生产计划管理(1).ppt
《生产计划管理(1).ppt》由会员分享,可在线阅读,更多相关《生产计划管理(1).ppt(39页珍藏版)》请在冰豆网上搜索。
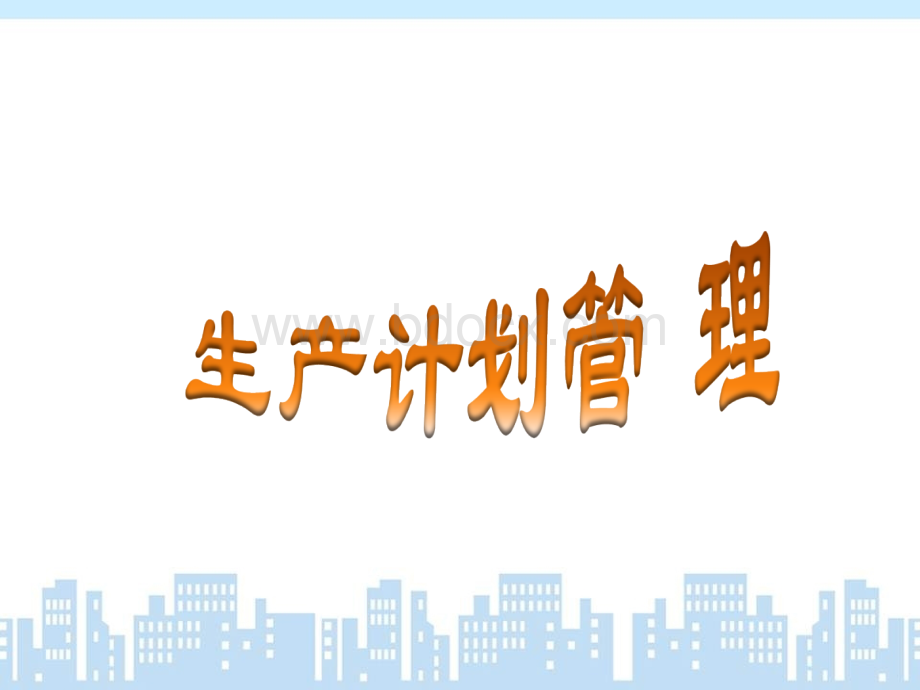
销售与生产运作流程图订单订单业务部业务部计划部计划部物料需求物料需求人力需求人力需求制造命令制造命令行政部行政部采购部采购部生产部生产部产品产品/工艺图工艺图材料表材料表生产通知单生产通知单机器负荷表机器负荷表人力记录人力记录人工、机器设人工、机器设备计划备计划材料需求计划材料需求计划工作进度计划工作进度计划前期准备工作前期准备工作5M1E5M1E生产能力核定的步骤生产能力核定的步骤生产能力(简称产能)是指生产设备在一定的时生产能力(简称产能)是指生产设备在一定的时间内所能生产的产品数量间内所能生产的产品数量产能分为正常产能和最大产能:
产能分为正常产能和最大产能:
正常产能:
指历年来生产设备的平均使用量。
正常产能:
指历年来生产设备的平均使用量。
最大产能:
指生产设备所能产出的最大产量。
最大产能:
指生产设备所能产出的最大产量。
决定产能的两个步骤决定产能的两个步骤第一步:
毛产能第一步:
毛产能设备设备名称名称可用可用机器数机器数可用可用天数天数每天每天班数班数每班每班时数时数只只/时一周毛一周毛产量总数产量总数人员人员编制编制车床车床377118850840011铣床铣床443067201刨床刨床5560168001钻床床540112001备注:
注:
以机器每周计划开7天,每天1班,每班开8小时,以车床为例:
一周毛产量总量:
50只/时X8小时X3台X7天=8400只决定产能的两个步骤决定产能的两个步骤第二步:
实际产能第二步:
实际产能设备设备名称名称只只/时一周毛产量总一周毛产量总数(双)数(双)工作时工作时间目标间目标百分比百分比合格率合格率百分比百分比一周一周实际总数(双)数(双)车床车床50840090%95%7182铣床铣床3067205745刨床刨床601680014364钻床床40112009507备注:
注:
机器生产有机器检修、保养、改机、换线、待料等时间,实际的工作时间达不到计划时间,且生产的产品有次品,因此以车床为例,总产量:
8400X90%X95%7182只没有计划和目标没有计划和目标的企业或个人的企业或个人生产任何生产任何环节的突环节的突发事件发事件客户需求发生客户需求发生重大调整或者重大调整或者更改设计更改设计计划部门计划部门采购采购原材料原材料仓库仓库冶炼冶炼车间车间半成品半成品仓库仓库铜套车间铜套车间成品成品仓库仓库运输运输出货出货重新部署重新部署重新优化重新优化重新部署重新部署重新优化重新优化立即反应立即反应,快速反馈快速反馈冷却器冷却器车间车间1.1.由于生产安排与采购脱节而造成停工待料,甚至一天由于生产安排与采购脱节而造成停工待料,甚至一天打鱼二天晒网;打鱼二天晒网;2.2.由于缺乏生产计划,无法优先安排紧急的订单生产,由于缺乏生产计划,无法优先安排紧急的订单生产,当前急需出货的没有完成,后面很长时间才出货的却当前急需出货的没有完成,后面很长时间才出货的却已经生产出来,堆积在成品仓库里;已经生产出来,堆积在成品仓库里;3.3.前后工序的半成品和材料衔接不上,需要的材料不及前后工序的半成品和材料衔接不上,需要的材料不及时来,暂时不需要的却拼命送过来;时来,暂时不需要的却拼命送过来;4.4.由于生产现场安排不合理,采取无休止的加班;由于生产现场安排不合理,采取无休止的加班;5.5.由于生产计划安排不合理,生产车间,半成品堆积象由于生产计划安排不合理,生产车间,半成品堆积象仓库,严重影响生产现场不顺畅;仓库,严重影响生产现场不顺畅;6.6.相关人员工作不能相互配合,你做你的计划,相关人员工作不能相互配合,你做你的计划,我做我的产品,造成生产计划成率低,浪费人我做我的产品,造成生产计划成率低,浪费人力物力;力物力;7.7.计划、生产及物料进度协调性不强,影响交货计划、生产及物料进度协调性不强,影响交货期,降低公司声誉;期,降低公司声誉;8.8.生产经常紊乱,品质跟着失控,造成经常性的生产经常紊乱,品质跟着失控,造成经常性的返工,经常返工又影响生产计划的执行,造成返工,经常返工又影响生产计划的执行,造成恶性循环;恶性循环;9.9.由于采购与仓管失控,造成原材料积压过多,由于采购与仓管失控,造成原材料积压过多,造成企业资金调度困难。
造成企业资金调度困难。
生产计划管理的目标在适当的时侯,在适当的时侯,以适当的价格,以适当的价格,向顾客提供适当质量的产品和向顾客提供适当质量的产品和服务。
服务。
产品是不是在交货期前越早生产出来越好?
例如:
交货期为09.8.30,结果在8.5就已经完成了。
计划的管理要素计划的管理要素设施设备管理:
设施设备管理:
保保持足够、完好和灵持足够、完好和灵活的生产运作能力活的生产运作能力物料管理:
物料管理:
以最经以最经济的方法保证及时济的方法保证及时充足的物料供应充足的物料供应人力资源管理:
人力资源管理:
有有效、高效地配置和效、高效地配置和使用人力资源使用人力资源信息管理:
信息管理:
及时准及时准确地收集、传递和确地收集、传递和处理必要的信息处理必要的信息1.1.1.1.人力是否可以充分支持,不能的话,加班、倒班是人力是否可以充分支持,不能的话,加班、倒班是人力是否可以充分支持,不能的话,加班、倒班是人力是否可以充分支持,不能的话,加班、倒班是否可以解决。
否可以解决。
否可以解决。
否可以解决。
2.2.2.2.机器设备是否准备好,其产能是否能达到预定产能,机器设备是否准备好,其产能是否能达到预定产能,机器设备是否准备好,其产能是否能达到预定产能,机器设备是否准备好,其产能是否能达到预定产能,若人力或机器无法达到,发外包是否可以解决。
若人力或机器无法达到,发外包是否可以解决。
若人力或机器无法达到,发外包是否可以解决。
若人力或机器无法达到,发外包是否可以解决。
3.3.3.3.物料是否已到位,未到位是否完全有把握在规定的物料是否已到位,未到位是否完全有把握在规定的物料是否已到位,未到位是否完全有把握在规定的物料是否已到位,未到位是否完全有把握在规定的时间到位时间到位时间到位时间到位4.4.4.4.工艺流程是否有问题,有问题能否在规定时间内解工艺流程是否有问题,有问题能否在规定时间内解工艺流程是否有问题,有问题能否在规定时间内解工艺流程是否有问题,有问题能否在规定时间内解决。
决。
决。
决。
5.5.5.5.产品的品质是否稳定,有无办法控制。
产品的品质是否稳定,有无办法控制。
产品的品质是否稳定,有无办法控制。
产品的品质是否稳定,有无办法控制。
6.6.6.6.环境是否适合生产产品环境的要求。
环境是否适合生产产品环境的要求。
环境是否适合生产产品环境的要求。
环境是否适合生产产品环境的要求。
1、生产什么东西产品名称、规格型号;2、生产多少数量或重量;3、在哪里生产部门、单位;4、要求什么时候完成生产周期、交期;生产计划排程案例生产计划排程案例理论上,排序问题的难度随着工作中心数量的增加而增大,而不理论上,排序问题的难度随着工作中心数量的增加而增大,而不是随着作业数量的增加而增大是随着作业数量的增加而增大案例:
案例:
在一周的开始,有在一周的开始,有55位顾客提交了他们的订单。
原始数据为:
位顾客提交了他们的订单。
原始数据为:
订单(以到达的顺序)订单(以到达的顺序)加工时间加工时间/天天交货期交货期/天天334422661156792如何优先安排生产计划?
如何优先安排生产计划?
AABBCCDDEE方案一方案一利用利用FCFS(FCFS(先来先服务)规则,其流先来先服务)规则,其流程时间的结果如下:
程时间的结果如下:
加工顺序加工顺序加工顺序加工顺序加工时间加工时间加工时间加工时间交货日期交货日期交货日期交货日期流程时间流程时间流程时间流程时间34261567920+3=33+4=77+2=99+6=1515+1=16总流程时间总流程时间=3+7+9+15+16=50(天)(天)平均流程时间平均流程时间=50/5=10天天将每个订单的交货日期与其流程时间相比较,发现只有博创能将每个订单的交货日期与其流程时间相比较,发现只有博创能按时交货。
其余将会延期交货,延期时间分别为按时交货。
其余将会延期交货,延期时间分别为1,2,6,14天。
每天。
每个订单平均延期(个订单平均延期(0+1+1+2+6+14)/5=4.6天。
天。
AABBCCDDEE方案二方案二利用最经济,排序结果为:
利用最经济,排序结果为:
加工顺序加工顺序加工顺序加工顺序加工时间加工时间加工时间加工时间交货日期交货日期交货日期交货日期流程时间流程时间流程时间流程时间13246257690+1=11+3=44+2=66+4=1010+6=16总流程时间总流程时间=1+4+6+10+16=37(天)(天)平均流程时间平均流程时间=37/5=7.3天天订单申达、振雄将会延期交货,延期时间分别为订单申达、振雄将会延期交货,延期时间分别为4天和天和7天。
每个订单平均延期(天。
每个订单平均延期(0+0+0+4+7)/5=2.2天。
天。
EEAACCBBDD方案三方案三利用利用Ddate(Ddate(最早交货期最先加工最早交货期最先加工)规则,排序结果为规则,排序结果为加工顺序加工顺序加工顺序加工顺序加工时间加工时间加工时间加工时间交货日期交货日期交货日期交货日期流程时间流程时间流程时间流程时间13426256790+1=11+3=44+4=88+2=1010+6=16总流程时间总流程时间=1+4+8+10+16=39(天)(天)平均流程时间平均流程时间=39/5=7.8天天在这种情况下,三个订单将会延期,平均延期时间为在这种情况下,三个订单将会延期,平均延期时间为(0+0+2+3+7)/5=2.4天。
天。
EEAABBCCDD补救措施补救措施生产报告生产报告(生产日报表生产日报表)实施作业实施作业(车间车间)生产计划安排生产计划安排(生产部生产部)及时联络协调及时联络协调(效果效果欠佳欠佳,无法交货时无法交货时)差异分析差异分析效果确认效果确认生产进生产进度控制度控制流程流程生产异生产异常原因常原因1.1.根据材料采购到位情况再安排生产;根据材料采购到位情况再安排生产;2.2.订单按交货期或紧急的顺序生产,保证交货期;订单按交货期或紧急的顺序生产,保证交货期;3.3.可以对生产进度进行全程监控;可以对生产进度进行全程监控;4.4.可以防止原材料无计划采购而积压过多,降低可以防止原材料无计划采购而积压过多,降低库存;库存;5.5.形成整个公司生产处于可控状态。
形成整个公司生产处于可控状态。
ITHINKICANITHINKICAN学会做事学会做事=解决能力问题解决能力问题学会做人学会做人=解决理念问题解决理念问题主要是针对生产中出现品质不良展开分析讨论,并将结果整理在大家容易看到的地方,以提醒防止发生这样的问题,而且大家随时可以提出新的建议并进行讨论修订。
55月迟交货次数月迟交货次数(担当者别)(担当者别)王王上月平均上月平均糟糕糟糕,这个月这个月我最差我最差,要认真要认真做做,下个月决不下个月决不能能.张张赵赵李李1.1.无论是谁都能判明是好是坏(异常)无论是谁都能判明是好是坏(异常)2.2.能迅速判断能迅速判断,精度高精度高3.3.判断结果不会因人而异判断结果不会因人而异按照责任主管的不同,一般可以分为公司管理看板、部门车间管理看板、班组管理看板三类。
好东西要与好东西要与我们大家共享我们大家共享车间通过看板向员工传达公司的各种信息、车间内部的动态、车间通过看板向员工传达公司的各种信息、车间内部的动态、学习资料以及安全常识等学习资料以及安全常识等,达到互相监督、共同管理的目的达到互相监督、共同管理的目的.其中其中的的“想说就说想说就说”栏目主要是让员工有一个公开的渠道来表达自己想栏目主要是让员工有一个公开的渠道来表达自己想法与观点法与观点,提出对公司有益的建议提出对公司有益的建议.通过这种通过这种“全员参与、持续改进全员