用计数抽样检验的基本原理之概率计算.docx
《用计数抽样检验的基本原理之概率计算.docx》由会员分享,可在线阅读,更多相关《用计数抽样检验的基本原理之概率计算.docx(15页珍藏版)》请在冰豆网上搜索。
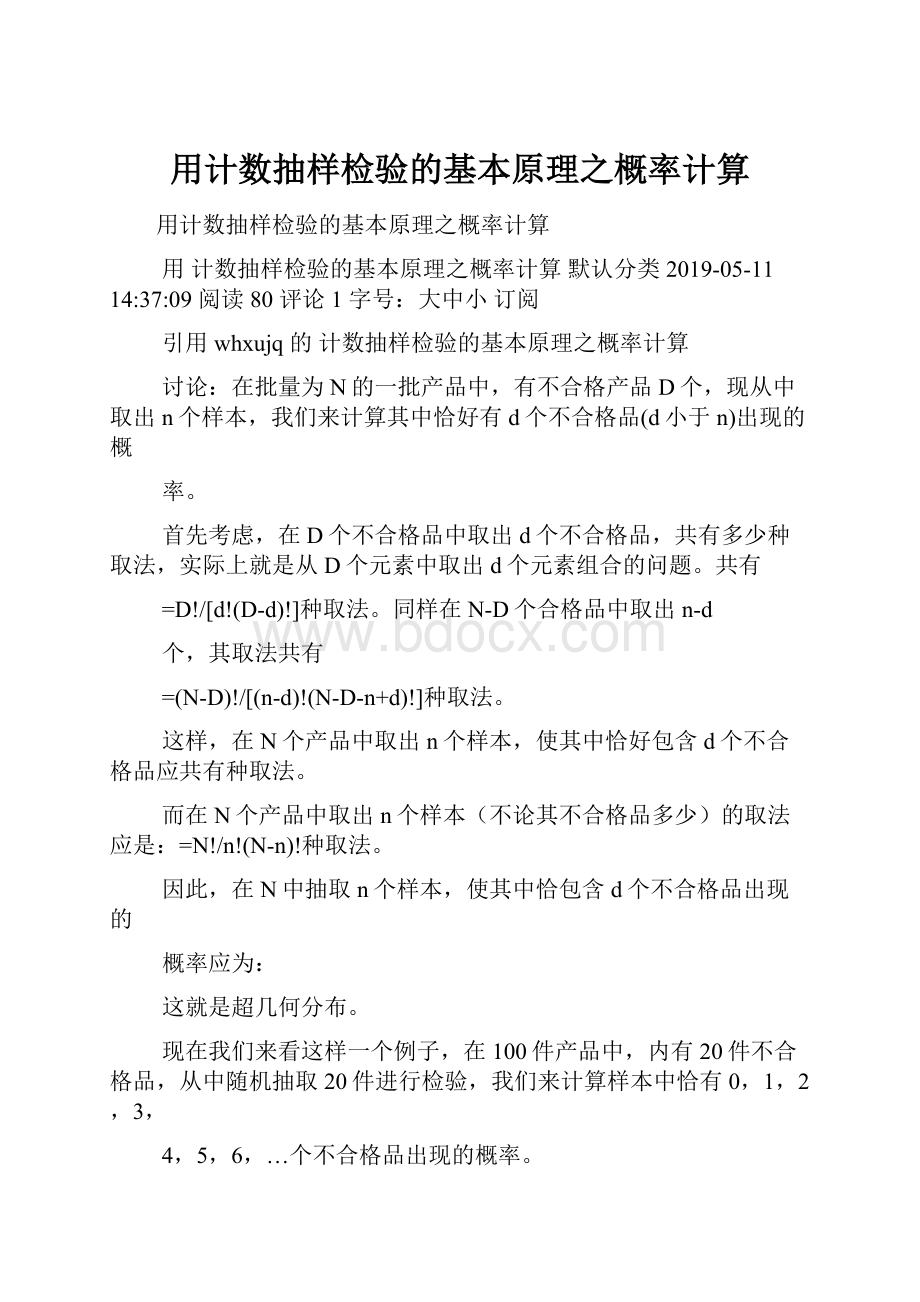
用计数抽样检验的基本原理之概率计算
用计数抽样检验的基本原理之概率计算
用计数抽样检验的基本原理之概率计算默认分类2019-05-1114:
37:
09阅读80评论1字号:
大中小订阅
引用whxujq的计数抽样检验的基本原理之概率计算
讨论:
在批量为N的一批产品中,有不合格产品D个,现从中取出n个样本,我们来计算其中恰好有d个不合格品(d小于n)出现的概
率。
首先考虑,在D个不合格品中取出d个不合格品,共有多少种取法,实际上就是从D个元素中取出d个元素组合的问题。
共有
=D!
/[d!
(D-d)!
]种取法。
同样在N-D个合格品中取出n-d
个,其取法共有
=(N-D)!
/[(n-d)!
(N-D-n+d)!
]种取法。
这样,在N个产品中取出n个样本,使其中恰好包含d个不合格品应共有种取法。
而在N个产品中取出n个样本(不论其不合格品多少)的取法应是:
=N!
/n!
(N-n)!
种取法。
因此,在N中抽取n个样本,使其中恰包含d个不合格品出现的
概率应为:
这就是超几何分布。
现在我们来看这样一个例子,在100件产品中,内有20件不合格品,从中随机抽取20件进行检验,我们来计算样本中恰有0,1,2,3,
4,5,6,…个不合格品出现的概率。
①、没有不合格品,d=0
=[(100-20)!
*(100-20)!
]/[100!
(100-40)!
]≈0.0066
②、只有一个不合格品,d=1
=[(20!
)2*(80!
)2]/[100!
*(19!
)2*61!
]≈0.0433
③、有二个不合格品,d=2
=[(20!
)2*(80!
)2]/[2*100!
*(18!
)2*62]!
≈0.192
这样算下去可得:
P(3)≈0.216,P(4)≈0.244,P(5)≈0.192,
P(6)≈0.109,…,P(20)≈
这是超几何分布的计算方法,也是理论的计算方法,在GB2828
中还有两种近似计算方法,即二项式分布计算方法和泊松分布计算方法,在设定一定的近似条件后,都可以推导出来,这里不再赘述。
通过这一组数据,我们可以看到,样品中不合格数等于20的可能性微乎其微,而d=4即等于样本的平均不合格数的可能性最大,如果此时我们规定一个合格判定数Ac,就可以计算出该批产品在抽样方案
(n|Ac)时的接收概率(即被判为合格批的概率)。
1、什么叫接受概率:
在抽样检验中,检查批被判定合格的可能性(大小)(概率值)为接受概率。
用Pa(或LCP)表示。
2、接受概率的计算:
当一个抽样方案给定后,即n与Ac值给定后,批质量一定的批产品就会有一个固定的被接受概率(判为合格),那么这个概率是怎样得
来的呢?
首先我们先回忆一下合格判定数的概念,Ac是作出批合格判断的样本所允许的最大不合格品数或不合格数,也就是说当样本中的不合格品数(或不合格数)d≤Ac时,判该批合格,若d>Ac时,就判批不合格。
接着我们前面的讨论,可以知道,在批量为N的一批产品中,如不合格品数为D,从中抽取n个样本,其中恰好有d个不合格品出现的概
率为:
这时,若d≤Ac,均判批产品合格,那么该批产品被判合格的总概率应该是样本中不合格品d小于等于Ac的各值(d=1,2,3,…,Ac)
出现的概率的总和,即:
Pa=P(0)+P
(1)+P
(2)+…+P(Ac)
用连加符号表示,即:
这就是接受概率的计算公式。
我们再接着看前面讲的例子。
如果规定Ac=0,那么:
Pa=P(0)=0/0066=0.66%
如果规定Ac=1,那么:
Pa=P(0)+P
(1)=0.0066+0.433=4.99%
依此类推,可得:
Ac=3,Pa=39.19%;Ac=4,Pa=63.59%;Ac=5,Pa=82.79%;Ac=6,Pa=93.69%;Ac=7,Pa=98.29%,Ac=8,Pa=99.74%;从以上一组数据,我们可以看出,当n不变时,批质量相同的产品批,当Ac较小时,其接收概率较小,随着Ac的增大,批接收概率也不断增大。
即批质量一定的产品在抽样检验时,被判合格的可能性与规定的Ac值有很大关系,在n不变时,Ac越大,批被判合格的可能性也越大,在本例中,当Ac=8时,即允许样本中有比平均值多出一倍的不
合格品时,抽样检验的接收概率已经接近100%。
抽样检验在紧固件公司产品验收中的应用
东风汽车紧固件有限公司质量部赵芳朱达宏
摘要:
紧固件产品生产批量大、结构较总成结构简单、价格便宜,如采用全数检验在人力和物力上必会带来更多的投入。
为了降低检测费用、但又保证产品质量的情况下,选用紧固件行业常选用的GB2828抽样标准,制定一套符合我公司实际情况的抽样检查验收方案。
关键词:
抽样检验可接受质量水平过程平均
在产品制造过程中,为了保证产品合乎质量标准,防止不合格品出厂或流入下道工序,通常对产品进行全数检验(即100%检验)。
但是,在许多情况下,对于破坏性检验、批量大检验时间长、生产效率高或检验费用高的产品,全数检验是不现实的或者是没有必要的,此时抽样检验是一种有效的方法。
抽样检验是从一批产品中随机抽取一部分进行检验,并据此判定产品是否合适的活动。
其特点是:
检验对象是一批产品;应用数理统计原理推断产品批合格与否;合格批中可能包含不合格品,不合格批中也可能包含合格品。
一般用于下述情况:
1)破坏性检验,如产品的可靠性试验、产品寿命试验、材料的疲劳试验、零件的强度检验等;2)批量大,全数检验工作量大的产品的检验,如螺钉、螺母等;3)测量对象是流程性材料,如钢水化验,钢板的检验等;4)其他适用全数检验不经济的场合。
抽样检验的分类,按检验特性值的属性可分为计数抽样检验和计量抽样检验;按抽取样本的个数可分为一次抽样检验、二次抽样检验、多次抽样检验和序贯抽样检验;按抽样方案可否调整来分,有调整型抽样检验和非调整型抽样检验。
在实际抽样检验过程中,往往将批质量判断规则转换为一个具体的抽样方案,在检验过程中根据样本中出现的不合格(品)数来判断检验批是否合格。
一个抽样方案通常有两个参数和一个接收准则:
一是抽取的样本量n,二是对样本进行检验时,判断批合格与否的合格判定数Ac。
抽样方案通常用(n,Ac)表示。
统计抽样检验理论承认采用抽样检验避免不了承担风险,但如何使生产方风险和使用方风险降到最小,此时需提出适当的质量要求和选择合理的抽样方案。
由于紧固件产品生产批量大、数量较多,部分有性能要求的产品需进行抗拉、金相组织等破坏性检验,如果采用全数检验不经济,也不可行。
鉴于上述情况在产品验收检验中,依据计数调整型抽样标准GB2828,制定了适合自身验收检查的抽样方案。
一、确定质量标准
依据产品图纸中规定的单位产品的技术性能、技术指标、外观等特性,将我公司产品分为螺栓(包括螺柱)、螺母、铆钉、销、管接头、螺钉等六大类产品,在检验指导书中明确各类别产品抽样检验的具体项目。
二、确定可接受质量水平AQL
可接受质量水平AQL是调整型抽样方案的基础,是影响、调节和控制生产方风险和使用方风险。
可接受质量水平AQL是认为可以接受的连续交检批的过程平均上限值,又称合格质量水平。
它是用来描述过程平均的一个重要指标,当生产者提供了等于或优于AQL值的产品质量时,则应当几乎全部接收交检的产品批。
也就是说,正在生产的产品批的平均质量至少像AQL值一样好时,可以认为这种产品批基本上是满意的。
在正常条件下,只要生产者的过程
平均一直保持优于AQL值的水平,这种抽样体系对于生产者是有利的;而当生产者提交的产品批的质量坏于AQL值时,基于AQL的接收准则,一般不能对使用方进行令人满意的质量保证;生产方很快就会发现拒收批的比例在增加,即退回的产品批多起来,最后甚至暂停检验,这样,生产者就要被迫改进产品质量。
那么AQL如何确定呢?
通常可采用以下几种方法:
1)依据过程平均来确定;2)同供应方协商决定(AQL值的确定应是生产方可能提供的质量和使用方认为理想的质量之间的折衷;这样可以减少由AQL引起的纠纷。
该方法多用于质量信息很少(如新产品等)的场合);3)AQL的分配法(涉及成品与其组成之部件AQL间的关系);4)按不合格类别(对于不合格类别不同的产品,分别规定不同的AQL值;越是重要的检验项目,验收后不合格造成的损失越大)。
我们这里采用依据过程平均来确定AQL值。
过程平均是一时期或一定量产品范围内过程水平的平均值。
一般用一系列连续提交批初次检验的不合格品率或每百单位产品不合格数的平均值来表示。
过程平均不能计算或选择的,但是可以根据过去抽样检验的数据来估计过程平均。
假设有k批产品,其批量分别为N1、N2、Nk,经检验,其不合格品数分别为D1、D2、Dk,则过程平均不合格品率为:
D1+D2
++Dk
P(k≥20)N1
+N2+
+Nk
由此可见过程平均的值必须等到过程把全部产品加工出来进行全检后才能得到,但是这是不现实的,通常是进行抽样检验用样本数来估计过程平均。
从上述批中依次抽取样本量为的n1+n2++nk个样本,样本中的不合格品数分别为d1+d2++dk个,利用样本估计的过程平均不合格品率为:
d1+d2
++dk
(k≥20)P'n1+n2+
+nk
如果规定的AQL值大于过程平均,几乎所有批都能抽检合格,生产不致中断;如果规定的AQL值小于过程平均,则不合格批增多,生产方常挑选产品或中断生产,处于不经济的生产状态。
鉴于过程平均与AQL之间的关系,为确定出AQL值,对我公司的管接件分厂、特殊工艺分厂、冷成型一分厂、冷成型二分厂的过程平均进行了如下估算:
1、管接件分厂:
月
份1月份
批1234567891011121314151617181920号
批[***********][***********][**************]7量00000000000000000005
样5050505050505050505050505050505050505050本
量
不00000100000000002000合
格
品
数
1月份过程平均:
3/1000=0.3%
按照上述方法估算出管接件2~6月份的月过程平均分别如下表:
月份2月份
月过程平均0.43月份0.34月份0.35月份0.26月份0.4
则:
1~6月份过程平均为:
0.3167%
依据上述方法估算出其余各分厂的月过程平均分别如下:
2、特殊工艺分厂:
月份1月份2月份3月份4月份5月份6月份月过程平均0.20.30.30.30.20.3则:
1~6月份过程平均为:
0.2667%
3、冷成型一分厂:
月份1月份2月份3月份4月份5月份6月份月过程平均0.30.20.20.40.40.3则:
1~6月份过程平均为:
0.3%
4、冷成型二分厂:
月份1月份2月份3月份4月份5月份6月份月过程平均0.30.20.20.30.30.4则:
1~6月份过程平均为:
0.2833%
则1~6月份整个过程平均为:
0.2767%
一般用于估算过程平均的批数,通常不少于20批,如果是新产品,开始时可用5到10批的样本估计。
在估算过程平均的时候,我们将1)不同类型的不合格品(或不合格)分别估计;2)利用二次或多次抽样方案的样本数据估计过程平均时,仅使用了第一样本的结果;3)估计过程平均时将再次提交批的数据剔除,只使用初检批的样本数据;4)检验不是截尾的,即抽样检验进行过程中,即使可以作出接收或拒收判定时,也并未终止检验。
根据以上分析可见:
AQL取0.25,略高于过程平均值。
三、决定检验水平
检查水平反映了批量和样本大小之间的关系;在GB2828中规定了两类检验水平:
一般检验水平(Ⅰ、Ⅱ、Ⅲ)和特殊检验水平(S-1、S-2、S-3、S-4)。
在选择检查水平时应考虑:
产品的复杂程度与价格(构造简单、价格低廉的产品应比构造复杂、价格昂贵的产品的检查水平低);检查费用(若检查费用低于产品价格,宜选高检查水平);破坏性检查(适于选低检查水平,甚至选特殊检查水平);生产的稳定性(稳定连续性生产宜选用低检查水平,不稳定或新产品生产宜选用高检查水平);各批间的质量差异程度(批间质量差异小而且检查总是合格的产品批,宜用低检查水平)。
由于紧固件产品较总成构造简单、价格低廉,并且部分有特性要求的产品需进行破坏性检查,因此选择特殊检验水平S-4。
四、选择抽样方案类型
GB2828中规定了一次、二次和五次抽检方案类型。
在同一个AQL值和同一个样本量字码时,采用任何一种抽样方案类型,其QC曲线基本一致。
因此,不能笼统的说,某种类型一定比另一种类型好,一般还应考虑以下因素:
1)产品的检查费用;2)抽样的费用。
当抽样费用比检验费用还高时,则采用一次抽样有利;3)从管理上考虑。
二次和多次抽查的样本大小随产品批的质量好坏而变化大,这就造成管理上的一些困难,如在进行破坏性检查时如何准备样品,准备多少样品难以估计;此外,二次和多次检查的判断对检查人员素质要
求较高,增加管理的复杂性。
此时,采用一次抽查更有利;4)检查所需的时间。
在试验条件相同的情况下,一次抽检方案比二次、五次抽检方案得出结论的时间短。
由于紧固件与其他类别的产品相比价格较低,因此在产品不是很昂贵和检验费用不是很高的情况下,选择一次抽检方案。
五、组成检验批
一个检验批就是需要检验的一组单位产品,通常简称为“批”。
批的形式有“稳定的”和“流动的”两种。
所谓稳定批是指批中所有单位产品是同时提交检验的;流动批中的各个单位产品是一个个从检验点通过,由检查员直接进行检验。
一般说来,只要条件允许最好采用稳定批的形式。
构成一个批的所有单位产品应当尽可能整齐,即:
检验批应是同型号、同等级、同种类的产品,且生产条件和生产时间基本相同的单位产品组成。
为保证抽样检验的可靠性,不能将不同来源、不同时期生产的产品混在同一批交检。
六、规定检验的严格度
GB2828规定了三种严格度不同的检验。
三种检验分别是正常检验、加严检验和放宽检验。
正常检验的设计原则是:
当质量优于AQL时,则以很高的概率接收交检批,以保护生产方的利益。
那么使用方的利益如何来保护呢?
加严检验就是当生产者提供的产品质量差于AQL时,保护使用方利益的一个重要措施。
在这三种不同的严格度中,放宽检验是非强制性的;但正常检查转为加严检验是带有强制性的。
三种检验之间的转移规则如下:
由于基于AQL的抽样方案考虑更多的是生产方风险,为了更好的保护使用方利益,降低使用方风险,我公司仅采用正常和检验两种检验严格度。
七、检索抽样方案
抽样方案的确定主要根据样本大小字码和合格质量水平,检索GB2828抽样标准而来。
我公司抽样方案如下:
批量(N)
≤500000
八、抽取样本AQL检验严格度0.25正常检验加严检验抽样方案nAc500800
按抽样方案的样本大小从批中随机抽取所要的样本。
在抽取样本时,对于紧固件而言,检查螺纹旋合性时,不应有意将磕碰伤较严重的产品剔除。
九、样本的测量与记录
按照检验指导书要求的检验项目、量检具对被测样本实施检验,并将检验结果客观的记录下来,统计出样本中的不合格品数。
十、判断批合格与否
对于一次抽样方案,根据样本检验的结果,当样本为零缺陷时则判断该批产品合格。
十一、检验后的处置
不论是抽样检验还是全数检验,发现的不合格品一律从批中剔除;对与提交检查判为不合格的批,退回生产方全数检查并剔除不合格品后,再次提交检查,其抽样方案按正常一次抽样方案。
为比较新方案的合理性,我们将2019年用户反映质量问题的频次与2002年同期相比较:
2002年同期反映频次为201次,2019年同期反映频次为162次,由此可见采用新的抽样方案后将使用方风险有所降低。
紧固件产品批量大、价格较便宜,若采用全数检验要投入更多的人力、物力,提高检测费用。
抽样检验可以减少检验工作量、提高劳动生产率,科学的统计抽样检验要比全数检验产生错检和漏检的现象少得多;并且全数检验是一种消极的检验方法,而抽样检验一旦一批产品判为不合格,成批产品要退还生产者或要求生产者逐个挑选,它能加强生产者的质量责任感,促进生产者力求达到更高的质量水平。
一.抽样检验方法标准的应用
(一)基本概念
1.抽样检验:
抽样检验指从批量为N的一批产品中随机抽取其中的一部分单位产品组成样本,然后对样本中的所有单位产品按产品质量特性逐个进行检验,根据样本的检验结果判断产品批合格与否的过程。
2.单位产品:
构成产品总体的基本单位。
3.样本大小:
样本中所包含的单位产品数量,一般用n表示。
4.单位产品的质量表示方法:
计数、计量
5.不合格和不合格品
不合格:
单位产品的质量特性偏离技术标准(规范)要求,即不符合规定的。
按单位产品质量特性的重要程度可分为A类不合格、B类不合格和C类不合格。
不合格品:
具有一个或一个以上不合格的单位产品。
按不合格的重轻程度可划分为A类不合格品、B类不合格品、C类不合格品。
6.检查批及批量
(1)检查批:
为实施抽样检查回汇集起来的单位产品,简称批。
(2)批量:
批中所包含的单位产品数,即提交检查的一批产品中所包含单位产品的总数,以N表示。
常用的计数抽样标准
GB2828-87逐批检查计数抽样程序及抽样表(适用于连续批的检查)
GB2829-87周期检查计数抽样程序及抽样表(适用于生产过程稳定性的检查)
1.GB2828-87的应用
使用原则
a.在生产稳定的条件下
b.适用于连续批的检查,不适用于孤立批
基本思想
a.由抽样次数为一次,二次,五次,检查严格度为正常,加严,放宽及特宽组成共12张抽样方案表
b.合格质量水平AQL:
认为可接受的连续提交检查批的过程平均值.
c.检查水平IL
d.检索方法
a.由N及规定的IL确定出样本大小字码CL
b.由规定的抽样方案类型,检查严格度确定所要采用的抽样方案表
c.由N,IL,CL,AQL检索出相应的抽样方案
d.同行原则
判定原则
其中Re=Ac+1Ac:
合格判定数Re:
不合格判定数
示例
例1N=1000IL=IAQL=0.40查出正常检查一次抽样方案
由表2查出CL=G,
由G和AQL=0.40在表3中查出抽样方案为n=32,Ac=0,Re=1
抽样方案为:
32[0,1]
例2N=500IL=ⅡAQL值:
A类不合格=0.65B类不合格=2.5,
查出一次正常检查抽样方案
由表2查CL=H
由H和AQL=0.65在表3中查出抽样方案n=80,Ac=1,Re=2
由H和AQL=2.5在表3中查出抽样方案n=50,Ac=3,Re=4
则抽样方案为:
A类80[1,2]B类50[3,4]
用A类不合格n=80划一处理,样本大小为J
则A类80[1,2]B类80[5,6]
(6)当AQL小于或等于10的合格质量水平数值时,可以是每百单位不合格品数,也可以是每百单位产品不合格数;当AQL大于10时仅表示每百单位产品不合格数。
AQL参考数值
特高
高
中
低
AQL
≤0.1
≤0.65
≤2.5
≥4.0
适用范围
飞机、舰艇、重要军工产品
一般军用和一般工农业产品
一般民用产品
确定检查水平一般应考虑多方面因素及方法
当n≥N时的规定
例:
N=100IL=ⅡAQL=0.10查出一次抽样方案
批的处理
a合格批应整批接受,但应除去样本中的不合格品;
b不合格批原则上整批拒收;
c合格批在库房中存放一定时间后应重新逐批检查,合格后方可交付。
转移规则
2.GB2829的应用
原则
a主要控制系统误差,不考虑随机误差
b用于对生产厂家能否成批生产合格品或继续维持成批生产合格产品能力的一种判断方法。
检索方法
a规定判别水平DL有三类:
ⅠⅡⅢ
b确定不合格质量水平RQLRQL为不可接受的批质量下限值
c选择抽样方案类型
d检索抽样方案
示例
例1DL=IRQL=30一次抽样方案
例2DL=ⅡRQL=50二次抽样方案
当RQL小于100时,可以是每百单位产品不合格品数,也可以是每百单位产品不合格数;大于或等于100时,仅为每百单位产品不合格数。
RQL参考值
特高
高
中
低
RQL
重要军工产品
一般军用和工农业产品
教育和生活用品
无论使用哪种抽样方案类型,其提交检查批的鉴别能力基本上是相同的。
在规定相同的RQL的条件下,判别水平Ⅲ对生产过程稳定性的鉴别能力最强,判别水平I最弱。
3.GB2828与GB2829的不同点
适用范围
GB2828连续批的检查,检查目的是将随机误差控制在AQL以下