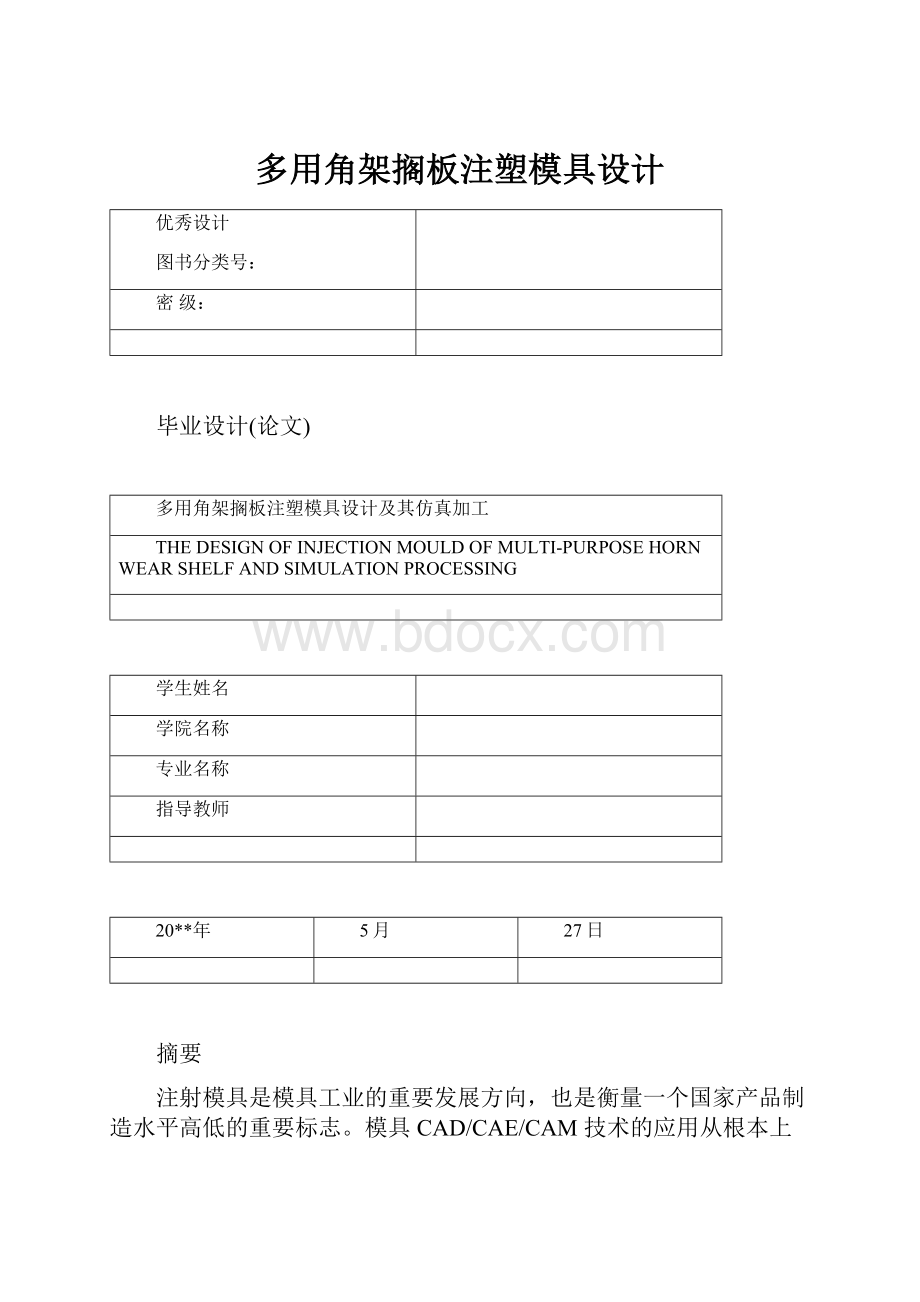
多用角架搁板注塑模具设计
优秀设计
图书分类号:
密级:
毕业设计(论文)
多用角架搁板注塑模具设计及其仿真加工
THEDESIGNOFINJECTIONMOULDOFMULTI-PURPOSEHORNWEARSHELFANDSIMULATIONPROCESSING
学生姓名
学院名称
专业名称
指导教师
20**年
5月
27日
摘要
注射模具是模具工业的重要发展方向,也是衡量一个国家产品制造水平高低的重要标志。
模具CAD/CAE/CAM技术的应用从根本上改变了传统的产品开发和模具生产方式,大大提高了生产效率、产品品质以及企业自身的竞争力。
本文根据多用角架搁板实物模型进行了模型特征重构,在此基础上基于PRO/E软件设计出一套合理的注射模具。
首先分析了多用角架搁板制件的工艺特点,包括材料性能、结构工艺性、成型特性与条件等,并选择了成型设备。
然后介绍了香皂盒注射模的分型面选择、型腔数目及布置形式,重点介绍了浇注系统、成型零件、冷却系统、脱模机构的设计。
然后选择模架,并对注射机的工艺参数进行了校核。
在此基础上,本文讲诉了如何运用Mastercam软件对多用角架搁板凸模进行仿真加工。
关键词注射模具;PRO/E;Mastercam;仿真加工
Abstract
Injectionmoldingisanimportantdirectionofdevelopmentofmoldindustries,italsoisanimportantindicatorofthelevelofonecountry’sindustry.TheapplicationofmoldingCAD/CAE/CAMfundamentallychangedthewayoftraditionalproductdevelopmentandmanufacturingmethod,improvedproductionefficiency,thequalityofproductsandcompetitivenessofinterprises.
Themodelwasreconstructedbasedontherealmulti-purposehornwearshelf.AppropriateinjectionmoldwasdesignedbasedonPRO/E.First,thetechnologicalcharacteristicsofthemulti-purposehornwearshelfwereanalyzed,includingmaterialproperties,theprocessofthestructure,formingcharacteristicsandconditions,andtheformingequipmentwereselected.Thenthepartinglinewasselected,thenumberofcavityandlayoutweredetermined.Aspecificintroductionwasmadeonthegatingsystem,thecoolingsystem,theformingpartsandthestrippinginstitutions.Thenthestandardmouldbaseswereselected,andcheckedthetechnologicalparametersoftheformingequipment.Onthisbasis,thispaperalsotellsabouthowtousetheMastercamtocompletethesimulationprocessingofmulti-purposehornwearshelf.
KeywordsInjectionmoldPRO/EMastercamsimulationprocessing
1绪论
1.1模具工业的地位和发展前景
塑料注射成型所用的模具称为注射成型模,简称注射模。
它是实现注射成型工艺的重要工艺装备。
塑料模具为模具总量近40%,而且这个比例还在不断上升。
这类模具主要是两类:
一类是大型模具,一类是精密模具。
大型模具主要是以汽车仪表板,保险杠和家电产品模具为代表的成型模具。
精密模具是以集成电路、塑封模具为代表的成型模具。
注射模具被欧美等发达国家誉为“磁力工业”。
很大部分工业产品依赖注射模具才得以规模生产、快速扩张,由于注射模具对社会生产和国民经济的巨大推动作用和自身的高附加值,世界模具工业,尤其是注射模具工业发展较快,当前全球模具工业的产值已经达到600亿~650亿美元,是机床工业产值的两倍,其中注射模具工业的产值已经达到240亿至260亿。
纵观发达国家对模具工业的认识与重视,我们感受到制造理念陈旧则是我国模具工业发展滞后的直接原因。
模具技术水平的高低,决定着产品的质量、效益和新产品开发能力,它已成为衡量一个国家制造业水平高低的重要标志。
因此,模具是国家重点鼓励与支持发展的技术和产品,现代模具是多学科知识集聚的高新技术产业的一部分,是国民经济的装备产业,其技术、资金与劳动相对密集。
目前,我国模具工业的当务之急是加快技术进步,调整产品结构,增加高档模具的比重,质中求效益,提高模具的国产化程度,减少对进口模具的依赖。
现代模具技术的发展,在很大程度上依赖于模具标准化、优质模具材料的研究、先进的设计与制造技术、专用的机床设备,更重要的是生产技术的管理等。
21世纪模具行业的基本特征是高度集成化、智能化、柔性化和网络化。
追求的目标是提高产品的质量及生产效率,缩短设计及制造周期,降低生产成本,最大限度地提高模具行业的应变能力,满足用户需要。
在科技发展中,人是第一因素,因此我们要特别注重人才的培养,实现产、学、研相结合,培养更多的模具人才,搞好技术创新,提高模具设计制造水平。
在制造中积极采用多媒体与虚拟现实技术,逐步走向网络化、智能化环境,实现模具企业的敏捷制造、动态联盟与系统集成。
我国模具工业一个完全信息化的、充满着朝气和希望而又实实在在的新时代即将到来。
1.2课题内容和意义
本次设计的课题设计内容主要包括以下几点:
1.进行多用角架搁板塑件的三维造型设计;
2.从塑料品种、塑件形状、尺寸精度、表面粗糙度等方面考虑注塑成型工艺的可行性和经济性,进行塑件成型的工艺性分析;
3.根据塑件的质量和模具型腔数大致确定模具的结构,初步确定注射机型号,了解注射机与模具有关的技术参数;
4.考虑塑件成型位置及分型面选择,模具型腔数,型腔的排列,流道布局及浇口位置设置来进行凸、凹模零件设计;
5.将模具三维模型导入CAM软件中,进行注塑成型模具三维型面的数控仿真加工;
6.由模具三维结构图绘制出二维装配图,依据装配图完成模具主要零件的设计和图样绘制。
本次毕业设计通过对注塑成型模具的设计,可了解常用塑料的性能、塑料制品的设计原则及方法,掌握注射模具常用结构的组成、特点及应用场合,并由此熟悉注射成型工艺及仿真加工的全过程。
通过学习现代化的设计制造方法,积极开展CAD/CAM技术在注射模具设计中的推广应用,从而提高自己进行模具设计的工作能力。
2塑件成型工艺性分析
2.1塑件结构分析
在家居用品中,搁板的使用越来越受欢迎,各式各样的搁板既可用作厨房碗碟的收纳工具、客厅的CD架、卧房床头的书架等实用工具,还可以是一件靓丽的装饰品,倘若使用得当,搁板可以瞬间为家居增色。
本设计中的多用脚架搁板能够用来放置塑料盆一类的日用品。
其结构外形如下图2-1所示,其椭圆形凸台是用来使得相同的搁板竖直连接在一起,方便您装拆且为您节省空间的同时,也已成为一件靓丽的装饰品。
正面反面
图2-1多用角架搁板外形
2.2塑件的工艺性分析
2.2.1塑件材料的选择
塑件的材料要在保证产品的使用性能、物理性能、力学性能、耐腐蚀性能和耐热性能的前提下,尽量选用价廉且成型性能又好的塑料。
该产品用于承载物品,要求有较好的力学性能,有较大的强度和刚性,屈服强度高,弯曲疲劳寿命要高;有稳定的化学性能,对接触物(水、洗化用品)有很好的耐腐蚀性,卫生程度较高,日常使用时无毒安全,成型工艺性较好,所选的塑料流动性好,易于成型,有较高的表面光泽;市场价格尽量低,产品有较大的利润空间和市场竞争力。
ABS常用作电器外壳,机械强度较高,但是耐热性差,洗浴时的较高温度会使该材料产生较大变形。
PA化学稳定性较差,注射成型时熔融温度范围窄,热稳定性差,温度控制较复杂。
PC价格昂贵,成本太高,化学稳定性差,不耐碱、酮、脂等,成型工艺较复杂,常用来制造光学零件。
PP价格低廉,化学稳定性好,机械强度较高,成型工艺性较好,主要用来制造日用品。
通过以上分析可以看出,PP是制造塑料置物架的最佳材料,几种常用塑料相关资料见表2-1。
表2-1几种常用塑料相关资料
塑件品种
结构特点
使用温度
化学稳定性
性能特点
成型特点
主要用途
ABS
线型结构
非结晶型
小于70℃
较好
机械强度较好,有一定的耐磨性。
但耐热性较差,吸水性较差
成型性能好,成型前原料要干燥
应用广泛,如电器外壳、汽车仪表盘、日用品等
聚酰胺(尼龙)
线型结构结晶型
小于70℃(尼龙6)
较好,不耐强酸和氧化剂,能溶于甲酚,苯酚,浓硫酸等
抗拉强度,印度,耐磨性,自润滑性突出,吸水性强
熔点高,熔融温度范围较窄,成型前原料要干燥.熔体黏度低,要防止溢料,制品易产生变形等特点
耐磨零件及传动件,如齿轮,凸轮等,电气零件中的骨架外壳,阀类零件
聚碳酸酯(pc)
线型结构非结晶型
小于130℃耐寒性好,脆化温度-100℃
有一定的化学稳定性,不耐碱,酮,酯等
透光率较高,介电性能好,吸水性小,力学性能好,抗冲击,抗蠕变性能突出,但耐磨性较差
熔融温度高,熔体粘度大,成型前原料需干燥,粘度对温度敏感,制品要进行后处理
在机械上用作齿轮,凸轮,蜗轮,滑轮等,电机电子产品零件,光学零件等
聚丙烯(pp)
线型结构结晶型
10-120℃
较好
耐寒性差,光养作用下易降解老化,力学性能比聚乙烯好
成型时收缩率大,成型性能较好,易产生变形等缺陷
板,片,透明薄膜,绳,绝缘零件,汽车零件,阀门配件,日用品等
PP塑料的相关参数见表2-2。
表2-2PP塑料相关参数
性能项目
试验条件
测试标准
测试数据
数据单位
基本性能
熔体流动速率
23℃,2.16kg
ASTMD-1238
30
g/10min
密度
---
ASTMD-1505
0.9
g/cm3
机械性能
拉伸屈服强度
50mm/min
ASTMD-638
270
Kg/cm2
弯曲模量
---
ASTMD-790
6000
Mpa
续表2-2
性能项目
试验条件
测试标准
测试数据
数据单位
机械性能
洛氏硬度
---
ASTMD-785
100
R标尺
弯曲强度
---
GB9341
>50
Mpa
热性能
维卡软化点
1kgf
ASTMD-1525
152
℃
热变形温度
4.6kg/cm2
ASTMD-648
105
℃
2.2.2塑件的壁厚
塑件的壁厚对其质量有很大的影响,壁厚过小不能满足使用强度和刚度的要求,而本产品对强度和刚度的要求较高。
壁厚太大则浪费原材料,在大批量生产时造成生产成本提高,利润空间降低;注射成型时则易造成塑件内部产生气穴,外部产生凹陷;冷却时需要更长的冷却时间,增加了冷却系统设计和加工的难度。
从以上诸方面考虑,应在满足使用的前提下对塑件进行最大限度的薄壁化。
同一塑件的壁厚应当尽可能一致,塑件壁厚不同将导致收缩不同,最终导致变形或开裂。
PP塑料最小壁厚及推荐壁厚见表2-5。
表2-5PP塑料最小壁厚及推荐壁厚
塑件材料
最小壁厚
小型零件推荐壁厚
中型零件推荐壁厚
大型零件推荐壁厚
PP
0.85
1.45
1.75
2.40—3.20
本产品属于中型塑件,推荐壁厚为1.75mm,但是考虑到塑件的力学要求,应使用较大壁厚,这里取壁厚为2mm。
2.2.3塑件的表面质量
塑件的表面粗糙度和外观质量决定了塑件的表面质量。
一般来说,原材料的质量、成型工艺和模具表面粗糙度都会影响到塑件的表面粗糙度,尤其是以型腔壁的表面粗糙度影响最大。
因此,模具的型腔壁表面粗糙度是塑件表面粗糙度的决定性因素。
产品的外观面应有很好的光泽度且非常光滑,对表面粗糙度要求较高,应不大于1.60,产品的内表面与使用无关且不影响外观,对表面粗糙度无太高要求,为了降低模具制造成本,凸模成型表面的粗糙度设计为3.20。
PP材料通过注射成型所能达到的表面粗糙度范围是0.10~1.60,满足塑料角架搁板的表面粗糙度要求。
使用注射成型时几种常用材料所能达到的塑件表面粗糙度见表2-3。
表2-3使用注射成型时几种常用材料所能达到的塑件表面粗糙度
材料
Ra参数范围/um
0.025
0.05
0.10
0.20
0.40
0.80
1.60
3.20
6.30
ABS
-----
-----
-----
-----
-----
-----
-----
PC
-----
-----
-----
-----
-----
-----
PA
-----
-----
-----
-----
-----
PP
-----
-----
-----
-----
-----
PE
-----
-----
-----
-----
-----
-----
-----
2.2.4塑件的精度等级
影响塑件精度的因素很多,如模具制造精度及其使用后的磨损程度,塑料收缩率的波动,成型工艺条件的变化等。
在一般生产过程中,为了降低模具的加工难度和模具的生产成本,在满足塑料使用要求的前提下将尽可能地把塑件尺寸精度设计得低一些。
目前我国颁布了工程塑料模塑塑料件尺寸公差的国家标准GB/T14486-1993。
该标准将塑件分成7个精度等级,MT1的精度要求最高,一般不采用。
见表2-4
表2-4PP材料模塑件公差等级
材料代号
模具塑料
公差等级
标注公差尺寸
未注公差尺寸
高精度
一般精度
PP
聚丙烯
MT3
MT4
MT6
MT2
MT3
MT6
MT2
MT3
MT5
根据此表和塑件的设计使用要求,塑件的精度选用MT3。
2.2.5塑件的脱模斜度
塑件冷却后产生收缩时会紧紧包在凸模上,或由于粘附作用紧贴在型腔内。
为了便于脱模,防止塑件表面在脱模时出现顶白、顶伤、划伤等,在塑件设计时应使其表面有合理的脱模斜度。
脱模斜度的选择要遵循以下原则:
(1)塑件精度要求高时,应采用较小的脱模斜度;
(2)较高较大的塑件尺寸,应选用较小的脱模斜度;
(3)形状复杂的、不易脱模的,应选用较大的脱模斜度;
(4)塑件的收缩率大的应选用较大的脱模斜度值;
(5)塑件壁较厚时,会使成型收缩增大,脱模斜度应采用较大数值。
常用塑料的脱模斜度见表2-6。
由于PP塑料的收缩率很大,所以应选择较大的脱模斜度,选择脱模斜度为3。
。
表2-6常用塑件的脱模斜度
塑料名称
脱模斜度
型腔
型芯
PEPPPA
25’—45’
20’—45’
HPVC
35’—40’
30’—50’
PSABSPOM
35’—1/30’
30’—40’
热固性塑件
25’—40’
20’—50’
2.3PP塑件的注射工艺
PP塑件的注塑工艺参数如下表2-7
表2-7PP塑件的注塑工艺参数
预烘干
不需要,如贮藏条件不好,在80℃下烘干1小时
温度
喂料区温度/℃
30~50
料筒/℃
后段
160~180
中段
1800~2000
前段
200~230
喷嘴/℃
220~300
熔料/℃
220~280
模具/℃
40~80
压力
注射/Mpa
70~120
保压/Mpa
50~60
背压/Mpa
5~20
续表2-7
预烘干
不需要,如贮藏条件不好,在80℃下烘干1小时
时间
注射/s
1~5
保压/s
20~50
冷却/s
20~50
成型周期/s
40~120
螺杆转速/
30~60
3分型面的选择
3.1分型面位置的确定
分型面是指分开模具取出塑件和浇注系统凝料的可分离的接触表面。
一副模具根据需要可能有一个或两个以上的分型面。
它的合理选择是塑件能够完好成型的条件,不仅关系到塑件的脱模,而且涉及模具结构和制造成本。
合理的分型面不但能满足制品各方面的性能要求,而且使模具结构简单,也会有令人满意的成本。
在选择分型面的时候,应该遵循以下几个原则:
(1)符合塑件脱模的基本要求,就是能使塑件从模具内取出,分型面位置应设在塑件脱模方向最大的投影边缘部位;
(2)分型线不影响塑件外观,即分型面应尽量不破坏塑件光滑的外表面;
(3)确保塑件留在动模一侧,利于推出且推杆痕迹不显露于外观面;
(4)应尽量避免形成侧孔、侧凹,若需要滑块成型,力求滑块结构简单,尽量避免定模滑块;
(5)确保塑件质量,例如:
将有同轴度要求的塑件部分放到分型面的同一侧等;
(6)满足模具的锁紧要求,将塑件投影面积大的方向放在定、动模的合模方向上,而将投影面积小的方向作为侧向分型面;
(7)合理安排浇注系统,特别是浇口位置;
(8)有利于模具加工。
从塑件模型可以看出,将塑件周边把手的最下端侧面作为分型面。
分析本产品的结构特点和使用要求,选择主分型面为塑件的上表面。
见图3-1。
图3-1分型面示意图
分型面设计方法有阴影曲面分型面、裙边分型面、侧面影像曲线分型面、复制曲面、延伸曲面、合并曲面等设计方法。
在主分型面的设计中,采用复制塑件上表面的方法,并进行相关的编辑。
具体设计过程为:
(1)复制塑件上表面。
(2)延伸塑件分型面边至工件表面。
(3)合并曲面,使分型面为一个整体。
应用Pro/e创建出的分型面见图3-2。
正面反面
图3-2主分型面
3.2型腔数目的确定
为了使模具与注射机的生产能力相配,提高生产效率和经济性,并保证塑件的精度,模具设计时应确定型腔数目。
型腔数目的确定一般遵循以下原则:
(1)型腔的数目及排列形式与浇注系统、冷却系统有关。
型腔的数目及排列形式的设计要考虑到后者的结构;
(2)模具加工条件好,加工精度高时可以增加型腔数目,反之应减少型腔数目;
(3)型腔越多,模具加工周期越长。
设计时要考虑加工周期;
(4)多型腔模具的可靠性及灵活性不如单型腔。
但在空间利用和能耗上优于单型腔;
(5)型腔的数目与塑件外形尺寸有关。
一般尺寸较小的塑件采用多型腔,尺寸较大的塑件采用少型腔,甚至单型腔;
(6)模具中每增加一个型腔,制品尺寸精度将降低4%。
型腔数目的确定要考虑到塑件精度。
多用角架搁板的外形尺寸较大,考虑到模具结构形式和模架的结构尺寸,以及制造费用和各种成本费等因素,应采用一模一腔。
4注射机型号的选择
4.1体积质量的计算
通过PRO/E建模设计分析计算塑件的质量属性,计算结果见图4-1。
图4-1塑件质量属性的计算
根据经验,浇注系统的凝料体积按照塑件体积的0.2~1倍来估算。
在该设计中,采用直流道,其结构简单,因此浇注系统的凝料按照塑件体积的0.3倍来估算,故一次注入模具型腔内的塑料熔体的总体积(单个塑件的体积和浇注系统的凝料体积之和)为
V总=(1+0.3)V塑=1.3⋅313.333cm3=407.333cm3式(4.1)
式中V总——表示型腔内的塑料熔体的总体积;
V塑——表示塑件的体积。
4.2注射机的选择
根据塑件体积估算注射机的公称注射量,计算如下:
V公=V塑/0.8=407.333/0.8=509.1cm3式(4.2)
式中V公——表示注射机的公称注射量。
根据以上计算,并考虑到模具尺寸和开模行程较大,初步选定公称注射量为1000cm3,型号为XS-ZY-1000的注射机,其主要参数见表4-1。
表4-1注塑机主要技术参数
理论注塑容量/cm3
1000
注射方式
螺杆式
螺杆柱塞直径/mm
85
注射行程/mm
260
注射压力/Mpa
121
模板最大厚度/mm
700
螺杆转速/(r/min)
21-83
模板最小厚度/mm
300
锁模力/KN
4500
电机功率/KW
40
模板最大行程/mm
700
拉杆空间/mm
650×550
4.3注射机相关参数的校核
(1)注射压力的校核
由表2-2可知,PP塑料所需的注射压力为70~120MPa,该注射机的公称注射压力为121MPa,则:
k1p0=1.3⋅90=117<121MPa式(4-3)
式中k1——表示注射压力安全系数k1=1.25~1.4,取k1=1.3;
p0——表示PP塑料所需的注射压力,取p0=90Mpa。
所以,注射机注射压力合格。
(2)锁模力的校核
塑件在分型面上的投影面积A。
应用PRO/E创建塑件在分型面方向上的投影面,并测量投影面积,见图4-2。
A=103502mm2。
图4-2塑件投影面积的计算
浇注系统在分型面上的投影面积为A浇,即流道凝料包括浇口在分型面上的投影面积,是塑件在分型面上的投影面积A的0.2~0.5倍。
由于本产品流道设计简单,无分流道,因此流道凝料投影面积可以适当取小。
A浇=0.2A=0.2⋅103502mm2=20700.4mm2式(4.4)
A总=A浇+A=20700.4mm2+103502mm2=124202.4mm2式(4.5)
F胀=A总p模=124202.4mm2⋅22Mpa=2292.45KN式(4.6)
式中F胀——表示模具型腔内的胀型力;
p模——模具型腔内的压力,通常取注射压力的20%~40%,范围是20~40Mp。
对于粘度较大的精度较高的塑料制品应取较大值,PP属于低等粘度、精度要求一般的塑件,因此取22MPa作为p的值。
由表4-1可知注射机的公称锁模力F锁=4500KN。
锁模力安全系数k2=1.1~1.2,这里取k2=1.2,
k2
F胀=1.2