难加工材料加工技术.docx
《难加工材料加工技术.docx》由会员分享,可在线阅读,更多相关《难加工材料加工技术.docx(17页珍藏版)》请在冰豆网上搜索。
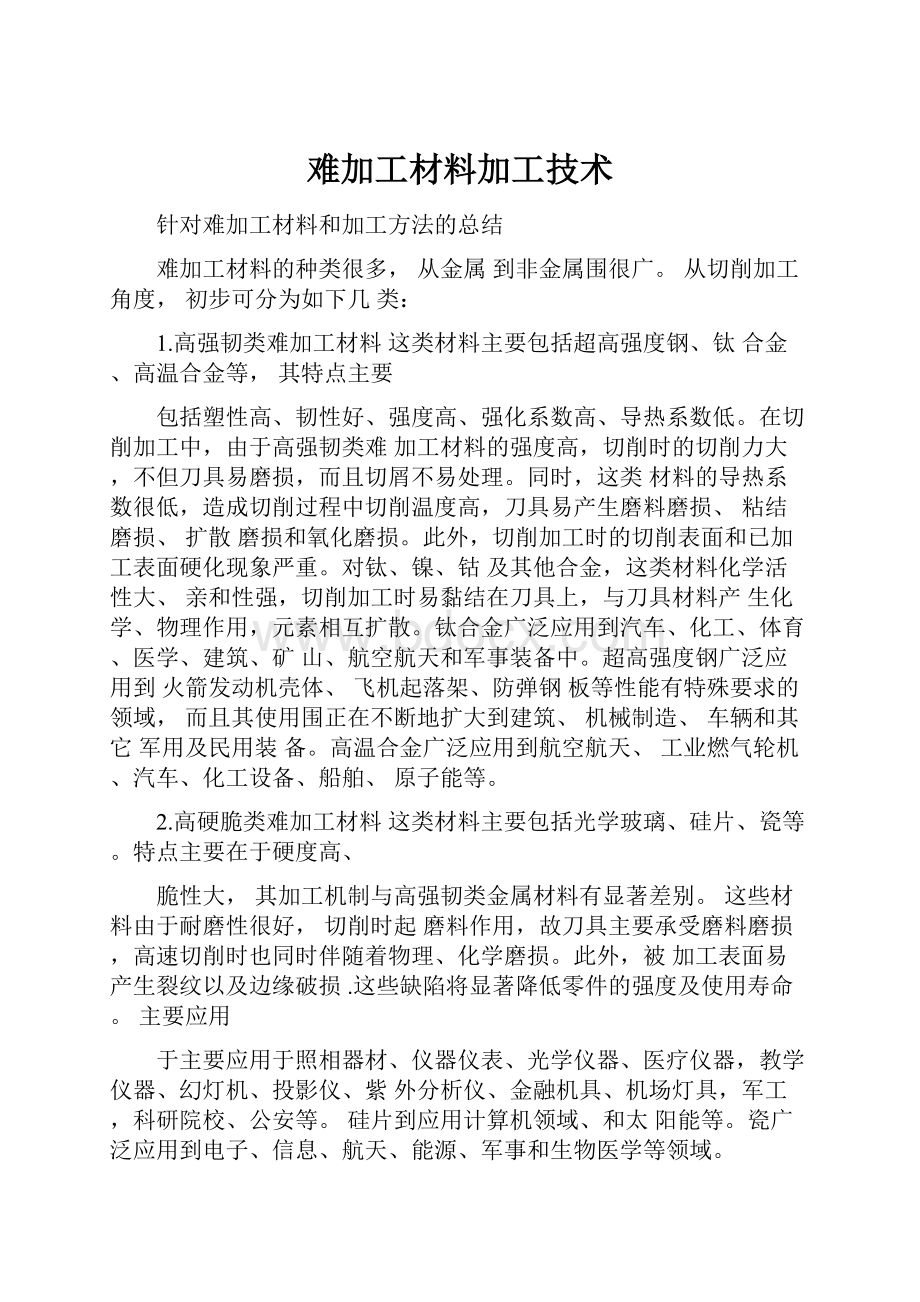
难加工材料加工技术
针对难加工材料和加工方法的总结
难加工材料的种类很多,从金属到非金属围很广。
从切削加工角度,初步可分为如下几类:
1.高强韧类难加工材料这类材料主要包括超高强度钢、钛合金、高温合金等,其特点主要
包括塑性高、韧性好、强度高、强化系数高、导热系数低。
在切削加工中,由于高强韧类难加工材料的强度高,切削时的切削力大,不但刀具易磨损,而且切屑不易处理。
同时,这类材料的导热系数很低,造成切削过程中切削温度高,刀具易产生磨料磨损、粘结磨损、扩散磨损和氧化磨损。
此外,切削加工时的切削表面和已加工表面硬化现象严重。
对钛、镍、钴及其他合金,这类材料化学活性大、亲和性强,切削加工时易黏结在刀具上,与刀具材料产生化学、物理作用,元素相互扩散。
钛合金广泛应用到汽车、化工、体育、医学、建筑、矿山、航空航天和军事装备中。
超高强度钢广泛应用到火箭发动机壳体、飞机起落架、防弹钢板等性能有特殊要求的领域,而且其使用围正在不断地扩大到建筑、机械制造、车辆和其它军用及民用装备。
高温合金广泛应用到航空航天、工业燃气轮机、汽车、化工设备、船舶、原子能等。
2.高硬脆类难加工材料这类材料主要包括光学玻璃、硅片、瓷等。
特点主要在于硬度高、
脆性大,其加工机制与高强韧类金属材料有显著差别。
这些材料由于耐磨性很好,切削时起磨料作用,故刀具主要承受磨料磨损,高速切削时也同时伴随着物理、化学磨损。
此外,被加工表面易产生裂纹以及边缘破损.这些缺陷将显著降低零件的强度及使用寿命。
主要应用
于主要应用于照相器材、仪器仪表、光学仪器、医疗仪器,教学仪器、幻灯机、投影仪、紫外分析仪、金融机具、机场灯具,军工,科研院校、公安等。
硅片到应用计算机领域、和太阳能等。
瓷广泛应用到电子、信息、航天、能源、军事和生物医学等领域。
3.兼具高强韧和高硬脆类难加工材料这类材料主要包括金属基复合材料、瓷基复合材料
等。
其特点主要包括具有高比强度、比模量,良好的导热性、导电性、耐磨性、高温性能,低的线膨胀系数,高的尺寸稳定性等。
在复合材料的高效机械加工中会出现一些常规材料所没有的问题,如增强相硬且脆(或坚韧),使刀具磨损大;某些基体材料韧且不导热,加工时产生的热量不易散发,钻刀具;层压复合材料在加工时极易分层等。
根据这些特点,加工时应采取相应的措施,如选择合适的刀具和合理的加工余量,制定专门的加工工艺,采取适当的加工润滑和冷却措施。
并设计专用的加工夹具以保证加工质量。
对以上难加工材料还是主要用机械加工来实现,下面详细介绍加工方法,实现难加工材料的有效加工,1.关键在于优选刀具材料:
高性能高速钢、新型硬质合金、涂层刀具、瓷刀具、CBN刀具和金刚石刀具;2.选择合适的刀具几何参数;3.采用适当的冷却润滑条件;4.采用优化的加工参数。
高速钢Highspeedsteel:
高速钢可以锻造,淬火前可以切削加工,强度高,所以广泛用于齿轮刀具、螺纹刀具、拉刀等复杂刀具。
高性能高速钢:
增加V、Co、Al、稀土等元素,提高高速钢的性能。
高速钢M42:
是当前航空航天生产中应用较广泛的高性能高速钢,
Al高速钢501:
在加工高强度钢等难加工材料时也具有良好的性能。
粉末冶金高速钢:
粉末冶金高速钢无碳化物偏析,晶粒粉细小均匀,杂质含量少,抗弯强度比冶炼高速钢提高2倍以上,在600℃时的高温硬度高出2~3HRC,刀具寿命提高0.5~2倍。
进口牌号ASP2060、ASP2080,国产牌号M42-P硬质合金Cementedcarbide:
当前硬质合金刀具材料的进展主要体现在以下几个方面
涂层技术:
涂层技术分为化学气相涂层(CVD)和物理气相涂层(PVD)。
涂层材料:
传统:
C、N或O的二元化合物,如TiC、TiN、Al2O3等。
新型多元化合物:
TiCN、TiAlN、TiCrN、AlCrN、TiAlSiN氮化碳(CNx)、氮化物等,软涂层刀具:
MoS2、WS2。
涂层结构:
多层沉积、复合涂层、纳米涂层,涂层数达2000层,每层厚度为2.5nm。
细化晶粒:
减小晶粒尺寸可以提高硬质合金的硬度、耐磨性、韧性。
普通硬质合金的晶粒尺寸约10微米以下,细晶粒<1微米、超细晶粒<0.5微米。
梯度材质:
采用梯度材质可以兼顾硬质合金的硬度和韧性。
梯度结构硬质合金具有特殊的结构或成分梯度变化,对不同的部位赋予不同的性能,使整体制品获得优异的综合机械性能。
瓷刀具Ceramic高速钢与硬质合金的主要成分钨、钴资源在全球围日趋枯竭,瓷刀具材料使用的主要成分铝、硅、氧、氮等在地壳中含量丰富;
分类:
氧化铝基瓷、氮化硅基瓷、氧化铝氮化硅复合瓷(Sialon)和晶须增韧瓷。
优点:
很高的硬度和耐磨性,硬度达93~95HRA,适于加工50~65HRC的高硬度材料;高温性能好,在1200℃的高温下仍能进行切削;与金属的亲和力小,具有良好的抗粘结性能;化学稳定性好,扩散磨损小,抗氧化能力好;摩擦系数也低于硬质合金。
缺点:
强度和断裂韧性较低,脆性较大,导热性差,抗热震性不高。
发展和预测:
提高瓷刀具的力学性能的研究:
采热压和热等静压工艺,加入各种增韧补强相,如金属碳化物、氮化物、硼化物、稀土元素及金属和晶须等。
一些瓷刀具的强度和韧性已接近硬质合金。
瓷刀具占刀具市场的份额将增加到15%~20%,金属切削加工工业即将进入新的“石器时代”。
超硬刀具:
立方氮化硼刀具和金刚石刀具CBN&Diamond
立方氮化硼刀具材质:
立方氮化硼(CBN)是氮化硼(BN)的同素异构体,其结构、化学键类型晶格常数与金刚石相似,因此具有与金刚石相近的硬度和强度。
PCBN刀具粘结剂组分包括金属粘结剂、瓷粘结剂和金属-瓷组合粘结剂三大类,CBN含量在40%~95%之间,CBN晶粒尺寸发展到微米和亚微米级。
不同的粘结剂组分、CBN含量和晶粒尺寸适应于不同的工件材料和
不同的加工条件。
性能:
硬度:
单晶的硬度为8000~9000HV,聚晶烧结体PCBN的硬度为3000~5000HV。
在切削耐磨材料时其耐磨性是硬质合金刀具的30~50倍;耐热性:
达1400℃~
1500℃,在800℃时的硬度还高于瓷和硬质合金的常温硬度;其它:
较好的化学稳定性、较好的导热性和较低的摩擦系数,用途:
硬态干式切削难加工材料,加工硬度高于50HRC的
材料,实现高硬度零件的以切代磨加工。
金刚石刀具:
特点:
是最硬的刀具(8000~12000HV),高的导热性,低的热胀系数,高的弹性模量和较低的摩擦系数。
用途:
加工有色金属和非金属材料效果良好。
但其主要成分C,在Fe中有较高
的溶解度,所以不能加工铁族金属。
分类:
单晶、聚晶(PCD)、CVD厚膜和CVD涂层四类单晶
金刚石刀具:
用单个金刚石大晶粒做刀具,各向异性,主要用于精密、超精密加工。
PCD刀
具:
将金刚石粉末在高温高压下压制成多晶体压块作为刀片,其晶粒呈无序排列,不具方向
性。
CVD厚膜金刚石刀具:
利用化学气相沉积(CVD)技术沉积厚度达0.5~1mm的无衬底的刚
石厚层膜,将厚膜切割后钎焊在硬质合金基片上作为刀片。
同PCD相比,其热稳定性更好,
但脆性较高。
因导电性差,不能用电加工(EDM)制造成形。
其应用领域与PCD相近,由于其高
纯度以及由此带来的耐磨性和热稳定性的提高,所以更适应于高耐磨工件的加工。
CVD涂层
金刚石刀具:
是在硬质合金基体上采用CVD技术沉积小于30μm的薄膜。
目前CVD涂层金刚石产品的市场还不是很大。
钛合金及其加工技术刀具材料及使用条件:
低速加工:
高钴高速钢、高钒高速钢;中速加工:
细晶粒硬质合金,此时粘接磨损严重,不宜采用含Ti刀具,可采用Al2O3涂层刀具;高速加工:
某些牌号的CBN刀具;涂层硬质合金刀具、基体含钛硬质合金刀具或含钛涂层硬质合金刀具。
刀具几何参数由于回弹严重,后角要大,>15°;因后角大,前角不能过大,以保证刃口强度;采用大螺旋角铣刀。
切削液含极压添加剂的油基切削液,但建议不含氯;高压(100bar)喷射冷
却液可成倍提高刀具耐用度。
注意:
低速下YT14和TC4具有更强的粘接倾向,易于发生粘接磨损,因而YT14的磨损率高于YG8,含钛刀具不适于加工钛合金;高速下YG8和TC4的高元素差别易于导致扩散磨损,因而YT14的磨损率低于YG8,含钛刀具适于加工钛合金;含钛刀具不适于加工钛合金的传统不全面,需要补充修改。
高温合金及其加工技术
刀具材料及使用条件:
拉刀、丝锥等:
钴高速钢(M42),V=10m/min;超细晶粒硬质合金、涂层硬质合金:
V=30~70m/min,硬度增高速度降低;Si3N4瓷,Sialon瓷、Al2O3+TiC复合瓷、SiC晶须增韧Al2O3瓷(肯纳KY4300),V>200m/min;(低速时磨损加剧),瓷刀具用于半精加工;高含量CBN刀具刀具几何参数:
车刀前角<10°,后角15°左右;铣刀前角10°左右,后角15°左右,螺旋角30~45°;瓷刀具、CBN刀具务必采用负前角。
切削液:
高速钢刀具采用水基切削液,
以冷却为主,防止刀具热塑变形;硬质合金刀具采用极化切削油,抑制粘接、扩散磨损;瓷、CBN刀具慎用切削液:
利用工件热软化,使切削容易,刀具韧性差,防止热疲劳和激冷
裂纹。
高强度钢加工技术刀具材料选择高速钢:
Co高速钢、Al高速钢、粉末冶金高速钢、涂层高速钢;硬质合金:
添加钽、铌或稀土元素P类合金、P类涂层合金及TiC基和Ti(C、N)基合金;瓷刀具:
Al2O3基瓷,如Al2O3+TiC复合瓷(Si3N4瓷效果不好);CBN刀具:
低含量高强度材质。
刀具几何参数要求刃部强度高,所以硬质合金刀前角-2°~-4°,瓷和CBN-10°左右;刀尖圆弧半
径:
粗加工时1~2mm;精加工时0.5~0.8mm。
切削用量:
切削速度是加工45钢时的30%左右,强度越高,速度越低;高速钢<10m/min,硬质合金30~80m/min,瓷、CBN可达100~150m/min以上,但一般用于小切深精加工。
断屑技术:
选择合理的断屑槽或断屑台,以断屑为目标进行切削用量优化,采用振动断屑等强制断屑技术。
冷却润滑技术:
在一定切削用量围车削高强度钢时,干切削可以显著提高刀具耐用度,其机理可能是:
在一定切削温度下刀具和工件材料硬度差增大;刀具的磨损以磨料磨损为主时,减小润滑效果使得粘接区增大、滑动区减小,从而减小磨料磨损。
碳纤维复合材料加工技术切削加工性特点MachinabilityofCFRP碳纤维硬度达HV600以上,接近高速钢硬度,对刀具造成磨料磨损;加工过程没有强烈塑性变形,切削温度低,不会发生粘接磨损、扩散磨损;材质各向异性,纤维向强度高,纤维间、层间强度低,易于发生撕裂、分层等特有的加工质量问题;切削加工产生大量有害粉尘,需要加以防护。
刀具选择:
高速钢刀具无法使用,一般采用K类硬质合金刀具,最佳刀具是
金刚石刀具。
关键:
刃口保持锋利,可切断纤维,而不是挤断。
切削用量:
必须高速加工V=600~6000m/min;关键:
控制V/Vf比值足够大。
“快刀斩乱麻”快:
1)锋利,2)高速。
玻璃、硅片、瓷加工技术
1)切削加工
瓷材料的切削加工不仅适用于半烧结体瓷,也适用于完全烧结体瓷。
半烧结体瓷的切削加工是为了尽可能减少完全烧结体瓷的加工余量,从而提高加工效率,降低加工成本。
日本的研究人员使用各种刀具在不同温度下对Al2O3瓷和Si3N4瓷半烧结体进行了切削试验。
试验中根据不同的加工要求,采用了干式切削与湿式切削等方法,获得了有价值的研究成果。
国外一些研究者针对完全烧结体瓷的切削加工进行了试验研究。
日本的研究人员在使用聚晶金刚石刀具对Al2O3瓷与Si3N4瓷进行切削试验时发现,粗粒聚晶金刚石刀具在切削过程中磨损较小,加工效果较好;在使用金刚石刀具切削ZrO2瓷时,达到了类似于切削金属
时的效果。
他们还探讨了瓷塑性切削极限问题,指出当Al2O3瓷的临界切削深度apmax=
2μm时,SiC瓷的apmax=1μm,Si3N4瓷的apmax=4μm(ap>apmax时,瓷材料会产生脆性破坏;ap美国的研究人员对单晶锗进行了一系列金刚石车削试验,成功地实现了脆性材料的塑性超精密车削,并提出了临界切削厚度的计算公式。
用金刚石刀具切削脆性材料并获得高质量的加工表面是近十几年来发展起来的新技术,通常称为脆性材料的超精密车削加工。
2)研磨、抛光加工
研磨、抛光加工是采用游离磨料对被加工表面材料产生微细去除作用以达到加工效果的一种超精加工方法。
在瓷材料的超精加工与光整加工中,特别是在用于瓷轴承的瓷球的精密加工中,研磨、抛光加工有着不可替代的位置。
光学玻璃、蓝宝石等光学材料,硅片、GaAs基片等半导体材料,Al2O3瓷、Si3N4瓷等瓷材料的镜面加工大多采用研磨、抛光加工方法。
从材料的去除机理上看,研磨加工是介于脆性破坏与弹性去除之间的一种加工方法,而抛光加工基本上是在材料的弹性去除围进行。
研磨、抛光加工由于材料去除量小,加工效率低,一般只用于超精加工的最终工序。
研磨、抛光加工的材料去除率与被加工材料的韧性有较大关系,韧性越高,加工效率越低。
3)ELID磨削加工
ELID磨削技术是由日本物理化学研究所的大森整等人于1987年提出的一种磨削新工艺,其基本原理是利用在线的电解作用对金属基砂轮进行修整,即在磨削过程中在砂轮和工具电极之间浇注电解磨削液并加以直流脉冲电流,使作为阳极的砂轮金属结合剂产生阳极溶解效应而被逐渐去除,使不受电解影响的磨料颗粒凸出砂轮表面,从而实现对砂轮的修整,并在加工过程中始终保持砂轮的锋锐性。
ELID磨削技术成功地解决了金属基超硬磨料砂轮修整的难题,同时在线电解的微量修整作用使超细粒度砂轮在磨削过程中能保持锋锐性,为实现稳定的超精密磨削创造了有利条件。
日本的研究人员使用#8000(最大磨粒直径约为2μm)铸铁基金刚石砂轮对硅片进行磨削,获得了最大表面粗糙度值为0.1μm的高精表面。
使用青铜基砂轮对瓷材料进行精密磨削也达到了相同的加工效果。
工业大学采用ELID磨削技术对硬质合金、瓷、光学玻璃等脆性材料实现了镜面磨削,磨削表面质量与在相同机床条件下采用普通砂轮磨削相比大幅度提高,部分工件的表面粗糙度Ra值已达到纳米级,其中硅微晶玻璃的磨削表面粗糙度可达Ra0.012μm。
这表明ELID磨削技术可以实现对脆性材料表面的超精加工,但加工过程中仍存在砂轮表面氧化膜或砂轮表面层的未电解物质被压入工件表面而造成表面层釉化及电解磨削液配比改变等问题,有待于进一步研究解决。
4)塑性法加工
传统的材料去除过程一般可分为脆性去除和塑性去除两种。
在脆性去除过程中,材料去除是通过裂纹的扩展和交叉来完成的;而塑性去除则是以剪切加工切屑的形式来产生材料的塑性流。
对于金属的加工,塑性切削机理很容易实现,而对于脆性材料如工程瓷和光学玻璃等,采用传统的加工技术及工艺参数只会导致脆性去除而没有显著的塑性流,在超过强度极限的切削力作用下,材料的大小粒子发生脆性断裂,这无疑将影响被加工表面的质量和完整性。
由加工实践可知,在加工瓷等脆性材料时,可采用极小的切深来实现塑性去除,即材料去除机理可在微小去除条件下从脆性破坏向塑性变形转变。
超精加工技术的最新进展已可将加工进给量控制在几个纳米,从而使脆性材料加工的主要去除机理有可能由脆性破坏转变为塑性流。
塑性切屑变形过程可以显著降低次表面(表层)破坏,这种硬脆材料的新型加工技术
称为塑性法加工。
近年来,许多学者应用金刚石磨削方法对脆性材料塑性方式磨削的理论和工艺、脆-塑
性转变、材料特性、切削力和其它参数的关系进行了系统研究,研究重点是被加工零件的塑性方式表面形成机理和几何精度,其中包括相关机床和砂轮技术的研究与开发。
1991年,
英国国家物理实验室的研究人员首先采用四面体(Tetraform)结构并应用具有良好工程性的减振机理来设计机床的主要结构,研制出世界上第一台Tetraform-1型超精密磨床。
用该
磨床对瓷、硅片和单晶石英试件进行了大量塑性磨削试验,获得了高质量的样品,其特点是:
(1)可采用相对较大的切深(大至10μm)进行加工;
(2)表面几何形状精度高,试件周围几乎没有碾痕;(3)机床可在无环境隔离条件下磨削高质量试件;(4)次表面破坏深度仅为传统磨削的1%~2%,甚至小于抛光加工对光学元件的影响。
基于Tetraform原理,1995年英国
Fra-zer-Nash咨询和Granfield精密工程联合研制了Tetraform-2型多功能磨床。
发展趋势表
明,脆性材料塑性加工技术在超精加工领域有着巨大的应用潜力。
随着现代科学技术的发展,脆性材料在现代高技术行业的诸多领域,特别是在航空航天、光学及电子领域中,具有十分重要的作用,而且往往对工件的加工精度和表面质量有非常高的要求。
但是到目前为止,脆性材料的加工仍然是一件困难的事情。
因为它们最突出的一个特性,就是材料脆性高,断裂韧性低,材料的弹性极限和强度非常接近。
当材料所承受的载荷超过弹性极限时,就发生断裂破坏,在己加工表面产生裂纹和凹坑,严重影响其表面质量和性能【1】。
所以,脆性材料的可加工性极差。
过去,人们一直沿用古老的研磨、抛光工艺,对脆性材料进行光整加工。
这些加工方法生产效率低,加工精度不易保证,而且加工过程不易实现计算机控制,对于曲面形状复杂的工件,甚至无法加工。
因此,已经远远不能适应现代高科技发展和高效率的要求。
超精密加工,主要包括超精密切削(车、铣)、超精密磨削、超精密研磨(机械研磨、机械化学研磨、研抛、非接触式浮动研磨、弹性发射加工等)以及超精密特种加工(电子束、离子束以及激光束加工等)。
上述各种方法,均能加工出普通精密加工所达不到的尺寸精度、形状精度和表面质量。
每种超精密加工方法,都是针对不同零件的要求而选择的【2】。
特种加工是应用物理的(力、热、声、光、电)或化学的方法,对具有特种要求(如高精度)或特殊加工对象(如难加工的材料、形状复杂或尺寸特微小的材料、刚度极低的材料)进行加工的手段
(1)不用机械能这些加工方法
与工件的机械性能无关,故可加工各种高性能的材料;
(2)非接触加工,工件不承受大
的作用力;(3)微细加工,工件表面质量高。
加工余量的去除是微细进行,不仅可加工曲
面狭缝,还能获得高精度、极低粗糙度的加工表面;(4)简单进给运动,加工复杂型面工
件;(5)各种加工方法可以复合成新的加工工艺,以便于推广。
由于特种加工技术具有
常规加工技术无法比拟的优点,在难切削材料、【3】复杂型面、精细表面的加工中已成为重要的工艺手段。
一、特种加工在绝缘工程瓷加工中的应用工程瓷材料因具有高强度、高硬度、质轻、耐磨、耐高温和耐腐蚀等特性,而被日益广泛地应用于电子、机械、冶金、化工及航空航天等领域中。
但由于工程瓷具有很高的硬度和较大的脆性,给其成形加工带了很大的困难。
机
械磨削是目前最常用的工程瓷加工方法,该加工方法需用昂贵的金刚石砂轮和高刚度的磨
床,加工成本高、效率低,且磨削时砂轮和工件之间存在强烈的作用力,易使工件表面产生微
裂纹而降低零件的使用寿命。
为此,人们开展了绝缘工程瓷的激光加工、超声加工、电火
花加工、等离子弧加工、磁力研磨,以及相关的相复合加工等技术,并取得了较大的研究进
展【4】。
1.激光加工工程瓷目前国外学者对瓷材料激光加工技术的研究主要集中在打孔、切割、划线和型腔加工等方面。
洪蕾等人用自行研制的机械斩光盘调QCO2,冲激光器对Si3N4瓷切割试验表明,在高峰值能量(≥15kW)、短脉冲宽度(1μs)、高脉冲频率(20kHz)和适当的平均功率(300W)条件下,采用高速(>220mm/s)多次重复走刀切割工艺,可以得到无裂纹的精细切口。
可心等人采用0.25MPa氧气作辅助气体,用800W的连续波CO2激光在厚度13.5mm的氮化硅瓷上加工出了直径0.72mm的无损伤深孔,深径比达18.75[5]。
TsaiChwan2Huei等人提出了基于裂纹加工单元的激光铣削方法,他们采用CO2和Nd:
YAG激光器对Al2O3瓷进行了基于裂纹加工单元的激光铣削加工,并在Al2O3瓷零件上加
工出了形状较复杂的型腔。
研究结果表明,采用该方法进行激光铣削所需要的功率比通常
的方法低。
HenryMatt等人对TBC瓷、聚晶金刚石、硬质合金和不锈钢等材料的激光铣削工艺进行了试验研究。
为把激光加工技术更好地应用于瓷加工中,人们还探讨了激光预热辅助切削或磨削等方法,其目的是增强瓷被加工部位的韧性,以达到降低切削或磨削力、提高加工效率和质量等目的。
I.D.Marinescu等人对Al2O3、Ferrite、ZrO2和Si3N44种材料进行了激光预热磨削试验,发现激光预热磨削不仅能减少磨削过程中温度的影响作用,而
且还能降低瓷的硬度,增大去除量而不引起磨削裂纹。
美国Purduce大学的C.J.Rozzi等人对激光辅助切削工程瓷技术进行了研究,建立了激光辅助切削ZrO2、Si3N4等瓷材料的瞬时三维温度场传递的物理、数学模型,并总结出了相应的加工规律。
2.超声加工工程瓷与电火花加工、电解加工、激光加工等特种加工技术相比,超声加工既不依赖于材料的导电性,又没有热物理作用,加工后工件表面无组织改变、残余应力及烧伤
等现象等发生;加工过程中宏观作用力小,适合于加工不导电工程瓷。
T.B.THOE等人对超
声加工Al2O3、ZrO2、SiC等瓷的工艺规律和加工机理进行了研究,给出了的研究结果,
并用超声加工技术在Si3N4瓷上加工出了航空航天用的涡轮叶片。
研究资料表明,采用超声磨削工程瓷时,当磨削深度小于某临界值时,工程瓷的去除机理与金属磨削相似,工件材料在磨刃的作用下通过塑性流动形成切屑,避免了较深变质层的形成,塑性磨削可以获得Ra
<0.01μm的表面质量。
超声磨削工程瓷的优点是加工效率比普通磨削高一倍以上,可采用
较大的磨削用量,能有效防止砂轮堵塞,减少砂轮的修整时间。
3.3.电火花加工工程瓷在用电火花工艺加工工程瓷方面,日本长冈技术科学大学福泽康与丰田工业大学毛利尚武的研究成果最具有代表性,他们提出了用辅助电极的方法加工绝缘
瓷材料。
该方法是利用