dynaform筒形件实验报告.docx
《dynaform筒形件实验报告.docx》由会员分享,可在线阅读,更多相关《dynaform筒形件实验报告.docx(17页珍藏版)》请在冰豆网上搜索。
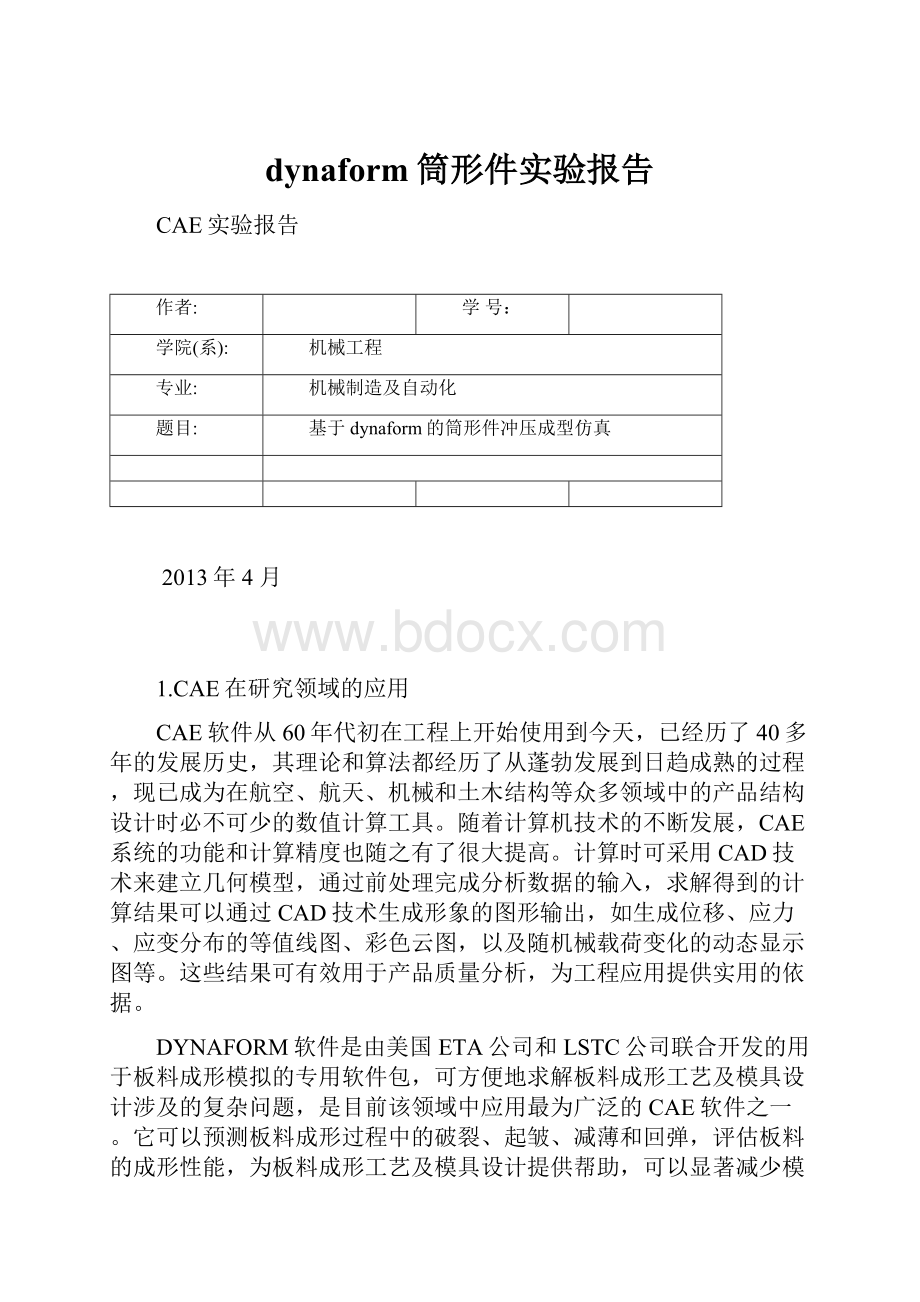
dynaform筒形件实验报告
CAE实验报告
作者:
学号:
学院(系):
机械工程
专业:
机械制造及自动化
题目:
基于dynaform的筒形件冲压成型仿真
2013年4月
1.CAE在研究领域的应用
CAE软件从60年代初在工程上开始使用到今天,已经历了40多年的发展历史,其理论和算法都经历了从蓬勃发展到日趋成熟的过程,现已成为在航空、航天、机械和土木结构等众多领域中的产品结构设计时必不可少的数值计算工具。
随着计算机技术的不断发展,CAE系统的功能和计算精度也随之有了很大提高。
计算时可采用CAD技术来建立几何模型,通过前处理完成分析数据的输入,求解得到的计算结果可以通过CAD技术生成形象的图形输出,如生成位移、应力、应变分布的等值线图、彩色云图,以及随机械载荷变化的动态显示图等。
这些结果可有效用于产品质量分析,为工程应用提供实用的依据。
DYNAFORM软件是由美国ETA公司和LSTC公司联合开发的用于板料成形模拟的专用软件包,可方便地求解板料成形工艺及模具设计涉及的复杂问题,是目前该领域中应用最为广泛的CAE软件之一。
它可以预测板料成形过程中的破裂、起皱、减薄和回弹,评估板料的成形性能,为板料成形工艺及模具设计提供帮助,可以显著减少模具设计时间及试模周期,从而提高产品品质和市场竞争力。
目前,DYNAFORM软件已在世界各大汽车、航空、钢铁公司以及众多的大学和科研单位得到了广泛的应用;自进入中国以来,DYNAFORM软件已在长安汽车、汽车、宝钢、中国一汽、汇众汽车公司和一拖等知名企业得到了成功应用。
2.确定CAE分析对象
圆筒形零件的冲压成型过程是一个较为复杂的受力变形过程,其最终的成型结果好坏与否凸模冲压速度、压边圈压力大小及其加载曲线有很大关系。
本次试验采用dynaform专业板料成型分析软件来分析给定条件下的圆筒件冲压成型过程的受力与变形,根据结果分析其中问题以及有待改进的地方。
3.问题描述
为了分析圆筒形件的冲压成型过程,并从分析结果中给出防止出现零件缺陷的措施,现给定筒形件冲压模型,材料选用铝合金AA6009,毛坯厚度1.0mm,模具接触间隙1.0mm,凸模冲压速度5000mm/s,压边圈压力200000N。
要求使用dynaform软件仿真零件成型过程并分析受力与变形情况,最后提出改进意见。
4.仿真实验步骤
4.1导入模型
首先采用solidworks建立凸模和毛坯件的三维模型,再转存为igs格式文件,之后导入dynaform软件数据库中。
图4.1凸模模型导入图4.2毛坯件导入
4.2网格划分及检查
首先对凸模进行网格划分,具体参数设置如下:
图4.3凸模网格划分参数
划分好之后的网格如下:
图4.4凸模的网格划分
划分网格之后要对其进行检查与修补:
图4.5检查凸模网格
4.3毛坯料网格划分
首先将导入的毛坯件所在层切换当前零件层,之后点击:
工具→毛坯生成器,在这里可以设定毛坯料的网格划分大小(如图2.6),之后同样在:
前处理→modelcheck/repair里对划分好的网格进行检查和修补(如图2.7)。
图4.6毛坯料网格划分
图4.7毛坯料网格检查
4.4生成凹模
首先新建凹模零件层,之后在前处理→单元中选择复制/偏移,选择凸模进行偏移。
具体参数如下:
图4.8偏移参数设置
图4.9偏移后模型
4.5设定压边圈
首先新建压边圈的零件层,之后从凸模边沿选择单元添加到压边圈层。
具体操作如下图:
图4.10选择压边圈单元并添加到BLINDER层
图4.11建立压边圈
4.6定义毛坯属性
在工具→定义毛坯中可以定义毛坯的材料和物理属性,这里选择材料为热滚DQSK,具体材料参数包括密度、氏系数、泊松比等,如图2.12;同时定义材料厚度为1mm。
图4.12定义BLINK层(毛坯)属性
图4.13材料参数设置
图4.14定义毛坯厚度
4.7分析设置
这里设定冲压类型为inverteddraw(单动作拉延模),接触间隙设为1。
图4.15分析设置界面
4.8定义工具
在工具→定义工具界面,根据各零件层作用及名字定义工具。
首先凹模为
图4.16定义工具DIE
DIE层,定义工具DIE包含零件DIE。
同样的方法去定义工具PUNCH和BINDER。
图4.17定义工具PUNCH和BINDER
4.9工具定位
在工具→定位工具→自动定位中将坯料BLANK层作为主工具,其余为从工具,接触间隙设为1,进行自动定位。
图4.18自动定位设置图4.19定位后工具位置
5.成型方案及结果分析
5.1凸模速度加载曲线
首先对凸模(PUNCH)加载速度曲线,根据条件速度加载为5000mm/s,位移48mm。
图4.1工具加载曲线界面图4.2凸模加载速度设置
图3.3加载速度曲线
5.2压边圈压力加载曲线
和上述类似的方法,对压边圈(BINDER)进行压力曲线设置,定义作用力为200000N,方向-z。
加载曲线如下图:
图5.4作用力加载
图3.5压边圈作用力加载曲线
5.3动画演示
在加载完成速度压力后,可以查看演示动画确认冲压动作和方向。
图3.6演示动画
5.4分析结果
在以上所有条件都完成之后,即可分析计算结果。
点击:
分析→LS-DYNA,分析类型选为fullrundyna。
具体设置如下:
图5.7分析设置
6.成型结果
打开生成的d3plot文件,结果为动画形式,截取最后一帧的结果作为分析对象,查看其成型极限图,厚度分布图以及主要应变图如下:
图6.1成型极限图
图6.2厚度分布图
图6.3主要应变图
7.实验分析与结论
本次试验坯料厚度1mm,网格大小1mm,模具划分网格大小为5mm,冲压速度5000mm/s,压边力200000N。
从成型极限图能看出圆筒成型时底边属于SAFE级别的形变没有断裂的危险,而桶壁边沿向上逐渐由起皱趋势且逐渐增强。
再从厚度分布可以看出冲压后材料厚度在0.85-1.5mm之间分布,而底边边缘处为厚度最薄处。
从应变图能看出应变较大的地方靠近筒壁上方,说明此处拉伸形变较大,与成型极限图相对应。
整体来观察筒形件的成型过程发现主要问题是壁口褶皱较多,对成型结果有一定影响。
分析原因有以下几点:
1.压边力不够大,导致材料壁口起皱。
2.毛坯及模具的网格划分不够细致,导致后处理分析是出现褶皱
3.冲压方法的影响。
由于采用一步成型法,压边圈的位置始终固定,压力几乎为线性恒定施加在材料上,在材料成型时对材料有很大的摩擦和拉扯力,甚至可能造成材料破损断裂。
所以为改善这种情况,优化方案如下:
1.增加压边力。
2.细化网格划分。
3.改为二步冲压成型法,改进压边圈的速度及压力曲线,避免硬性加压情形。
4.调整模具间隙。
5.减小毛坯与压边圈摩擦系数。
8.总结
本次CAE的数值仿真主要是运用的DYNAFORM板料成形专业仿真软件对筒形件的冲压成型进行仿真分析,在实验过程中学到了很多东西。
首先由于第一次接触DYNAFORM软件,所以实验过程的第一个收获就是学习并掌握了一项新的软件;同时在筒形件的仿真设计过程中也对板料成形的工艺过程有了深层次的了解;第三则是通过对零件的仿真分析发现了筒形件成型工艺中的可能存在的各种缺陷,并通过分析结果给出了防治措施,这是我体验到CAE软件在机械制造领域的重要作用;最后,这次实验中我也遇到不少问题,我也都曾请教过师兄或是自己想办法解决,通过这一过程是我在学习能力上也有了很大的进步,让我感到欣慰。