粉末冶金工艺.doc
《粉末冶金工艺.doc》由会员分享,可在线阅读,更多相关《粉末冶金工艺.doc(10页珍藏版)》请在冰豆网上搜索。
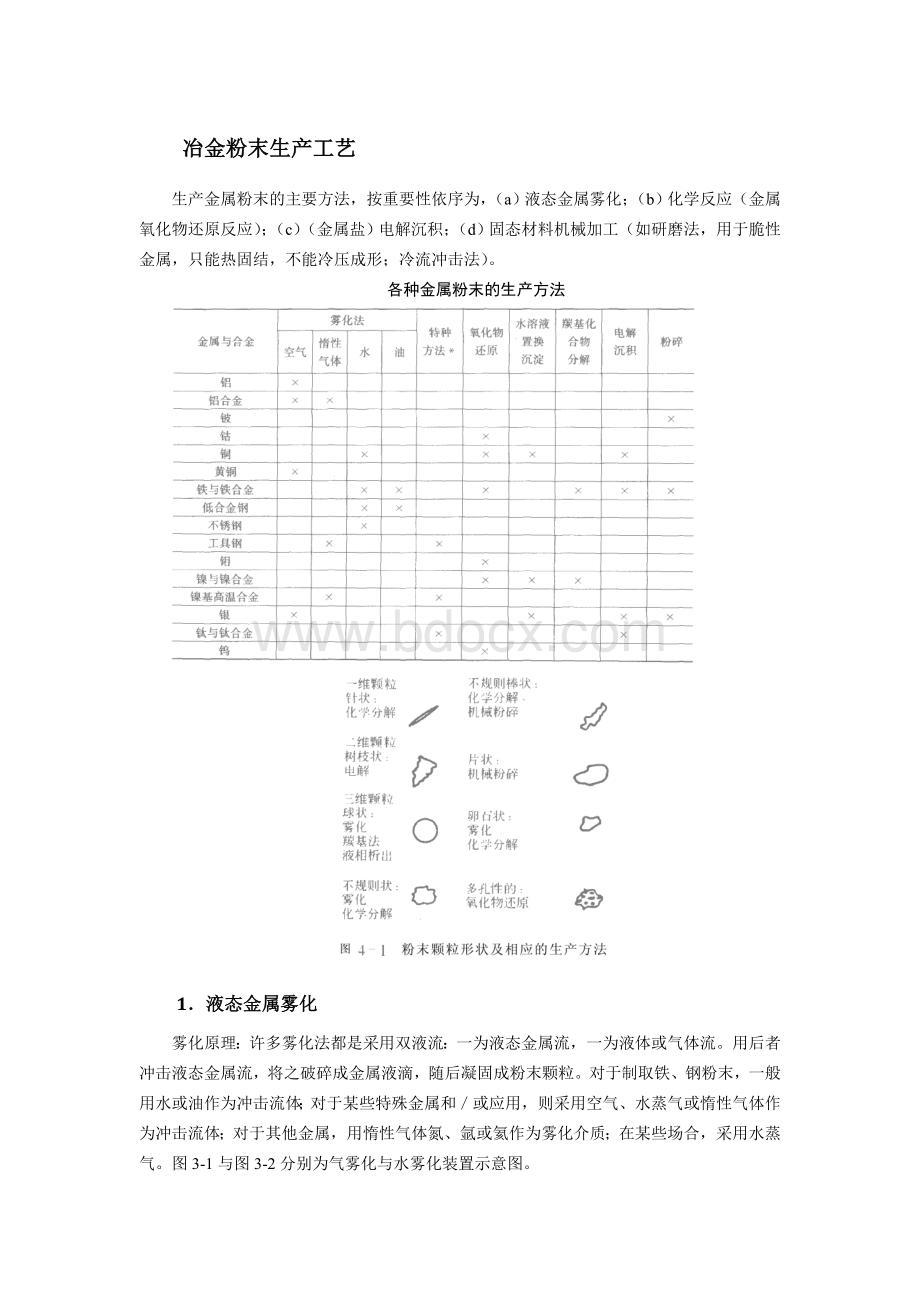
冶金粉末生产工艺
生产金属粉末的主要方法,按重要性依序为,(a)液态金属雾化;(b)化学反应(金属氧化物还原反应);(c)(金属盐)电解沉积;(d)固态材料机械加工(如研磨法,用于脆性金属,只能热固结,不能冷压成形;冷流冲击法)。
各种金属粉末的生产方法
1.液态金属雾化
雾化原理:
许多雾化法都是采用双液流:
一为液态金属流,一为液体或气体流。
用后者冲击液态金属流,将之破碎成金属液滴,随后凝固成粉末颗粒。
对于制取铁、钢粉末,一般用水或油作为冲击流体;对于某些特殊金属和/或应用,则采用空气、水蒸气或惰性气体作为冲击流体;对于其他金属,用惰性气体氮、氩或氦作为雾化介质;在某些场合,采用水蒸气。
图3-1与图3-2分别为气雾化与水雾化装置示意图。
熔点较低的金属(如锡和铝)通常采用气体雾化。
对于高熔点合金,诸如高温合金与工具钢,采用惰性气体,特别是氩气,作为雾化介质气体进行雾化,防止金属氧化。
鉴于液体介质的散热速率比气体高得多,故用液体介质雾化容易制得不规则的颗粒。
因此,生产粉末冶金结构零件用的铁粉、钢粉、铜粉及不锈钢粉,通常都是用水雾化法生产。
这主要是因为不规则形状的颗粒粉末用一般刚性磨具压制成形后,借助于粉末颗粒间的相互联结,生坯具有足够高的强度,便于搬运。
在工业上用水雾化法生产不锈钢粉时,是在一个用氮气吹洗的雾化筒内,用压力为的高压水喷射流雾化不锈钢液流生产的。
图3-6为水雾化不锈钢粉颗粒的扫描电镜照片。
铁粉与铜粉也在用水雾化法生产。
图3-7为水雾化铜粉颗粒的光学显微镜照片。
雾化铜粉颗粒的不规则形状,是在雾化过程中由细小的球形颗粒聚结形成的。
对于含锰与铬的铁合金,用水雾化法生产的粉末会在颗粒表面形成锰与铬的氧化物,这些氧化物在随后的退火作业中难以被还原。
解决这个问题的方法之一是,用油作为雾化介质,以之雾化含锰或铬的铁合金熔体。
因此,也称之为油雾化法。
特种雾化方法:
2.用化学反应法制取金属粉末
在金属粉末生产中,最常用的化学反应法是氧化物还原法,通常用这种方法制取铁粉、铜粉、钻粉、钨粉及钼粉。
用一种金属从水溶液中替换出另外一种金属的过程叫做金属置换。
用金属置换法可制取铜粉、铅粉、锡粉、银粉及金粉等。
取铜粉、铅粉、锡粉、银粉及金粉等。
从热力学上讲,只能用负电位较大的金属去置换溶液中正电位较大的金属。
反应的通式为:
Me12++Me2=Me1+Me22+
例如用铁置换铜粉
CuSO4+Fe=Cu+FeSO4
3.电解沉积
电解制取金属粉末的原理是,溶液中通以直流电时,于金属盐水溶液中离解的金属离子在阴极上放电,反应式为:
Men++ne-=Me
金属离子一般来源于金属阳极和含这种金属的盐的电解液。
但是,采用不溶解阳极时,金属离子就只能靠电解液供给。
用电解沉积法生产金属粉末已有几十年的历史。
可是电解金属粉末的价格较高。
比如电解铁粉与铜粉,当用雾化法能生产出具有适当纯度的铜粉与铁粉时,电解粉末的生产很快就衰落了.
4.固态材料机械粉碎法
主要包括机械粉碎法和冷流冲击法
冶金粉末特性
包括冶金粉末的粒度,颗粒形状、粒度分布、化学成分、粉末颗粒组织、金属粉末的松装密度与流动性、金属粉末的振实密度、压缩性、生坯密度和压缩比、自燃性、爆炸性及毒性等重要参数。
松装密度是粉末自然地充满规定容器时单位容积的粉末质量,即除重力外,不受任何力作用的松散粉末的密度。
松装密度可用流速计、测试仪和容量计测定。
粉末的振实密度是以一定方式振动后粉末的密度,因此振实密度大于松装密度。
测定振实密度时,取标准质量的粉末并用机械或人工振实。
压缩性是指在单轴方向载荷作用下松散粉末致密化的能力,一般表示为在规定条件下,用规定的压力,在规定尺寸的模具中,由粉末压制成的压坯的生坯密度。
压缩比是松装粉末的体积对压坯体积之比,即生坯密度对松装密度之比。
为了正确设计模具,必须知道压缩比。
粉末冶金工艺
1.压制
用粉末冶金生产结构零件的第一个重要工序一般是压制。
在压制过程中,用一个或几个模冲将阴模中的粉末颗粒压缩在一起。
如果阴模和模冲是仿形的,则得到的粉末压坯就具有最终零件的几何形状特征。
对于大多数实际应用,压坯在烧结之前强度低,不能直接使用。
但是,压制这一重要工序不仅制成了零件的几何形状,还将影响零件的烧结、零件的最终强度以及压坯尺寸在烧结过程中是否发生明显变化。
单轴向压制:
金属粉末在刚性模具中在较慢速度下的单轴向压制,即作用在粉末体上的压力是由上模冲,或者是由上、下模冲同时施加的,这称为常规压制。
常规压制是一种最广泛使用的粉末固结方法。
步骤:
(1)混合
在用刚性模具压制成形以前,一般都要将不同的金属粉末进行混合,例如用于制作自润滑青铜轴承的铜粉和锡粉,或用于制作结构零件的铁粉、铜粉和石墨粉。
即使零件是由一种金属粉末制作的,一般在压制前也要将粉末与润滑剂混合均匀。
(2)润滑
粉末在刚性模具中压制成零件时,必须进行润滑以减小压坯与阴模壁之间的摩擦力。
自动压制时,若不进行润滑,将压坯从模具中脱出时所需的脱模压力迅速增大。
压制几个压坯后,压坯就会卡死在模具中。
低剪切强度的润滑剂可将金属表面隔离开。
但即使充分润滑的表面也不可能实现完全分离,因为金属的粗糙表面穿过润滑膜与阴模壁相接触仍然会产生摩擦力。
对于常用的金属粉末,最常用的润滑剂是硬脂酸、硬脂酸盐(诸如硬脂酸锌和硬脂酸锂),以及合成蜡。
自动压制时的润滑可采用将粉末状的润滑剂与金属粉末混合在一起,或者将润滑剂溶于溶剂中形成溶液或悬浮液润滑模壁。
自动压制时采用模壁润滑在技术上是可行的。
但是,由于以下两个问题,模壁润滑在工业实践中还不常见:
1)如何通过以液体为载体的溶液或悬浮液的形式精确地涂覆适当数量的润滑剂;2)如何在涂覆润滑剂与用粉末充填模具之间快速并完全除去液体载体。
因此,将润滑剂与粉末相混合的方法仍在普遍使用。
尽管如此,将金属粉末与润滑剂粉末相混合进行润滑的方法仍存在严重的不足之处,如减低强度与影响尺寸控制。
加入的润滑剂必须在烧结之前或在烧结过程中分解,同时分解的产物必须全部从烧结炉的预热带排出。
(3)压制
压制时发生的过程有:
1)颗粒的大量移动和重排;2)颗粒的变形与断裂;3)颗粒表面间的冷焊。
颗粒主要沿压力作用的方向移动。
颗粒之间以及颗粒与模壁之间的摩擦力阻止颗粒的大量移动,同时有些颗粒也阻碍其他颗粒移动,最终颗粒发生变形。
首先是弹性变形,接着是塑性变形。
塑性变形导致加工硬化,从而削弱了在适当压力下颗粒进一步变形的可能性。
压制金属或合金粉末时,塑性变形和加工硬化的开始取决于相应金属或合金的力学性能。
例如,由软的铝粉压制的压坯,其颗粒变形明显早于由硬的钨粉压制的压坯。
最后颗粒断裂形成较小的碎块。
由陶瓷粉压制的压坯,通常是颗粒发生断裂而不产生塑性变形。
单轴向压制的缺点在于应力分布不均,导致密度不均,严重的会导致分层、碎裂和裂纹等缺陷
冷等静压:
将金属粉末制成金属制品通常包括四道基本工序,它们是:
筛分(粒度分级)、混合、压制及烧结。
粉末冶金的一般工艺:
于室温下将金属粉末装于模具中用压机压制成型。
这是成型的产品是“生”压坯,还必须在高温下,于保护气氛或真空中进行烧结,以进行强化。
粉末冶金最重要的应用是:
结构零件(与铸造或锻造零件相竞争),以可控隙度为目标的多孔性零件,难熔金属,硬质合金,金属摩擦材料,电触头材料,磁性材料及弥散强化材料。
冷压制与烧结的零件,其材料一般具有多孔性,因此,其材料密度比铸锭冶金制作的材料密度低,从而材料的力学性能也较低。
使用复压、再烧结或熔渗可以提高结构零件的强度,其韧性、冲击强度及疲劳强度通常任然比常规零件低。
为消除粉末冶金结构零件材料中的孔隙,可将有金属粉末制作的预成型坯进行热压或热锻。
用常规压制—烧结工艺生产的零件,其材质具有多孔性,对于大部分零件而言,和常规零件相比,由于多孔会导致零件材料的力学性能减低,因此是一种缺陷。
可是,烧结零件具有的多孔性,其最优利的应用是烧结金属含油轴承。
实际上,烧结青铜含油轴承是20世纪20年代中期开发的,粉末冶金结构零件在其基础上发展起来的。
烧结青铜自润滑含油轴承是由90%铜粉与10%锡粉(有时添加石墨粉)的混合粉,用常规压制—烧结工艺生产的。
烧结时,铜与锡形成青铜合金。
多孔性烧结青铜含油轴承的标准显微组织如下,青铜基体中的黑色区为孔隙。
烧结时,尺寸发生少量变化,因此,烧结后轴承必须进行精整。
烧结青铜含油轴承(90%Cu-10%Sn)500X浸油设备
一般将烧结金属含油轴承的孔隙度控制在15%~30%(体积分数),此时孔隙都是小的,相互间以及与轴承表面都是连通的。
因此,含浸润滑油后,轴承可作为润滑油的贮存装置。
将含油轴承组装于轴承座中,当轴开始运转时,因摩擦产生热量,轴承温度升高,致使润滑油从材料孔隙中溢出,并在轴承与轴之间形成润滑油膜。
当轴停止运转时,润滑油又被重新吸收到轴承材料的孔隙内。