低温冷风深孔加工系统设计.docx
《低温冷风深孔加工系统设计.docx》由会员分享,可在线阅读,更多相关《低温冷风深孔加工系统设计.docx(40页珍藏版)》请在冰豆网上搜索。
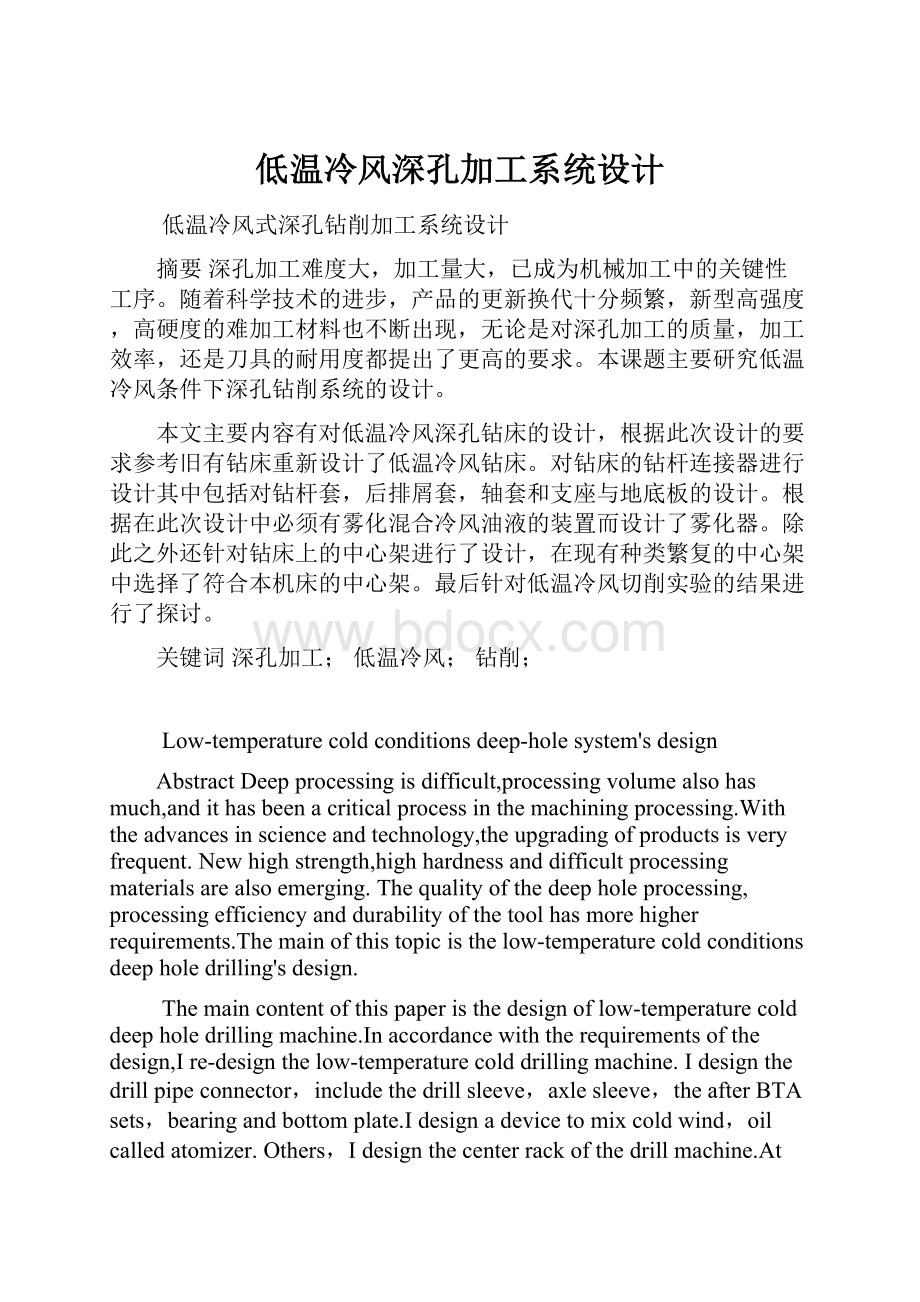
低温冷风深孔加工系统设计
低温冷风式深孔钻削加工系统设计
摘要深孔加工难度大,加工量大,已成为机械加工中的关键性工序。
随着科学技术的进步,产品的更新换代十分频繁,新型高强度,高硬度的难加工材料也不断出现,无论是对深孔加工的质量,加工效率,还是刀具的耐用度都提出了更高的要求。
本课题主要研究低温冷风条件下深孔钻削系统的设计。
本文主要内容有对低温冷风深孔钻床的设计,根据此次设计的要求参考旧有钻床重新设计了低温冷风钻床。
对钻床的钻杆连接器进行设计其中包括对钻杆套,后排屑套,轴套和支座与地底板的设计。
根据在此次设计中必须有雾化混合冷风油液的装置而设计了雾化器。
除此之外还针对钻床上的中心架进行了设计,在现有种类繁复的中心架中选择了符合本机床的中心架。
最后针对低温冷风切削实验的结果进行了探讨。
关键词深孔加工;低温冷风;钻削;
Low-temperaturecoldconditionsdeep-holesystem'sdesign
AbstractDeepprocessingisdifficult,processingvolumealsohasmuch,andithasbeenacriticalprocessinthemachiningprocessing.Withtheadvancesinscienceandtechnology,theupgradingofproductsisveryfrequent.Newhighstrength,highhardnessanddifficultprocessingmaterialsarealsoemerging.Thequalityofthedeepholeprocessing,processingefficiencyanddurabilityofthetoolhasmorehigherrequirements.Themainofthistopicisthelow-temperaturecoldconditionsdeepholedrilling'sdesign.
Themaincontentofthispaperisthedesignoflow-temperaturecolddeepholedrillingmachine.Inaccordancewiththerequirementsofthedesign,Ire-designthelow-temperaturecolddrillingmachine.Idesignthedrillpipeconnector,includethedrillsleeve,axlesleeve,theafterBTAsets,bearingandbottomplate.Idesignadevicetomixcoldwind,oilcalledatomizer.Others,Idesignthecenterrackofthedrillmachine.Atlast,thispaperdiscussedtheexperimentalresultsoflowtemperaturecoldwindcutting.
KeyWordsdeepholeprocessing;lowtemperaturecoldwind;drilling
1绪论
1.1本课题的研究意义和目的
机械制造行业的进步对世界经济的发展做出重要贡献,但是也在一定程度上会对环境造成污染。
如今,全世界都在提倡绿色制造,其目标是实现对资源的合理运用,节约成本。
在继续保持工业经济高速增长的同时,如何减小或避免对环境带来进一步地破坏,成为全社会共同关心的话题,绿色制造自然也就引起了更多人的关注。
要想获得正常生产和节能减排的“双赢”,还得要从制造过程中寻找解决之道,绿色切削技术作为可持续发展的制造模式成为制造企业的选择之一。
我国“十一五”规划纲要第一次提出了“节能减排”这一概念。
“节能减排”符合绿色环保发展理念,从国家层面上确定了发展方向,这对工业制造领域有何影响呢?
根据数据统计,有70%的环境污染物来自制造业。
现代制造业给人类带来空前物质文明的同时,也给社会带来了更多的废气、废渣、废液等废弃物。
目前我国深孔加工都是采用湿式加工法,湿式加工需要大量的切削液,并要及时对切削的处理,即会增加成本,又会污染环境。
从某种角度来说,工业制造领域在“节能减排”这一大趋势下受到的影响显然是最大的。
如此大的压力转嫁到工业制造企业本身,单纯地通过限制企业数量和影响正常生产来实现无疑是不现实的。
毕竟,以牺牲工业制造企业的数量和规模实现节能减排的目标只能解决一时之痒,无法从根本上解决问题。
那么,在国家提倡“节能减排”大环境下,要想获得正常生产和节能减排的“双赢”,还得要从制造过程中寻找解决之道,绿色切削技术作为可持续发展的制造模式成为制造企业的选择之一。
低温冷风式钻削技术作为一种绿色加工技术收到日益受到重视。
该技术就是就是将压缩空气的温度降低到零下20℃~30℃,甚至更低,混入微量润滑剂,对切削点实施冷却,润滑和排屑。
低温冷风式钻削技术具有节约切削剂采购费用,降低成本;切削可直接回收,增加效益;有利于自动加工,检测和监控;延长刀具寿命,降低刀具成本,缩短机床准备时间等等优点。
低温冷风钻削技术可使道具的切削效率更高,切削性能更好,应用前景广阔。
并使企业在清洁加工中,获得巨大经济效益。
所以低温冷风式加工技术在石油机械、工程机械以及军工等机械行业中普遍使用。
因此,对低温冷风式深孔加工技术的研究,无论从经济效益还是社会效益等方面都具有重要的意义和价值。
1.2国内外的研究现状
绿色制造是解决制造业资源消耗和环境污染问题的根本方法,是实施环境污染源头控制的关键途径,是21世纪制造业实现可持续发展之路。
目前,绿色加工技术主要包括生物稳定型切削液加工、干式切削加工、低温干切削加工、液氮冷却切削加工、喷雾冷却切削加工、低温冷风切削加工、水蒸汽冷却润滑加工和低温冷风微量润滑加工等。
1.2.1生物稳定型切削液
生物稳定型切削液依靠配方中所含的的特定成分来延长其使用寿命,当该特定成分的含量降低后就不具有抗菌的功能,很容易被生物分解,不会对环境造成污染。
目前,生物稳定型切削液在国外已经形成系列产品,并向国内市场推广,但是价格贵,生物稳定型切削液的使用寿命不长是现在的主要研究问题。
1.2.2干式切削技术
干式切削技术是在切削加工工程中完全不使用任何切削液的加工方式。
在干式切削加工过程中,由于缺少切削液的润滑、冷却、辅助排屑等作用,切削时承受较大的负荷,切削温度高,刀具能否克服这些不利影响,是其顺利实施的关键。
目前,干式切削技术实施的前提是:
①、采用热稳定、快速排屑的高速机床;②、采用新型的刀具材料和涂层技术;③、合理选择和刃磨刀具几何形状。
在国内采用PCBN刀具高速干切削冷铸轧获得了很好的效果。
1.2.3低温干切削技术
低温干切削技术是根据当温度降低时,金属材料变脆,塑性减小的低温脆性特点来实现切削加工的。
也就是把工件在极低的温度下冷却一段时间,然后取出,使工件材料在低温状态下进行干式切削加工。
但是这种加工方法在国内外的文献中很少有相关的研究报道。
1.2.4液氮冷却切削技术
液氮冷却切削技术是将-180℃液氮送入切削区,使刀具、工件和切削区处于低温冷却状态进行切削加工。
它也是利用材料的低温脆性进行的加工方法。
但是该项技术难度大、成本高。
美国怀特州立大学的S.Y.Hong和印度工学院的S.Paul对液氮冷却切削进行了理论和试验研究[8,9,10],试验表明,在超低温加工状态下,刀具材料能够保持良好的切削性能,可以提高刀具寿命,保证了切削效率和加工质量。
目前,液氮冷却切削技术主要存在以下需要解决的问题:
(1)液氮的存储、运输等费用带来了附加成本;
(2)液氮在切削加工中的润滑性不够;
(3)液氮使用的安全性需要特别加以注意;
(4)在超低温下切削出来的工件表面具有极强的化学活性,暴露在空气中会很快生锈,因此必须解决工件防锈问题[11];
(5)尚需对不同工件材料的低温切削性能以及刀具的切削特性等作进一步深入研究。
1.2.5水蒸汽冷却切削
水蒸汽冷却切削是将过热水蒸汽喷射到切削区以达到冷却润滑的一种切削方法。
水蒸汽冷却切削可以减小切削力和工件表面粗糙度值,明显降低切削温度,生成的切屑更规则合理,润滑性有所提高。
水蒸气价格低廉又无污染,是一种很好的绿色润滑剂。
目前,该技术仍处于研究阶段,主要存在以下问题:
水蒸汽发生装置能耗较大,尚须进一步研究能耗低、保温性好、结构简单合理的水蒸汽发生装置。
水蒸汽的润滑机理还需进一步深入研究,切削过程的润滑模型尚不明确。
需对不同的工件材料进行大量切削性能试验和研究,选择合理的加工参数及确定最优喷射角度和流量等。
1.2.6喷雾冷却切削技术
喷雾冷却切削技术是利用气液两相流体的混合体以高压(3~7个大气压)雾化的方式喷射到切削区,雾化的质点颗粒在切削区的高温作用下发生相变(汽化),吸收大量的切削热,降低切削温度。
日本的陈德成等人采用的喷雾加工法是利用高压气流引导微量切削油对切削区进行喷雾润滑的加工方式,喷雾气流供给切削区,其中的微小油粒子覆盖刀具、被切削材料和切屑,达到冷却和润滑的目的。
阎通海等人利用气液两相流冷却装置进行了一系列油雾润滑和油气润滑车削实验,证明这种方式润滑效果好,有效减少刀具磨损,应用于高速切削中效果良好。
1.2.7低温冷风切削技术
低温冷风切削技术是指将压缩空气冷却至0~-70°C,同时以射流冲击的形式强烈冲刷加工区的冷却方式。
日本学者横川和彦教授对此做了较为全面的实验研究,结果表明:
它可以显著均匀地降低加工区、刀具及工件的温度,有效地抑制刀具磨损,提高刀具耐用度,改善已加工表面的加工质量,提高零件加工精度,而且无须做加工尺寸补偿,还可以节约切削液的购入费用及其相关的设备费用和维护费用,对环境无污染。
目前对于该技术的研究还存在一些问题。
①低温冷风切削对于不同的被加工材料有着不同的影响,而国内对这方面的研究工作开展较少,缺乏试验数据,难以提供科学、合理的切削参数;②该方法的冷却润滑系统比较复杂,不利于推广应用;③该方法只有冷却功能而无润滑功能,并且使用时发出的噪声较大;④对风冷切削技术缺乏系统性的试验研究,对一系列技术参数没有量化和优化。
近几年来,国外对低温冷风切削技术的研究已趋成熟,低温冷风切削技术已为机床生产企业所接受并相继推出采用该技术的机床产品。
如日本安田工业公司的加工中心采用在电机轴、刀杆轴的中心插入绝热风管的结构,使-30℃的低温冷风直通刀刃,该结构大大改善了切削条件,更有利于低温冷风切削加工工艺的实施。
此外,日本三井精机推出的加工中心、罔本工作机械推出的平面磨床、森精机推出的车床等都使用了低温冷风切削技术。
为了保证切屑的迅速处理,这些机床的结构都作了较大的调整。
同时,与之配套的低温冷风发生系统的生产也实现了商品化,并正在成为日本机床行业新的销售热点。
国内华东船舶工业学院的任家隆
对亚
干式切削机理进行了如下研究。
本试验
采用的试验装置如图所示,即将压缩
机产生的压缩气体送至冷风发生装置,
并由仪器、开关调节到所需温度,再由
喷嘴喷射到刀具前刀面和切屑之间,从
而起到排屑和冷却切削区的作用。
而
亚干式切削时,添加剂以滴注方式随风
带入前刀面和切屑之间。
本研究均以连续切削为研究对象,所有相同材料,相同类别的试验均在同一根试件上完成;在切削稳定性试验时采用同一根材料,分段连续切削完成,以增加同类试验的可比性。
实验结果表明:
(1)亚干式切削、冷风冷却切削是一种较优的冷却万方数据切削方法,随着切削热、切削力的上升其冷却效果愈显著,其中亚干式切削更为明显。
(2)亚干式切削能保护被加工零件的尺寸稳定性,显著提高刀具使用寿命,减小加工表面的粗糙度值,有助于精密加工、自动化加工的实现。
(3)一般冷风温度越低,其冷却效果会越好;但由于诸多因素的综合作用,冷风温度与冷却效果之间并不是完全的线性关系,从生产成本、冷却效果等多方面进行综合优化还需要作进一步研究。
1.2.8低温冷风微量加工技术
低温冷风微量加工技术是将低温压缩空气与少量植物润滑液混合气化,将其喷射到加工区,对刀具和工件之间的加工部位进行润滑,也减少摩擦和防止切屑粘到刀具上,同时也冷却了加工区(微量油雾在加工区汽化会吸收大量切削热)并有利于排屑,从而显著地改善切削加工条件。
低温冷风微量润滑切削时气液两相流的喷射速度较高,动能较大,因而使润滑液渗透能力大大增强,并且气液两相射流中微量液体的尺寸很小,遇到温度较高的金属时极易汽化,因此其向切削区渗透能力大大增强。
由于润滑油的汽化潜热比较大,在进行机械加工时,可以吸收刀具和工件切削时产生的大量热量,吸热气化,显著降低区的温度;并且,微量润滑油的使用,对环境的影响很小,同时也大大改善了加工的环境,给机械加工提供了一个良好的作业环境。
低温冷风微量润滑技术只要使用得当,加工后的刀具、工件和切屑都是干燥的,避免了后期的处理,切屑经过回收还可以使用,并不污染环境,提高了利用率,低温冷风微量润滑技术不仅可以大大降低冷却液成本,保护工人和环境,同时还可以改善刀具寿命和工件表面粗糙度。
1.3深孔加工的特点
刀杆受孔径的限制,直径小,长度大,造成刚性差,强度低,切削时易产生振动、波纹、锥度,而影响深孔的直线度和表面粗糙度。
在钻孔和扩孔时,冷却润滑液在没有采用特殊装置的情况下,难于输入到切削区,使刀具耐用度降低,而且排屑也困难。
在深孔的加工过程中,不能直接观察刀具切削情况,只能凭工作经验听切削时的声音、看切屑、手摸振动与工件温度、观仪表(油压表和电表),来判断切削过程是否正常。
切屑排除困难,必须采用可靠的手段进行断屑及控制切屑的长短与形状,以利于顺利排除,防止切屑堵塞。
为了保证深孔在加工过程中顺利进行和达到应要求的加工质量,应增加刀具内(或外)排屑装置、刀具引导和支承装置和高压冷却润滑装置。
1.4主要设计的内容
本文主要设计了用于低温冷风深孔加工的机床。
设计新装置如雾化器,负压装置,中心架等零件的设计。
2系统总体方案的布局和设计
2.1机床的设计
为了此次的课题对学校现有深孔钻床进行改造,使其成为符合的设计要求的机床。
普通深孔钻床,其冷却是使用切削液,缺点是切削液使用量大,浪费,容易造成环境污染。
如下图:
图2-1普通深孔钻床
2.3机床的选择
车床型号的选择主要取决于最大钻孔直径和最大工件外径,最大钻孔直径决定深孔钻削的功率(即被改造车床的功率),最大工件外径决定了被改造车床的回转直径。
因此,选择被改造车床型号首先应考虑机床功率。
我国国产的C630型号主电机功率一般为11KW,所以加工常用孔径(直径小于70MM)的深孔时,常选用C630型号车床,其功率可达到要求,并且操作方便。
机床的主要技术参数:
床身上最大工件回转直径630mm
刀架上最大车削直径345mm
最大工件长度750/1400/3000/5000mm
主轴孔径70mm
马鞍内回转直径800mm
马鞍内有效长度300mm
主轴转速级数正转18级,反转9级
主轴转速范围正转14~750r/min,反转20~800r/min
纵向快速移动速度9m/min
横向快速移动速度6m/min
最大纵向行程650mm、1280mm
最大横向行程390mm
刀架工位数4或6
主电动机功率11kw
机床外型尺寸(长×宽×高)2842/3492/5092/7492×1639×1275mm
机床重量3.5/3.7/4.5/5.1t
机床标准附件:
顶尖套及顶尖φ32mm三爪卡盘拨盘φ25~100mm跟刀架地脚螺栓常用工具型号C630重量3700(kg)主电机功率11(kw)外形尺寸2842×1830×2000(mm)最大加工直径345(mm)最大加工长度1050(mm)最大回转直径630(mm)主轴通孔直径70(mm)主轴转速范围800(r/min)主轴转速级数16
首先进行功率的校核:
1.切削功率计算:
目前,还没有成熟的计算深孔钻削功率的经验公式,一般可用麻花钻的功率计算公式近似计算。
钻削扭矩
式中M是钻削扭矩,Nm;
d是钻孔直径,mm;
f是钻孔进给量,mm/r。
d取最大30来计算,f取0.15,则
钻削轴向力
式中N是钻削轴向力,N。
钻削功率
式中P是钻削功率,kW;
n是钻孔转速,r/s。
查《深孔加工技术》表3.2取切削速度v=80m/min。
最大加工直径为D=30mm。
所以:
得n=850r/min,即n=14r/s。
故
考虑到麻花钻有横刃和刀具材料为高速钢等因素,取计算值的70%作为深孔钻削功率的近似值。
所以车床11kW的功率满足加工需要.
下图是经过改装的低温冷风式深孔钻床,采用低温冷风进行冷却,具有节约切削剂采购费用,降低成本;切削可直接回收,增加效益;有利于自动加工,检测和监控;延长刀具寿命,降低刀具成本,缩短机床准备时间等等优点。
低温冷风钻削技术可使道具的切削效率更高,切削性能更好,应用前景广阔。
图2-2低温深孔钻削系统
1.工件2.中心架3.负压装置4.钻杆5.数控面板
6.钻杆连接器7.空气压缩机8.冷风机9.雾化器10排屑箱
2.2工作原理
该机床的工作原理是用压缩机把空气进行压缩进入冷风机后一路经冷却装置冷却至一10℃一一40℃,另一路经过雾化装置将冷却液雾化,然后和冷却的空气混合,再经过深孔钻床上的进气装置将高压冷风和雾化颗粒形成的混合气液流体经钻杆外壁和孔壁之间输送到钻头的切削部位以冷却刀具并将切屑从钻杆内部向后吹出。
3钻杆连接器结构设计
3.1钻杆连接器的作用
该装置主要用于钻杆连接,经冷却过的冷风与油混合的雾化液由该装置进入冷却钻头,排出钻屑。
3.1.1钻杆套设计
在实际应用中,钻杆连接处的大小有很多种,所以我们不可能为每个都做专用的连接器,每次换钻杆时都更换联结器,这样既浪费金钱又浪费时间。
我们要制造的只是可以和钻杆联结器配合的钻杆套,这样在加工时,每次要换的就只是一个钻柄套。
钻杆套外圈是和联结器配合的,是一定的。
内圈可以根据不同的枪钻柄部尺寸来定。
由于加工过程中钻杆套是需要经常更换的,所以它和联结器的连接既要可靠又要方便拆卸,本课题是利用了梯形螺纹连接。
它的定位是利用两个小台阶来实现的。
整个装置要求的密封性比较严格,所以在它与联结器配合的地方可以放一个防漏挡圈,同理,在钻杆套与钻杆连接的地方也需要这样一个防漏圈,这样既可以防漏,又可以起缓冲作用,避免它与轴向定位台阶形成过定位。
钻杆与钻杆套的连接时靠一个锁紧螺母来完成的。
由于在加工过程中钻杆需要旋转,必定产生扭矩,所以还需要螺钉和定位块来完成固定。
根据思路设计出下图的钻杆套:
图3-1钻杆套
3.1.2钻杆连接器后排屑套的设计
在应用中,后排屑套主要起排屑作用。
后排屑套与钻杆连接器同样是配合的,鉴于排屑时有压力,而且需要利用排屑套来调整负压的大小,所以后排屑套尾部采用螺纹结构,通过螺纹的旋进旋出调整负压。
同样防止排屑套的滑动,在其尾部需要锁紧螺母进行固定。
根据上述思路设计出后排屑套如下图
图3-2后排屑套
3.1.3钻杆连接器内套的设计
钻杆连接器内套主要是用来固定钻杆套和后排屑套,内套和支座配合的关系。
冷风和油混合后的雾化液需要从内套进入,所以内套的设计必须留出一个孔隙以便冷风的进入。
根据要求设计出下图的内套:
图3-3内套
3.1.4钻杆连接器支座的设计
钻杆连接器支座主要用来连接钻杆套,后排屑套,内套等零部件的。
支座上部需要设计一个进气口,以便冷风的进入。
没有特殊要求所以采用一般钻杆连接器的结构。
3.1.5钻杆连接器底板的设计
钻杆连接器底板用于将支座固定在溜板箱,底板下部需要设计燕尾槽。
3.2钻杆连接器的设计
综合所有的零部件,将其进行装配得到最终的钻杆连接器。
下图为新设计的钻杆连接器
图3-4钻杆连接器总装图
3.3钻杆连接器工作原理
1处为钻杆连接处,随着钻杆的不断钻削,钻屑从钻杆尾部进入钻杆连接器内部。
经过压缩冷却的冷风从2处进入钻杆内部,冷风从钻杆套与后排屑套的之间的间隙进入。
由于钻杆套与后排屑套相错,从钻杆排出的钻屑形成喷射流。
在这块射流区形成低压区。
这样在内管前后造成压力差,后端产生一定的吸力,从而是前端带有切屑的混合雾加速向后流动,排出切屑。
4中心架的结构设计
4.1中心架的选择
随着加工制造业的发展,机床附件的选择是必须面对的问题。
在机床附件当中,中心架是加工较长工件必不可少的选择。
中心架在选择当中一般有两种形式,一种为可编程液压中心架,一种为手动中心架。
可编程液压中心架的自动化程度高,可以在加工程序中按照加工内容、加工顺序编入加工的步骤,达到程序化自动加工。
可编程液压中心架多使用在小批量复杂零件的生产,可实现在一次装夹中完成除夹持的部分外其余的全部加工,这种液压中心架多使用在车铣复合加工中心类机床;手动中心架一般使用在批量比较大,分步加工的场合,由于工件多次装夹,中心架起到长工件一头在装夹过程中支撑定心的作用,液压中心架由于结构和成本的问题,起不到这个作用,所以手动中心架多用在普通车床上。
由于工件的刚性减弱,切削力使工件变形加大,在加工过程中,容易发生震动、加工出现较大的误差,甚至造成工件掉落的恶性事故,所以采用中心架作为辅助支撑,增加工件的刚性和切削的稳定性有效地防止因为夹持压力的变化导致的工件中心偏移,因此也就能提高定心的精度。
车床中心架就能够用于外径转向、内径转向、切面、钻孔、磨削、感应淬火等加工。
适合外圆加工,旋转加工,研磨定位焊接等。
下图为几种常用的中心架,考虑到这次设计的要求,最终选择第二种中心架作为此次设计的中心架。
图4-1中心架
图4-2中心架
4.2中心架的使用和调整
当加工的工件长度与直径比超过2.5倍以上,由于工件的刚性减弱,切削力使工件手变形加大,在加工过程中,容易发生震动、加工出现较大的误差,甚至造成工件掉落的恶性事故,所以采用中心架作为辅助支撑,增加工件的回转刚性和切削的稳定性。
为了保证工件的精度和实现稳定的切削,需要采用较高精度的轴承。
在架位车好装上中心架后,必须要做的一个工作就是要低速试运转10分钟,检查工件是否跑出来。
一般工件向外跑为中心架的支撑中心低于或高于主轴中心,这样会产生危险,需要特别注意,尤其是安装调整中心架后,必须检查中心架各锁紧是否牢固,在这里还有中心架支持工件位置的问题,注意支撑的位置离主轴越远越好。
对于比较短的工件,千万不能支撑在工件长度的中心位置上,这样中心架成为中心的支点,当切削过程产生的切削力通过支点传给三爪,造成三爪架持力降低,产生掉活的现象。
4.3中心架的设计思路
在实际生产中,各种零件都是由多个部分组成的,如壳体、端盖、工件支撑套等,各个部分装配在一起,在工作中相互配合来完成特定的功用。
我所设计的深孔钻床中心架既由支座、轴承盖、轴承及工件支撑套组成的,