机电毕业设计倒装复合冲裁模设计.docx
《机电毕业设计倒装复合冲裁模设计.docx》由会员分享,可在线阅读,更多相关《机电毕业设计倒装复合冲裁模设计.docx(31页珍藏版)》请在冰豆网上搜索。
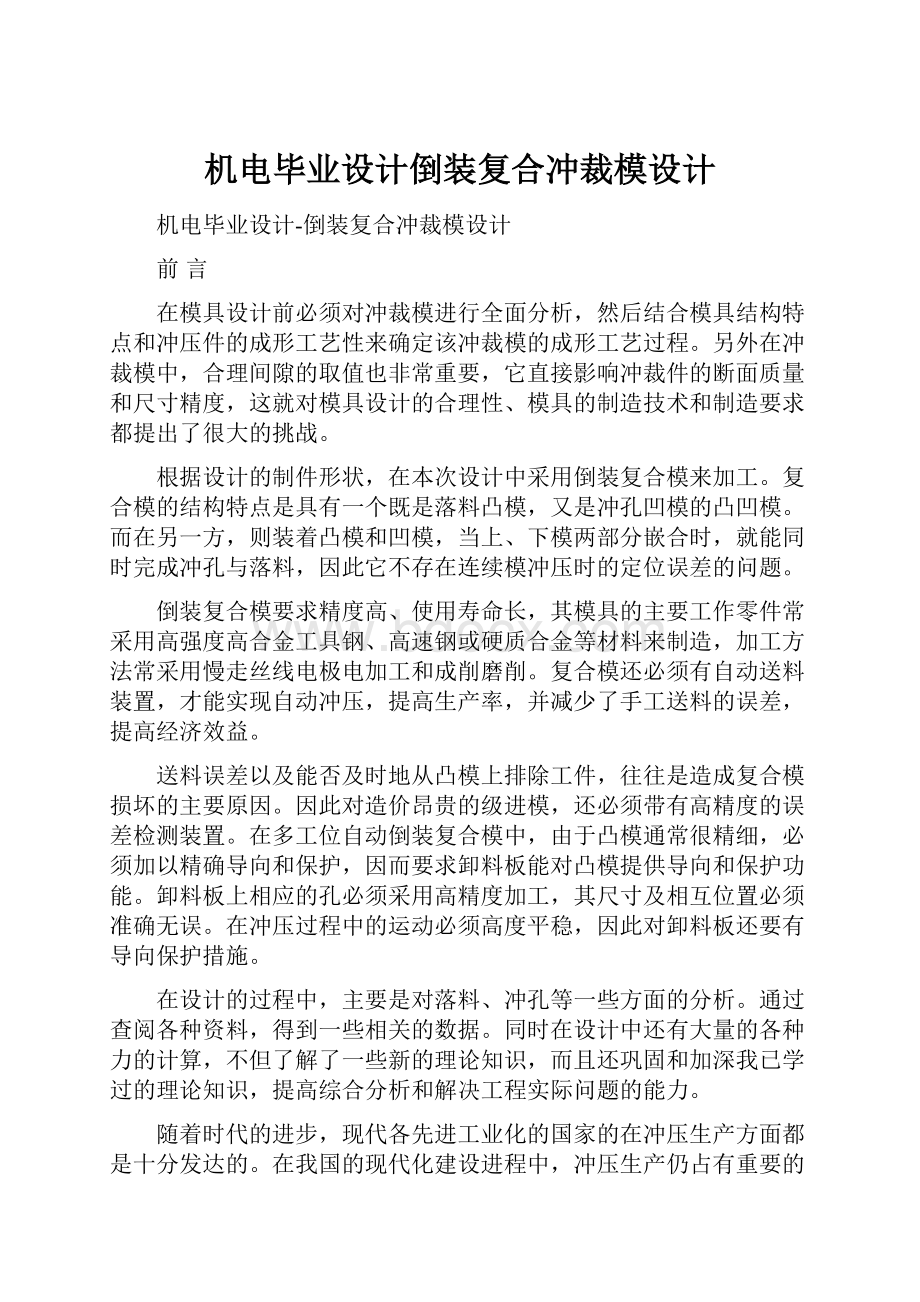
机电毕业设计倒装复合冲裁模设计
机电毕业设计-倒装复合冲裁模设计
前言
在模具设计前必须对冲裁模进行全面分析,然后结合模具结构特点和冲压件的成形工艺性来确定该冲裁模的成形工艺过程。
另外在冲裁模中,合理间隙的取值也非常重要,它直接影响冲裁件的断面质量和尺寸精度,这就对模具设计的合理性、模具的制造技术和制造要求都提出了很大的挑战。
根据设计的制件形状,在本次设计中采用倒装复合模来加工。
复合模的结构特点是具有一个既是落料凸模,又是冲孔凹模的凸凹模。
而在另一方,则装着凸模和凹模,当上、下模两部分嵌合时,就能同时完成冲孔与落料,因此它不存在连续模冲压时的定位误差的问题。
倒装复合模要求精度高、使用寿命长,其模具的主要工作零件常采用高强度高合金工具钢、高速钢或硬质合金等材料来制造,加工方法常采用慢走丝线电极电加工和成削磨削。
复合模还必须有自动送料装置,才能实现自动冲压,提高生产率,并减少了手工送料的误差,提高经济效益。
送料误差以及能否及时地从凸模上排除工件,往往是造成复合模损坏的主要原因。
因此对造价昂贵的级进模,还必须带有高精度的误差检测装置。
在多工位自动倒装复合模中,由于凸模通常很精细,必须加以精确导向和保护,因而要求卸料板能对凸模提供导向和保护功能。
卸料板上相应的孔必须采用高精度加工,其尺寸及相互位置必须准确无误。
在冲压过程中的运动必须高度平稳,因此对卸料板还要有导向保护措施。
在设计的过程中,主要是对落料、冲孔等一些方面的分析。
通过查阅各种资料,得到一些相关的数据。
同时在设计中还有大量的各种力的计算,不但了解了一些新的理论知识,而且还巩固和加深我已学过的理论知识,提高综合分析和解决工程实际问题的能力。
随着时代的进步,现代各先进工业化的国家的在冲压生产方面都是十分发达的。
在我国的现代化建设进程中,冲压生产仍占有重要的地位。
相信在以后的发展中,模具以及冲压设备等会随着科学技术的发展而不断发展。
第一章模具设计
冲压工艺是通过冲压模具来实现的,因此做好模具设计是冲压工艺的一项关键的工作。
模具设计主要是确定模具的类型、结构和模具零件的选用、设计与计算等。
1、冲模的分类
冲压件的品种、式样很多,导致冲模的类型多种多样。
(1)按工序性质可分为落料模、冲孔模、切断模、整修模、弯曲模、拉深模、成形模等。
(2)按工序组合程度可分为单工序模、级进模和复合模。
但工序模:
在一副模具中只完成一个工序。
如落料模、冲孔模、弯曲模、拉深模等。
级进模:
在一次行程中,在一副模具的不同位置上完成不同的工序。
因此对工件来说,要经过几个工位即几个行程才能完成。
而对模具来说,则每一次行程都能冲出一个制件。
所以级进模生产率相当高。
复合模:
在一次行程中,在一副模具的同一个位置上,能完成两个以上工序。
因此复合模冲压出的制件的精度较高,生产率也高。
(3)按导向方式可分为无导向的开式模。
有导向的导板模、导柱模等。
(4)按卸料方式可分为刚性卸料模、弹性卸料模等。
(5)按送料、出件及排除废料的方式可分为手动模、半自动模、自动模等。
(6)按凸、凹模的材料可分为硬质合金模、锌基合金模、薄板模、钢带模、聚氨酯橡胶模等。
2、冲模零件的分类
凡属模具,无论其结构形式如何,一般都是有固定和活动两部分组成、固定部分是用压铁、螺栓等紧固件固定在压力机的工作台面上,称为下模;活动部分一般固定在压力机的滑块上,称为上模;上模随着滑块作上下往复运动,从而进行冲压工作。
一套模具根据其复杂程度不同,一般都有数个、数十个甚至更多的零件组成。
但无论其复杂程度如何,或是哪一种结构形式,根据模具零件的作用又可以分成五个类型的零件。
1)、工作零件是完成冲压工作的零件,如凸模、凹模、凸凹模等。
2)、定位零件这些零件的作用是保证送料时有良好的导向和控制送料的进距,如挡料销、定距侧刀、导正销、定位板、导料板、侧压板等。
3)、卸料、推件零件这些零件的作用是保证在冲压工序完毕后将制件和废料排除,以保证下一次冲压工序的顺利进行。
如推件器、卸料板、废料切刀等。
4)、导向零件这些零件的作用是保证上模与下模相对运动时有精确的导向,使凸模凹模间有均匀的间隙,提高冲压件的质量。
如导柱、导套、导板等。
5)、安、固定零件这些零件的作用是使上述四部分零件连接成“整体”保证各零件的相对位置,并使模具能安装在压力机上。
如上模板、下模板、模柄、固定板、垫板、螺钉、圆柱销等。
由此可见,在看模具图时,特别是复杂模具,应从这五个方面去识别模具上的各个零件。
因此本次模具设计就从这五个方面着手来设计。
3、定位零件
定位部分零件的作用是使毛坯(条料或块料)送料时有准确的位置,保证冲出合格制件,不致冲缺而造成浪费。
(一)定位件
主要指定位板或定位销,一般用于对单个毛坯的定位。
(二)导料件
主要指导料板和侧压板,它对条料或带料送料时起导正作用。
(三)挡料件
其作用是给予条料或带料送料时以确定的进距。
主要有挡料销、活动挡料销、自动挡料销、始用挡料销和定距侧刀等。
(1)固定挡料销
结构简单,常用的为圆头形式。
当挡料销孔离凹模刃口太近时,挡料销可移离一个进距,以免削弱凹模强度,也可以采用钩形挡料销。
.
(2)活动挡料销
这种挡料销后端带有弹簧或弹簧片,挡料销能自由活动,这种挡料销常用在带弹性卸料板的结构中,复合模中最常见。
(3)自动挡料销
采用这种挡料销送料时,无需将料抬起或后拉,只要冲裁后将料往前推,便能自动挡料,故能连续送料冲压。
(4)始用挡料销
有时又称为临时挡料销,用于条料在级进模上冲压时的首次定位。
级进模有数各工位,数个工位时往往就需要用始用挡料销。
始用挡料销的数目,视级进模的工位数而定。
(5)定距侧刀
这种装置是以切去条料旁侧少量材料而达到挡料的目的。
定距侧刀挡料的缺点是浪费材料,只有在冲制窄而长的制件(进距小于6~8mm)和某些少、无废料排样,而用别的挡料形式有困难时才用。
冲压厚度较薄(
<0.5mm)的材料而采用级进模时,也经常使用定距侧刀。
在设计中采用的是固定挡料销,因为它结构简单,而且能满足要求,且安装方便。
考虑到此挡料销在凹模上的安装位置,所以,没能采用活动挡料销,因为活动挡料销有弹簧装置,需要在凹模上挖槽。
(四)导正销
导正销多用于级进模中,装在第二工位以后的凸模上。
冲压时它先插进已冲好的孔中,以保证内孔与外形相对位置的精度,消除由于送料而引起的误差。
但对于薄料(t<0.3mm),导正销插入孔内会使孔边弯曲,不能起到正确的定料作用,此外孔的直径太小(d<1.5)mm时导正销易折断,也不宜采用,此时可考虑采用侧刀。
此次模具设计采用了4个定位销将导料板和凹模先固定,以免在安装时板件错位而引起误差。
对于上、下模座和固定板、垫板的固定也是分别采用两个定位销定位。
本次设计的挡料件是两块导料板,它的作用是对条料送料时起着导正作用。
导料板与条料的间隙为1mm。
挡料件是两个活动挡料销,这种挡料销常用在弹性卸料板的结构中,且能自由活动。
因为距离凹模刃口太近,所以,其中的一个挡料销移离了一个进距,这样避免了削弱凹模的强度
4、压料、卸料零件
(一)推件装置
推件由刚性和弹性两种形式。
一般说来弹性推件装置在冲裁时
能压住制件,冲出的制件质量较高,但弹性元件的压力有限,当冲裁较厚材料是推件的力量不足或使结构庞大。
刚性推件不起压料作用,但推件力大。
刚性推件要考虑不应过多地削弱上模板的强度,推件力应尽可能分不均匀。
有时也做成刚、弹性结合的形式,能综合两者的优点。
(二)卸料装置
卸料装置也有刚性(即固定卸料板)和弹性卸料板两种形式。
此外废料切刀也是卸料的一种形式。
固定卸料板卸料力大,但无压料作用,毛坯材料厚度大于0.8mm以上时多采用。
弹性卸料板的卸料力小,但有压料作用,冲裁质量较好,多用于材料厚度小于1.5mm的冲裁薄料。
弹性卸料装置一般由卸料板、弹性元件(弹簧或橡胶)和卸料螺钉组成。
此结构可装于上模,也可装于下模。
本设计采用的是弹性卸料装置。
卸料板与落料凸模之间留有0.15mm的间隙。
(三)、压边圈
采用压边圈可以防止拉深件凸缘部分起皱,装在双动机上的拉深模,凸模装在内滑块上,压边圈装在外滑块上。
装在单动机上的拉深模,倒装形式结构可在下面装弹顶器或者利用压力机的气垫,有较大的压边力和压边行程。
本次设计中用不到压边圈。
5、连接与固定零件
(一)、模柄
中、小型冲模通过模柄将上模固定在压力机的滑块上。
通常的模柄形式有:
1)压入式模柄,它与上模座孔采用过渡配合,并且加销钉防止转动。
对这种模柄的圆柱度与肩台端面圆跳动均有要求,上模座厚度要较大。
2)旋入式模柄,通过螺纹与模座连接,用螺丝防松,装卸方便。
多用于有导柱的冲模。
3)凸模模柄,用3~4个螺钉固定在上模座的窝孔内多用于较大型的模具上。
4)通用模柄,凸模直接装入模柄孔中,由螺钉压紧,便于更换凸模。
5)浮动模柄,凹球面模柄与凸球面垫块连接,装入压力机
滑块后,允许模柄少许倾斜,可以减少滑块误差对模具导向精度的影响。
一般用带有导向装置的高精度的模具,如薄料和硬质合金冲裁模。
其缺点是安装时冲模中心很难对正滑块中心,不能纠正滑块与模柄轴心线之间的偏离。
除浮动模柄外,其它模柄装入上模座后,模柄的轴心线对上模座上平面的垂直度误差在全长范围内不大于0.05mm。
本次设计所采用的模柄是压入式模柄,其形状简单,加工和安装方便。
本次设计中采用的是压入式模柄,该模柄结构简单,安装和拆卸方便。
(二)、上、下模座
上、下模座上不仅要安装冲模的全部零件,而且要承受和传递冲压力。
所以模座不仅应有足够的强度,还要有足够的刚度。
模座的刚度不足,会降低冲裁寿命。
因此,模座要有足够的厚度,一般取为凹模厚度的1~1.5倍。
应按标准选取。
标准模座由对角导柱上、下模座,后侧导柱上、下模座,中间导柱上、下模柱,滚动导向上、下模座,以及无导柱规定的钢板及铸铁模座
1.1计算凸、凹模刃口尺寸
落料以凹模为基准,凹模刃口的基本尺寸取接近或等于零件的最小极限尺寸,以保证凹模磨损在一定范围内也能冲制合格制件。
凸模刃口的基本尺寸按凹模刃口基本尺寸减去一个最小间隙。
冲孔以凸模为基准,凸模刃口的基本尺寸取接近或等于孔的最大极限尺寸,以保证凸模磨损在一定范围内仍可使用。
二凹模的基本尺寸则按凸模刃口的基本尺寸加上一个最小的间隙。
查表2-10得间隙值Zmin=0.34,Zmax=0.39
对冲孔Ф26mm采用凸、凹模分开的加工方法,其凸、凹模刃口部分尺寸计算如下:
查表2-12得凸、凹模制造公差:
δ凸=0.02mmδ凹=0.025mm
校核:
Zmax-Zmin=0.05δ凸+δ凹=0.045
满足Zmax-Zmin≥δ凸+δ凹条件
查表2-13得因数x=0.5
按式(2-2)d凸=(d+XΔ)0-δ凸=(26+0.5×0.24)-0.020mm=26.12-0.020mm
d凹=(d凸+Zmin)+δ凸0=(26.12+0.39)+0.0250mm=26.51+0.0250mm
对外轮廓的落料,由于形状较复杂,故采用配合加工方法,其凸、凹模刃口部分尺寸计算如下:
当以凹模为基准件时,凹模磨损后,刃口部分尺寸都增大,因此均属于A类尺寸。
零件图中未标注公差的尺寸,由书末附录D中查出其极限偏差:
1200-0.87R100-0.36
查表2-13得因数x为:
当Δ≥0.5时,x=0.5
当Δ<0.5时,x=0.75
按式(2-4)Aj=(Amax-XΔ)+Δ/40
45凹=(45-0.5×0.56)+0.56/40mm=44.72+0.140mm
44凹=(44-0.5×0.54)+0.54/40mm=43.73+0.140mm
120凹=(120-0.5×0.87)+0.87/40mm=119.57+0.220mm
R10凹=(10-0.75×0.36)+0.36/40mm=9.73+0.090mm
1.2计算冲压力
在冲裁过程中,冲压力是冲裁力、卸料力、推件力和顶件力的总称。
冲压力是选择压力机、设计冲裁模和校核模具强度的重要依据。
该模具采用弹性卸料和下出料方式。
1.落料力(采用材料抗拉强度进行计算)
F1=Ltσb=(321.4×2.2×3OO)N=212×103N
2.冲孔力(采用材料抗拉强度进行计算)
F2=Ltσb=(81.64×2.2×3OO)N=53.9×103N
3.落料时的卸料力(根据经验公式计算)
F卸=K卸F1
查表2-15:
取K卸=0.03
故F卸=(0.03×212×103)N=6.36×103N
冲孔时的推件力
F推=nK推F2
取图2-17b的凹模刃口形式,h=5mm,则n=h/t=5mm/2.2mm≈2个
查表2-15:
K推=0.05
故F推=(2×0.05×53.9×103)N=5.39×103N
选择冲床时的总压力为:
F总=F1+F2+F卸+F推=227.6KN
1.3确定模具压力中心
以冲裁模为例,说明模具压力中心计算。
冲裁力合力的作用点称为模具的压力中心。
为了保证冲裁平衡工作,冲裁的压力中心必须通过模柄轴线,切和压力机滑块的中心线重合。
否则,模具在工作时就会产生偏荷弯距,加速压力机的导向机构不均匀磨损,还会使模具的间隙得不到保障,刃口迅速变钝,从而影响工件的加工精度,降低模具的使用寿命。
冲模压力中心的确定,在冲裁大型复杂形状工件,多凸模冲裁及两许冲裁时尤为重要。
冲裁力的压力中心和冲裁力的重心不同,他是指冲裁力合力的作用点,与冲裁力的大小及位置有关。
而工件的中心取决于工件的形状及其质量分布。
只有当工件具备中心对称形状时,其压力中心才能与中心重合。
(1)简单形状工件压力中心凡是质量分布均匀,具有中心对称形状的冲裁件,其压力中心语重心相重合。
此时的压力中心均位于工件轮廓图形的几何中心上。
(2)复杂形状的工件的压力中心绝大多数的冲裁件,沿冲裁轮廓的端面厚度不变。
轮廓各部分的冲裁力与轮廓的长度成正比,同时冲裁力沿轮廓分布。
因此,求轮廓各部分冲裁力的合力点,即压力中心,可转化为求轮廓线的重心位置。
计算步骤:
⑴按比例画出凸模工作部分剖面的轮廓图;
⑵在轮廓内外任意距离处,选定坐标轴
和
;
⑶将轮廓线分成若干基本线段,计算各基本线段的长度
(途中冲裁力与冲裁线长度成正比,故冲裁线段的长短,即可代表冲裁力的大小);
⑷计算基本线段的中心位置到
轴的距离
及到
轴的距离
;
⑸根据“对同一轴线的分力之和的力矩等于各分力矩之和”的原理,可按下式求出冲模压力中心到
轴和
轴的距离
到
轴的距离:
到
轴的距离:
如图2-40所示。
因零件左右对称,即xc=0。
故只计算yc。
将工件冲裁周边分成l1,l2,……l6基本线段,求出各段长度及各段的重心位置:
压力中心图
l1=45mmy1=0
l2=88mmy2=22mm
l3=25mmy3=44mm
l4=135mmy4=77mm
l5=31.4mmy5=116.9mm
l6=81.64mmy6=22mm
yc=(l1y1+…l6y6)/(l1+…l6)mm=46.27mm
1.4凹模、凸凹模的结构设计
冲Ф26mm孔的圆形凸模,由于模具需要在凸模外面装推件块,因此设计成直柱的形状。
尺寸标注如图凸模所示。
凹模的刃口形式,考虑到本例生产批量较大,所以采用刃口强度较高的凹模,即图2-17b所示的刃口形式。
凹模的外形尺寸,按式(2-25)和式(2-26):
H=Kb=0.24×120mm=29mm,c=1.5H=43mm。
尺寸标注如图凹模所示。
本模具为复合冲裁模,因此除冲孔凸模和落料凹模外,必然有一个凸凹模。
凸凹模的结构简图如图凸凹模所示。
校核凸凹模的强度:
按式(2-27)得凸凹模的最小壁厚m=1.5t=3.3mm,而实际最小壁厚为9mm,故符合强度要求。
凸凹模的外刃口尺寸按凹模尺寸配制,并保证双面间隙0.34~0.39。
凸凹模上孔中心与边缘距离尺寸22mm的公差,应比零件图所示精度高3~4级,即定为22±0.15mm。
凸模T10A60-64HRC
凹模T10A60-64HRC
凸凹模T10A60-64HRC
1.5模具总体设计及主要零部件设计
总体设计
第一节模具类型的选择
由冲压工艺分析可知,采用连续冲压,所以模具类型为连续模。
第二节定位方式的选择
因为该模具采用的是条料,控制条料的送进方向采用导料板,无侧压装置。
控制条料的送进步距采用挡料销初定距,导正销精定距。
而第一件的冲压位置因为条料长度有一定余量,可以靠操作工目测来定。
第三节卸料、出件方式的选择
因为工件料厚为1.0mm,相对较薄,卸料力也比较小,故可采用弹性卸料。
又因为是连续模生产,所以采用下出件比较便于操作与提高生产效率
第四节导向方式的选择
为了提高模具寿命和工件质量,方便安装调整,该级进模采用中间导柱的导向方式。
主要部件结构设计
第一节工作零件的结构设计
(一)冷冲模设计的一般方法:
确定冷冲模类型冲模的种类很多必须综合考虑冲压件的批量,尺寸,精度要求,形状和生产条件等多方面因素。
1冲件批量和冲裁类型
2确定模具精度等级
3确定模具结构类型其它因素如形状,大小,精度等。
(二)选定冷冲模的基本结构:
进行模具结构设计,确定结构件形式和标准。
1成形工件零件与标准件,导正销的确定如凸模,凹模及凸凹模的结构形式是整体,组合还是镶拼的,采用何种固定形式。
2选定位元件如定位板,挡料销等级进模还要考虑是否有挡料销,导正销和定凸模。
3卸料与退件机构的确定卸料有刚性卸料和柔性卸料两种形式。
刚性卸料通常采用固定卸料板结构形式,柔性卸料常采用弹簧或橡皮作为弹性元件。
4导向零件的种类和表准的确定包括是否采用导向零件,采用何种形式的导向零件
5模架种类及规格的确定。
(三)模具设计计算:
在冷冲模类型和机构的方案的模拟过程中,已确定了每道冲压工序的工件形状和尺寸,模具工作零件就是以此为依据进行计算的。
其它零件如导向零件,定位零件,固定零件,压料卸料零件,紧固零件等
应尽可能按冷冲压标准选用,只有在无标准选用时,才进行设计。
对某些零件还应该进行强度校核。
图2-42所示为本例的模具总图。
该复合冲裁模将凹模及小凸模装在上模上,是典型的倒装结构。
两个导料销24控制条料送进的导向,固定挡料销2控制送料的进距。
卸料采用弹性卸料装置,弹性卸料装置由卸料板16、卸料螺钉23和弹簧20组成。
冲制的工件由推杆5、推板7、推销8和推件块13组成的刚性推件装置推出。
冲孔的废料可通过凸凹模内孔从冲床台面漏下。
1.5.1卸料弹簧的设计计算:
1)根据模具结构初定6根弹簧,每根弹簧分担的卸料力为:
F卸=6360N/6=1060N
2)根据预压力F预(>1060N)和模具结构尺寸,由书末附录C1初选出序号为68-72的弹簧,其最大工作负荷F1=1550N>1060N
3)校检是否满足S1≥S总。
查书末附录C1及负荷——行程曲线,并经过计算可以得到以下数据:
序号
H0/mm
H1/mm
S1=H0-H1
S预(F预=1060N)
S总=S预+S工作+S修磨
68
60
44.5
15.5
10.5
18.7
69
80
58.2
21.8
15
23.2
70
120
85.7
34.3
23
31.2
71
160
113.2
46.8
30
38.2
72
200
140.5
59.5
40
48.2
注:
S工作=t+1=3.2mm,S修磨=5mm
由表中数据可见,序号70-72的弹簧均满足S1≥S总,但序号70的弹簧最适合因为其它弹簧太长,会使模具高度增加。
70号弹簧规格为:
外径:
D=45mm
钢丝直径:
d=7.0mm
自由高度:
H0=120mm
装配高度:
H2=H0-S预=120mm-23mm=97mm
1.5.2主要工作零件
模架选用适用中等精度,中、小尺寸冲压件的后侧导柱模架,从右向左送料,操作方便。
上模座:
L/mm×B/mm×H/mm=250×250×50
下模座:
L/mm×B/mm×H/mm=250×250×65
导柱:
d/mm×L/mm=35×200
导套:
d/mm×L/mm×D/mm=35×125×48
垫板厚度取:
12mm
凸模固定板厚度取:
20mm
凹模的厚度已定为:
29mm
卸料板厚度取:
14mm
弹簧的外露高度:
54(=97-6-37)mm
模具的闭合高度:
H模=(50+12+20+29+2.2+14+54+65)mm=246.2mm
1.5.3模具总图
如图2-42所示为一副倒装复合冲裁模装配图。
◆主视图
常取模具的工作位置,采用剖面画法。
◆俯视图和仰视图
一般是将模具的上模部分(或是下模部分)拿掉,视图只反映模具的下模俯视(或上模仰视)可见部分,这是冲模的一种习惯。
◆侧视图和局部视图等视图必要时画出。
◆制件图
常画在图样的右上角,要注明制作材料、规格以及制件本身的尺寸、公差及有关技术要求。
对于由数副模具冲压成的制件,除绘制出本工序的成品制件图外,还要绘出上工序的半成品图(毛坯图一般放在左上角)。
◆排样图
对落料。
复合模和级进模,必须在制件图的下方绘出排样图。
排样图上应标明料宽、步距和搭边值。
复杂和多工位级进模的排样图,一般单独绘制在一张图样上。
◆技术要求及说明一般在标题栏上方写出该模具的冲压力、模具闭合高度、模具标记、所选设备型号等要求。
◆列出零件明细表
1-导套2-挡料销3-上模座4-螺钉5-推杆
6-模柄7-推板8-推销9-垫板10-螺栓
11-销钉12-凸模固定板13-推件块14-凹模
15-凸模16-卸料板17-导柱18-下模座19-凸凹模
20-弹簧21-销钉22-螺钉23-卸料螺钉24-导料销
图2-42倒装复合冲裁模
第二章模具的装配及工作过程
2.1模具的装配
(一)组件装配
(1)将压入式模柄装配于上模座内,并磨平端面。
(2)将凸模装入凸模固定板内,为凸模组件。
(3)将凸凹模装入凸凹模固定板内,为凸凹模组件。
(二)确定装配基准件
落料冲孔复合模应以凸凹模为装配基准件,首先确定凸凹模在模架中的位置。
(1)安装凸凹模组件,加工下模座落料孔。
首先确定凸凹模组件在下模座上的位置,然后用平行夹板将凸凹模组件和下模座夹紧,在下模座上划出漏料孔线。
(2)加工下模座漏料孔,下模座漏料孔尺寸应比凸凹模漏料孔尺寸单边大0.5-1mm。
(三)安装上模部分
(1)检查上模各个零件尺寸是否满足装配技术条件要求,如推板顶出端面应凸出端面落料凹模端面等。
打料系统各零件尺寸是否合适,动作是否灵活等。
(2)安装上模、调整冲裁间隙。
将上模系统各零件分别装于上模座和模柄孔内。
用平行夹板将落料凹模、空心垫板、凸模凹件、垫板和上模座轻轻加紧,然后调整凸模组件和凸凹模的冲裁间隙,以及
调整落料凹模和凸凹模落料凸模的冲裁间隙。
可以采用垫片法调整,并对纸片进行手动试冲,直至内、外形冲裁间隙均匀。
在通过平行夹板将上模各板夹紧夹牢。
(3)钻铰上模销孔和螺孔。
上模部分通过平行夹板夹紧,在钻床上以凹模上的销孔