我国烧碱生产技术发展现状.docx
《我国烧碱生产技术发展现状.docx》由会员分享,可在线阅读,更多相关《我国烧碱生产技术发展现状.docx(18页珍藏版)》请在冰豆网上搜索。
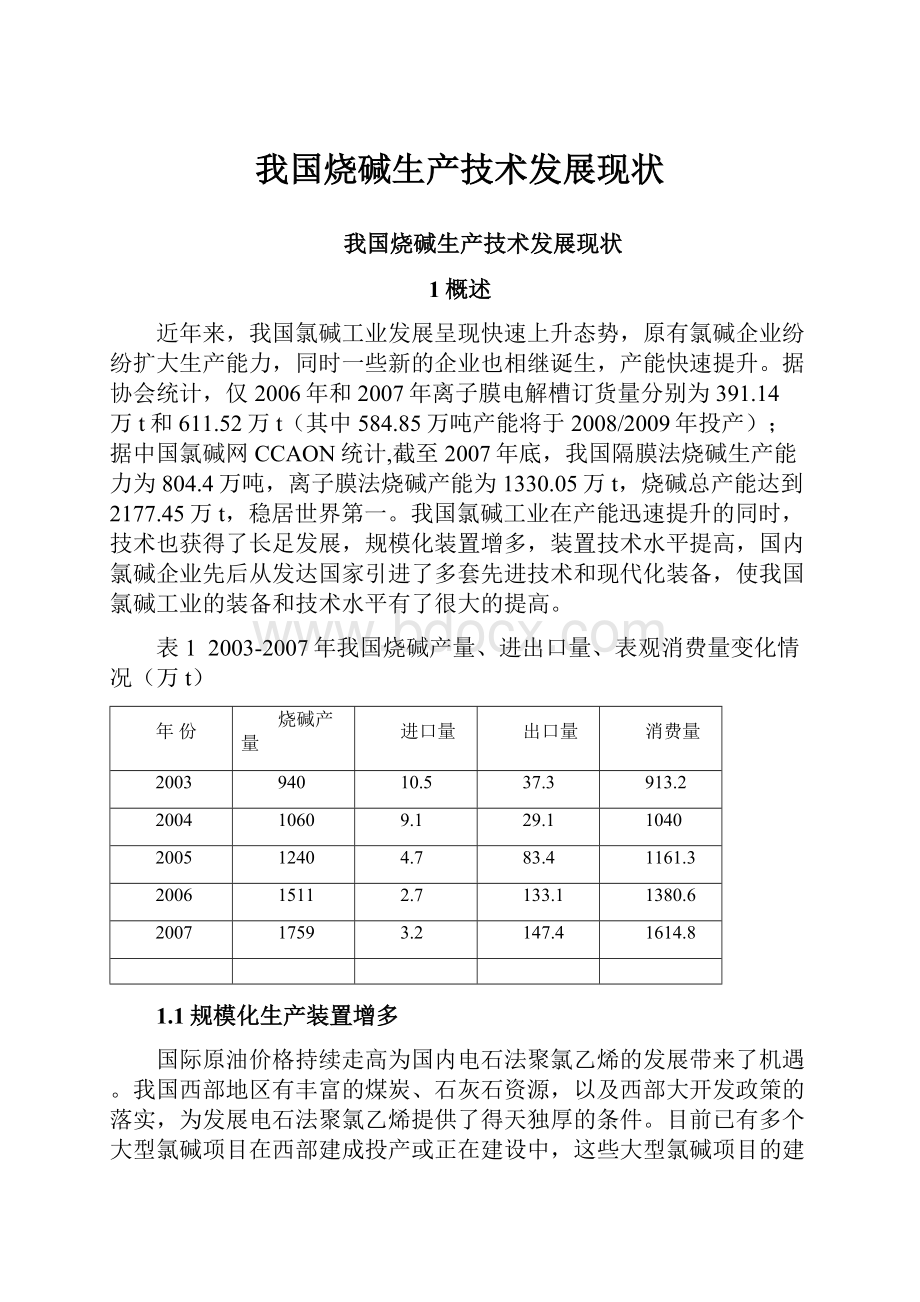
我国烧碱生产技术发展现状
我国烧碱生产技术发展现状
1概述
近年来,我国氯碱工业发展呈现快速上升态势,原有氯碱企业纷纷扩大生产能力,同时一些新的企业也相继诞生,产能快速提升。
据协会统计,仅2006年和2007年离子膜电解槽订货量分别为391.14万t和611.52万t(其中584.85万吨产能将于2008/2009年投产);据中国氯碱网CCAON统计,截至2007年底,我国隔膜法烧碱生产能力为804.4万吨,离子膜法烧碱产能为1330.05万t,烧碱总产能达到2177.45万t,稳居世界第一。
我国氯碱工业在产能迅速提升的同时,技术也获得了长足发展,规模化装置增多,装置技术水平提高,国内氯碱企业先后从发达国家引进了多套先进技术和现代化装备,使我国氯碱工业的装备和技术水平有了很大的提高。
表12003-2007年我国烧碱产量、进出口量、表观消费量变化情况(万t)
年份
烧碱产量
进口量
出口量
消费量
2003
940
10.5
37.3
913.2
2004
1060
9.1
29.1
1040
2005
1240
4.7
83.4
1161.3
2006
1511
2.7
133.1
1380.6
2007
1759
3.2
147.4
1614.8
1.1规模化生产装置增多
国际原油价格持续走高为国内电石法聚氯乙烯的发展带来了机遇。
我国西部地区有丰富的煤炭、石灰石资源,以及西部大开发政策的落实,为发展电石法聚氯乙烯提供了得天独厚的条件。
目前已有多个大型氯碱项目在西部建成投产或正在建设中,这些大型氯碱项目的建设将加速我国氯碱行业向规模化发展。
但总体上看,我国氯碱行业的集约化经营度还比较低的,如美国烧碱总产能约1400万t,仅有13家生产商,装置31套。
世界十大氯气生产商的总产能为2049万t,约占全球总产能的40%。
据协会技术经济网2007年统计数据显示,2007年我国烧碱产量大于30万t/a的企业有6家,20-30万t/a的企业有14家,10-20万t/a的企业有43家,低于10万t/a的企业有100多家,相比之下,我国氯碱企业的集中度是非常低的,全球十大氯气生产商情况见表2。
表2全球十大氯气生产商
名次
公司名称
氯气总产能/万t
全球份额/%
1
DOW
665.8
12.71
2
Occidental
274.3
5.42
3
FormosaPC
186.4
3.56
4
PPG
169.4
3.24
5
Solvay
169.2
3.23
6
Bayer
161
3.07
7
Atofina
123.8
2.37
8
Olin
105.0
2.00
9
AsahiGlass
103.8
1.98
10
TosohCorp.
90.6
1.73
合计
2049.6
39.15
1.2装置的技术水平不断提高
面对日益高涨的原油价格、环保要求的不断提高、十一五节能减排目标的实现,发展离子膜烧碱已经成为氯碱企业调整产品结构、节能降耗、保护环境、增强市场竞争力的主要措施,绝大多数企业都将离子膜法工艺作为扩建或改造项目的首选工艺,国内新建烧碱装置中,基本都采用离子膜法生产工艺。
预计到2009年,我国离子膜法装置生产能力将达到2000万t。
2我国烧碱生产工艺技术现状分析
2.1电解系统
2.1.1离子膜电解工艺技术
离子膜电解法制碱技术因其具有节能、产品质量高、无污染等诸多优点而被世界公认为技术最先进和经济最合理的制碱方法。
近年来,不论是盐水的精制方法、电解槽型、电极材料,还是离子膜本身的性能都有了飞跃发展。
1983年,盐锅峡化工厂引进日本旭化成离子膜法电解技术揭开了我国氯碱工业规模化、工业化生产离子膜法烧碱的新篇章。
随着改革开放的深入,国内许多氯碱企业纷纷引进先进技术。
20多年来,先后有数十家氯碱企业从日本、美国、英国、意大利、德国等国家的世界8大驰名公司引进了数十种离子膜法电解槽,总产能超过1300万t/a。
1984年,北京化工机械厂引进了旭化成、旭硝子离子膜法电解槽制造技术、阳极活性涂层、活性阴极等技术,采用这些引进技术先后制造了复极槽和单极槽。
经过多年的技术转换、消化、吸收和创新,北京化工机械厂制造的具有自主知识产权的国产化离子膜法电解槽已达到世界同类产品的先进水平。
1993年7月,沧州大化集团首家采用了北京化工机械厂制造的MBC-2.7型复极式离子膜法电解槽,为推广国产化离子膜法电解槽开创了先河。
2.1.1.1引进技术
20世纪80年代为技术空白阶段,探索式谨慎引进技术,仅从国外4个公司引进少量离子膜法电解技术装置;20世纪90年代为技术发展阶段,开拓式全面引进技术,从国外6个公司引进大量离子膜法电解技术装置;21世纪初期为技术创新阶段,理性选择引进技术,侧重从旭化成、氯工程、伍迪三大公司选择引进先进的离子膜法电解技术装置。
从1983年盐锅峡化工厂引进日本旭化成离子膜法电解技术至今,世界上绝大多数能够制造离子膜法电解槽技术装置的公司的各种类型、规格的离子膜法电解槽技术装置,包括复极槽单极槽,强制循环形式的、自然循环形式的、半强制循环形式的,小单元面积的、大单元面积的,低电流密度的、高电流密度的,都被引进和采用。
2.1.1.2槽型选择
在20世纪80年代,复极式离子膜法电解槽占绝对优势;进入20世纪90年代,单极式离子膜法电解槽发展迅速,数量大增,生产能力已接近复极式离子膜法电解槽;进入21世纪,复极式电解槽急速发展,数量再次大大超越单极式电解槽,其近几年在氯碱行业一统天下,在新建或改扩建离子膜法烧碱装置时,选择高电流密度、自然循环复极式离子膜法电解槽已成为绝大多数氯碱企业的共识。
2.1.1.3装置规模大型化
20世纪80年代我国引进的离子膜法电解装置为1万-2万t/a;20世纪90年代,上海氯碱化工股份有限公司一次引进l5万t/a,锦化化工(集团)有限责任公司一次引进12万t/a;进入2l世纪,上海天原化工集团一次引进36万t/a,齐鲁股份有限公司氯碱厂一次引进20万t/a,新疆天业化工股份公司一次引进18万t/a大型离子膜法电解装置。
2008年,陕西北元化工一次引进40万t/a。
2.1.1.4电流密度趋高化
离子膜法电解技术不断创新,逐步趋向高电流密度。
早期离子膜法电解槽的电流密度在3.3kA/m左右,电极保证寿命为6年。
而进入2l世纪,北京化工机械厂与旭化成公司合作,后经转换自行制造的ZMBCH-2.7型高电流密度自然循环复极式离子膜法电解槽,其电流密度可达6kA/m;引进的旭化成公司ML32-NCH型离子膜法电解槽、伍迪公司BM-2.7型离子膜法电解槽、氯工程公司BiTAC型离子膜法电解槽,其电流密度均可达到6kA/m,电极保证寿命达8年。
2.1.1.5直流电耗渐低化
离子膜法电解技术进步,其主要目标是降低直流电耗。
早期的直流电耗均在2300KWH/t左右,如旭化成公司标准型自然循环复极槽,电流密度为3.06kA/m时,直流电耗为2430kW·h/t;其改进型自然循环复极槽,电流密度为3.35kA/m时直流电耗为2228kW·h/t。
近几年涌现出一批更加先进的电流密度更高、直流电耗更低的新型离子膜法电解槽,如ML32-NCH型、BiTAC型、BM-2.7型和ZMBCH-2.7型等高电流密度自然循环复极槽,电流密度为5kA/m时,直流电耗均在2130kW·h/t左右。
旭化成公司研制的高电流密度零极距电解槽在天津大沽运行结果显示,高电流密度零极距电解槽比NCH电槽的直流电消耗低近100kW·h/t,且电流密度越高,直流电消耗差距越大。
高电流密度零极距电解槽优势更明显。
氯工程研制的新型n-BiTAC电解槽在芜湖融汇化工运行结果显示,实际直流电耗比BiTAC电解槽直流电消耗低约90kW·h/t。
2.1.1.6向高电流密度自然循环复极式方向发展
高电流密度自然循环复极式离子膜法电解槽具有诸多优势
(1)高电流密度的优势
①强化生产能力。
与早期的3.3kA/m电流密度的离子膜法电解槽相比,相同条件下电流密度为5.5kA/m时,可提高烧碱产量约66.7%。
②降低投资费用。
以旭化成复极式离子膜法电解槽生产l万t/a烧碱为例,在运行电流密度为3.3kA/m时需要98对电极,即需要99个单元槽和98张离子交换膜,而运行在高电流密度4.2kA/m时,则只需78对电极,即需要79件单元槽和78张离子交换膜。
两者相比,单元槽数和离子交换膜数均相应减少20%,电解槽维修费用和更换离子交换膜的费用也低,既节省占地面积,又减少建筑厂房投资。
③减少副反应,提高电流效率。
提高电流密度后,在电解液中氢氧化钠浓度保持不变时,必须相应加大通过离子交换膜的盐水流量,也就必然减少了OH-的反迁移,减少副反应,有利于提高电流效率。
(2)自然循环的优势
采用自然循环方式的离子膜法电解槽,一般是利用电解反应过程中在电解室内生成气体的携带作用,并利用电解槽内部结构造成的电解液密度差,使电解液在电解槽内部循环,其推动力为氯气泡,电流密度越高,单位时间内产生的气泡量越多,推动力也越大。
一般国外运行电流密度为6kA/m左右。
目前国内电解槽运行的电流密度最高为5.5kA/m,正常运行时以4.5kA/m为宜。
采用自然循环形式可提高装置运行的安全、平稳性,减少循环设备和动力能源的消耗,延长离子交换膜的使用寿命,其最终目的是降低生产成本,提高离子膜法电解装置的综合经济效益。
(3)复极式电解槽的优势
复极式电解槽具有流程短、设备少、投资省、单台生产能力大(单台生产能力达2万t/a的电解槽)、占地面积小、布置合理等特点,单元槽串联供电,低电流,高电压,电流效率高,槽间电压损失少;易采用微机控制,管理方便,单元槽用油压紧,检修方便。
2.1.2隔膜电解工艺技术
2.1.2.1改性隔膜技术
国内改性隔膜吸附制造技术和扩张阳极的制造技术都已很成熟,改性隔膜和扩张阳极技术在国内很多工厂都得到了广泛的应用,基本上都采用国产四氟乳液作改性剂,与使用进口SM-2改性剂相比,隔膜的制造成本可大幅度下降。
隔膜的烧结过程是隔膜制作的关键,要求烧结炉内温差控制±3℃内,烧结过程中炉温上升速度能够达到3℃/min以上,因此温度控制最好使用简单的程序控制器实现自控。
结合金属阳极的重涂,采用改性隔膜技术,对普通盒式阳极进行改造是一项技术经济性非常好的技术改造,同样电流密度下,可使槽电压下降0.2V左右,节能效果非常明显。
2.1.2.2活性阴极改性隔膜节能型电解槽
隔膜电解槽的活性阴极技术借鉴了离子膜电解槽的活性阴极技术。
隔膜电解槽所用的活性阴极材料为316L,用超低碳不锈钢板冲孔制成,网孔直径为2.4mm,开孔率为38%左右(而普通阴极网袋开孔率为20%左右)。
采用高温、高浓度碱蚀工艺,将不锈钢表面的Cr、Fe等成分腐蚀掉,在不锈钢表面形成多孔的富镍表层(镍属于中过电位金属,在电流密度为1A/cm时过电位为0.5~0.7V),使阴极活性层的比表面积增大,以降低阴极电流密度,从而降低阴极的析氢电位,也就降低了槽电压。
活性阴极改性隔膜节能型电解槽特点:
(1)活性阴极与普通阴极相比,析氢电位降低200mV左右,活性阴极改性隔膜电解槽的槽电压较普通隔膜电解槽下降0.17V。
(2)活性阴极改性隔膜电解槽氯中含氧体积分数较普通隔膜电解槽上升0.13%,依据氯碱生产技术中虎克公式计算,则阳极效率下降0.26%,相当于电流效率下降0.26%。
(3)活性阴极改性隔膜电解槽氯中含氢量较普通隔膜电解槽低。
2.1.3电解方面新技术介绍
2.1.3.1氧阴极技术
由伍迪公司与拜耳公司共同研发的氧阴极技术(ODC)用于盐酸电解已成功地实现了工业化,2台1万吨氯气/年离子膜法电解盐酸溶液电解槽分别于2003年10月和2004年5月在拜耳公司的Brunsbuettle投入工厂运行。
每台电解槽有76个单元,采用第二代ODC(RhSy)电极,单元有效面积为2.5m2,运行电流密度为5kA/m2,直流电耗1100kW·h/tCl2,较传统的隔膜法盐酸溶液电解槽的电耗下降700kW·h,膜和气体扩散电极的预计寿命为4a。
最大工业化的21.5万t/a盐酸电解装置将于2008年在拜耳上海MDI/TDI一体化工业区投产。
拜耳公司预计用于NaCl溶液电解生产烧碱和氯气的氧阴极技术在2010年开发成功。
2.1.3.2氢燃料电池在氯碱行业的应用
理论上,电解需要电力的20%可由氯碱装置生产的全部H2来供应。
荷兰NedStack和阿克苏诺贝尔基础化学品公司在荷兰Delfzijl建设合资的膜法电解装置,该装置采用了50KW质子交换膜(PEM)燃料电池发电,项目采用来自电解槽的H2副产品为原料,系统由12个质子交换膜反应堆构成,反应堆由NedStack公司制造,每一个拥有75PEM燃料电池。
每一个电池的有效面积为200cm2。
该系统发出峰值电力为120MW,应用中的静态电力为50kW,在56%(低热值氢气)操作点下,拥有理想的燃料电池转化效率。
截至2008年4月中旬,该系统与电网相连已运行超过4000小时。
燃料电池发电超过200MW·h。
据悉,不久应用于氯碱工业计划将使该系统放大至1MW。
阿克苏诺贝尔公司也计划在德国Bitterfeld的氯碱装置上投运15KW碱式燃料电池。
碱式燃料电池比PEM系统的优点是成本较低。
另外,美国Nuvera燃料电池公司完成在意大利Brescia的Caffaro化学公司氯酸盐生产装置上Forza燃料电池的现场试验。
该120KW设施由Uhdenora公司设置,已发电18.5万KWh,使用率超过95%。
目前我国还没有一家氯碱企业采用该项技术,主要是因为需要氢气和氯气合成生成的氯化氢用于聚氯乙烯生产。
2.2盐水系统
2.2.1原盐结构多样化
随着氯碱企业生产规模的不断扩大,原盐消耗量也在不断上升。
为降低盐水生产成本,氯碱企业都在不断优化原盐结构。
尤其2004和2005年国内海盐欠产,供应短缺,卤水、进口盐、真空精制盐的用量大幅增加。
目前,靠近卤水资源的氯碱企业充分利用卤水,卤水用量比例越来越高。
针对有些地区卤水总铵、锶含量较高的特点,可分别加入NaCIO及控制较高的Na2CO3过量,制得合格的盐水。
此外,对大量使用真空盐的工厂,使用中需要注意防结块剂亚铁氰化钾对电解槽的影响。
由于K4[Fe(CN)6]在盐水精制过程中不能被除去,进入电解槽阳极室后会被氧化成Fe3+,导致阳极液中铁离子浓度过高,并以Fe(OH)3的形式沉积于离子膜的阳极侧,Fe(OH)3也会沉积在电解槽阳极液出口软管上,使软管颜色变红,看不清管内液体流动情况。
所以在使用真空盐时,需预先与真空盐生产商进行沟通,少加或不加防结块剂亚铁氰化钾。
对同时生产食用盐的生产商,还需防止食用盐中的碘混入氯碱工业用盐中。
2.2.2一次盐水精制
(1)表面膜过滤技术和新型一次盐水精制技术
随着电解系统大规模地采用离子膜法生产工艺,离子膜电解槽的设计电流密度大幅提高以及金属阳极隔膜电解槽普遍改造为扩张阳极改性隔膜电解槽。
改进盐水生产工艺,提高盐水质量已得到各氯碱生产企业普遍重视。
盐水精制系统的技术进步,主要围绕如何更加有效除去Ca2+、Mg2+等阳离子和阴离子SO42-。
传统的盐水精制工艺采用道尔型(或改良道尔型)澄清设备、砂滤器、碳素管过滤器来实现盐水一次精制,目的是将盐水中的钙、镁离子除到5×10-6以下,SS除到1×10-6以下。
目前新建的离子膜烧碱装置的盐水一次精制系统较多地采用表面膜过滤技术,其优点是膜分离盐水精制工艺流程较传统工艺简单,去除了碳素管过滤器等工艺环节,不需大型的澄清桶砂滤器等设备,占地面积小,投资少,运行费用较低操作方便。
目前我国在盐水精制工艺中采用的过滤膜主要有新加坡凯发公司的HVM膜,美国戈尔公司的GORE-TEX膜和颇尔ZF膜。
从目前已投入运行的装置的运行实绩来看,表面膜过滤技术用于盐水一次精制是非常成功的。
除此之外,新型一次盐水精制技术CN过滤器和陶瓷膜过滤器也被国内一些企业采用。
这两种新技术在中国氯碱工业协会组织的2007年全国烧碱行业技术年会上已进行了介绍。
CN过滤器用于盐水精制过滤,第一台装置在自贡鸿鹤开车成功,目前江苏江东(新厂区)一次盐水工段采用的全部为CN过滤器。
CN过滤器与普通砂滤器有以下几点不同:
①改过滤流程上进下出为下进上出。
②改过滤介质的密度比盐水大为比盐水小,这样过滤层从固定床变为悬浮床。
由于这样一改过滤器的下部有沉清功能,使这台设备洗清功能与过滤功能合二为一,提高了过滤器的容污能力。
同时反冲与排污合二为一。
陶瓷膜是一种固态膜,由无机材料加工而成陶瓷膜有自然多孔的陶瓷外层,此层作为附着在膜管内壁的膜层的支撑体。
构成膜层的组分一般有A12O3、TiO2、ZrO2或SiC等。
膜孔用高技术含量的加工工艺经高温烧结而成。
陶瓷过滤器是不予涂的无机膜精密过滤器。
由于其孔径在50nm左右,平均孔径为40nm,过滤后SS可达到2006年,九江新康达化工实业有限公司率先在国内采用了无机陶瓷膜过滤技术盐水精制系统,省去了体积庞大的澄清桶,工艺简单,盐水质量可靠。
(2)纳滤膜过滤SO42-技术
精制盐水的运行指标对离子膜的影响有多个方面,其中硫酸根离子的含量高低是一个重要指标,指标过高将影响离子膜的电解效率,并以硫酸钡晶体的形式沉积在阴极侧的表面,也就是离子膜的增强纤维上,造成电解槽电流效率下降、槽电压上升和离子膜使用寿命缩短。
控制盐水中硫酸根离子的方法包括:
硫酸钡或硫酸钙化学沉淀法,离子交换法,硫酸钠结晶法,盐水排放法。
目前国内去除硫酸根离子主要还是传统的BaCl2法,虽然有些工厂在尝试BaCO3法、CaCl2法,但由于BaCO3的溶解问题和反应生产BaSO4包裹在BaCO3外面从而降低了Ba的利用效率等问题,以及CaSO4溶度积大和反应生产的CaSO4易沉积在管道、设备中造成堵塞等问题而难以推广。
传统的BaCl2法虽然简单,除SO42-效果好,但成本高,同时由于BaCl2是剧毒物质,需要严格管理。
加拿大凯密迪开发的纳滤膜过滤技术(简称SRS,即SulphateRemovalSystem),利用膜对二价硫酸根离子的排斥作用,将硫酸根离子从盐水中分离出来,离子膜法电解淡盐水经SRS系统分离后,渗透盐水中硫酸根离子浓度为1.5g/L,排放的高芒水中硫酸根离子浓度为85g/L。
对高芒盐水的处理可采用结晶法或排入海中。
该技术自1997年在美国西方化学公司建成工业示范装置后,已在台湾台塑等公司获得商业化应用。
上海天原集团华胜公司引进了该技术。
凯膜公司已与加拿大凯密迪公司达成战略合作,共同推广SRS技术,目前国内已有多家企业采用该项技术。
此外,离子交换法为应用两性离子交换树脂,可以同时除去SO42-及氯酸。
该方法不产生污泥,除使用软水以外不使用其他药剂,是划时代的新技术,但由于该方法消耗的软水量较大,在日本仅有东曹公司使用,目前还没有国内企业应用的报道。
2.2.3盐水二次精制
盐水二次精制技术几乎没有变化,螯合树脂塔系统有二塔和三塔工艺流程,越来越多的工厂选择出于安全考虑,选择了三塔工艺。
二次盐水质量在线分析仪表虽有厂家引进,但维护困难,基本上都用不好,主要依靠ICP每天的分析。
不同型号的螯合树脂对杂质离子的选择吸附能力有一定差异,各企业可以根据自己一次精制盐水的质量情况,选择更加适合的树脂。
2.2.4盐水综合法工艺
国外拥有离子膜和隔膜法两种制碱工艺的氯碱厂,通常采用蒸发结晶盐重饱和离子膜法电解淡盐水供隔膜法电解使用的综台法供水工艺,既减少一次精制盐水的生产量和制造费用,又可将SO42-和对离子膜有害的杂质离子通过隔膜碱带出,可以说是一种比较好的盐水供给工艺。
该工艺的关键设备是结晶盐重饱和器,需要注意的是结晶盐溶解过程中液体上升速度必须控制不超过6m/h,这样可以有效解决细盐颗粒的夹带问题。
采用综合法盐水工艺,离子膜法烧碱和隔膜法烧碱的装置能力最好能满足一定的比例,最佳比例为3:
2,若比例过高或过低将影响综合法工艺的经济性。
对于国内既有隔膜法烧碱又有离子膜法烧碱的企业而言,采用综合法盐水工艺,对减少一次精制盐水的生产量和制造费用,提高隔膜法电解的盐水质量,延长石棉隔膜的使用寿命,尤其对延长改性隔膜的使用寿命都将有很大的好处。
2.3氯氢处理
2.3.1氯气干燥
氯气处理由氯气的干燥及压缩两部分组成。
氯气干燥工艺基本为氯气水洗塔→氯气冷却器→水除雾器→填料塔→泡罩塔→酸雾捕集器→透平压缩机→用户,多采用二塔干燥流程。
但为了确保干燥效果和适应各种生产负荷,目前趋向于三塔干燥流程,即2台填料塔加1台组合塔,处理后能更好地满足透平机要求。
这里水除雾器效果是其中的关键,如氯气中夹带的盐不除干净,酸雾捕集过滤层表面会截留较多白色固体颗粒,很容易堵塞过滤器,从而使系统阻力升高,影响生产。
在对引进设备消化的基础上,国内生产的泡罩塔已能完全替代进口设备,如浙江临安汇通玻璃钢公司生产的PVC/FRP泡罩塔已在多家氯碱厂使用,单台设备的生产能力可以为15万t/a烧碱装置配套。
酸雾的捕集,相比国产纤维除雾器,孟莫克公司(原孟山都公司)生产的布林克除雾器的正常使用寿命很长,用于干氯气中酸雾的去除可达十年以上寿命。
2.3.2氯气压缩输送
氯气压缩输送设备,透平机与纳氏泵相比具有明显的节能优势,一般可节能20%左右,而且单台机器的输气量大,因此,有一定规模的氯碱工厂大都采用透平压缩机。
国内锦化机生产的1800~4500m3/h的系列透平机在国内有广泛的用户,杭州振兴、求是公司生产的小透平机也颇受欢迎。
对于规模超过10万t/a以上的烧碱装置,基本上都使用进口大型透平机组,如日本三菱重工、荏原制作所、神户制钢、德国PGW等公司的产品。
对于生产规模在5万t/a以下的工厂,大流量纳氏泵仍然是压缩输送氯气较理想的设备。
大型纳氏泵(西门子技术、淄博制造)因其简单、易操作仍有旺盛生命力,与传统纳氏泵相同,仅是生产能力较大。
2.3.3氯气液化和输送
目前国内液氯生产厂大多数采用中压法,引进的螺杆式带经济器的氟里昂制冷机组用于氯气液化已有很多年,机组运行稳定可靠,操作方便,系统开车时间短。
单台机组的生产能力可根据需要进行选择,从年产两三万吨液氯到10~20万t液氯的机组都有选择。
与老的氨-氯化钙盐水间接冷冻法工艺相比,氟里昂法工艺具有明显的节能优势和安全优势,可节约电能约30%~40%,而且从根本上杜绝氯和氨可能接触产生NCl3的机会。
高压法可以省去冷冻机组,对于以生产液氯为主的工厂来说,与氟里昂中压法工艺相比可节约电能20%,具有很大的节能优势。
中压法可分为一级液化和二级液化两种流程。
若低浓度液氯尾气能得到适当处理,可采用一级液化流程;若处理低浓度液氯尾气有困难,希望多生产液氯,可采用二级液化流程。
第1液化器出来的尾气中含氢已达4%~5%(体积分数),进入第2液化器中继续液化时,极易发生爆炸,必须在其尾气出口处设置防爆膜,同时设置尾气吸收装置,以免氯气外逸。
该工艺中的氯气压力和液化温度都易实现,应用企业较多。
高压法:
氯气压力为1.4~1.6MPa(表压),液化温度为3O~5O℃。
高压法常采用3级压缩方式。
在生产能力较小时可用往复式压缩机,生产能力大时则应用透平式压缩机。
由于往复式压缩机对气体纯度要求较高,因此一般在进气前设置液氯洗涤器,以降低氯气中