发动机可靠性试验方法.docx
《发动机可靠性试验方法.docx》由会员分享,可在线阅读,更多相关《发动机可靠性试验方法.docx(17页珍藏版)》请在冰豆网上搜索。
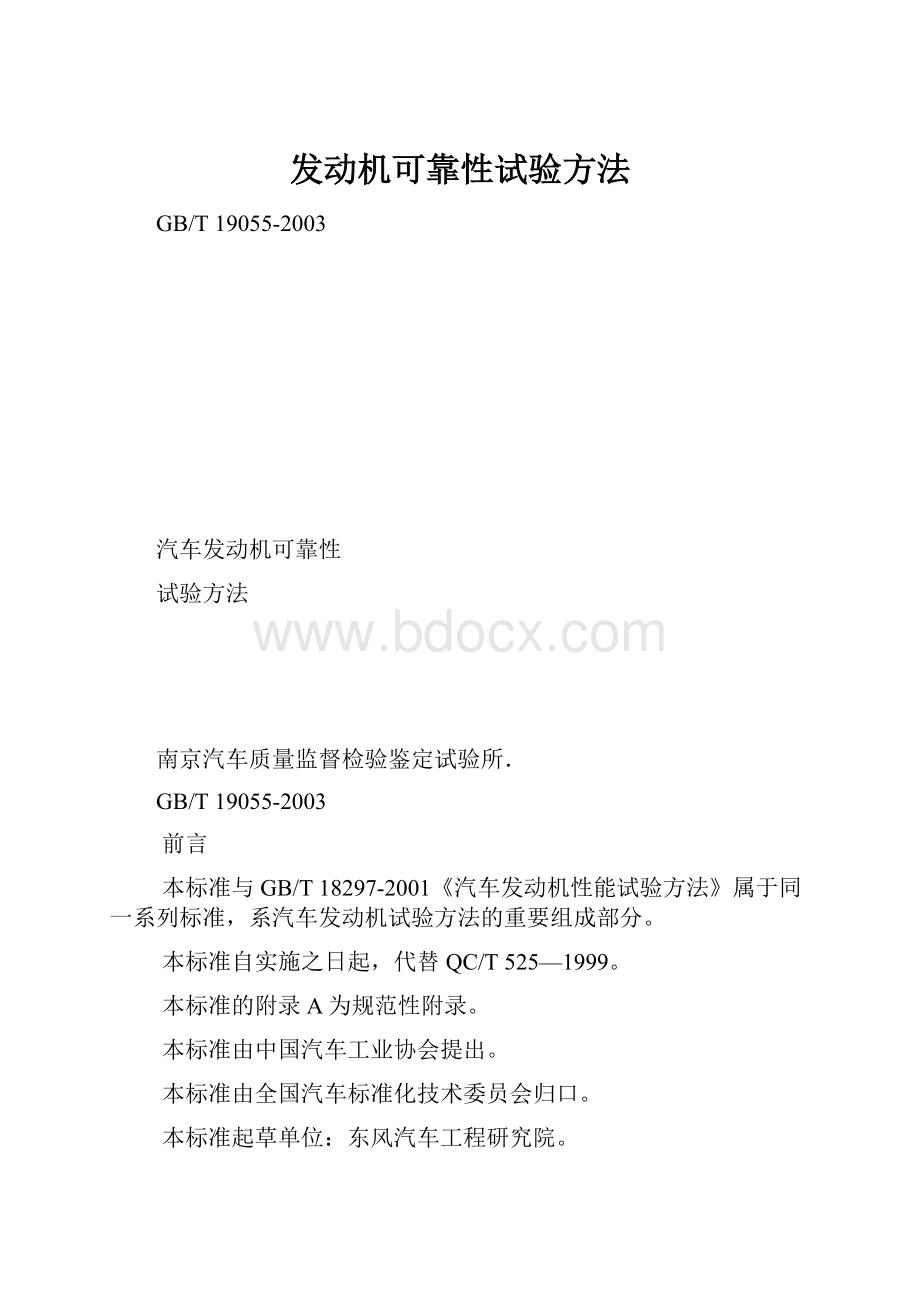
发动机可靠性试验方法
GB/T19055-2003
汽车发动机可靠性
试验方法
南京汽车质量监督检验鉴定试验所.
GB/T19055-2003
前言
本标准与GB/T18297-2001《汽车发动机性能试验方法》属于同一系列标准,系汽车发动机试验方法的重要组成部分。
本标准自实施之日起,代替QC/T525—1999。
本标准的附录A为规范性附录。
本标准由中国汽车工业协会提出。
本标准由全国汽车标准化技术委员会归口。
本标准起草单位:
东风汽车工程研究院。
本标准主要起草人:
方达淳、吴新潮、饶如麟、鲍东辉、周明彪。
引言
本标准系在JBn3744—84即QC/T525—1999《汽车发动机可靠性试验方法》长期使用经验的基础上参考国外的先进技术,制定了本标准。
本标准对QC/T525—1999的重大技术修改如下:
——拓展了标准适用范围,不仅适用于燃用汽、柴油的发动机,还适用于燃用天然气、液化石油气和醇类等燃料的发动机;
——修改了可靠性试验规范,对最大总质量小于3.5t的汽车用发动机采用更接近使用工况的交变负荷试验规范;对最大总质量在3.5t~12t之间的汽车用发动机采用混合负荷试验规范,以改进润滑状态;冷热冲击试验过去仅在压燃机上进行,现扩展到点燃机,并增加了“停车”工况,使零部件承受的温度变化率加大;
——修改了全负荷时最大活塞漏气量的限值,首次推出适用于不同转速范围的非增压机、增压机、增压中冷机的限值计算公式,使评定更为合理;
——为使汽车发动机满足国家排放标准对颗粒排放物限值的要求,修改了额定转速全负荷时机油/燃料消耗比的限值(由原来1.8%改为0.3%);
——增加“试验结果的整理”的内容,并单独列为一事,要求对整机性能稳定性、零部件损坏和磨损等进行更为规范和详尽的评定;
——增加“试验报告”的内容,并单独列为一章,明确试验报告主要内容,使试验报告更为规范。
——增加了附录A《汽车发动机可靠性评定方法》,使评定更为准确和全面,
——鉴于汽车发动机排放污染物必须满足国家排放标准的要求,在认证时按排放标准进行专项考核,故本标准不再涉及。
.
汽车发动机可靠性试验方法
1范围
本标准规定厂汽车发动机在台架上整机的一般可靠性试验方法,具中包括负荷试验规范(如交变负荷、混合负荷和全速全负荷)、冷热冲击试验规范及可靠性评定方法。
本标准适用于乘用车、商用车的水冷发动机,不适用于摩托车及拖拉机用发动机。
该类发动机属往复式、转子式,不含自由活塞式。
其中包括点燃机及压燃机;二冲程机及四冲程机;非增压机及增压机(机械增压及涡轮增压、水对空及空对空中冷);适用于燃用汽油、柴油、天然气、液化石油气和醇类等燃料的发动机。
新没计或重大改进的汽车发动机定型、转厂生产的发动机认证以及现生产的发动机质量检验均可按本标准规定的办法进行可靠性试验。
本标准还可作为发动机制造厂和汽车制造厂之间交往的技术依据。
2规范性引用文件
下列文件中的条款通过本标准的引用而成为本标准的条款。
凡是注日期的引用文件,其随后所有的修改单(不包括勘误的内容)或修订版均不适用于本标准,然而,鼓励根据本标准达成协议的各方研究是否可使用这些文件的最新版本。
凡是不注日期的引用文件,其最新版本适州于本标准。
GB/T15089机动车辆及挂车分类
GB/T17754摩擦学术语
GB/T18297-2001汽车发动机性能试验方法
3术语和定义
GB/T17754和GB/T18297确立的以及下列术语和定义使用于本标准。
3.1
气门下沉量valvesinkage
气门与气门座的接触锥面在工作中磨蚀,气门沿其轴线方向陷入气门座的距离。
3.2
最大净功率转速speedofmaximumnetpower
不高于额定转速的情况下,发动机带全套车用附件(见GB/T18297-2001第7章)所输出的最大有效功率时的转速,符号为np。
3.3
最大净扭矩转速speedofmaximumnettorque
发动机带全套车用附件(见GB/T18297-2001第7章)所输出的最大有效扭矩时的转速,符号为nM
3.4
额定净功率ralednetpower
发动机带全套车用附件(见GB/T18297-2001第7章),在额定转速下、全负荷时所输出的校正有效功率。
4试验发动机
试验发动机2台(A发动机及B发动机)应符合发动机制造厂的技术条件,所有紧固件应拧紧至规定值,气门间隙调整至规定值,采用制造厂规定的润滑脂及密封胶。
5试验一般要求
试验所用仪表精度、测量部位及试验数据的计算按GB/T18297--2001第4章和第5章的规定。
6对试验一般条件的控制
6.1燃料
燃料牌号按发动机制造厂的规定。
汽油温度控制在298K±5K,柴抽温度控制在311K±5K;其他燃料温度控制按发动机制造厂的规定。
6.2机油
机油牌号按发动机制造厂的规定。
机油温度控制在363K到398K之间或按发动机制造厂的规定。
6.3冷却液
采用软水(钙、镁含量均低于200mg/ke)或采用发动机制造厂规定的冷却液。
冷却液温度控制在361K到383K之间或按发动机制造厂规定的温度;冷热冲击试验时,水温的控制按9.4表4的规定。
6.4异常燃烧的避免
点燃机在台架可靠性试验全过程中,不应发生爆震、早燃及过高燃烧室温度,可按发动机制造厂的规定对火花塞热值、燃料辛烷值、点火提前角及混合气浓度进行适当调整,并在试验报告中注明。
7试验时发动机所带附件及各系统的调整
7.1进气系统
采用装车的标准进气系统.
排气系统7.2
采用装车的标准排气系统或具有相等阻力(在额定功率工况下,与标准排气系统的背压相差不大于2kPa)的试验室排气系统。
7.3排放控制装置
除特殊规定外,均应安装并处于工作状态
7.4冷却系统
不装车用风扇,可用外加吹风机对发动机吹拂。
节温器置定在全开的位置。
冷却系统应密封,能建立起厂家规定的放气阀开启压力,压力超过时能自动放气,在试验中(尤其是冷热冲击试验),冷却水在水套里的流量及流向应与装车状态一致。
7.5点火系统
点燃式发动机的点火提前角按发动机制造厂的规定。
7.6燃料供给系统
采用试验室供给系统,即在装车的供给系统中增加燃料消耗量测量、燃料温控等装置,试验室供给系统需满足发动机制造厂的要求,如燃料压力、温度、流量、清洁度等。
压燃式发动机的供油提前角按发动机制造厂的规定。
7.7发电系统
应安装装车的发电机、调压器及蓄电池(在充满电状态)等,并处于工作状态。
8工作程序
本程序在2台发动机(A发动机、B发动机)上进行。
8.1试前精密测量
a)A发动机测量曲轴轴颈/轴瓦、缸筒/活塞组、凸轮/挺杆/摇臂和气门/导管摩擦副的尺寸和间隙(确定磨损用);测量曲轴、凸轮轴止推间隙及齿隙;测量气门/气门座接触带宽和气门下沉量(试前为基准点)等;
b)B发动机测量缸垫自由状态厚度及尺寸、缸体上平面及缸盖下平面的平面度、排气歧管密封面的平面度和尺寸(确定变形用)等。
8.2磨合
按发动机制造厂的规范磨合。
发动机安装到台架后,第一次起动前,检查并清除整个进气系统内的尘埃及异物。
在磨合初期及末期按10.4.1取机油油样和未使用过的机油油样一起进行分析。
性能初试8.3
净功率、负荷特性、机械损失功率、活塞漏气量及机油消耗量试验按GB/T18297—2001的8.3、8.4、8.7、8.10及8.9.3的规定进行。
机油消耗量测量仅在额定转速全负荷下运行24h。
8.4可靠性试验
按第9章的规定进行
8.5性能复试
重复8.3。
8.6拆检
拆检A发动机和B发动机:
a)检测紧固件(如螺栓、螺母等)拧紧力矩松动量。
即拧松紧固件,再准确地拧回到原来的位置(事先应做好记号),此拧回力矩与试验前的拧紧力矩之差为松动量;
b)对主要摩擦副的表面拍摄局部清晰照片。
主要摩擦副有轴颈/轴瓦、缸筒(头环换向处)/活塞(裙部)/环、凸轮/挺杆/摇臂、气门/气门座等;
c)拍摄断口的断面及裂纹的放大照片;
d)拍摄活塞顶上、下表面、火花塞瓷体与电极、油嘴的照片;
e)拍摄在油底壳、罩盖、缸盖上表面、活塞和凸轮等表面上的沉积物、油泥及漆膜的照片;
f)拍摄密封件,如缸垫、进排气管垫、排气管及油封等窜漏的印迹。
其中d)、e)及f)所指零部件,拍照前不应清洗。
在每张照片下方均应附有说明。
8.7试后精密澜量
重复8.1。
精测后要妥善保管所有零部件,以备进一步检查和分析。
9.可靠性试验规范
按发动机装车类别进行可靠性试验,试验规范及运行持续时间见表1。
表1不同最大总质量汽车用发动机可靠性试验规范及运行持续时间
单位为小时
附和试验规范(在A发动机上进a
行)冷热冲击试验规范装机汽车类别
)(按GB/T15089(在B发动机上进行)全速全负交变负荷混合负荷荷
汽车最大总质量200
-
-
400
≤3500kg
3500kg<汽车最大总质-1000-300量≤12000k汽车最大总质量500
-
1000
-
12000kg
a装乘用车及商用车的发动机均按本表分类
9.1交变负荷试验规范
交变负荷试验规范如图1。
油门全开。
从最大净扭矩的转速(n)均匀地升至最大净功率的转速(n),历时1.5min;pM在n稳定运行3.5min;随后均匀地降至n,历时1.5min;在n稳定运行3.5min。
重复上述MpM交变工况,运行到25min。
油门关闭,转速下降至怠速(n)运行到29.5min;油门开大,无负荷,使转速均匀上升i到105%额定转速(105%n)或上升到发动机制造厂规定的最高转速,历时0.25min±0.1min;r随即均匀地关小油门,使转速降至n,历时O.25min±0.1min。
M至此完成了一个循环,历时30min。
运行800个循环,运行持续时间400h。
9.2混合负荷试验规范
混合负荷试验规范见图2及表2,不同工况间转换在1min内完成,均匀地改变转速2。
1000h个循环,运行持续时间1000,共60min负荷。
每循环历时.
表2混合负荷试验规范
工况序号发动机转速负荷工况时间
510怠速ni最大净扭矩的转速10油门全开2nM最大净扭矩的转速40油门全开3np5
油门全开额定转速4
nr9.3全速全负荷试验规范
全速全负荷试验规范见表3。
表3全速全负荷试验规范
转速负荷运行持续时间h
1000
额定转速n油门全开t9.4冷热冲击试验规范以内完成;工况2,表中工况1到,2到的转换在5s343冷热冲击试验规范见图及表。
不同最15s1443到,到的转换在以内完成,均匀地改变转换及负荷。
每循环历时6min。
1)见表h大总质量汽车用发动机运行持续时间(.
表4冷热冲击试验规范
工况序号转速负荷冷却水出口温度K工况时间s
升至最大净功率的转378±2°或tp1(热)油门全开cn385±2速bp1502n自然上升怠速i150
自然上升30
0降至最大净功率的转360-t0
-15-15
(冷)4p-4
速n311或高怠速nhpia散热器盖在绝对压力150kPa放气时,冷却水温升至378K±2K,或按发动机制造厂的规定。
b散热器盖在绝对压力190kPa放气时,冷却水温升至378K±2K,或按发动机制造厂的规定。
ct系发动机自行加热至规定出水温度所需的时间。
p10检查及维护
检查及维护按下列要求进行,随机型的差异,其内容及周期可作适当增减。
检查的结果及维护情况应详细记录。
10.1随时的检查
10.1采用故障诊断器、仪表和计算机等随时检查运行数据,若超过限值范围,根据故障严重程度,发出警报或紧急停车,进行处理和维护。
若属于发动机故障,则计为故障停车。
记录停车的运行时间、原因及处理情况。
.
10.1.2判断有无异常燃烧,如爆震及早燃等,若有应立即消除。
10.1.3监听发动机运动件(如曲柄连杆机构和配气机构等)的运行异响,必要时采取措施。
10.2每1h的检查
在1h内适时地记录校正最大净扭矩、校正最大净功率、额定净功率、点火提前角、燃料消耗量、机油压力及温度、进气管内压力及温度、排气管内压力及温度、排气温度、燃料温度、运行工况下全负荷活塞最大漏气量及运行持续时间(h),并画在以运行持续时间为横坐标的监督曲线上。
还需适时记录发动机相应转速及进气状态等。
10.3每24h的检查及维护
10.3.1停机静置16min后,用量杯加机油准确地至油标尺上限,所加机油的重量用来计算该24L平均机油/燃料消耗比,并画在监督曲线上。
机油消耗量的测定还可用其他方法。
10.3.2检查发动机向内向外漏油、漏水和漏气情况.如排气管开裂、法兰连接处漏气、气缸垫密封失效引起的机油乳化,缸筒内进水和气体窜入冷却系内等。
保持发动机及其周围的清洁,以便及时发现泄漏。
10.3.3检查火花塞电极及瓷体,若有严重烧蚀及裂纹,换用冷一级的火花塞。
10.3.4巡视发动机及试验设备,并检查紧固件、连接件及管路,尤其是软管。
检查皮带张紧情况,必要时张紧。
10.3.5检查所有液面高度.
1O.4每96h的检查及维护
10.4.1使发动机怠速运行,从主油道取机油样,第一次放出的机油还回油底壳,再取—定数量的机油油样(不计入发动机机油消耗量)。
抽样取出后,关紧阀门。
对油样进行分析,测定黏度、不溶解物百分数、总酸度、总碱度及金属元素含量、磨屑形貌等。
10.4.2更换机抽及机油滤芯。
10.5每192h的检查及维护
10.5.1测量气门间隙及气门下沉量(B发动机不测气门下沉量),并将其间隙调整至规定值。
10.5.2调量起动机拖动时气缸压缩压力,找出缸压远低于各缸平均值的个别气缸。
测量时置节气门于全开位置,并拆去所有气缸的火花塞或喷油器。
10.5.3更换火花塞,检查喷油器开启压力、喷雾及滴漏等情况。
10.6504h的检查及维护
更换空气滤清器及燃油滤清器的滤芯。
10.7可靠性试验终了检测
取机油油样,测量机油消耗量、气缸压缩压力、气门间隙及气门下沉量(例行检查与终了检测是靠近时,可一并进行)。
.
11试验结果的整理
11.1运行时间的要求
依据发动机实际运行持续时间(h),运行过程中所更换的零部件及其时间(h),按附录A的A.1进行评定。
11.2性能的稳定性
11.2.1比较初试(按8.3)及复试(按8.5)性能曲线及主要参数。
11.2.2绘制可靠性试验过程中,按10.2和10.3记录的校正最大净扭矩、校正最大净功率、额定净功率、运行工况下全负荷最大活塞漏气量、24h平均机油/燃料消耗比与运行持续时间(h)的关系曲线,分析可靠性试验性能变化趋势。
按A.2、A.3及A.4的限值进行评定。
11.3零部件的损坏
记录故障停车、紧固件松动、密封失效、橡胶件老化、堵塞、变形、裂纹、断裂、零部件损坏发生的运行时间(h)及维护作业情况;提供损坏部位、裂纹、断口和窜漏印迹等照片;用精密测量数据分析变形量分别按A.5、A.6、A.7和A.8进行评定。
11.4零部件磨损
11.4.1依据机油油样分析结果,判断零部件窘掘情况及机油品质。
11.4.2整理精密测量数据,确定主要摩擦副[按8.6b)]的磨损量。
11.4.3区分零部件磨损的形式,判定磨损的严重程度,提供磨损的照片,按A.9进行评定
11.4.4描述摩擦副表面接触情况并提供照片,按A.10进行评定。
11.5零部件表面沉积物
描述零部件表面沉积物的状态并提供照片,按A.11进行评定。
12试验报告
试验报告至少应包括;
a)前言:
说明试验任务的来源;
b)目的;
c)试验对象:
试验发动机技术参数按GB/T18297-2001附录A“点燃机主要参数表”或附录B“压燃机主要参数表”的内容填写,并附加图形、照片及必要的说明;
d)试验设备及仪表:
应写明主要设备及仪表名称、厂家、型号、精度、标定日期及测量部位;
e)试验条件、试验发动机所带附件及各系统的调豢和试验程序:
注明依据的试验标准及其编号,与标准不同之处,应加以说明;
f)试验结果:
对原始试验数据加以处理,尽可能用曲线表示,重要的数据可以列表;按第11章要求编写;
e)结论:
根据试验结果和评定,对该发动机可靠性作出通过、基本通过或不通过的结论;对基本通过的发动机,应提出改进和补充试验的建议;
试验日期。
h)
附录A
(规范性附录)
汽车发动机可靠性评定方法
A.1为使发动机可靠性有一致的评定基础,在没有重大的结构损坏的前提下,允许更换少量的零部件,运行持续时间(h)达到表1的规定,才进行评定。
试验中更换的零部件未达到设计的寿命,则该零部件可靠性不合格。
A.2在运行过程中,校正最大净扭矩、校正最大净功率及额定净功率下降不应超过初始值的5%。
A.3额定转速、全负荷时机油/燃料消耗比不得超过0.3%。
A.4四冲程发动机在全负荷时最大活塞漏气量(B)不得超过限值(B)。
LmaxB=CV=0.6%V(n/2)r(298/T)
mtrHrL式中:
C——系数(选定为0.6%);
Vt——四冲程发动机在标准状态下额定转速时的理论吸气量,单位为升每小时(L/min),即充气系数ηv=1;
V——发动机排量,单位为升(L);Hnr——额定转速,单位为转每分钟(r/min);
r——额定转速、全负荷时增压机的压比,即压气机出口的绝对压力p与压气机进口绝or对压力pi之比(r=p/p),非增压机令r=1;roirTm——进气歧管内进气温度单位为开[尔文](k),非增压机令Tm=298K。
A.5发动机可靠性试验故障用首次故障时间、故障停车次数及故障平均间隔时间[即运行持续时间(h)与故障次数之比]来评定。
A.6根据紧固件的拧紧力矩松动量,分析松动原因及对发动机可靠性和密封性的影响。
A.7发动机不得向内、向外漏油或漏水;空气不得渗入发动机负压系统。
发动机内不得有燃气窜入油道或水道、油水混合等。
主要评定缸垫、进排气管垫、排气管、油封等零部件的密封性。
A.8对零部件裂纹或断裂的评定
A.8.1零部件裂纹或断裂的严重程度按表A.1分类。
表A.1裂纹或断裂程度的分类
类别程度形貌危害性
通过探伤仪或用10倍的放不会发展,不引起A轻微裂纹大镜才能发现故障
有可能扩展,引起肉眼可见中等裂纹B
故障
裂纹很可能扩展引起故障较大的裂纹或断裂C
尺寸较大的裂纹或断裂零件断裂但未引起故障
D
导致重大故障关键部位的大裂纹或断裂严重裂纹或断裂.
A.8.2分析零部件裂纹或断裂的原因
由机械交变应力引起的疲劳裂纹或断裂,主要发生在连杆、曲轴、缸体、油底壳、齿轮、支架及高压油管等零部件上;由燃烧或摩擦产生的热疲劳裂纹或断裂,主要发生在缸盖、活塞、喷嘴、排气歧管及增压器等零部件上。
A.9摩擦表面的评定
A.9.1主要摩擦副[按8.6b]的表面一般磨损、粘着磨损及磨料磨损的程度,按表A.2、表A.3和表A.4分类。
表A.2摩擦表面一般磨损分类
类别AB形貌类别程度危害性材料转移擦痕
程度形貌可见加工痕不可测出,轻微磨损
轻度磨损
迹或光亮勉强可测量
CD
中度磨损严重磨损
可测量有深度磨损或局部过
可能引起故障导致重大故障
量磨损
危害表A.3磨损表面粘着磨损分类
表面变颜色、A轻微擦伤无无局部光亮或少量擦痕擦痕多处、面有可能扩展,引积较大,感觉表层材料转移B中度擦伤起故障有深度
擦痕分布宽而次表层材料转引起故障C粘着深移大面积粘着和材料撕裂转移导致重大故障严重粘着(撕裂D
)
撕裂
表A.4磨损表面磨料磨损分类
形貌
类别程度危害性用指甲或铅笔感划痕深度划痕数量觉A无很饯轻微划痕很少无B无不易较浅轻度划痕少量可能有影响,但不C较探中等数量略有中度划痕会引起故障
D
导致重大故障有深很多严重划痕或破坏
A.9.2按GB/T17754区分发动机零部件出现的其他磨损形式,如腐蚀磨损(缸套-环换向区、排气门/排气门座锥面等)、疲劳磨损(挺杆、轴瓦、齿轮表面等)、微动磨蚀(轴瓦钢背、飞轮压紧处、飞轮壳压紧处、湿缸套止口处等)、电蚀(火花塞电极等)和(水泵叶轮等)。
A.10摩擦副接触状态的评定
主要摩擦副[(8.6b)]的接触带应在正常位置,接触面积大小恰当,不得有断带现象。
A.11零部件表面沉积物的评定
A.11.1按表A.5对活塞环槽和环表面的沉积物进行分类。
表A.5活塞环槽和环表面沉积物的分类
形
类程危害环与环槽沉积物厚状几乎看不到沉A轻微沉积灵活有明显的沉积物活B中等沉积未占满间量少饨转沉积物较多几可能引起故C较严重沉积不灵)占满间
死转占满间导致重大故D
严重沉积)
动A.11.2分析油底壳、罩盖、缸盖上表面、活塞、进气门和凸轮等表面上的沉积物、油泥及漆膜,评定油料品质和零部件工作状态的关系。