柴油加氢精制说明书共24页.docx
《柴油加氢精制说明书共24页.docx》由会员分享,可在线阅读,更多相关《柴油加氢精制说明书共24页.docx(30页珍藏版)》请在冰豆网上搜索。
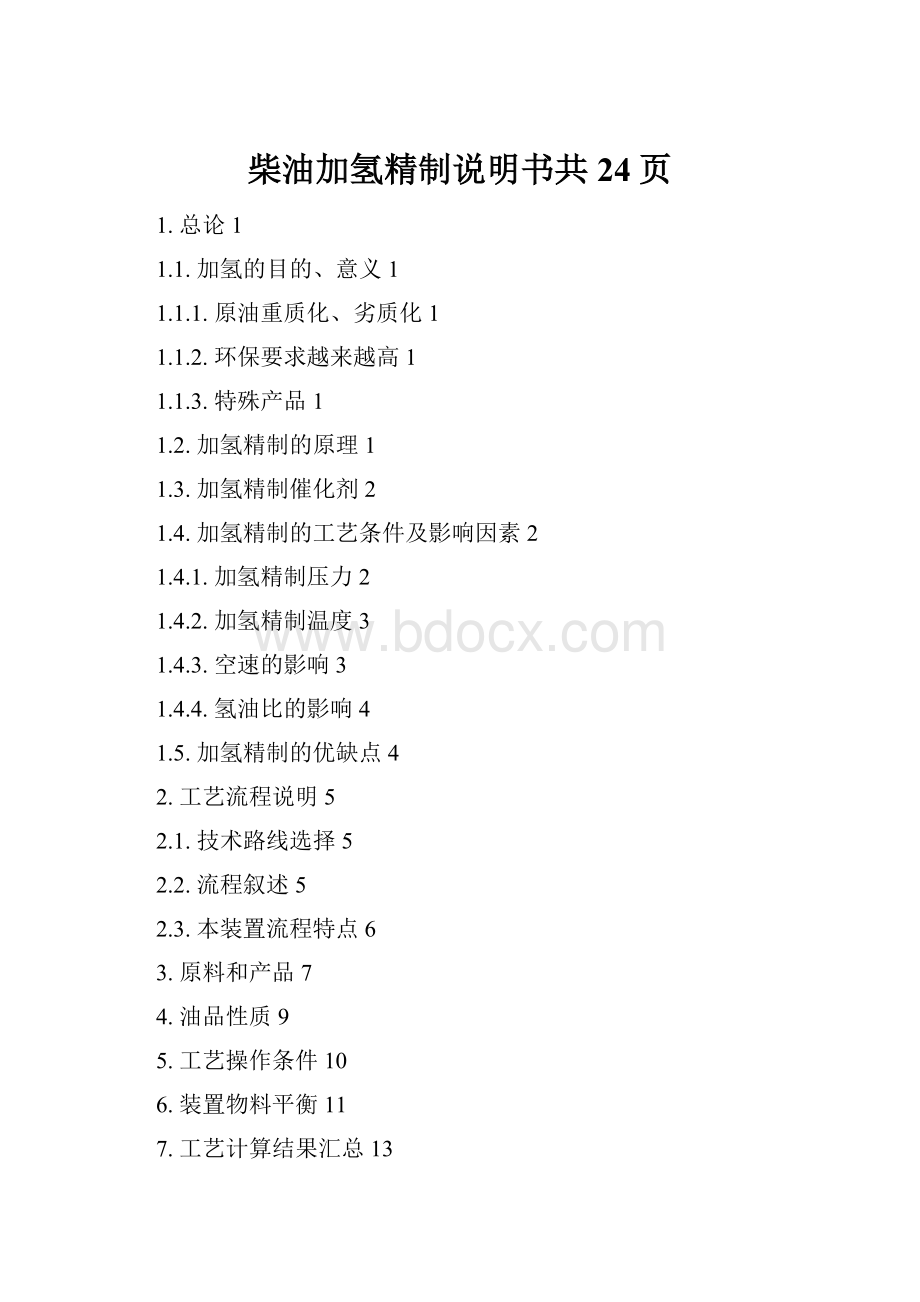
柴油加氢精制说明书共24页
1.总论1
1.1.加氢的目的、意义1
1.1.1.原油重质化、劣质化1
1.1.2.环保要求越来越高1
1.1.3.特殊产品1
1.2.加氢精制的原理1
1.3.加氢精制催化剂2
1.4.加氢精制的工艺条件及影响因素2
1.4.1.加氢精制压力2
1.4.2.加氢精制温度3
1.4.3.空速的影响3
1.4.4.氢油比的影响4
1.5.加氢精制的优缺点4
2.工艺流程说明5
2.1.技术路线选择5
2.2.流程叙述5
2.3.本装置流程特点6
3.原料和产品7
4.油品性质9
5.工艺操作条件10
6.装置物料平衡11
7.工艺计算结果汇总13
8.自控方案说明16
9.平面布置说明17
10.生产控制分析项目18
11.人员定编19
12.装置对外协作关系20
13.环境保护及消防安全21
13.1.排除“三废”数量和处理21
13.1.1.废气21
13.1.2.废水21
13.1.3.废渣21
13.2.噪音处理21
13.3.安全生产和劳动保护21
1.总论
1.1.加氢精制的目的、意义
1.1.1.原油重质化、劣质化
20世纪90年代中期,全球炼油厂加工原油的平均相对密度为0.8514,平均硫含量(质量分数,下同)为0.9%。
进人21世纪后,原油平均相对密度升至0.8633,含硫量升至1.6%。
原油密度升高,硫含量增大是21世纪原油质量变化的总体趋势。
很多由这些重质、劣质原油生产出来的油品都需要加氢精制以提高质量【1】。
1.1.2.环保要求越来越高
虽然原油质量不断劣质化,但世界各国对车用燃料油的质量要求仍然在不断提高。
以柴油硫含量为例,美国已经开始要求l0ppm的超低硫柴油,欧洲也开始执行硫含量<50ppm的标准。
国内而言,在北京,2019年已参照欧Ⅲ排放标准执行,硫含量控制在350ppm以内,2019年参照欧Ⅳ排放标准执行,硫含量控制在50ppm以内。
可以预期,国内燃油质量指标必将进一步升级与国际标准接轨【2】。
1.1.3.特殊产品
某些特殊产品,如食品级的石蜡,对其中的重金属杂质含量、硫含量以及不饱和程度的要求非常苛刻,而加氢精制可以使其达到质量要求。
1.2.加氢精制的原理
加氢精制(也称加氢处理),是指在氢压和催化剂存在下,使油品中的硫、氧、氮等有害杂质转变为相应的硫化氢、水、氨而除去,并使烯烃和二烯烃加氢饱和、芳烃部分加氢饱和,以改善油品的质量。
有时,加氢精制指轻质油品的精制改质,而加氢处理指重质油品的精制脱硫。
加氢精制可用于各种来源的汽油、煤油、柴油的精制,催化重整原料的精制,润滑油、石油蜡的精制,喷气燃料中芳烃的部分加氢饱和,燃料油的加氢脱硫,渣油脱重金属及脱沥青预处理等。
氢分压一般分1~10MPa,温度300~450℃。
催化剂中的活性金属组分常为钼、钨、钴、镍中的两种(称为二元金属组分),催化剂载体主要为氧化铝,或加入少量的氧化硅、分子筛和氧化硼,有时还加入磷作为助催化剂。
在加氢精制过程中,各类物质加氢反应活性总体趋势为:
脱金属>二烯烃饱和>脱氧>单烯烃饱和>脱硫>脱氮>芳烃饱和。
加氢精制中还存在加氢裂解副反应,可以从催化剂等途径控制副反应的发生。
1.3.加氢精制催化剂
加氢技术主要包括催化剂及其工艺技术的开发。
而开发出高活性加氢催化剂是提高加氢精制技术的核心。
传统加氢精制催化剂一般以Ⅵ族金属为活性组分,人们对加氢催化剂进行了多种研究与试验,认为加氢催化剂的活性组分基本上有3大类:
Co-Mo,Ni-Mo与Ni-W三个系列。
对这三个系列的研究结果表明:
加氢脱硫的活性顺序是Co-Mo>Ni-Mo>Ni-W;加氢脱N的活性顺序是Ni-W>Ni-Mo>Co-Mo;芳烃、烯烃加氢饱和的活性顺序是Ni-W>Ni-Mo>Co-Mo。
在新型加氢催化剂的开发研究方面,人们除了继续优化硫化物催化体系外,还对过渡金属碳化物和氮化物进行了大量研究。
虽然过渡金属氮化物和碳化物催化剂的HDS初始活性高于硫化物催化剂,但其稳定性较差。
20世纪90年代后期,许多研究者发现,WP作为一种新型的加氢精制催化剂,具有良好的加氢脱氮(HDN)和加氢脱硫(HDS)性能。
这是因为过渡金属磷化物不仅具有优良的HDS和HDN活性,而且其稳定性很高【3】。
载体在加氢精制催化剂中起担载活性组分和获得高分散率活性组分的作用,优良的载体可提高贵金属催化剂的效率和降低催化剂的成本。
因此载体性质是影响加氢精制催化剂性能的重要因素之一。
工业用γ-Al2O3因具有高比表面积和高熔点等特点,广泛应用于加氢精制过程。
目前,国内外研究者已经开始致力于三元及至多元载体的考察,今后的工作重点是进一步研究多组分氧化物载体的复合技术,探讨多组分氧化物载体负载后的构效关系,并找出复合型催化剂载体组成、微相结构的一般规律,为其应用提供理论依据。
同时寻找更多的单组分氧化物用于多组分复合,使其取代氧化铝载体在工业上使用成为可能。
我国开发研制的加氢催化剂很多,代表性的有FH-5,RN-1与RN-10等催化剂。
据研究表明,FH-5催化剂的脱硫能力优于脱氮能力,当原料含氮量明显增加时,脱氮能力明显下降,而脱硫能力变化不大,较适合于加工高硫的原料,如进口中东原油的各种馏分油及重油催化裂化柴油的加氢精制。
RN-1与FH-5相比,在脱氮活性和芳烃加氢饱和上有一定的优势,而RN-10具有较强的脱硫脱氮能力,尤其脱氮能力明显优于FH-5及RN-1,原料中含氮明显增大时,其活性保持不变或下降不明显,适合加工高硫高氮原料,如国产原油(属高氮原油)的各种馏分油及重油催化裂化柴油的加氢精制。
本次柴油精制装置采用RN-1催化剂,属于W-Ni型催化剂【4】。
1.4.加氢精制的工艺条件及影响因素
1.4.1加氢精制压力
反应压力的影响是通过氢分压来体现的。
加氢装置系统中的氢分压决定于操作压力、氢油比、循环氢纯度以及原料的汽化率。
柴油馏分(180~360℃)加氢精制的反应压力一般在4.0~8.0MPa(氢分压3.0~7.0MPa)。
柴油馏分在加氢精制条件下可能是汽相,也可能是汽液混相。
在处于汽相时,提高压力使反应时间延长,从而提高了反应深度,特别是脱氮率显著提高,这是因为脱氮反应速度较低,而加氢脱硫在较低的压力时已有足够的反应时间。
如果其它条件不变,将反应压力提高到某个值时,反应系统会出现液相,有液相存在时,氢通过液膜向催化剂表面扩散的速度往往是影响反应速度的控制因素,提高反应压力会使催化剂表面上的液层加厚,从而降低了反应速度。
如果压力不变,通过提高氢油比来提高氢分压,则精制深度会出现一个最大值。
出现这种现象的原因是:
在原料完全汽化以前,提高氢分压有利于原料汽化,而使催化剂表面上的液膜减小,也有利于氢向催化剂表面的扩散,因此在原料油完全汽化以前,提高氢分压(总压不变)有利于提高反应速度。
在完全汽化后提高氢分压会使原料分压降低,从而降低了反应速度。
因此,为了使柴油加氢精制达到最佳效果,应选择有利于刚刚完全汽化时的氢分压。
1.4.2加氢精制温度
对于不同的原料、不同的催化剂,反应的活化能不同,因此提高反应温度对反应速度提高的幅度也不同。
活化能越高,提温使反应速度提高得也越快。
但是,由于加氢精制反应是放热反应,从化学平衡上讲,提高反应温度会减少正反应的平衡转化率,对正反应不利。
在加氢精制通常的使用温度下,脱硫反应不受热力学控制,因此,对于馏分油的加氢脱硫,提温提高了总的脱硫速度;对于脱氮和芳烃饱和反应,在一定反应条件下,究竟是受热力学控制还是受动力学控制需要做具体分析。
工业上,加氢装置的反应温度与装置的能耗以及氢气的耗量有直接关系,最佳的反应温度应是使产品性质达到要求的最低的温度。
因此,在实际应用中,应根据原料性质和产品要求来选择适宜的反应温度。
1.4.3空速的影响
空速是指单位时间里通过单位催化剂的原料的量,它反应了装置的处理能力。
空速大意味着单位时间里通过催化剂的原料多,原料在催化剂上的停留时间短,反应深度浅;相反,空速小意味着反应时间长,因此无论从反应速度还是化学平衡上讲,降低空速对于提高反应的转化率是有利的。
但是较低的空速意味着在相同处理量的情况下需要的催化剂数量较多,反应器体积较大,装置建设投资(包括反应器和催化剂的费用)大,这在工业上是不希望的。
因此,工业上加氢过程空速的选择要根据装置的投资、催化剂的活性、原料性质、产品要求等各方面综合考虑。
1.4.4氢油比的影响
加氢过程是放热反应,大量的循环氢可以提高反应系统的热容量,从而减少反应温度变化的幅度;高氢分压可以使油分压降低,降低了油汽化温度,从而降低了反应温度。
因此,加氢过程中需要将大量氢气循环使用,其所用的氢油比往往大大超过化学反应所需的数值。
提高氢油比意味着氢分压的提高,这需要增大循环压缩机的流量,动力消耗增大,从而操作费用增大。
因此适宜氢油比的选择也是一个经济上的优化问题。
1.5.加氢精制的优缺点
加氢精制能有效地使原料油中的硫、氮、氧等非烃化合物氢解,使烯烃、芳烃选择加氢饱和并能脱除金属和沥青质等杂质,具有处理原料范围广,液体收率高,产品质量好等优点【5】。
通过加氢精制改善油品质量在炼油厂中得到了很好的应用,但加氢精制装置设备昂贵,操作费用大而且氢耗很高,中小炼油厂难以承担。
因此,一些非加氢精制技术如溶剂精制、吸附精制等也得到了广泛的应用。
2.工艺流程说明
2.1.技术路线选择
根据原料性质,选择柴油加氢精制的主要工艺条件有:
反应器压力4.0MPa,反应器入口温度320摄氏度(末期),体积空速2.5,氢油比300。
脱硫率在90%左右,产品收率达99.5%以上。
反应过程中有少量焦炭沉积,降低了催化剂活性,可以通过控制燃烧法再生,使催化剂寿命可达5~6年。
考虑到本装置的原料是催化裂化柴油,所以压力为4.0MPa,若原料为焦化柴油,则压力应提高到6.0~8.0MPa。
2.2.流程叙述
原料油经换热器和加热炉加热至338.5℃,然后与混合氢混合进入固定床反应器,在氢压下发生加氢脱硫、脱氮、脱氧、烯烃饱和、多环芳烃环烷化、脱金属、烃裂解等各种反应,总反应为放热反应。
根据原料情况和加氢深度,催化剂采用单层装填,反应器中间不注冷氢。
反应生成物经一系列换热冷却后,进高压分离器闪蒸分出循环氢循环使用;高分液体则经低压分离罐进一步分离轻烃并溶解除去H2S后送往汽提塔汽提。
催化裂化柴油(T=40℃,P=0.3MPa,G=125000Kg/hr)自罐区来,先进入原料油缓冲罐V101,经原料油泵P101后,压力P升至4.4MPa。
然后进入换热器E103进行预热,与经换热器E102换热降温后的反应物进行换热,温度T升至237.1℃,压力P降至4.3Mpa,然后进入加热炉F101进行加热。
在加热炉里,原料油先经对流室,温度T升至261.8℃,然后进入辐射室,进一步升温至338.5℃,压力P降至4.1MPa。
原料油出加热炉后与300℃的混合氢混合并进入反应器R101。
新氢(重整氢)(T=40℃,P=1.5MPa,G=3375Kg/hr)至罐区来,先进入缓冲罐V102,然后经新氢一级压缩和一个水冷器E105和二级压缩之后,T=97.62℃,P=4.5MPa,再与T=58.15℃,P=4.5MPa,G=8596.74Kg/hr的循环氢混合形成混合氢(T=70.6℃,P=4.5MPa,G=11971.74Kg/hr)。
混合氢经换热器E101和反应产物换热后,T=300℃,P=4.1MPa,然后与T=338.5℃的原料油混合作为反应物,其G=136971.74Kg/hr,一同进入反应器R101进行反应。
反应器的入口T=320℃,P=4.0MPa,出口处T=358℃,P=3.9MPa。
反应器R101的产物经E101与混合氢换热后,T=330℃,P=3.8MPa,然后进入E102与经E202换热后的反应产物(低分罐出料)换热,换热后T=270℃,P=3.7MPa,之后经E103与原料油换热,T=120℃,P=3.6MPa。
在此处注入工业软水,G=3750Kg/hr,T=40℃。
软水和反应产物一起进入水冷器E104冷凝后T=40℃,P=3.5MPa。
接着,物料进入高压分离罐V105,排除含硫、含氮污水和含氢气体,污水从V105的底部排除,含氢气体从顶部离开,其中G=2225Kg/hr的气体作为高分排放,用以平衡系统总压,另一部分G=8596.74Kg/hr作为循环氢使用。
循环氢自高分罐出来后先进入循环氢脱油罐V106脱除油分,出V106后,T=40℃,P=3.5MPa,经循环氢压缩机C102后,其T=58.15℃,P=4.5MPa,再与新氢(T=97.62℃,P=4.5MPa)混合。
经高分罐分离后的反应产物T=40℃,P=3.5MPa,G=126150Kg/hr,进入低压分离罐V107,再排放掉残余的含硫气体,其G=387.5Kg/hr。
分离后的反应产物T=40℃,P=0.7MPa,G=125692.5Kg/hr,这些物料经换热器E202与汽提塔塔釜产物——精制柴油进行换热,换热后T=115℃,P=0.7MPa,G=125692.5Kg/hr,再进入E102与经E101的换热后的反应产物进行换热,使其T=200℃,P=0.36MPa,然后物料进入汽提塔,其气化率为5%。
物料从第14块塔板处进入汽提塔,过热蒸汽从第一块塔板下方进入塔内,其T=300℃,P=0.4MPa,G=3750Kg/hr。
在汽提塔内,蒸汽向上带走物料中的粗汽油、溶解气等成分,将柴油提纯。
塔顶出料T=147℃,P=0.35MPa,经水冷器E201冷凝后,T=40℃。
之后物料进入回流罐,在回流罐中,溶解气自上方排出,其G=2605Kg/hr,水和粗汽油从下方排出,水的排出量G=3750Kg/hr,粗汽油的一部分抽出作为回流,G=8799.8Kg/hr,另一部分作为塔顶产品,G=1900Kg/hr。
缓蚀剂自缓蚀剂罐来,经泵P104打入汽提塔顶,以防止H2S腐蚀管线。
塔釜出料T=194℃,P=0.37MPa,进入E202与低分罐出料进行换热,换热后,T=120℃,P=0.27MPa,然后进入冷却器E203冷却至T=50℃,进入柴油脱水罐V110,脱除产品中少量水分后,得到目标产品精制柴油,其质量流量G=121187.5Kg/hr。
2.3.本装置流程特点
1)本装置采用催化裂化柴油为原料,氢气来源为重整氢。
2)原料油和氢气的混合采用炉后混氢形式,降低了对加热炉材质的要求。
3)装置采用冷高分流程,高分后的液体进入冷低分罐进行进一步分离。
4)原料油缓冲罐用重整氢或氮气进行保护,防止生胶。
5)装置采用RN-1型催化剂,这种催化剂在脱氮活性和芳烃加氢饱和上有一定的优势,适用于催化裂化柴油,并且工艺条件缓和。
6)不设循环氢脱硫,利用高压分离器排放掉一部分H2S保证循环氢纯度。
7)在换热器E104前注软化水,以防止管道堵塞。
8)汽提塔采用水蒸气汽提,汽提塔顶加缓蚀剂以防H2S腐蚀。
3.原料和产品
本装置处理的原料油为重油催化裂化柴油,含有烯烃和芳烃,其中硫、氮、氧等杂质的含量较高,产品质量差、安定性差、不易保存,易生成胶质和沉渣。
如果直接使用对机器的损害很大。
本装置采用单塔气提精制柴油,所以只能保证主要产品精制柴油的纯度,而另一产品粗汽油的纯度不能得到保证。
表3.1原料油,中间产物,产品的性质数据
项目
原料油
生成油
精制柴油
粗汽油
密度d420
0.8642
0.8578
0.8595
0.7350
凝点℃
-5
-6
闪点℃
72
85
含硫ppm
1800
180
含氮ppm
261
58
硫醇硫ppm
15
1
碱性氮ppm
179
12
溴价gBr2/100g
20.5
4.1
十六烷值
41.5
43.1
酸度mgKOH/100ml
5.8
0.14
实际胶质mg/100ml
65.6
20
铜片实验(100,3hr)
合格
色度(ASTMD1500)
3.5
1.0
平均分子量
197.34
194.43
196.01
99.37
IBP
182
108
202
53
恩氏蒸馏
10%
219
216
218
74
30%
245
243
243
87
50%
267
268
268
105
70%
291
290
290
136
90%
321
320
320
162
EBP
339
338
338
180
表3.2柴油加氢精制中气体的组成(mol%)
新氢
循环氢
反应前
反应后
低分罐
低分罐
回流罐
回流罐
组分
重整氢
高分排放
混合氢
生成气
溶解气
排放气
排放气
溶解气
氢
87.68
80.86
83.08
77.60
2.00
43.10
2.03
0.42
甲烷
4.81
10.45
8.66
10.39
5.45
20.71
5.58
3.43
乙烷
3.41
5.07
4.54
5.83
22.85
18.85
22.73
21.58
丙烷
2.31
2.04
2.13
2.98
26.98
9.3
27.06
28.21
丁烷
1.61
0.83
1.08
1.81
28.40
4.83
28.46
30.77
戊烷
0.00
0.15
0.10
0.47
9.2
0.96
9.29
10.09
硫化氢
0.00
0.60
0.41
0.81
5.39
2.55
4.85
5.50
氨
0.00
0.00
0.00
0.11
0.00
0.00
0.00
0.00
平均分子量
5.50
6.50
6.18
7.95
44.49
18.11
44.46
46.42
4.油品性质
表4.1油品性质计算结果
项目
原料油
加氢生成油
精制柴油
粗汽油
0.8642
0.8578
0.8595
0.7350
0.8684
0.8620
0.8637
0.7399
比重指数(API)
31.45
32.65
32.33
59.74
特性因数K
11.37
11.43
11.42
11.89
十六烷值
41.32
42.94
平均分子量
197.34
194.93
196.01
99.37
平均沸点
℃
268.6
266.8
267.8
112.8
270.6
268.9
269.8
115.5
257.8
255.7
257.0
101.8
266.4
264.5
265.5
110.1
262.1
260.1
261.3
105.9
临界温度℃
455.1
451.9
453.1
289.5
临界压力atm
19.72
19.51
19.52
29.07
焦点温度℃
487.8
485
487
358
焦点压力atm
26.5
27.0
26.7
53.8
在
1atm
平
衡
闪
蒸
℃
0%
231.8
175.8
240.3
83.9
5%
238
200
10%
244.8
241.5
245.1
90.4
20%
253
251
30%
262.5
259.9
262.0
99.1
50%
275.4
272.1
276.9
109.4
70%
292.0
290.1
292.0
131.6
90%
304.3
302.5
304.3
142.0
100%
309.1
307.2
309.1
146.8
5.工艺操作条件
本装置年处理量为100万吨,反应阶段为末期,反应器温度为320℃,回流比为4.63,每年开工时数为8000小时,其它的主要操作条件见下表:
表5.1柴油加氢精制主要操作条件
项目
数值
反应部分
催化剂
RN-1(NiO-WO3/Al2O3)
反应器温度
320(末)
反应器压力MPa
4.0
氢油比V/V
300
体积空速hr-1
2.5
高分罐压力MPa
3.5
低分罐压力MPa
0.7
注水量W%
3.0
汽提部分
汽提塔顶压力MPa
0.35
回流罐压力MPa
0.30
塔顶回流比R
4.63
汽提蒸汽量W%
3.0
6.装置物料平衡
该部分的计算包括装置总物料平衡计算、各类加氢反应的耗氢量及反应放热量的计算、加氢精制装置纯氢消耗量的计算和加氢装置内硫化氢的平衡计算,共5项内容。
计算结果分别列表如下:
表6.1装置总物料平衡表
(年开工时数以8000小时/年)
物料项目
物料量
重量
%
公斤/小时
吨/天
入
方
原料油
125000
3000
100
重整氢
3375
81
2.70
总计
128375
3081
102.70
出
方
精制柴油
121187.5
2908.5
96.95
粗汽油
1900
45.6
1.52
高分排放气
2225
53.4
1.78
低分排放气
387.5
9.3
0.31
回流罐排放气
2605
62.52
2.084
溶于水中的硫化氢
27.5
0.66
0.022
溶于水中的氨气
30
0.72
0.024
设备漏损
12.5
0.3
0.01
总计
128375
3081
102.70
注:
粗汽油包括0.03的溶解气在内
表6.2各类加氢反应的耗氢量汇总表
项目
化学耗氢量
重量分数
Nm3/T原料油
Kg/hr
%
1加氢脱硫
2.34
26.152
5.43
2加氢脱氮
1.26
14.078
2.93
3加氢脱氧
0.0966
1.078
0.22
4烯烃饱和
22.96
256.25
53.18
5芳烃饱和
6.29
70.254
14.58
6加氢裂解
10.22
114.017
23.66
总计
43.17
481.829
100
表6.3反应放热计算汇总表
项目
反应放热量
重量分数
Kcal/T原料油
Kcal/hr
%
1加氢脱硫
1405.92
175740
3.59
2加氢脱氮
756.84
94605
1.93
3加氢脱氧
57.95
7243.5
0.15
4烯烃饱和
28929.6
3616200
73.90
5芳烃饱和
3399.19
424899
8.68
6加氢裂解
4597.16
574644.38
11.75
总计
39146.66
4