化工仿真技术实习报告.docx
《化工仿真技术实习报告.docx》由会员分享,可在线阅读,更多相关《化工仿真技术实习报告.docx(21页珍藏版)》请在冰豆网上搜索。
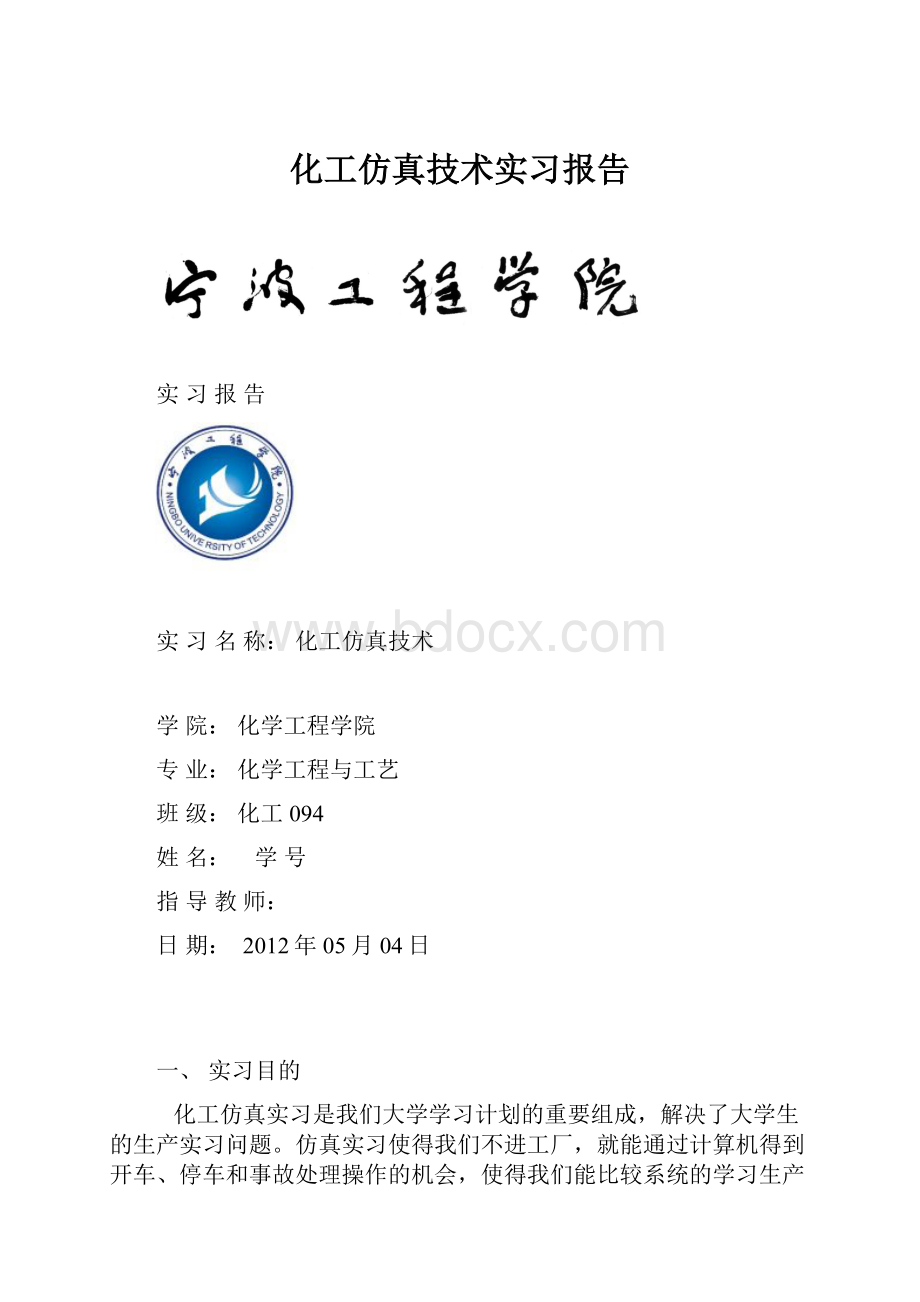
化工仿真技术实习报告
实习报告
实习名称:
化工仿真技术
学院:
化学工程学院
专业:
化学工程与工艺
班级:
化工094
姓名:
学号
指导教师:
日期:
2012年05月04日
一、实习目的
化工仿真实习是我们大学学习计划的重要组成,解决了大学生的生产实习问题。
仿真实习使得我们不进工厂,就能通过计算机得到开车、停车和事故处理操作的机会,使得我们能比较系统的学习生产过程的基本程序和具体操作方法,分析操作参数的合理性、设备及仪表是否运转正常,从而加强我们对基本理论的理解、基本方法的运用和基本技能的训练。
仿真教学有强调工业背景、适用面广、操作与控制界面先进、突出操作实践、内容由浅入深,由简到繁,相互呼应,相互补充、附有大量思考题、实用性强、提倡新的教学方法等优点,能从分发挥学生创造意识的环境。
可很好的将我们所学的理论知识和时间相结合,进一步巩固深化我们的专业知识和技能。
二、实习内容
第1章离心泵及其液位
1、工艺流程简介
如图所示,离心泵系统由一个储水槽、一台主离心泵、一台备用离心泵、管线、调节器及阀门等组成。
上游水源经管线由调节阀V1控制进入储水槽。
上游水流量通过孔板流量计FI检测。
水槽液由调节器LIC控制,LIC的输出信号连接至V1。
离心泵的入口管线连接至水槽下部。
管线上设有手操阀V2及旁路备用手操阀V2B、离心泵入口压力表PI1。
离心泵设有高点排气阀V5、低点排液阀V7及高低点连通管线上的连通阀V6。
主离心泵电机开关PK1,备用离心泵电机开关是PK2。
离心泵电机功率N、总扬程H及效率M分别有数字显示。
离心泵出口管线设有出口压力表PI2、止逆阀、出口阀V3、出口流量检测仪表、出口力量调节器FIC及调节阀V4。
2、工艺流程图
3、开车步骤
1.检查各开关、手动阀门是否处于关闭状态。
2.将液位调节器LIC置手动,调节器输出为零。
3.将液位调节器FIC置手动,调节器输出为零。
4.进行离心泵充水和排气操作。
开离心泵入口阀V2,开离心泵排气阀V5,直至排气口出现蓝色点,表示排气完成,关闭阀门V5。
5.为了防止离心泵开动后储水槽液位下降至零,手动操作LIC的输出使液位上升到50%时投自动。
或先将LIC投自动,待离心泵启动后再将LIC给定值提升至50%。
6.在泵出口阀V3关闭的前提下,开离心泵电机开关PK1,低负荷起动电机。
7.开离心泵出口阀V3,由于FIC的输出为零,离心泵输出流量为零。
8.手动调整FIC的输出,使流量逐渐上升至6kg/s且稳定不变时投自动。
9.当储水槽入口流量FI与离心泵出口流量FIC达到动态平衡时,离心泵开车达到正常工况。
此时各检测点指示值如下:
FIC:
6.0kg/sFI:
6.0kg/s
PI1:
0.15MPaPI2:
0.44MPa
LIC:
50.0%H:
29.4m
M:
62.6%N:
2.76kW
第二章热交换器
一、工艺流程简介
本换热器为双程列管式结构,起冷却作用,管程走冷却水(冷流)。
含量30%的磷酸钾溶液走壳程(热流)。
工艺要求:
流量为18441kg/h的冷却水,从20℃上升到30.8℃,将65℃流量为8849kg/h的磷酸钾溶液冷却到32℃。
管程压力为0.3MPa,壳程压力为0.5MPa。
流程图中:
阀门V4是高点排气阀。
阀门V3和V7是低点排液阀。
P2A为冷却水泵。
P2B为冷却水备用泵。
阀门V5和V6分别为泵P2A和P2B的出口阀。
P1A为磷酸钾溶液泵。
P1B为磷酸钾溶液备用泵。
阀门V1和V2分别为泵P1A和P1B的出口阀。
FIC-1是磷酸钾溶液的流量定值控制。
采用PID单回路调节。
TIC-1是磷酸钾溶液壳程出口温度控制,控制手段为管程冷却水的用量(间接关系)。
采用PID单回路调节。
检测及控制点正常工况值如下:
TI-1壳程热流入口温度为65℃TI-2管程冷流入口温度为20℃
TI-3管程冷流出口温度为30.8℃TIC-1壳程热流出口温度为32℃
FR-1冷却水流量18441kg/hFIC-1磷酸钾流量8849kg/h
二、工艺流程图(CAD绘制)
三、开车步骤
1.开车前设备检验。
冷却器试压,特别要检验壳程和管程是否有内漏现象,各阀门、管路、泵是否好用,大检修后盲板是否拆除,法兰连接处是否耐压不漏,是否完成吹扫等项工作(本项内容不包括在仿真软件中)。
2.检查各开关、手动阀门是否处于关闭状态。
各调节器应处于手动且输出为零。
3.开冷却水泵P2A开关。
4.开泵P2A的出口阀V5。
5.调节器TIC-1置手动状态,逐渐开启冷却水调节阀至50%开度。
6.开磷酸钾溶液泵P1A开关。
7.开泵P1A的出口阀V1。
8.调节器FIC-1置手动状态,逐渐开启磷酸钾溶液调节阀至10%。
9.壳程高点排气。
开阀V4,直到V4阀出口显示蓝色色点,指示排气完成,关V4阀。
10.手动调整冷却水量。
当壳程出口温度手动调节至(31.5-32.5)℃且稳定不变后打自动。
11.缓慢提升负荷。
逐渐手动将磷酸钾溶液的流量增加至8800kg/h左右投自动。
开车达正常工况的设计值见工艺说明。
第三章精馏系统
一、工艺流程简介
脱丁烷塔是大型乙烯装置中的一部分。
本塔将来自脱丙烷塔釜的烃类混合物(主要有C4、C5、C6、C7)等,根据其相对挥发度的不用,在精馏塔内分离为塔顶C4馏分,含少量C5馏分,塔釜主要为裂解汽油,即C5以上组分的其他馏分。
因此本塔相当于二元精馏。
工艺流程为:
来自脱丙烷塔的釜液,压力为0.78MPa,温度为65℃(由TI-1指示),经进料手操阀V1和进料流量控制FIC-1,从脱丁烷塔(DA-405)的第21块塔板进入(全塔共有40块塔板)。
在本塔提馏段第32块塔板处设有灵敏板温度检测及塔温调节器TIC-3(主调节器)与塔釜加热蒸汽流量调节器FIC-3(副调节器)构成串级控制。
塔釜液位由LIC-1控制。
塔釜液一部分经LIC-1调节阀作为产品采出,采出流量有FI-4指示,一部分经再沸器(EA-405A/B)的管程汽化为蒸汽返回塔底,使轻组分上升。
再沸器采用低压蒸汽加热,釜温由TI-4指示。
设置两台再沸器的目的是釜液可能含烯烃,容易聚合堵管。
万一发生此种情况,便于切换。
再沸器A的加热蒸汽来自FIC-3所控制的0.35MPa低压蒸汽,通过入口阀V3进入壳程,凝液由阀V4排放。
再沸器B的加热蒸汽亦来自FIC-3所控制的0.35MPa低压蒸汽,入口阀为V8,排凝阀为V9。
塔釜设排放手操阀V24,当塔釜液位超高但不合格不允许采出时排放用。
塔顶和塔底分别设有取压阀V6和V7,引压至差压指示仪PDI-3,及时反映本塔的阻力降。
此外塔顶设压力调节器PRC-2,塔底设压力指示仪PI-4,也能反映塔压降。
塔顶的上升蒸汽出口温度由TI-2指示,经塔顶冷凝器(EA-406)全部冷凝成液体,冷凝液靠位差流入立式回流罐(FA-405)。
冷凝器以冷却水为冷却剂,冷却水流量由FI-6指示,受控于PRC-2的调节阀,进入EA-406的壳程,经阀V23的排出。
回流罐液位由LIC-2控制。
其中一部分液体经阀V13进入主回流泵GA405A,电机开关G5A。
泵出口阀为V12。
回流泵输出的物料通过流量调节器FIC-2的控制进入塔顶。
备用回流泵的入口阀V15,出口阀为V14,泵电机开关是G5B。
另一部分作为产品经入口阀V16,用主泵GA-406A送下道工序处理。
主泵电机开关为G6A,出口阀为V17。
顶采泵输出的物料由回流罐液位调节器LIC-2控制,以维持回流罐的液位。
回流罐底设排放手操阀V25,用于当液位超高但不合格不允许采出时排放用。
手操阀VC4是C4充压阀。
系统开车时塔压低会导致进料的前段时间内入口部分因进料大量闪蒸而过冷,局部过冷会损坏塔设备。
进料前用C4冲压可防止闪蒸。
二、工艺流程图(CAD绘制)
三、开车步骤
1.开车前的准备工作:
将各阀门关闭。
各调节器置手动,且输出为零。
2.开“N2”开关,表示氮气置换合格。
3.开“G.Y.开关,表示公用工程具备。
4.开“Y.B.”开关,表示仪表投用。
5.开C4充压阀VC4,待塔压PRC-2达0.31MPa以上,关VC4,防止进料闪蒸,使塔设备局部过冷(此步不完成,后续评分为零)。
6.开冷凝器EA-406的冷却水出口阀V23。
7.开差压阀V6和V7。
8.开进料前阀V1,手动操作FIC-1的输出约20%(进料量应大于100koml/h),进料经过一段时间在提留段各塔板流动和建立持液量的时间迟后,塔釜液位LIC-1上升。
由于进料压力达0.78MPa,温度为65℃,所以进塔后部分闪蒸使塔压上升。
9.通过手动PRC-2输出(即冷却水量),控制塔顶压力在0.35MPa左右,投自动。
10.当塔釜液位上升达60%左右时,暂停进料。
开再沸器EA-405A的加热蒸汽入口阀V3和出口阀V4。
11.手动开加热器蒸汽量FIC-3的输出约为20%,使塔釜物料温度上升直到沸腾。
塔釜温度低于约108℃的阶段为潜热段,此时塔顶温度上升较慢,回流罐液位也无明显上升。
12.注意当塔釜温度高于108℃后,塔顶温度及回流罐液位明显上升。
说明塔釜物料开始沸腾。
为了防止回流罐抽空,当回流罐液位上升至10%左右,开GA405A泵的入口阀V13,启动泵G5A,然后开泵出口阀V12。
手动FIC-2的输出大于50%,进行全回流。
回流量应大于300koml/h。
13.调整塔温进行分离质量控制。
此时塔灵敏板温度TIC-3大约为69~72℃左右。
缓慢调整塔釜加热FIC-3,以每分钟0.5℃提升TIC-3直到78℃(实际需数小时)。
缓慢提升温度的目的是使物料在各塔板上充分进行气液平衡,将轻组分向塔顶升华,将重组分向塔釜沉降。
当TIC-3的给定值升至78℃时,将灵敏板温度控制TIC-3投自动(主调节器),将FIC-3投自动(副调节器),然后两调节器投串级。
同时观察塔顶C5含量AI-1和塔底C4含量AI-2,应当趋于合格。
同时注意确保塔釜液位LIC-1和回流罐液位LIC-2不超值(当塔顶AI-1不合格且LIC-2大于80%,应及时开阀门V25排放。
同理,当塔釜AI-2不合格且LIC-1大于80%,应及时开阀门V24排放)。
14.此刻塔顶及塔釜液位通常尚未达到50%,重开进料前阀V1,手动操作FIC-1的输出。
可逐渐提升进料量,由于塔压及塔温都处于自动控制状态,塔釜加热量和塔顶冷却量会随进料增加而自动跟踪提升。
最终进料流量达到370kmol/h时将FIC-1投自动。
15.手动FIC-2的输出将回流量提升至350kmol/h左右,投自动。
16.塔顶采出:
提升进料量的同时,应监视回流罐液位。
当塔顶C5含量AI-1低于0.5%且LIC-2达到50%左右时,先开V16阀,开泵G6A(GA406A),再开泵出口阀V17。
手动调节LIC-2的输出,当液位调至50%时投自动。
17.塔顶采出:
提升进料量的同时,应监视塔釜液位。
当塔釜C4含量AI-2低于1.5%且LIC-2达到50%左右时,手动调节LIC-1的输出,当液位调至50%时投自动。
18.将塔顶压力调节器PRC-2和PIC-1投超驰(用投串级代替)。
19.微调各调节器给定值,使精馏塔到达设计工况:
FIC-1370kmol/h
FIC-2350kmol/h
LIC-150%
LIC-250%
TIC-378℃
PRC-20.35MPa
AI-1<0.5%
AI-2<1.5%
第四章吸收系统
一、工艺流程简介
来自前一工序的生成气(富气,其中C4组分(包括C4、C2)占25.13%,CO和CO2占6.26%,N2占64.58%,H2占3.5%,O2占0.53%)从板式吸收塔DA-302底部经手操阀V1进入,与自上而下的吸收油(贫油,C6油)接触,将生成气中的C4组分吸收下来,未被吸收的不凝气(贫气)由塔顶排出,经手操阀V2进入盐水冷却器EA-306的壳程和尾气分离罐FA-304,通过手操阀V22回收冷凝的C6和C4,尾气经压力调节器PIC-308输出调节阀排至放空总管进入打气。
PIC-308的输出调节阀设有前阀V4、后阀V5和旁路手操阀V3。
冷却盐水经手操阀V26进入EA-306的管程,通过手操阀V27排出。
C6油通过手操阀V6进入吸收油储罐FA-311,经罐底出口阀V7和V8至泵G2A(G2B为备用泵),由出口阀V9排出,通过吸收油流量调节器FRC-311的输出调节阀(其前阀为V12,后阀为V13)打入塔顶,与自下而上的生成气接触,吸收其中的C4组分为富油,从吸收塔底排出。
塔底富油经出口阀V14、出口富油刘两调节器输出调节阀,再经贫、富油热交换器EA-311的壳程,通过手操阀V17进入解吸塔DA-303。
解吸塔塔顶生产出C4产品,解吸塔底部的C6油通过塔釜液位调节器LIC-312的输出调节阀进入贫、富油热交换器EA-311的管程,出口经手操阀V20进入贫油冷却器EA-312的壳程,再经手操阀V21返回吸收油储罐FA-311循环使用。
冷却器EA-312采用冷冻盐水使贫油温度下降,有利于提高吸收效率。
盐水由入口阀V24进入EA-312管程,出口温度调节器TIC-312的输出调节阀,再经手操阀V25排出。
随着生产过程的进行,尾气分离罐的液位将上升,吸收油因部分损耗导致储罐的液位有所下降。
要定期用V22排放尾气分离罐内的液体,用V6补充新鲜C6油进入储罐。
主要工艺条件和指标:
吸收塔顶压1.2MPa左右吸收油温度4~6℃
富气流量5000kg/h贫油流量13500kg/h
质量指标吸收塔顶尾气中C4<0.5%,C6<0.6%
二、工艺流程图(CAD绘制)
三、开车步骤
1.开车前的准备工作
将各调节器置手动,且输出为零
将各手操器和开关关闭
开“GYG”,表示公用工程具备
开“YBT”,表示仪表投用
开“N2S”,表示系统氮气吹扫完成
开“N2H”,表示氮气置换合格
2.建立吸收塔和解吸塔系统C6冷循环和热循环
开阀门V6,向FA-311引入贫油,LI-311上升
当LI-311上升至50%之前,先全开V7、V8,启动泵G2A,然后开V9、V12、V13。
当LI-311上升至55%左右,手动开FRC-311的输出约20%,当塔内持液量建立后,吸收塔液位LIC-310上升。
注意调整V6阀,保证LI-311不超限。
当LIC-310达到50%之前,全开V14、V15、V16和V17。
当LIC-310接近50%时,手动开FIC-310,C6油进入解吸塔,LIC-312上升。
当LIC-310达到50%时将LIC-310和FIC-310同时投入自动和串级。
当LIC-312达到50%之前,全开V18、V19、V20、V21、V24和V25。
当LIC-312达到50%时投自动。
此时已建立C6油的冷循环。
由于设备及管线的持液量也基本建立,若继续进C6油会导致LI-311迅速上涨。
应注意关小V6,防止LI-311超限。
建立C6油循环时,稳定工况的关键是控制FRC-311不宜过大,否则难于控制各液位。
冷循环一旦建立,解吸塔会立即升温。
可观察到系统各测量点温度上升,说明系统已进入热循环阶段。
3.氮气升压为了稳定富气进塔的流量,提高开车阶段的吸收效率,在接收富气前将吸收塔用氮气升压有好处。
开氮气充压阀VN2,将DA-302压力提到1.0MPa以上,关VN2。
4.接收富气(C4混合气)确认热循环已建立,氮充压完成,可开始进富气。
逐渐开V1,同时开V2约10%~20%左右。
注意各检测点压力逐渐上升。
开V4、V5,当PIC-308压力升至1.2MPa左右时投自动。
随压力上升,逐渐开大V1和V2,使FI-308达到2000kg/h左右。
进富气达到一定负荷后,开V26和V27,调整两阀使TI-308在5℃一下,以便在FA-304中分离C6油。
5.手动开TIC-312的输出使温度降低至5℃左右,投自动。
6.投自动和比值调节设“AKB”为53.5%左右,将FRC-311投自动和比值调节(以串级表示)。
7.提升进富气负荷逐渐开大V1和V2,待吸收塔顶温TI-309下降至7.0℃左右,使进气流量缓慢提高到5000kg/h左右。
注意当LI-309高于60%时,可适当开V22阀。
由于C6油在吸收解吸过程中有一定的损耗,当LI-311下降时应适当开大V6补充C6油。
8.将系统调整到正常工况
设计值范围如下:
项目
数值
项目
数值
FI-308
5000kg/h
FRC-311
13300kg/h
PIC-308
1.20MPa
TI-308
<5.0℃
TIC-312
5.0℃
LIC-310
50%
LIC-312
50%
LI-309
50%
LI-311
50%
AI-301
<0.6%
AI-302
<0.6%
第五章间歇反应
一、工艺流程简介
间歇反应过程在精细化工、制药、催化剂制备、染料中间体等行业应用广泛。
本间歇反应的物料特性差异大;多硫化钠需要通过反应制备;反应属放热过程,由于二硫化碳的饱和蒸汽压随温度上升而迅猛上升,冷却操作不当会发生剧烈爆炸;反应过程中有主副反应的竞争,必须设法抑制副反应,然而主反应的活化能较高,又期望较高的反应温度。
如此多种因素交织在一起,使本间歇反应具有典型代表意义。
在叙述工艺过程之前必须说明,选择某公司有机厂的硫化促进剂间歇反应岗位为参照啊,目的在于使本仿真培训软件更具有工业背景,但并不拘泥于该流程的全部真实情况。
为了使软件通用性更强,对某些细节作了适当的变通处理和简化。
有机厂缩合反应的产物是橡胶硫化促进剂,它能大大加快橡胶硫化的速度。
硫化作用能使橡胶的高分子结构变成网状,从而使橡胶的抗拉断力、抗氧化性、耐磨性等加强。
它和促进剂D合用适用于棕色橡胶的硫化,与促进剂M合用适用于浅色橡胶硫化。
本间歇反应岗位包括了备料工序和缩合工序。
基本原料为四种:
硫化钠(Na2S)、硫磺(S)、邻硝基氯苯(C6H4ClNO2)及二硫化碳(CS2)。
备料工序包括多硫化钠制备与沉淀,二硫化碳计量,邻氯苯计量。
1.多硫化钠制备反应
此反应是将硫磺(S)、硫化钠(Na2S)和水混合,以蒸汽加热、搅拌,在常压开口容器中反应,得到多硫化钠溶液。
反应时有副反应发生,此副反应在加热接近沸腾时才会有显著的反应速度。
因此,多硫化钠制备温度不得超过85℃。
多硫化钠的含硫量以指数n表示。
实验表明,硫指数较高时,促进剂的缩合反应产率提高。
但当n增至4时,产率趋于定值。
此外,当硫指数过高时,缩合反应中析出游离硫的量增加,容易在蛇管和夹套传热面上结晶而影响传热,使反应过程中压力难于控制。
所以硫指数应取适中值。
a)二硫化碳计量
二硫化碳易燃易爆,不溶于水,相对密度大于水。
因此,可以采用水封隔绝空气保障安全。
同时还能利用水压将储罐中的二硫化碳压至高位槽。
高位槽具有夹套水冷系统。
b)邻硝基氯苯计量
邻硝基氯苯熔点为31.5℃,不溶于水,常温下呈固体状态。
为了便于管道输送和计量,必须将其熔化,并保存于具有夹套蒸汽加热的储罐中。
计量时,利用压缩空气将液态邻硝基氯苯压至高位槽,高位槽也具有夹套保温系统。
c)缩合反应工序
缩合工序历经下料、加热升温、冷却控制、保温、出料及反应釜清洗阶段。
邻硝基氯苯、多硫化钠和二硫化碳在反应釜中经夹套蒸汽加入适度的热量后,将发生复杂的化学反应,产生促进剂M的钠盐及其副产物。
缩合反应不是一步合成,实践证明还伴有副反应发生。
缩合速率的大小与这个副反应有密切关系。
当硫指数较低时,反应是向副反应方向进行。
主反应的活化能高于副反应,因此提高反应温度有利于主反应的进行。
但在本反应中若升温过快、过高,将可能造成不可遏制的爆炸而产生危险事故。
保温阶段之目的是尽可能多地获得所期望的产物。
为了最大限度地减少副产物的生产,必须保持较高的反应釜温度。
操作员应经常注意釜内压力和稳定,当温度压力有所下降时,应向夹套内通入适当蒸汽以保持原有的釜温、釜压。
缩合反应历经保温阶段后,接着利用蒸汽压力将缩合釜内的料液压入下道工序。
出料完毕,用蒸汽吹洗反应釜,为下一批作业做好准备。
本间歇反应岗位操作即告完成。
二、工艺流程图(CAD绘制)
三、开车步骤
1.准备工作
检查各开关、手动阀门是否关闭。
2.多硫化钠制备
1打开硫化碱阀HV-1,向多硫化钠制备反应器R1注入硫化碱,使液位H-1升至0.4m,关闭阀HV-1。
2打开熔融硫阀HV-2,向多硫化钠制备反应器R1注入硫磺,液位H-1升至0.8m,关闭HV-2。
3打开水阀HV-3,使多硫化钠制备反应器R1液位H-1升至1.2m,关闭HV-3。
4开启多硫化钠制备反应器搅拌电机M1开关M01。
5打开多硫化钠制备反应器R1蒸汽加热阀HV-4,使温度T1上升至81~84℃(升温需要一定时间,可利用此时间差完成其他操作)。
保持搅拌5分钟(实际为3小时)。
注意当反应温度T1超过85℃时将使副反应加强,此种情况会报警扣分。
6开启多硫化钠输送泵M3的电机开关M03,将多硫化钠料液全部打入沉淀槽F1,静置5分钟(实际为4小时)备用。
3.邻硝基氯苯计量备料
1检查并确认通大气泄压阀V6是否关闭。
2检查并确认邻硝基氯苯计量槽F4下料阀V12是否关闭。
3打开上料阀HV-7。
4开启并调整压缩空气进气阀HV-5。
观察邻硝基氯苯计量槽F4液位H-5逐渐上升,且邻硝基氯苯储罐液位H-4略有下降,直至计量槽液位H-5达到1.2m。
由于计量槽装有溢流管,液位一旦达到此高度将不再上升。
但如果不及时关闭HV-7,则储罐液位H-4会继续下降。
注意储罐液位下降过多,将被认为操作失误而扣分。
5压料完毕,关闭HV-7及HV-5。
打开泄压阀V6。
如果忘记打开V6,会被认为操作失误而扣分。
4.二硫化碳计量备料
1检查并确认通水池的泄压阀V8是否关闭。
2检查并确认二硫化碳计量槽F5下料阀V14是否关闭。
3打开上料阀HV-10。
4开启并调整自来水阀HV-9,使二硫化碳计量槽F5液位H-7上升。
此时二硫化碳储罐液位H-6略有下降。
直至计量槽液位H-7达到1.4m。
由于计量槽装有溢流管,液位将不再上升。
但若不及时关闭HV-10,则储罐液位H-6会继续下降,此种情况会被认为操作失误而扣分。
5压料完毕,关闭阀门HV-10及HV-9。
打开泄压阀V8。
如果忘记打开泄压阀V8会被认为操作失误而扣分。
5.像缩合反应釜加入三种物料
1检查并确认反应釜R2放空阀HV-21是否开启,否则会引起计量槽下料不畅。
2检查并确认反应釜R2进料阀V15是否打开。
3打开管道冷却水阀V13约5秒,使下料管冷却后关闭V13。
4打开二硫化碳计量槽F5下料阀V14,观察计量槽液位因高位势差下降,直至液位下降至0.0m,即关闭V14。
5再次开启冷却水阀V13约5秒,将管道中残余的二硫化碳冲洗入反应釜,关V13。
6开启管路蒸汽加热阀V11约5秒,使下料管预热,关闭V11。
7打开邻硝基氯苯计量槽F4下料阀V12,观察液位指示仪,当液位H-5下降至0.0m,即关V12。
8再次开启管路蒸汽加热阀V11约5秒。
将管道中残余的邻硝基氯苯冲洗干净,即关闭