项目管理产品制造标准化.docx
《项目管理产品制造标准化.docx》由会员分享,可在线阅读,更多相关《项目管理产品制造标准化.docx(10页珍藏版)》请在冰豆网上搜索。
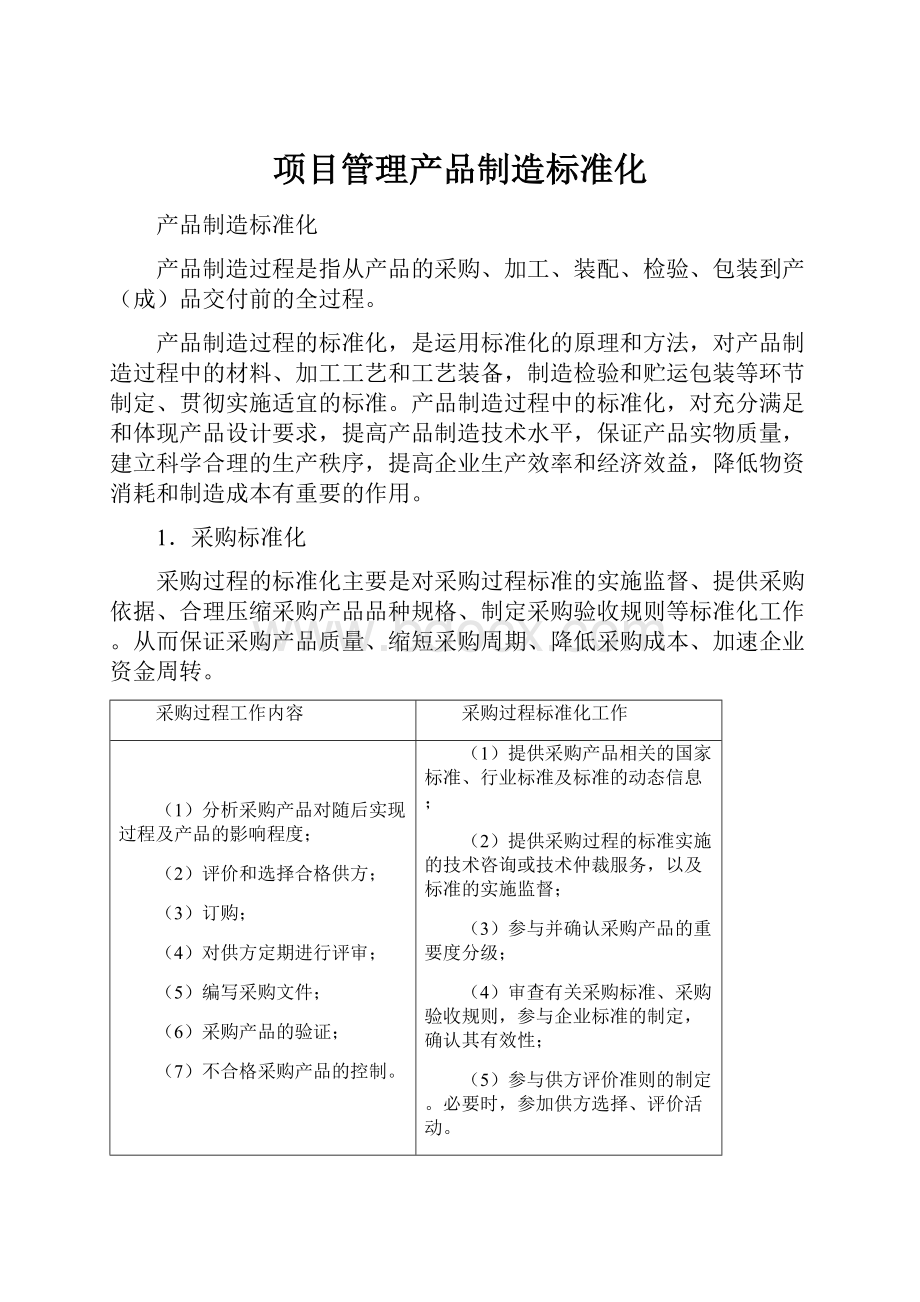
项目管理产品制造标准化
产品制造标准化
产品制造过程是指从产品的采购、加工、装配、检验、包装到产(成)品交付前的全过程。
产品制造过程的标准化,是运用标准化的原理和方法,对产品制造过程中的材料、加工工艺和工艺装备,制造检验和贮运包装等环节制定、贯彻实施适宜的标准。
产品制造过程中的标准化,对充分满足和体现产品设计要求,提高产品制造技术水平,保证产品实物质量,建立科学合理的生产秩序,提高企业生产效率和经济效益,降低物资消耗和制造成本有重要的作用。
1.采购标准化
采购过程的标准化主要是对采购过程标准的实施监督、提供采购依据、合理压缩采购产品品种规格、制定采购验收规则等标准化工作。
从而保证采购产品质量、缩短采购周期、降低采购成本、加速企业资金周转。
采购过程工作内容
采购过程标准化工作
(1)分析采购产品对随后实现过程及产品的影响程度;
(2)评价和选择合格供方;
(3)订购;
(4)对供方定期进行评审;
(5)编写采购文件;
(6)采购产品的验证;
(7)不合格采购产品的控制。
(1)提供采购产品相关的国家标准、行业标准及标准的动态信息;
(2)提供采购过程的标准实施的技术咨询或技术仲裁服务,以及标准的实施监督;
(3)参与并确认采购产品的重要度分级;
(4)审查有关采购标准、采购验收规则,参与企业标准的制定,确认其有效性;
(5)参与供方评价准则的制定。
必要时,参加供方选择、评价活动。
(6)开展原材料、外购件的标准化工作
1)选用标准原材料:
优先选用符合国家和行业标准的原材料
2)制定原材料企业标准:
①将选定的原材料国家和行业标准替代为材料企业标准;
②无现行可寻的原材料,制定采购规范或企业标准。
3)外购件标准化工作按1)、2)进行。
2.工艺标准化
工艺是指根据产品图样和有关技术文件的要求,将原材料、半成品加工成产品的方法,是企业进行生产准备、加工操作、技术检验和生产管理的依据。
工艺标准化是运用标准化的原理和方法,对有重复性等特征的工艺文件、工艺要素、工艺过程进行统一、简化、协调、优化及标准的制定和贯彻实施的活动。
工艺概念
标准化内容
(1)工艺术语、符号、代号
贯彻执行国家和行业标准规定的工艺术语、符号、代号。
如:
工艺方法、工艺要素、工艺文件、工艺装备与工件装夹、典型表面加工及装配等。
(2)工艺文件
1)工艺文件完整性:
企业可参照JB/T9165.1《工艺文件完整性》标准确定生产制造中应具备的成套工艺文件;
2)工艺文件格式:
企业可参照JB/T9165.2《工艺规程格式》和JB/T9165.3《管理用工艺文件格式》标准制定本企业各类工艺文件的格式要求;
3)工艺文件管理:
企业可根据JB/T9165.7《工艺管理导则 工艺文件标准化审查》和JB/T9169.8《工艺管理导则 工艺文件修改》制定相应的企业管理标准。
(3)工艺要素
1)工艺参数:
分析确定影响工艺质量的参数项目,根据它们之间的联系,进行优化和定量。
2)工艺尺寸:
直接导致工艺尺寸多样化的工艺结构要素(如圆角、倒角、退刀槽的尺寸规格)、工艺性要素(如中心孔、起吊孔、螺孔的中间加工的过渡尺寸)和工艺余量要制定统一的企业标准,减少批件的品种、规格和边角余料的损失,压缩切削加工工具、夹具、量具的尺寸规格,提高工艺准备和工艺操作的效率。
3)工艺余量:
制定通用工艺余量标准,首先要考虑专业工艺(如铸造、锻造、电镀、热处理、表面处理)对加工对象的工艺性保证要求,再考虑专业自身的条件、技术经济指标和其它专业工艺性要求。
4)工艺规程典型化:
①零件工艺典型化—组织零件加工族,按零件的几何形状相似性、尺寸相似性和工艺相似性筛选分类而形成零件的典型工艺规程。
②零件工序典型化—对零件加工中某个工序的设备条件、工艺参数、操作方法等加以规范。
③工艺方法典型化—根据企业产品特点,将某种工艺条件、参数、操作方法、工艺装备等典型化,以通用工艺守则的形式固定下来。
(4)工艺管理
1)工艺工作程序规范化:
企业参照JB/T9169.2《工艺管理导则 产品工艺工作程序》,制定本企业工艺方案、工艺路线、工艺规程、工艺装备、小批试制中的工艺验证、工艺准备及验证工作的检查总结和工艺整顿对工艺规程、工艺装备中存在问题等的工艺工作程序标准。
2)生产现场工艺管理:
①工序质量控制—编制工序质量因素分析、工序能力测定和工序控制的技术规范;
②现场定置管理—企业可参照JB/T9169.10《工艺管理导则 生产现场工艺管理》制定生产现场人、物和场地结合状态的分类与标志,工作和生产场地、处理区管理、工艺器具等管理办法。
3.工艺装备标准化
工艺装备是产品制造过程中所用的各种工具如刀具、量具、夹具、模具、辅具、钳工工具和工位器具的总称。
开展工艺装备标准化应贯彻实施国家、行业的工艺装备标准,尽量采用外购的标准工艺装备;合理压缩工艺装备的品种规格,扩大工艺装备的通用化,减少专用工艺装备;对重复使用的工艺装备制定企业标准;企业工艺装备的设计、制造、验证、保管、使用都应制定相应的管理标准,使之有序化、规范化。
工艺装备
标准化内容
(1)刀具
1)企业常用的标准刀具品种、规格、图样汇集成册。
2)企业常的,无国家和行业标准可循的刀具,制定为本企业的刀具标准。
(2)量检具
1)合理选择标准的量检具,尽量不使用专用量检具。
2)企业常用的专用量检具,可作为企业的通用量检具汇集成册,供工艺设计选用。
(3)夹具
1)通用夹具已经标准化,企业可以外购。
2)专用夹具:
①制定夹具典型结构标准;
②制定夹虎基础件、定位件、导向件、紧固件、夹紧件和操作件标准。
3)根据工艺需要,对可重复使用的通用夹具零部件和少数专用件组合成易于组装和拆卸的各种组织夹具制定统一规则。
(4)模具
1)采用国家标准和行业标准,并按具体情况对标准进行细化和补充。
2)采用模具的标准件和通用件设计各类模具使用的通用模架。
3)编制典型模具图册和模具通用零部件图册。
(5)机床辅具
1)采用已有的标准机床辅具,补充制定企业特殊的辅具标准。
2)编制辅具生产图册。
(6)钳工工具
1)采用已有标准和补充制定企业标准。
2)编制通用钳工工具明细表,规定工具的名称、代号、使用范围等。
(7)工位器具
1)企业对经常重复使用的工位器具的结构和尺寸进行优化统一,并制定企业标准。
2)编制工位器具图册。
(8)工艺装备管理
1)工艺装备设计管理标准化:
参照JB/T9167《工艺装备设计管理导则》。
2)工艺装备制造、使用管理标准化:
参见JB/T5060《工艺装备制造与使用管理导则》
4.质量检验标准化
质量检验就是对产品的一个或多个质量特性进行观察、测量、试验,并将结果和规定的质量要求进行比较,以确定每项质量特性合格情况的检查活动。
质量检验标准化是对质量检验的依据、检验手段、检验数据处理和传递等所实施的标准化管理活动。
质量检验分类
质量检验要求
质量检验标准化工作
(1)进货检验
1)确定进货检验依据:
有关的国家标准、行业标准;企业标准、检验规程;图样、检验指导书;合同或技术协议等。
2)确定检验项目:
检验项目的编号;检验项目的名称;检验项目技术要求的条款编号;检验项目试验方法的条款编号等。
3)确定接收准则:
根据不合格严重性分级,确定采购产品检验判定规则。
1)确定进货检验的管理内容与职责要求。
2)确定进货检验的方式或类型。
3)确认进货检验的依据。
4)确定检验项目及要求。
5)确定抽样标准的选择。
6)确定判定规则。
7)规定进货检验程序。
(2)进台验证
1)查验提供的质量凭证:
核查物品的名称、规格、编号(批号)、数量、交付单位、日期、产品合格证书或质量合格证明等。
2)确认检验依据的正确性、有效性:
检验依据的技术文件,一般有现行的国家标准、行业标准、企业标准、采购合同或协议等。
3)查验检验凭证(报告、记录等)的有效性:
查验凭证检验数据填写的完整性、产品数量、编号和实物的一致性,确认签章手续是否剂备等。
4)需要进行复核检验的,应确定进行复检机构,复检后应出具检验报告。
(3)过程检验
1)部件(装)检查,是指对部件(装)的所需的零件进行合格查验和确认,然后按产品图样或工艺规程等对该部件(装)进行检验,检验合格发放工序合格证,方可转入总装或入库。
2)工序间检验,是指按产品图样、工艺规程、作业指导书及相关的技术协议等,对工序实行首检、巡检和终检的方式。
3)特殊工序检验,是指按工艺规程、作业指导书及工序监控要求,对特殊工序进行监控和巡检,重点监视工艺参数的控制,并作监控记录,检验合格后方可转序。
4)关键工序检验,是指按检验指导书、产品图样等技术文件,对关键工序进行检验,检验合格方可转序。
1)确定过程检验的管理内容与职责要求。
2)确定过程检验的类型和检验要求。
3)确认过程检验的依据及检验依据的有效性。
4)确定过程检验规则。
5)规定检验记录的要求。
6)确定各类检验的工作程序要求。
(4)最终检验
对成批生产的产品、试销产品、特殊订货的产品、超过贮存周期的产品、改制、修理的产品和“三包”产品等,进行出厂、交付检验。
1)明确最终检验的管理部门的职责和要求。
2)确定产品最终检验的对象。
3)检验依据:
①企业明示采用的国家标准、行业标准;
②企业产品标准(或产品技术条件、技术规范等)。
③技术协议(或技术合同)。
4)检验项目:
确定检验顺序,检验规则和复检规则。
5.产品包装标准化
产品包装标准化是以保证产品安全和质量为目的,对产品的包装容器、包装尺寸、包装材料、包装技术要求及试验方法等制定和实施标准的活动。
产品包装要求
产品包装标准化工作内容
1)根据产品结构、质量特性、精度和易损性,产品需经手的运输环境、气候、期限及装卸条件及顾客(用户)对包装的要求,确定采用的包装技术(如防潮、防锈、防震等)、包装材料(包括辅助材料、辅助物)和包装标志。
2)产品外包装应具有足够的机械强度,能承受运输过程中的最大摇摆、振动、挤压、撞击、摔跌等,并保证产品不受损坏。
3)包装标志字迹要清楚、牢固耐久,保证在运输、交付及运输到目的地的全过程保持清晰可辨。
4)设计并完成包装图样和包装设计文件、工艺文件及必要的产品包装标准或规范。
5)进行必要的包装试验验证,考核包装设计和工艺质量是否满足规定的要求。
1)包装分级:
规定分级档次:
不同等级对包装试验项目和定量值的要求;不同等级对包装容器(结构、材质、尺寸)的要求;不同等级对包装材料和包装方法的要求等。
2)包装技术要求:
包括包装环境、包装材料、包装容器、包装要求及包装标志等。
3)包装件运输:
根据可能遇到的流通环境条件,规定运输、装卸的要求。
4)包装件的贮存:
应规定贮存场所、贮存条件、贮存方式(单放、堆放等)、贮存期限等。
5)包装件的试验方法:
一般按产品的性质、运输条件等规定应做的试验项目。
6)包装件的检验规则:
根据包装件的性质(危险品、一般货物)确定检验方案、判定规则。
7)包装标志:
主要指产品外包装上的图形符号与简单的文字说明,也是国际物流中心的统一规定。
一般都有现行的国家标准和行业标准,企业应贯彻执行。
8)包装容器:
确定包装容器的结构、尺寸、材料、材质和性能要求,辅助物的结构尺寸,包装标志的内容、位置、制作要求,包装试验的项目要求和所执行的标准等。
9)包装工艺:
一般应包括内包装和外包装工艺。
如:
防锈工艺规程、涂漆工艺规程、产品包装程序和验收要求等。
还应规定包装场所的环境条件、使用工具、材料、方法、程序、试验方法和验收要求等。