四冲程发动机活塞连杆组设计.docx
《四冲程发动机活塞连杆组设计.docx》由会员分享,可在线阅读,更多相关《四冲程发动机活塞连杆组设计.docx(9页珍藏版)》请在冰豆网上搜索。
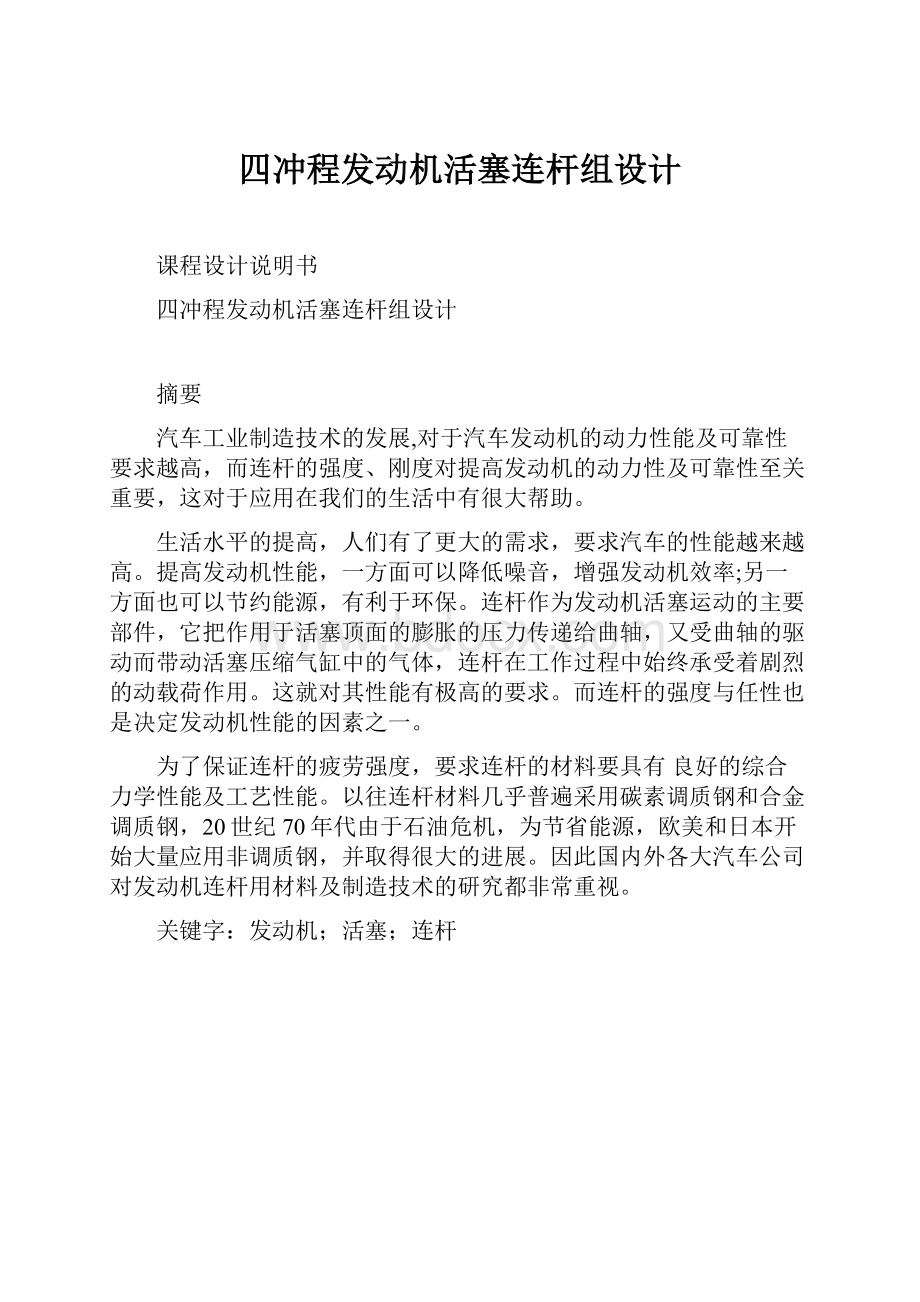
四冲程发动机活塞连杆组设计
课程设计说明书
四冲程发动机活塞连杆组设计
摘要
汽车工业制造技术的发展,对于汽车发动机的动力性能及可靠性要求越高,而连杆的强度、刚度对提高发动机的动力性及可靠性至关重要,这对于应用在我们的生活中有很大帮助。
生活水平的提高,人们有了更大的需求,要求汽车的性能越来越高。
提高发动机性能,一方面可以降低噪音,增强发动机效率;另一方面也可以节约能源,有利于环保。
连杆作为发动机活塞运动的主要部件,它把作用于活塞顶面的膨胀的压力传递给曲轴,又受曲轴的驱动而带动活塞压缩气缸中的气体,连杆在工作过程中始终承受着剧烈的动载荷作用。
这就对其性能有极高的要求。
而连杆的强度与任性也是决定发动机性能的因素之一。
为了保证连杆的疲劳强度,要求连杆的材料要具有 良好的综合力学性能及工艺性能。
以往连杆材料几乎普遍采用碳素调质钢和合金调质钢,20世纪70年代由于石油危机,为节省能源,欧美和日本开始大量应用非调质钢,并取得很大的进展。
因此国内外各大汽车公司对发动机连杆用材料及制造技术的研究都非常重视。
关键字:
发动机;活塞;连杆
1连杆组设计
1.1连杆的材料
活塞连杆材料多数采用45的,跟40Mn2等优质的钢材,最近几年,也会采用粉末冶金,本连杆采用40MnB的,运用钢材制造的磨锻,来制造毛坯。
这里有两种方法可以进行锻造,一种是连杆体和盖分开锻造,分开锻造具有较高的强度,金属纤维都是连续的,这个是从锻造的材料来看的,而连杆体整体锻造金属纤维是断裂的,这样的话,强度就消减了很多。
整体锻造跟分开锻造主要还是取决于材料设备的能力,整体的锻造,它是需要有很大的锻造设备来进行的,而分开锻造是不需要的。
整体锻造一般还是比较多用的,整体锻造无形中增加了切开连杆的工作步骤,但是它也有优点,可以提高材料的利用率,加工起来也较为方便,虽然需要大的锻造设备,但是方便简单易操作,仅仅需要一谈锻造设备,一次就可以完成。
这样利于管理,组织起来也是比较方便的。
大多数情况下,多采用连杆整体锻造工序。
这个方便实用性强。
1.2连杆的结构特点
连杆的作用是传递活塞与曲轴间的作用力,并将活塞的往复运动转化为曲轴的旋转运动,连杆应保证足够的强度和刚度。
发动机连杆为模锻件,由连杆小头、杆身和连杆大头三部分组成。
连杆大头是分开的,一半为连杆盖,另一半与杆身为一体,通过连杆螺栓连接起来。
连杆大头孔内分别装有轴瓦。
由于连杆体与连杆盖的结合面是与大、小头孔中心连线倾斜,故称为斜剖式连杆。
连杆小头装有青铜衬套,通过活塞销与活塞连接。
连杆大头是可分开式,内装半圆形轴瓦,大头与曲轴连杆轴连。
连杆小头:
连杆小头与活塞销连接呈浮式结构,发动机工作时活塞销与连杆小头可以相对自由转动,因此沿销的长度方向和圆周方向的磨损比较均匀。
为提高摩擦副的耐磨性,连杆小头内孔压入青铜衬套。
青铜衬套分为两段,分别从小头的两端压入。
小头的顶上有一个集油孔,当曲轴旋转时,激溅起来的机油甩到活塞内腔的顶部,冷却活塞后,落下一部分通过集油孔聚集并流入连杆的小
杆身:
发动机为了在最小质量最大的强度,连杆杆身断面加工成“工”字型。
连杆大头:
连杆通过与曲轴上的连杆轴颈相连,连杆大头为分开式。
连杆大头轴承盖固定螺母,其拧紧力矩为100~120N·M。
图1发动机活塞连杆图
1.3连杆的主要技术要求
小头孔φ55mm(未装铜套)是与活塞销配合的表面,加工尺寸精度为IT6,圆柱度公差为0.0040.006mm、表面粗糙R0.8。
小头孔与活塞销的配合精度要求较高,如果配合间隙过小,会影响连杆与活塞间的传动力效果,如果配合间隙过大,就会产生晃动,使发动机在运行中发出敲击声,考虑到工作后的摩损量0.01因此,安装时必须保证连杆小孔与活塞销之间的配合间隙。
要在加工中直接满足这一要求显然是困难的,因此在装配时,把连杆小头孔分成四组,每2.5um的尺寸间隔为一组,分组进行装配,才能有效控制配合间隙。
1.4连杆的工作条件
发动机工作时,曲柄连杆机构直接与高温高压气体接触,曲轴的旋转速度又很高,活塞往复运动的线速度相当大,同时与可燃混合气体和燃烧废气相接触,曲柄连杆机构还要受到化学腐蚀作用,并且润滑困难。
可见,曲柄连杆机构的工作条件相当恶劣,它要承受高温、高压、高速、和化学腐蚀作用。
曲柄连杆机构发动机的主要运动机构。
其功用是将活塞的往复运动转变为曲轴的旋转运动,同时将作用于活塞上的力转变为曲轴对外输出的转矩,以驱动汽车车轮转动。
曲柄连杆机构由活塞组、连杆组和曲轴、飞轮组等零部件组成。
2连杆的机构设计
2.1连杆长度
1.连杆的长度L,它通常是由连杆比λ=来决定的。
连杆比λ为中心曲柄连杆机构的特性参数,它对活塞运动规律会产生深刻地影响,同时其也是发动机设计中的一一个重要参数。
合理的连杆比应保证连杆及其相关机件在运动时不与其他机件发生运动干涉。
对于S≤120mm的发动机而言,λ值的一般范围为1/3.2~1/3.8。
综合对比各方面.的影响因素后,决定仍采用原492Q汽油机的连杆比,即λ=1/3.65由于S=2r,所以曲柄半径r=40mm。
根据λ=r/L,可得连杆长度L=146.52mm,取L=146.52mm。
现代高速发动机趋向于将λ取大,减小L的尺寸。
但L也不能太小L的选择原则就是在满足以上两个要求的情况下,L越短越好。
由于连杆长度的压缩比和装配关系,所以其制造公差要保持在±0.05-±0.1的范围内。
2.活塞平均速度Cm的计算,活塞平均速度Cm,虽然只能粗略地估计活塞运动的快慢,但它是表征发动机强化程度(热负荷和机械负荷)的重要参数之一。
一般而言,增大Cm可使发动机功率增大,但活塞组的热负荷和曲柄连杆机构的惯性力也随之增大,磨损加剧,寿命下降。
所以,--般汽车发动机的活塞平均速度C在9~15m/s范围内。
2.2连杆小头
结构设计分析采用薄壁圆环形结构,这种结构简单轻巧,制造方便,工作时应力分布均匀,材料利用率高
小头的轴承孔直径已经在活塞组的设计中确定了,d1=22mm
小头宽度根据经验公式B=(1.2~1.4)d1=26.4mm~30.8mm取B=29m
小头的外径一般比孔径大20~35%, D1=(1.2~1.35)d=26.4~29.7mm,D1=28mm
小头的最小径向厚度δ=(D1-d2)/2=3mm
2.3连杆大端的结构设计
连杆大端与连杆盖的分开面采用平切口,因为这类连杆具有较大的刚度,轴承孔受力变形小,制造费用低等优点 。
平切口连杆在连杆螺栓头和螺母支承平面的根部容易出现裂纹,因此在该处倒了一个半径为2m的圆角。
为了提高连杄大端结构刚度和紧凑性,连杄螺栓孔间距离C应尽可能小,一般C=(1.241.31)D2,因为D2=40mm,所以取C=50mm.连杆大头的厚度d2/D2=0.65~0.7,得d2=29.9~32.2,d2取27mm。
2.4连杆杆身机构设计
为了在较小的重量下得到较大的刚度,汽车发动机的连杆杆身一般为便于模锻或铸造的“工”字形截面。
为了使连杆在相同载荷作用下,在连杆的摆动平面内和垂直于摆动平面内的稳定性相同,应使I≈41“工”字形断面的宽度H由小头到大头逐渐加大,并以大圆弧向大,小头过渡,其高度B和中间筋厚度在接近近大头和小头处逐渐加大,这样就可以使杄身等强度并提高大、小端的刚度。
两侧的凸筋应稍厚并倒圆角,还要用较大圆角过渡到中间筋,过渡圆角半径p=25mm(小头),p=40mm(大头)以避免锻造时产生裂纹。
已知H/D=0.327,B/H=0.78,t/H=0.17由D=84可得H=25.83,B=20.15,t=4.39。
2.5连杆各个数据的计算及其确认(mm)
(活塞的行程84,气缸内径80,单位mm)
小头轴承孔直径:
d1=22
小头的宽度:
B=(1.2-1.4)d1=(26.4-30.8),取B=29
小头的外径:
D1=(1.2-1.35)d1=26.4-29.7,取D1=28
连杆小头中心线到连杆大头中心线线的距离为:
入=r/L,故L=r/入,入的取值范围为:
1/3.2-1/3.8,取入=1/3.5.S=2r,S=3.8,r=40。
故连杆小头中心线到连杆大头中心线的距离为:
r=41/1/3.5=40。
取L=146.52
最小径向厚度:
D1-d1/2=26-20/2=3
大头的厚度:
d2=(0.65-0.7)D2=26-28,d2取27
大头直径:
D2=(0.42-0.55)D=(35.28-46.2).D2取41
过度圆角:
小头P=25,大头P=40
连接螺栓孔间距C,C=(1.24-1.31)D2=(49.6-52.4),
螺栓高度:
H1=(0.41-0.58)D2=16.4-23.2,H1取20。
2.6活塞连杆组的装配
①活塞连杆组装入气缸前,应对气缸壁进行清洁。
②根据连杆上的标记和活塞上的标记,将活塞连杆组推入气缸。
应注意不同系列发动机活塞顶上的标记方向有别,一般是朝向发动机的前方,用字或箭头表示。
但是也有标记朝向发动机后方的,装配时切不可装错。
③当活塞连杆组推入气缸接近活塞环时,应注意活塞环开口位置。
新型发动机多数为强化发动机,仅有两道气环一道油环,应使各环开口相错120°,并使环开口偏离活塞销中心线30°。
④在安装连杆大头盖时,应注意使连杆体与盖的相同标记位于同一侧,并在定位面上涂上干净机油。
⑤连杆螺栓拧入前,应在螺纹部位涂上少许机油,两只螺栓交替拧紧,当力矩达不到规定时应更换螺栓。
⑥活塞连杆组装配完后,应检查活塞在气缸中是否有偏缸现象。
如果有偏缸,说明活塞连杆组在修配中,各零件公差不符合规定,应查明原因,妥善处理。
图2活塞连杆组装配
图3行驶的汽车
总结
本章课程说明了在设计活塞连杆组的时候各项数据,完全可以达到工厂的需要。
本次的设计课程也完美的解释了在设计活塞以及连杆的时候要注意的事项以及要求。
也计算出个活塞连杆组的各项参考数据,经过对比网络和现时活塞数据,完全可以达到生产要求。
经过本次的课程设计,给予了我们实践的机会,也使我积累了必须的经验,为以后的学习打下了基础,也为毕业设计铺平了道路。
本次课程设计为了让自身的设计更加的完善,更加的贴合工程标准,一次次翻阅汽车设计类的书籍。
同时也是比哦不可少的,我们做的课程设计一次次的修改数据,一次次的计算数据,当然也有很多次的失败设计,我们也是没有采用,因为哪样的设计,理论上可用,实际上加工困难,增加产品的成本。
所以我们认为我们所计算的数据完全可以用来产品的生产。
也完全满足工厂要求。
通过这次我们亲身的设计实践,让我们对这些专业课的基础知识和基本理论能有进一步的理解和掌握。
设计的整个过程都有老师在一旁指导,有问题可以及时解决,学到了很多发动机和活塞连杆的知识,这也是我觉得这次设计比以前简单的原因吧。
我把这次课程所学到的东西总结为以下几点:
1.分析、设计、绘图、运用各种标准和规范、查阅各种设计手册与资料。
2.计算,绘图的应用能力等方面得到进一步的提高。
3.初步建立了工程的观念处理问题。
4.能够全面地检验并巩固我们以前所学的专业课知识,并通过结合实际,让我们能从一个全新的角度重新学习、认识以前学过的专业课知识。
参考文献
1.陈家瑞.汽车构造(第三版)上册[M].北京:
机械工业出版社,2009;
2.肖生发.汽车构造学习指导与习题精解[M].北京:
北京大学出版社,2013;
3.尉庆国.汽车发动机构造及原理[M].北京:
国防工业出版社,2012;
4.苏铁熊.汽车发动机构造及原理[M].北京:
人民邮电出版社,2015;
5.中国标准出版社.内燃机标准选编[M].北京:
中国标准出版社,2017.
6.吴兆汉等.内燃机设计[M].北京:
北京理工大学出版社.1990