轮胎的设计与制造.docx
《轮胎的设计与制造.docx》由会员分享,可在线阅读,更多相关《轮胎的设计与制造.docx(11页珍藏版)》请在冰豆网上搜索。
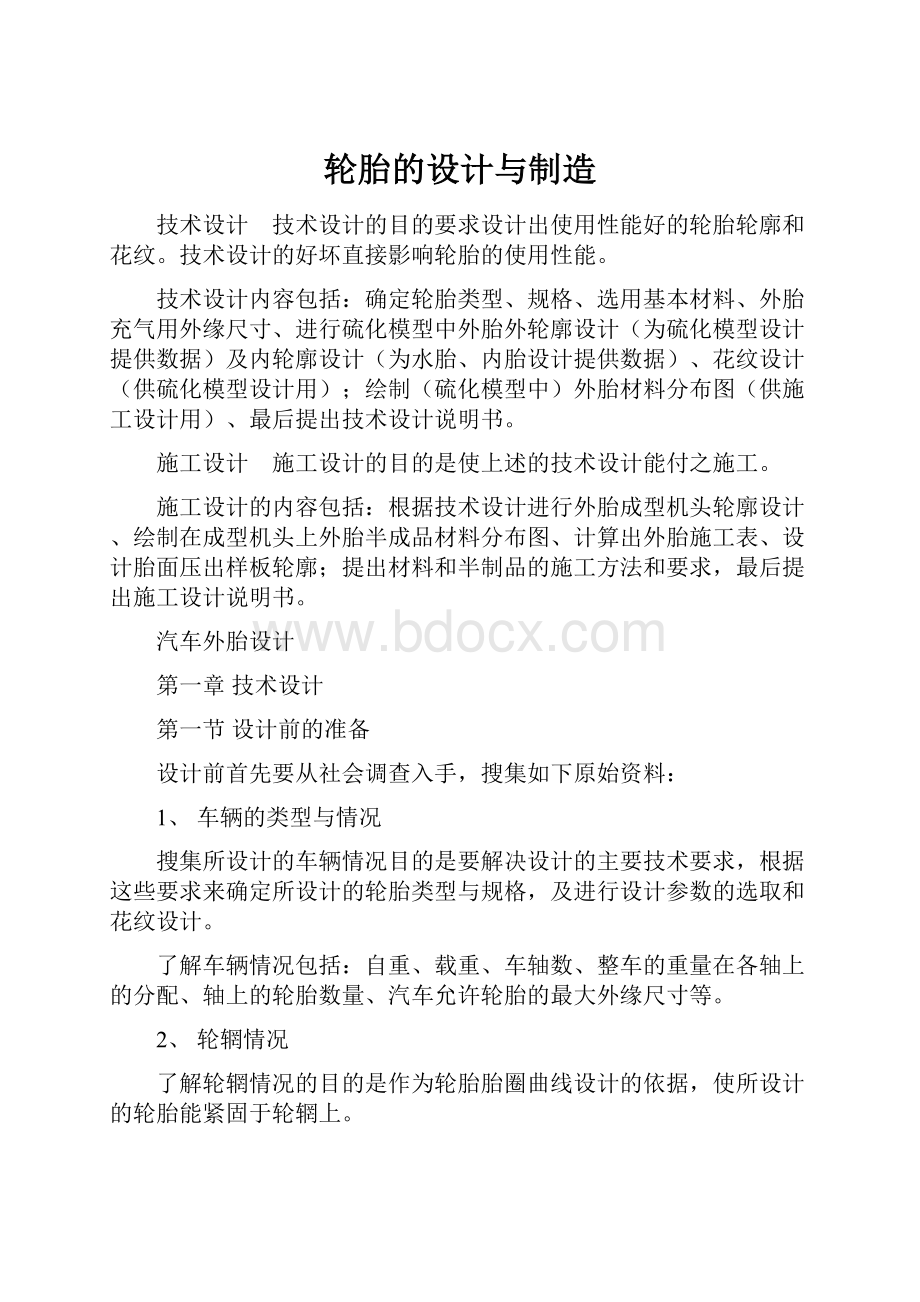
轮胎的设计与制造
技术设计 技术设计的目的要求设计出使用性能好的轮胎轮廓和花纹。
技术设计的好坏直接影响轮胎的使用性能。
技术设计内容包括:
确定轮胎类型、规格、选用基本材料、外胎充气用外缘尺寸、进行硫化模型中外胎外轮廓设计(为硫化模型设计提供数据)及内轮廓设计(为水胎、内胎设计提供数据)、花纹设计(供硫化模型设计用);绘制(硫化模型中)外胎材料分布图(供施工设计用)、最后提出技术设计说明书。
施工设计 施工设计的目的是使上述的技术设计能付之施工。
施工设计的内容包括:
根据技术设计进行外胎成型机头轮廓设计、绘制在成型机头上外胎半成品材料分布图、计算出外胎施工表、设计胎面压出样板轮廓;提出材料和半制品的施工方法和要求,最后提出施工设计说明书。
汽车外胎设计
第一章技术设计
第一节设计前的准备
设计前首先要从社会调查入手,搜集如下原始资料:
1、车辆的类型与情况
搜集所设计的车辆情况目的是要解决设计的主要技术要求,根据这些要求来确定所设计的轮胎类型与规格,及进行设计参数的选取和花纹设计。
了解车辆情况包括:
自重、载重、车轴数、整车的重量在各轴上的分配、轴上的轮胎数量、汽车允许轮胎的最大外缘尺寸等。
2、轮辋情况
了解轮辋情况的目的是作为轮胎胎圈曲线设计的依据,使所设计的轮胎能紧固于轮辋上。
了解轮辋的情况包括:
轮辋的类型、轮辋的规格与代号、轮辋的断面曲线等。
见《橡胶手册》P177—P185。
3、双轮距
轮胎充气后在负荷下的断面宽不能超过双轮距,否侧装双胎的两胎胎侧会互相磨擦。
一般两胎间的间隙要求在25—30mm。
4、车速其它使用条件如路面情况
高速车与底速车的设计参数是有区别的。
高带车要求速度高、安全、行驶平稳。
底速车一般为载重用,要求载重量大、速度也要快。
了解路面情况和使用条件(耐热、耐寒等)是给花纹设计提供依据用。
5、单胎负荷要求
了解单胎负荷是供确定轮胎规格及 帘布层层数之用。
6、国内外其它厂、牌同规格轮胎的结构及使用情况。
1层数、内压、负荷及层级等方面情况。
2充气前、后以及负荷下的轮胎和曲线变化情况。
3轮胎物理机械性能试验及机床试验情况。
4实际使用中的性能和优缺点情况。
5使用单位的建议和要求。
第二节 确定技术要求
在完成原始资料搜集工作的基础上,对新产品设计应与使用方确定技术要求,以作为设计依据。
设计后可进行试产,试验后经试验和使用鉴定后再确定为暂行技术标准,经主要领导部门批准后进行生产。
对于改进产品设计亦应在充分收集资料的基础上,根据国家标准或新定产品技术要求进行设计。
技术要求包括:
1、轮胎类型、规格、帘布层数、胎面花纹。
2、基本系数、最大负荷(kg)、相应气压(kg/cm2)标准轮辋或适用轮辋。
3、主要尺寸:
充气后外直径D`及断面宽B`;负荷下静止半径和断面宽;内胎双层最小厚度;垫带中部最小厚度及边缘最大厚度。
4、内胎气门嘴型式或尺寸标准。
5、要求行驶里程或使用寿命。
第二节设计步骤与方法
一、确定骨架材料:
人造丝、尼尨、钢丝。
二、确定轮胎类型:
根据车辆的类型及使用条件而定。
三、确定轮胎的规格:
根据要求的单胎最大负荷量、充气压力、轮辋标准、汽车予留给轮胎的空隙、双胎距、道路条件等而定。
所选取的轮胎规格其允许最大负荷量应大于车辆制造厂所规定的单胎最大负荷量,一般大5~10%,这样当车辆稍超载时,轮胎不致于超负荷使用,以保证轮胎的行驶寿命。
四、确定设计时所用轮辋型号、规格。
五、确定充气后外缘尺寸:
包括充气后外直径D`及充气后断面宽B`,各种规格的轮胎充气后外缘尺寸一般都有国家标准,故设计的轮胎其充气后外缘尺寸应在国家标准允许公差范围内,并参考国内、外同类型、同规格轮胎的尺寸。
六、轮胎负荷能力的计算:
选定轮胎规格及确定轮胎充气后外缘尺寸之后,必需验对其负荷能力,应用海尔公式进行验算,算出的负荷能力应大致符合国家标准规定,而要大于车辆制造厂规定的单胎负荷量,一般大5~10%。
海尔公式:
Q=0.231AKP0.585BM1.39(BM+d)
式中:
Q——轮胎实际负荷能力kg
A——速度系数见表2-1-1
K——轮胎类型系数见表2-1-2
P——轮胎充气压力kg/cm2
d——轮辋直径cm
BM—在理想轮辋上充气轮胎断面宽cm
其计算可才用下式:
(角度比例法)
(公式推导见附录)
(1)
表2-1-1
行驶
路面
与车
速
非公路行驶胎
正常路面
各种车速
16km/小时
良好公路
最大车速16km/小时
最大车速16—40km/小时
A
1.45
1.40
1.35
1.30
1.25
1.20
1.00
1.70
1.20
2.00
备注
断面宽
平板拖车用
静负荷用胎
6.00~
14.00
16.00~
21.00
24.00~
32.00
6.00~
14.00
16.00~
21.00
采矿与伐木用
24.00~
30.00
采矿与伐木用
表2-1-2
轮胎类型
低压乘用胎
低压载重胎
农业拖拉机胎
宽轮辋拖拉机胎
K
0.425
0.465
0.476
0.392(农业机械胎)
拖拉机胎0.225
0.255
备注
棉线胎体
人造丝胎体
尼龙胎体
限于24吋直径轮辋
①限于24吋直径轮辋
②BM为轮辋宽与断面宽之比为80%的轮辋上测定
规格:
在确定轮胎程负荷下的静半径时,应根据各种轮胎的压缩系数适当考虑,一般载重胎的压缩系数为10—13%,轿车胎为14—16%,农业拖拉机和工程机械胎可达20%左右,同种轮胎在不同使用条件下可用不同的压缩系数,走在好路面上行驶时,则采用较低的气压,高载轮胎中的第二层级轮胎的压缩系数同第一级轮胎(一级胎)一样,内压比第一层级高20%,第二层比第一层高5—10%,同时,内压也比第一层级轮胎高30%左右,在确定轮胎负荷及断面宽时,应保证双轮间距在20mm以上。
(2)
(3)
当使用轮辋宽对充气轮胎断面宽之比(C/B`)接近0.625时,用
(1)式;当C/B`接近0.7时,用
(2)式;当C/B`接近0.85进,用(3)式。
轮辋类型、规格、代号确定后,轮辋宽度C便可查手册得出。
BM也可用下式计算:
(尺寸比例法)
式中:
B`、C同上,当确定轮辋宽度时应根据充气轮胎断面度来选定:
一般比值为:
C/B`(载重)普通轮辋0.6~0.66、宽轮辋0.7~C/B`(轿车)普通轮辋0.85、宽轮辋0.7
K1—为充气轮胎断面宽变化系数,北京橡胶院根据实测及国外资料统计,认为载重尼龙胎K1选取0.400是比较适宜的。
B1`、B2`——分别为宽轮辋,窄轮辋上充气轮胎断面宽;
C1、C2——分别为宽轮辋宽、窄轮辋宽。
无论用角度比例法或是尺寸比例法算出的BM的数据是非常接近的。
另外北京橡胶院郑正乍付总工程师自1973年以来以美国TRA公式为基础,对轮胎负荷计算公式进行了一系列的研究,在《橡胶工业》1978年3期上发表了他的负荷计算公式,计算方法简单,计算结果接近美国公式。
从海尔公式说明了如下几个问题:
1、内压与负荷的关系
从公式可知,轮胎的负荷能力随其充气压力增大而增大,因此,不同的内压有其相应的负荷能力。
如表2-1-3所示。
表2-1-3 9.00-20尼龙胎的气压和负荷标准
层级
10
12
气压P kg/cm2
4.25
4.5
5.0
5.25
5.6
6.0
负荷Q kg
1670
1760
1830
1910
1980
2050
空心轮胎的负荷由内压来承受,而内压是由胎体帘线承受。
因此,为提高负荷能力,不能无限制地增加压力,否则帘线受力大,胎体安全倍数下降。
因此各种规格的轮胎,在技术条件中都要规定其使用内压标准和负荷标准。
以保证轮胎既有较高的负荷能力,而又有良好的使用性能及较长的使用寿命。
2、内压负荷与变形的关系
轮胎在超负荷与内压不足的情况下都会导致轮胎变形增大,即下沉量增大。
这样,由此而产生的各部件应力也增大,会出现肩空、肩裂。
负荷下的下沉量,计算其下沉率,数据填在上表中,并对该胎进行水压爆破试验,计算轮胎实际安全倍数,数据填在上表中。
最后才根据该类型的轮胎所规定的下沉率范围和胎体安全倍数来确定所设计的轮胎的使用负荷标准和内压标准。
3、轮辋宽、轮胎断面宽与负荷的关系
在设计时如果轮辋型号、规格已为车辆设计时所决定,则轮辋宽度就已确定下来了,不存在选用轮辋的问题。
否则,应尽可能选用较宽的轮辋,因为轮辋增宽,轮胎充气断面宽增大,上面充气轮胎断面宽变化系数
的值说明了轮辋宽度增加1毫米,充气轮胎断面宽增大K1毫米(K1为正值)。
轮胎充气后断面宽增大,则轮胎的负荷能力就随之提高,如图2-1-1所示。
且轮辋增宽,车辆行驶平稳,临界速度可提高,在保持原来负荷能力前提下,还可适当降低内压,改善缓冲性能。
因而,目前无论是载重胎还是乘用胎都向宽轮辋方向发展。
七、硫化模型中外胎的横断面外轮廓设计
(一)断面宽B与断面高H外直径D的确定
首先确定H/B值,然后根据B`/B值的变化范围,并参考相同或接近于所设计的外胎(规格和H/B值都相同或较接近)的外缘尺寸变化实测结果,最后才确定B`/B值,通过下式算出B、H、D值:
式中B`——充气外胎断面宽,其它符号同上
将计算出的B用接近所设计的外胎(规格H/B均相同或接近)进行实际测量来校正。
B确定后计算H及D:
式中:
d——轮辋直径,
其它符号意义同上。
为加工方便,B、H和D计算结果必需取整数(以mm表示),然后再反过来核算所取的设计参数H/B、B`/B。
H/B取值范围如下:
载重胎:
普通花纹1.10~1.20
越野花纹1.15~1.25
轿车胎:
普通花纹0.96~1.14
越野花纹1.08~1.20
日本轿车胎:
普通结构0.92~0.97
0.85~0.90
0.80~0.93
0.78、0.70、0.60
子午胎结构0.70~0.78
B`/B取值范围如下:
载重胎1.08~1.15
轿车胎1.06~1.12
上述的设计顺序是先计算断面宽B,然后计算断面高H和外直径D。
也可先计算外直径D,然后计算断面高H和断面宽B。
方法如下:
计算模型外胎外直径D:
式中D`——充气外胎外直径;
D`/D——充气外胎外直径与模型外直径之比。
其取值范围如下:
载重胎0.990~0.999
轿车胎0.985~0.999
载重胎B比充气胎小8~15%,D大0.1~1.0%;
轿车胎B比充气胎小6~12%,D大0.1~1.5%
计算断面高H:
式中符号意义同上。
图2-1-2外胎断面示意图
计算断面宽B:
关于H/B、B`/B、D`/D三个设计参数:
1、H/B值
①H/B值对轮胎形状,变形情况,使用性能的影响H/B值是轮胎结构设计中具有代表性的参数,它决定了轮胎的形状及轮胎充气前后外轮廓基本尺寸变化情况(见第二章第一节),因而H/B值直接影响着轮胎的使用性能,从而其它结构参数的先择必需考虑H/B值的影响。
H/B值大,轮胎断面外形较直,即胎侧曲率较小,胎侧屈挠范围大,能分散肩部和子口部的应力,从而可改善那两个部位的质量毛病。
过去使用的窄轮辋,C/B值较小,在负荷作用肩部和子口部受应力较大,加上过去多使用棉帘线作骨架材料,其疲劳性能较差,因而常发生子口折断毛病。
为解决这个问题,一方面在轮辋宽度C没有改变的条件下减少断面宽B以增大C/B值,使屈挠应力上移,有效地减少子口部位应力,另一方面增大H/B,以增大胎侧曲挠范围,避免应力集中于子口,而且由于要提高里程,而将花纹加深,为使内轮廓接近圆形或长椭圆形,因而H/B值逐渐向增大方向发展。
如9.00-20的H/B值从1.092增大至1.164,H/B值大的另一优点是可提高胎面的耐磨性能,这是由于H/B值大,轮胎断面内轮廓呈长椭圆形,充气时接近圆形,以达到平衡轮廓,因而轮胎充气后断面膨胀率大,即B`/B>1,面外直径则收缩,即D`/D<1(见第一篇图2-1
(1)),胎面呈改缩状态工作,耐磨性好。
但H/B大的缺点是:
增大胎面与帘布层间剥离力及胎侧的伸张力。