第5章模压成型工艺汇编.docx
《第5章模压成型工艺汇编.docx》由会员分享,可在线阅读,更多相关《第5章模压成型工艺汇编.docx(23页珍藏版)》请在冰豆网上搜索。
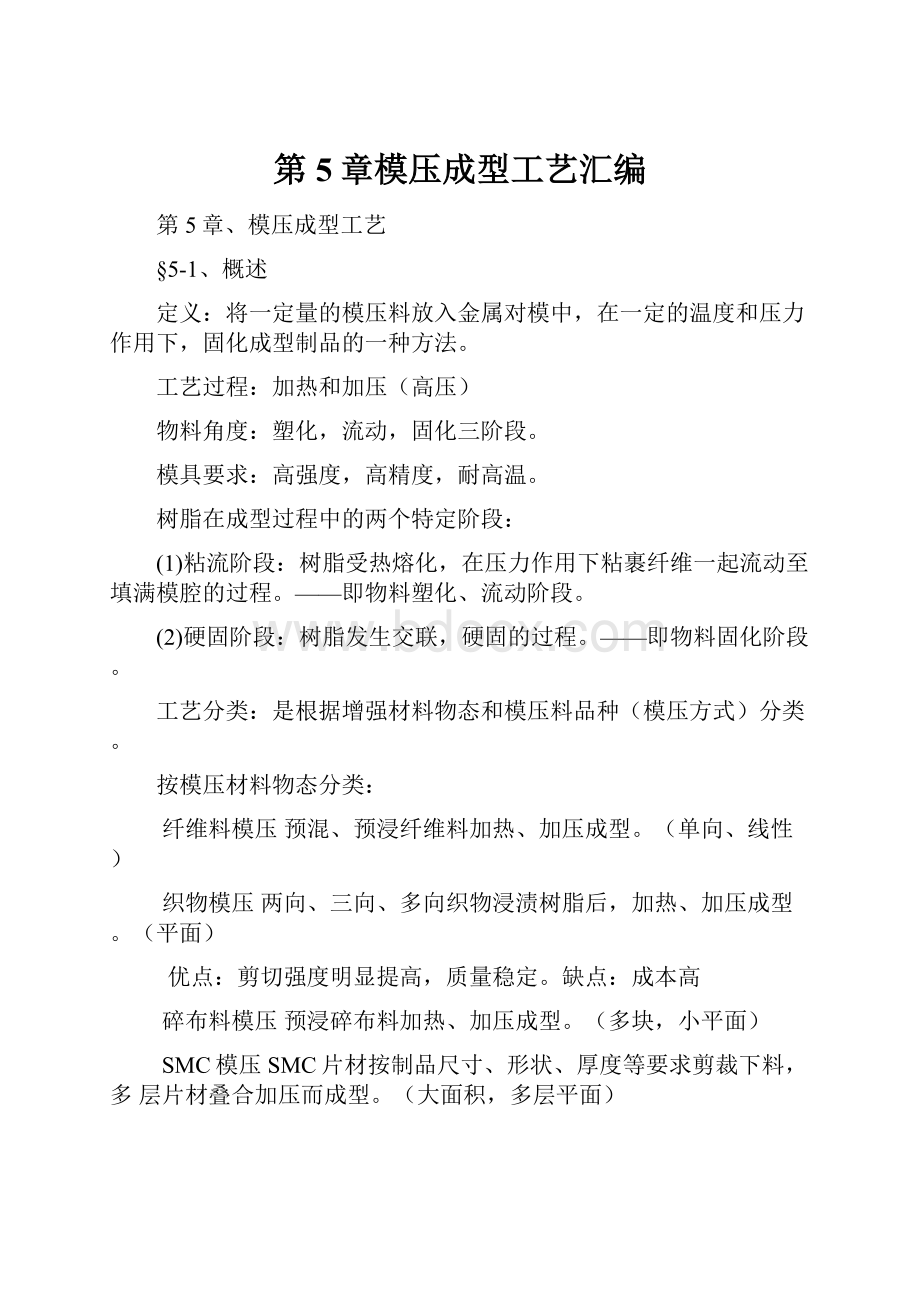
第5章模压成型工艺汇编
第5章、模压成型工艺
§5-1、概述
定义:
将一定量的模压料放入金属对模中,在一定的温度和压力作用下,固化成型制品的一种方法。
工艺过程:
加热和加压(高压)
物料角度:
塑化,流动,固化三阶段。
模具要求:
高强度,高精度,耐高温。
树脂在成型过程中的两个特定阶段:
(1)粘流阶段:
树脂受热熔化,在压力作用下粘裹纤维一起流动至填满模腔的过程。
——即物料塑化、流动阶段。
(2)硬固阶段:
树脂发生交联,硬固的过程。
——即物料固化阶段。
工艺分类:
是根据增强材料物态和模压料品种(模压方式)分类。
按模压材料物态分类:
纤维料模压预混、预浸纤维料加热、加压成型。
(单向、线性)
织物模压两向、三向、多向织物浸渍树脂后,加热、加压成型。
(平面)
优点:
剪切强度明显提高,质量稳定。
缺点:
成本高
碎布料模压预浸碎布料加热、加压成型。
(多块,小平面)
SMC模压SMC片材按制品尺寸、形状、厚度等要求剪裁下料,多层片材叠合加压而成型。
(大面积,多层平面)
预成型坯模压短切纤维制成与制品形状和尺寸相似的预成型坯,放入模中,倒入树脂混合物,压力成型。
(大型、深型、高强、异型、体形、均厚度制品)
按模压成型方式分类:
层压预浸胶布或毡剪成所需形状,层叠后放入金属模内,压制成型。
缠绕预浸的玻纤或布带,缠绕在一定模型上,加热、加压。
(管材)
定向铺设单向预浸料(纤维或无维布)沿制品主应力方向铺设,然后模压成型。
§5-2、模压料
树脂、增强材料、辅助剂构成模压料的三大块。
§5-2-1、原料
1、树脂:
酚醛型(镁、氨酚醛,改性聚乙烯醇缩丁醛),环氧型(634,648,F-46),环氧酚醛型(也可列为酚醛型),聚酯型。
2、增强材料:
纤维型(玻纤,碳纤,尼龙纤),(形状有纤维状,短切毡,布或绳)
3、辅助材料:
稀释剂,玻纤表面处理剂,填料,脱模剂及颜料等。
目的:
使模压料具有良好的工艺性和制品的特殊要求。
(1)稀释剂:
丙酮、乙醇(非活性)
用途:
降低树脂粘度,改进树脂浸渍性能,有活性与非活性之分。
(2)表面处理剂:
改进树脂与增强材料的粘结及树脂——纤维界面状态。
种类:
对环氧及酚醛模压料,常用的玻纤表面处理剂有KH-550,用量为纯树脂重量的1%,不宜过多或过少。
(3)粉状填料:
提高模压料的流动性,降低制品收缩率,提高制品表面的光泽度、质量和均匀性及赋予制品以某种特殊性能。
MoS2可提高制品的耐磨性。
§5-2-2、模压料的制备
分为预混法和预浸法两种。
1、短切纤维模压料制备
(1)预混法(手混和机混)
工艺流程:
树脂调配
玻璃纤维热处理切割混合撕松烘干模压料
机混法步骤:
a、180℃处理40~60min(350℃处理10~15min),除去玻纤表面石蜡浸润剂,残油量<0.3%。
b、切割成30~50mm长度,疏松。
c、按树脂配方配成胶液,用工业酒精调配胶液密度在1.0g/cm3
d、按纤维:
树脂=55:
45(质量比)在捏合机内充分混合。
(图4-1)
e、捏合的预混料,逐渐加入撕松机撕松。
(图4-2)
f、撕松的预混料在网格屏上晾置。
g、80℃烘房中烘20~30min,进一步除去水分和挥发物。
h、装入塑料袋中备用。
(2)预浸法
a、纤维从导架导出,经集束环经入胶槽浸渍。
b、浸渍后,过割胶辊进入第一、二级烘箱烘干。
第一级温度110~120℃,第二级温度150~160℃。
c、牵引辊牵出、切割。
三个主要工艺参数:
树脂溶液比重,环氧酚醛(6:
4),d=1.00~1.025
烘箱温度
牵引速度
2、模压料质量控制
模压料呈散乱状态,纤维无一定方向,模压时流动性好,适合制造形状复杂的小型制品。
因此,控制好质量,对模压特性及制品性能有很大影响。
(1)三项质量控制指标
树脂含量,挥发物含量及不溶性树脂含量。
几种典型模压料质量指标
模压料
指标
预浸料
预混料
机械法
手工法
机械法
手工法
镁酚醛
环氧酚醛
环氧酚醛
镁酚醛
616酚醛
616酚醛
树脂含量
40±5
45±3
42±4
40~50
40±4
35±5
挥发物含量
<3
<1.5
<2
2~3.5
2~4
<4
不溶性树脂含量
<8
<4
<5
5~10
<15
3~20
(2)指标控制方法
取模压料1~1.5g,称重G1(精确至0.001g),放入105±2℃的烘箱内烘30min,取出后在干燥器内冷却至室温,称重G2。
挥发物含量:
V%=(G1-G2)/G1×100%
取模压料1~1.5g,称重(精确至0.001g),将其浸入丙酮溶液中浸泡15min,取出放入105±2℃的烘箱内烘30min,在干燥器内冷却至室温,称重G3。
称重后将料放入550~600℃炉中灼烧10~20min,将树脂全部烧尽,取出后在干燥器内冷却至室温,再称重G4。
树脂含量:
R=[G1(1-V)-G4]/G1(1-V)×100%
不溶性树脂含量:
C=(G3-G4)/[G1(1-V)-G4]×100%
测量时要三份平行实验,如模压料中含有无机填料,上述公式需加以修正。
(3)影响模压料质量的几个主要因素
a、树脂溶液粘度
降低粘度:
有利于树脂对纤维的浸透和减少纤维强度损失。
过低:
导致纤维离析,影响树脂对纤维的粘附。
用加入溶剂调整密度来实现,用密度控制粘度。
酚醛预混料树脂胶液粘度控制在1.00~1.025g/cm3。
b、纤维长度
过长易结团,机混法:
长度20~40mm,手混法:
长度30~50mm。
c、烘干条件
一般快速固化酚醛型预混料(镁酚醛)烘干温度为80℃,烘干20~30min。
慢速固化酚醛型预混料(氨酚醛)烘干温度为80℃,烘干50~70min。
环氧酚醛型预混料的烘干温度为80℃,烘干20~40min。
d、浸渍时间
在确保纤维均匀浸透情况下,应尽可能缩短时间。
3、模压料的工艺性及其影响因素
工艺性主要为模压料的流动性、收缩率和压缩性。
(1)流动性
流动性好:
成型温度与压力较低,复杂制品。
流动性差:
成型温度与压力提高,不易复杂制品。
热固性聚合物熔体粘度:
η=f(γ,T,α)
γ:
剪切速率,T:
温度,α:
固化度。
流动度:
Φ=1/η•Ae-at
A,a:
常数,t:
加热时间。
外部影响因素:
流动度与时间、温度、压力的相互关系。
塑化
加热初期流动度增大
固化前期流动度相对稳定
固化期及后流动度速降——交联
温度升高流动度增大——塑化
温度续升流动度快降——交联
压力升高流动度增大——提高剪切变形,剪切速率
压力续升流动度增缓——功耗速增
综合评估温度最重要
Arrhenius方程:
η=A•eHη/RT
图4-3,4-4
解决方法:
模压温度Tk,塑化,交联的交界温度。
内部影响因素:
a、高聚物分子量,链结构,分子量分布
相同温度下:
分子量大、链段多,分子链重心难移——粘度大。
η0=AMw3.4
η0:
剪切速率较低时的表观粘度
A:
经验常数
Mw:
重均分子量
解决方法:
低分子量溶剂或增塑剂降低粘度。
分子量分布对粘度影响:
剪切速率小,分布宽高于分布窄。
剪切速率大,分布宽低于分布窄。
温度敏感性:
分布宽,温敏低;分布窄,温敏高。
图4-5,4-6
b、模压料质量指标与组分
挥发份对流动性影响:
挥发份增加,流动性增加
挥发份过高,成型时树脂大量流失
挥发份过低,流动性下降,成型难
c、增强材料形态、含量
线性好于平面性,短比长好,短长混用。
d、合理的压制制度,模具的结构、形状及光洁度都会有影响
流动性过大的,合模时产生溢料,局部聚胶、贫胶和纤维分布不均。
(2)模压料的收缩性
定义:
脱模后尺寸会减小是模压料的固有特性。
Q:
收缩率
a、实际收缩率:
模具空腔或制品在压制温度下的尺寸与制品在室温下的尺寸之间的差值。
Q实=(a-b)/b×100%
a:
模具空腔或制品在压制温度下的尺寸mm
b:
制品在室温下的尺寸mm
b、计算收缩率:
在室温下模具空腔尺寸与制品尺寸之间的差值。
Q计=(c-b)/b×100%
c:
模具空腔在室温下的尺寸mm,设计模具时的重要数据。
c、收缩的主要原因:
热收缩和结构(化学)收缩。
热收缩:
模压制品的线膨胀系数比模具材料大(塑料线膨胀系数25~120×10-6℃-1,钢材线膨胀系数11×10-6℃-1)
因此制品脱模冷却后收缩率大于模具收缩率。
制品小,模具大(与墙地砖热压后膨胀正好相反)表4-3
结构收缩:
固化过程中缩聚反应产生交联。
一般高强度短纤维模压制品收缩率在0~0.3%。
d、影响收缩的因素
※原材料的影响
树脂与添加物的种类与含量
※模具结构和制品形状的影响
不溢式与溢式模具,模具刚度,薄壁制品
※成型工艺条件
温度制度,压力制度
见表4-4,4-5
(3)模压料的压缩性
压缩比:
模压料和模压制品二者比容的比值。
压缩比=模压料(或坯体)的比容/制品比容>1
SMC,BMC压缩比较小。
纤维状模压料压缩比达6~10(蓬松)
处理方法:
预成型纤维
§5-3、SMC成型工艺
§5-3-1、SMC的特点与种类
1、SMC的特点
SMC——片状模塑料(SheetingMoldingCompound)
1953年,美国Rubber发明不饱和聚酯的化学增稠。
1960年,德国Bayer公司实现SMC工业化生产。
定义:
SMC是不饱和聚酯树脂及辅助剂、填料所成树脂糊浸渍短玻纤粗纱或玻毡,并在两边用聚乙烯或聚丙烯包覆后形成的片状模压成型材料。
特点:
(1)干法生产FRP制品一种中间材料,它具有独特的增稠作用,即浸渍玻纤时体系粘度低,浸渍后粘度急剧上升,达到稳定。
(2)重现性好。
(3)操作处理方便,增稠剂化学增稠,使SMC处于不粘手状态,避免一般预成型的粘滞性。
(4)作业环境清洁。
(5)SMC能使玻纤同树脂一起流动,可成型带有肋条和凸部的制品。
(6)可压截面变化不大的大型薄壁制品。
(7)制品表面光洁度高。
(8)生产率高,成型周期短,成本低,易机械化、自动化。
2、SMC的种类
(1)BMC——块状模塑料(BulkMoldingCompound)
相近:
与SMC组成近似。
用途:
压制和挤出成型。
区别:
BMC中纤维含量低,纤维短,填料含量大,强度低,小型制品。
(2)TMC——厚片状模塑料
相近:
组成与制作与SMC类似。
区别:
比SMC厚的多(0.63cm:
5.08cm),浸透性更好,成本更低。
(3)结构SMC——纤维形态和分布不同的SMC
SMC—R——纤维不规则分布
SMC—C——连续纤维单向分布
SMC—D——不连续纤维定向分布
SMC—C/R,SMC—D/R区别:
纤维含量高(Wt达30~70%,多为50%以上),树脂为高反应性间苯二甲酸聚酯树脂,强度大大提高。
(4)高强SMC,即HMC和XMC
HMC——少填料,多短纤,少树脂的片状模塑料。
XMC——少填料,多连续定向玻纤,少树脂的片状模塑料。
代替钢材,铝材。
(5)LS—SMC(LomShrinkage—SMC)——低收缩SMC
尺寸精度高,表面光洁度高。
(6)ITP—SMC(InterpeneteratingThickingProcess—SMC)——渗透增稠片状模塑料
室温熟化,高刚性,耐冲击,尺寸稳定。
(7)高弹SMC,耐热SMC,耐燃SMC
§5-3-2、SMC的组分及性能
不饱和聚酯树脂及其助剂
SMC三大员玻纤
填料
1、不饱和聚酯树脂及其助剂
(1)不饱和聚酯树脂的工艺要求
a、低粘度,便于浸渍
b、易同增稠剂反应
c、固化迅速
e、热强度高
牌号,不同的用途决定。
(2)交联剂
机理:
与聚酯发生共聚反应,使聚酯大分子通过交联单体自聚的“链桥”而交联固化改善树脂固化后的性能。
工艺上使树脂糊初始粘度降低。
种类:
苯乙烯,甲基丙烯酸甲酯,乙烯基甲苯,邻苯二甲酸二丙烯酯。
253厂的促进剂E。
(3)引发剂
贮存,操作安全,室温不分解,制得SMC贮存期长。
如引发剂H(白色糊状),凝胶时间25℃,12~20min。
引发剂L(无色透明液体),凝胶时间25℃,12~22min。
实例:
促进剂与引发剂配方使用。
(4)阻聚剂
阻止不饱和聚酯在室温下的交联聚合,必须在引发剂和所用树脂的临界温度内不失效,但又不极大影响固化、成型周期。
PBO、HQ、CL—PBO、TBC……
(5)增稠剂
贮存和成型SMC时要求坯体粘度较高,目的是满足模压要求和使制品的收缩率降至最低。
工艺要求:
SMC粘度由很低迅速增高,达熟化粘度并长期稳定。
控制SMC生产到模压制品全过程各阶段的粘度变化。
图4-7
a、增稠剂选择原则:
制备SMC时,粘度低树脂对玻纤、填料的充分浸渍
此后粘度迅速升高贮运、模压
增稠坯料迅速充满模腔树脂、纤维不离析
增稠后粘度,贮存期内保证模压
生产中稳定的重现性
b、增稠剂的品种及使用:
ⅡA族金属氧化物或氢氧化物
混合增稠剂效果更理想
过量MgO加入引起制品自我潮解,耐水性下降
c、影响增稠效果的因素:
※聚酯树脂酸值
酸度越高,粘度变化越大,图4-10
253厂树脂从16~32变化,实际以mgKOH/g表示酸值
※增稠剂活性
碘吸附值表示活性
※微量水分
0.1~0.8%微量水迅速增稠(初期)
>1.0%则不如不加水的快(初期)
因此必须对填料、增稠剂、低收缩添加剂与玻纤使用前测定含水量
※温度的影响
温度升高,增稠加快,
图4-12
d、增稠机理
第一阶段:
酸碱反应,生成碱式盐。
O
…COOH+MgO…C—O—MgOH
O
熟化
…COOH+Mg(OH)2…C—O—MgOH+H2O
Ca再进行脱水
…COOMeOH+HOOC……COOMeOOC…+H2O
…COOMeOH+HOMeOOC……COOMeOMeOOC…+H2O
第二阶段:
以配位键形成络合物
O
归于—C—基存在剩余自由电子,顾可形成配位键,而配位键在压力时可消除。
…C—O—Me—
OO
—Me—O—C…稠化、熟化
O
…C—O—Me—
(6)低收缩添加剂
克服聚酯树脂固化时将发生的7~10%体积收缩,并使表面光滑,无裂缝,收缩量低。
a、机理:
聚酯树脂发生热膨胀,交联中产生固化收缩,在固化收缩时,低收缩剂热膨胀力就阻止收缩。
稍迟于树脂固化收缩,而其收缩时,周围已固化。
低收缩效果图见4-13
b、选择
PVC聚氯乙烯,PS聚苯乙烯,PE聚乙烯,PVAc聚醋酸乙烯酯,添加量5%左右。
(7)无机填料
a、分类
氧化硅及硅酸盐类石棉,滑石粉,瓷土,氧化硅,硅藻土,火山灰等
碳酸盐类碳酸钙
硫酸盐类硫酸钡,硫酸钙
氧化物类氢氧化铝
b、性能选择
细度:
325目(44μm)。
大:
分离、沉淀,小:
吸油量高的填料加入量少。
油吸附量:
被亚麻仁油润湿的质量百分比,一般要求要求填料具有较低的油吸附量。
触变性:
物料受到外力作用(如剪切力、振荡)时,粘度显著下降,除去此力时,物料又逐渐恢复到原来粘度的一种物理现象。
不宜选用灵敏度大的填料。
c、填料对制品成本影响
单位体积成本为:
Rc=Km+K-(Km-Kc)·Xc
Km,Kc:
树脂糊、填料的单位体积成本。
K:
加填料的操作成本。
Xc:
填料的体积分数。
不加填料的成本Rc=Km
Rc的意义:
加填料的操作成本小于这部分填料替代树脂糊而降低的成本。
则K-(Km-Kc)<0才能盈利,K-(Km-Kc)>0亏损。
Km与Kc差值越大,K越小,无亏损点Xc0越小,经济效益高。
Xc还与填料密度有关:
Xc=1/[1+ρc/ρm·(1-yc)/yc]
ρc,ρm:
填料、树脂的密度。
yc:
填料的质量分数。
ρc/ρm越小:
Xc越大。
(8)内脱模剂
机理:
是一些熔点比普通模制温度稍低的化合物,它与液态树脂相容,与固化后的树脂不相容,固化时从内部逸到模具界面形成障碍,从而脱模。
国内用硬脂酸锌,熔点133℃
日本用硬脂酸亚铅
欧、美用硬脂酸钙,熔点150℃,硬脂酸镁,熔点145℃。
(9)增强材料
短切玻纤、毡,石棉纤维,麻,有机纤维。
玻纤性能:
易切割、分散,浸渍性好,抗静电,流动性好,强度高。
§5-3-3、SMC生产工艺
1、生产过程
见图4-18
(1)树脂糊制备
批混法(国内),连续计量混合法(国外)。
批混法:
树脂和除增稠剂外的各组分计量后先混合,再通过计量和混合泵加入MgO增稠剂。
粘度控制指标:
树脂原始粘度
3.5Pa·S
引发剂、单体加入后
8Pa·S
填料加入后
15Pa·S
增稠剂加入后
30Pa·S
增稠剂加入30min后(加入玻纤成片)
50Pa·S
连续计量混合法:
将树脂与其他部分分为两部分单独制备,计量后进入静态混合器,均匀后再成型。
(2)玻纤切割与沉降
粗纱切割速度80~130m/min
防静电,玻纤分布均匀。
(3)浸渍、压实
反复挤压捏合,达到充分混合和充分浸渍。
(4)收卷
收卷装置的转速、转矩随卷径的变化规律:
M=A·1/n=T·v/2πn
r=B·1/n=v/2π·1/n
T:
收卷张力
v:
收卷线速度
r:
片料卷绕半径
n:
收卷转速
M:
转矩
(5)熟化与存放
熟化使粘度达到模压粘度范围并稳定后才能交付使用。
存放要防止苯乙烯挥发,非渗透性薄膜密封包装。
2、配方
满足制品性能要求,考虑可模压性。
均匀性(制品性能),流动性(可模压性)
关键:
选择树脂与填料的搭配。
吸收能力高的填料与吸收能力低的填料的合理搭配,解决均匀性和流动性的有效途径。
3、工艺参数
(1)一般参数(见书P96)
(2)参数计算
上糊量与纤维输送量
切割机转速和纱团数
刮板间隙
所有参数均应根据实际情况选择适当系数。
§5-4、模压工艺
模压工艺流程见书P97,图4-26。
§5-4-1、压制前准备
1、预热和预成型
压制前对模压料预先加热处理称为预热。
目的:
改善模压料的工艺性能
增加流动性
便于装模
降低制品收缩率
降低成型压力
预热方法:
加热板预热
红外线预热
电烘箱预热(热鼓风)80~100℃
远红外预热60~80℃
高频预热
t<30min
将模压料在室温下预先压成与制品相似的形状称为预成型。
可提高生产率。
2、装料量估算
装料量=(ρ模压料+V制品)×103~105%
(1)简化计算法
复杂制品简化成一系列几何形状进行估算。
(2)密度比较法:
其它材料比较
ω模压=ω材/ρ·ρ模压(1+α)
ρ:
密度
ω:
质量
α:
3~5%
(3)铸型比较法:
与密度比较法近似
3、脱模剂选用
内脱模剂,外脱模剂
外脱模剂多用机油、油酸、硬脂酸用于酚醛型模压料。
硅酯或有机硅用于环氧及环氧酚醛型模压料。
§5-4-2、模压工艺参数
温度制度、压力制度
1、温度制度
包括:
装模温度,升温速度,最高模压温度和恒温、降温以及固化温度。
(1)装模温度:
镁酚醛150~170℃,氨酚醛、酚醛环氧型80~90℃,结构复杂及大型制品装模温度在室温~90℃。
(2)升温速度
一般采用10~30℃/h,氨酚醛小尺寸制品1~2℃/min。
(3)最高模压温度
主要依树脂放热曲线来确定,如:
氨酚醛80℃开始缩聚,140~150℃最为激烈,180℃固化反应逐渐完成,应将模压温度定在180℃左右。
工艺上温度的确定:
升温速率趋于零的峰值温度,先选取稍大于树脂固化温度,再通过工艺——性能试验最后制定合理的模压制度。
(4)保温时间
指在成型压力和模压温度下保温的时间。
作用是使制品固化完全和消除内应力。
取决于模压料固化反应时间,不稳定导热时间。
影响因素:
模压料品种,制品结构尺寸,加热装置的热效率及环境温度等。
书中列举了几种典型模压料的保温时间,见表4-14。
(5)后固化处理
目的是提高制品固化反应程度,又称老化过程。
温度过高或时间过长反而使制品性能下降。
2、压力制度
(1)成型压力
取决于两个因素:
填压料的种类及质量指标
制品结构形状尺寸
由工艺——性能试验确定。
成型压力是用单位压力表示的。
单位压力定义:
制品在水平投影方向上单位面积所承受的力P单,选用压力时需知这几个参数。
压机最大压力:
T,KN(1KN=0.1吨力)
表压:
P表,MPa
最大允许表压:
P最大,MPa
制品水平投影面积:
f制品,cm2
压机柱塞截面积:
F柱塞,cm2
压机效率系数:
k
P单·f制品——制品承受总压
P表
P最大/T——最大允许表压与最大压力关系
k·P表·F柱塞=P单·f制品
T=9.8×10-2P最大·F柱塞
P表=P单·f制品·P最大×9.8/T×10-2
(2)加压时机
合理选择加压时机是保证制品质量的关键之一。
加压过早、过迟的缺陷。
确定加压时机的三种方法:
a、经验,树脂拉丝时
b、温度指示,近凝胶温度(DSC测定)
c、在大量气体放出之前
(3)排气
防起泡、分层等。
图4-33表示了压制过程压机行程的变化过程。
§5-4-3、典型模压工艺与制品
1、典型模压工艺
快速、慢速两种,由模压料类型决定。
书中列举的快、慢速成型工艺的实例。
2、模压制品常见缺陷分析
这是工艺学必须学会解决的问题。
见书P104~105