封闭板成形模及冲压工艺.docx
《封闭板成形模及冲压工艺.docx》由会员分享,可在线阅读,更多相关《封闭板成形模及冲压工艺.docx(36页珍藏版)》请在冰豆网上搜索。
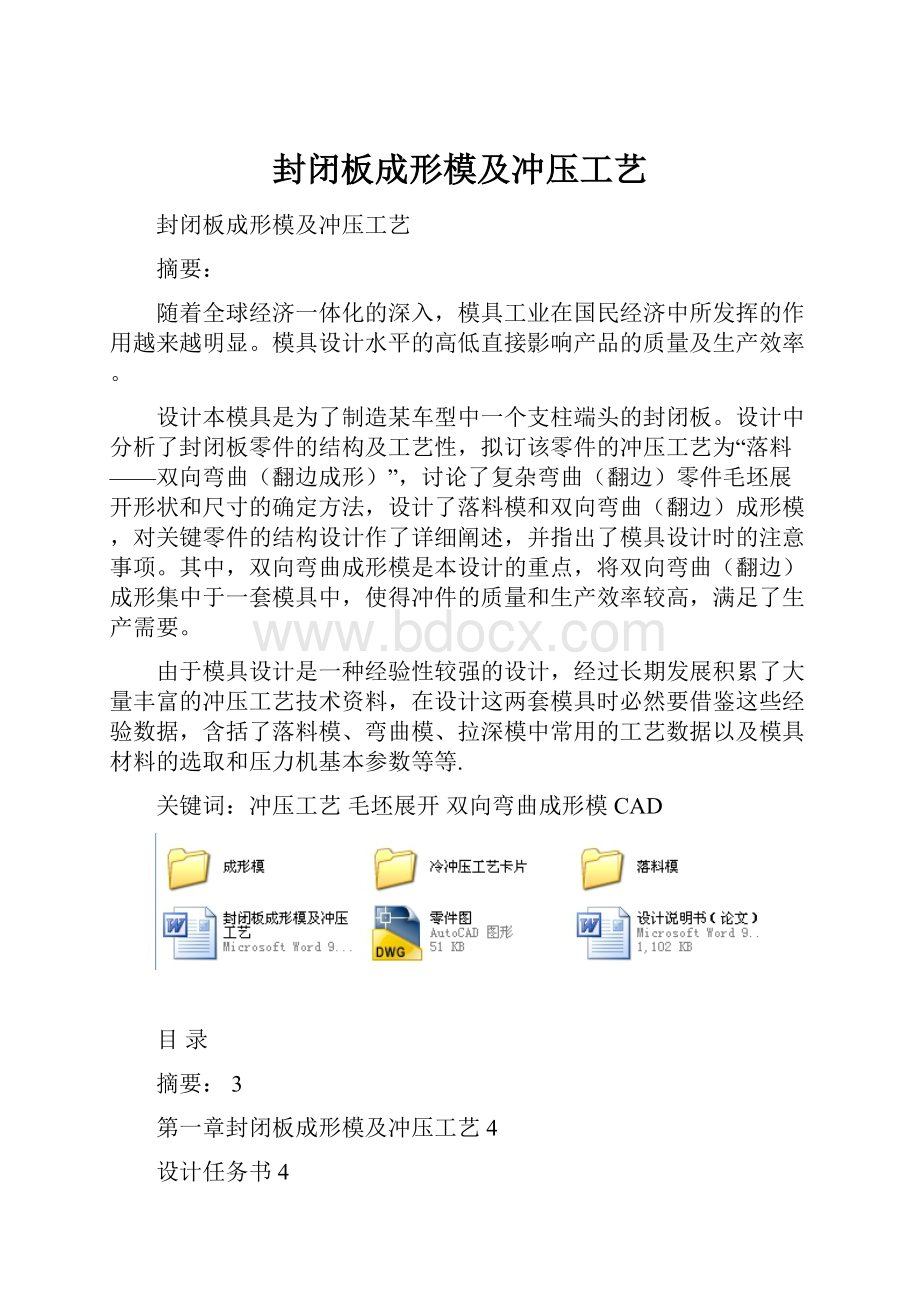
封闭板成形模及冲压工艺
封闭板成形模及冲压工艺
摘要:
随着全球经济一体化的深入,模具工业在国民经济中所发挥的作用越来越明显。
模具设计水平的高低直接影响产品的质量及生产效率。
设计本模具是为了制造某车型中一个支柱端头的封闭板。
设计中分析了封闭板零件的结构及工艺性,拟订该零件的冲压工艺为“落料——双向弯曲(翻边成形)”,讨论了复杂弯曲(翻边)零件毛坯展开形状和尺寸的确定方法,设计了落料模和双向弯曲(翻边)成形模,对关键零件的结构设计作了详细阐述,并指出了模具设计时的注意事项。
其中,双向弯曲成形模是本设计的重点,将双向弯曲(翻边)成形集中于一套模具中,使得冲件的质量和生产效率较高,满足了生产需要。
由于模具设计是一种经验性较强的设计,经过长期发展积累了大量丰富的冲压工艺技术资料,在设计这两套模具时必然要借鉴这些经验数据,含括了落料模、弯曲模、拉深模中常用的工艺数据以及模具材料的选取和压力机基本参数等等.
关键词:
冲压工艺毛坯展开双向弯曲成形模CAD
目录
摘要:
3
第一章封闭板成形模及冲压工艺4
设计任务书4
一、选题的依据及课题的意义4
二、国内外研究概况及发展趋势5
三、实验方案6
4.结论7
第二章封闭板成形模及冲压工艺设计8
2.1零件结构及工艺分析8
2.1.1零件结构8
2.1.2工艺分析9
第三章落料模设计10
3.1落料毛坯形状和尺寸的确定10
3.2弯曲成形部分的毛坯形状和尺寸的计算11
3.2.1三处翻边成形的毛坯尺寸的确定和计算12
3.3排样和裁板14
3.3.1确定排样方式并计算材料利用率14
3.3.2裁板15
3.4落料模结构设计16
3.4.1总体结构16
3.4.2导向装置17
3.4.3定位装置17
3.4.3卸料装置17
3.5落料模工艺计算17
3.5.1计算冲压力17
3.5.2确定压力中心18
3.5.3凸、凹模刃口尺寸及制造公差19
3.6工作零件的设计20
3.6.1凹模设计20
3.6.2凸模设计21
3.7卸料元件的设计21
3.7.1卸料橡胶的选用和设计21
3.7.2卸料螺钉的设计23
3.8设计其它零件并校核压力机23
3.8.1其它零件的设计及选用23
3.8.2校核压力机24
第四章双向弯曲(翻边)成形模设计25
4.1成形模结构设计25
4.1.1总体结构25
4.1.2工作原理27
4.2成型模工艺计算27
4.2.1弯曲力的计算27
4.2.2回弹量的确定29
4.2.3计算压力中心29
4.2.4工作部分尺寸计算29
4.3关键零件的设计30
4.3.1凹模设计30
4.3.2翻边凸模设计31
4.3.3弹簧的设计31
4.4设计其它零部件并校和核压力机32
4.4.1模座的选用32
4.4.2定位装置的设计33
4.4.3顶料板的设计33
4.4.4弯曲凸模的设计33
4.4.5计算闭合高度并校核压力机33
参考文献34
第一章封闭板成形模及冲压工艺
设计任务书
一、选题的依据及课题的意义
随着全球经济一体化的深入,模具工业在国民经济中所发挥的作用越来越明显,模具技术水平的高低,已成为衡量一个国家制造水平高低的重要标志,并在很大程度上决定着产品的质量、效益和新产品的开发能力。
模具设计是一种相对来讲经验性较强的设计。
设计人员在长期的工作中积累的经验和知识对模具设计起着十分重要的影响。
近年来,模具CAD/CAM技术已成功应用于模具工业,有效提高了模具设计与制造水平。
模具是现代工业生产中应用广泛的优质、高效、低耗、适应性很强的生产技术,或称成型工具、成型工装产品,是技术含量高、附加值高、使用广泛的新技术产品,是价值很高的社会财富。
由于模具生产技术的现代化,在现代工业生产中,模具已广泛应用于电动机和电器产品、电子计算机产品、仪表、家用电器产品与办公设备、汽车、军械、通用机械等产品的生产中。
模具技术水平的高低,已成为衡量一个国家制造水平高低的重要标志,并在很大程度上决定着产品的质量、效益和新产品的开发能力。
为此本人选择了“封闭板成型模及冲压工艺设计”作为毕业课题。
二、国内外研究概况及发展趋势
目前,随着汽车及轻工业的迅速发展,模具设计制造日益受到人们的广泛关注,已成为一个行业。
将高新技术应用于模具设计与制造,已成为快速制造优质模具的有力保证:
1)、CAD/DAE/CAM的广泛应用,显示了用信息技术带动和提升模具工业的优越性。
在欧美,CAD/DAE/CAM已成为模具企业普遍应用的技术。
在CAD的应用方面,已经超越了甩掉图板、二维绘图的初级阶段,目前3D设计已达到了70℅--89℅,PRO/E、UG、CIMATRON等软件的应用很普遍。
2)、为了缩短制造周期,提高市场竞争力,普遍采用高速切削加工技术。
3)、快速成型技术与快速制模技术获得普遍应用。
有SLA、SLS、FDM、LOM等各种类型的快速成型设备。
国外工业先进国家都拥有上万个模具企业与支持模具企业或为模具企业提供生产装备的企业相组成的强大的产业基础。
这是为适应社会产品工业化规模生产的重要条件和特点。
如汽车的工业化规模生产需要一大批专业性模具企业为其提供模具,同时根据汽车零件的生产技术要求,这些模具企业还配有相应的先进技术装备,包括数控和计算机数控机床、CAD/CAM系统,以及各种工艺装备。
模具的社会效益很高,是高技术含量的社会产品,其价值和价格主要取决于模具材料、加工、外购件的劳动与消耗三项直接发生的费用和模具设计与试模等技术费用,后者,是模具价值和市场价格的主要组成部分,其中一部分技术价值计入了市场价格,而更大一部分价值,则是模具用户和产品用户受惠变为社会效益。
如电视机用模,其模具费用仅为电视机产品价格的1/3000~1/5000,尽管模具的一次投资较大,但在大批量生产的每台电视机的成本中仅占极小的部分,甚至可以忽略不计,而实际上,很高的模具价值为社会所拥有,变成了社会财富。
所以设计本模具具有非常重要的现实意义。
本模具设计是为制造某车型中一个支柱端头上的封闭板,该零件左、右对称,生产中要求左、右件数量相等。
而且该零件本身属不对称的异形件,存在双向的弯曲(翻边)成形,单件冲压时存在着横向不平衡力,影响模具寿命和冲压质量,将左、右件合在一套模具上一次冲压成形,就能消除横向不平衡力,同时,也提高了冲件质量和生产效率。
据此,拟定该零件的冲压工艺为“落料——双向弯曲(翻边)成形,并设计了落料和成形两套模具。
在使用AutoCAD进行模具设计时,可以方便、快捷地调用工艺资料,达到了提高产品质量,缩短周期,降低成本,增加经济效益的目的,具有非常重要的现实意义。
因此,模具广泛应用于汽车制造业,有助于推动我国汽车行业的发展。
由于本人水平有限,本论文中必然存在不少纰漏及错误之处,敬请评阅老师批评指正。
三、实验方案
本课题要研究的是某车型中一个支柱端头上的封闭板成型模的设计。
该零件左右对称,生产中要求左、右件数量相等,生产纲领为中等批量。
由于该零件存在着双向弯曲(翻边),因此初步拟订如下两种工艺方案:
方案一:
落料→外缘弯曲(翻边)→弯曲成形
方案二:
落料→双向弯曲(翻边)
以上两种工艺方案中,前一种方案需要三副模具,若定位不好的话,很容易造成零件的不一致,影响零件质量,且工作效率低,后一种方案,成形模结构较复杂,但冲压质量好,生产效率较高,故决定采用后一种冲压工艺方案。
在设计落料模之前,首先要确定落料毛坯形状和尺寸,其中既有理论计算,也涉及到定性地估算,最终通过实验确定。
该零件虽说是左右对称件,但展开后的形状却是相同的,因此只需设计一副落料模即可,该模具采用下出料弹压卸料结构。
双向弯曲(翻边)成形模结构复杂,其关键之处在于为了保证成形的可靠,要求成形动作按设计意图顺序动作,其中上下模弹簧规格的选择起着决定性的作用。
该模具每一个冲压过程完成左、右各一件封闭板零件的成形加工,坯料靠定位板定位,这样不仅能消除横向不平衡力,同时,也提高了冲件质量和生产效率。
在选择压力机时,涉及到压力中心的确定,拟订采用一种基于AutoCAD中“工具”的压力中心确定方法,快速直接,简单方便,精度较高。
4.结论
该零件虽说是左、右对称件,且存在着双向弯曲成形,但合理安排冲压工艺,仔细进行模具设计后,其加工过程并不复杂。
通过该零件的冲压工艺和模具设计可以看出,形状复杂的弯曲(翻边)成形零件,在计算展开尺寸时,不仅需要根据书本知识进行计算,适当的经验以及对冲件工艺性的改进也是必要的另外,合理安排冲压工艺,并进行精心地设计,可最大限度地满足冲件质量和生产的要求。
在设计成形模时,要注意以下几点:
(1)凹模采用整体结构,内孔由线切割加工,使左、右对称性好,冲件质量高。
(2)合理选择上、下弹簧的弹力,保证模具顺序动作。
(3)精确调整限位圈的高度,冲压时靠其准确、快速控制模具的闭合高度。
(4)注意控制好弯曲模具与顶料板、弯曲凹模之间的间隙,并且顶料板的淬火硬度不能太高(43~48HRC),防止顶料板从中间断裂。
第二章封闭板成形模及冲压工艺设计
2.1零件结构及工艺分析
2.1.1零件结构
本课题设计的零件是某车型上支柱端头的封闭板,材料为08Al,料厚1mm,如图1所示。
零件图所示为封闭板左件,封闭板右件与其对称,生产中要求左、右件数量相等,生产纲领为中等批量。
该零件从图纸要求的尺寸和使用情况看,尺寸精度要求并不太高,外形尺寸按IT14级即可,弯曲(翻边)高度的尺寸公差还可适当放大。
图1封闭板零件图
2.1.2工艺分析
该零件从形状上看是不对称的异形件,且存在双向弯曲(或翻边)成形,就其弯曲部分看,成形并不困难,但翻边部分即三处带圆弧的转角处的成形存在一定的困难。
(1)零件图中R5mm处的翻边成形可按矩形件转角的拉深成形处理,由于底角半径r=1.5mm,所以
……………………………(2.1)
式中D——坯料直径(mm);
d——圆筒形工件直径(mm),取5×2=10mm;
h——圆筒形工件高度(mm),取10+1=11mm。
将以上数据带入(2.1)式得
=
=23.4mm。
因此最大相对高度h/D=11/23.4≈0.47,故成形并不困难,可一次拉深成形。
(2)而圆角R3.5mm处的翻边成形难度较大,属孔的翻边成形,由于其翻边半径R小于翻边高度,因此成形后此处必然拉裂,必须对其进行工艺处理,降低翻边高度。
(3)R1mm处若按拉深模型进行计算,则由于底角半径r=1.5相对于转角半径1.5(中性层半径)不可忽略,所以
………………(2.2)
式中D——坯料直径(mm);
d——圆筒形工件直径(mm),取(1+0.5)×2=3mm;
h——圆筒形工件高度(mm),取10+1=11mm;
r——底角半径(mm),取1.5mm。
将以上数据带入(2.2)式得:
=
=11.5mm
因此相对高度h/D=11/11.5≈0.95,且毛坯的相对厚度t/D=1/11.5≈0.09又较大,故其一次成形有较大的困难。
但从结构上看,其圆弧部分并不多,夹角仅为52°左右,成形时多余三角形的材料并不太多,同时上部与其相邻的直角弯曲成形部分较短,且另一边是开放的,其对多余三角形所施加的切向力并不大,即圆角部分的多余三角形材料并不是完全按纯拉深时的径向流动,相反,这里由于切向缺少材料约束而以横向流动为主,这就大大改善了材料变形情况,使其能够一次翻边成形。
当然,这使得此处的材料变形情况也变得较复杂,给毛坯展开计算带来了一定的难度。
但考虑到右上部相邻的转角开了工艺缺口,故直壁部分翻边后有一定的误差也是允许的,只要保证外形尺寸即可,这使得毛坯形状的确定还是有可能的。
第三章落料模设计
3.1落料毛坯形状和尺寸的确定
图2所示为落料毛坯展开图,其弯曲成形部分按常规的弯曲件毛坯尺寸计算方法计算即可,见图3所示。
这里着重讨论工艺分析中谈到的3处翻边成形的毛坯尺寸的确定和计算,即图2的I、II、III处,图4所示为这3处的计算简图。
图2毛坯展开图
3.2弯曲成形部分的毛坯形状和尺寸的计算
∵R/t=1.5/1=1.5,查表4-1[9],得K=0.369。
∴ρ=R+Kt…………………………………(2.3)
式中ρ——中性层半径(mm);
R——弯曲内半径,取1.5mm;
K——中性层位置系数,取0.369;
t——材料厚度,取1mm。
将以上数据带入(2.3)式,得ρ=R+Kt=1.5+0.369×1=1.869mm
L=π/180×α×ρ……………………………(2.4)
式中L——中性层展开长度(mm);
α——弯曲中心角度(º);
ρ——中性层半径(mm)。
将数据带入(2.4)式,得:
L1=π/180×α1×ρ=π/180×74×1.869=2.414mm;
L2=π/180×α2×ρ=π/180×90×1.869=2.936mm;
S1=15-(1.5+1)×Sin37o=13.495mm;
S2=74.25-1.5×Sin37o-1.5=71.847mm;
S3=10-1.5=8.5mm。
∴弯曲直壁的展开高度H=S3+L2/2=8.5+2.9/2=9.9mm;
总体展开长度
L=L1+L2+S1+S2+S3=2.414+2.936+13.495+71.847+8.5=99.192mm;
中间部分的展开长度L中=99.192-15-9.9=74.29mm。
图3弯曲成形部分的展开计算简图
3.2.1三处翻边成形的毛坯尺寸的确定和计算
(1)图4a所示为图3中Ⅰ处的展开尺寸简图,该转角具有R1mm的过渡圆弧,毛坯展开时通常是将其按盒形件转角处的拉深成形处理。
但此零件由于上段的直角弯曲段较短,且外侧缺少材料的约束,使得圆弧部分拉深时的多余三角形材料并不像纯拉深时那样全部转化为圆弧直壁,使直壁高度增加,而是在切向应力的作用下横向流动。
图4a中这种横向流动远大于径向流动,这种材料的流动导致此处的变形变得复杂,使毛坯展开的定量计算较困难,只能定性的估算,然后通过试验确定。
具体做法是:
将直角弯曲侧壁的开放边ac向右倾斜取边长为弯曲直壁的高度9.9mm,这是假设材料横向流动后a点流到了b点。
ab段长度的确定是假设R1mm对应扇形部分的材料分为两部分,一部分为宽1.37mm(按R1.5mm中性层弧长,圆弧夹角为52.4º计算)的材料全部转化为△abc部分,按面积相等原则,初步估算ab=3mm。
当然,若成形尺寸要求高的话,则ab的长度要待试模后再行修整,由于本课题对此要求不高,所以不必再进行修整。
图4翻边部分展开尺寸计算简图
(2)图4b所示为图2中Ⅱ处的展开尺寸简图。
该处的变形属圆孔翻边,对于图中圆弧半径为R3.5mm,翻边高度为9.9mm的情况,翻边成形时边缘必然开裂,故需进行工艺处理,降低该处的翻边高度,改善成形性能。
具体做法如下:
由圆孔翻边系数公式K=d/D,得:
d=KD……………………………(2.5)
式中d——翻边前毛坯孔的直径(mm);
D——翻边后孔的中性层直径,D=(3.5+0.5)×2=8mm;
K——翻边系数,取K=0.47。
将以上数据代入(2.5)式,得d=KD=0.47×8=3.76mm。
故翻边前毛坯的半径r=d/2=1.88mm。
考虑到凹模的强度,将R1.88mm的圆弧按60°夹角(R3.5mm处的圆弧的圆心角)用两条直线过渡到弯曲直边,其交线处再用半径值为9.9mm的圆弧光滑过渡,如此便确定了其展开尺寸。
(3)图4c所示为图2.2-1中Ⅲ处的毛坯展开简图。
该处的变形属盒形件拉深时转角处的变形,其计算过程较为典型。
即先按筒形件拉深变形计算出转角的圆弧半径R11.7mm,并画出圆弧,如图4c所示,然后过ab线段的中点向半径R11.7mm的圆弧引切线,并反向延伸至弯曲边的直线,交接处用R11.7mm的圆弧光滑过渡连接,即完成该处的毛坯展开。
上述毛坯展开只是初步估算,最终尺寸还要经过试模确定。
3.3排样和裁板
3.3.1确定排样方式并计算材料利用率
计算冲裁件的面积A:
充分利用AutoCAD2000计算物体质量特性的功能,依次点取“工具”(Tools)菜单“查询”(Inquiry)→“质量特性”(MassProperties),得面积A=5685mm2。
拟订两种排样方案,如下:
方案一:
直排,且无侧压装置。
(见图5)
查表2—16[3],得最小搭边值a=2mm,a1=1.5mm。
条料宽度B-△=[D+2(a1+△)+b0]
…………………………(2.6)
式中B——条料公称宽度(mm);
D——垂直于送料方向的工件尺寸,取D=15+74.29+9.9=99.19mm;
a——侧搭边值(mm);
b0——条料与导板之间的间隙,查表3—18[4],得b0=0.2mm;
△——条料宽度的公差,查表3—18[4]得△=0.6mm。
将以上数据代入(2.6)式得
B-△=[D+2(a1+△)+b0]
=[99.19+2×(2+0.6)+0.2]
=104.6
mm
进距h=57.5+9.9×2+1.5=78.8mm
∴一个进距的材料利用率η=nA/Bh=(1×5685)/(104.6×78.8)=69.0%
图5排样方案一
方案二:
对排,且无侧压装置。
(见图6)
查表3—17[4],得最小搭边值a=a1=2.5mm,D=57.5+9.9×2=77.3mm。
查表3—18[4],得b0=0.1mm,△=0.5mm。
图6排样方案二
将以上数据代入(2.6)式得:
B-△=[D+2(a1+△)+b0]
=[77.3+2×(2.5+0.5)+0.1]
=83.4
mm
进距:
h=(15+74.29+9.9)+(15+66.75-19+9.9)+2.5×2=176.84mm
∴一个进距的材料利用率η=nA/Bh=(2×5685)/(83.4×176.84)=77.1%
比较上述两方案,虽然对排比直排省料,但存在着下述问题:
如果采取送一次料冲一件的方法,即用单凸模,模具结构与直排时基本相同,模具费用也相差不大,但在冲完一行后,需要到头冲另一行,冲另一行时,条料的刚度很差,给送料造成很大的困难。
如果采取一次冲两件的方法,即用双凸模,则模具结构复杂了,模具长度增大了,因而模具费用也增加了。
而直排的模具结构简单,且与对排相比,材料的利用率相差不多,所以决定选择方案一,即有搭边的直排。
3.3.2裁板
08Al厚度为1mm,由材料手册查得规格为1×850×1800
若采用纵裁,则每板条数n1=850÷104.6=8条,余13.2mm;
每条个数n2=(1800-1.5)÷78.8=22个,余64.9mm;
每板个数n3=n1×n2=8×22=176个。
若采用横裁,则每板条数n1=1800÷104.6=17条,余21.8mm;
每条个数n2=(850-1.5)÷78.8=10个,余60.5mm;
每板个数n3=n1×n2=17×10=170个。
显然,纵裁时材料利用率高,所以决定采用纵裁。
3.4落料模结构设计
3.4.1总体结构
该零件虽说是左、右对称件,但展开后的形状却是相同的。
因此落料模只需设计1副模具即可。
模具采用导柱导向下出料式弹压卸料结构,冲出的零件通过凹模的内孔从冲床台面孔漏下,见图7。
模具的上部分由上模座7、导套5、模柄11、凸模固定板6、凸模10、卸料板15、卸料橡胶14和螺钉、销钉组成,下部分由凹模3、下模座2、导柱4以及螺钉、销钉组成。
图7落料模
3.4.2导向装置
采用模架导向,不仅能保证上、下模的导向精度,而且能提高模具的刚性、延长模具的使用寿命、使冲裁件的质量比较稳定、使模具的安装调整比较容易,因此决定采用模架作为上、下模的导向装置。
采用压入式模柄,固定段与上模座孔采用H7/m6过渡,并加骑缝销防止转动,装配后模柄轴线与上模座垂直度较好。
3.4.3定位装置
条料的送进,由两个定位销控制其方向,由一个钩形挡料销控制其进距,这种定位零件结构简单、制造方便,装在凹模上。
为此,在卸料板上与单了定位销和钩形挡料销相应的位置上加工三个通孔,工作时,可使卸料板压紧条料;为便于刃磨,在下模座上相应的位置处也加工通孔,以便于拆挡料销。
3.4.3卸料装置
由于实现外形分离的凸模装在上模,拟采用橡胶作为弹性元件的卸料装置装在上模,由卸料板、橡胶和卸料螺钉组成弹压卸料装置。
冲程时,橡胶块受压缩而积蓄能量,并使卸料板产生压力而起压料作用,冲出的落料件通过凹模的内孔从冲床台面孔漏下。
回程时,橡胶块释放能量,使卸料板产生反向推力而将废料从凸模上卸下。
在冲压时,还可压紧条料,提高冲裁质量。
3.5落料模工艺计算
3.5.1计算冲压力
由于该模具采用下出料弹压卸料结构,因此压力机在本模具的冲压过程中,除要克服冲裁力以外,还要克服卸料力、推件力。
(1)冲裁力的计算
F=Ltбb…………………………………(2.7)
式中F——冲裁力(N);
L——冲裁轮廓的总长度,
由AutoCAD“工具”→查询→面积,查得L=327mm;
t——板料厚度,取1mm;
бb——板料的抗拉强度,由《材料手册》查得бb=390MPa。
将以上数据代入(2.7)式,得F=Ltбb=327×1×390=127530N。
(2)卸料力的计算
F卸=K卸F…………………………………(2.8)
式中F卸——卸料力(N);
K卸——卸料力系数,查表2-15[3]得K卸=0.06;
F——冲裁力,F=127530N。
将以上数据代入(2.8)式,得F卸=K卸F=0.06×127530=7651.8N。
(3)推件力的计算
F推=nK推F…………………………………(2.9)
式中F推——推件力(N);
n——同时卡在凹模孔内的工件或废料片数,n=h/t,
h为凹模直刃高度(取h=5mm),t为板料厚度(取t=1mm),
∴n=h/t=5/1=5
K推——推件力系数,查表2-15[3],得K推=0.05;
F——冲裁力,F=127530N。
将以上数据代入(2.9)式,得F推=nK推F=5×0.05×127530=31882.5N。
综上,选择冲床时的总冲压力
F总=F+F卸+F推=127530+7651.8+31882.5=167064.3N。
初步选择开式双柱可倾压力机J23-25(查附录B3[3])。
3.5.2确定压力中心
压力中心是冲裁模各个冲裁力的合力作用点,在进行冲裁模设计时,必须使模柄中心线与冲模压力中心重合。
如果二者偏移量超过允许范围,滑块将承受偏心载荷,在偏心弯矩的作用下,将导致:
滑块与导轨非正常磨损,影响压力机精度和寿命;凸、模间隙不均匀,降低冲压件质量和加剧磨损,甚至碰撞和损坏零部件。
因此,准确求得压力中心是冲裁工艺设计和冲模设计的重要环节。
图8压力中心
本冲压件轮廓形状复杂,无法直接计算其压力中心,故采用基于AutoCAD2004的冲模压力中心确定方法来求其压力中心,具体做法如下:
第一步:
用AutoCAD绘出刃口的轮廓线,选定坐标系xoy如图8所示,并用“快捷工具”→“修改(Modify)"→“段线合并(join)"定义为多段线;
第二步:
用“偏移(Offset)”命令将轮廓线分别向两侧偏移极小的距离(0.05mm