PCB钻铣控制系统教程资料.docx
《PCB钻铣控制系统教程资料.docx》由会员分享,可在线阅读,更多相关《PCB钻铣控制系统教程资料.docx(50页珍藏版)》请在冰豆网上搜索。
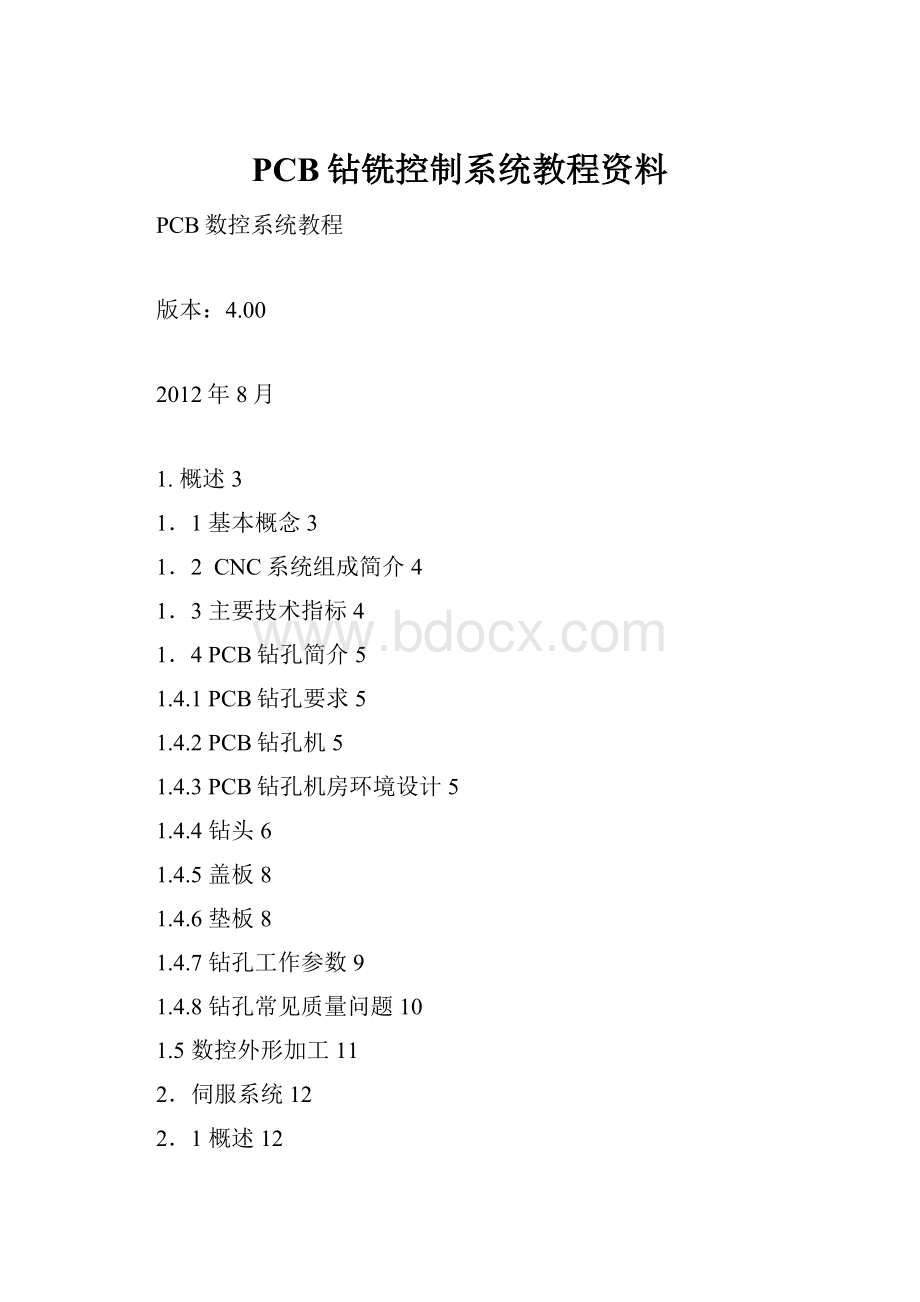
PCB钻铣控制系统教程资料
PCB数控系统教程
版本:
4.00
2012年8月
1.概述3
1.1基本概念3
1.2CNC系统组成简介4
1.3主要技术指标4
1.4PCB钻孔简介5
1.4.1PCB钻孔要求5
1.4.2PCB钻孔机5
1.4.3PCB钻孔机房环境设计5
1.4.4钻头6
1.4.5盖板8
1.4.6垫板8
1.4.7钻孔工作参数9
1.4.8钻孔常见质量问题10
1.5数控外形加工11
2.伺服系统12
2.1概述12
2.2伺服系统的检测装置13
2.3伺服电机13
2.3.1松下MINASA系列主要参数14
2.3.2安川Σ-II系列主要参数14
2.4主轴驱动系统14
2.4.1主轴15
2.4.2变频器15
3.数据采集卡17
3.1概述17
3.2MT73001卡说明17
4.运动控制卡17
4.1概述17
4.2主要参数18
4.3参数输入方法19
5.机床调试20
5.1线路检查20
5.2通电检测20
5.3轴运动调试20
5.4IO测试21
5.5工作行程设置21
5.6刀库位置校准,刀具更换测试21
5.7刀具检测21
5.8海德汉开放式电子尺调节22
5.10保护功能:
23
5.11精度检测24
6.钻铣文件格式24
6.1Excellon格式24
6.2CAM软件自动生成钻孔文件26
6.2.1DOS版Protel生成钻孔文件26
6.2.2PADS2000生成钻孔文件26
6.2.3PROTEL99生成钻孔文件27
6.3钻孔文件示例27
6.4外形文件示例28
7维修保养29
7.1 数控系统维修工作的基本条件29
7.2 现场维修29
7.3 维修调试后的技术处理32
7.4MantatCNC系统故障分析32
7.5维护保养34
7.6系统文件的备份34
8 用户新机安装调试34
1.概述
1.1基本概念
数控(NC),即数字控制(NumericalControl)的简称,是一种自动控制技术,是用数字化信号对机床的运动及加工过程进行控制的一种技术。
计算机数控(ComputerizedNumericalControl─CNC),是以计算机为核心的数控系统。
目前所说的数控,一般均指计算机数控。
数控机床就是装备了数控系统的机床。
PCB数控机床是专门用于印制电路板(PCB)钻孔和外形加工的特种机床。
插补即知道了一个曲线的类型、起点、终点、速度等信息后,在起点和终点之间进行数据点的密化(轨迹控制)。
例如PCB铣床锣外形就用到插补技术。
大多数机器零件的形状,一般都是由一些简单的几何元素(直线、圆弧等)构成。
在数控机床上加工直线或圆弧,实质上是数控装置根据有关的信息指令进行“数据密化”的工作。
例如加工一段圆弧,已知条件仅是该圆弧的起点A和终点B的坐标,圆心O的坐标及半径R,要想把圆弧段
光滑地描绘出来,就必须把圆弧段A、B之间各点的坐标值计算出来:
把这些点填补到A、B之间,通常把这种“填补空白”的“数据密化”工作称为插补。
把计算插补点的运算称为插补运算。
把实现插补运算的装置叫作插补器。
刀具补偿刀具补偿包括刀具半径补偿(亦称为刀具偏移运算)和刀具长度补偿。
所谓刀具半径补偿,就是具有这种功能的数控装置能使刀具中心自动从零件实际轮廓上偏离一个指定的刀具半径值(补偿量),并使刀具中心在这一被补偿的轨迹上运动,从而把工件加工成图纸上要求的轮廓形状。
当数控装置具有刀具半径补偿功能时,在程序编制时不考虑加工所用的刀具半径,直接按照零件的实际轮廓形状来编制控制介质的程序指令,而在加工时,把实际采用的刀具半径值输入,系统便自动地算出每个程序段在各坐标方向的补偿量。
所谓刀具长度补偿,就是具有这种功能的数控装置能使刀具在轴向(z方向)上的实际位移量大于或小于程序给定值。
刀具长度尺寸的补偿方法通常是通过设在控制面板上的刀具长度补偿拨码盘或刀补开关进行。
PCB数控机床特点:
1)高精度,定位精度0.005,重复精度0.003,钻孔精度0.05。
2)高速度,移动速度20m/min~50m/min。
3)多轴运动控制,控制轴数4~10轴。
4)高速主轴,通常主轴最高转速50000~180000r/min,甚至高250000r/min。
5)自动化程度高,如自动换刀,刀长度/直径自动检测,断刀自动检测等等,进口的高档机床还有自动上下料等等功能。
1.2基于PC的控制系统组成简介
说明:
该数控系统基于工业电脑IPC,操作系统可用Windows98,Windows2000,WindowsXP。
运动控制部分采用进口专用运动控制卡,可自动进行轨迹控制、点位控制、Jog运动,可实现S形或梯形加减速运动。
数据采集卡用于开关量输入输出,以及数模转换(D/A)输出(用于变频器调速)。
1.3主要技术指标
1.定位精度和重复精度
所谓定位精度就是指实际位置与指令位置的一致程度。
不一致量表现为误差。
被控制
的机床坐标的误差,也包括驱动此坐标自匀控制系统的误差在内。
对指定坐标用“+”“-”
数字及允许误差值表示,例如对指定的某长度,表示成:
x坐标值,±ε。
定位精度和定位时间是数控装置(特别是点位控制系统)的两个基本要求。
定位精度关系到工件质量,定位时间关系到生产率,两者往往互相矛盾。
应当首先满足定位精度的要求,而后尽量缩短定位时间。
重复精度是在同一条件下,用相同的方法,重复进行同一动作时,控制对象位置的一致程度,亦称为精密度。
2.可靠性
机器的可靠性通常用<平均无故障工作时间>和<平均修复时间>来衡量
平均无故障工作时间=总工作时间/总故障次数
平均修复时间=总故障停机时间/总故障次数
3.轴线性移动速度和加速度
移动速度是指单个轴线性移动最高速度,通常用米每分钟(m/min)来表示。
加速度用m/s2为单位,也用g为单位:
1g=9.8m/s2
4.钻孔精度
机床实际钻孔准确度,通常用高倍CCD摄像头扫描来检测。
5.加工面积
指机床实际可加工的最大区域(不包含刀具库区域)。
1.4PCB钻孔简介
1.4.1PCB钻孔要求
钻孔是PCB制作过程中的一道重要工序,加工要求:
1.高精度普通板<0.08mm,高精度板<0.05mm
2.高速度钻孔速度平均每分钟>200次,要求机器要有较高的移动速度和加减速,并采用叠层钻孔以提高生产效率
3.高品质孔壁质量要好,披锋少
1.4.2PCB钻孔机
钻孔机的型式及配备功能种类非常多以下评估重点
1)轴数和产量有直接关系
2)有效钻板尺寸
3)钻孔机台面选择振动小强度平整好的材质
4)主轴(Spindle)
5)钻盘自动更换钻头及钻头数
6)压力脚
7)XY及Z轴传动及尺寸精准度XY独立移动
8)集尘系统搭配压力脚排屑良好且冷却钻头功能
9)分步钻孔的能力
10)断针侦测
1.4.3PCB钻孔机房环境设计
PCB钻孔机房设计必须考虑以下环境因素:
1)温度湿度控制
2)干净的环境
3)地板的承受重量
4)接地
5)外界震动干扰
1.4.4钻头
钻孔作业中会使用的物料有钻针(DrillBit),垫板(Back-upboard),盖板(Entryboard)等,如下图:
钻头品质对钻孔质量有直接的影响,以下将就其材料外型构及管理简述之
1.钻针材料钻针组成材料主要有三:
a.硬度高耐磨性强的碳化钨(TungstenCarbide,WC)。
b.耐冲击及硬度不错的钴(Cobalt)。
c.有机黏着剂.三种粉末按比例均匀混合之后,于精密控制的焚炉中于高温中在模子中烧结(Sinter)而成。
耐磨性和硬度是钻针评估的重点,其合金粒子愈细能提高硬度以及适合钻小孔,通常其合金粒子小于1micron。
2.外型结构钻针之外形结构可分成三部份,见图,即钻尖(drillpoint)退屑槽(或退刃槽Flute)及握柄(handle,shank)
钻尖部份(DrillPoint),如下图所示:
(1)钻尖角(PointAngle)
(2)第一钻尖面(PrimaryFace)及角
(3)第二钻尖面(Secondaryface)及角
(4)横刃(Chiseledge)
(5)刃筋(Margin)
钻尖是由两个窄长的第一钻尖面及两个呈三角形钩状的第二钻尖面所构成的,此四面会合于钻尖点,在中央会合处形成两条短刃称为横刃(Chiseledge),是最先碰触板材之处,此横刃在压力及旋转下即先行定位而钻入stack中,第一尖面的两外侧各有一突出之方形带片称为刃筋(Margin),此刃筋一直随着钻体部份盘旋而上,为钻针与孔壁的接触部份.而刃筋与刃唇交接处之直角刃角(Corner)对孔壁的品质非常重要,钻尖部份介于第一尖面与第二尖面之间有长刃,两长刃在与两横刃在中间部份相会而形成突出之点是为尖点,此两长刃所形成的夹角称钻尖角(Pointangle),钻纸质之酚醛树脂基板时因所受阻力较少,其钻尖角约为90~110,钻FR4的玻纤板时则尖角需稍钝为115~135,最常见者为130者第一尖面与长刃之水平面所呈之夹面角约为15称为第一尖面角(PrimaryFaceAngle),而第二尖面角则约为30,另有横刃与刃唇所形成的夹角称为横刃角(cheiselEdgeAngle)。
退屑槽(Flute)
钻针的结构是由实体与退屑的空槽二者所组成实体之最外缘上是刃筋,使钻针实体部份与孔壁之间保持一小间隙以减少发热其盘旋退屑槽(Flute)侧断面上与水平所成的旋角称为螺旋角(HelixorFluteAngle),此螺旋角度小时,螺纹较稀少,路程近退屑快,但因废屑退出以及钻针之进入所受阻力较大,容易升温造成尖部积屑积热,形成树脂之软化而在孔壁上形成胶渣(smear)此螺旋角大时钻针的进入及退屑所受之磨擦阻力较小而不易发热,但退料太慢。
握柄(Shank)
被Spindle夹具夹住的部份,为节省材料有用不锈钢的钻针整体外形有4种形状:
(1)钻部与握柄一样粗细的StraightShank,
(2)钻部比主干粗的称为CommonShank
(3)钻部大于握柄的大孔钻针
(4)粗细渐近式钻小孔钻针
3.钻头检测与重磨
1)检查方法20~40倍实体显微镜检查。
2)钻头的重磨要用专用磨钻头机。
1.4.5盖板
1.盖板的作用
1)定位
2)散热
3)减少毛头
4)保护铜面
2.材料种类
1)复合材料-是用木浆纤维或纸材,配合酚醛树脂当成黏着剂热压而成的其材质与单面板之基材相似此种材料最便宜.
2)铝箔压合材料─是用薄的铝箔压合在上下两层中间填去脂及去化学品的纯木屑.
3)铝合金板─5~30mil,各种不同合金组成,价格最贵。
4)普通铝片—通常在0.15-0.25mm厚度。
是目前普遍使用的。
上述材料依各厂之产品层次,环境及管理.成本考量做最适当的选择.其品质标准必须:
表面平滑,板子平整,没有杂质,油脂,散热要好.
1.4.6垫板
1.垫板的作用
1)保护机床台面
2)防止出口性毛头
3)保证钻透PCB板
1.材料种类
1)复合材料-其制造法与纸质基板类似但以木屑为基础再混合含酸或盐类的黏着剂高温高压下压合硬化成为一体而硬度很高的板子.
2)酚醛树脂板phenolic─价格比上述的合板要贵一些也就是一般单面板的基材.
4)铝箔压合板─与盖板同。
5)VBU垫板──是指VentedBackUp垫板上下两面铝箔中层为折曲同质的纯铝箔空气可以自由流通其间一如石棉浪一样。
6)纸板,通常用厚度2.5mm,是目前普遍使用的。
垫板的选择一样依各厂条件来评估.其重点在:
不含有机油脂,屑够软不伤孔壁,表面够硬,板厚均匀,平整等。
1.4.7钻孔工作参数
进刀速度(Feed)和刀具旋转速度(Speed)是最重要的参数。
1.进刀速度:
每分钟钻入的深度。
2.旋转速度:
每分钟旋转的圈数。
2.回刀速度:
刀具抬起的速度。
4.步数(啄钻):
即一个孔分几次下钻,大钻头通常采用这个方法。
5.深度:
下钻的深度,确保钻透工件。
参数的设定一般原则:
1)钻头直径越小需要转速越高。
2)直径1mm左右的钻头进刀最快,更大或者更小的钻头进刀要慢些。
3)大钻头(大于3.175)要分步下钻。
4)重磨多次的钻头转速、进刀要慢些。
1.4.8钻孔常见质量问题
现象
原因
解决办法
孔大
1)钻孔文件错误
2)钻头使用错误
3)钻头不良
4)主轴偏摆大
5)断针补孔导致
1)使用正确的钻孔文件
2)更换正确的钻头
3)检测钻头品质
4)检修主轴
5)检查补孔作业条件和方法
孔小
1)钻孔文件错误
2)钻头使用错误
3)钻头重磨次数太多
1)使用正确的钻孔文件
2)更换正确的钻头
3)确认钻头重磨次数的范围
多孔,少孔
1)钻孔文件错误
2)断针补孔导致
3)操作失误
4)电脑病毒
5)机床控制软件有缺陷
1)使用正确的钻孔文件
2)检查补孔作业条件
3)进行操作训练
4)查杀电脑病毒
5)升级软件
偏孔
1)工作参数设置不当
2)主轴偏摆大
3)脏物导致
4)叠层太多
5)压力脚步平
6)铝片不平整
7)钻头重磨次数太多
8)主轴夹头内有赃物
9)机床精度故障
1)修正钻孔参数
2)检修主轴
3)清洁加工件
4)减少叠层
5)调整或更换压脚
6)更换铝片
7)更换钻头
8)清洗夹头
9)检测机床精度
披锋
1)垫板二次使用
2)钻头使用太久
3)垫板太软
1)不要重复使用垫板
2)严格控制钻头寿命
3)更换较硬的垫板
移位
1)销钉松动
2)机床零点发生偏移
1)重新上销钉
2)检查机床
钻不透
1)下限设置偏高
2)钻头太短
3)钻头崩尖
4)垫板厚度不够
1)重新设置下限值
2)更换钻头
3)检查钻头品质
4)更换合适的垫板
1.5数控外形加工
成形是最后一道工序(数控铣/冲压成型)。
1.精度外形误差<0.15mm
2.边沿要光滑
3.具有刀具直径自动补偿功能
铣的技术包括选择,走刀方向、下刀点和定位方法。
是保证铣加工精度的重要方面。
走刀方向
当铣刀切入板材时,有一个被切削面总是迎着铣刀的切削刃,而另一面总是逆着铣刀的切削刃。
前者,被加工面光洁,尺寸精度高。
主轴总是顺时针方向转动。
所以不论是主轴固定工作台运动或是工作台固定主轴运动的数控铣床,在铣印制板的外部轮廓时,要采用逆时针方向走刀。
这就是通常所说的逆铣。
定位方法和下刀点
定位方法可分为两种;一是内定位,二是外定位。
定位问题,属于机械工程的范畴。
除上述的铣垫板、销钉之外,定位方法也是很重要的,应使操作者认识。
内定位是通用的方法。
所谓内定位是选择印制板内的安装孔,插拨孔或其它非金属化孔作为定位孔。
孔的相对位置力求在对角线上并尽可能挑选大直径的孔。
实际证明:
不能使用金属化孔。
因为孔内镀层厚度的差异会改变一个孔到另一个孔配合的一致性和质量。
还有,在保证印制板定位的条件下,销钉数量愈少愈好。
下刀点和加工顺序选择的好,能使框架保持最大的强度。
选择的不好,框架变形而使印制板报废。
铣的工艺参数
用硬质合金铣刀铣印制板外形,铣刀的切削速度计算公式如下:
S=pdn/1000(m/min)
式中:
p:
PI(3.1415927)
d:
铣刀直径,mm
n;铣刀转速,r/min
与切削速度相匹配的是进给。
若进给太低,由于磨擦热使印制板材料软化甚至溶化或烧焦,堵塞铣刀的排屑槽,切削无法进行。
如果进给太快,铣刀磨损快,承受的径向负荷大,让刀量大,工作质量差,尺寸不一致。
如何判断进给的快慢呢?
要考虑下述诸项:
印制板材料,厚度,每叠块数,铁刀直径、排屑槽。
只有低于额定负载,主轴马达的转速才能保持。
负载增大,转速下降,直至铣刀折断。
有两种情况造成此结果:
一是主轴马达功率不足,二是每叠板数太多,切削负荷太大。
2.伺服系统
2.1概述
伺服驱动系统简称伺服系统(Servosystem),是指以机械的位置、速度、角度、力矩或姿态等等作为控制对象的自动控制系统。
按伺服系统调节理论,伺服系统通常可分为开环、半闭环和全闭环。
开环系统:
通常采用步进电机,没有角度和位置检测装置
半闭环系统:
采用伺服电机,通常采用旋转编码器作为角度检测装置,不具有位置检测装置
全闭环系统:
在半闭环的基础上加了位置检测装置
PCB高端钻孔通常系统XY轴采用全闭环控制,Z轴采用半闭环控制。
2.2伺服系统的检测装置
检测装置的主要作用是检测位移和速度,发送反馈信号,构成半闭环或全闭环。
常见的检测装置有光栅、磁栅、编码器等。
1.直线光栅(电子尺)
光栅是利用光的透射、反射和干涉现象制成的一种光电检测装置。
光栅有两类:
透射光栅和反射光栅。
2.旋转编码器
旋转编码器是一种旋转式测量元件,通常装在被检测的轴上,随被测轴一起旋转,可将被测轴的角位移转换成增量脉冲形式或绝对式的代码形式。
目前用的光电编码器可分为增量式和绝对式。
(1)增量式编码器按每圈发出的脉冲数来分,其输出波形有A、B、Z三相,通常采用差分输出,目的在于增加信号的传输距离和提高抗干扰能力。
若A相超前B相,对应电机作正向旋转;若B相超前A相,对应电机作反向旋转。
A、B的脉冲个数代表正、反向位移量。
Z相脉冲每一圈的固定位置产生一个脉冲,通常用来确定机床的基准点(零点)。
(2)绝对式编码器通过读取编码盘上的图案来表示轴的位置,其规格按位数来分。
2.3伺服电机
常用的伺服电动机分为四大类:
直流伺服电机、交流伺服电机、步进电机、直线电机。
目前PCB钻铣系统通常采用交流伺服。
可参阅伺服电机说明书。
伺服工作方式:
位置,速度,力矩
位置模式:
即控制电机运动精确定位到指定的位置。
通常采用输入指令脉冲的方式控制伺服运动(运动距离有脉冲个数决定),脉冲方式通常有三种,1双脉冲(正转脉冲,反转脉冲),2单脉冲(脉冲+反向),3AB正交脉冲。
双脉冲方式:
即有两路脉冲输入(CW,CCW),其中一路脉冲表示正转脉冲指令,另一路脉冲表示反转脉冲指令。
单脉冲方式:
即只有一路脉冲输入(Pulse,Dir),脉冲通道输入指令脉冲,反向通道表示正反转。
速度模式:
伺服驱动器工作在速度模式(位置控制由运动控制卡进行)。
通常用电压控制伺服电机的转速,电压范围-10V~+10V。
2.3.1松下MINASA系列主要参数
00控制方式选择:
0位置,1速度
10位置环增益,增益越高定位时间越快,位置控制模式下有效。
11速度环增益,增益越高伺服响应越快,位置和速度模式下都有效。
12速度环积分时间常数,值越小伺服响应越快,位置和速度模式下都有效。
44每转输出脉冲数,电机每转一圈从OA\OB输出的脉冲个数,通常为2500。
46,4B输入脉冲倍频分子分母。
50速度指令输入增益,可以设定电机转速和输入模拟电压之间的关系(r/min/v)。
51速度指令输入逻辑取反
52速度指令零漂调整,可以调整轴的误差为0。
2.3.2安川Σ-II系列主要参数
Pn000功能选择基本开关(详见安川说明书)
Pn100速度环增益
Pn101速度环积分时间常数
Pn102位置环增益
Pn103惯量比
Pn110自动调谐开关
Pn200位置控制指令选择开关
Pn201PG分频比,电机每转一圈从输出的脉冲个数
Pn202,Pn203输入脉冲倍频分子分母
Pn300速度指令输入增益,0.01V/额定转速,额定3000r/min,参考设置750
F001自动调谐时的刚性等级
F007保存自动调谐的结果,把测得的惯量比结果写入记忆。
F00A调整零速偏差
2.4主轴驱动系统
主轴驱动系统主要用于控制刀具旋转运动的速度和扭力,PCB数控钻铣床一般采用高频变频器来控制主轴的运动。
2.4.1主轴
PCB数控钻铣床采用的是专用高速主轴,铣床主轴最高转速在60000转/分钟,采用滚珠轴承;钻机主轴最高转速在125000转/分钟以上,采用空气轴承。
PreciseASC160主轴技术参数
机械参数
值
备注
速度范围
15000~160000r/min
安装直径
61.91mm
轴加速度
<5G
重量
3.2kg
最大钻孔直径
6.35mm
静态偏摆Staticrun-out
≦5um
动态偏摆Dynamicrun-out
≦10um
空气轴承压强
0.55Mpa–0.6Mpa(5.5–6.0bar)
空气轴承流量
<40NL/min
在标准气压下L/min
最小冷却剂流量
>1.5L/min
噪音@150000r/min
>75dBA
电参数
额定功率
0.5kW@42000r/min
电压范围
41V-215V
频率范围
250Hz–2670Hz
电流
<4.5A@160000r/min
2.4.2变频器
(1)变频器工作原理
变频器是利用电力半导体器件的通断作用将工频电源变换成另一频率的电能控制装置。
我们现在使用的变频器主要是采用交-直-交方式(VVVF变频或矢量控制变频)。
先把工频交流电源通过整流器转换成直流电源,然后再把直流电源转换成频率、电压均可控制的交流电源以控制电动机。
变频器的电路一般由整流、中间直流环节、逆变和控制四个部分组成。
整流部分为三相桥式不可控整流器,逆变部分为IGBT三相桥式逆变器,且输出为PWM波形,中间环节为滤波、直流储能和缓冲无功功率。
●组成:
变频器主要由整流(交流变直流)、滤波、再次整流(直流变交流)、制动单元、驱动单元、检测单元微处理单元等组成的。
●转速的计算
电机旋转速度单位:
r/min每分钟旋转次数,也可表示为rpm.
例如:
2极电机50Hz3000[r/min]
4极电机50Hz1500[r/min]
电机的旋转速度同频率成比例, 旋转速度近似地确决于电机的极数和频率。
n=60f/p
n:
同步速度
f:
电源频率
p:
电机极对数
由于PCB钻机用的都是2极电主轴,即电机极对数为1,所以转速计算公式可以简化为:
n=60f.
●电压频率曲线
如果仅改变频率而不改变电压,频率降低时会使电机出于过电压(过励磁),导致电机可能被烧坏。
因此变频器在改变频率的同时必须要同时改变电压。
输出频率在