水管 锅炉检验工艺.docx
《水管 锅炉检验工艺.docx》由会员分享,可在线阅读,更多相关《水管 锅炉检验工艺.docx(33页珍藏版)》请在冰豆网上搜索。
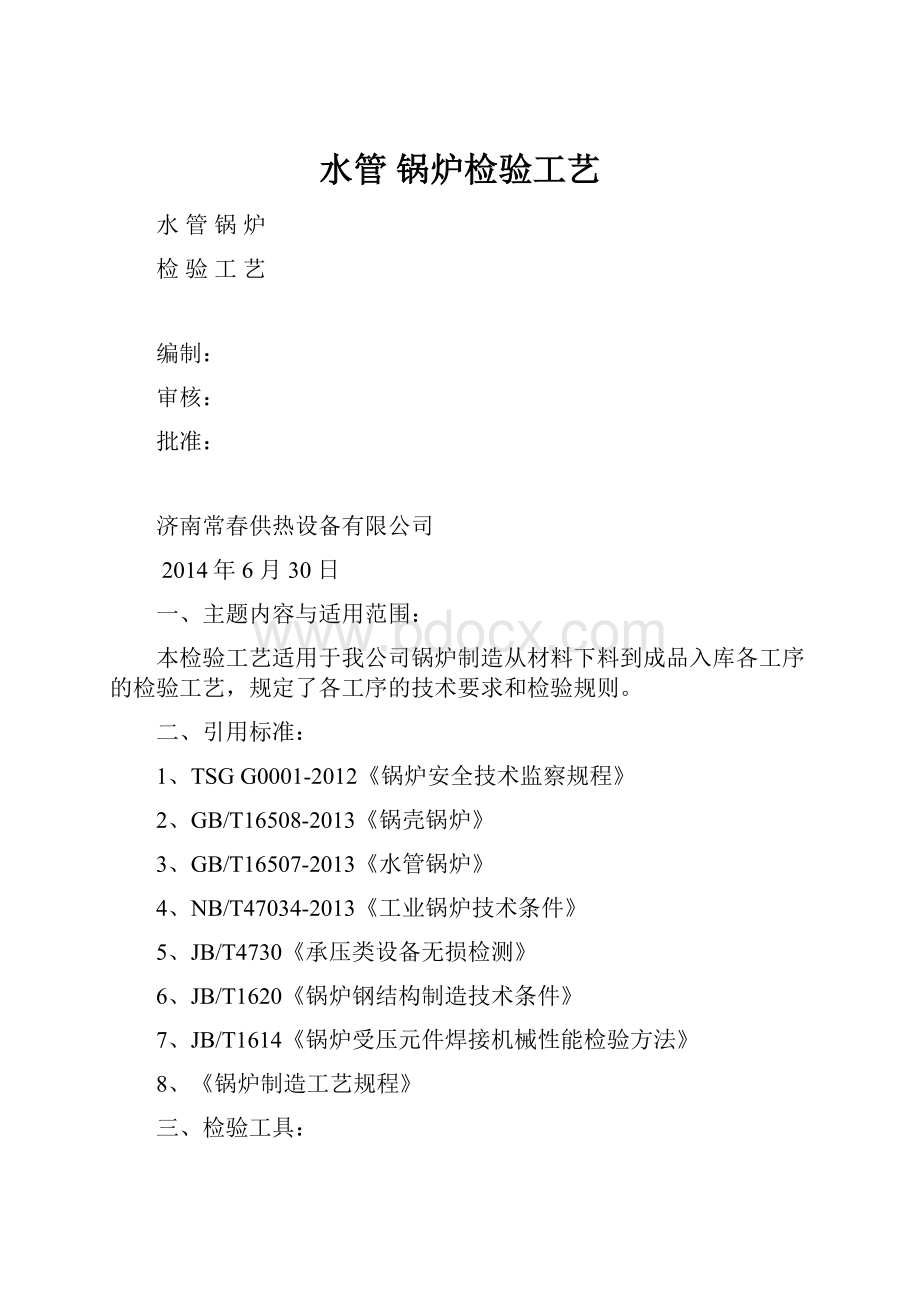
水管锅炉检验工艺
水管锅炉
检验工艺
编制:
审核:
批准:
济南常春供热设备有限公司
2014年6月30日
一、主题内容与适用范围:
本检验工艺适用于我公司锅炉制造从材料下料到成品入库各工序的检验工艺,规定了各工序的技术要求和检验规则。
二、引用标准:
1、TSGG0001-2012《锅炉安全技术监察规程》
2、GB/T16508-2013《锅壳锅炉》
3、GB/T16507-2013《水管锅炉》
4、NB/T47034-2013《工业锅炉技术条件》
5、JB/T4730《承压类设备无损检测》
6、JB/T1620《锅炉钢结构制造技术条件》
7、JB/T1614《锅炉受压元件焊接机械性能检验方法》
8、《锅炉制造工艺规程》
三、检验工具:
钢卷尺、直尺、直角尺、游标卡尺、深度尺、高度尺、塞尺、万用量规、焊接检验尺、样板、粉线、量块、测厚仪、温度计、
钢制通球、对比量块、手电筒。
四、各受压部件检验表格。
筒体、封头、集箱类、公称外径大于或等于219mm的管子、本体总装
名称
序号
检查项目
标准
技术要求
检查方法
备注
标
记
1
材料标记
GB/T16507.5-2013
第5.1条
锅炉主要受压元件用的材料(锅壳、封头、集箱类、公称外径大于或等于219mm的管子)的材料标记应能追溯到材料的质量证明书。
目测
其他受压元件(公称外径小于219mm的管子)和承受载荷的非受压元件(锅筒上、集箱类产品上的支吊架)的材料标记应便于识别,以防止材料混用。
2
材料标记移植
GB/T16507.5-2013
第5.2条
应在制造过程中保留材料标记。
锅炉受压元件用的材料切割下料前,应当作标记移植,并且便于识别。
目测
3
制造过程中的标记
GB/T16507.5-2013
第5.3条
产品制造过程中有临时性的标记和永久性的标记
目测
焊工标记和无损检测标记应作为永久性的标记保留,生产过程中标记被覆盖或因加工而丢失标记时应作标记移植。
目测
4
标记方法
GB/T16507.5-2013
第5.4.1条
a)、钢印、b)、震动蚀刻或其他蚀刻工具
c)、涂漆或用标记笔标记;d)、其他不损坏锅炉安全性的方法(如贴票签等)
GB/T16507.5-2013
第5.4.2条
下列情况不应用钢印标记:
a)、不锈钢管及壁厚小于5mm的管子;
b)、在管子弯头内外弧区域不应用钢印标记
c)、客户要求不允许用钢印标记的材料。
GB/T16507.5-2013
第5.4.3条
无法在焊缝附近标注焊工标记和无损检测标记的可以用定位图表示
名称
序号
检查项目
标准
技术要求
检查方法
备注
冷
热
成
型
1
成型壁厚
GB/T16507.5-2013
第6.1.1条
受压元件成形后的实际厚度不小于设计需要的最小壁厚。
2
切割下料
GB/T16507.5-2013
第6.2.3条
热切割表面应通过机械加工或打磨的方法去除所有过烧金属、割渣、有害刻痕及多余金属等。
用磨光机进行清理
3
锅壳、集箱类筒体和封头成型后外观质量
GB/T16507.5-2013
第6.3.4条
a)卷制或压制后的筒体和压制后的封头应清除内外表面的氧化皮、凹陷和疤痕,当其深度不影响设计最小成型厚度且呈圆滑过渡时,可不予修磨;若底部呈尖锐状态应修磨成圆滑过渡。
深度影响最小成形厚度的按评定合格的焊补工艺进行焊补及修磨,并经无损检测合格。
b)、人孔扳边加工完后应经表面检查,不应有裂缝。
4
管子成形
GB/T16507.5-2013
第6.4条
1)、管子制造要求详见下表中《管子制造部分》
目测
2)、壁厚缩颈加工后,管子的外表及壁厚的过渡区应平滑、无裂纹。
焊
缝
布
置
1
筒节
拼接焊缝
GB/T16508.4-2013
第4.4.3.1条
锅筒上相邻两筒节纵向焊缝,不应彼此相连其焊缝中心线间距离(外圆弧长)至少为较厚钢板厚度的3倍,并且不小于100mm。
用钢卷尺测量
GB/T16508.4-2013
第4.4.3.8条
筒体拼接时,锅壳、炉胆任一筒节长度不小于300mm,
用钢卷尺测量
GB/T16508.4-2013
第4.4.3.7条
名义内径≤1800mm的锅壳,每节筒体纵向拼接焊缝不应多于2条
目测
每节筒体纵向焊缝间外圆弧长不应小于300mm
用钢卷尺测量
名称
序号
检查项目
标准
技术要求
检查方法
备注
2
焊接表面质量
《锅规》第4.5.1条
对接焊缝高度不低于母材表面,焊缝与母材平滑过渡,焊缝和热影响区表面无裂纹、夹渣、弧坑和气孔。
目测
锅筒(锅壳)、炉胆、集箱的纵(环)缝及封头(管板)的拼接焊缝无咬边,其余焊缝咬边深度不超过0.5mm,管子焊缝两侧咬边总长度不超过管子周长的20%,且不超过40mm。
用钢卷尺测量
坡口加工
3
坡口型式
GB/T16508.4-2013
第4.4.4.1条
焊接接头的坡口型式、尺寸和装配间隙应符合设计文件的规定。
坡口质量
GB/T16508.4-2013
第4.4.4.2条
坡口表面应有裂纹、分层、夹杂物等缺陷。
目测
坡口清理
GB/T16508.4-2013
第4.4.4.4条
施焊前,应清除坡口及两侧母材表面至少20mm范围内(以离坡口边缘的距离计)的氧化皮、油污、熔渣及其他有害杂质。
用磨光机和刺轮进行清理
焊
缝
布
置
1
筒节
拼接焊缝
GB/T16508.4-2013
第4.4.3.1条
锅筒上相邻两筒节纵向焊缝,不应彼此相连其焊缝中心线间距离(外圆弧长)至少为较厚钢板厚度的3倍,并且不小于100mm。
用钢卷尺测量
GB/T16508.4-2013
第4.4.3.8条
筒体拼接时,锅壳、炉胆任一筒节长度不小于300mm,
用钢卷尺测量
GB/T16508.4-2013
第4.4.3.7条
名义内径≤1800mm的锅壳,每节筒体纵向拼接焊缝不应多于2条
目测
每节筒体纵向焊缝间外圆弧长不应小于300mm
用钢卷尺测量
2
焊接表面
质量
《锅规》第4.5.1条
对接焊缝高度不低于母材表面,焊缝与母材平滑过渡,焊缝和热影响区表面无裂纹、夹渣、弧坑和气孔。
目测
锅筒(锅壳)、炉胆、集箱的纵(环)缝及封头(管板)的拼接焊缝无咬边,其余焊缝咬边深度不超过0.5mm,管子焊缝两侧咬边总长度不超过管子周长的20%,且不超过40mm。
用钢卷尺测量
名称
序号
检查项目
标准
技术要求
检查方法
备注
管孔加工
2
管孔尺寸
GB/T16508.4-2013
附录A.2
受压元件上焊接管口的型式应为插入式、凹座式或骑座式
加工方法
对管子外径不大于108mm的插入式圆形径向孔应采用机械加工。
管孔尺寸
GB/T16508.4-2013
附录A.2
用机械加工方法开设插入式圆形径向管孔时,管孔直径应按下表
管子外径do
≤45
>45--108
用卡尺测量
管孔直径d1
do+0.5
do+1.0
用热切割方法开设插入式圆形径向孔时,管孔直径管孔直径不应大于管子外径加2
用卡尺测量
骑坐式的管孔,管孔直径应等于管子内径
3
制造公差
机械加工
GB/T16508.4-2013
附录A.3.1
用机械类加工方法开孔石,管孔直径的偏差按GB/T1804中C级(粗糙度),且宜采用正偏差。
用卡尺测量
热切割
附录A.3.2
用热切割方法开孔时,管孔直径的偏差范围为±1mm。
管孔表面质量
附录A.3.3
机械加工方法开孔时,管孔的表面粗糙度参数值Ra≤25um
对比量块
用手工热切割方法开孔时,管孔的表面粗糙度参数值Ra≤100um
4
管口中心距偏差
G/T16508.4-2013第4.4.6.6条
≤260
纵向±1.5,环向±2.0
用钢卷尺测量
>260~~500
±2.0
>500~~1000
±2.5
>1000~~3150
±3.0
>3150~~6300
±4.0
名称
序号
检查项目
标准
技术要求
检查方法
备注
筒
体
1
纵缝对接边缘偏差
《锅规》
第4.3.3.4条GB/T16507.5-2013
第6.5.1.1/2条
10%δ且≤3
用样板的中心基准线对准焊缝中心,用深度尺在焊缝边缘处测量样板外缘。
环缝对接边缘偏差
15%δ+1且≤6
用样板及深度尺测量焊缝两侧的高度差即为环向焊缝对接边缘偏差,测量几处以最大值计算。
2
棱角度
《锅规》4.3.3.5条
锅筒(锅壳)纵向棱角度≤4
用样板与直尺测量。
≤1800mm的筒体,也可用万用量规测量
GB/T16507.5-2013第6.5.1.5条
纵缝形成的环向棱角≤(δs/10+2)且≤4mm
轴向棱角应按6.5.1.3削薄或堆焊。
3
圆度
《锅规》4.3.3.5条GB/T16507.5-2013
第6.5.1.4条
锅筒的任意同一截面上最大内径与最小内径之差不应大于其名义内径的1%。
即Dmax-Dmin≤1%Dn
筒接竖直放置,在端口每隔45°用卷尺测量内径的最大值与最小值之差,两端分别测量以最大值计算。
4
直线度偏差
GB/T16507.5-2013
第6.5.1.6条表3
筒体长度L(mm)
L≤5
5<L≤7
7<L≤10
在筒体两端离焊缝边缘100mm处各放一等高垫块,在其上拉一直线,用钢尺测量直线到筒体的最大距离,减去垫块高度即为直线度。
遇焊缝需离开50mm。
在相距90°两个方向上测量,以最大值计算,为避免拉线下垂的因素,拉线位置与筒体之间是水平方向。
筒体直线度偏差△W
≤5
≤7
≤10
5
长度偏差
GB/T16507.5-2013
第6.5.1.6条表3
L≤5
+10,-5mm
用卷尺测量筒节两端间的长度,测量几处以最大差值计算。
5<L≤10
+20,-10mm
6
焊工钢印
在规定的位置有焊工钢印
目测。
7
焊缝表面质量
《锅规》第4.5.1条
对接焊缝不低于母材,焊缝与母材平滑过渡,焊缝和热影响区表面无裂纹气孔夹渣及咬边
目测。
8
筒节表面质量
无机械损伤
名称
序号
检查项目
标准
技术要求
检查方法
备注
封
头
1
封头拼接焊缝
GB/T16508.4-2013第4.4.3.1条
封头、管板、炉胆顶或者下脚圈拼接焊缝与相邻筒节的纵向焊缝,不应彼此相连其焊缝中心线间距离(外圆弧长)至少为较厚钢板厚度的3倍,并且不小于100mm。
用钢卷尺测量
GB/T16508.4-2013第4.4.3.10条
封头的拼接焊缝离封头中心线的距离不应大于封头名义内径的30%,并不应通过扳边人孔,也不应布置在人孔扳边圆弧上。
用钢卷尺测量
2
对接边缘偏差
GB/T16508.4-2013第4.4.5.2条
封头拼接焊缝两边钢板的实际边缘偏差值不大于其名义厚度的10%δ且不超过3mm.
用J06样板及深度尺测量焊缝两侧的高度差即为焊缝对接边缘偏差,测量几处以最大值计算。
拼接焊缝
3
圆度
G/T1650.7-2013
第6.5.1.7条
同一截面上最短内径与最小内径之差,封头不应大于其名义内径的1%。
即Dmax-Dmin≤1%Dn
在端口每隔450用卷尺测量内径的最大值与最小值之差。
4
总高度公差
GB/T25198-2010
第6.3.7条
(-0.2%~~0.6%)DN
在封头端面任意两直径位置上放置直尺或拉紧钢丝,在直尺或钢丝交叉处垂直测量封头总深度或封头总高度与标准值之差。
5
形状偏差
GB/T16508.4-2013
第4.4.5.6条
外凸
≤1.25%Di
用带间隙的全尺寸的内样板检查,检查时应使样板垂直于待测表面,用直尺测量样板与封头的距离,其值与标准间隙之差,多测量几处取最大值
内凹
≤0.625%Di
6
扳边元件
直段长度
《锅规》
第3.10条
扳边元件内径
≤600≥25
封头切边后,将封头口朝下放置于平台上,直角尺一边靠于平台,另一边靠近封头,读取直角尺离开封头起点到平台的距离,在相距90°的四个方向上分别测量,取最小值。
>600≥38
7
扳边孔直段减薄量
GB/T16508.4-2013第4.4.1.1.b)条
受压元件的扳边孔,当没有加强圈或不可能加强时,其直段边缘的厚度不小于该元件设计厚度的70%。
游标卡尺在扳边口上测量,按最薄厚度计算
8
扳边孔中心偏移
≤5
将封头置于平台上,找出封头和扳边孔的实际中心线,用钢尺测量两中心线间的距离与设计的差值即是。
名称
序号
检查项目
标准
技术要求
检查方法
备注
集
箱
1
集箱拼接长度
GB/T16508.4-2013
第4.4.3.8条
集箱筒体任一筒节长度不应小于500mm。
用钢卷尺测量
2
对接接头边缘偏差
GB/T16507.5-2013
第6.5.4.1.1条
集箱类部件筒体的坡口内壁应尽量对准并且平齐。
当接头两侧的公称外径和名义壁厚相等时,外表面的边缘偏差不得超过名义壁厚的10%,且最大不超过4mm,超出上述规定后公称外径不同使边缘偏差超限时,应将超出部分削薄。
用样板和深度尺进行测量
GB/T16507.5-2013
第6.5.4.1.2条
集箱类部件筒体对接接头内表面的边缘偏差如果大于名义壁厚的10%加0.5mm,或者大于1mm时,超出的部分应予以內镗或削薄。
GB/T16507.5-2013
第6.5.4.1.3条
对接接头外侧边缘偏差超差时的削薄要求按6.5.1.3条
缩孔
GB/T16507.5-2013
第6.4.3.2条
壁厚缩颈加工后,管子的外表及壁厚的过渡区应平滑、无裂纹。
目测
3
集箱长度偏差
GB/T16507.5-2013
第6.5.4.2.1条表5
本体长度L
m
长度偏差△Lmm
用钢卷尺测量
两端开口
一端开口,一端封闭
两端封闭
<20
+5~-8
+8~-10
±10
4
集箱直线度偏差
<20
1.0mm/m
用等高垫块、钢线及深度尺测量
名称
序号
检查项目
标准
技术要求
检查方法
备注
弯
管
1
弯管表面质量
GB/T16507.5-2013
第6.4.2.4.4条
1)、弯头表面不应有裂纹等尖锐性缺陷。
2)、管子的表面机械损伤,其深度值不应超过管壁厚度的负偏差。
3)、任何弯头沿管子中心线方向不应有宽度超过12mm的瘪痕。
2
弯管波纹幅度及波距
GB/T16507.5-2013
第6.4.2.4.4条
波纹幅度h=(d1+d3)/2-d2≤3%×Do
波距A>12h
用样板和深度尺测量
3
弯曲角度偏差
GB/T16507.5-2013
第6.4.2.4.3条
公称外径Do≤108mm的管子,弯头平面弯曲角度的偏差≤±1°
公称外径Do>108mm的管子,弯头平面弯曲角度的偏差≤0.5°
在平台上放样,然后用角度尺测量
公称外径Do≥108mm时,弯头两端间的距离,距离偏差一般≤4mm
在平台上放样,然后用钢卷尺测量
4
弯头圆度
GB/T16507.5-2013
第6.4.2.4.2条
圆度=2×[(Dmax-Dmin)/(Dmax+Dmin)]×100%
1)、成排弯管子圆度≤12%
2)、其他管子:
当R/Do≤1.4时,圆度≤14%
当1.4<R/Do≤2.5时,圆度≤12%
当R/Do≥2.5时,圆度≤10%
用卡尺测量
5
弯头外侧壁厚
GB/T16507.5-2013
第6.4.2.4.1条a)
管子弯后弯头外侧任何一点的厚度不得小于下式的计算值
δa≥δmin×[(1-1/(4R/Do+2)]
用测厚仪进行测量
6
弯头内侧壁厚
GB/T16507.5-2013
第6.4.2.4.1条a)
公称外径大于100mm的管子,弯后弯头内侧任何一点的厚度不得小于下式的计算值δa≥δmin×[(1+1/(4R/Do-2)]
7
弯管通球
GB/T16507.6-2013
第5.1条
公称外径≤60mm的对接接头或弯管应进行通球试验
用符合要求的钢球进行测试,通过为合格
8
通球直径
GB/T16507.6-2013
第5.3条
通球用钢球的制造直径偏差为-0.2mm,即实际选用钢球直径允许比通球直径小0.2mm。
GB/T16507.6-2013
第5.5条
R/D
1.0≤R/D<1.4
1.4≤R/D<1.8
1.8≤R/D<2.5
2.5≤R/D<3.5
≥3.5
db
≥0.70d
≥0.75d
≥0.80d
≥0.85d
≥0.90d
注:
R为管子弯曲半径,D和d为管子的公称外径和内径,mm
名称
序号
检查项目
标准
技术要求
检查方法
集箱类部件本体尺寸偏差
1
管接头偏差
GB/T16507.5-2013第6.5.4.3条图9表6
a
管接头横向倾斜度△a均不大于±2mm
用水平尺和直角尺测量
b
成排管接头中相邻两管接头管端节距P的偏差△P不超过±3mm
任意两管接头管端节距偏差不超过±6mm
用钢卷尺测量
c
管接头的高度偏差以两端管接头的高度为基准线进行测量,△h不超过±2mm。
用高度尺进行测量
d
尺寸偏差
△h1
△h
△h2
△p
△p1
△t1
△t2
△t3
光管水冷壁
±2
±2
-
±3
±6
±2.5
±6
±6
名称
序号
检查项目
标准
技术要求
检查方法
法兰
1
法兰
GB/T16507.5-2013第6.5.4.4条
法兰的端面倾斜度△f不大于2mm
法兰螺栓孔在螺栓圆上的偏移△a
法兰外径
法兰螺栓孔偏移△a
用卡尺测量
≤100
≤1
>100~200
≤2
>200
≤3
法兰高度H的偏差不超过±2mm
用专用量具或装配夹具检查。
2
各法兰管接头密封面表面质量
无径向划痕和任何损伤
目测
名称
序号
检查项目
标准
技术要求
检查方法
水
压
试
验
清理
GB/T16508.4-2013第5.6.2.1条
受压元件内外部应清理干净,无锈斑和涂漆。
充水时应将内部的空气排尽再封闭排气口
目测。
外部检查
GB/T16508.4-2013第5.6.2.2
水压试验前,各连接部位的紧固件应装配齐全,并紧固妥当。
GB/T16508.4-2013第5.6.2.3
试验所用的管路应无堵塞和渗漏,保持正常的工作状态。
水压试验
一般要求
GB/T16507.6-2013第9.1
a)、无损检测和热处理后进行
b)、场地应当由可靠的安全防护设施;
c)、水压试验应当在环境气温高于或等于5℃时进行,低5℃时应有有防冻措施;
d)、所用的水应是洁净水,水温应当保持高于周围露点的温度以防止
表面结露,但也不宜温度过高以防止引起汽化和过大的温差应力;
GB/T16508.4-2013第5.6.1
e)、如采用压力表测量试验压力,则应使用两只量程相同、并经检定合格且在有效期内的压力表,量程应为试验压力的1.5倍~3倍,最好采用2倍。
压力表的精度不应低于1.6级,表盘直径不应小于100mm。
保压时间
GB/T16507.6-2013第9.3.1条表7
整体水压试验保压时间为20min;
水压试验过程控制
GB/T16507.6-2013第9.4
进行水压试验时,水压应当缓慢地升降。
当水压上升到工作压力时,应暂停升压,检查有无漏水或者异常现象,然后升压到试验压力,达到保压时间后,降到工作压力进行检查。
检查期间压力应当保持不变。
水压试验合格标准
GB/T16507.6-2013第9.5
1、在受压元件金属壁和焊缝上没有水珠和水雾;
2、水压试验后,没有发现明显的残余变形。
名称
序号
检查项目
标准
技术要求
检查方法
出厂资料
1
产品出厂资料
GB/T16508.4-2013第6.1.1
1、锅炉图样(包括总图、安装图和主要受压元件图)
受压元件的强度计算书或计算结果汇总表
安全阀排放量的计算书或计算结果汇总表
锅炉质量证明书,包括产品合格证(含锅炉产品数据表,见附录A)、金属材料证明、焊接质量证明和水压试验证明等。
锅炉安装说明书和使用说明书
受压元件与设计文件不符的变更资料
热水锅炉的税流程图及水动力计算书或者计算结果汇总表
产品合格证上应有检验责任工程师和质量保证工程师签章和单位公章
GB/T16507.6-2013第11.1
特种设备制造监督检验证书
对于定型产品应提供定型产品能效测试报告
铭牌
2
铭牌内容
GB/T16508.4-2013第6.2.1条
制造单位名称、锅炉型号、设备代码、产品编号、
额定蒸发量(t/h)或者额定热功率(W)
额定工作压力(MPa)
额定蒸汽温度(℃)或者额定出口/进口水(油)温度(℃)
再热蒸汽进口、出口温度(℃)及进口、出口压力(MPa)
锅炉制造许可证级别和编号
制造日期(年、月)