接触网零部件制造工艺及装备.docx
《接触网零部件制造工艺及装备.docx》由会员分享,可在线阅读,更多相关《接触网零部件制造工艺及装备.docx(6页珍藏版)》请在冰豆网上搜索。
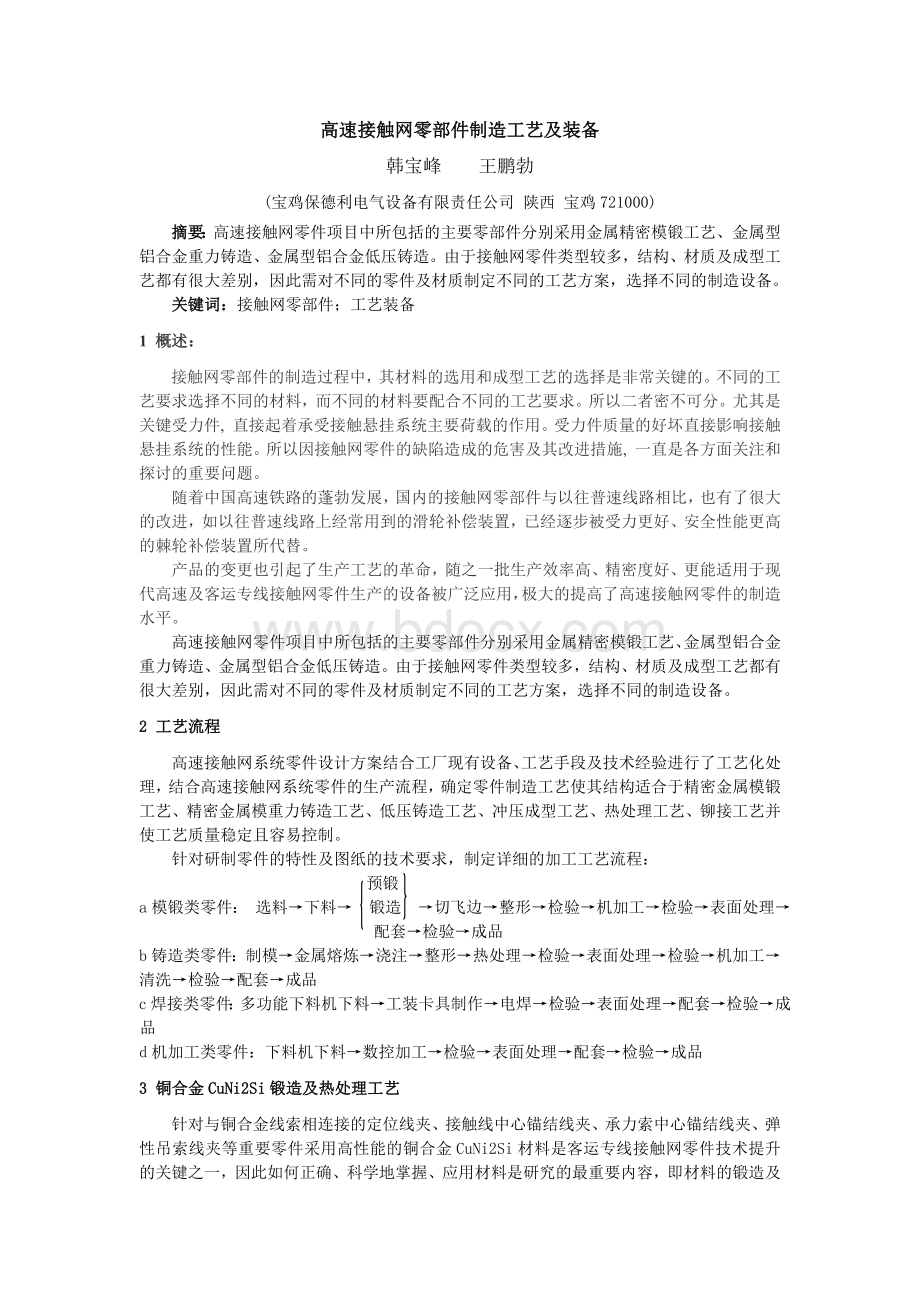
高速接触网零部件制造工艺及装备
韩宝峰王鹏勃
(宝鸡保德利电气设备有限责任公司陕西宝鸡721000)
摘要:
高速接触网零件项目中所包括的主要零部件分别采用金属精密模锻工艺、金属型铝合金重力铸造、金属型铝合金低压铸造。
由于接触网零件类型较多,结构、材质及成型工艺都有很大差别,因此需对不同的零件及材质制定不同的工艺方案,选择不同的制造设备。
关键词:
接触网零部件;工艺装备
1概述:
接触网零部件的制造过程中,其材料的选用和成型工艺的选择是非常关键的。
不同的工艺要求选择不同的材料,而不同的材料要配合不同的工艺要求。
所以二者密不可分。
尤其是关键受力件,直接起着承受接触悬挂系统主要荷载的作用。
受力件质量的好坏直接影响接触悬挂系统的性能。
所以因接触网零件的缺陷造成的危害及其改进措施,一直是各方面关注和探讨的重要问题。
随着中国高速铁路的蓬勃发展,国内的接触网零部件与以往普速线路相比,也有了很大的改进,如以往普速线路上经常用到的滑轮补偿装置,已经逐步被受力更好、安全性能更高的棘轮补偿装置所代替。
产品的变更也引起了生产工艺的革命,随之一批生产效率高、精密度好、更能适用于现代高速及客运专线接触网零件生产的设备被广泛应用,极大的提高了高速接触网零件的制造水平。
高速接触网零件项目中所包括的主要零部件分别采用金属精密模锻工艺、金属型铝合金重力铸造、金属型铝合金低压铸造。
由于接触网零件类型较多,结构、材质及成型工艺都有很大差别,因此需对不同的零件及材质制定不同的工艺方案,选择不同的制造设备。
2工艺流程
高速接触网系统零件设计方案结合工厂现有设备、工艺手段及技术经验进行了工艺化处理,结合高速接触网系统零件的生产流程,确定零件制造工艺使其结构适合于精密金属模锻工艺、精密金属模重力铸造工艺、低压铸造工艺、冲压成型工艺、热处理工艺、铆接工艺并使工艺质量稳定且容易控制。
针对研制零件的特性及图纸的技术要求,制定详细的加工工艺流程:
预锻
a模锻类零件:
选料→下料→锻造→切飞边→整形→检验→机加工→检验→表面处理→配套→检验→成品
b铸造类零件:
制模→金属熔炼→浇注→整形→热处理→检验→表面处理→检验→机加工→清洗→检验→配套→成品
c焊接类零件:
多功能下料机下料→工装卡具制作→电焊→检验→表面处理→配套→检验→成品
d机加工类零件:
下料机下料→数控加工→检验→表面处理→配套→检验→成品
3铜合金CuNi2Si锻造及热处理工艺
针对与铜合金线索相连接的定位线夹、接触线中心锚结线夹、承力索中心锚结线夹、弹性吊索线夹等重要零件采用高性能的铜合金CuNi2Si材料是客运专线接触网零件技术提升的关键之一,因此如何正确、科学地掌握、应用材料是研究的最重要内容,即材料的锻造及热处理工艺是能否成功制造出优质零件的关键、难点。
对此进行了此种材料的化学成分、机械性能,初步制订出产品的试制工艺,经过试验、试制、比较,最终确定了国产铜合金CuNi2Si产品的锻造及热处理工艺,形成完整、系统的铜合金CuNi2Si锻造工艺及热处理工艺,锻件的机械性能、外观及内在质量的检验标准。
因产品性能最终取决于锻造工艺及锻后热处理工艺,制定试棒及产品模具的预热等锻造工艺参数:
包括材料塑性成型性能研究、锻造设备和锻造能量的选取,锻造温度、加热时间、成形速度与变形量、锻后热处理工艺。
针对生产的CuNi2Si试棒及产品中各种缺陷的种类,主要分析CuNi2Si合金锻件产生过热、过烧、锻造裂纹、切边撕裂、折叠、晶粒粗大、应力腐蚀开裂、氢气病等缺陷等锻造及热处理缺陷的原因,研究采取措施,并实施。
1)过热、过烧:
CuNi2Si合金过烧时,模锻件表面粗糙,无金属光泽,边缘处开裂;过烧后,断口氧化很严重,无金属光泽,裂纹沿晶界扩展。
为防止过热、过烧,严格控制加热温度和时间,在精密锻造中采用无氧化的加热方法,由于感应炉加热具有升温快,炉温易控制,氧化和脱碳少,劳动条件好,便于实现机械化和自动化的优点,因此采用感应加热炉进行原材料毛坯加热。
2)锻造裂纹
CuNi2Si合金锻裂的原因主要有下列几方面:
①坯料内部或表面有缺陷;②锻造温度不合适,材料塑性低;③变形程度过大或拉应力过大;锻造温度对CuNi2Si合金的塑性影响很大。
CuNi2Si合金中由于加人了大量合金元素,始锻温度低,锻造温度范围窄,并存在中温脆性区。
加热温度过高,容易产生过热、过烧,引起锻裂或粗晶。
锻造温度过低时,由于再结晶不充分,塑性降低,也常常产生裂纹。
对策:
①材料应具有可锻性,正确选择材料的状态及制造方式,对于裂纹在表面的进行车皮;②要控制锻造温度不要过高或过低,并要避开中温脆性区;③设计零件的工艺结构应力求简单对称;有合理的锻造斜度和圆角半径。
3)切边撕裂:
CuNi2Si合金锻件在胎模锻和模锻后,如立即进行切边,往往会在切边处有撕裂锻件本体的现象。
当锻件冷却后再切边时,就可避免这种缺陷。
4)折叠:
CuNi2Si合金变形时,表面容易起皱。
因此,较易产生折叠。
例如,拔料时,如变形后的台阶较尖锐,在第二次锤击时就容易产生折叠。
因此,锻造铜合金时,工具和模具转角处的圆角半径要大一些,并要注意润滑;对于一些高度与直径比例不大的管接,适于采用在漏盘中挤压成型;对较易产生折叠的铜合金锻件,要考虑到以后的清理,在确定加工余量和计算用料时,比碳钢取得大些。
5)晶粒粗大:
CuNi2Si合金晶粒长大后不能像碳钢那样通过热处理加以细化,因此,晶粒粗大将使产品性能下降。
为了避免形成上述粗大晶粒,在锻造时我们注意以下几点:
①锻造时每次变形程度应大于10%~15%;②为保证适宜的终锻温度,应根据成形方式和变形量大小选择合适的始锻温度。
③(α+β)CuNi2Si铜的加热温度应稍低于α+β→β的转变温度。
6)应力腐蚀开裂:
如果CuNi2Si合金锻件内存在残余应力,则在潮湿大气中,特别是在含氮盐的大气中会引起应力腐蚀开裂,也称季裂。
防止这种缺陷的对策是:
①锻造时,应使锻件上各处的变形量和变形温度比较均匀。
例如,锻造长轴类铜合金锻件时,应将工件经常调头变形,使各部分的变形温度相近,以减小内应力;②铜合金锻造后,要及时进行消除应力退火。
-
7)氢气病:
所有铜镍合金,在高温下极易氧化。
含有氧的铜合金,如在含有H2、CO、CH4等的还原气氛中加热,则这些气体会向金属内扩散,与Cu2O化合而生成不溶于铜的水蒸气或CO2。
这种水蒸气具有一定的压力,力图从金属内部逸出,结果在金属内部形成微小裂纹,使合金变脆,即氢气病。
因此,加热铜合金时,炉子气氛最好是中性的。
针对以上锻造缺陷产生的原因,我们在锻造工艺制定与验证时避免形成缺陷因素的存在,制订合理的锻造工艺。
形成国内外CuNi2Si合金材料包括表面质量、化学成份、机械性能等项目的企业验收标准。
以确保铜合金接触网零件的优质、安全、稳定,加速国外产品的国产化进程,确定定位线夹、接触线中心锚结线夹、承力索中心锚结线夹、弹性吊索线夹等铜合金CuNi2Si接触网零部件采用金属模锻工艺制造,原材料化学成分进行控制,锻造温度、冷却方式的试制确定后严格按工艺实施,直接在模具内采用锻造成型的方法,避免压合组织内部的微小裂纹、气孔等缺陷,锻造后通过时效强化热处理,保证零部件整体机械性能,尺寸精度高,内在组织细密。
4铝合金ENAC-AlSi7Mg0.3、ENAC-AlSi7Mg0.6铸造及热处理工艺
结合国外铝合金ENAC-AlSi7Mg0.3、ENAC-AlSi7Mg0.6铸件原型产品的设计方案,确定腕臂支持类零件如:
承力索座、套管座、双耳套筒、定位支座、锚支定位卡子等零件采用铝合金ENAC-AlSi7Mg0.3、ENAC-AlSi7Mg0.6,通过试制,确定合理熔炼及浇注工艺,采用淬火及时效处理改善件内部的显微组织及使用性能,提高铸件的强度和塑性。
4.1接触网铝合金铸件主要采用金属型重力铸造造,其内在组织致密、外观质量好、结构可靠、安全性高。
熔炼工艺是铸件生产中的一个有机组成。
一个优质铝铸件的获得,需要有一套优化的铸造方法、铸造工艺、熔炼工艺及浇注工艺相结合。
在铝合金ENAC-AlSi7Mg0.3、ENAC-AlSi7Mg0.6铸造时除气及精炼成为熔炼工艺的控制的难点。
通过实际工艺验证,对除气工艺分两步,第一步,先对从中频熔炼炉倒入保温浇注炉的铝液用六氯乙烷(C2Cl6)进行初步除气,这是一般常用工艺,技术难度不大;下一步,在加入Sr变质后通入氩气进行再次除气,因为加入Sr后铝液吸气倾向增大,这时通入氩气既可以除气又可以加速Sr的扩散,提高变质的速度,细化晶粒,提高变质效果,起到一举两得效果。
变质处理是铸造铝合金熔炼的又一个关键环节,它同除气工艺一样也是一个控制难点,而且与除气工艺处理相比,控制难度更大。
变质处理有多种方法,选择一种适合我国的处理工艺难度很大,通常的变质方法有:
钠变质、锶变质、锑变质、钡变质、稀土变质。
在诸多变质剂中,Na的变质效果最佳,其次是Sr,但Na变质有衰退现象,腐蚀工具和环境,变质处理时易增大含气量和夹渣物,而Sr变质抗衰退性好,无腐蚀现象发生。
由于国内存在金属型铸造,每一坩埚铝合金液浇注持续时间长,加之国内生产的铸造铝合金接触网零件,服役状态均为致命零件,必须保证百分之百的安全,不能发生任何问题,否则都可能产生无法预料的损失,而变质处理是获得零件高性能的关键环节,只有变质良好的金属液浇出的零件通过热处理才能获得高性能产品,根据这些特点,选用Sr长效变质剂进行变质。
生产用含Sr变质剂主要有两种:
一类是纯Sr金属,另一类为Al-Sr中间合金,均已商品化,纯Sr金属含量高,加入量少,但相对吸收量少,保存困难,空气中保存容易引起氧化。
而Al-Sr中间合金中,含Sr量太低的铝锶合金因含铝量高,加入量多,影响铝液温度,据资料介绍含Sr8%的合金吸收最好,考虑到实际含量的波动及烧损,选用含Sr10%的铝锶中间合金。
变质处理时Sr的实际加入量、加入时铝液的温度、变质的时间是一个互相影响,又互相联系的有机整体。
根据合金的特点,选择在初步加C2Cl6除气后加入Sr进行变质处理,然后紧跟着进行除气工艺,这样既可以除气又可以通过加入氩气加速Sr的扩散,提高变质效果。
变质处理工艺结果的判断,是用断口来检查的。
一般资料都有介绍:
变质效果良好时断口呈银白色,组织细小呈丝绒状;变质过度时断口呈青灰色有闪亮的白点;变质不足,断口呈暗灰色,有硅的亮点。
断口的判断从资料的介绍看,好像很容易判断,实际判断的时候很难把握,不同的人判断的结果相差很大。
为了得到与性能相符的断口,可以先进行变质,然后浇注试块看断口,再浇注出不同断口的试棒,放入炉内进行热处理,然后用热处理后的试棒性能与其对应断口相比较,找出合适的断口,并据此确定变质的各种工艺参数,并将合格断口作为比较试样,作为以后进行热处理的对照参考物。
4.2铝合金ENAC-AlSi7Mg0.3、ENAC-AlSi7Mg0.6铸件热处理
热处理可以改变工件内部的显微组织,赋予或改善工件的使用性能,提高铸件的强度和塑性,改善合金的耐腐蚀性能。
其热处理内容包括:
固溶及时效处理。
根据铸件结构形状、尺寸、合金特性,并且将试棒随工件一起同炉热处理,把铸件加热到工艺要求的温度(高温单相区,接近于共晶的熔点),在该温度下保持足够长的时间,使强化相充分溶解到固溶体中,然后快速冷却,使固溶体的过饱和状态保留至室温,以获得强化效果。
然后进行时效处理,将铸件加热到固定温度,保温一定时间后出炉,在空气中缓慢冷却到室温的工艺。
使强化相沉淀析出,得以硬化,提高强度。
(1)固溶处理、时效处理过程的分析
1)固溶处理
(a)温度:
为了保证第二相质点在处理过程中具有较高的溶解速度,在处理后达到高的溶解度,固溶温度应尽可能的高,但其上限应低于合金组织中低熔点组织的熔点;
(b)保温时间,由强化组员