用应变寿命和断裂机理的方法分析渗碳件的弯曲疲劳寿命.docx
《用应变寿命和断裂机理的方法分析渗碳件的弯曲疲劳寿命.docx》由会员分享,可在线阅读,更多相关《用应变寿命和断裂机理的方法分析渗碳件的弯曲疲劳寿命.docx(20页珍藏版)》请在冰豆网上搜索。
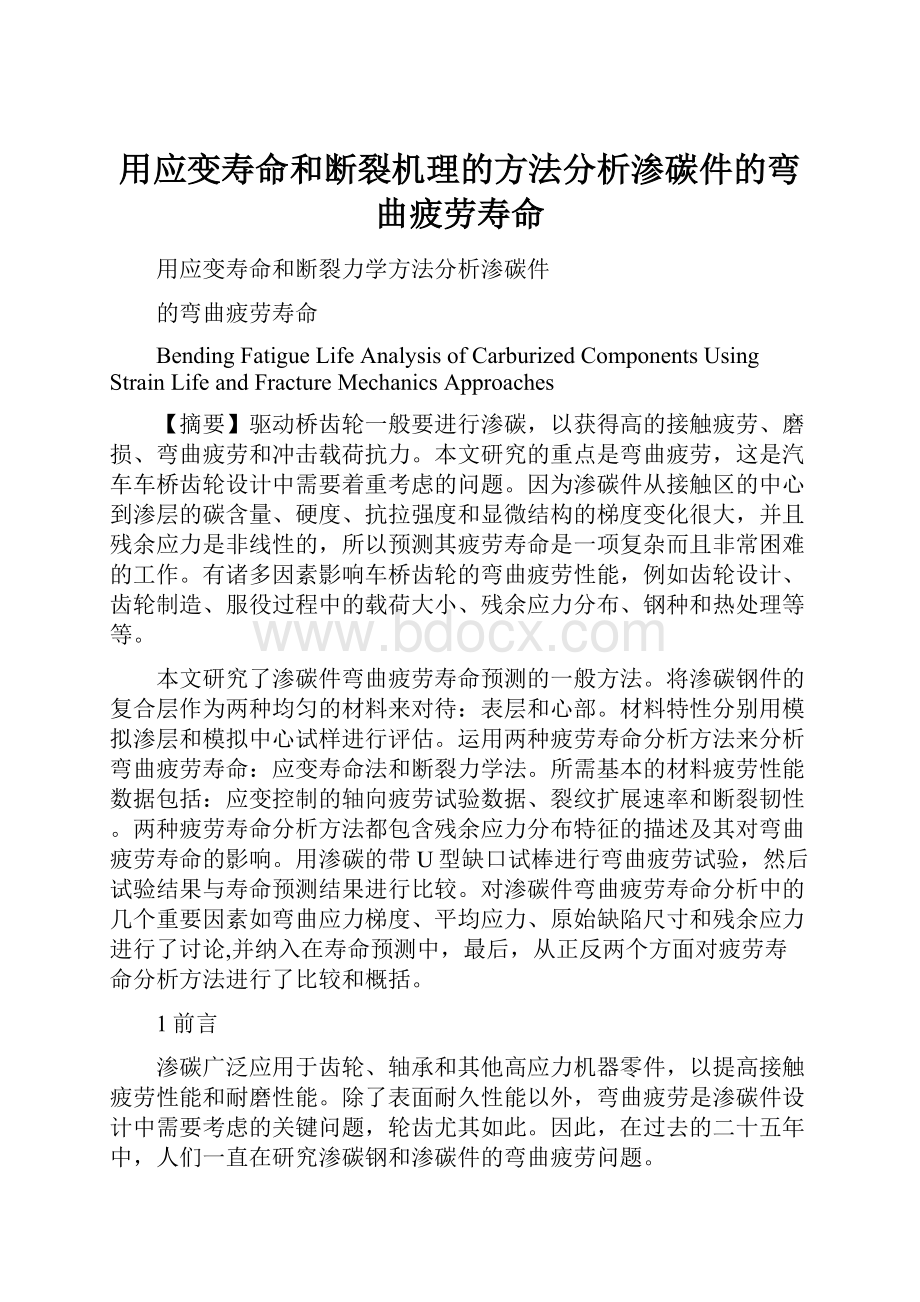
用应变寿命和断裂机理的方法分析渗碳件的弯曲疲劳寿命
用应变寿命和断裂力学方法分析渗碳件
的弯曲疲劳寿命
BendingFatigueLifeAnalysisofCarburizedComponentsUsingStrainLifeandFractureMechanicsApproaches
【摘要】驱动桥齿轮一般要进行渗碳,以获得高的接触疲劳、磨损、弯曲疲劳和冲击载荷抗力。
本文研究的重点是弯曲疲劳,这是汽车车桥齿轮设计中需要着重考虑的问题。
因为渗碳件从接触区的中心到渗层的碳含量、硬度、抗拉强度和显微结构的梯度变化很大,并且残余应力是非线性的,所以预测其疲劳寿命是一项复杂而且非常困难的工作。
有诸多因素影响车桥齿轮的弯曲疲劳性能,例如齿轮设计、齿轮制造、服役过程中的载荷大小、残余应力分布、钢种和热处理等等。
本文研究了渗碳件弯曲疲劳寿命预测的一般方法。
将渗碳钢件的复合层作为两种均匀的材料来对待:
表层和心部。
材料特性分别用模拟渗层和模拟中心试样进行评估。
运用两种疲劳寿命分析方法来分析弯曲疲劳寿命:
应变寿命法和断裂力学法。
所需基本的材料疲劳性能数据包括:
应变控制的轴向疲劳试验数据、裂纹扩展速率和断裂韧性。
两种疲劳寿命分析方法都包含残余应力分布特征的描述及其对弯曲疲劳寿命的影响。
用渗碳的带U型缺口试棒进行弯曲疲劳试验,然后试验结果与寿命预测结果进行比较。
对渗碳件弯曲疲劳寿命分析中的几个重要因素如弯曲应力梯度、平均应力、原始缺陷尺寸和残余应力进行了讨论,并纳入在寿命预测中,最后,从正反两个方面对疲劳寿命分析方法进行了比较和概括。
1前言
渗碳广泛应用于齿轮、轴承和其他高应力机器零件,以提高接触疲劳性能和耐磨性能。
除了表面耐久性能以外,弯曲疲劳是渗碳件设计中需要考虑的关键问题,轮齿尤其如此。
因此,在过去的二十五年中,人们一直在研究渗碳钢和渗碳件的弯曲疲劳问题。
早期开展的工作
(1)和
(2)主要集中在4027和8620钢模拟渗层和模拟中心单调循环应力-应变寿命特性,采用的是应变寿命疲劳分析方法。
模拟渗层基本呈现的是完全弹性行为,在断裂点的总应变小于1%。
模拟中心显示了循环软化,而模拟渗层显示了循环硬化。
在疲劳性能方面,两项研究工作都得出了这样的结论:
模拟渗层材料因其具有更高的强度在高周情况下要优越一些,而模拟中心材料在低周情况下表现出更高的疲劳抗力。
渗层和中心应变寿命曲线的交点大约在100,000次交变(50,000周次)。
这两项复杂的研究工作虽然没能使用轴向疲劳数据来预测渗碳件的弯曲疲劳寿命,但是建立了认识渗碳的渗层和中心材料轴向疲劳性能的基础。
断裂力学方法也广泛地用于渗碳件和渗碳钢的弯曲疲劳分析(3-7)。
在文献(3)中,通过运用线性弹性断裂力学(LEFM)理论建立了表面和次表层残余应力对疲劳寿命影响的模型。
残余应力对疲劳寿命的影响可以通过分析因残余应力而导致的应力集中来加以量化。
文献(4)进行了各种模拟钢材的断裂韧性K1c试验。
对影响表面渗碳钢K1c的多种因素进行了全面的研究,这些因素包括合金元素、残余奥氏体和碳含量。
更多的研究工作是在上世纪九十年代进行的,特别是运用断裂力学方法(5-7)对渗碳齿轮轮齿弯曲疲劳的分析。
文献(5)提出了一种独特而原始的分析方法。
将渗碳轮齿处理成碳含量和硬度连续变化的合成材料。
渗碳钢的疲劳裂纹扩展速率和断裂韧性作为硬度的函数进行描述。
残余应力也通过硬度分布加以估算。
然后运用LEFM理论计算齿轮弯曲疲劳寿命,并且估算轮齿弯曲强度。
在文献(7)中,根据软件包CRACKS(16)运用断裂力学方法对轮齿弯曲疲劳寿命进行了分析,估算钢材和残余应力对轮齿弯曲疲劳寿命的影响。
预测的疲劳寿命与单齿疲劳试验数据的相关性好。
除了应变寿命和断裂力学两种方法以外,带缺口试棒和单齿疲劳试验也广泛地用来评估齿轮弯曲疲劳性能(8-9)。
在文献(8)中,用带缺口的试棒在弯曲载荷下做了大量的试验工作,评价了几种因素的影响,例如钢的化学成分、中心硬度、渗层深度和加载速率等等。
Dowling及其合作者也利用带缺口试棒研究了渗碳工艺、合金化、表面氧化和次表层的残余应力对弯曲疲劳性能的影响。
科罗拉多州矿业学校(ColoradoSchoolofMines)的先进钢处理技术和产品研究中心(AdvancedSteelProcessingandProductsResearchCenter,ASPPRC)。
,从上世纪八十年代以来,一直在开展渗碳齿轮钢弯曲疲劳方面的研究工作。
通过对改进的Brugger悬臂梁型试样进行试验推导出应力-寿命曲线,用应力-寿命曲线来描述渗碳钢的疲劳性能。
然而,他们研究的重点是合金化、热处理和显微结构对弯曲疲劳性能的影响。
ASPPRC的研究并不涉及弯曲疲劳寿命分析或寿命预测,这可能是由于他们的研究重点在于钢和处理技术有关。
如上所述,虽然进行了大量的研究工作,但针对寿命分析或寿命预测的研究部分很少,特别是用应变寿命方法。
因此,本文的主要目标是研究弯曲疲劳寿命预测的一般方法,尤其是应变寿命方法。
此外,本文研究工作受到了以下三个因素的启发:
1、这些年来对更高的动力性、更低的重量、更快推向市场和更长保修期要求增长的趋势。
结果,计算式疲劳设计方法被汽车工业采用以减少设计周期和试验工作量。
2、疲劳寿命预测软件基于有限元分析,例如,FE-Fatigue(18)和FE/Safe(19)近几年已得到了应用。
但是,渗碳件弯曲疲劳寿命预测的方法还没有被明确提出。
3、最近,美国钢铁协会(AISI)组织了一个合作研究项目,研究汽车用碳钢和渗碳合金钢控制轴向应变的疲劳特性。
循环应力应变曲线和应变寿命疲劳特性数据库正在开发之中,其中包括一些通用的齿轮钢,例如8620、4320和4620。
该数据库不仅使弯曲疲劳寿命预测成为可能,而且也对如何使用这些数据以及相关的应变寿命方法预测渗碳件的弯曲疲劳寿命提出了挑战。
具体技术目标如下:
1、使用应变寿命方法以及轴向应变控制的疲劳试验数据预测渗碳钢U型缺口试棒的弯曲疲劳寿命;
2、应用断裂力学方法预测渗碳钢U型缺口试棒的弯曲疲劳寿命;
3、具体在预测渗碳件的弯曲疲劳性能方面,对应变寿命方法和断裂力学方法进行比较。
2试验结果与分析
2.1U型缺口试棒弯曲疲劳数据
2.1.1材料
从热处理前的驱动桥主动轮杆部截取U型缺口试棒,流线沿试样的长度方向。
材料为SAE8620钢。
化学成分按照ASTME415-99标准进行分析,如下表所示(Wt%):
表1试样A2和B2的化学成分(SAE8620钢)
C
Mn
P
S
Si
Ni
Cr
Mo
Cu
Al
A2
0.22
0.86
0.013
0.015
0.24
0.46
0.54
0.18
0.11
0.019
B3
0.21
0.86
0.013
0.015
0.23
0.46
0.53
0.18
0.11
0.019
SAE8620
规范
0.18
~
0.23
0.70
~
0.90
≤0.025
≤0.030
0.15
~
0.35
0.40
~
0.70
0.40
~
0.60
0.15
~
0.35
≤0.035
0.15
~
0.50
试样先气体渗碳,淬火,再回火。
有效渗碳层深1.24mm(0.049英寸),渗层硬度62HRC,心部硬度42HRC,渗层晶粒度为9.25级(按照ASME112标准评定),对应的平均晶粒直径为14.6微米。
2.1.2金相组织
渗层金相组织是高碳回火马氏体和残余奥氏体,如图1所示。
中心金相组织主要是低碳回火马氏体,如图2所示。
全部试样渗层都有一层晶间氧化物(IGO),厚约13至15微米(0.0005至0.0006英寸),如图3所示。
图1典型的渗层金相组织
硝酸酒精腐蚀,标记长度为0.0508mm(0.002英寸),
同时显示了表面的IGO层
图2典型的中心金相组织
硝酸酒精腐蚀,标记长度为0.0508mm(0.002英寸)
图3表面典型IGO的背散射电子像
深度约为13-15微米,硝酸酒精腐蚀
2.1.3残余应力(RS)和残余奥氏体数据
A组是先渗碳,淬火,再回火的原始试样。
B组试样与A组试样一同进行热处理,然后进行喷丸强化。
测量A和B两组试样次表层的残余应力分布,结果如表2所示。
表2渗碳试样A1和喷丸强化试样B4的残余应力数据
试样A1
试样B4
深度(mm)
RS(MPa)
RS(MPa)
0.0
-267
-523
0.025
-174
-841
0.050
-226
-1022
0.076
-263
-1344
0.152
-278
-1322
0.229
-243
-1152
0.305
-285
-854
0.381
-318
-572
平均
-257
-954
同时测量试样A1和B4的残余奥氏体含量,结果如表3所示。
表3试样A1和B4的残余奥氏体含量
试样A1
试样B4
深度(mm)
RA(%)
RA(%)
0.0
11.50
0.60
0.025
18.40
4.80
0.050
22.00
8.10
0.076
25.70
9.30
0.152
31.90
12.00
0.229
20.40
12.50
0.305
23.80
12.10
0.381
18.60
12.60
平均
21.53
9.0
从表中可以看出,喷丸强化显著增加了残余压应力,减少了残余奥氏体量。
2.1.3U型缺口试棒几何形状和疲劳试验数据
U型缺口试棒的截面为12.7mm×12.7mm(0.5英寸×0.5英寸)的正方形,长为64mm(2.5英寸),缺口深度为1.9mm(0.075英寸),缺口半径为2.29mm(0.090英寸)。
三点弯曲疲劳试验在载荷控制的条件下进行,所有试验的最小应力均为220MPa。
因此R(R=最小应力/最大应力)的范围为0.13至0.25。
因为试验是在载荷控制的条件下进行的,所以失效判据是位移变化。
在高载荷和低周情况下,疲劳寿命包括裂纹萌生和裂纹扩展时间,而在低载荷和高周情况下,疲劳寿命主要是裂纹萌生时间,可能还有较短的裂纹扩展时间。
应用线性弹性有限元分析建立了缺口根部应力与所加载荷的函数关系。
A组和B组试样的疲劳试验结果示于下面的表4和5中。
表4A组试样原始疲劳试验数据
最大-最小应力(MPa)
疲劳寿命(周次)
1710-220
2199、2975、3251、4242
1500-220
4620、7131、7797、8191
1289-220
16612、17554、23643、23976
1072-220
52656、177962
2件2×106超越
855-220
4件2×106超越
表5B组试样(喷丸强化)疲劳试验数据
最大-最小应力(MPa)
疲劳寿命(周次)
1710-220
10024
1500-220
70536
1289-220
2件2×106超越
1072-220
2件2×106超越
855-220
4件2×106超越
2.2用应变寿命方法进行寿命预测
在这一部分,使用应变寿命(局部应变)方法以及由AISI(美国钢铁协会)研究得出的8620钢渗碳渗层材料对称循环(R=-1)轴向应变寿命疲劳数据(17),来预测U型试棒的疲劳寿命。
2.2.18620钢全渗碳层应变寿命原始数据
本项研究所使用的应变寿命数据来自美国钢铁协会棒钢疲劳委员会的钢应变寿命数据库,8620钢经渗碳淬火,替代38。
材料数据示于表6中。
表68620钢全渗碳渗层对称循环轴向应变寿命材料特性
弹性模量E
202GPa
屈服强度
920MPa
极限抗拉强度
1202MPa
伸长量
1.0%
硬度
59HRC
循环强度系数K'
3493MPa
循环应变硬化指数n'
0.196
疲劳强度系数σ'f
1283MPa
疲劳强度指数b
-0.071
疲劳韧性系数ε'f
0.142%
疲劳韧性指数c
-0.111
循环应力应变关系由公式1描述:
公式1
应变寿命关系由公式2描述:
公式2
其中,Δε/2表示应变幅,Δσ/2表示应力幅,Nf表示失效时的循环周次。
两个公式中的其他材料常数在上面的表6中定义并给出具体数值。
2.2.2寿命预测过程
用轴向应变寿命数据预测U型缺口试棒弯曲疲劳寿命,必须考虑以下几个因素:
•由渗碳和/或喷丸引起的残余应力
•平均应力或R值
•弯曲应力和/或缺口应力梯度
•渗层中材料、强度和金相组织的梯度
在本项研究中,我们把长为12.7mm(U型缺口试棒的厚度)、深为0.050mm(0.002英寸)的缺口根部的表层材料看作是受应力的材料体,我们假定其处于最大外加应力和恒定残余应力之下,同时,该材料体本身的硬度和显微组织是均一的。
当根据应变寿命材料数据判定此受应力的材料失效时,我们就认为该U型缺口的试样失效。
也就是说,这里运用的是裂纹萌生寿命分析方法。
运用裂纹扩展方法可以分析任何可能的剩余寿命。
应用此假定,即假定材料体本身不变,弯曲和/或缺口应力梯度、残余应力梯度和渗层材料硬度梯度可计算得出。
在本项研究中,该材料体深度的选择可以是任意的。
然而,所选择的深度应该与有限元分析中的最小有限元尺寸或无损检测中最小可检测裂纹尺寸有关。
对于A组试样,从试样表面到深度为0.050mm处的平均残余应力为-222MPa,而对于B组试样,平均残余应力为-795MPa。
然后把残余压应力加到外加应力上,结果,最大和最小外加应力都将减少。
然后,使用循环应力应变关系公式1和Neuber关系把弹性应力和应变(在残余应力修正之后)转换成真应力和真应变。
弹性应力×弹性应变=真应力×真应变
示例:
A组数据#1
外加应力范围:
1710-220MPa。
在残余应力-222MPa修正之后,应力范围变成1488--2MPa。
在高弹性应力应变点:
应力为1488MPa,应变为1488/202000=0.7366%,请注意,应变=应力/E,其中E=202GPa。
经Neuber修正之后,真应力和应变分别为1160MPa和0.936%。
在最小应力和应变点,最小应力=-2MPa,对应的应变可以通过滞后公式中计算得出:
若Δσ=1162,则Δε计算的结果为0.596%。
因此,对应于外加弹性应力范围1710-220MPa,局部真应力和应变为:
Δε/2=0.298%,σmax=1160MPa,σm=580MPa,
其中,σmax:
应力峰值,σm:
平均应力
最后,疲劳寿命可以通过表6中给定的应变寿命常数和两个平均应力修正公式(20、21)计算出来:
SWT(Smith、Watson和Topper)公式(20):
Morrow公式:
用Morrow公式进行计算,疲劳寿命为250周次;而用SWT公式进行计算,N=650周次。
对于A组和B组试样的每个外加应力级别,可以重复以上整个过程。
完整的疲劳寿命预测结果示于表7、8和图4、5中。
表7通过应变寿命方法对A组渗碳试样所作的寿命预测结果
外加应力(MPa)
通过Morrow公式预测的寿命(周次)
通过SWT公式预测的寿命(周次)
1710-220
250
650
1500-220
1500
2300
1289-220
15000
11500
1072-220
350000
120000
855-220
3250000
1362000
图4A组带U型缺口试棒试验数据以及通过Morrow和SWT寿命公式预测的寿命。
具有两百万周次疲劳寿命的数据点超越
表8通过应变寿命方法对B组渗碳和强力喷丸试样所作的寿命预测结果
外加应力(MPa)
通过Morrow公式预测的寿命(周次)
通过SWT公式预测的寿命(周次)
1710-220
1500
1000
1500-220
25000
12500
1289-220
176800
198000
1072-220
1千万次超越
1千万次超越
图5B组强力喷丸的带U型缺口试棒试验数据以及通过Morrow和SWT寿命公式
预测的寿命。
具有两百万周次疲劳寿命的数据点超越
2.3用断裂力学方法进行寿命预测
在这一部分,使用基于线性弹性断裂理论的CRACKS程序来预测带U型缺口试棒的疲劳寿命。
用于预测裂纹扩展时间的断裂力学方法是基于这样的假设:
疲劳寿命的主要部分是裂纹扩展时间,而裂纹萌生时间可以忽略。
由于气体渗碳的带U型缺口试棒有深达15-20微米的表面晶间氧化层,所以原始缺陷和重要裂纹扩展时间的假定应进行修正。
计算裂纹扩展时间的通用公式如下:
其中:
K:
应力集中因子
β:
几何因子
σ:
外加应力或残余应力
a:
裂纹长度
裂纹扩展速率:
da/dN=f(R、ΔK)
其中:
N:
周次
R:
最小K/最大K
ΔK:
引力集中因子范围
f:
包括曲线拟合常数的一个函数
裂纹扩展速率与ΔK的关系通过裂纹扩展速率测定试验确定。
通过从原始裂纹尺寸直至断裂失效发生(通常由Kmax=Kc定义,其中Kc为材料的断裂韧性)求裂纹扩展速率表示的积分,可以计算裂纹扩展时间。
CRACKS程序根据权重函数方法和矩形截面内单个半椭圆表面裂纹几何形状,通过外加应力和残余应力来计算应力集中因子K。
沿厚度方向的非线性应力分布可以进行模拟,但是沿着宽度方向的应力假定为常数。
对于带U型缺口试棒,使用以下输入数据。
带U型缺口试样截面宽度为12.7mm,厚度10.8mm。
沿试样厚度方向的外加应力假定为是线性的,而测量的次表层采用的是非线性残余应力分布。
原始裂纹假定为半椭圆形表面裂纹。
在渗层,裂纹深度=0.0006英寸=15微米,裂纹长度=0.0024英寸=61微米。
裂纹深度是根据试样表面晶间氧化层的深度确定的。
在中心,假定裂纹是半园形的,裂纹半径=渗层深度=0.049英寸=1.24mm。
渗层的原始裂纹尺寸对渗层疲劳寿命有显著的影响,特别是在高周情况下。
这一问题将在讨论中更详细地论述。
为了计算裂纹扩展时间并确定最后的断裂,8620钢渗碳渗层与中心的裂纹扩展和断裂韧性特性可用在输入数据中,如表9所示。
当应力集中范围比从裂纹扩展试验中确定的裂纹扩展临界值小时,就确定为不具备裂纹扩展条件(无限寿命)。
相应的应力范围可以看作疲劳极限,因而疲劳极限取决于原始裂纹尺寸、材料裂纹扩展临界值和残余应力。
表98620钢全渗碳渗层和伪渗碳中心的断裂和疲劳特性
8620钢
渗层
中心
硬度(HRC)
61
40
Kc(MPam1/2)
20
107
ΔKth(MPam1/2)
3.6
4.6
表10对A组渗碳试样通过CRACKS所作的寿命预测
最大-最小应力(MPa)
渗层寿命
中心寿命
整体寿命(周次)
1724-220
2172
1313
3485
1517-220
3851
2396
6247
1310-220
7317
4436
11753
965-220
32115
14058
46173
900-220
没有裂纹扩展
一百万次超越
表11对B组渗碳试样通过CRACKS所作的寿命预测
最大-最小应力(MPa)
渗层寿命
中心寿命
整体寿命(周次)
1724-220
19690
1313
3485
1517-220
48063
2396
6247
1448-220
69760
4436
11753
1379-220
没有裂纹扩展
一百万次超越
图6使用断裂力学方法所作的寿命预测。
具有两百万周次
的数据点超越
3讨论
3.1残余应力(RS)对疲劳寿命的影响
A组和B组带U型缺口试棒弯曲疲劳试验数据表明,喷丸强化引起的残余压应力提高低周疲劳寿命3到20倍(在1710-220MPa时由3000周次提高到10,000周次,在1500-220MPa时由7000周次提高到170,000周次)。
同时,喷丸化也提高疲劳极限大约50%(由860MPa提高到1270MPa)。
应变寿命和断裂力学两种方法都可以模拟残余应力对弯曲疲劳寿命的影响。
在本文研究工作中,使用应变寿命方法时,考虑的只是表面渗层附近(深至假定的材料体积)的平均RS,而在使用断裂力学方法时,考虑的是全部测量的RS分布。
下表显示了两种方法所预测的疲劳极限的比较。
表12疲劳极限的比较(最大应力为1710MPa,最小应力为220MPa,一千万周次)
A组试样(渗碳)
B组试样(喷丸)
试验数据
860
1270
应变寿命
810(低6%)
1080(低15%)
断裂力学
900(高5%)
1370(高8%)
如表12中的结果所示,应变寿命和断裂力学这两种方法都很好地预测了带U型缺口试棒的疲劳极限。
由应变寿命方法所作的预测偏向于保守,而由断裂力学方法所作的预测偏向于非保守。
3.2裂纹萌生时间及裂纹扩展时间
从理论上说,应变寿命方法计算裂纹形核时间,而断裂力学计算裂纹扩展时间。
从图1中可以看出,对于A组试样当寿命N低于10,000周次时裂纹扩展的时间比较重要,使用应变寿命所作的寿命计算结果是相当保守的。
图2表明,直到一百万周次,应变寿命方法仍然是保守的。
这说明,对B组有喷丸强化引起的残余应力的试样而言,裂纹扩展时间更显著。
在文献(22)中,根据声发射判据作出了相似的结论,也就是说,在高载荷时裂纹扩展阶段占支配地位,而在低载荷时裂纹萌生阶段占支配地位,然而,在(22)中残余应力的影响并没有加以考虑。
裂纹形核尺寸的定义或区分裂纹形核时间和裂纹扩展时间的相关问题已经争论多年。
现在的认识是,裂纹形核尺寸大约在0.1至0.5mm之间。
然而,随着无损检测技术(如声发射和超声波)的发展和对小裂纹扩展更充分的认识,可以检测到更小的裂纹,因而裂纹扩展时间特别是小裂纹扩展时间,在乘用车与商用车部件的寿命分析和耐久性设计中,变得越来越重要。
3.3小裂纹和过渡裂纹尺寸
在本文研究工作中,渗层原始裂纹深度是根据深为15微米的晶间氧化层确定的,裂纹长度假定为61微米,是裂纹深度的4倍。
为了验证这样的原始裂纹对于LEFM仍然是可修正的,计算过渡裂纹尺寸如下:
根据文献(24),
其中:
ΔKth:
钢的裂纹扩展临界值
Δσe:
光滑试样的疲劳极限
8620渗碳层性能数据:
ΔKth=3.6MPam1/2(R=0.05);Δσe=600MPa(R=0.05),它是通过R=-1时的疲劳极限800MPa(ISI光滑试样轴向疲劳试验)和Goodman平均应力修正计算得出的。
结果:
a0=1/π(3.6/600)2=11.5微米
渗碳渗层的原始裂纹长为61微米,深为15微米,大于过渡裂纹尺寸。
3.4材料疲劳寿命原始数据
在应变寿命方法中,把控制应变的对称变轴向疲劳寿命数据和循环应力应变数据用作材料原始疲劳数据来计算带U型缺口试棒弯曲疲劳寿命。
在断裂力学方法中,把断裂韧性和来自紧凑拉伸长裂纹试样的裂纹扩展速率da/dN及ΔK用作材料疲劳数据。
三组试样:
带U