电石生产的节能减排.docx
《电石生产的节能减排.docx》由会员分享,可在线阅读,更多相关《电石生产的节能减排.docx(12页珍藏版)》请在冰豆网上搜索。
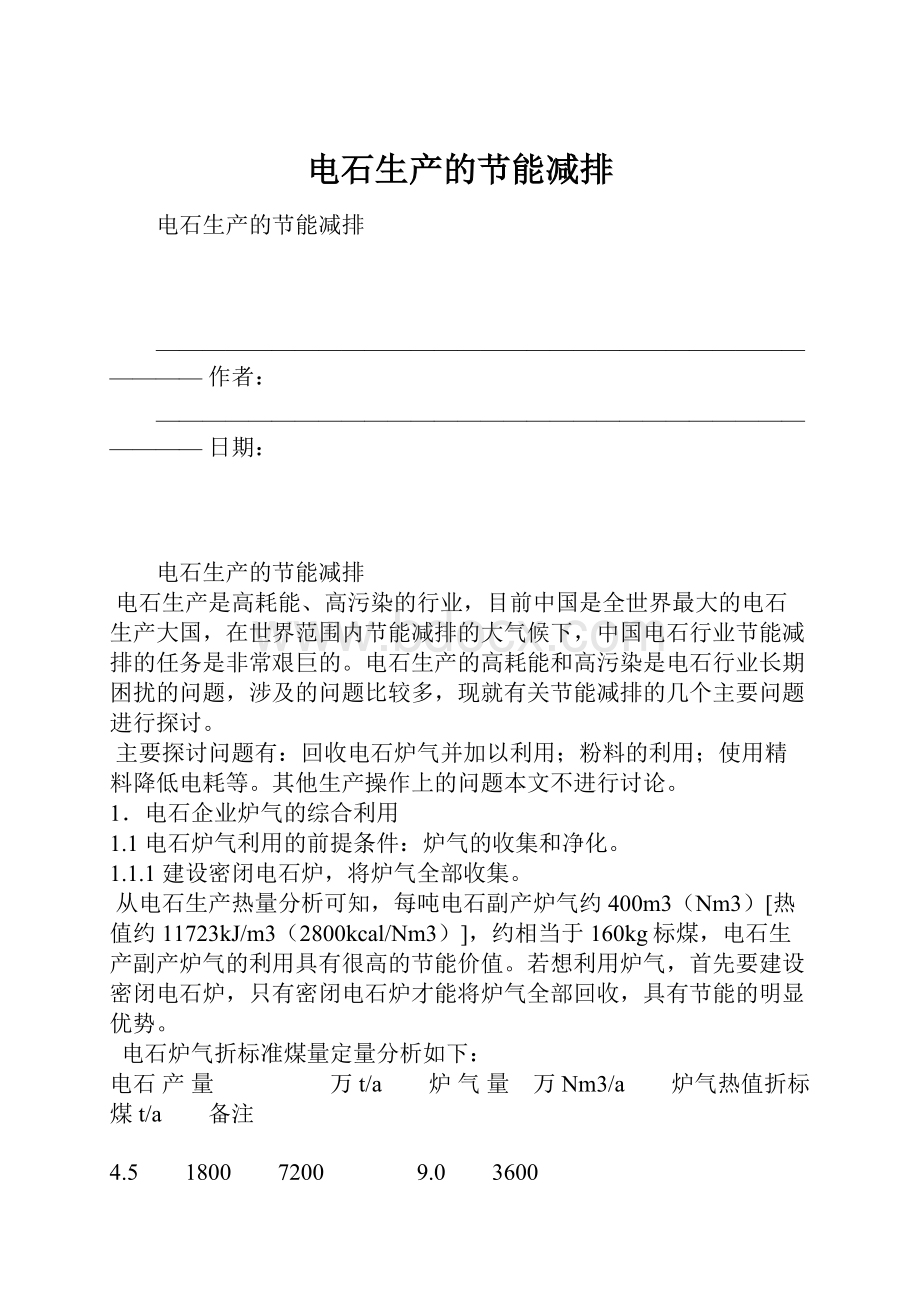
电石生产的节能减排
电石生产的节能减排
————————————————————————————————作者:
————————————————————————————————日期:
电石生产的节能减排
电石生产是高耗能、高污染的行业,目前中国是全世界最大的电石生产大国,在世界范围内节能减排的大气候下,中国电石行业节能减排的任务是非常艰巨的。
电石生产的高耗能和高污染是电石行业长期困扰的问题,涉及的问题比较多,现就有关节能减排的几个主要问题进行探讨。
主要探讨问题有:
回收电石炉气并加以利用;粉料的利用;使用精料降低电耗等。
其他生产操作上的问题本文不进行讨论。
1.电石企业炉气的综合利用
1.1电石炉气利用的前提条件:
炉气的收集和净化。
1.1.1建设密闭电石炉,将炉气全部收集。
从电石生产热量分析可知,每吨电石副产炉气约400m3(Nm3)[热值约11723kJ/m3(2800kcal/Nm3)],约相当于160kg标煤,电石生产副产炉气的利用具有很高的节能价值。
若想利用炉气,首先要建设密闭电石炉,只有密闭电石炉才能将炉气全部回收,具有节能的明显优势。
电石炉气折标准煤量定量分析如下:
电石产量 万t/a 炉气量 万Nm3/a 炉气热值折标煤t/a 备注
4.5 1800 7200 9.0 3600
06年全国产量 14400 1177 470800 1883200
密闭电石炉技术,在国内无论是装备或生产管理已拥有成熟的经验。
从六十年代至今,引进过日本、挪威等国家的多种密闭电石炉设计和制造技术。
设计和制造均已国产化。
25500KVA的密闭电石炉已拥有多台,把持器的形式已有多种,更大型的密闭电石炉也在筹划建设中。
1.1.2炉气净化技术
炉气净化本身不是节能的直接措施,而且要消耗掉一部分动力。
由于密闭电石炉炉气含有大量的粉尘,含尘量约80~150g/m3(Nm3),不能远距离输送,为利用电石炉气,必须将炉气中的粉尘除去,将炉气进行净化,使炉气能够输送,进而加以利用。
炉气净化的工艺方法可采用干法或湿法。
湿法净化技术成熟,但由于耗水量大,且净化后的污水中含有CN-造成二次污染,必须进行污水处理,故流程较长,其发展受到限制。
炉气干法净化,从八十年代至今,引进过日本、挪威等国家的技术。
国内各工厂在使用过程中存在一些问题,分别进行了一些改造和完善,有的工厂改造后已取得良好的成效,已达到正常连续运行。
(湿法净化和干法净化的具体方法这里不做介绍)
1.2电石炉气利用
净化回收后的炉气利用途径有多种。
可作为企业内部的燃料使用,也可输出作为能源或碳一化学生产的原料。
下面介绍几种主要炉气利用的方法:
1.2.1 气烧石灰窑。
在电石企业内,气烧石灰窑所需用的炉气与电石生产副产炉气量理论上基本平衡。
炉气作为气烧石灰窑的燃料,既节能又消除了炉气的污染,而且气烧石灰质量均匀,反应活性好,可使电炉电耗下降。
气烧石灰窑是一项先进的技术,在电石企业内部,气烧石灰窑以电石生产副产炉气作为燃科是最合理的炉气利用措施。
采用气烧窑时应选用热效率高的窑型。
现将几种气烧窑能耗参考指标介绍如下:
西德维曼斯台
尔公司双筒窑 西德维曼斯台
尔公司双斜窑 日本金刚石公
司中心喷咀窑 意大利费尔卡克斯公司方型双梁窑
热耗J/kg石灰
(kcal/kg石灰) 360000~3777000
(860~950) 393600~4145000
(940~990) 4187000~5024000
(1000~1200) 3893000
(930)
气烧石灰窑,在国内已引进过西德、意大利等国家的双套筒窑、方型双梁窑等多种形式的技术。
设计和制造均已国产化。
使用情况良好。
1.2.2余热锅炉
余热锅炉是一项密闭电石炉炉气不经过除尘而直接利用的技术。
从七十年代杭州电化厂等工厂开发成功至今,已取得许多经验。
余热锅炉的形式也在不断改进和完善,技术已比较成熟。
密闭电石炉余热锅炉产生蒸汽量经验数据如下:
国内某厂1吨电石产生约2吨蒸汽(0.8Mp)。
密闭电石炉余热锅炉还有良好的环境效益,同时将炉气中氰离子进行了焚烧。
1.2.3利用炉气作燃料干燥炭材。
1.2.4炉气输出作为专用燃料,例如吉林电石厂曾利用电石炉气送化肥厂作专用燃料。
1.2.5炉气输出掺入城市煤气作燃料,例如吴凇电石厂曾利用电石炉气输出掺入城市煤气使用。
1.2.6利用炉气作原料的碳一化学研究
例如吴凇电石厂曾开发成功利用电石炉气制造光气。
例如吉林电石厂也曾研究开发利用电石炉气制造草酸,但没有实现工业化。
2电石企业粉料的综合利用:
空心电极技术。
空心电极是一项利用粉料的先进技术。
在石灰,炭材加工,运输和贮存过程中,会产生10~15%左右的石灰粉、焦粉,无烟煤粉等粉料,若将粉料弃掉则浪费了能源,增加了成本,污染了环境,而采用空心电极技术可将这部分粉料作为生产电石的原料消耗掉,并使电极糊的消耗下降,是一项很好的节能措施。
既降低了电石单位产品全焦耗,节省了电极糊,又利于电炉的调节。
因此空心电极技术是一项很好的节能措施。
采用空心电极后节约能源折标准煤量定量分析如下:
电石产量(万t/a) 4.5 9.0 1177 备 注
节
约
实
物
(t/a) 耗焦粉 2547 5094 666182 以电石焦耗566kg计
空心电极耗粉料10%估算
耗灰粉 4208 8415 1100495 以电石灰耗935kg计
空心电极耗粉料10%估算
节约电极糊 675 1350 176550 采用空心电极前电极糊耗35kg/t电石,采用空心电极后电极糊耗20kg/t电石计
实
物
折
标
准
煤
(t/a) 焦粉折标煤 2473 4946 646827 1kg焦粉折0.971kg标准煤
灰粉折标煤 571 1142 149348 3977460J/kg
以石灰热耗(950kcal/kg)估算
电极糊折标煤 578 1157 151300 1kg电极糊折0.857kg标准煤
折标煤总计 3622 7245 947485
空心电极技术,从八十年代至今,引进过日本、西德、挪威等国家的技术。
国内工厂在使用过程中又予以改造和完善,设计和制造均已国产化。
3采用精料,以减少杂质副反应耗电损失。
3.1 电石生产中杂质副反应耗电损失
选用精料,可以减少杂质的副反应的耗电损失。
关于电石生产的耗电定量分析,由于原料、设备,操作等方面的差异,国内外密闭电石炉热平衡数据不尽相同,现参考取日本金刚石公司提供热平衡数据如下:
注:
以输入电能为100作基准。
从上表可知,杂质副反应耗电占电石生产输入电能的4.12%,其杂质耗电量折标准煤举例如下(电石单位产品电炉电耗以3300度/吨计)。
电炉产量
(万t/a) 杂质副反应耗电
(kWh/a) 耗电折算标准煤(t/a) 备 注
4.5
9.0
1177 6118200
12236400
1600249200 752
1504
196690 以杂质副反应耗电占
输入电能4.12%估算
1kWh折0.1229kg标准煤
从上表可知,杂质副反应耗电从宏观看也很可观。
因此,电石生产应采用精料,最大限度地降低杂质副反应耗电。
3.2 严格控制石灰石原料质量,保证石灰质量。
国内电石用石灰石矿工业指标一般要求为:
CaCO3≥96%
MgO≤1%
SiO2≤l%
R2O3≤l%
S≤0.2%
P≤0.06%
从国外资料可知,西德、日本等国家密闭电石炉用石灰石CaCO3含量在98%以上,含泥量在0.2%以下。
密闭电石炉用石灰石除应符合电石用石灰石一般要求外,有条件的地方,宜选择CaCO3≥97%,MgO≤0.6%的优质石灰石,石灰石中夹带的泥沙应采取清理措施,以保证生产出优质石灰。
生产实践证明,石灰石中杂质增加,或石灰生烧量增加,均使电炉电耗增加,且对电炉带来其它不利影响。
因此,要控制石灰石中杂质含量和石灰生烧量等。
3.2.1石灰石中杂质的影响
石灰石中的杂质对电耗焦耗都有直接影响,而且对熔炼操作极为不利。
因为在反应中金属氧化物还原时要消耗热量,浪费焦炭和电能。
关于石灰石中的杂质对电耗影响收集到的参考经验数据差异较大。
而杂质的还原率,还和电石质量有关,电石质量越高,还原率也就越大。
据物料平衡,它们的还原率MgO是80~100%,SiO2是40~60%,Fe2O3是30~50%,AL2O3是5~10%
3.2.2石灰生烧量的影响
在电石炉内,生烧石灰中的碳酸钙要进一步分解生成石灰,再与焦炭反应生成电石。
分解碳酸钙要耗电,增加了电石的电耗。
同时生烧石灰中有二氧化碳成分计入,生烧率过高,要影响到炉料的配比,打乱电石炉的正常生产秩序。
关于石灰生烧对电耗影响收集到的参考数据是,石灰生烧量每增加1%,当石灰投炉量为900公斤/吨电石时,将使每吨电石增加电耗8.5度,并多用焦炭1公斤。
石灰生烧量:
气烧窑≤4%,混烧窑≤6(8)%,并应尽量提高石灰活性。
3.2.3石灰吸水的影响
在生产和贮运石灰过程中,因接触空气而生成一部分氢氧化钙,另外,碳材中的水分对石灰的风化也有影响。
石灰吸水也是注意的重要问题。
除了粉化石灰严重影响生产操作外,消石灰在电石炉内反应的过程中要消耗电能和焦炭。
——26千卡
——39.6千卡
石灰吸水情况是很容易发生的。
收集到的可参考的经验数据如下:
在干燥仓库中存放四昼夜后,其含水量几乎增加3倍;在普通仓库中存放19昼夜后,其含水量几乎增加12倍,可达到10%。
因此石灰出窑后预防吸潮很重要。
3.3优选焦炭
冶金焦是生产电石的主要碳素材料,固定碳应≥84%,灰分≤15%。
国外电石生产用焦炭固定碳高,约在90%以上。
鉴于国内实际情况,期望使用固定碳高的焦炭。
入电石炉的焦炭必须经过干燥,使水分≤1%。
生产实践证明,焦炭中灰分增加或水分增加,均使电炉电耗增加,因此,要控制焦炭中灰分含量和水分含量。
3.3.1焦炭中的灰分对电耗的影响
据西德资料介绍,炭素中的灰分每增加1%,每吨电石就要多耗电57~60度。
日本也有资料说对发气量为300升/公斤的电石有如下关系:
灰分含量(%) 7 9 10
焦炭耗用量(公斤/吨) 540 551 546
电耗(度/吨) 3200 3280 3360
分析表中数据粗略推算,炭素中的灰分每增加1%,每吨电石就要多耗电40~80度。
如取平均值,也是在60度左右。
因此,力求使用灰分少的焦炭是十分必要的。
一般要求含C≥84%。
3.3.2焦炭中的水分对电耗的影响
国内某电石厂曾有过测定结果:
焦炭中的水分每公斤要耗电2度,投炉量一般是625公斤,那么,每增加1%的水分,每吨电石将增加电耗12.5度,生产实耗是10~15度,同时增加焦炭消耗2.6公斤/吨。
国内另一有机化工厂曾做过十天以上专门性的对比试验,结果表明:
当焦炭水分由9.4%减少到5.6%时,电耗下降48度/吨;粗略推算,每增加1%的水分,每吨电石将增加电耗12.6度。
同时电石的产量增加35公斤;电石发气量提高1.9升/公斤。
以上两厂测定结果非常相近。
因此使用干燥过的焦炭是十分必要的,通常要求应控制水分在1%以下。
3.4严格入炉原料粒度
炉料粒度在适宜的尺寸范围内,可提高产量和降低电耗。
炉料粒度对电石生产也是很重要的。
粒度过大,接触面积小,反应较慢;粒度过小,炉料透气性不好,影响电石炉的操作。
各种碳材在粒度不同时其电阻相差很大。
一般是粒度越小,电阻越大。
电极易于深入炉内,对电石炉操作有利。
但粒度过小,则透气差,容易使炉料结块,反而不利。
因此要合理选择炉料粒度。
石灰粒度要和电石炉容量大小及焦炭粒度大小配合起来确定。
生产实践可供参考经验数据是:
电石炉容量KVA 焦炭粒度(毫米) 石灰粒度(毫米)
20000以上 5~20 8~40
10000~20000 3~18 5~35
5000~10000 3~15 5~30
石灰和焦炭粒度合格率规定,是为了保证炉料的透气性和反应的均匀性。
入电石炉石灰和焦炭粒度合格率应≥90%,应无可见杂质。
3.5改善碳素材料结构
碳素材料一般以焦炭为主。
无烟煤电阻大,对调节炉内电阻作用较大,而且价格低,又可降低成本。
表面上看,无烟煤固定碳含量低,但因其挥发分高。
在生产电石过程中,待其挥发分跑掉后,剩余部分固定碳相应升高,成为很好的碳素材料。
生产实践也证明,在炭材中掺入一定量的优质无烟煤是适宜的。
石油焦固定碳含量高,灰粉低,电阻大,反应活性好。
对调节炉内电阻有明显的作用,有利于提高电石质量和降低电耗,有条件的地方可在炭材中掺入一定量的石油焦。
炉料里掺石油焦,不但可提高电石产量和质量、降低电耗,而且由于炉料总电阻增加,总灰分减少,反应性好,电极稳定深埋,对加速恢复炉温也很有利。
国内某厂曾在10000KVA开放炉中试验用过,收集到的经验数据如下:
在焦炭中掺用25%油焦时,比未掺油焦的,电耗低84~92度/吨,发气量提高1~8升/公斤,产量增加60公斤时,减少焦耗25公斤/吨电石。
在有条件的地方,在碳素材料中可掺入一定的优质无烟煤或石油焦,使碳素材料结构更加合理,以增大炉内电阻降低电耗。
根据生产实践证明,混合使用碳素材料比较好。
其组成比例如下:
焦炭 50%
无烟煤 30%
石油焦 20%
总之,对碳素材料的要求是:
固定碳含量高,比电阻大,活性高,灰分、挥发分和水分含量要低,粒度适宜。
其他碳素材料:
兰炭是使用块煤经人工堆积、低温闷烧,自燃掉大部分挥发物而炼成的一种土焦(或叫半焦)。
兰炭固定碳含量高,灰粉低,比电阻大。
但也有强度较差,不易干燥、质量不稳等缺点。
因其价格低廉的优势而受到企业的青睐,有些工厂已取得了使用经验。
有些电石炉使用了大量的粉末,虽然利用了焦粉,但却增加了电耗,对操作还不利。
采用合格的焦粒,把筛下焦粉压球代焦,加入电石炉内使用是一个综合利用的途径。
焦球是利用电石废料:
湿焦粉、湿石灰粉按一定比例20%混匀压合好,经CO2碳化好的小扁球。
把它掺入炉料作为碳材使用。
已有多个工厂取得了成功的经验。
4 加强电极糊的管理
电石生产必须选用合格的电极糊,密闭电石炉必须选用密闭电极糊。
不得滥用电极糊,密闭炉不得使用开放炉用电极糊,以防止电极事故,增加能耗。
电极糊应堆放在防雨防尘的库房内,电极糊加入电极筒后,电极筒顶端应有活动盖板。
以防止灰尘落入。
密闭炉用非标准电极糊,一般要求是:
挥发分:
13~15%
灰 分:
<5%
制造电极糊的原料是:
固体碳素材料(无烟煤、石油焦和人造石墨等)和粘结剂(煤焦油、煤沥青)。
用作粘结剂的原料,经焙烧后要能够转变为坚固的焦碳纲,起焦结的作用,形成自焙电极整体。
标准电极糊的粘结剂是单独的煤沥青,软化点为65~75℃。
而非标准电极糊(密闭电极糊)粘结剂是中沥青和煤焦油混合配料,软化点比较低,55+/-2℃(密闭电极糊)。
5 出炉热电石生产余热(显热)的回收。
出炉热电石余热利用:
出炉电石温度一般在1800℃左右,如果冷却后的温度以250℃计,则进入大气的热量理论值如下:
电石产量
(万t/a) 进入大气的热量
万千卡/年
(万千焦/年)
热量折标煤
t/a 备注
4.5 1953000
(8176820) 2790
9.0 3906000
(16353640) 5580
1177 510818000
(2138692698) 729740
即使能利用50%也是很可观的.
杭州电化厂等曾建设隧道窑,利用热电石显热干燥焦碳,但运行时间不长。
在设计中考虑余热回收时,应对余热回收作出技术经济评价。
6 电石炉设计应选取合理工艺.电气参数
要提高热利用率,降低电耗,在设计中必须选取合理的二次电压、电流电压比、电位梯度等主要电气参数。
必须选取合理的电极直径、电极圆心圆直径和炉膛直径等主要工艺参数。
大、中型密闭电石炉和气烧窑在有条件的情况下,宜考虑采用微型计算机数据处理系统,以考核生产指标,进行科学管理。
有条件的情况下,宜考虑装设能进行自动控制和调节的微型计算机系统进行生产控制,以准确调节工艺参数,降低消耗,提高产品质量,以求得最佳节能效果。
7新建电石厂厂址选择
新建电石厂宜靠近优质石灰石矿山,以缩短运输距离,减少运输能耗;同时宜靠近电站,以缩短输电距离,减少输电能耗损失;以及宜靠近铁路,公路或水路,以方便原料的运入和产品的运出,减少运输能耗。
因此,厂址的选择应进行综合评价。
本文不探讨密闭电石炉的操作上的节能问题。
8 电石行业现状和发展方向
8.1电石行业装置水平的现状分析
1977年全国电石产量99万吨(生产能力140万吨),1987年全国电石产量239万吨(生产能力271万吨),2006年全国电石产量1177万吨,是20年前的492%。
目前全国电石炉总产能和台数尚无准确统计数据,今年收集到的几个电石生产主要省份(内蒙、宁夏、山西、四川四省)最新数据整理如下:
内蒙、宁夏、山西、四川四省今年(07年)最新统计数据表
内蒙、宁夏、山西、四川四省今年(07年)最新统计数据表
电石炉容量
(KVA) 四省总台数(台) 台数比(%) 四省总容量
(万KVA) 容量比(%)
≥6000~<16500 362 75 363.04 62
≥16500~<25000 104 22 183.95 31.5
≥25000 15 3 38.25 6.5
合计 481 100 585.24 100
从上表分析可知:
1)内蒙、宁夏、山西、四川是我国电石生产大省,四个省电石炉总容量为585.24万KVA,总产能约在1100万吨左右。
四个省实际总产量缺少数据,按四川提供的产量产能比估算,也要在880万吨以上,占全国06年实际产量的75%左右。
其中内蒙自治区尤为突出,现有电石炉总容量为已达251.93万KVA,总产能将接近500万吨。
目前,这几个省还有多个拟建和在建的电石项目,这几个省也是国家节能减排的重点关注对象,电石产业的发展和乙炔下游产品的发展前景密切相关,一旦产品过剩,供大于求,肯定是优胜劣汰。
各企业必须要有忧患意识,尽早作好节能减排工作,以求得企业生存和持续发展的主动权。
2)从炉型上分析,收集到宁夏、山西的数据整理如下:
宁夏现有100台电石炉,其中有7台密闭炉,密闭炉总容量为16.2万KVA。
数量比占7%。
容量比占10.5%。
山西现有136台电石炉,其中有12台密闭炉,密闭炉总容量为12.1万KVA。
数量比占8.8%。
容量比占9.8%。
宁夏 山西 小计 备注
密闭炉台数(台) 7 12 19
密闭炉台数比(%) 7 8.8 8.1
密闭炉总容量(万KVA) 16.2 12.1 28.3
密闭炉容量比(%) 10.5 9.8 10.2
分析上表可看出,绝大部分(约90%)电石炉为内燃炉。
尽管内燃炉的也可以建设管理得很好,电石炉电耗和环保指标都可达标,但从节能角度分析,大量炉气潜热没有回收利用。
从国家宏观产业政策看是很不合理的。
试定量分析,即使现有的密闭炉装置炉气已经全部回收利用,也还有90%的内燃炉炉气潜热没有利用。
如果用上表数据粗线条估算全国电石行业,每年则白白浪费掉的炉气潜热折标煤约为188万吨*90%=169万吨,数量惊人。
3)从单台电石炉容量上分析,收集到内蒙、宁夏、山西、四川四省的数据整理如下:
电石炉容量(KVA) 台数比(%) 容量比(%)
≥6000~<16500 75 62
≥16500~<25000 22 31.5
≥25000 3 6.5
分析上表可看出,绝大部分电石炉单台容量在16500KVA以下,一般讲是在小型炉之列。
尽管有的小型炉已经取得了不错的生产成绩,但由于小型炉在装备和自动化水平等方面的总是存在先天不足,从现代工业发展方向看是趋向大型化、自动化、集约化。
大型化的电石炉易于实现电石炉的密闭化和自动化,从而达到更好的节能目标。
8.2电石行业的发展方向
由于历史的原因,我们有些电石企业的装置水平较低、单台装置规模较小。
需求量大、发展迅猛是我国电石行业近年发展的特点。
但我们要注意电石发展中存在的重复、低水平建设问题,如果不加以合理地调控和引导,任其发展,必然会加剧生产能力过剩、资源消耗高、技术水平低、安全条件差、污染严重等矛盾。
因此应从全局和可持续发展的角度,进一步加大工业布局调整的力度,通过技术改造和进步,做大做强现有的符合国家产业政策要求的企业,严格按照行业发展的规划,限制发展小规模、低水平、重污染的企业。
《电石行业准入条件》的实施,对遏制低水平扩张和盲目发展,将会起到积极作用。
目前的准入条件,考虑到电石行业实际困难,在装置规模和炉型上要求并不够高,但节能减排是大势所趋,电石生产的大型化、密闭化势在必行,电石生产企业要充分利用好目前过度时期的时间,从国家的大局和企业自身可持续发展的角度需求出发,冷静研究、慎重决策企业自身发展规划,从而保证企业及全行业持续稳定健康发展。