2期密闭电石炉自控技术方案要点.docx
《2期密闭电石炉自控技术方案要点.docx》由会员分享,可在线阅读,更多相关《2期密闭电石炉自控技术方案要点.docx(17页珍藏版)》请在冰豆网上搜索。
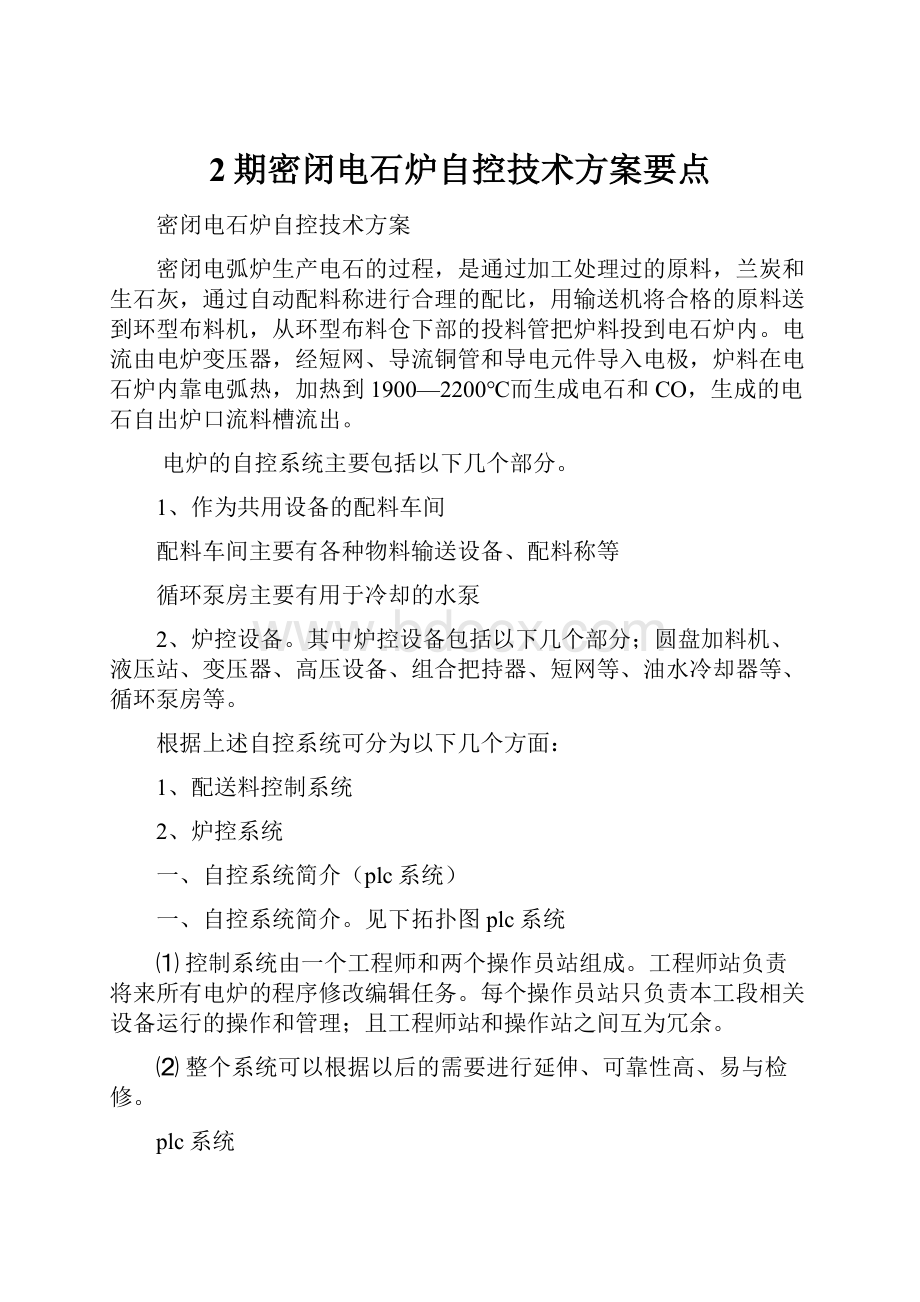
2期密闭电石炉自控技术方案要点
密闭电石炉自控技术方案
密闭电弧炉生产电石的过程,是通过加工处理过的原料,兰炭和生石灰,通过自动配料称进行合理的配比,用输送机将合格的原料送到环型布料机,从环型布料仓下部的投料管把炉料投到电石炉内。
电流由电炉变压器,经短网、导流铜管和导电元件导入电极,炉料在电石炉内靠电弧热,加热到1900—2200℃而生成电石和CO,生成的电石自出炉口流料槽流出。
电炉的自控系统主要包括以下几个部分。
1、作为共用设备的配料车间
配料车间主要有各种物料输送设备、配料称等
循环泵房主要有用于冷却的水泵
2、炉控设备。
其中炉控设备包括以下几个部分;圆盘加料机、液压站、变压器、高压设备、组合把持器、短网等、油水冷却器等、循环泵房等。
根据上述自控系统可分为以下几个方面:
1、配送料控制系统
2、炉控系统
一、自控系统简介(plc系统)
一、自控系统简介。
见下拓扑图plc系统
⑴控制系统由一个工程师和两个操作员站组成。
工程师站负责将来所有电炉的程序修改编辑任务。
每个操作员站只负责本工段相关设备运行的操作和管理;且工程师站和操作站之间互为冗余。
⑵整个系统可以根据以后的需要进行延伸、可靠性高、易与检修。
plc系统
工程师站操作员站操作员站
配料站1#炉炉控2#炉炉控
plc系统
⑶一般情况下,一个操作站负责配料,另一台操作站负责布料及电炉相关设备的操作。
⑷每台电炉都配有手自动两用操作模式。
⑸手动台的功能:
能手动完成电极压放、电极升降;电炉停送电,并有自锁装置,防止误操作。
能操作变压器的档位。
能远程启动液压站、并显示系统压力;能显示三相进线电压、三项一次电流、三项二次对地电压;三项二次电极电流、每个电极的功率因素、总有功、总无功。
见下图
二、自控系统功能介绍
(一)配送料系统
1实现手动操作和自动控制配料功能;
2生产过程动态模拟,能实时显示工作状态和每种物料的目标重量,实际重量。
3可随时变更配方。
4每批料数据都有历史记录,可对耗料进行报表统计、查询统计。
5报表打印和预览
6现场配有称重控制箱
7上料车定位功能
8手动可以在现场、计算机远程操作;自动可以通过锁定或解锁功能操作某一段或全部。
(二)炉控部分
1布料控制:
⑴自动时根据料位情况,自动补料,也可以进行某一段的自动操作;手动可以在电脑或手动台远程操作,也可以现场操作。
⑵在电石冶炼过程中,还经常发生物料不能自行落下的现象,从而导致物料在料仓中燃烧,而烧毁料仓及检测元件,故根据下料的速度确定某根料管超过一定时间没有进行配料,则该料管报警。
同时还显示设备运行的状态
2电极升降:
手动可以在手动台或现场进行操作;自动时,按照目标值,系统自动控制电极升降的行程,通过位移传感器的检测显示大立缸的行程及控制上限、上上限;下限、下下限并报警。
电极升降的操作分为远程、就地两种模式。
3电极压放:
自动压放和手动远程、现场手动压放。
⑴自动压放由系统自己完成,可根据实际工矿调节压放时间和次数
⑵通过旋编的有效测量,统计每一次的压放量、每班的压放次数和压放量。
⑶压放时有自动、手动远程、现场等多种操作模式。
远程在手动台或计算机上操作。
4高压设备可通过符合国标或国际标准协议的通讯接口自动链接在控制系统,以检测停送电及负荷运行情况。
手动在手动台进行操作并有自锁装置,防止误操作。
5变压器部分:
⑴自动检测油温、水温、瓦斯及报警。
⑵控制油水冷却泵工作。
⑶在计算机上,显示和操作变压器的档位及报警。
6液压站部分:
⑴对于储能式液压站,根据系统压力自动控制液压泵并报警,手动台显示系统压力同时可操作液压泵的起停。
⑵可以手自动控制压放台的各种电磁阀。
⑶液压站油温检测及自动控制,确保夏天不过热,冬天油路不冻结,而影响生产。
⑷油路压力继电器动作报警
⑸过滤油泵压力继电器动作报警
7循环水部分:
⑴主要检测系统水压及各个冷却水槽的水压、控制循环水泵和系统水压。
⑵检测、显示各个冷却水管的温度及报警。
每一个冷水管道,并可在计算机系统设定上限、上上限报警值。
⑶水循环组态界面相当于一台电炉的实际效果图,便于平时的维护和检查。
如下图所示
8冶炼过程工艺参数
⑴炉压:
炉膛压力是密闭炉生产的非常关键的仪表,按照密闭炉正常生产要求,炉压保持在正负10Pa作用,选择正负300Pa的炉压变送器,实现炉压检测。
由于密闭炉炉气温度越高,并且含有焦油、灰尘较多,因此炉压检测仪表必须配置降温、降尘专用的灰尘装置,并且系统要配置手动清灰装置,间隔一定时间对炉压检测管进行氮气反吹扫,确保炉压的检测稳定可靠。
⑵炉气温度:
密闭炉炉气温度能够间接反映电炉炉膛内温度,炉膛温度越高,炉内温度越高,根据实际应用经验,选择0—1100摄氏度的热电偶即可以安全可靠检测。
⑶氢、氧、一氧化碳的显示
⑷直排阀的手动控制,在净化系统出现问题时,可手动打开阀门。
⑸一次线电流:
密闭电炉一般都采用三台单相变压器给炉体供电,炉内负荷大小从变压器的一次电流能够直接看出来。
⑹二次电极电流:
每根根据能量守恒原理计算出二次电流,反映给表工,以便操作。
⑺二次相电压:
二次相电压是表征电极相对于炉底的高度
⑻流压比:
二次电流对二次电压的比值,每根电极的电流电压比
⑼操作电阻:
每根电极的操作电阻,是衡量物料均衡的一个重要参数。
⑽每根电极的功率因素、有功、无功。
⑾炉底温度一只热电偶
⑿炉底分机的控制
三、工艺简介主要包括下面几个方面
1、配送料部分
2、炉控部分
(一)配送料部分
原料输送到原料仓的控制部分。
配料控制控制部分。
混合料输送过程的控制部分
⑴原料贮运;电石生产主要原料焦炭、石灰、电极糊控制生石灰过烧率小于2%,石灰氧化镁含量小于1%,石灰粒度5-40毫米,焦碳含水小于2%,操作电流小于75-80KA,焦炭干燥时由装载机送到受料斗中,经带式输送机及斗式提升机送到破碎筛分楼筛分5-25mm通过带式输送机送至炭材干燥中间料仓。
石灰需要时经带式输送机送至石灰破碎筛分楼进行破碎筛分。
破筛后8~45mm的石灰大倾角输送机送至配料站配料。
0~8mm的石灰送至石灰粉仓;
⑵炭材干燥;合格粒度(≤40mm)焦炭由胶带输送机分别送入湿焦炭仓,再由电机振动给料机把焦炭送入回转干燥机进行烘干。
经过烘干后的物料由胶带输送机斗式提升机送往配料站,储存备用。
烘干炭材的热量由热风炉供给,达到400~600℃,炭材物料流入烘干机内,由回转干燥机转动,其内部栅格式扬板使物料均匀扬起,使热风与物料充分接触,热风把物料中水份带走,起到干燥物料作用。
热风炉以煤为燃料。
用过的热风低于160℃进入旋风除尘器、布袋除尘器净化排空,收集的炭材粉被送入炭材粉仓,除尘后的废气达标经烟囱排空。
1、原料输送工艺流程:
即原料送到原料仓部分
⑴石灰输送过程总料斗V010×2只——电震机D0#×2——大倾角皮带机L0101——分料器X0103×2台——大倾角皮带——筛分机——配料站可逆皮带L0202——原料仓V0202×8只。
⑵兰碳输送过程:
烘干的兰碳皮带机L0102——大倾角皮带机L0201——震筛机X0201——合格的兰碳到可逆皮带机L0202——兰碳储料仓V0202×8只
⑶原料输送过程自动化控制要求,根据原料仓的料位控制送料过程,当原料仓的原料处于低位时,送料设备根据所需的料仓的呼叫,进行补充加料。
当原料仓的料位处于高位时,送料设备停止送料。
⑷原料仓的料位的确定,下料位一般安装在能保证2个小时以上的用料;上料位安装在原料的堆积角的下沿,从而保证原料不冒顶。
⑸原料仓顶部的可你行走皮带机的控制,一般根据原料下了口的位置进行初步定位控制,从而保证给所需的料仓进行补料。
⑹综合以上所诉,原料输送的控制是,如1#石灰仓低料位呼叫,配料站可你皮带机工作找到1#石灰下料仓的入口——筛分机工作——大倾角皮带机工作——粉料器切到所需的部位——大倾角L0101——电震机工作。
料加满后,送料设备按照启动的逆向逐步停止。
即,送料设备的起动与停止是顺其逆停。
2、配料控制部分一般电石炉配料系统在配料车间(或配料站)完成配料,称重设备采用三用一备,两台电石炉使用四台配料称。
⑴配料工艺过程
石灰振动给料机——配料秤——振动给料机
兰碳震动给料机——配料称——震动给料机
⑵配料控制原理
配料控制原理:
采用减重法进行配料,首先将称重斗上满,即基本达到额定计量(入1000KG左右),后运行称重斗下振动给料机,先高速运行,再根据下料的情况逐步减速,直至停止。
这里在上振动给料机运行时,下振动给料机停止;反之,亦然。
⑶称重模块的安装方式见下图:
传感器的安装采用悬臂梁安装方式和拉式两种方式。
A、拉式安装采用S型传感器,安装方便,传感器量程选型范围较宽。
B、压力式采用悬臂梁传感器,安装要求较高,称重斗间隙较小。
如下图
⑷配方设置:
在配料之进行配方前,必须进行配方设置,点击配方设置按钮,弹出设置窗。
仓号:
系统自动根据选定仓号打开电震机配料。
物料名:
填写对应仓号的原料名称,保证一致。
目标重量值:
配方中各原料所需的重量。
当配方修改后,需要保存到当前配方名或另存为其他配方名,点击保存配方按钮,
统计值实时值显示
报表打印和预览
3、混合料输送过程的控制部分
由于配料和混料基本采用2用2备的,这里只叙述一条合格原料的输送过程。
其工艺过程如下
⑴配好的合格石灰——V203配料仓——粉料器X0205——上皮带机L0203(下皮带机)——粉料器X0206——大倾角皮带机
⑵配好的合格兰碳——V203配料仓——粉料器X0205——上皮带机L0203(下皮带机)——粉料器X0206——大倾角皮带机
这里的控制要求同样是顺起逆停。
配送料的控制及操作见下图
炉控部分包括布料控制;液压站部分;电极升降缸控制及电极压放控制;变压器的检测;高压分合闸;电炉生产所需的工艺参数和循环水部分,具体参看以下叙述。
(二)混合料布料过程控制部分
1、根据电炉下料仓的料位情况,控制方法采用呼叫优先原则。
如1#料仓需要配料,在上限位发出信号时,则开启圆盘下料机并延时启动1#气动、阀延时启称卸料结束。
输送系统依次延时待料走完后,依次停止相应设备;停设备时,与启动相反。
当料位达到下料位时,即刻报警准备停炉。
十二个料仓的下料位以或逻辑相连接。
2、炉上12只混料仓
3、每料仓安装料位计两只,料位计采用高性能阻悬式料位计,电气信号为开关量
4、上限料位开关为缺料——加料开关,当上限为料位开关发出缺料信号时,通知配料计算机,起动原料输送系统和环形给料机,以及启动环形给料机下料气缸,启动失重斗称配料系统进行配料。
每次配料只进一罐量,从而保证料仓不缺料。
故需计算上料位的高度。
5、当两仓以上的料仓发出缺料信号时,计算机按发出缺料信号的前后按次序调度配料。
6、下限料位开关为停炉信号开关,当下限料位开关发出信号时,电石炉马上采取停电措施,以防料封层破坏,炉气进入环性加料机产生爆炸事故。
7、当计算机发出向某仓配料的调度命令后,开始计时(时间依据为配料卸料时间+皮带输料时间+环形给料机下料时间),达到计时周期,缺料料仓仍然没有消除缺料信号时,计算机发出故障报警。
通知巡检人员进行检查。
8、12只电炉料仓在下料时,其下料的时间均不相同,在程序上可以设定某一最大时间,当某个料仓在规定的时间内没有呼叫加料,则报警并通知巡检人员,是否有情况。
(三)液压系统
液压系统由液压站和压放台两大部分组成,液压站为组合把持器和升降电极大立缸提供动力,通过组合把持器实现对电极的压放操作;同时还控制电极升降。
作为密闭炉系统,液压站的操作正确与否、准确与否非常重要,关系着安全生产,其控制功能及安全操作显得尤为重要,主要有以下几个部分。
1、液压站主要由油压、2台压放油泵、3台升降油泵、1台备用油泵、过滤油泵及1台冷却泵、油箱压力及温度检测元件组成。
2、各油路油压压力检测0—25Mpa,压力高低报警
液压站油温检测及自动控制,确保夏天不过热,冬天油路不冻结,影响生产。
3、电极压放和升降时对应油泵自动启动,延时停止,使得控制操作既简单方便、又节能,减少设备磨损。
4、油路压力继电器动作报警
5、过滤油泵压力继电器动作报警
6、备用泵切换只需要选择对应油泵开关即可,投备切换选择开关为能够360度旋转,六位,分别为备用泵、压放泵、升降泵1、升降泵7升降泵3,投备切换选择是只需将旋钮开关选择至对应油泵即可,系统自动将油路电磁阀切换至对应油路,无需调整线路。
8、目前有很多企业使用的是储能式液压站,其结构简单,电机数量也少,维护方便
9、油泵紧急停止
10、加热器及送风机控制:
能够对三相电极加热器实现中温、高温、低温控制及监视;能够对三相电极加热器送风机实现控制及监测。
(四)压放及大立缸的控制过程
组合把持器简介:
本案组合把持器有七个夹紧横向小油缸及七个纵向压放小油缸组成。
夹紧油缸可松开和包紧电极上的7道筋肋,压放油缸使横向油缸上升或下降2cm,完成电极压放。
电极在工作中始终保持一定的长度,可实现电极定时压放(根据电极工作部的长度决定),累计压放的长度与电极消耗应相平衡;每组油缸有一个夹紧油缸和一个压放油缸,共需要14电磁阀。
控制要求如下,在油压保证前提下,压放过程是:
每个电极上的7个小油缸先处于抱紧状态,先松开一个夹紧小油缸,上升该组小油缸,上升到位后,抱紧该组压放小油缸,再如此执行完剩余的小油缸的动作,最后同时下压,下压到位后就完成了小油缸的压放。
电极压放可实现定时自动压放。
1、电极压放控制:
电极压放有以下功能,自动压放和手动压放,自动压放可以定时压放,也可以手动单步完成。
2、电极压放由夹紧压放油缸控制,正常时电极由夹紧油缸上的碟簧张力作用于卡钳来夹持电极。
压放时,夹紧油缸得油卡钳松开电极筋板,压放缸下腔给油,压放缸升起,然后夹紧油缸泄油卡钳又夹紧电极筋板,夹紧油缸顺序完成以上动作后,压放油缸同时给油实现电极的压放。
3、压放手动控制单组油缸分别实现夹钳松、把持缸升动作,全部执行完成后进行整体压放;开关360度旋转,操作方便简单。
4、自动压放:
电极压放过程控制:
电极压放系统可按下列三种途径实现,一是自动压放,也就是计算机定时压放;另一种压放是人工压放,即在操作室和电脑操作台由操作人员根据电极位置开关量显示位置,采取的不定时压放;第三种压放方式为机旁压放,即通过压放箱的手动按钮进行压放,主要为维护和调整时使用,每根电极上装有位移传感器,用以准确显示把持器压放的距离及报警。
每电极有7组液压夹钳升降缸,以一号电极为例,逻辑次序为
a夹钳松开→a夹钳上升→a夹钳夹紧→
b夹钳松开→b夹钳上升→b夹钳夹紧→;
c夹钳松开→c夹钳上升→c夹钳夹紧→
d夹钳松开→d夹钳上升→d夹钳夹紧→
e夹钳松开→e夹钳上升→e夹钳夹紧→
f夹钳松开→f夹钳上升→f夹钳夹紧→
g夹钳松开→g夹钳上升→g夹钳夹紧→
a、b、c、d、g、f、g夹钳缸全部下降,实现一次下降。
5、电极升降控制:
电极升降由液压装置给与动力。
电极升降靠两侧大立缸来完成,上升阀得电时电极升起;下降阀得电时,电极下降。
6、通过电极升降动作,能够调整入炉功率,采用电阻或电流冶炼时,三相电流或电阻得平衡成为关键因素,这就要求系统能够自动调节三相电极升降,达到三相基本平衡。
7、电极升上限、下限位保护,防止电极提出水冷套或者下降至炉底造成事故,通过位移传感器的检测,在计算机上显示大立缸的行程。
8、电极工作长度检测(计算tga折算长度加水冷套上沿与护屏上沿的距离)
(五)变压器部分
1、变压器档位的显示和操作
2、变压器油温、水温的报警;油水冷却泵的控制
3、变压器容量的实时监测和报警
4、变压器瓦斯报警
(六)电炉高压分合闸控制
1、专用高压分合闸开关,具有预备合闸、合闸;预备分闸、分闸四个状态位的分合闸开关
2、电炉分合闸锁:
由于电炉变采用35KV直接上炉,开关站35KV开关接到合闸命令后执行动作,容易由于储能机构的原因,造成合闸失败(自动控制系统识别为回讯故障),在机构检修正常后会自动合闸,因此必须将电炉分和闸锁加锁,避免电炉在条件满足后自动送电,发生误送电事故。
3、紧急分闸按钮:
在遇到特殊情况下,考虑安全的因素,可以直接拍下紧急分闸按钮,系统会将电炉变,确保安全。
(七)电炉工艺参量
1、炉气温度:
密闭炉炉气温度能够间接反映电炉炉膛内温度,炉膛温度越高,炉内温度越高,根据实际应用经验,选择0—1100摄氏度的热电偶即可以安全可靠检测。
2、炉膛压力:
炉膛压力是密闭炉生产的非常关键的仪表,按照密闭炉正常生产要求,炉压保持在正负10Pa作用,选择正负500Pa的炉压变送器,实现炉压检测。
由于密闭炉炉气温度越高,并且含有焦油、灰尘较多,因此炉压检测仪表必须通过降温处理,并且还要配置手动或自动清灰装置,间隔一定时间对炉压检测管道进行氮气反吹扫,确保炉压的检测稳定可靠。
3、直排阀;遇到特殊情况,按下急停按钮,阀门自动开启,保护人生设备的安全。
4、炉底温度检测,测量每只电极底部的温度,炉底风机手动控制
5、一次电流:
密闭电炉一般都采用三台单相变压器给炉体供电,炉内负荷大小从变压器的一次电流能够直接看出来。
5、二次电流;利用能量守恒原理计算出二次电流,反映给表工,以便操作。
6、二次对地电压:
间接反映电极的深浅程度
7、流压比:
二次电流对二次电压的比值
8、运动电阻;根据电炉的某些电参数,可以计算出能够反映电炉炉况电阻的工艺参量。
由运动电阻可以判断在同一种物料的情形下,电极应该上升还是下降的操作。
9、操作电阻:
主要用来控制电流电压比。
同时也是衡量物料均衡的一个重要参数。
10、每根电极的一次电流、一次电压、二次电流、二次电压、功率因素、有功、无功及每个班实际用电量等。
11、电压档位,可通过上位机和仪表进行操作并显示。
12、炉底温度及炉底分机的控制
13、氢、氧及一氧化碳含量的显示和报警
(八)循环数部分:
主要完成电炉冷却水的检测、控制、报警,监测部位如下:
1、循环水进口压力、温度各一个
2、每个循环水槽进口水压一个
3、循环泵的水压调节
4、各冷却管温度,共计81个,所列如下:
直排烟囱4组;变压器6组;底部环9组;护屏12组;短网21组;备用3组;密封套3组;水冷套6组;中心盖板6组
(九)炉控主画面