仪表设计通则.docx
《仪表设计通则.docx》由会员分享,可在线阅读,更多相关《仪表设计通则.docx(20页珍藏版)》请在冰豆网上搜索。
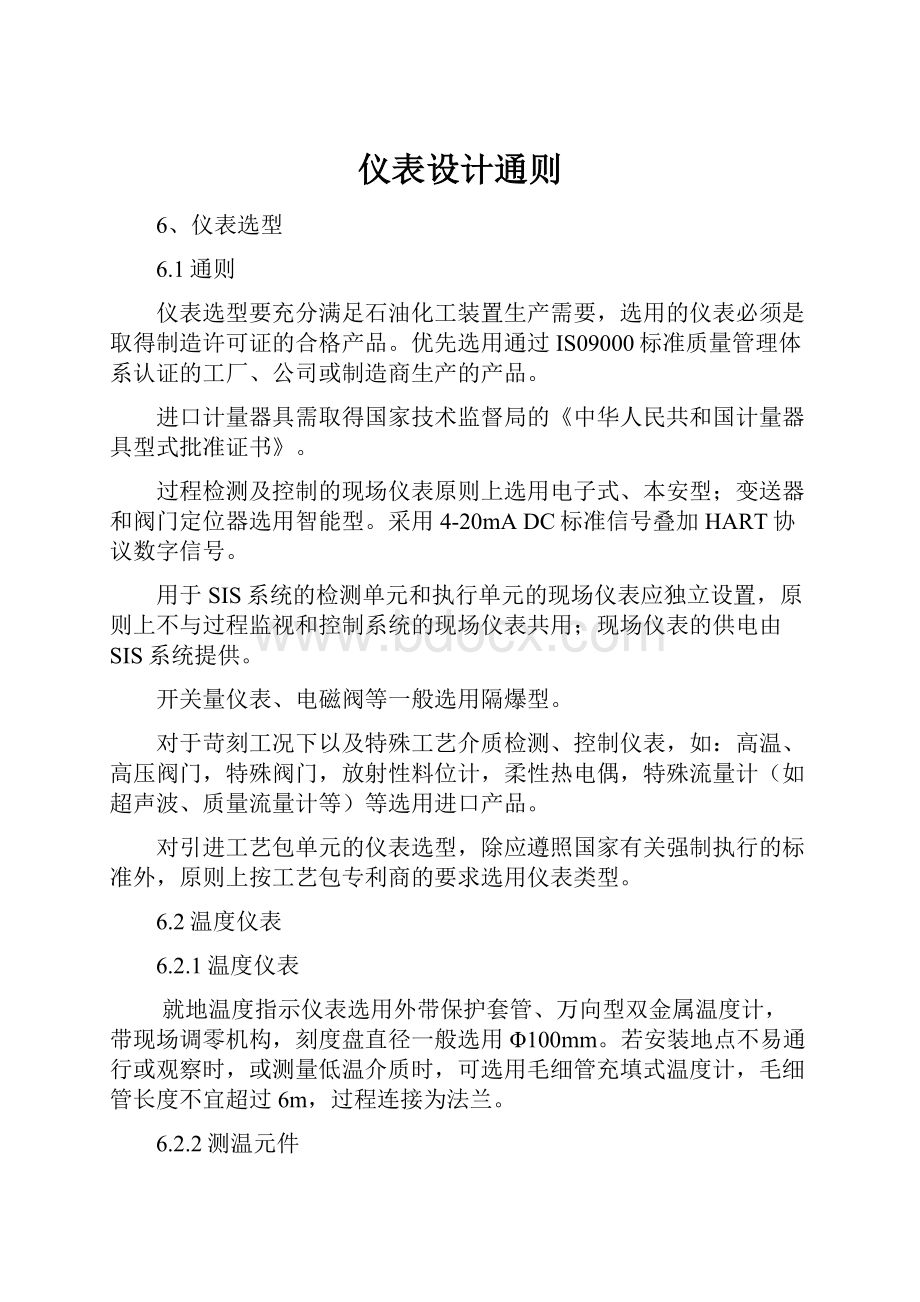
仪表设计通则
6、仪表选型
6.1通则
仪表选型要充分满足石油化工装置生产需要,选用的仪表必须是取得制造许可证的合格产品。
优先选用通过IS09000标准质量管理体系认证的工厂、公司或制造商生产的产品。
进口计量器具需取得国家技术监督局的《中华人民共和国计量器具型式批准证书》。
过程检测及控制的现场仪表原则上选用电子式、本安型;变送器和阀门定位器选用智能型。
采用4-20mADC标准信号叠加HART协议数字信号。
用于SIS系统的检测单元和执行单元的现场仪表应独立设置,原则上不与过程监视和控制系统的现场仪表共用;现场仪表的供电由SIS系统提供。
开关量仪表、电磁阀等一般选用隔爆型。
对于苛刻工况下以及特殊工艺介质检测、控制仪表,如:
高温、高压阀门,特殊阀门,放射性料位计,柔性热电偶,特殊流量计(如超声波、质量流量计等)等选用进口产品。
对引进工艺包单元的仪表选型,除应遵照国家有关强制执行的标准外,原则上按工艺包专利商的要求选用仪表类型。
6.2温度仪表
6.2.1温度仪表
就地温度指示仪表选用外带保护套管、万向型双金属温度计,带现场调零机构,刻度盘直径一般选用Φ100mm。
若安装地点不易通行或观察时,或测量低温介质时,可选用毛细管充填式温度计,毛细管长度不宜超过6m,过程连接为法兰。
6.2.2测温元件
一般温度测量的测温元件宜选用热电阻/热电偶,RTD/mV信号经隔离型温变安全栅转换为4-20mA,进控制系统。
非危险区域内的温度信号直接进控制系统,如动力站,空分站。
测温元件一般不采用双式结构(特殊要求的除外),需要在两地显示或既要控制又要报警联锁时,应选用两只单独安装的测温元件。
测温元件一般采用绝缘型,普通铠装芯外径采用Φ6mm。
当测温元件为热电偶时,应具有断偶保护功能。
加热炉炉管表面温度测量采用1/2”铠装刀刃式热电偶,耐热GH3030镍基高合金钢外护套;
除特殊情况外,所有温度元件应有保护套管,保护套管材质不低于316不锈钢,保护套管型式采用锥形棒料整体钻孔式(一般外径Φ22)。
插入深度按如下原则确定:
管道安装时保护管应插至管道内径的1/3-2/3处,在设备上安装时保护管应插入设备内400mm左右。
除专利商或设备成套商的特殊要求外,本项目中不采用温度开关。
为减少测温元件的种类,热电偶尽量选用符合IEC60584标准“K”型或“E”,或采用Pt100热电阻,三线制,0℃时电阻为100Ω,符合IEC60751标准。
温度检测元件类型及分度号选用原则见下表:
检测元件名称
分度号
温度范围(℃)
铂热电阻R0=100Ω
Pt100
-200~650
镍铬-镍硅热电偶
K
0~1000
镍铬-康铜热电偶
E
0~750
铂铑10-铂热电偶
S
0~1300
铂铑13-铂热电偶
R
0~1300
铂铑30-铂6热电偶
B
0~1600
6.2.3远传用热电偶、热电阻的接线盒材质一般为铸铝(铝合金),防水型(IP65),电气连接口一般为1/2”NPT。
6.3压力仪表
6.3.1测量稳定压力时,正常操作压力应为压力仪表量程的1/3~2/3范围内;测量脉动压力时,正常操作压力应为压力仪表量程的1/3~1/2范围内。
6.3.2一般情况下,压力表选用表壳直径ф100mm;精度不低于1.6级;压力表连接螺纹一般采用M20×1.5;压力表应有后部泄压安全措施。
压力表类型选择原则如下:
a)一般选用全不锈钢压力表YTF-100,有腐蚀场合(如测量氨气、汽油、液化石油气及其它腐蚀性液体等)选用氨用压力表YA-100;
b)对于粘度较大、腐蚀性较强、易结晶的介质,选用“YTP”系列隔膜式压力表;
c)加热炉微差压测量采用“YE”膜盒式压力表;
d)有振动场合的压力表选用抗振压力表。
6.3.3远传压力、差压测量均采用智能型变送器(4-20mADC标准信号叠加HART协议数字信号)。
差压变送器选型时应考虑其耐静压的等级。
压力、差压变送器的隔离膜片的材质最低要求为316L不锈钢,更高的材质应根据实际需要选用;测量室材质为316不锈钢,放大器外壳材质为铸铝。
智能型差压变送器应带不锈钢整体三阀组。
压力测量选用智能型普通压力变送器;微压、压差测量选用智能型差压变送器;测量腐蚀性或易凝、易堵介质的压力或压差时,分别选用智能型膜片密封式法兰压力变送器或智能型双法兰差压变送器,并采取反冲洗等措施。
6.3.4压力表或压力变送器应有超量程保护设施。
6.3.5压力、差压变送器的过程连接尺寸一般为:
1/2"(F)NPT,电气连接口为1/2"(F)NPT。
6.3.6除专利商或设备成套商的特殊要求外,本项目中不采用压力开关。
6.4流量仪表
6.4.1工艺最大流量不应超过流量仪表量程的90%,正常流量测量应为流量仪表量程的50%~70%,最小流量不应小于流量仪表量程的10%。
6.4.2除工艺包专利商特殊要求外,一般流量测量优先选用标准节流装置+差压变送器方式。
差压变送器应带不锈钢整体三阀组。
采用差压式流量测量时,节流装置采用国际标准ISO5167-1(2003年版)和国标(GB/T2624.1~4-2006)计算、制造和验收,孔板的β值应在0.2~0.7之间,计算差压原则上按0~6,0~10,0~16,0~25,0~40,0~60kPa的范围选用。
节流元件采用法兰取压,取压法兰一般选用PN50(梯型槽)系列,取压口规格:
NPT1/2;带节流装置引压短管;不带上、下游直管段;一般工况,螺栓材质:
35CrMoA;螺母材质:
35号钢;法兰材质与管道材质一致。
高温工况下,螺栓材质25Cr2MoVA;螺母材质:
30CrMoA;法兰材质与管道材质保持一致。
6.4.3流量计量仪表的选用原则:
a)计量仪表精度要求:
装置内部为1.0~1.5级,进出装置为0.5~1.0级,进出厂为0.2级。
液体流量计量采用温度补偿,气体流量计量采用温度和压力补偿;
b)进出装置原料和产品的计量可采用质量流量计;
c)粘稠介质流量测量采用1/4圆孔板或楔式流量计;
d)进装置的蒸汽、净化风、非净化风、氮气等计量可采用法兰取压同心锐孔板、阿纽巴流量计及涡街流量计;
e)小管道(DN≤25)流量测量选用金属管转子流量计,配套带过滤器和工艺配对法兰及紧固件;用于控制的流量选用内藏孔板;
f)埋地管道(循环水,新鲜水等)流量计量选用管道式电磁流量计或超声波流量计;
6.4.4本项目不采用流量开关,凡参与安全联锁保护的流量参数,均应按上述要求确定流量计的类型,且4-20mADC标准信号直接进入SIS系统参与逻辑运算。
6.4.5流量计的电气接口一般选用1/2”NPT,如果流量计需要外供电时,供电电气接口与信号电气接口应当分开设置。
6.5液位仪表
6.5.1就地液位计
a)一般场合就地液位指示选用玻璃板(双色)液位计或磁性翻板液位计。
对无色、水、清洁和浅色介质采用反射式玻璃板液位计;其它介质采用透光式玻璃板液位计。
当测量低温介质时应设有防霜措施.
b)易冻、易凝介质采用带蒸汽夹套的双色石英玻璃板液位计;
c)高温高压介质场合应采用高温高压玻璃板液位计;
d)玻璃板液位计采用制造厂的标准长度(L≤1700mm),当需要采用2个或2个以上的玻璃板液位计方能满足测量范围要求时,各玻璃板液位计之间不应有视觉盲区,即相邻两台玻璃板液位计在垂直方向应重叠200mm。
e)有毒介质采用磁性浮子液位计。
6.5.2液(界)位测量
a)优先选用双法兰差压变送器或差压变送器测量液(界)位;尽量少采用灌隔离液的导压管的方案;如果测量范围太大(超过10米),仍采用差压变送器,并加灌隔离液的导压管的方案。
b)测量范围L≤1200mm的场合当差压变送器不可用时可选用外浮筒液位变送器;
c)特殊场合也可采用放射性料位计、内浮筒液位计等;
d)汽包水位测量采用双室平衡器+差压式液位变送器。
e)地下容器的液(界)位的监控或联锁动作(如启、停泵等),可采用顶装式磁浮子液位计或内浮筒液位计。
f)大型储罐的液(界)位仪表采用雷达、伺服液位计。
6.5.3液(料)位变送器的电气接口一般选用1/2”NPT,如果液(料)位变送器需要外供电时,供电电气接口与信号电气接口应当分开设置。
6.6轴系仪表
机组轴系监测仪表、转速监测仪表等独立设置,按本特利产品选用。
本特利二次表带通讯接口和开关量信号,信号可引至CCS或DCS。
6.7调节阀
6.7.1调节阀选用气动薄膜或气缸执行机构。
一般情况下采用直通或角型阀体。
流量特性选择依次为等百分比,近似等百分比,线性。
6.7.2调节阀型式:
●口径≤DN200(8″)的调节阀优先选用Globe调节阀(单/双座和套筒式),口径≥DN250(10″)的调节阀或用于低压差场合的调节阀,应采用蝶阀或偏心旋转阀;调节型蝶阀开度为0~60%;
●在要求泄漏量小、阀前后压差较小的场合选用单座调节阀;
●在泄漏量要求不严、阀前后压差大的场合选用双座调节阀;
●在阀前后压差较大、工艺介质不含固体颗粒的场合或因阀门压降大引起较大噪声的场合选用套筒调节阀;
●调节精度要求不高的场合可选用自力式调节阀;
●含有固体颗粒的场合,应采用V型球阀或偏心旋转阀;
●对于高压差、闪蒸、空化、高噪声等情况,可选用角型阀或多级降压阀等。
6.7.3调节阀的基本要求:
调节阀Cv(阀流通能力)计算,按ISAS75.01标准计算;
调节阀的相对行程应满足:
等百分比阀30%~90%,正常流量50%~75%;线性阀10%~80%,正常流量40%~60%。
特殊场合的调节阀(如放空、泵或压缩机的最小回流控制等)可以不受上述相对行程范围的限制。
调节阀设计应使调节阀下游1米处和管道表面1米处的噪声等级不超过85dBA。
间歇使用或紧急操作的调节阀在上述位置的噪声不超过115dBA。
6.7.4根据下列不同的操作温度选用上阀盖型式:
●操作温度为-0℃~220℃时选用普通型;
●操作温度高于220℃时选用散热型。
●操作温度低于0℃时选用长颈型。
6.7.5阀内件材料选择:
阀内组件和阀座材质通常应为316不锈钢。
高差压或其它特殊场合,材料应经硬化处理或选用其他适合的材料。
操作温度低于220℃密封填料可选用聚四氟乙烯人字型填料或聚四氟乙烯混合填料。
操作温度为220℃或更高时应选用柔性石墨填料。
6.7.6调节阀附件的选择:
所有进口调节阀均带智能型电/气阀门定位器及气动附件;国产调节阀需要的智能型电/气阀门定位器,采用进口品牌,其它气动附件随阀带;电/气阀门定位器为本质安全型,电气连接口为1/2”NPT。
根据工艺操作需要,当调节阀未设旁路管线及无前、后切断阀时,应配带手轮机构;特殊调节阀,如:
角阀、三通阀、蝶阀、偏心旋转阀等,应配带手轮机构。
6.7.7执行机构的选择:
一般情况下选用气动薄膜或气缸执行机构。
调节阀执行机构的选择应保证在气源故障时,阀门处于“故障安全”位置。
必要时由阀门制造商配置贮气罐,贮气罐必须有国内认可的压力容器使用许可证。
6.7.8泄露等级
一般用调节阀的泄漏等级为ANSI-IV级,要求严密关闭场合可选用调节阀的泄漏等级为ANSI-V级;安全联锁用两位式紧急切断阀、放空阀的泄漏等级,除工艺包有特殊要求外应不低于ANSI-V级。
6.7.9安全联锁保护阀门
用于安全联锁保护的两位式阀门,由供应商整体配齐所有电/气动附件。
低压场合可选用国产关闭性严密(金属硬密封,ANSI-V级及以上)的ON/OFF作用的球阀或闸板阀,口径大时采用蝶阀,执行机构一般采用带弹簧复位的单作用气缸,若不能满足时则采用双作用气缸;高压场合,选用在国内同类装置使用业绩好的进口气缸式ON/OFF作用的两位式阀门,必要时可配带储气罐(VolumeTank)以保证仪表净化空气系统故障时阀门能够处于安全的开/关状态,贮气罐必须有国内认可的压力容器使用许可证。
用于安全联锁保护的两位式阀门,必须安装有阀位回讯开关,以便操作人员在全工程中心控制室随时监视阀门的开/关状态。
阀门回讯开关采用接近式开关。
安全联锁保护用的两位式(ON/OFF)阀门不得设置手轮机构。
6.7.10自力式调节阀仅用于N2、空气、燃料气和其它辅助用流体调节精度要求不高的场合。
6.7.11电动阀
电动执行机构选用三相380VAC,50Hz供电。
执行机构应包括电机控制系统和阀位开关,电动执行机构选用进口品牌。
6.7.12电磁阀
电磁阀一般采用24VDC供电,低功耗(<4W)、隔爆型、带接线盒和接线端子;远距离信号传输也可采用220VAC(UPS)供电方式。
电磁阀整体为不锈钢。
用于两位式切断阀联锁回路的电磁阀,工艺无特殊要求时,不带现场复位手柄,采用中心控制室逻辑复位模式。
6.8分析仪表
6.8.1根据工艺操作要求,设置必要的在线分析检测系统。
6.8.2在线分析仪表包括样气预处理系统和数据处理系统,并成套供货,复杂的在线分析仪应带有通讯接口,通过串行通讯接口(MODBUS)与DCS通信。
6.8.3过程分析仪根据需要安装在现场分析小屋内,分析小屋应由分析仪表制造厂成套供应,并配齐内部采样及返回管线、放空或排污管线、电源开关箱、气源管线、载气、标准气及防爆通风设施等。
6.8.4鉴于MTO等化工装置分析仪表的使用情况,各装置的在线工业色谱分析仪进行组网,设置分析仪表系统(PAS),对分析仪表进行实时监控和管理。
6.9可燃气体、有毒气体报警器
根据相关规范要求,分别设置可燃气体、有毒气体检测报警器。
可燃气体(烃类)检测报警器采用催化燃烧式(需采取防爆措施),带就地指示;有毒气体检测器采用电化学或半导体式。
电气接口为3/4”NPT。
6.10仪表的防爆与防护
6.10.1仪表的防爆
用于爆炸危险场所的仪表必须符合该场所相应的防爆要求,并取得国家有关防爆检验机构的相应防爆等级的防爆认证。
电子式仪表应优先选用本安型仪表(Exi),当无本安型仪表时也可选用隔爆型(Exd)。
对于有氢气存在的场合,防爆等级应不低于Exia(ib)IICT4(本安型)或ExdIICT4(隔爆型);对于其它易燃、易爆的场合,防爆等级应不低于Exia(ib)IIBT4(本安型)或ExdIIBT4(隔爆型)。
分析仪表、部分流量计等无本安型仪表时,可采用符合使用场所相应防爆等级要求的隔爆型或增安型仪表。
对于主装置以外的公用工程/罐区/污水处理场等以隔爆仪表为主的单元,整个装置可以全部选用隔爆型仪表,隔爆等级不低于防爆区域划分级别。
6.10.2安全栅
本项目的安全栅均选用隔离式安全栅。
安全栅必须与变送器构成符合安全标准的本质安全系统。
安全栅还必须与变送器、DCS匹配,以满足信号传送和现场仪表供电要求。
特殊仪表的安全栅应根据所选仪表的要求确定。
7、中心控制室和现场机柜室
7.1中心控制室的设计原则
中心控制室(CCR)是对工艺装置和公用工程进行生产过程集中监视、控制的中心,亦是信息处理中心、生产管理中心、消防控制中心、自控设备维护中心。
它将工艺过程相关的装置的数据和信息集中起来,形成流程化操作,将CCR内各装置的监视、控制、操作和管理融为一体,装置之间的生产、管理信息流集中共享,是现代化生产管理的需要,是降低成本、增加效益的有效途径。
按总流程和总平面布置,将装置的CRT操作站划分若干个操作区。
每个操作区有数个操作台,每个操作台带有CRT显示器和操作员键盘,根据装置及操作岗位的不同,设置不同数量的CRT显示器。
每个操作站可采用输入密码或键锁的方式规定操作员管辖的范围。
CCR设有遥控的闭路电视、扩音对讲电话系统,能够随时监视装置的特定区域(如:
装置火焰、火炬及储罐等)。
可燃/有毒气体检测系统(GDS)设置独立的CRT操作站。
7.2现场机柜室的设置原则
现场机柜室依据总平面布置以及装置与中心控制室的距离等条件,按装置或多个生产单元设置机柜间或联合机柜间。
现场机柜室的设置应便于项目实施、维护及管理、节省工程费用等。
现场机柜室设置在非爆炸危险区域。
现场
7.3中心控制室及现场机柜室内设备
7.3.1中心控制室机柜室初步按照上文5.1条配置。
中心控制室内设安装CRT显示器的DCS操作台、SIS操作台、可燃气体/有毒气体检测报警系统操作台、压缩机控制系统(CCS)操作台等。
所有操作台的外形尺寸及颜色应一致。
7.3.2机柜间
现场机柜室内设工程师站、安全栅柜、电源柜、系统机柜、端子柜,网络柜等。
机柜采用前后开门的方式,尺寸统一为800X800X2100mm(包括底座),颜色应一致。
8、仪表电源、气源、伴热、隔离、冲洗、接地
8.1仪表电源
中心控制室及现场机柜室的过程控制系统、安全仪表系统及现场仪表等均采用UPS电源供电。
UPS电源输出规格为单相220VAC、50Hz。
现场仪表的供电原则上采用24VDC直流供电。
24VDC电源采用双交流冗余的24VDC供电系统,24VDC输出接至母排联成24VDC电源网。
当现场仪表需要220VAC供电时,应采用“TN-S单相三线制”供电方式,即:
相线(L)、中线(N)、地线(PE)。
所有用电设备的供电,均应由各配电柜经由专用断路器供给,中心控制室及现场机柜室各自分别设置配电柜。
供电方案根据用电设备不同设置如下:
DCS系统设备(如控制柜、操作台等)由交流配电柜直接供给;
集中安装的单台220VAC仪表的供电经配电柜、交流配电器后供给;
机柜内安装仪表的24VDC供电电源应采用1:
1冗余配置,每台电源的负荷不超过50%。
仪表电源规格:
一般仪表电源:
AC220V±10%,50HZ±1HZ
DC24V~25.8V
凡不符合本规定的电源规格的特殊仪表必须自带电源变换设备。
UPS不间断电源:
输入AC220V±15%,50HZ±2.5HZ
输出AC220V±5%,50HZ±0.5HZ
波形失真率<5%
UPS的不间断时间为30分钟
由正常供电转换到备用电源的切换时间5ms。
8.2仪表气源
仪表气源采用净化风,装置内设置净化风罐,再由管道设计专业敷设净化风主管。
各仪表用风均从主管引接。
根据现场仪表用风点集中、分散的情况,采用气源分配器与分散过滤减压相结合的供风方式。
各供风点按仪表的要求设定供风压力。
装置单元用气量按每台调节阀2Nm3/h的消耗量估算。
8.3仪表伴热
仪表伴热采用蒸汽伴热、热水伴热或电伴热。
各装置由工艺安装专业敷设伴热蒸汽或热水及伴热回水主管线。
易冷凝、易沉淀、易结晶介质场合,导压管必须采取伴热和保温措施。
热水(或蒸汽)伴热管一般采用φ14×2(φ10×1)不锈钢管。
每个伴热回水管终端应设有截止阀。
当工艺管道采用电伴热时,仪表伴热也可采用电伴热。
热水伴热的热水用量按以下计:
60Kg/15m.h(差压变送器的正/负引压管捆扎在一起时,以单根导压管计)。
8.4仪表隔离液和冲洗油
本装置不设置自动隔离冲灌设备,不采用冲洗油方案。
8.5仪表接地
仪表接地包括保护接地和工作接地,工作接地包括信号回路接地、屏蔽接地、本质安全仪表系统接地,采用等电位连接的原则,与电气设备采用同一个接地网,一般接地电阻不大于4Ω。
同一回路信号接地、同一电缆屏蔽层只允许单点接地。
原则上在信号接受侧(室内)接地,回路信号接地、屏蔽接地、本质安全仪表系统接地应接在同一汇流母线上,再统一接到电气设备的接地网的接地干线上。
9、仪表材料及安装
9.1电线、电缆、补偿导线及电缆槽盒
9.1.1现场接线箱与机柜之间电缆选用阻燃型多股铜芯聚乙烯绝缘聚氯乙烯护套对绞分屏、总屏蔽计算机用控制电缆;现场接线箱(盘)到现场仪表的电缆应选用阻燃型多股铜芯聚乙烯绝缘聚氯乙烯护套钢丝铠装屏蔽控制电缆,其中本安回路采用本安电缆。
本安系统配线护套颜色为兰色,一般电缆护套颜色为黑色,接地电缆护套颜色为黄/绿色。
电缆截面积一般为1.0~1.5mm。
各种规格电线或电缆的应用场合如下:
2X1.5(1.0):
两线制变送器、电/气转换器、电气阀门定位器等4~20mADC信号;
2X1.5:
液位开关、阀位开关、电磁阀等开关量信号;
3X1.5:
热电阻等;
3X1.5:
可燃气体、毒性气体的监测报警器等;
3X2X1.5:
自保切断阀。
3X2X1.5:
自保切断阀
9.1.2现场仪表电缆敷设尽量采用现场接线箱,现场接线箱至现场机柜室采用多对(8、10、12)电缆。
9.1.3补偿导线选用聚乙烯绝缘聚氯乙烯护套的“KC”、“EX”型铜线编织屏蔽补偿导线。
规格为:
KC2X1.5或EX2X1.5。
9.1.4220VAC交流电源线宜采用:
3X2.5、4、6、10、16
9.1.5备用信号线:
备用信号线采用多对电缆,敷设至总图区仪表电缆槽盒或框架区附近的接线箱内。
其中:
备用电线电缆8X2X1.5;
备用补偿导线线缆KC8X2X1.5或EX8X2X1.5。
9.1.6仪表汇线槽盒:
仪表汇线槽盒按槽式电缆槽盒选用,材质为热浸锌碳钢。
槽盒的高度一般不宜超过300mm,槽盒的截面积应按电缆充填的实际截面积的2~3倍考虑。
9.1.7仪表槽盒内信号线放置原则
槽盒内信号线应按信号类型及电平等级分别排放,热电偶或热电阻、4~20mA本安信号线、非本安仪表如隔爆开关、隔爆电磁阀等的信号线等均各自排放,并用隔板隔开。
220VAC交流电源线穿保护管或在槽盒内独立分格敷设。
9.1.8现场分支电缆采用铠装电缆+小槽板+密封接头方式连接。
9.1.9电缆进/出现场机柜室应采用模块密封。
9.1.10各现场机柜室至全厂中心、区域控制室的通讯光纤,采用一路架空、一路埋地的方式敷设。
埋地一路采用保护管+检修井方案,或走电信的地下路由。
9.2供风管线
仪表供风管采用镀锌焊接钢管,管件连接采用螺纹镀锌管件,经过气源球阀后采用不锈钢管及管件,连接方式为卡套式。
一般情况下选用Φ8x1、Φ10x1,特殊情况下选用其它规格。
9.3导压管线
导压管线的基本要求如下:
一般工况导压配管选用φ12x1.5钢管316SSTUBE管,采用双卡套式阀门与管件。
当测量压力大于900Lb等场合,应采用1/2”316SSPIPE管(管道等级与配管一致),承插焊连接;导压配管横向敷设时,应与水平面有1/10或更大的坡度;在任何情况下,变送器的引入处不应出现“U”型弯,防止气体测量出现液阻,测量液体出现气阻;仪表导压管的长度,一般控制在10米以内,最长不超过15米;导压配管排污阀及堵头应配置在导压管的最低点,放空阀及堵头应配置在导压配管的最高点。
9.4仪表安装
9.4.1所有现场仪表及调节阀的位置应有足够的操作维修空间,便于观测、安装、更换、操作和维护。
9.4.2除直接安装在工艺配管上的仪表外,现场仪表安装高度为:
仪表中心距地面(或平台)距离一般为1.2m。