第二章绿色化工新技术剖析.docx
《第二章绿色化工新技术剖析.docx》由会员分享,可在线阅读,更多相关《第二章绿色化工新技术剖析.docx(29页珍藏版)》请在冰豆网上搜索。
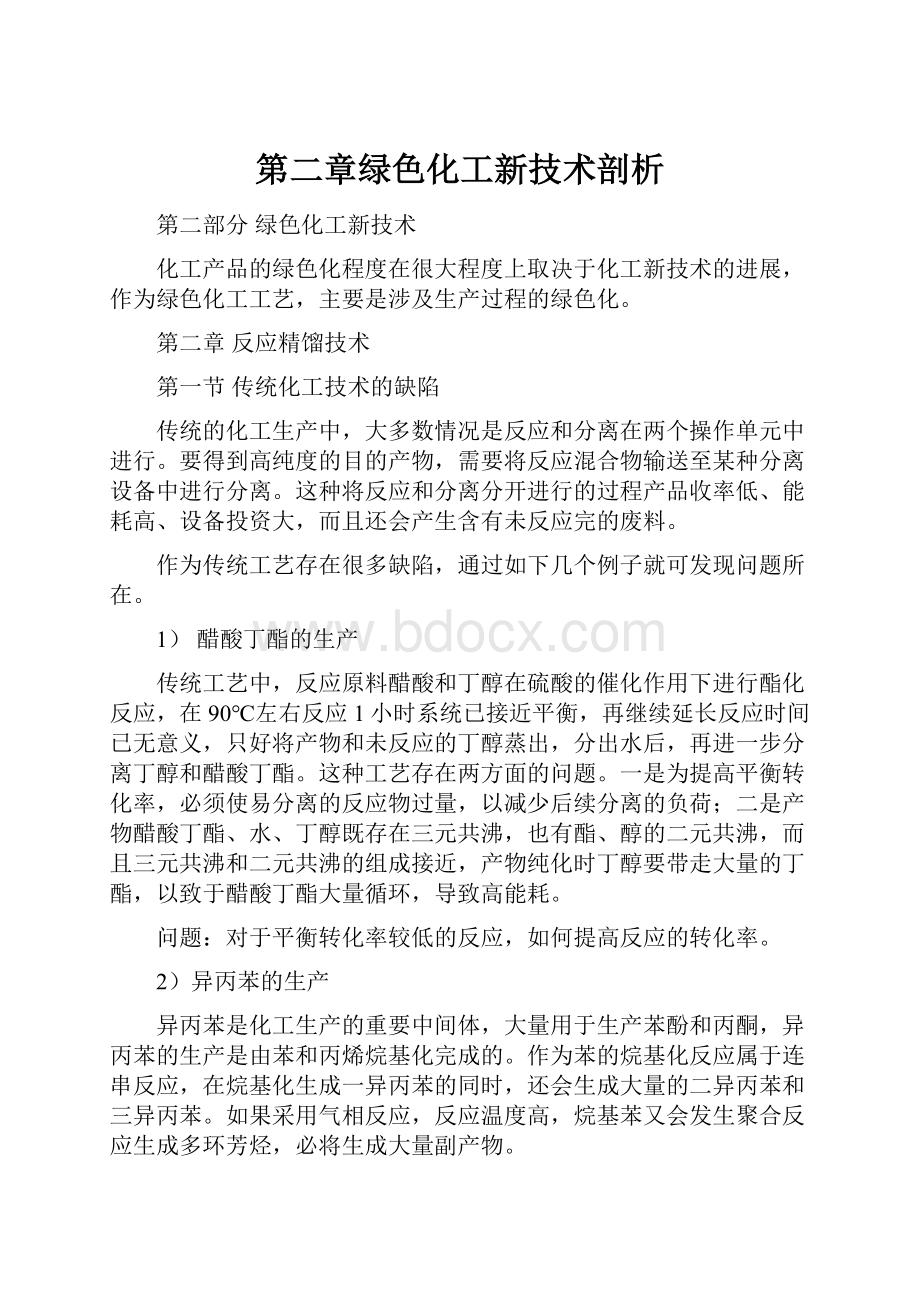
第二章绿色化工新技术剖析
第二部分绿色化工新技术
化工产品的绿色化程度在很大程度上取决于化工新技术的进展,作为绿色化工工艺,主要是涉及生产过程的绿色化。
第二章反应精馏技术
第一节传统化工技术的缺陷
传统的化工生产中,大多数情况是反应和分离在两个操作单元中进行。
要得到高纯度的目的产物,需要将反应混合物输送至某种分离设备中进行分离。
这种将反应和分离分开进行的过程产品收率低、能耗高、设备投资大,而且还会产生含有未反应完的废料。
作为传统工艺存在很多缺陷,通过如下几个例子就可发现问题所在。
1)醋酸丁酯的生产
传统工艺中,反应原料醋酸和丁醇在硫酸的催化作用下进行酯化反应,在90℃左右反应1小时系统已接近平衡,再继续延长反应时间已无意义,只好将产物和未反应的丁醇蒸出,分出水后,再进一步分离丁醇和醋酸丁酯。
这种工艺存在两方面的问题。
一是为提高平衡转化率,必须使易分离的反应物过量,以减少后续分离的负荷;二是产物醋酸丁酯、水、丁醇既存在三元共沸,也有酯、醇的二元共沸,而且三元共沸和二元共沸的组成接近,产物纯化时丁醇要带走大量的丁酯,以致于醋酸丁酯大量循环,导致高能耗。
问题:
对于平衡转化率较低的反应,如何提高反应的转化率。
2)异丙苯的生产
异丙苯是化工生产的重要中间体,大量用于生产苯酚和丙酮,异丙苯的生产是由苯和丙烯烷基化完成的。
作为苯的烷基化反应属于连串反应,在烷基化生成一异丙苯的同时,还会生成大量的二异丙苯和三异丙苯。
如果采用气相反应,反应温度高,烷基苯又会发生聚合反应生成多环芳烃,必将生成大量副产物。
问题:
对连串反应而言,如何提高中间产物的收率。
3)醋酸甲酯的水解
在聚乙烯醇生产中副产大量的醋酸甲酯、甲醇的混合物,由于醋酸甲酯和甲醇共沸,分离相当困难,传统工艺采用7塔流程分解、分离醋酸甲酯成为醋酸和甲醇,回用于生产系统。
流程示意图见图1。
图1醋酸甲酯分解的传统工艺流程
问题:
如何克服共沸对转化率的影响,减少设备数量和能耗。
第二节反应精馏的概念
为解决上述问题就需要借助于反应精馏技术,也就是在绪论部分所讲的强调“输出”的牵引,而不是靠输入物质和能量的推动
为了提高产品收率、降低设备投资和能耗,出现了将“反应和分离”结合在同一个设备中进行的新型分离过程,称为反应精馏。
反应精馏是将化学反应和精馏分离有机耦合在一起的过程,其中化学反应主要涉及液相均相催化反应和非均相催化反应。
因而催化反应精馏又有均相反应精馏和非均相反应精馏。
一、反应精馏技术的的特点
反应精馏是化学反应和精馏过程在同一个装置中进行的化工过程。
在这个过程中化学反应和汽-液之间(均相反应精馏)或气-液-固(非均相反应精馏)之间的传质同时进行,二者相互作用,一方面化学反应强化了传质过程,另一方面,传质过程可以移走产物,加速可逆反应的正反应速率、提高反应物的转化率。
反应精馏具有如下八大优点:
1)反应和精馏同时进行,可有效利用反应热用于产物中轻组分的汽化,从而减少再沸器的负荷,达到节能的目的。
2)由于反应器和精馏塔耦合成为一个设备,大幅度降低了设备投资。
3)反应产物一旦生成,即从反应区蒸出,破坏可逆反应的化学平衡,因而对于复杂反应来说,可以增加反应的转化率,提高反应的选择性。
4)因为反应生成的产物可以从反应区蒸出,反应区内反应物浓度始终维持在较高水平上,从而增加了反应速度,提高了生产能力。
5)在反应精馏塔内,各组分的浓度分布主要由相对挥发度决定,而与进料组分关系不大,因而反应精馏进料可以采用低纯度原料,可使某些系统内循环物流不经分离提纯直接得到利用。
6)在反应精馏塔内,各反应物的浓度不同于进料浓度,造成主副反应的速率差异,达到较高选择性。
对于传统工艺中某些反应物过量,从而需要分离回收的情况,能使原料消耗和能量消耗得到较大的节省。
通过内比调节,不需过量。
7)有时反应物的存在能改变系统各组分的相对挥发度,或绕过共沸组成,所以对于某些难分离物系,可以利用反应精馏来获得纯产品。
8)对连串反应而言,如果中间产物为目标产物,则可借助于反应精馏提高目的产物的选择性。
二、反应精馏的分类
按照其应用目的分类,反应精馏可以大致分为两类:
第一类,以精馏促进反应,可称之为“反应型反应精馏”这一类型的目的主要是为了实现反应过程的要求,如提高反应物的转化率或提高反应的选择性。
这一类过程从应用上说是以反应为主而精馏为辅的过程。
第二类,以精馏为目的,反应为之服务的,可称之为“精馏型反应精馏”。
按照反应精馏系统的相态分类,反应精馏大致可分为两类:
第一类,反应精馏系统仅存在气-液两相,催化剂溶于液相中,可称之为“均相反应精馏”;第二类,反应精馏系统中存在气-液-固三相,催化剂为固体,可随着液体自上而下,也可固定在各个反应段中,可称之为“非均相反应精馏”。
1、反应型反应精馏。
目前反应精馏技术已被应用于许多反应过程之中,这些反应包括:
酯化、酯交换、皂化、胺化、水解、异构化、烃化、卤化、脱水、乙酰化、硝化、氧化、醚化等。
2、精馏型反应精馏。
在化工分离过程中往往一些沸点极为接近的混合物,如某些同分异构体的混合物。
这类混合物的相对挥发度通常小于1.06,利用普通精馏来分离这些混合物往往需要较高的回流比(R>15)和很多的塔板数(N>200)。
因此,设备费用和操作成本都很高,很不经济。
精馏型反应精馏的特点是将第三组分即反应夹带剂引入蒸馏塔中,使夹带剂和异构体中的某一部分有选择地发生快速反应,生成难挥发物质,从而使轻组分很容易地从塔顶分离出来,当夹带剂及其产物能在反应器或再沸器中发生反应生成目的产物时,不再需要夹带剂回收系统,否则,重组分反应夹带剂及其产物从塔底排出后,必须进入另一个或几个塔中将之分离成纯重组分和纯夹带剂。
反应夹带剂的选择是整个过程的关键,作为反应性夹带剂,从适用的角度来考虑必须具备以下条件:
(1)与所分离的组分反应速度快,且可逆、无副反应。
(2)可与被分离组分中的一种选择性反应。
(3)其沸点要么比难挥发组分的沸点要高,要么比最易挥发组分的沸点还要低。
(4)从经济角度考虑,其价格适中、腐蚀性小、无毒且易得。
对于一个难分离的物系,选择满足上述条件的反应物是很困难的,因此“精馏型反应精馏”的应用范围较窄。
3、均相反应精馏
均相反应精馏塔大部分都采用板式塔,为保证一定的转化率。
需要足够的停留时间,因而在反应塔板上要有足够高的液层,故一般情况下,反应塔板内的堰高大于普通精馏塔的堰高,且在实际生产中将它设计成可调的形式,但这样会导致较高的压降,引起釜温过高。
因此,为了不使温度过高,且能保证足够的停留时间,往往在塔外适当的位置并联反应器来提供额外的反应体积。
精馏塔为传质分离设备,通常有板式塔和填料塔两种基本形式,塔内具有较大的空隙率、汽液接触面积和两相间的相对运动速度。
反应精馏塔是催化反应和精馏分离共存的场所,同时满足两种过程的需要,是反应精馏过程成功的关键,许多著名的化工公司开发了许多反应精馏塔的结构,成功的应用在工业反应精馏过程中。
4、非均相反应精馏
均相精馏存在着如下三大缺陷。
1)提馏段中无法终止反应;
2)催化剂与塔釜液的分离;
3)酸催化剂的强腐蚀问题。
正是由于上述缺陷,非均相催化反应精馏得以迅速发展。
在非均相催化反应精馏过程中将催化剂固定在各个反应段,提馏段无催化剂,也就不会发生反应;下降的液体中无催化剂,也就谈不上催化剂的分离问题;催化活性中心在固体催化剂内部固定,不与设备直接接触,因而可有效避免酸催化剂的腐蚀问题。
三、反应精馏的适用范围
反应精馏技术不能适用于所有的化学反应,反应精馏技术的应用受以下条件限制:
1)操作必须在组分的临界点以下,否则蒸汽与液体形成均相混合物,将无法进行分离。
2)在催化反应适应的压力、温度范围内、反应组分必须能进行精馏操作。
3)原料和反应产物挥发度必须有较大的差别和适宜的序列,反应物与产物不能存在共沸现象。
4)过程用的催化剂不能和反应系统各组分有互溶作用。
原料中不能含有催化剂毒物,对在反应中容易在催化剂上结焦的石油化工过程不宜用。
5)精馏温度范围内,催化剂必须有较高的活性、稳定性和较长的寿命。
另外,反应精馏还要求反应温度比较缓和,在反应精馏塔内,各块塔板上的温度为塔板上液体的泡点,反应在此温度下应该有比较合适的反应速率,很明显高温或高压反应不适合反应精馏。
反应精馏工艺相当于简化后的传统工艺。
虽然传统的化工工艺流程通常只有一段反应器,但对于反应精馏塔,为了使反应进行的比较彻底,反应段通常需要多块塔板。
在塔板总数和催化剂装填量一定的条件下,反应段塔板数存在最佳值。
此外,在非反应精馏塔内,轻重组分的进料位置并不十分重要,但在反应精馏塔内,为了使反应物充分接触,轻重组分的进料位置就十分关键。
通常轻组分在反应段底部进料,而重组分在反应段顶部进料。
第三节反应精馏塔的结构及设备选择
一、均相反应精馏塔设备结构及选择原则
均相反应精馏塔大部分都采用板式塔,为保证一定的转化率。
需要足够的停留时间,因而在反应塔板上要有足够高的液层。
故一般情况下,反应塔板内的堰高大于普通精馏塔的堰高,且在实际生产中将它设计成可调的形式,但这样会导致较高的压降,引起釜温过高。
因此,为了不使温度过高,且能保证足够的停留时间,往往在塔外适当的位置并联反应器来提供额外的反应体积。
精馏塔为传质分离设备,通常有板式塔和填料塔两种基本形式,塔内具有较大的空隙率、汽液接触面积和两相间的相对运动速度。
反应精馏塔是催化反应和精馏分离共存的场所同时满足两种过程的需要,是反应精馏过程成功的关键,许多著名的公司开发了许多反应精馏塔的结构,成功应用在工业反应精馏技术中。
对均相催化反应精馏的设备选择主要依据是反应速率和相对挥发度。
选择思路如图2、图3所示。
二、非均相反应精馏塔设备结构及选择原则
非均相催化设备的选择原则如图4所示。
通常的反应精馏塔分为三部分,最上部是精馏段,中间是多级反应段,下部是提馏段,外带冷凝器和塔底再沸器。
结构示意图见图5。
具体应用时需根据情况进行调整,有的不需要精馏段,有的不需要提馏段。
第四节、非均相反应精馏塔内件的现状与发展
一、非均相催化精馏塔发展现状
按反应和精馏的耦合方式不同,催化精馏塔分为两种结构形式:
一种是反应和精馏同时进行,化学反应发生在塔板上或具有催化作用的填料层内;另一种是催化反应和精馏分离交替进行。
国外研发了多种催化精馏塔结构,目前成功的有CR&L结构、IFP结构、Chevron结构和库拉列结构等;此外,还在努力开发框板式、填料隔栅式等催化精馏塔。
国内南京大学致力于筛板上固定催化剂的反应精馏塔、青岛科技大学喷射旋液式反应精馏塔、齐鲁石化研究院(滴流式反应精馏塔)等许多科研单位在这方面取得了很大进展。
二、催化剂装填技术的发展(反应部分)
鉴于催化精馏过程中的催化剂起催化和传质作用,所以要求催化剂结构有较高的催化效率和较好的分离效率。
因此,反应段催化剂床层的结构设计与安装至关重要。
为了让催化反应和精馏分离达到最佳耦合,使整个催化精馏塔操作稳定。
设计和选择反应段装填方式的原则是:
a.为催化剂提供均匀的空间分布,防止溶胀时发生挤压破碎。
b.为催化反应提供足够的表面积和停留时间。
c.为汽液两相提供通畅的流动通道,保证有较高的传质效率。
按以上原则,催化精馏塔装填料方式分为板式塔装填、填充式装填、悬浮式装填和催化剂散装四种。
1、板式塔催化剂装填方式的技术发展
催化剂颗粒直接堆放在塔板上,气液的上下流动使装在塔板上的催化剂呈流化状态,使整个反应区催化剂分布均匀,催化效率高,气、液、固三相接触效果好,但是床层空隙率小,压降大,易造成破损。
人们把催化剂床层设计成同心圆套管结构的板式塔填料方式。
内筒两侧设置类似普通精馏塔的弓形降液管,分别是液相进出塔板的通道。
催化剂装在外层环形管两侧,管内设置多个隔板,隔板上装有一定高度的玻璃珠或设置多孔栅板,起支撑催化剂和分布液体的作用。
采用这种特殊结构,可以任意选定催化剂的装填量,因而催化精馏塔对于快慢反应均能适用。
对于这种催化剂装入降液管中的填充方式,uOP公司进行了相应改进。
将降液管引到塔外催化剂床层与普通塔板交替布置,床层设蒸汽通道,其面积可占床层面积的1%-30%,直径不小于3cm(最好不小于5cm),催化剂的上下底面覆以筛网固定支撑催化剂床层,取得了较好的效果。
2、填充式催化剂装填料方式的发展
填充式催化剂装填料方式是将催化剂装入玻璃纤维制成的小袋中,用不锈钢波纹丝网覆盖,再卷成圆柱体,形成捆扎包。
这种结构装卸方便,而且其强度很高,催化剂结构的尺寸可大可小,在安装时相邻两层催化剂结构的波纹丝网走向错开,使气液分布均匀。
缺点是催化剂被一层玻璃布包着,催化精馏过程中催化剂包内传质阻力大,因此催化剂效率不能充分发挥。
美国Koch公司研制出一种称为Katamax的新型催化剂填料方式,催化剂装入两片波纹网构成的夹层中,然后将其捆成砖状规则地装入塔中,经检验该催化剂填料方式的催化剂效率大于75%,且传质效果和精馏塔相当。
1999年,Sulzer公司推出了Katapak—S型以及Katapak—Sp型催化剂填充方式。
据称性能和指标均超过Katamax,它是把催化剂颗粒放入两片金属波纹丝网的夹层中,集合形成横向通道使气液两相充分接触,催化剂完全润湿、催化反应效率极大提高,传质过程和常规的规整填料一样,且夹层可用各种材料制成,不仅适合腐蚀性产品的生产,且当催化剂活性降低时,可在塔内再生。
当催化剂完全失活更换时,可再次将催化剂填充在网内。
3、悬浮式装填方式的发展
悬浮式催化精馏(SCD)有两种方式,一是催化剂悬浮于进料中从反应段上部加入塔内,在下部和液体一起进入分离器,分出的清液到提馏段,催化剂可以循环使用。
另一是催化剂在塔板中的筛网上靠上升蒸汽悬浮。
悬浮式催化精馏的主要优点是催化剂可以悬浮液的形式加入或取出,而不影响精馏塔的正常操作,减少了传质传热阻力,催化剂效率得到提高;其主要缺点是催化剂与产物分离和稳定操作困难、催化剂在流动中有损失,且增加了设备投资等。
文献中,与传统工艺相比,利用悬浮式催化精馏合成线性烷基苯有独特的优势。
实验结果表明:
在20℃下,采用PW非均相催化剂就能促进反应较快的进行,且提高了目标产物线性烷基苯的产率。
4、催化剂散装填料发展
催化剂填料主要是将催化剂活性材料与离子交换树脂、增强材料、致孔剂、粘合剂和助剂混合后,加工成鞍形和环形填料。
制作方法主要有乳液聚合、嵌段聚合和沉降聚合。
催化剂填料具有催化作用和散装填料的分离作用;单位体积催化精馏塔效率最高;反应段有较大的比表面积、空隙率,床层压降低,为气液接触创造了良好的条件;催化剂容易装卸,低成本,操作方便等优点。
但是由于高分子材料的溶胀特性,在一些反应物系中,可使催化剂填料膨胀,互相挤压破碎,热稳定性差,且催化剂加工困难。
三、同级式反应与分离的反应精馏塔
同级反应分离就是反应与分离在同一级进行的,这种反应精馏塔较传统的反应器和精馏塔来说,它更适合于反应平衡转化率较低的反应,因为同级反应与分离实现了反应与分离的多次循环,这样就可以大大提高反应的最终平衡转化率。
具有此特点的反应器是催化填料式反应器与“背包式”反应器
1、催化填料式反应器
催化填料式反应器包括催化填料式反应器和催化剂打包式反应器。
催化填料是反应精馏填料塔的基本构件,它既有催化反应功能,又有普通的填料的分离能力,因此合适的催化填料应符合如下三个基本要求:
1)在塔内形成均匀的空间分布;
2)有足够的自由空间和接触面积,以降低塔的压降、保证汽液接触充分,合适的空隙率应该达到50%以上;
3)足够的弹性,使催化剂在膨胀或收缩时不至于磨损。
反应精馏的催化剂多数为固体,它不与反应体系各组分互溶。
原料中含有的催化剂应易于消除。
反应中易在催化剂上结焦的物系不宜采用反应精馏技术。
因为反应精馏要求催化剂要有足够的寿命。
80年代,CR&L公司相继提出了多种催化填料结构:
长圆住型催化填料、球型催化填料、椭圆型催化填料。
催化填料如同普通填料一样,只要在塔内自由填放即可。
若将催化填料制成规整填料状装在用玻璃布缝制的小口袋里,并用具有较大开孔率的不锈钢丝覆盖、支撑,卷成钢丝网和布袋相间的捆束式圆柱状催化填料。
这种催化填料装入塔时,可以提供较为均匀的空间分布,使液相能与催化剂充分接触,并有足够的汽液流动通道和接触面积。
A:
催化填料塔的结构
通常催化填料为散装填料,采用不规则堆放方法,均匀装填于塔内。
而已有的两种的规整填料为散装填料的填装则应按一定要求进行,波纹催化填料的装填方法类似于惰性波纹填料,在填料盘内填料元件既要垂直排列,又要使相邻两填料元件上的波纹倾斜方向相反,在波纹状面之间形成一系列相互交叉的三角形流道,同时填料元件上的波纹的方向与塔的纵轴倾角a,其值分别为30°、45°、60°,组成盘外径与塔内径相近的高效精馏塔层,相邻二层波纹的排列方式构成90°交叉安放,以不断改变汽液两相的流动方向,促进质量传递。
同样,在捆束式催化剂填料的装填中,相邻两层填料应交错配置,以防止上升蒸汽的短路。
B:
催化剂打包式反应器
第一种是它将催化剂用多孔的、能包裹住催化剂颗粒的材料将催化剂包成包,再将一个或多个这样的包置于一个多孔盒内,此多孔盒规则排列于塔板的进口堰、出口堰附近,利用塔板上液体的自然流动,在催化剂表面进行反应,再利用塔板进行分离;第二种是将催化剂置于塔板的降液管之中。
利用塔板的自然降液,在催化剂表面进行反应,再利用塔板进行分离。
这两种结构的催化反应精馏塔都是在普通塔板上的局部放置催化剂,利用塔板的自然降液完成催化反应,因此催化剂表面更新缓慢,而且气、液相与催化剂接触时间较短,只进行一次接触,就进入下一层塔板,反应时间短、转化率较低,很难发挥催化反应精馏的优点。
该反应器的优缺点如下:
优点:
该反应器可以看作是反应与分离在同一塔盘上同时进行,对于低平衡转化率的反应也有一定的分离效果。
设计思路简单,操作方便。
缺点:
制作麻烦,催化填料及催化剂构件制作复杂,催化剂失活后装卸不便,不易再生。
包裹物和支撑体难以重复使用,使成本大幅上升,约增加500%。
催化剂利用率较低,将催化剂包裹后,液体反应物或产物只有通过扩散才能进入催化剂床层,反应以后也要通过扩散离开催化剂床层,由于扩散阻力的存在,容易造成产物在催化剂内部的滞留,导致可逆反应接近化学平衡,宏观化学反应速率减慢,同样连串反应中间产物的滞留,易引起深度反应的发生,使反应转化率下降,且由于将催化剂打包放置在降液管以后,用于装载催化剂的体积有限,蒸汽不穿过包装的催化剂,这就使得在反应精馏塔内的反应空间减少,使反应精馏塔的处理量减少,所以将催化剂打包不适合大规模的生产。
2、“背包式”反应精馏塔
所谓“背包式”反应精馏塔,将催化剂置于塔外的反应器中,采用管道将上下相邻或相间的塔板与反应器出口相连的组合设备,如图6所示。
图6“背包式”反应精馏塔
“背包式”反应精馏是将多个装填催化剂的反应器连接到精馏塔上,通过循环抽料泵将精馏塔内的物料抽送至反应器中进行反应,根据反应器的不同,可以分为一次通过、单级再循环、多级再循环。
以一次通过为例,反应液体从反应段的一层塔盘上引出,进入外挂的反应器,待反应液体在“背包”里完成反应,然后通过一管路将汽液两相重新引入塔内,然后部分再反应,部分与汽相相接触,实现汽液的分离。
“背包式”反应器的优缺点如下:
优点:
实现了在同一塔盘上同时进行反应与分离的单元操作,待反应液在反应器中与催化剂进行接触,反应生成的混合物从反应器中循环出来再返回精馏塔中与蒸汽进行气-液接触,接触后的蒸汽再与精馏塔较高级反应器内循环出的溶液再一次进行气-液接触,随着蒸汽通过这一连续的汽-液接触,汽相中的轻组分浓度逐渐增加,能达到较高的分离纯度。
且催化剂的利用率较高,反应速率较快。
对于低平衡转化率的反应最后也能达到较好的分离效果。
缺点:
由于该设备有外挂的反应器组成,这就增加了设备设计的难度,同时还要配上与反应器数目相匹配的循环抽料泵,增加了设备的投资与维护费用。
四、交替式反应与分离的反应精馏塔
交替式反应与分离是反应与分离交替完成的,不是在同一塔盘上完成的,一级实现反应,下一级实现分离。
此种反应器较同级反应与分离的反应器来说更加适合于反应平衡转化率高的反应,因为它没有在同一塔盘上实现多次的反应与分离。
有此特点的反应器有催化剂床层为滴流式反应器和催化剂床层为灌流式反应器。
1、催化床层为滴流式反应器
如图1-3所示,滴流床式反应器是将催化剂散装于塔盘之间的填料层里,待反应的液体从反应器的上部进入,通过催化填料层后从下部滴出,下面的蒸汽上升,在塔盘处与反应液再次相接触,使得反应与分离交替进行。
图7就是滴流床式反应器的结构图。
该反应器的优缺点如下:
图7滴流床式反应器
优点:
催化剂床层与塔壁之间有气相通道,以便蒸汽通过。
由上一级分馏塔盘下降的液体通过催化剂床层进行反应,再经过床层底部的筛孔滴流进入下一级分馏塔盘;由下一级塔盘上升的蒸汽由浮阀孔道穿过塔盘经过气体通道进入上一级塔盘,在每个塔盘处实现一次分离。
该结构形式避免了汽相与液相在催化剂床层的直接接触,克服了催化剂床层压力过大的缺点。
缺点:
滴流式反应器是反应与分离交替进行,对于低平衡转化率的反应是不实用的。
另外,由于催化剂的散堆装填,液体从上面滴流而下,由于重力作用,液体在上面的停留时间短,反应不够充分,而实际起效用的是底部的催化剂,这就使得催化剂利用率低;同时如果液体流量控制不好使得进入催化剂床层的液体要多于流出催化剂床层的液体,待反应液就会在没有经过催化剂床层的时候就从催化剂床层上部溢流而出,这就使得这部分液体得不到反应,从而降低了反应的转化率。
2、催化床层为灌流式反应器
灌流床式反应器中反应液体从上面进入反应器,中间有液体通道,当液体到达反应器底部时,由于下面是封闭的,液体只能从下向上穿过催化剂床层而流出,而在穿过催化剂床层的时候反应液在催化剂存在下发生反应,反应完成后,液体沿四周空隙流下,在下层塔盘处与汽相接触,实现分离。
灌流床式反应器也是反应与分离交替进行。
图8是灌流床式反应器的结构示意图。
灌流床式反应器的优缺点如下:
图8灌流床式反应器
优点:
此结构简化了控制催化剂床层液面的方法,液体的流向自下而上,上一块塔板的液体通过中心降液管进入催化剂床层底部,然后通过催化剂床层,这就使得催化剂完全浸没在反应液中,使反应液充分反应。
反应完的液体溢流至床层与塔板的环隙降液区进入下一块塔板,这样则无须专门的液面控制系统。
缺点:
对于低平衡转化率的反应该结构也不能实用。
另外由于待反应液的过多填充于催化剂床层内,使得反应速度相对较慢。
同时还要考虑到催化剂的比重问题,如果催化剂的比重比待反应液的比重大,则无须增添催化剂压紧装置,但如果催化剂的比重要比反应液的小或相差不太多,则需要安装压紧装置,而安装上压紧装置后,会使通过催化剂床层的反应液流量减少,影响反应精馏塔的生产能力。
由于液体的流向是自下而上,则要求降液管要有一定的高度保证液体有足够的重力势能将液体从催化剂底部流向上部,所以得进行阻力降计算,计算出所需降液管的高度,比较麻烦,且塔盘压降比较大,对于硬件的选择要求比较高。
五、关于反应精馏塔结构的评述
反应精馏塔填料塔与普通精馏填料塔一样,具有结构简单、操作弹性大等优势,但反应精馏塔的基础是催化填料,将催化剂进行包裹并用弹性构件支撑,使其具有足够的空隙率和表面积,达到普通惰性填料的性能,才能使反应精馏顺利进行。
从已有的催化填料结构来看,两个方面的缺陷是客观存在的,一是催化剂利用率较低,将催化剂包裹后会使宏观化学反应速度变慢,反应选择性下降;二是装卸不便,催化剂不易再生,使生产成本增加。
对于催化床层为滴流式