轴承滚子的有限元简化模拟研究.docx
《轴承滚子的有限元简化模拟研究.docx》由会员分享,可在线阅读,更多相关《轴承滚子的有限元简化模拟研究.docx(10页珍藏版)》请在冰豆网上搜索。
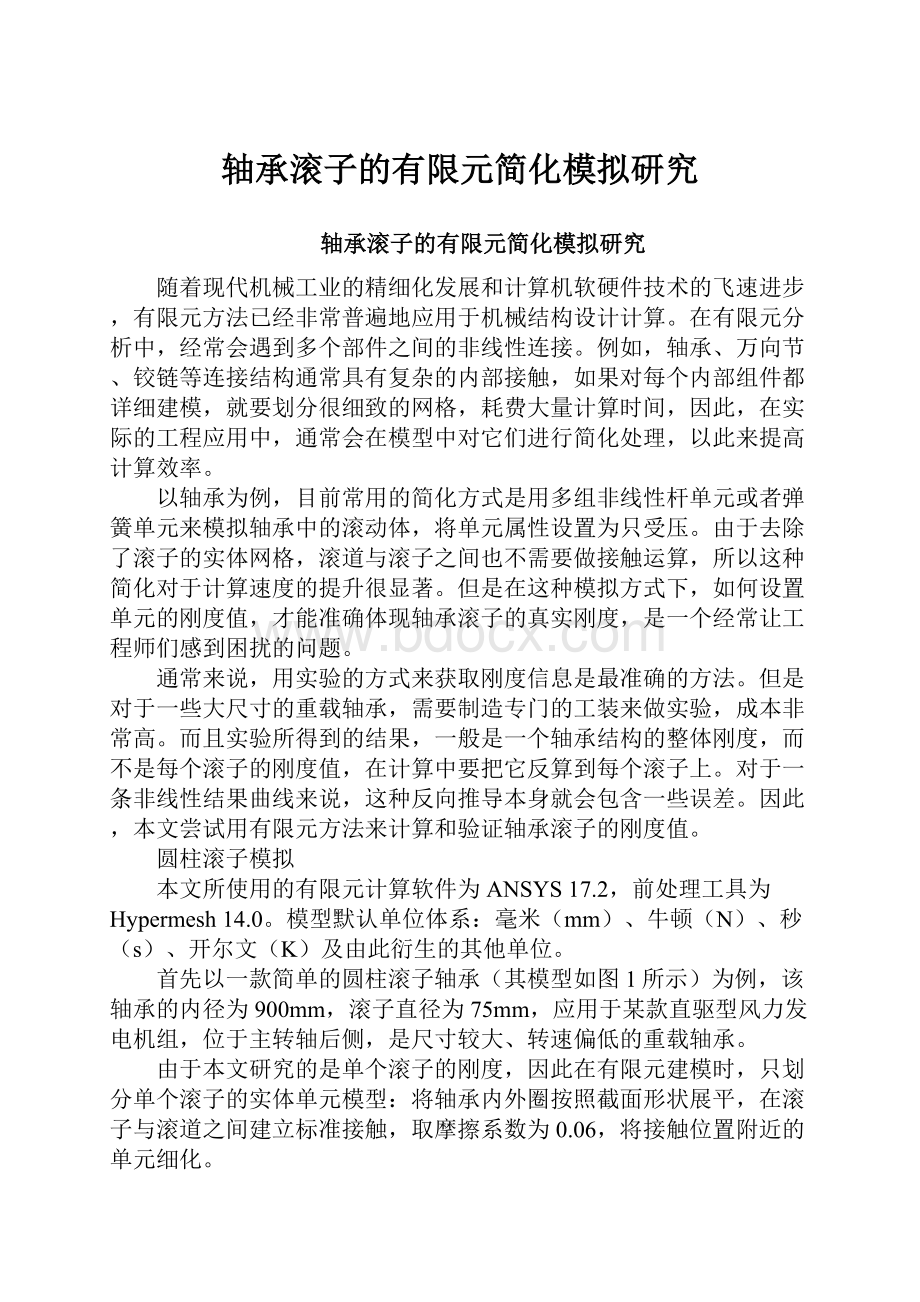
轴承滚子的有限元简化模拟研究
轴承滚子的有限元简化模拟研究
随着现代机械工业的精细化发展和计算机软硬件技术的飞速进步,有限元方法已经非常普遍地应用于机械结构设计计算。
在有限元分析中,经常会遇到多个部件之间的非线性连接。
例如,轴承、万向节、铰链等连接结构通常具有复杂的内部接触,如果对每个内部组件都详细建模,就要划分很细致的网格,耗费大量计算时间,因此,在实际的工程应用中,通常会在模型中对它们进行简化处理,以此来提高计算效率。
以轴承为例,目前常用的简化方式是用多组非线性杆单元或者弹簧单元来模拟轴承中的滚动体,将单元属性设置为只受压。
由于去除了滚子的实体网格,滚道与滚子之间也不需要做接触运算,所以这种简化对于计算速度的提升很显著。
但是在这种模拟方式下,如何设置单元的刚度值,才能准确体现轴承滚子的真实刚度,是一个经常让工程师们感到困扰的问题。
通常来说,用实验的方式来获取刚度信息是最准确的方法。
但是对于一些大尺寸的重载轴承,需要制造专门的工装来做实验,成本非常高。
而且实验所得到的结果,一般是一个轴承结构的整体刚度,而不是每个滚子的刚度值,在计算中要把它反算到每个滚子上。
对于一条非线性结果曲线来说,这种反向推导本身就会包含一些误差。
因此,本文尝试用有限元方法来计算和验证轴承滚子的刚度值。
圆柱滚子模拟
本文所使用的有限元计算软件为ANSYS17.2,前处理工具为Hypermesh14.0。
模型默认单位体系:
毫米(mm)、牛顿(N)、秒(s)、开尔文(K)及由此衍生的其他单位。
首先以一款简单的圆柱滚子轴承(其模型如图1所示)为例,该轴承的内径为900mm,滚子直径为75mm,应用于某款直驱型风力发电机组,位于主转轴后侧,是尺寸较大、转速偏低的重载轴承。
由于本文研究的是单个滚子的刚度,因此在有限元建模时,只划分单个滚子的实体单元模型:
将轴承内外圈按照截面形状展平,在滚子与滚道之间建立标准接触,取摩擦系数为0.06,将接触位置附近的单元细化。
在实体单元有限元模型(图2)中,对内圈滚道内表面所有节点约束Y方向位移,内外圈单侧截断面所有节点约束X方向位移,单侧端面约束Z方向位移。
在此约束条件下,内圈没有刚体位移自由度,外圈有整体沿Y方向上下移动的自由度。
对滚子两端面中心点约束X方向自由度,侧边中点约束Z方向自由度,用于模拟轴承保持架对滚子的整体限位作用。
滚子在YZ平面内不能整体平移和转动,但是滚子本身的弹性变形不受限制。
加载时对外圈滚道外表面所有节点施加强制的均匀位移,分析滚子受压时产生的反力。
总位移1mm,分十步均匀加载。
图3显示了最终分析步下,滚子与滚道之间的接触状态和接触应力。
由于本模型未考虑工艺倒角和滚子修形,所以在端面边缘处出现了应力集中现象,不过该局部并不影响整体刚度结果。
如果要精确计算滚子和滚道的接触应力,那么还是建议把倒角和修形因素全部加入有限元模型。
有限元计算结果与根据ISO/TS16281―2008标准提供的公式计算的理论结果如图4所示,由图可以看到,两条曲线数值比较相近。
这证明在整体刚度的计算上,实体单元的有限元模型与解析算法的结论基本一致。
得到位移与反力的关系曲线后,就可以用简化的方式来模拟轴承滚子。
具体的方法是把一个滚子简化为一排非线性弹簧单元(例如,ANSYS软件中的Combin39单元),这些单元必须平行、均布(图5)。
将弹簧单元的拉伸刚度设为0,压缩刚度按图4中的计算结果均分设置,注意位于两端的单元剛度值要设置成中间单元刚度值的一半。
由简化后的有限元模型(图5)可知,在网格数量上,该模型比实体滚子有限元模型要少得多。
而且去除了接触计算,模型的计算速度极大提升。
在本文的算例中,使用同一台计算机进行计算,实体滚子接触模型的计算时间大约是1小时7分钟,简化模型只有3秒。
然而在统计计算结果后发现弹簧单元产生的反力比预想值低40%左右,这是由于在设置弹簧刚度时,使用的是整个系统的位移与反力关系(图4中的蓝色曲线),轴承内外圈的弹性变形并没有被分离出去。
用这种模型模拟轴承计算显然会造成太大的误差,因此必须对弹簧单元的刚度值进行修正。
修正前后的刚度结果如图6所示,由图可以看到,修正的效果是非常明显的。
但是,需要特别注意的是,由于各型号轴承的内外圈厚度与滚子直径比例不同,修正系数公式
(1)不能直接用于其他轴承模拟。
在模拟其他型号轴承时,需要建立一个对应的单滚子模型重新试算,以确定公式
(1)中的线性放大系数和幂指数,或者采用其他的数学模型对刚度值进行修正,以计算结果的位移与反力曲线判断精度。
以上是关于圆柱滚子轴承的简化模拟方式,类似圆柱形状的滚子也可以用这种方法,比如锥角不超过30度的锥滚子轴承和鼓形滚子的调心轴承。
不过球形滚子的轴承显然不能用这种方式来简化,下面就讨论一下球形滚子的有限元简化模拟方式。
球形滚子模拟
本文使用的球形滚子轴承模型(图7),直径约3m,滚子直径60mm,应用于某款风力发电机组的偏航系统。
图8显示了以实体单元模拟滚球的局部有限元模型,其中的接触设置与上一算例完全一致。
与圆柱滚子轴承不同,滚珠轴承除径向力外,还可以承受一定的轴向力和弯矩,因此在加载方式上,本算例分别采用了径向位移和轴向位移两种载荷。
图9显示了两个方向上最终载荷步下滚子与滚道之间的接触压力,整体刚度计算结果如图10所示。
从位移与反力曲线可以看到,对于单个球形滚子,径向刚度大概是轴向刚度的2倍左右。
由于各个型号的球滚子轴承在设计时预留的接触角不同,滚道形状差异较大,因此,刚度计算公式并不统一,只能按照实际的接触位置进行建模计算。
对于球形滚子的简化模拟,同样是用一组非线性弹簧单元来代替实体滚子,这些单元全部穿过球心,在接触位置与滚道共节点(图11)。
根据球形结构的几何特性,将弹簧刚度的初始值设置为径向总刚度值除以弹簧份数后所得数值的两倍。
简化后的模型,计算时间同样是秒级的,大幅度提高了计算效率。
但是和圆柱滚子的算例一样,将球形滚子简化成弹簧后,同样会造成压力过于集中,需要修正刚度。
经过试算,针对径向刚度进行修正,得到修正公式
(2),修正后的整体刚度结果如图12所示。
从结果中可以看到,针对径向结果进行修正的刚度值,在轴向刚度上的拟合结果并不是特别精确,和实体模型结果大约有5%的差异。
从数值中可以看出,公式
(2)与公式
(1)的修正系数差距非常大,这说明圆柱滚子和球形滚子简化后,在整体刚度表现上有较大的差别。
如果不进行试算的话,不能直接套用其他类型轴承的修正公式。
全轴承模拟
通过上面的方法,得到单个滚子的简化模型和适合的刚度设置值之后,就可以进行全轴承的模拟了。
在建模计算中,尽量保持内外圈实体网格与试算模型的网格一致。
或者反过来说,先建立应用于计算的全轴承简化模型,然后用同样的截面网格来拉伸试算模型,这样能尽量保证试算数据的有效性。
在建模过程中还要注意一点,弹簧单元的复制份数一定要和实际滚子数对应,也就是说内外圈的环向扫掠网格数,必须是滚子个数的整数倍,否则无法做成共节点。
图13显示了本文第一个算例的全轴承简化模型,该轴承的滚子数量是37个。
建立好轴承整体模型之后,就可以将它装配到组件结构的有限元模型中,进行计算分析。
运用这种简化方式,可以极大程度地减小模型规模,提高计算效率,但是有以下几点使用限制:
(1)利用弹簧单元简化模拟轴承滚子,滚道的实体单元与弹簧单元之间是共享节点的,一旦内圈和外圈发生较大的相对转动,就会导致弹簧单元倾斜,无法正确计算反力。
因此,内外圈轴承所连接的部件,必须用直接或间接的方式约束相对转动的自由度。
而且在后处理过程中,要检查弹簧单元首尾节点的环向相对位移,当位移超过滚子直径一定比例时,反力结果不再可信。
這一比例可由分析人员根据计算结果的精确度要求自行设定。
(2)本文介绍的轴承滚子简化方式,可以用于静态或准静态下轴承刚度、反力、滚子承载分布等方面的有限元计算,但是不适用于动态或瞬态计算。
计算结果中的滚子和滚道应力也是不真实的,不能直接用于轴承本身的强度分析。
(3)试算中的变形范围设置,取决于轴承应用环境的实际载荷。
本文算例中使用的都是1mm,在实体接触压力结果中,局部压应力达到6800MPa,已经远远超过轴承滚子的承受范围,在设计工况中不可能应用这么大的载荷。
因此,在针对实际工程问题时,可以先对载荷工况做一个大致的判断,然后设定合理的变形范围进行刚度拟合,以得到更精确的结果。
总结与展望
本文通过两个不同形式的轴承算例,论述了一种用于有限元计算的简化建模方式。
该方式利用弹簧单元代替实体滚子,可以极大地简化模型规模,提高计算效率。
为了得到与实体单元计算相近的轴承刚度,文中对弹簧单元刚度进行了修正。
修正后的轴承整体刚度,与实体模型的结果差距不超过5%,符合大部分工程计算的精度要求。
但是在采用该方式简化计算之前,还是需要先建立单个滚子的实体单元局部模型和对应的简化单元局部模型进行对比计算,以确定弹簧刚度值和修正系数。
因此,如果能通过一系列不同尺寸轴承的计算,设计一个通用的计算公式,将使这一简化方法更加方便实用。
另外,本文中使用的刚度修正系数公式,在修正精度上并不是非常高,需要通过进一步的探索和尝试,找到一种更适合的数学模型。