溶液丁苯橡胶聚合工艺设计.docx
《溶液丁苯橡胶聚合工艺设计.docx》由会员分享,可在线阅读,更多相关《溶液丁苯橡胶聚合工艺设计.docx(41页珍藏版)》请在冰豆网上搜索。
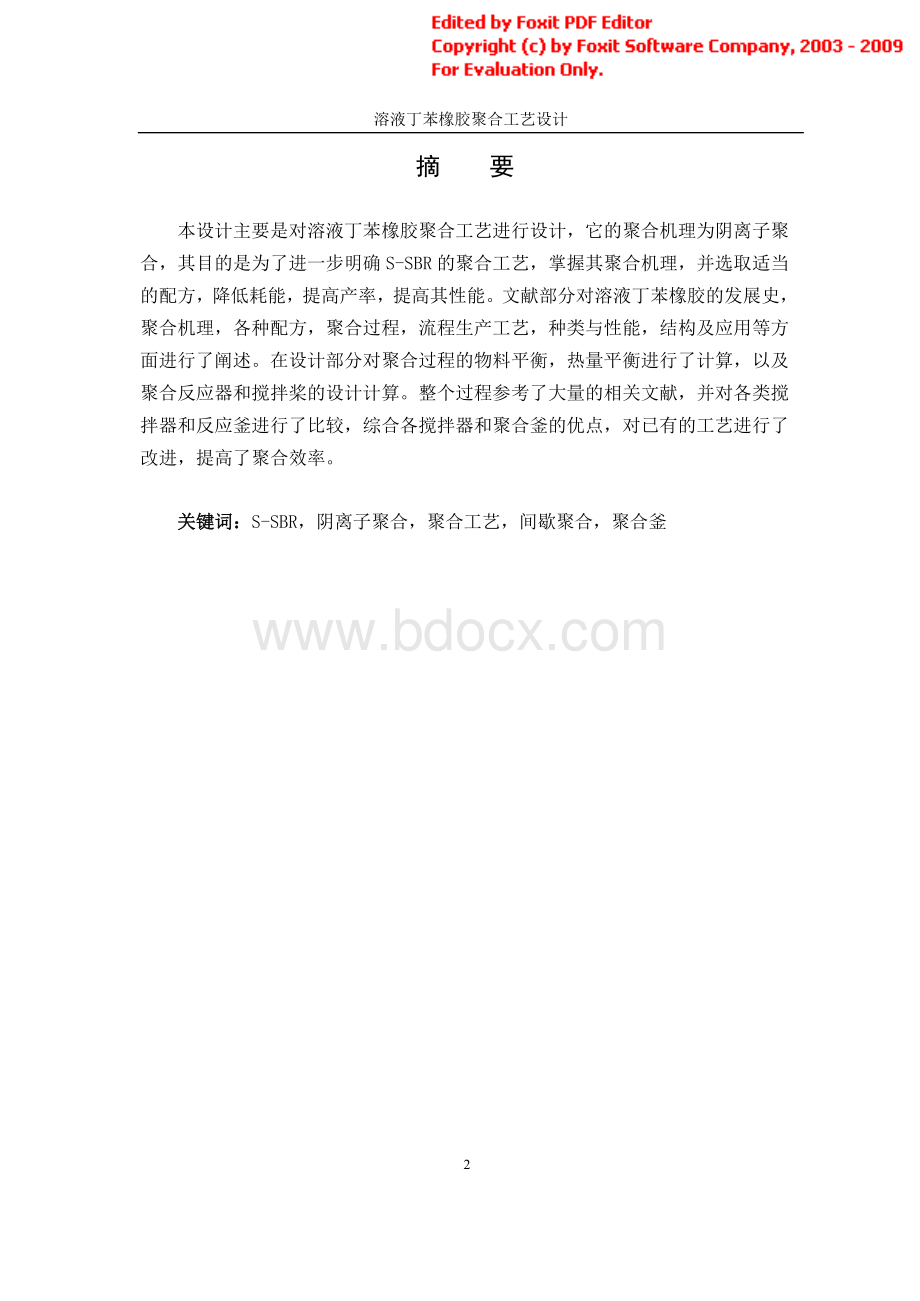
溶液丁苯橡胶聚合工艺设计
摘 要
本设计主要是对溶液丁苯橡胶聚合工艺进行设计,它的聚合机理为阴离子聚合,其目的是为了进一步明确S-SBR的聚合工艺,掌握其聚合机理,并选取适当的配方,降低耗能,提高产率,提高其性能。
文献部分对溶液丁苯橡胶的发展史,聚合机理,各种配方,聚合过程,流程生产工艺,种类与性能,结构及应用等方面进行了阐述。
在设计部分对聚合过程的物料平衡,热量平衡进行了计算,以及聚合反应器和搅拌桨的设计计算。
整个过程参考了大量的相关文献,并对各类搅拌器和反应釜进行了比较,综合各搅拌器和聚合釜的优点,对已有的工艺进行了改进,提高了聚合效率。
关键词:
S-SBR,阴离子聚合,聚合工艺,间歇聚合,聚合釜
III
Abstract
Thedesignismainlytodesignthesolutionstyrene-butadienerubberpolymerizationprocess.It’spolymerizationmechanismisanionpolymerization.ThepurposeofthedesignistofurthercatchontheS-SBRpolymerizationtechnics,masterthemechanism,choiceproperformulation,leasetheusingpower,improvetheyield,andimproveit’sperformance.TheliteratureisincludingthedevelopmenthistoryoftheS-SBR,polymerizationmechanism,differentkindsofformulation,polymerizationprocess,flowedproducetechnics,categories,property,construction,andapplicationandsoon.Besides,inthedesignpart,includethepolymerizationprocess’smaterielbalance,quantityoftheheatbalance,andpolymerizationkettle’sbeaterdesigncalculation.Duringthewholecourse,withamountofcorrelativeliterature,aftercomparingwiththedifferentbeatersandpolymerizationkettle,improvethepastmechanismandimprovethepolymerizationefficiency.
Keywords:
S-SBR, anion polymerization, polymerization mechanismintermittentpolymerization,polymerizationkettle
目 录
第一章 前 言 1
1.1总述 1
1.2内容简介 2
第二章 总 论 4
2.1文献 4
2.1.1 S-SBR聚合反应机理-阴离子聚合:
4
2.1.2 S-SBR的发展简史及与E-SBR的比较 5
2.1.3溶聚丁苯的结构、性能及应用:
8
2.1.4溶液丁苯橡胶的聚合工艺:
9
2.1.5生产控制因素 14
第三章 设 计 20
3.1物料衡算 20
3.1.1设计要求:
20
3.1.2原料要求:
20
3.1.3配方要求:
20
3.1.4反应时间及控制温度. 20
3.1.5计算过程:
21
3.2设备计算 23
3.2.1釜式聚合反应器的结构 24
3.2.2确定反应釜釜身与封头形式 24
3.2.3搅拌器的选择与确定 24
3.2.4计算与设计部分 25
3.3热量衡算 30
3.3.1数据整理 30
3.3.2计算过程 30
第四章 问题与发展前景 33
第五章设计体会与收获 34
参考文献 35
致 谢 37
附 图
A溶液丁苯橡胶生产工艺流程图B溶液丁苯橡胶聚合釜总图
5
第一章 前 言
1.1总述
溶液丁苯橡胶于60年代初由Firestone公司和Phillips公司率先实现工业化生产,最初的目的是因苯乙烯价格上升,想生产能达到乳液丁苯橡胶性能水平的低苯乙烯含量的溶液丁苯橡胶。
但很快就发现溶液丁苯橡胶具有比乳液丁苯橡胶更优异的机械性能,因而引起广泛的重视。
目前世界溶液丁苯橡胶总消费量大约占丁苯橡胶总消费量的40%左右。
基本生产技术:
溶液丁苯橡胶的工业生产中,通常使用烷基锂,主要是丁基锂为引发剂,烷烃或环烷烃为溶剂,四氢呋喃为无规剂,醇类为终止剂。
其基本技术路线有两种:
1)Phillips法:
该公司专利覆盖了连续聚合工艺和间歇聚合工艺,但以间歇工艺为主;2)Firestone法:
其基本工艺与Phillips法相同,以连续聚合为主,也可用间歇聚合工艺。
这两种工艺所生产的聚合物微观结构为:
顺式1,4-含量35%-50%,反式1,4-含量35%-55%,1,2-含量10%左右。
Phillips公司目前已经不生产溶液丁苯橡胶,但其技术仍被欧洲许多公司所采用,如Enichem和Petrochem公司等。
其它技术都是在上述两种基本技术的基础上发展的。
最早生产的溶液丁苯橡胶,其玻璃化温度低(Tg为-70℃左右),乙烯基结构含量只有10%-13%,分子量分布窄且呈单峰分布,虽然其耐磨性和耐寒性比乳液丁苯橡胶好,但粘着性能与加工性能稍差。
作为轮胎用胶没有表现出明显的优越性。
70年代中期,石油危机使汽车的节能成为突出的问题。
汽车的耗能中很大一部分用于克服轮胎的滚动阻力,小汽车总能耗的20%用于克服轮胎的滚动阻力。
而轮胎滚动阻力的将近40%产生于轮胎的胎面。
虽然轮胎的滚动阻力可以通过改进轮胎结构设计和改变胶料配方等手段得到改善,但是降低轮胎滚动阻力最根本的途径还是改善基础胶的性能,加之国外对轮胎在高速行驶下的安全和舒适性的要求也越来越高。
因此,开发既有低滚动阻力又有高抗湿滑性和耐磨性的新型胎面用合成橡胶成为国外合成橡胶生产者的研究开发重点。
由于锂系催化剂制备的合成橡胶,特别是溶液丁苯橡胶生产灵活性大,聚合物结构与性能易调节,便于通过高分子设计手段开发具有特殊性能的合成橡胶新品种,因而成为开发新型轮胎胎面用胶的重点目标。
品种:
1937年德国首先投入工业生产,是一种综合性能较好的通用型品种,
根据生产丁苯橡胶时所用聚合反应的温度,助剂及单体配比等的不同,丁苯橡胶的种类很多,主要者见表1-1。
表1-1丁苯橡胶种类
品名
特点
高温丁苯低温丁苯
充油丁苯
在50度左右聚合
在5度左右聚合,弹性大强度大,耐磨耗性好加有含芳烃或环烷烃的石油馏分,易加工较耐寒,成本低
充碳黑丁苯
加有碳黑,生胶混炼时的电力消耗少
充油-碳黑丁苯充树脂丁苯
加有碳黑和石油,兼有充油,充碳黑丁苯的特色
加有树脂,物理性能比一般丁苯好
丁苯橡胶外观是浅黄褐色的弹性体,微有苯乙烯那种气味。
商品丁苯橡胶除含生胶之外,还含有多种助剂之类的非胶成分。
丁苯橡胶的介电性能较好,和其他通用橡胶一样,它在空气中长期受氧的作用后,性能会逐渐变坏,特别是在高温和光线的照射下更是如此。
〔1〕
丁苯橡胶的粘结性不好,在用它制造多层制品如轮胎,帘布,运输带,胶管等时成型过程中的贴合就有些困难。
制品在多次变形时(如轮胎行驶过程中)的发热量大,相对地将缩短使用寿命。
此外,它的弹性也较差。
丁苯橡胶的硫化速度较慢,因此,硫化促进剂的用量要大些。
丁苯橡胶的组成结构与天然橡胶不同。
天然橡胶不同。
天然橡胶主要是由有规则的聚异戊二稀(顺式-1.4)链组成,而丁苯橡胶则是丁二稀与苯乙烯的不规整共聚物。
1.2内容简介
本文包括文献和设计两部分,文献部分从理论上对溶液丁苯橡胶进行阐述,具体讲为对溶液丁苯橡胶的发展史,聚合机理,各种配方,聚合过程,流程生产工艺,种类与性能,结构及应用等方面进行了阐述。
而设计部分则针对物料,设备,热量衡算来进行,通过根据额定年产量,反应时间,进料温度的计算,选取适当的聚合温度,完成聚合反应器和搅拌桨的设计计
35
算,并计算出换热面积及电机的功率,设计出一个较完整的流程,进行一万五千吨溶液丁苯橡胶的设计生产。
设计目的是,了解并掌握溶液丁苯橡胶的聚合机理,聚合工艺,并对已有的工艺进行了改进,提高聚合效率。
第二章 总 论
2.1文献
2.1.1 S-SBR聚合反应机理-阴离子聚合:
可以发生阴离子聚合的单体主要有两类:
一是乙烯基或二烯烃单体.它们须带有可使负电荷稳定的吸电子取代基.二是环状单体如内酰胺、内酯、环氧杂烷、异氰酸酪等。
阴离子聚合引发剂为碱、路易士碱等碱金属、金属碳基物、胺、磷化氢以及格氏试剂等。
多数情况下,所加入的引发剂本身含有聚合的引发种(中心);但有些情况下实际聚合引发种和所加入的引发剂是不同的,是引发剂与溶剂的作用产物,例如在二甲基亚矾溶剂中阴离子聚合通常在极性溶剂中进行。
这种情况下,对应阳离子的影响可减少,有机碱特别适合。
所以四氢映喃、乙二醇甲醚、等常用作阴离子聚合引发剂,
阴离子聚合反应历程包括链引发与链增长,根据需要,链终止可以避免。
链引发和增长聚合引发种和单体发生反应时有二种情况:
一是聚合引发剂和
单体分子之间有两个电子转移而生成一个键;二是单电子转移而不生成键,链引发后即与单体继续作用而链增长。
由于阴离子聚合反应可以生成稳定的增长链.所以必须加入含有亲电基团的链终止剂,才可使之链终止。
此时亲电基团结合于端基上,根据链终止剂的官能数可分为单分子终止,双分子终止或引入第二种单体进行嵌段共聚。
反应历程如下图2.1。
阴离子聚合反应主要特点:
不存在链终止过程、阴离子聚合反应生成的增长链端基是稳定的状态分子量随单体用量的增多而增加.并且分子量分布狭窄。
对应离子对链段结构产生的影响,与游离基聚合反应不同。
阴离子引发剂中对应离子对主链结构产生影响。
溶剂对反应条件的影响,与自由基聚合反应不同,阴离子聚合过程中溶剂以及溶剂中的少量杂质不会影响链增长过程。
而是影响反应速度相链增长的模式。
在工业上的应用:
由于阴离子聚合过程中可以产生活性增长链合成分子量甚为狭窄的聚合物。
因此它为高分子提供了持殊的合成。
结合成利用先后加入不同种类单体进行阴离子聚合的方法合成AB型,ABA型以及多嵌段、星形、梳形等不同形
式的嵌段共聚物。
热塑性橡胶的生产是工业上重要成就。
利用在聚合反应结束时需加入终止剂这一特点,合成某些具有适当功能团端基的聚合物。
图2.1阴离子聚合反应历程
2.1.2 S-SBR的发展简史及与E-SBR的比较
发展历史:
SBR的生产已有50年的历史。
起初,乳液聚合是生产商品SBR的唯一方法。
这种聚合过程是:
单体在皂类、促进剂及其它改性剂的水溶液中进行聚合。
该聚合进行得不完全,剩余单体必须被提纯再利用。
聚合物胶乳经凝固、烘干后形成SBR产品,乳聚丁苯橡胶(E-SBR)中橡胶烃的质量分数为0.93,其余是皂类和脂肪酸。
溶液聚合是一种相对较新的工业化聚合过程,它促进了费尔斯通公司的发展,此种生产SBR方法的特点是单体在有机溶剂中而不是在水乳液中进行聚合,在聚合中不使用乳化剂,因而橡胶烃的质量分数高达0.99,应用催化剂和改性剂可以生产出特
定结构的聚合物,苯乙烯质量分数、微观结构(顺式/反式/乙烯基)、相对分子质量、相对分子质量分布和支化度等都极易控制,能够制得多种不同的聚合物。
溶液聚合反应进行得相当完全,这就省去了多余的回收过程,同时使产品质地更加均一。
通常,溶液聚合的SBR产品与乳液聚合相比,乙烯基质量分布窄,支化度小。
无终点的溶液聚合过程可使聚合物端基进行进一步反应,引进偶联剂(如四氯化锡)可显著改善聚合物的流变性能。
这种室温下很稳定的聚合物在通常混炼条件下分子链易断裂,产生新的结合点,从而提高了聚合物与补强填充剂(如炭黑)之间的相互结合。
Duradene溶聚丁苯橡胶(S-SBR)是费尔斯通公司开发的,用以替代E-SBR。
通常,由于S-SBR滚动阻力小,耐磨性好,在大部分轮胎应用中,S-SBR比E-SBR更具优势。
然而,要获得最佳综合性能的材料,有必要首先了解这两种橡胶在配合及加工方面的
差异。
配合方面:
S-SBR混炼胶的粘度比E-SBR高,因此设计配方时考虑的方面之一是充分利用溶液聚合的聚合物具有橡胶烃质量分数较大的特点。
增大炭黑和油的质量分数可获得与E-SBR相同的炭黑/橡胶烃并用比。
这样可在获得同等性能的条件下降低混炼胶成本。
按橡胶烃/炭黑(橡胶烃/油)相同比例原则将E-SBR混炼胶配方折算到S-SBR混炼胶配方,举例如下:
第1步:
E-SBR配方
E-SBR(E-SBR1502)100
炭黑65
油 20
第2步:
炭黑/聚合物与油/聚合物比例炭黑/聚合物(100×0.93)/65=1.43油/聚合物(100×0.93)/20=4.65
第3步:
按上述比例折算
炭黑(100×099)/143=692
油(100×099)/465=213
S-SBR(Duradene706)
100
炭黑
692
油
213
第4步:
相应调整其它配合剂用量因为E-SBR和S-SBR中苯乙烯和乙烯基质量分数也不尽相同,所以聚合物的比例可作一下调整。
在E-SBR与BR共混体系中,若用S-SBR代替E-SBR,这种调整是比较容易的,当然,配方设计者可以灵活地调整配方以达到胶料所需的最佳性能。
利用聚合物的结构差异,可大量用S-SBR代替E-SBR。
S-SBR的硫化速度比E-SBR快10%~20%,但二者具有相同的焦烧安全期,减小硫化剂用量或缩短硫化时间可降低硫化胶的成本。
加工方面:
E-SBR和S-SBR的加工特性有明显差异。
通常,可用与制备E-SBR混炼胶相同的方法制备S-SBR混炼胶,不同之处在于S-SBR在高功率混炼机中不断链,因此不必对其进行初期塑炼,混炼时可同时将所有组分加入炼胶机。
S-SBR的生胶强度一般低于E-SBR,因此需减小辊距10%~20%以避免混炼胶脱辊。
S-SBR不含固有的有机酸,故与金属的粘合性较高。
加入高达5份的有机酸(如硬脂酸)可在不影响性能的条件下减少粘辊倾向。
S-SBR易包冷辊,为此应使前辊和后辊间有5~10℃的温差。
锡偶联S-SBR的配合和共混与传统的S-SBR略有差别,由于硬脂酸影响炭黑的混入,故应将其推迟到炭黑母炼胶或最后混炼时加入。
芳烃油亦会影响炭黑分散,应尽量少加。
为获得最佳性能,有必要使用环烷油。
由于Sn-C键的断裂,聚合物重回到最初未偶联时的粘度值,因而混炼胶的粘度较一般S-SBR低,因此,为易于加工并获得较佳的综合性能,配入的油的用量较少。
聚合物间的结构及性能对比:
通过实验室制备混炼胶,对几种E-SBR和DuradeneS-SBR进行比较。
对未充油、充油和高玻璃化转变温度(Tg)的聚合物进行研究,采用ASTMD-3185配方作为实验配方。
利用图中矩形的落差表示聚合物间的固有差异,65℃的tanδ值表征滚动阻力,0℃的tanδ值表征抗湿滑性。
在未充油的聚合物中,E-SBR1502与4种S-SBR———Duradene706,711,715和740进行对比。
Duradene706与E-SBR1502结构相近,适宜进行对比,可见,Duradene706的滚动阻力较小,耐磨性较高,硫化速度较快Duradene711的苯乙烯质量分数较小,胶料的滚动阻力进一步降低,耐磨性更高,但抗湿滑性有所下降。
Duradene715的乙烯基质量分数较高,可使高性能轮胎具有优异的湿牵引力。
Duradene740是锡偶联聚合物,与Duradene711的苯乙烯质量分数大致相同,但乙烯基的质量分数相对较大,与Duradene711相比,滚动阻力相当,混炼胶粘度较低。
但
由于Tg不变,因而也保持较高的湿牵引力。
Duradene753和756的苯乙烯质量分数均较低,从而降低了胶料的抗湿滑性,但耐磨性提高。
在胎面胶中使用S-SBR可通过调节苯乙烯和乙烯基的质量分数来调节聚合物的Tg,使滚动阻力和抗湿滑性达到较佳的平衡。
自从溶液聚合物问世后,人们在了解和应用这种有益于轮胎工业的先进技术方面已做了许多工作。
一旦了解了这种橡胶在配合及加工方面的差异,即可发现S-SBR的性能优势是相当明显的。
均匀的质量、高橡胶烃质量分数、低滚动阻力及较高的耐磨性更利于Duradene系列S-SBR在轮胎中的应用。
2.1.3溶聚丁苯的结构、性能及应用:
溶聚丁苯橡胶结构与乳聚丁苯橡胶类似,均是无规结构,但由于两者聚合工艺不同,各自有其不同的结构特征,见表2.1
图2.2温度对结合苯乙烯量的影响 图2.3温度对1,2-结构含量的影响
溶聚丁苯橡胶中丁二烯链节的顺1,4含量明显高于乳聚丁苯橡胶,而乳聚丁苯橡胶则反1,4含量较高。
同时,溶聚丁苯橡胶的分子量分布窄,分散指数一般小于2,而乳聚丁苯橡胶则可达到4以上。
在结合苯乙烯量相同的情况下,溶聚丁苯的玻璃化温度Tg随1,2—结构含量的增加在一定范围内增加,使Tg有所提高。
由于溶聚丁苯橡胶的结构特点,使它具有优异的性能。
如橡胶低分子量级分少,做成轮胎后滚动阻力小,耐磨性提高。
同时,聚合物链的高线型结构,使它在填充大量的工业炭黑和油以后其物理机械性能仍不发生明显变化,且胶料硫化时收缩率很小。
Tg虽然稍有提高,但是做成的轮胎在冬季并不出现构纹龟裂。
这种特征是
聚丁二烯橡胶中1,2结构含量高,链段结合苯乙烯量有所增加,聚合物分子量呈双蜂所致。
若以含有丁二烯基阴离子的聚合物链端与四氯化锡偶联后形成具有一定支化度的橡胶,则在轮胎性能时表现出其滚动阻力比乳聚丁苯橡胶降低30%,抗湿滑性提高3%,耐磨性提高约10%。
表2.1溶液丁苯橡胶和乳聚丁苯橡胶结构特征
此外,溶聚丁苯橡胶为非污染性白色橡胶,其非橡胶成分含量很低:
一般为1
%,而普通丁苯为8%一7%;溶聚丁苯共聚物的灰分含量为0.05%一0.1%;而乳聚丁苯为0.4%一0.6%,这些性质使它在硫化时达到最佳性能所需要的硫磺和促进剂的量比乳聚丁苯低,而且硫化速度快。
溶聚丁苯可作为通用型橡胶用于轮胎、胶鞋、胶管等各类制品,也可以与其他橡胶并用。
2.1.4溶液丁苯橡胶的聚合工艺:
2.1.4.1溶液丁苯橡胶的生产工艺
4-1-1典型生产配方及工艺
生产溶液聚合丁苯橡胶的典型生产配方及工艺条件如表3.1.1所示
表2.2溶聚丁苯的典型配方及工艺条件
原料及辅助材料
例1
例2
单体
丁二烯
76
75
苯乙烯
24
25
溶剂
正己烷
400
—
环己烷
—
500
引发剂
n-BuLi
0.6
0.064
无规剂
THF
—
1.6
偶联剂
SnCl4
—
0.039
反应条件
反应温度,℃
40—120
反应条件
压力,,N/cm2
29.4—98
反应时间,h
1—6
聚合物浓度,%(重量)
15—20
转化率,%
80—100
4-1-2流程简述
溶聚丁苯橡胶的生产工艺流程如图2.4所示。
精制后的丁二烯,苯乙烯进入聚合釜,加入配制好的引发剂、无规剂后在聚合
釜内进行聚合。
反应是放热的,同时在聚合过程中粘度急剧上升,因此传热和搅拌是聚合反应的关键。
调节催化剂用量和配比可以控制门尼粘度和转化率。
离开聚合釜的胶液进入闪蒸塔,除去未反应单体和部分溶剂,使胶液浓度提高到25%,再进入渗混罐掺混以获得希望的门尼粘度。
掺混好的胶液进入凝聚釜,在热水中同时进行凝聚和脱除溶剂。
回收溶剂经分层罐除去大量的水后,返回溶剂精制工序。
凝聚后的胶粒进入振动筛除去水分,并经机械干燥机除去余下的水分。
干燥后的胶粒经提升机提升到达压块机,经称重,压块后由自动线送去包装即得到成品。
图2.4溶聚丁苯橡胶生产工艺流程
4-1-3重要工序及设备
1.原材料准备
①单体和引发剂溶聚丁苯橡胶的生产是锂系引发剂存在下的阴离子聚合所以对材料要求很高,
对生产溶聚丁苯橡胶的主要原料丁二烯、苯乙烯、环己烷和和正庚烷的规格要求如下:
l,3—丁二烯
>99.5%
硫 <10ppm
苯乙烯
>99.6%
晴 <5ppm
环己烷
>98%
过氧化物 <10ppm
水
<50ppm
双烯烃(丙二酸l,2—丁二烯)
<110ppm
醇类
<15ppm
炔烃总量
<100ppm
引发剂正(仲)丁基锂用正(仲)丁烷与金属锂在氩气保护下,以环己烷为溶剂直接反应制得。
②无规试剂
添加无规试剂来制造溶聚丁苯橡胶是工业上通常采用的方法。
常用的无规试剂为给电子试剂和碱金属烷氧基化合物两大类。
给电子试剂如醚类、胺类、含磷化合物类、混合吡啶等。
碱金属烷氧基化合物如叔丁氧基钾、叔丁氧基钠等尤其是前者也是优良的无规试剂。
两类无规试剂的加入都可以改变单体丁二烯和苯乙烯的相对反应活性,得到无规聚合物。
同时聚合机理的改变也会影响聚丁二烯的微观结构,使l,2结构随无视试剂的种类和添加量而变化。
③偶联剂
溶聚丁苯分子量分布窄,元文化度的结构特点,虽然赋予它一些优良的性能,但也造成对其成型加工的不利。
通过加入带有多官能团的偶联剂到活性聚合物体系中,让它与活性锂封端的聚合物相联结,使可使部分子链的分子量倍增,从而加宽分子量分布或提高分子链的文化度,使其加工性能和冷流性得到改善。
工业上常用的偶联剂是一些带有多官能团的化合物如二乙烯基苯、二乙烯基荼、四氯化硅、己二酸二乙酯等。
其中以SnCl4最为普遍。
各种偶联剂对硫化胶性能的影响如表2.3所示。
表2.3偶联剂对偶联聚合物硫化胶性能的影响
④防老剂
为防止橡胶老化,在凝聚前常向聚合物溶剂中加人防老剂。
常用的防老剂有污染型和非污染型两类。
前一类如苯基—β—萘胺(防老剂丁),后一类如2,6—二叔丁基—4—甲基苯酚(防