造船基础知识.docx
《造船基础知识.docx》由会员分享,可在线阅读,更多相关《造船基础知识.docx(19页珍藏版)》请在冰豆网上搜索。
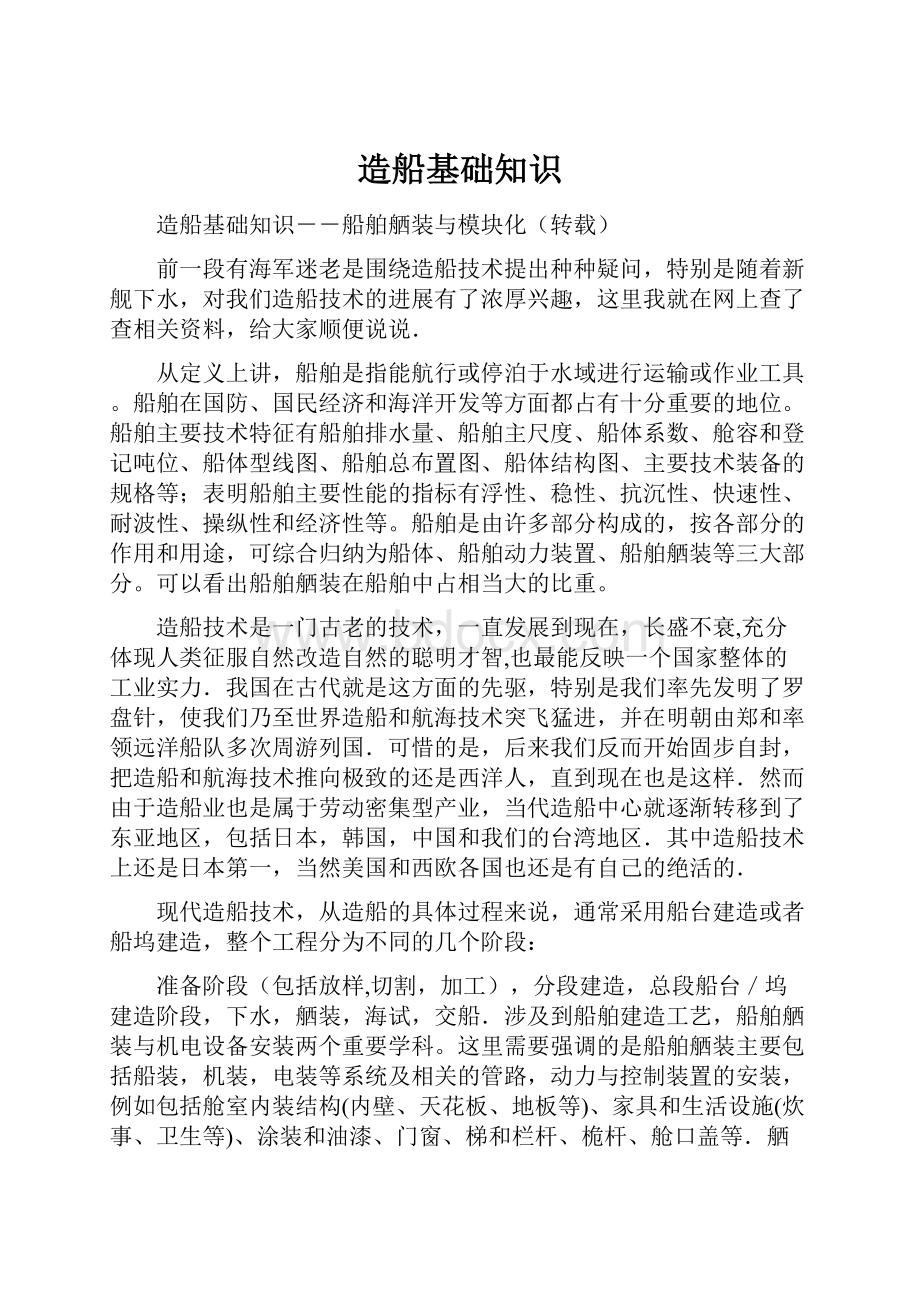
造船基础知识
造船基础知识--船舶舾装与模块化(转载)
前一段有海军迷老是围绕造船技术提出种种疑问,特别是随着新舰下水,对我们造船技术的进展有了浓厚兴趣,这里我就在网上查了查相关资料,给大家顺便说说.
从定义上讲,船舶是指能航行或停泊于水域进行运输或作业工具。
船舶在国防、国民经济和海洋开发等方面都占有十分重要的地位。
船舶主要技术特征有船舶排水量、船舶主尺度、船体系数、舱容和登记吨位、船体型线图、船舶总布置图、船体结构图、主要技术装备的规格等;表明船舶主要性能的指标有浮性、稳性、抗沉性、快速性、耐波性、操纵性和经济性等。
船舶是由许多部分构成的,按各部分的作用和用途,可综合归纳为船体、船舶动力装置、船舶舾装等三大部分。
可以看出船舶舾装在船舶中占相当大的比重。
造船技术是一门古老的技术,一直发展到现在,长盛不衰,充分体现人类征服自然改造自然的聪明才智,也最能反映一个国家整体的工业实力.我国在古代就是这方面的先驱,特别是我们率先发明了罗盘针,使我们乃至世界造船和航海技术突飞猛进,并在明朝由郑和率领远洋船队多次周游列国.可惜的是,后来我们反而开始固步自封,把造船和航海技术推向极致的还是西洋人,直到现在也是这样.然而由于造船业也是属于劳动密集型产业,当代造船中心就逐渐转移到了东亚地区,包括日本,韩国,中国和我们的台湾地区.其中造船技术上还是日本第一,当然美国和西欧各国也还是有自己的绝活的.
现代造船技术,从造船的具体过程来说,通常采用船台建造或者船坞建造,整个工程分为不同的几个阶段:
准备阶段(包括放样,切割,加工),分段建造,总段船台/坞建造阶段,下水,舾装,海试,交船.涉及到船舶建造工艺,船舶舾装与机电设备安装两个重要学科。
这里需要强调的是船舶舾装主要包括船装,机装,电装等系统及相关的管路,动力与控制装置的安装,例如包括舱室内装结构(内壁、天花板、地板等)、家具和生活设施(炊事、卫生等)、涂装和油漆、门窗、梯和栏杆、桅杆、舱口盖等.舾装作业面广,工程量大,舾装工程量通常占船舶建造总工程量的50%到60%,对复杂船型甚至更高.
为了减少船台/坞的占用周期,提高劳动效率,现在通常采用预舾装的办法.所谓预舾装就是将传统的码头,船内的舾装作业提前到分段,总段上船台(船坞)前进行的一种舾装方法.预舾装是在船体分段上船台(船坞)前将舾装件采用单元化预先组装.采用分段预装和总段预装的方法使得可以在地面上进行平行的分散作业,从而使高空作业平地做,外场作业内场做,仰装作业俯位做,减少了码头,船内多工种的混合作业.预舾装改善了作业条件,减少了劳动强度,提高了工作效率,大大减少了建造周期.
目前比较流行的,也是当前大家老是强调的模块化造船方法,其实具有125年历史的著名德国Blohm+Voss公司早在上个世纪七十年代初就开始开发模块化这一先进的舰船建造方法.多少年来,模块化造船方法得到了深入的研究和广泛的应用.从舰船总体到主机推进系统,全船控制系统,自动化系统,武器装备,机电装置,舾装设备纷纷采用了模块化技术,尤以居住舱室,机电装置,自动化系统及武器装备方面的模块化发展最快,效果更佳。
而且这种思想也被移植到其他制造业。
更为形象地讲,就好象现在的电脑配件,有了接口,按照说明书采用正确方法直接插入适当位置就可以了,大大简化了作业和装配难度。
国外造船先进国家,舾装单元已采用标准化,模块化。
通过机电设备模块化,标准化和过程简单化,减少船舶设计,生产,采购等整个寿命期运行以及保障方面所需的时间和复杂性降低船舶建造和服役期内的总成本。
这里所说的标准化,是指舾装设备,甚至分段都具有成批生产的同样规格的设计,通过大批量生产可以进一步降低成本,提高装配作业的效率,当然具体实施起来还有一定的难度,也是造船技术的发展方向之一。
美国,英国,前苏联,德国,日本,法国,挪威,丹麦,荷兰等众多工业化国家在标准化,模块化造船应用方面都取得了引人注目的成就,并且呈不断发展的趋势,模块化技术的研究和应用正在导致舰船设计思想,建造流程,维修管理方法上的重大变革,可以说有革命意义。
美国海军已提出,未来的舰船将使用由标准组件组成的模块来设计和建造.在民船领域,模块化建造将能充分发挥标准化和通用化的优势,可使技术复杂,批量小的船舶建造取得更大的效益.模块化建造方式有可能成为未来造船业的方向.
相比之下,我们在标准化,模块化造船技术这方面的努力还十分缓慢,比较日本和其他先进国家造船业船台船坞建造周期还是过长,虽然在新船的建造上已经初步有了体现,还需要奋起直追.
最后还要说明一点,船舶设计中模块化设计的思想和模块化造船技术是两回事,属于不同的概念,不能混为一谈。
说明
本原则工艺是4000HP拖轮生产准备和施工过程中的技术文件。
本船主船体线型及结构的放样采用微机与手工相结合的方法,放样精度执行CB/T3195-1995标准。
全船管系、通风、电气电缆等采用综合放样工艺。
本船采用分段建造法。
在车间胎架上建造各分段,验收后吊运至船台进行大合拢。
船体合拢过程中,上层建筑合拢前,应将机舱内的主要设备吊装定位,并采取有效的防火安全措施。
本原则工艺说明书编制的主要依据:
(1)4000HP拖轮全船技术规格书
(2)施工图纸资料
(3)中国的GB、CB、日本JIS工业标准,厂标建造标准。
一、船体
本船为双“Z”型推进器沿海港作拖轮。
本船为单甲板、横骨架式、三层甲板室全电焊结构。
机舱、船员舱、锚链舱设有双层底,其余为单层底,其构件满足中国船级社的“钢质海船入级与建造规范”的要求。
1、主要要素
总长
垂线间长
型宽
型深
设计吃水
肋距
梁拱
2、主要性能
设计航速节
系柱拖力
二、船体主要材料及技术条件
1、钢材
本船船体钢材及型材采用CCS认可的A级船用碳素钢(舵桨座为B级),但在下料之前应将其材料的出厂报告、机械性能、化学成分及CCS证书送CCS检验机构认可,并存档与交船资料一同交付船东。
2、焊接材料
本船尽量采用CO2气体保护焊,焊丝为3Y3级。
手工电弧焊采用CCS“I”级焊条,自动焊采用H08A焊丝。
三、船体分段划分
本船共划分为11个分段
四、船体分段建造方案
各分段建造方案见下表,各分段在胎架建造完毕报检合格后,吊运至船台大合拢。
分段/合拢序号重量(t)建造方法
001/137正造胎架
002/222反造甲板胎架
003/331正造胎架
004/420反造甲板胎架
005/533反造甲板胎架
006/634反造甲板胎架
007/737反造甲板胎架
008/827反造甲板胎架
009/921反造甲板胎架
010/106反造甲板胎架
011/113反造甲板胎架
五、船体建造精度要求
1、本船船体建造精度要求按中国船舶行业标准CB/T3195-1995“中小型船舶船体建造精度”验收。
2、船体主尺度公差
船长(总长)+/-30mm
型宽+/-10mm
型深+/-9mm
3、船体首尾端上翘、下垂值为+/-20
六、船体建造技术要求
1、钢材发料时,其表面质量应符合CB*3293要求
2、全船大部分外板、中龙骨、旁龙骨及甲板绗材、强肋骨、舷侧纵绗、肋板等采用微机套料,数控切割,数控下料以外的尽量采用半自动切割或剪料,船体零部件的制造加工技术要求参照CB/T3195-1995执行。
3、各类底座面板边缘必须进行倒角磨光。
4、曲面外板的形状加工,应选择适当压模,使加工件不至于产生明显的加工痕迹,确保其加工的光顺性。
5、建造、合拢前应做好中心线、肋骨检验线、水险(肋骨、舱壁地龙)并留有永久性标志并将中心线、肋骨线、水线反至舱内。
6、分段装焊完毕后,应在未脱胎前进行火工矫正,消除应力。
7、各分段在脱胎后,未吊离胎架前,质检部门应进行分段完工测量交验,并做记录备查。
8、全船在变形矫正及密性实验结束后,质检部门应进行船体实测,并做好记录,作为完工交船数据。
9、船体焊接程序原则
全船焊接程序及焊接工艺按《焊接工艺及规格表》执行。
10、船体焊接质量检验
(1)焊缝外观质量按(CB999-82)《船体焊缝表面质量检验标准》要求验收。
(2)船体外板焊缝内部质量检查采用X光拍片和超声波探伤,其具体部位见探伤图。
X光及超声波要求按(CB3323-89)《钢熔化对接头射线照相和质量分级》执行。
(3)船体结构焊缝出现缺陷时,应按《船体结构焊缝缺陷修整技术文件》CB125-73要求进行修整。
七、船体密性实验原则
1、密性实验按密性实验大纲要求执行。
2、密性实验前,受试舱室各类工程应完工交验,对局部要在密性试验后才能完成的工程,该部位船体应做补充实验。
3、实验过程中,如发现结构弱点或渗漏现象,必须进行及时的修补,并再试。
八、除锈、油漆
1、除锈方法
本船除主船体外板采用抛丸除锈外,其余钢材、型材及管材均采用化学除锈涂底漆。
2、分段及全船油漆按规格书及油漆工艺进行,并依据CB/Z231-87“船体涂装技术要求”进行检验。
3、下水前外板需经二次除锈方可涂装。
九、铁舾装建造精度要求
1、所有铁舾装件表面应光滑,无裂纹、毛刺及其它缺陷。
2、锚设备应满足CCS规范要求。
3、各类舱口盖门窗应开启灵活,并提供CCS保证书。
4、舾装件自制安装应满足CB*3324-87《钢质舾装件精度要求》。
5、消防救生设备应满足SOLAS规范要求。
十、下水
当船舶大部分建造工程完工时,即可下水。
1、本船下水前的完工程度如下:
(1)船体全部完工,密性实验完毕。
(2)机舱、舵桨仓主要设备安装就位,轴系安装完毕。
(3)锚机、锚及下水所必须的系泊装置安装完毕。
(4)部分舾装件如:
通海阀,防蚀锌板,橡胶护舷等安装完毕。
(5)船体油漆和载重线及吃水标志绘制完毕。
2、本船采用机械化纵向下水工艺,船体合拢小车兼做下水小车用。
下水墩木采用木质墩木并用木楔加紧。
中国液化天然气船的建造
广东LNG试点项目由国家计委统筹策划、协调组织。
在开展广东LNG试点项目上,是按照政府的既定方针,支持中国LNG航运业的发展,支持中国造船企业积极开拓LNG船的建造。
这既符合国际上其他LNG进口国的惯例,也是中国经济发展的需要。
目前,中国在LNG运输和造船方面的现状,概括起来应是:
有能力、有希望、有困难。
有能力即指中国的运输业和造船业有雄厚的物质基础,有多个有实力的船厂,有强大的运输队伍,能够担当起这项任务,有希望即指广东LNG试点项目是我国政府支持的第一个LNG项目,将有助于东南沿海地区调整能源结构和产业结构、改善环境,提高人民生活水平。
困难主要是指在液化天然气的运输和造船方面尚无经验。
中国船厂需要在项目开展过程中学习国外先进经验和技术,在研究、设计、生产、管理、标准等方面达到LNG船建造要求,也希望国外有经验的企业加强与中方合作。
希望有能力参与LNG项目竞争的国内船厂抓住机遇,作好充分准备,加强与外国企业的合作,吸收国外已成熟的造船技术与经验,推动中国造船业的发展。
建造方案
A:
全部由国内船厂承建,交船间隔=坞期7~8个月,考虑国内船厂的具体情况,2005年底仅能交付一条船,且船厂的技术积累时间明显不足。
B:
第一条船由国外船厂承建,其余在国内船厂承建,交船间隔=坞期7~8个月(国内船厂)、交船间隔=坞期6个月(国外船厂)。
考虑到国内船厂的LNG船建造周期要比国外长6个月,即42个月,如国内船厂2006年底交船,则国内船厂因比国外船厂起步晚半年,这样就可以解决设计图纸的消化吸收和人员的深度培训。
此方案较为可行。
所以从实际操作来看,广东LNG运输船建造最现实的方案是:
首制船在国外建造或与国外有经验的船厂合作建造,后续船在国内船厂建造,国外船厂提供技术和派专家指导,保证质量和进度。
同时通过厂际互动的原则,培养一批设计、建造管理LNG船的专业技术人员和工人。
船型的选择
目前LNG船主要的液货舱舱为薄膜型(membrane)和球型(MOSS)两种。
从总体上看薄膜型LNG船在船型性能方面要优于MOSS型,但MOSS型具有货物装载限制较少等使用操作上的优点,而且,在早期的LNG海运中,MOSS型船占有较大优势。
薄膜型船的液货舱按其采用绝热材料和施工方式的不同分为GTT型和MarkⅢ型
MarkⅢ型绝缘目前国内建造有一定的难度,而GTT型易于实现绝缘生产的国内建造。
GTT型在船体建造工艺方面比MarkⅢ型要求更高,无论是在精度控制还是焊接要求方面,掌握了GTT型的建造要求,基本上也就掌握了MarkⅢ型的建造技术。
在液货舱主、次屏壁的焊接上,GTT型可大量采用自动焊,焊接质量容易控制,而MarkⅢ型手工焊接较多,焊接质量不易控制。
目前国内建造的倾向于选用GTT型LNG船。
建议选用138000m3级的薄膜型LNG船,采用GTT型的液货舱型,其主尺度和主要性能如下:
舱容:
138000m3;
货舱数量:
4;
总长:
277米;
两柱间长:
266米;
型宽:
米;
型深(到主甲板):
26米;
设计吃水 米
主推进功率MCR:
40000hp/96rpm;
航速:
节;
货舱型式:
GTT。
广东深圳-澳大利亚,该航线2500海里,可适当放大液货舱容积,以船东实际要求为准,可通过加长液货舱长度实现。
液货装卸系统的技术关键是超低温泵和不锈钢管路的高质量焊接、安装工艺的实施及管路和绝缘铺设。
推进系统采用蒸汽透平或双燃料柴油机。
尽管我国能够建造LPG船、化学品船,但从未建造过LNG船,因此在船舶设计、制造、国外设备、材料引进、质量管理、生产管理等方面,必须采取积极、稳妥、科学务实的工作态度和有效措施。
LNG船设计建造技术难度大,工期长,企业必须制订造船质量控制、成本控制和按时交船的保障措施,以预防和控制风险。
所具备的条件
LNG船是国际上公认的高技术、高附加值、复杂型船舶,必须本着积极、稳妥、科学、务实的态度进行研究、开发建造,力争填补我国在这一行业的空白,推动国家造船业的发展。
设施优势
我国主要船厂拥有能够进行钢材预处理、数控切割和水下等离子切割的钢材处理中心,具有高自动化程度的平面分段制作流水线及船体合拢、船舶舾装、船舶涂装等多条生产线的集配、机装、电装、甲装、居装等完整的配套齐全的、具有国际先进水平的造船基础设施。
已经进行的前期准备工作
组织专家对建造LNG船相关的设计、建造信息、有关规范、规则、技术专利和市场前景进行了大量的调研工作。
参加了国内外举办的液化天然气专题讲座,邀请许多LNG船方面的专家和相关的国际著名船级社进行专题讲座和相互间的技术探讨。
与薄膜专利公司法国GTT公司进行了技术交流,就LNG船蒸汽透平动力系统进行技术交流,并考查过LNG船焊接技术和材料,与BV、DNV、LR、JIS、GL、ABS等进行了LNG船及其液货系统的详细技术交流,对两种类型液货系统的技术特点、建造工艺、推进方式、建造工艺有了全面的认识。
液货舱的制造技术是LNG船制造的关键环节之一,薄膜型液货舱制作工艺细致,技术复杂,且施工周期长,工作量大。
沪东中华造船厂制造了E-80模型舱的建造,已于2001年7月25日完成,并得到GTT公司和LR、BV、ABS、DNV等船级社的认可和高度评价。
加强国际合作
合作内容
应最大限度地利用国外船厂和专利公司在LNG船设计与建造中的成熟经验和专门技术,认真做好设计、建造中的各项工作,特别是技术培训工作,确保质量。
借鉴日本和韩国的成功经验,选择一家拥有LNG船建造和管理经验并且愿意和中国船厂合作的国外船厂,联合参与设计与制造,利用其成熟的技术、组织体系和管理手段不失为一上策。
在与国外专利持有者和造船厂签订的合作协议中,双方应详细规定在技术、设计、设备采购、建造等各阶段双方合作的方式和方法,对方在各阶段所提供设计图纸的范围及技术培训,专家来厂技术指导的内容和时间安排,协议应具有实际的可操作性。
特别要强调在设计、建造、质量控制等各方面的配合。
外方应向我企业提供整套的LNG船的设计图纸,技术文件、制造技术和全面的技术帮助,包括:
LNG船的基本设计;
LNG船的施工设计、工艺、所有设备的安装调试等有关的技术文件;
LNG船的生产管理组织体系;
LNG船质量管理体系;
工程技术人员和技术工人的全面培训;
LNG船建造规范。
LNG船建造规范、规则及港口国法定要求的熟悉与执行,特别是IGCCode(国际散装运输液化气体船舶构造和设备规则)的熟悉与执行。
质量控制与保障
培训专业技术工人,为了确保LNG船的建造成功,对参与LNG船建造的工人应进行专业技术培训,涉及的内容应包括:
LNG船基础知识,推进系统工艺培训,液货装卸系统工艺培训,液货舱系统工艺培训,工艺、建造人员的培训。
在LNG船的建造中,要编制LNG船专用建造工艺和质量标准,并严格贯彻执行这些专用工艺和质量标准。
LNG船代表世界货轮建造的顶尖技术,建造工艺和质量要求高,必须建立全新的造船概念。
中国船厂在硬件和软件方面初具建造LNG船的基本条件,但在生产过程的质量控制、液货舱薄膜的焊接工艺、绝缘木箱制作过程、船用发动机系统及规范标准等方面存在技术难点,通过与国外有经验的船厂、船级社的合作,进行技术引进和人员培训,吸收国外造船的成熟技术与专门经验,来提升质量的安全管理系统。
妥善落实和解决这些问题后,我国船厂是能够承担LNG船的设计、建造工作的。
广东LNG项目的开展,标志着由国家计委倡导的LNG项目运输以中方为主,带动LNG船国内建造的工作向前迈进了一大步。
应以广东LNG进口项目为契机,在尊重科学、尊重实践的基础上,早日实现我国LNG船舶承建的突破。
【论文】船舶焊接技术现状与展望
陈家本中国船舶工业集团公司第十一研究所摘要:
讲述了我国船舶焊接技术的现状,以及我国船舶焊接技术与发达国家之间的差距,展望了21世纪的船舶焊接技术。
前言
船舶焊接技术是船舶工业的主要关键工艺技术之一。
目前,世界各主要造船企业在20世纪90年代中期已普遍完成了一轮现代化改造。
同时,在此基础上又陆续启动了新一轮现代化改造计划。
投资目标很显然集中于高新技术,投资力度进一步加大,大量采用全新的造船焊接工艺流程,高度柔性的自动化焊接生产系统和先进的焊接机器人技术,以保证这些造船强国在国际竞争中具有独特的技术优势。
进入21世纪,面对新的挑战和机遇,对我国船舶焊接技术进行综合分析研究是极有现实性和针对性的,并以此来激励我们去做好当前必须做的各项工作,大力推进高效焊接技术,加快焊接技术改造步伐,努力将相对资源优势转化为科技竞争优势,促进船舶产业进步和产业升级。
否则,将不但难以实现船舶工业振兴的宏伟发展计划,甚至会出现我国现有的国际市场份额都难以维持的严峻局面。
1船舶焊接技术现状
受20世纪70年代中期和20世纪80年代期2次严重造船危机打击,世界造船业总局面发生了重要变化。
日本、韩国、中国(包括台湾省)造船业迅速发展起来,使世界造船中心由欧洲转向东亚,东亚地区的造船量占世界造船总量的78%(以总吨计算),在东亚地区造船诸国中又形成了日本、韩国、中国大连和上海的世界造船“金三角”地区。
这个狭小的“金三角”地区聚集着众多的世界一流的造船企业、研究开发中心及其船舶配套设备厂,其造船量占世界造船量的70%以上,有“世界造船基地”之称。
中国的造船能力和市场份额有明显增长,并将成为世界造船格局演变的重要推动力量。
我国造船业的规模据国家统计局统计,1999年年销售额超过500万元人民币的修造船企业有461家,职工达万人,销售总额达亿元人民币。
其中海船造修厂有72家,职工有万人,销售额达到亿元。
目前我国至少有30家船厂在建造出口钢质海船。
其中中国船舶工业集团公司9家,中国船舶重工集团公司4家,其他17家。
自20世纪90年代后半期起,我国造船业发展的一个重要特点是:
地方的和中外合资的与外方独资的造船企业发展迅猛,并形成了与中国船舶工业、中国船舶重工2大集团公司“三分天下”的格局。
我国的造船能力目前约为500万载重吨,占世界的5%~6%,预计2005年可达800万载重吨或更高水平占世界的12%~15%。
自改革开放以来,我国造船业在技术水平、船舶类型、建造质量以及建造周期等方面都取得了长足的进步,具备了一定的国际竞争力。
其中船舶焊接技术的长足进步贡献突出,并取得了较好的经济效益。
1.1造船生产中应用的高效焊接工艺方法
这些高效的焊接方法从20世纪70年代末期的3~5种发展到现在的35种,基本满足了建造出口船舶,海洋石油平台以及各类非船舶产品的需要。
1.2焊接高效化率大幅度提高
焊接机械化、自动化率自20世纪70年代以后有了较大幅度的提高,如1所示。
图1焊接高效化率、焊接机械化、自动化率增长图
船厂的焊接设备构成逐渐趋于合理
旋转式直流焊机已从1983年的%下降到2001年的%,最终将全部被淘汰,取而代之的是整流焊机、CO2气保护焊机、交流焊机、埋弧焊机以及船用机械化自动化平角焊机、垂直气电焊机等。
由于采用高效节能焊接电源可每年节约电能见表1。
表1船厂系统应用焊接设备更新后概算节能
1.4船舶焊接新工艺新技术新材料的应用与推广
由于船厂的产品特点是多品种、小批量,产品结构和材料变化频繁。
近年来,随着转换现代造船模式,大力推进区域造船法,使船舶焊接技术也发生了较大的变化,其中比较突出的是一些重点骨干船厂先后都引进了国外先进的平面分段装焊流水线,采用了拼板工位多丝埋弧自动焊单面焊双面成形新工艺、新装备。
其焊接范围可分别用于5~20mm和10~35mm的船用板材的对接拼板,同时在按区域造船的理论指导下,对船体的平面分段构架的装焊也采用了半自动或自动气保护角焊工艺,使焊接效率大大提高。
对于船台大合拢时的垂直对接缝(长度达15~30m)的焊接,原采用手工电弧立焊工艺,其缺点是生产效率低,劳动强度大,对焊工操作技术要求高,焊接质量不稳定。
我国造船行业从20世纪80年代中期开始应用CO2气电垂直自动焊工艺,使焊接效率大大提高。
对于船台大合拢时的垂直对接缝(长度达15~30mm)的焊接,原采用手工电弧立焊工艺,其缺点是生产效率低,劳动强度大,对焊工操作技术要求高,焊接质量不稳定。
我国造船行业从20世纪80年代中期开始应用CO2气电垂直自动焊工艺,焊接时,在焊缝背面安放梯形槽陶质衬垫,焊缝正面采用水冷铜滑块强制成形,以保持熔池稳定和焊缝成形良好,其焊接生产效率比常规手工焊提高5~7倍,焊接质量稳定,目前已在各主要船厂得到普遍应用。
1.5焊接材料应用方面
近几年药芯焊丝的应用异军突起,由于药芯焊丝具有熔敷效率高、焊缝质量好、焊接飞溅少、容易实现机械化和自动化焊接。
目前船厂已普遍采用药芯焊丝来焊接船舶结构。
同时它又与CO2焊接工艺技术相结合,使船厂在生产中尝到了甜头,所以目前一些船厂认为CO2气保护药芯焊丝焊接将是作为船厂的主要焊接工艺与焊接材料。
它的应用每年都呈明显的增长趋势,见表2。
表2气体保护药芯焊丝的应用比例%
由于大量推广应用CO2气保护药芯焊丝,从而也大大提高了我国船厂焊工人均日消耗的焊接材料量,如表3所示。
这也进一步降低了我国的造船成本缩短了船舶的建造周期。
另外在一些高附加值船的建造与非船产品如大型钢结构高层建筑大型桥梁等的焊接技术上也开创了许多创新的焊接技术取得了较大的经济效益和社会效益。
2与日本韩国之间的差距
我国的造船技术与日本、韩国之间尚存在着较大的差距。
我国