环形套筒窑工艺流程.docx
《环形套筒窑工艺流程.docx》由会员分享,可在线阅读,更多相关《环形套筒窑工艺流程.docx(12页珍藏版)》请在冰豆网上搜索。
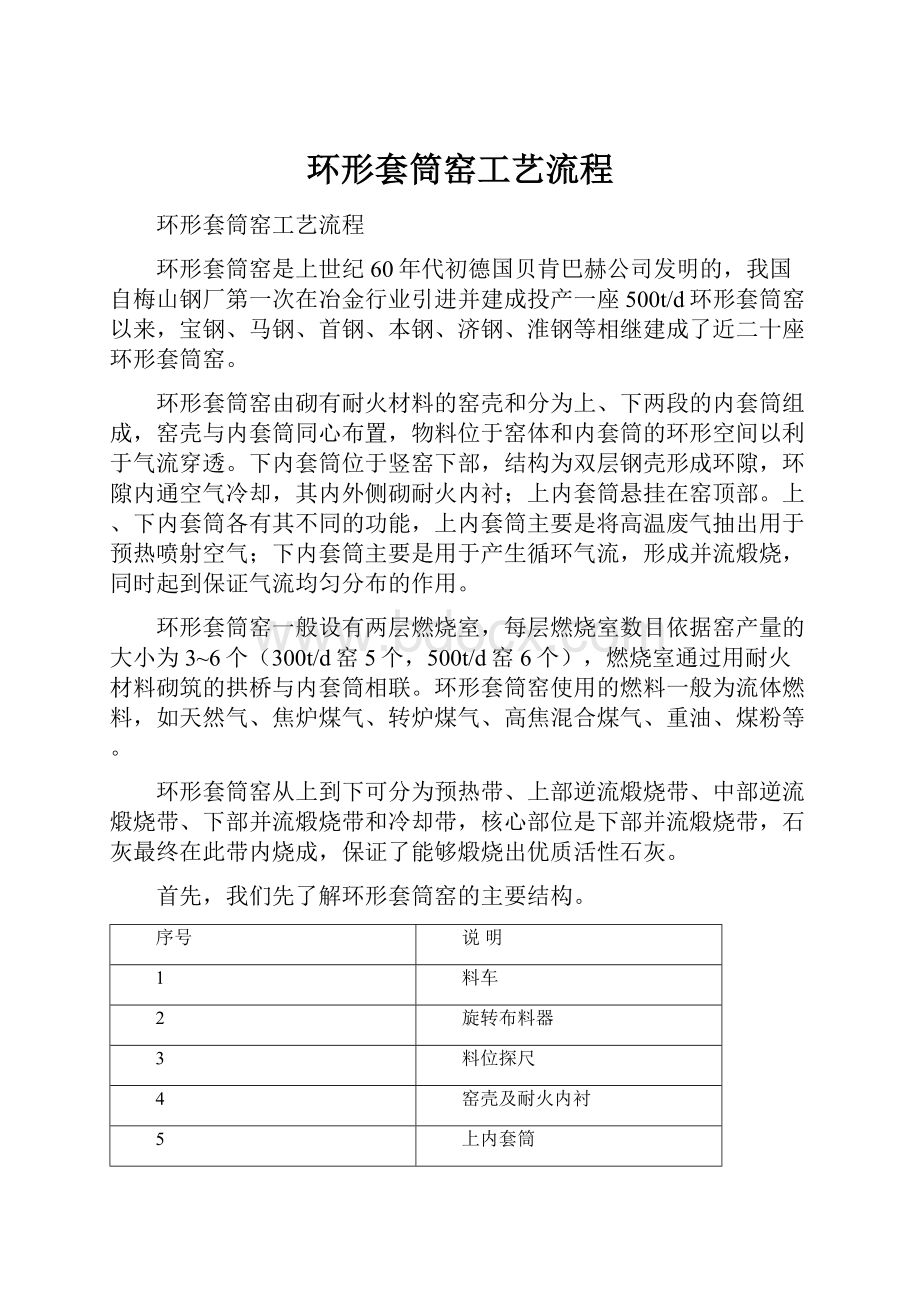
环形套筒窑工艺流程
环形套筒窑工艺流程
环形套筒窑是上世纪60年代初德国贝肯巴赫公司发明的,我国自梅山钢厂第一次在冶金行业引进并建成投产一座500t/d环形套筒窑以来,宝钢、马钢、首钢、本钢、济钢、淮钢等相继建成了近二十座环形套筒窑。
环形套筒窑由砌有耐火材料的窑壳和分为上、下两段的内套筒组成,窑壳与内套筒同心布置,物料位于窑体和内套筒的环形空间以利于气流穿透。
下内套筒位于竖窑下部,结构为双层钢壳形成环隙,环隙内通空气冷却,其内外侧砌耐火内衬;上内套筒悬挂在窑顶部。
上、下内套筒各有其不同的功能,上内套筒主要是将高温废气抽出用于预热喷射空气;下内套筒主要是用于产生循环气流,形成并流煅烧,同时起到保证气流均匀分布的作用。
环形套筒窑一般设有两层燃烧室,每层燃烧室数目依据窑产量的大小为3~6个(300t/d窑5个,500t/d窑6个),燃烧室通过用耐火材料砌筑的拱桥与内套筒相联。
环形套筒窑使用的燃料一般为流体燃料,如天然气、焦炉煤气、转炉煤气、高焦混合煤气、重油、煤粉等。
环形套筒窑从上到下可分为预热带、上部逆流煅烧带、中部逆流煅烧带、下部并流煅烧带和冷却带,核心部位是下部并流煅烧带,石灰最终在此带内烧成,保证了能够煅烧出优质活性石灰。
首先,我们先了解环形套筒窑的主要结构。
序号
说明
1
料车
2
旋转布料器
3
料位探尺
4
窑壳及耐火内衬
5
上内套筒
6
下内套筒
7
上烧嘴平台
8
下烧嘴平台
9
上燃烧室
10
下燃烧室
11
出灰机
12
出灰台
13
窑底料仓
14
振动出灰机
15
循环气体入口
16
拱桥
17
内套筒冷却空气导管
18
下环管(助燃空气环管)
19
喷射器及喷射管
20
烧嘴
21
循环气体管
22
废气管
23
换热器
24
上环管(驱动空气环管)
PZ
预热带
UB
上部逆流煅烧带
MB
中部逆流煅烧带
PF
下部并流煅烧带
CZ
冷却带
下面是一张环形套筒窑工艺流程图
然后,我们介绍环形套筒窑的物料走向。
石灰石原料经过破碎筛分后,粒度合格的原料进入窑前料仓,通常入窑石灰石粒度要求为40~80mm,也可以根据业主要求选择30~60mm的石灰石,需要保证的是物料的最大粒径:
最小粒径=2:
1。
在环形套筒窑PLC发出加料指令后,窑前料仓内的石灰石通过仓下振动出料机给至胶带输送机,由胶带输送机给称量斗加料。
当称量斗内物料重量达到设定值(通常为2.5t)后,胶带输送机停止给料,称量斗内的物料加入上料小车内。
上料小车在卷扬机的牵引下,沿上料导轨提升至窑顶。
在窑顶,上料小车内的原料先加入溜槽,沿溜槽进入中间料仓(或称为卸料闸门)内。
中间料仓的上部和下部各有一个液压闸门,两个闸门互为联锁控制,当向中间料仓加料时,下部液压闸门关闭,上部液压闸门开启,物料沿溜槽进入。
然后,上部液压闸门关闭,下部液压闸门开启,物料加入旋转布料器的旋转料仓内。
互为联锁的液压闸门可以防止加料过程中外界空气的进入。
旋转布料器为液压马达驱动,且只能向一个方向旋转。
下图为500t环形套筒窑旋转布料器工作过程示意:
我们设定,①~⑥为旋转布料器向窑内的加料点,且①点为旋转料仓的受料点。
开始加料时,当中间料仓的物料在①点加入到旋转料仓后,第一次向窑内的加料点在①点,旋转料仓不旋转,料仓下部的料钟下降打开,旋转料仓内的原料加入到窑内,然后料钟在液压缸的作用下提升,关闭旋转料仓。
料钟有配重小车配重,可以减小料钟液压缸的工作压力。
上料小车重复上述过程,原料在①点加入到旋转料仓内,第二次向窑内的加料点在②点,旋转料仓在液压马达的驱动下,旋转60°到②点(300t窑旋转72°),然后料钟下降在②点向窑内加料,料钟关闭后,旋转料仓在液压马达的驱动下,继续向前选转,回到①点受料位置。
这样的过程重复进行6次(300t窑为5次),直到旋转料仓在①~⑥点全部向窑内加料一次,才完成环形套筒窑一个加料周期。
原料加入窑内后,经过窑内的预热带预热,再经过窑内的上部逆流煅烧带、中部逆流煅烧带和下部并流煅烧带,煅烧成活性石灰后,进入石灰冷却带冷却后,由窑出料平台的出料机排至窑下料仓内。
出料机的每次出料量是固定的,约为50kg/台次,6台出料机一次可以出料300kg。
当环形套筒窑的产量调整时,我们调整的是出料机的周期工作时间。
在这里,我们要知道窑内几个带的大致划分:
预热带:
窑顶至上内套筒底部
上部逆流煅烧带:
上内套筒底部至上燃烧室
中部逆流煅烧带:
上燃烧室至下燃烧室
下部并留煅烧带:
下燃烧室至循环气体入口
冷却带:
循环气体入口至出料平台出料机
当窑下料仓内的成品到达高料位时,窑下料仓底部的带液压闸门的振动出料机开启,将窑下料仓内的成品排出窑,由高温耐热胶带输送机送往成品系统。
物料在窑内由窑顶向窑下流动的过程中,还将进行4次物料的再分布,这种再分布可以保证气流在物料之间的流动更均匀,生产的产品质量更好。
这4次再分布是通过窑壳与内套筒之间的连接结构实现的。
首先,原料从旋转料仓加入窑内时,会碰到上内套筒的悬挂梁(500t为6根,300t为5根),因为上内套筒是通过悬挂梁悬挂在窑顶的,这是第一次再分布。
然后向下在上拱桥进行第二次再分布,在下拱桥进行第三次再分布,最后在出料平台的出料机第四次再分布。
这四段再分布结构,上下之间是两两错开的,且夹角为30°(500t窑,300t则为36°)。
接着,我们介绍环形套筒窑内的气流走向。
了解环形套筒窑,主要理解环形套筒窑内的气流,根据各气流的性质,我们可以将环形套筒窑内的气流分为五种:
石灰冷却空气、内套筒冷却空气(其中下内套筒冷却空气为助燃空气)、驱动风、循环风和废气。
以下我们依次介绍这五种气流。
1.石灰冷却风
环形套筒窑在高温废气风机的抽力作用下,在窑内形成微负压,使得石灰窑内的气流不会喷出窑外。
这样实现了环形套筒窑的设备在线维护,且现场工作环境非常好。
因为窑内的微负压环境,石灰冷却空气通过风管自然吸入窑下料仓内,风管上设有电动调节阀,可以调节进风量。
石灰冷却风进入窑下料仓后,在料仓里冷却石灰后,通过出料平台出料机的成品之间的空隙进入窑内。
穿过窑内冷却带后,由循环气体入口进入下内套筒上段内部,与其余气体一起组成循环风。
具体气体流向见下图:
2.内套筒冷却空气
内套筒为双层钢壳结构,形成内套筒环隙空间,内套筒冷却空气在环隙空间内流动。
因为内套筒在窑内,虽然内套筒内、外壁均有耐火材料,但仍需在内套筒环隙空间内通入冷却空气进行强制冷却。
内套筒冷却空气由离心风机提供,为保证内套筒在设备意外状况下的安全,内套筒冷却风机为一用一备两台。
内套筒冷却空气通过管道输送至窑前,然后分为下内套筒冷却空气和上内套筒冷却空气。
下内套筒冷却空气从窑下料仓进入到下内套筒下段底部,然后沿着下内套筒下段粉尘排出管的环隙空间向上流动,在下内套筒上、下段连接立柱的开孔进入下内套筒上段的环隙空间。
最后由下内套筒上段上部的内套筒冷却空气导管(上拱桥内)排出下内套筒,后由管道引入窑换热器平台上的下环管,也称为助燃空气环管。
此时,下内套筒冷却空气约为200℃。
(另说明:
意大利弗卡斯公司设计的套筒窑,也有在下内套筒上段的上拱桥和下拱桥内均设有内套筒冷却空气导管,两个导管的直径一样,只是在下拱桥内的冷却空气导管内部设有一段导气锥,以限制下拱桥导管的气流量,保证上拱桥导管内有气流流动,冷却了下内套筒上段的上部区域。
)
进入下环管的下内套筒冷却空气,再分12个(500t窑)支管到上、下燃烧室平台的12个烧嘴,作为烧嘴的助燃空气。
支管上设有调节阀,可以调节各烧嘴的助燃空气流量。
另一部份内套筒冷却空气由管道引至窑上,作为上内套筒的冷却空气。
上内套筒冷却空气管道在窑换热器平台分为三支管(500t窑,300t为两支管),冷却空气通过三支管进入上内套筒环隙空间,冷却完上内套筒后通过一根总管排出,直接排放大气。
同时,在窑下燃烧室平台下方设有冷却空气环管,冷却空气也是通过一小支管引至上内套筒冷却空气上窑主管道。
此环管主要作用在于为上、下烧嘴火焰探测器提供冷却空气。
具体气流走向见下图:
3驱动风
驱动风由罗茨鼓风机提供,通常环形套筒窑产量可在60~120%之间调整,所以当驱动风机设计为两台时,一台为固定转速,风量应满足60%产量要求,另一台则为调速风机,用于进行产量的调整。
驱动风机输送的驱动风,通过管道输送至窑换热器平台上的换热器内,经过热交换后,20℃的空气被加热至400~450℃,然后由换热器热空气出口管输送至换热器平台上的上环管,也称为驱动风环管。
通常,在换热器平台上看不出上、下环管的具体样子,因为上、下环管被保温材料包裹在一起。
上环管内的驱动风因温度上升,体积膨胀,所以将上环管的驱动风通过支管引至6个喷射器内的喷射管(500t窑,300t为5个),由喷射管高速喷出,此时,在喷射管口位置的气体流速高达300m/s。
所以,可以在喷射器出口形成低压真空区,因而吸引窑内下燃烧室气体向喷射器流动,产生了形成窑内循环气体的动力。
可以推测,如喷射器出口位置的气体流速,决定了能带动的窑内循环气体的气体量。
在风机房内,因驱动风机与内套筒冷却风机布置在一起,所以驱动风和冷却风管道上有支管和阀门相连,用于紧急情况下两种风的应急供应。
具体气流走向见下图:
4循环风
循环气体是指下燃烧室燃烧产生的高温气体,经过并流煅烧带后,在循环气体入口与石灰冷却空气混合,进入下内套筒上段内部的这部分混合气体。
循环气体的流动是依靠驱动风在喷射器出口处产生的低压区,循环气体由高压向低压流动形成的。
进入下内套筒上段内的循环气体,在压力的驱动下,向着内套筒上部流动,最后从内套筒冷却空气导管下方的循环气体管流入喷射器内,在喷射器内与驱动风一起进入下燃烧室。
如此循环往复。
具体气流流向见下图:
5废气
环形套筒窑窑内燃烧产生的废气,最终将在高温废气风机的作用下,向着窑顶流动。
在窑顶气量调节阀的分配下,约70%的烟气进入上内套筒与窑壳之间的预热带,预热新加入窑内的原料并经过环形料层到达窑顶,最后由窑顶废气管道进入废气引风机。
另外30%的烟气则经上内套筒内部由管道进入换热器,作为驱动空气的预热气源,进入换热器的废气温度约在800~850℃,换热后温度降至300℃左右再进入废气管道。
窑内所有废气都由废气引风机抽出,进入废气引风机的废气温度一般在180~250℃左右,然后经袋式除尘器除尘达到国家废气排放标准后,由烟囱排入大气。
具体废气流向见下图:
此外,环形套筒窑燃烧所需要的热量由外界供入的燃料提供。
燃料经烧嘴喷射进入燃烧室,燃烧产生的高温气体经过拱桥下部形成的空间进入料层,为窑内的煅烧提供热量。
由于环形套筒窑下燃烧室以上是逆流煅烧,下燃烧室向下是并流煅烧,所以环形套筒窑上、下烧嘴供给的燃料量是不一样的,分配比率约为:
上/下=1.55/2.20。
由于上燃烧室提供的助燃空气量不足,只有50%左右,因此,在上燃烧室的中部逆流煅烧带的煅烧为不完全燃烧。
不完全燃烧的烟气中含有一定燃料,在废气引风机的作用下,烟气与来自经过拱桥进入料层的过剩空气相遇,继续进行完全燃烧,煅烧石灰石。
由于在这两煅烧带中,燃烧气流方向与物料的运行方向相反,所以称为逆流煅烧带。
在逆流煅烧带中,石灰石仅部分煅烧,而此时石灰石刚刚开始分解,需要大量吸收热量,故不会在逆流煅烧带产生过烧。
在下燃烧室供给燃料燃烧所需的助燃空气是过量的,空气过剩系数为2.0左右,这样保证了煅烧温度均匀,石灰石不会过烧。
下燃烧室燃烧产生的高温烟气(温度<1350℃分成两部分:
一部分经过中部逆流煅烧带、上部逆流煅烧带流向窑顶,过程如前所述;另一部分则会在喷射管高速气流所产生的负压抽力作用下向下流动,在下燃烧室与下内套筒的循环气体入口之间形成并流煅烧带,石灰石最终是在这一区域内煅烧完成。
在环形套筒窑重新开窑前,需要先对燃气管道进行吹扫,将管道内的混合气体全部排空,保证混合气体符合爆炸安全范围。
吹扫用气体常为氮气。
压缩空气在窑上主要用于换热器清灰、电磁阀的控制等。
此三种能源介质流向可见下图: