双孔垫片级进模设计.docx
《双孔垫片级进模设计.docx》由会员分享,可在线阅读,更多相关《双孔垫片级进模设计.docx(23页珍藏版)》请在冰豆网上搜索。
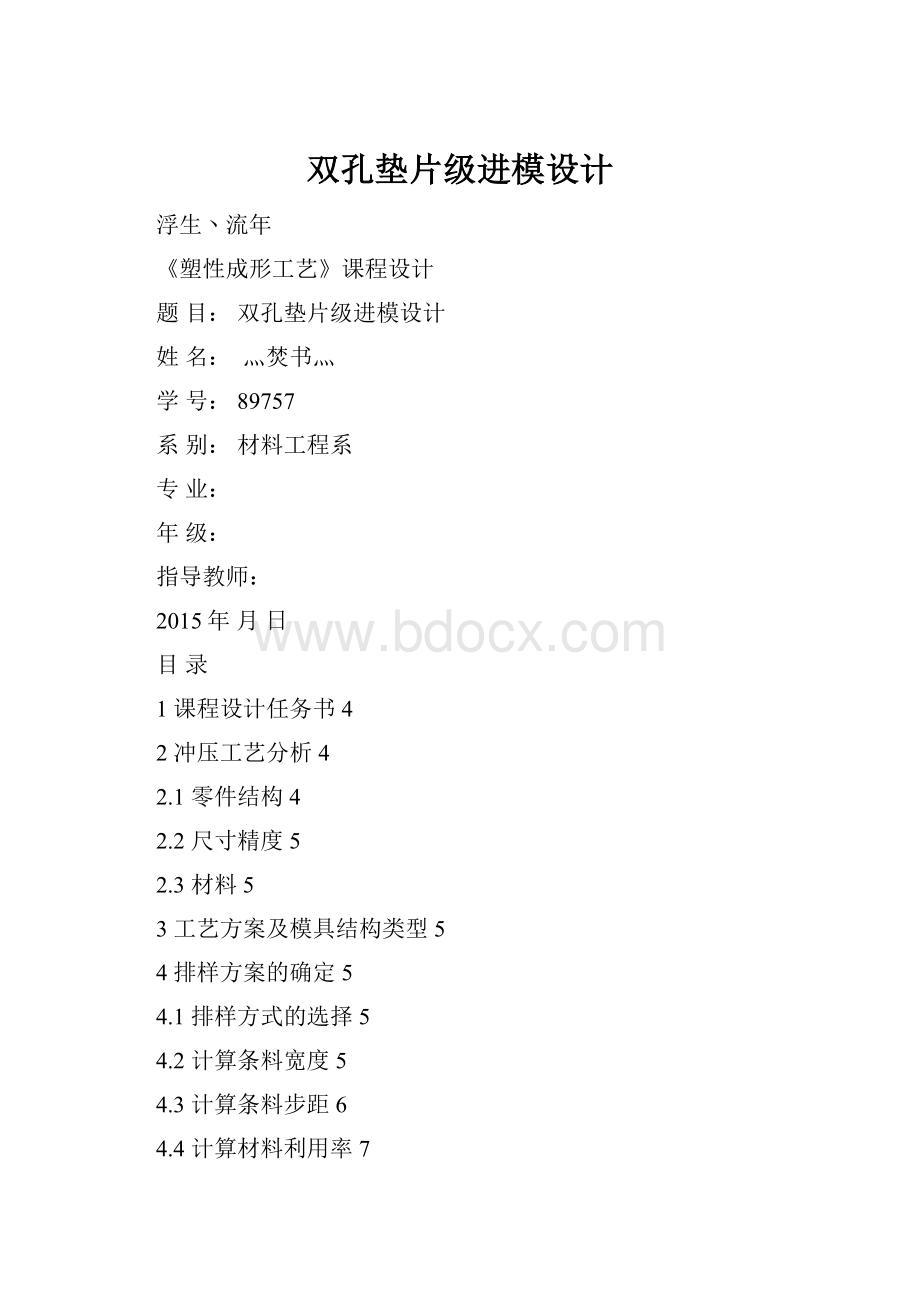
双孔垫片级进模设计
浮生丶流年
《塑性成形工艺》课程设计
题目:
双孔垫片级进模设计
姓名:
灬焚书灬
学号:
89757
系别:
材料工程系
专业:
年级:
指导教师:
2015年月日
目录
1课程设计任务书4
2冲压工艺分析4
2.1零件结构4
2.2尺寸精度5
2.3材料5
3工艺方案及模具结构类型5
4排样方案的确定5
4.1排样方式的选择5
4.2计算条料宽度5
4.3计算条料步距6
4.4计算材料利用率7
5工作零件刃口尺寸计算7
6工作零件结构尺寸与设计9
6.1落料凹模板结构尺寸9
6.2卸料部件的设计11
6.3垫板的结构设计11
6.4导料板的结构设计12
6.5承料板的结构设计12
6.6模柄12
6.7标准模架和导向零件12
6.8模座的选择13
6.9选择导柱和导套14
6.10凸模尺寸计算14
7冲压力与压力中心计算15
7.1冲压计算15
7.2压力中心16
8压力机的选择与校核17
8.1压力机的选择17
8.2校核18
8.2.1模具闭合高度的校核18
8.2.2校核导柱导套行程配合19
参考文献20
1课程设计任务书
设计题目:
双孔垫片级进模设计
工件图:
如图1所示:
材料:
45#钢
厚度:
1.5mm
技术要求:
零件公差按IT13选取
图1零件尺寸图
2冲压工艺分析
2.1零件结构
该零件结构简单,为圆形,并在对称中心线上有两个直径为14mm的圆孔。
孔与孔,孔与边缘之间的距离也满足要求,最小壁厚为5.5mm(直径为14mm的孔与最边缘的之间的尺寸)。
由此可以看出该零件具有良好的冲压性能。
2.2尺寸精度
零件上所有未标公差的尺寸,属于自由尺寸,可按IT13级确定工件尺寸的公差。
零件外形尺寸:
Φ500-0.46mm;零件内形尺寸:
Φ14+0.270mm;孔心距尺寸:
25mm。
适合冲裁加工。
2.3材料
零件采用45#钢,该零件的材料具备可塑性、高强度性、高硬度性,由《冷冲模设计》[1]表2-3可得,材料剪应力τ=480MPa。
适合冲裁加工。
3工艺方案及模具结构类型
该零件包括落料、冲孔两个基本工序,可以采用以下三种工艺方案:
方案一:
采用单工序模生产,模具结构简单,但需要两道工序、两套模具才能完成零件的加工,生产效率较低,难以满足零件大批量生产的需求。
方案二:
采用复合模生产,只需一副模具,冲裁较复杂零件时,比级进模低不安全,需采取安全措施冲件被顶到模具工作表面上,必须手动或机械排除,生产效率较低。
方案三:
采用级进模生产,只需一副模具,生产效率高,操作方便,精度也能满足要求,模具制造工作量和成本在冲裁简单的零件时比复合模低。
通过对上述三种方案的分析比较,该件的冲压生产采用方案三方案为佳。
4排样方案的确定
4.1排样方式的选择
该零件可采用以下三种排样方式:
方案一:
有废料排样沿冲件外形冲裁,在冲件周边都留有搭边。
冲件尺寸完全由冲模来保证,因此冲件精度高,模具寿命高。
方案二:
少废料排样材料利用率稍高,冲模结构简单,但因受剪切条料和定位误差的影响,冲件质量差,模具寿命较方案一低。
方案三:
无废料排样材料利用率最高,但冲件的质量和模具寿命更低一些。
通过上述三种方案的分析比较,综合考虑模具寿命和冲件质量,该冲件的排样方式选择方案一为佳。
4.2计算条料宽度
条料采用无测压装置送料,条料宽度按下式计算:
B=(D+2a1+2△+b0)0-△公式
(1)
式中D—冲裁件与送料方向垂直最大尺寸;
a1—冲裁件与条料侧边之间的搭边;
Δ—板料剪裁时的下偏差;
b0—条料与导料板之间的间隙。
查《冷冲模设计》表3-10确定搭边值;
两工件间的搭边:
a=0.9mm;
工件边缘搭边:
a1=1.08mm;
查《冷冲模设计》表3-11得剪裁的下偏差:
△=1.0mm
查《冷冲模设计》表3-13得条料与导料板之间的间隙:
b0=0.8mm
B=(D+2a1+2△+b0)0-△
=(50+2×1.08+2×1+0.8)0-1
=54.960-1mm
4.3计算条料步距
条料在模具上每次送进的距离称为送料步距,每个步距可冲一个或多个零件。
进距与排样方式有关,是决定侧刃长度的依据。
条料宽度的确定与模具的结构有关。
进距确定的原则是,最小条料宽度要保证冲裁时工件周边有足够的搭边值;最大条料宽度能在冲裁时顺利的在导料板之间送进条料,并有一定的间隙。
级进模送料步距S
S=Dmax+a1公式
(2)
式中Dmax—零件横向最大尺寸,
a1—搭边
S=50+0.9
=50.9mm
确定后排样图如下图2所示:
图2冲压件排样图
4.4计算材料利用率
冲裁件的实际面积与所用板料面积的百分比叫材料的利用率,它是衡量合理利用材料的重要指标。
一个进距内的材料利用率公式为
η=S1/S0×100%=S1/AB×100%公式(3)
式中S1—一个步距内零件实际面积;
S0—一个步距内所需毛坯面积;
A—送料步距;A=50.9mm
B—条料宽度;B=54.96mm
S0=AB=50.9×54.96=2797.5mm2
S1=π(
)2-2π(
)2=π(
)2-2π(
)2=1654.8mm2
η=S1/S0=1654.8/2797.5×100%=59.1%
5工作零件刃口尺寸计算
落料部分以落料凹模为基准计算,落料凸模按间隙值配制;冲孔部分以冲孔凸模为基准计算,冲孔凹模按间隙值配制。
既以落料凹模、冲孔凸模为基准,凸凹模按间隙值配制。
1)落料凹模尺寸计算
冲裁间隙:
查《多工位级进模设计与制造》[2]表2-4得
Zmin=0.190mmZmax=0.240mm
Zmax-Zmin=0.240-0.190=0.040mm
凸模和凹模的制作偏差:
查《冷冲模设计》表3-6得
δ凹=+0.030mmδ凸=-0.020mm
|δ凹|+|δ凸|=0.050mm>0.040mm
不满足|δ凹|+|δ凸|≤Zmax-Zmin的要求
故采用黄金分割
δ凸=0.4(Zmax-Zmin)公式(4)
=0.4×0.040
=0.016mm
δ凹=0.6(Zmax-Zmin)公式(5)
=0.6×0.040
=0.024mm
磨损系数:
查《冷冲模设计》表3-5得
x=0.5
凹模尺寸计算公式:
D凹=(Dmax-xΔ)+δ凹0公式(6)
式中D—冲裁件的基本尺寸
Δ—冲裁件的尺寸公差
x—磨损系数
δ—制造偏差
凸模尺寸计算公式:
D凸=(Dmax-xΔ-Zmin)0-δ凸公式(7)
式中d—冲裁件的基本尺寸
Δ—冲裁件的尺寸公差
Z—冲裁模的间隙
x—磨损系数
δ—制造偏差
计算结果:
D凹=(Dmax-xΔ)+δ凹0
=(50-0.5×0.46)+0.0240
=49.77+0.0240mm
D凸=(Dmax-xΔ-Zmin)0-δ凸
=(50-0.5×0.46-0.190)0-0.016
=49.580-0.016mm
2)冲孔凸模尺寸计算
冲裁间隙:
查《多工位级进模设计与制造》表2-4得
Zmin=0.190mmZmax=0.240mm
Zmax-Zmin=0.240-0.190=0.040mm
凸模和凹模的制作偏差:
查《冷冲模设计》表3-6得
δ凹=+0.020mmδ凸=-0.020mm
|δ凹|+|δ凸|=0.040mm=0.040mm满足要求
磨损系数:
查《冷冲模设计》表3-5得
x=0.5
凹模尺寸计算公式:
d凸=(dmax+xΔ)0-δ凸公式(8)
式中d—冲裁件的基本尺寸
Δ—冲裁件的尺寸公差
x—磨损系数
δ—制造偏差
凹模尺寸计算公式:
d凹=(dmax+xΔ+Zmin)+δ凹0公式(9)
式中d—冲裁件的基本尺寸
Δ—冲裁件的尺寸公差
Z—冲裁模的间隙
x—磨损系数
δ—制造偏差
计算结果:
d凸=(dmax+xΔ)0-δ凸
=(14+0.5×0.27)0-0.020
=14.1350-0.020mm
d凹=(dmax+xΔ+Zmin)+δ凹0
=(14+0.5×0.27+0.190)+0.0200
=14.325+0.0200mm
3)孔心距的计算
孔心距公称尺寸L=25mm,查《机械设计课程设计手册》[3]表9-1的公差为0.330mm,即L=25±0.330mm
6工作零件结构尺寸与设计
6.1落料凹模板结构尺寸
1)凹模洞口的类型选择
冲孔凹模的孔口形式通常有如图3所示的几种。
图中a)、e)为直壁形,刃口强度高,刃磨后空口尺寸不变,制造方便。
但是在孔口内易于积存工件或废料,增大了凹模的胀力、推件力和孔壁的磨损;磨损后每次的修磨量大,模具的总寿命较低。
a)适用于圆形或矩形工件;e)适用于形状复杂的工件。
b)、c)、d)的孔口为锥形,孔口内不易于积存工件或废料,孔壁所受的胀力、摩擦力小,所以冲孔凹模的磨损及每次的饿刃磨量小。
但刃口强度较低,且刃口的尺寸在修磨后略有增大。
一般用于形状简单,精度要求不高和较薄的冲裁件。
c)适用于较复杂的冲裁加件;d)用于冲裁薄料和凹模厚度较薄的情况。
f)为凸台式凹模,适用于冲裁软而薄的金属与非金属材料,这种材料一般不淬火或淬火强度不高,可以用手锤敲打凸台斜面以调整模具间隙,直到试冲出满意的冲压件为止。
图3凹模洞口
而根据上述分析本模具采用a)为合理。
2)落料凹模板尺寸
凹模厚度:
H=kb(≥15mm)公式(10)
式中b—冲压件最大外形尺寸;
k—系数,考虑板料厚度的影响,其值可查《冷冲模设计》表4-3;k取0.25
H=0.25×50=12.5mm取H=16mm
凹模壁厚:
c=(1.5~2)H(其结果大于或等于30~40mm)公式(11)
c=(1.5~2)×16=30mm取c=30mm
凹模板的长:
L长=2c+S步距+D/2+d/2公式(12)
L长=2×30+50.9+50÷2+14÷2
=142.9mm
凹模板的宽:
L宽=2c+b公式(13)
L宽=2×30+54.9
=114.9mm
查《冲压模具标准件选用与设计指南》[4]表4-2凹模板长=160mm;凹模板宽=125mm。
由于凹模刃口需要修模量(4~6)mm,实取H=25mm。
故确定凹模板外形为:
160×125×25(mm)落料凹模板零件图如图4所示:
图4落料凹模零件图
3)落料凹模板的固定方式
凹模一般采用螺钉和销钉固定。
螺钉和销钉的数量、规格及它们的位置应可根据凹模的大小,可在标准的典型组合中查得。
位置可根据结构需要作适当调整。
螺孔、销孔之间以及它们到模板边缘尺寸,应满足有关要求。
6.2卸料部件的设计
1)卸料板的设计
卸料板采用Q235制造,卸料板轮廓尺寸与落料凹模轮廓尺寸相同,厚度根据JB/T8066.2-1995规定,选用160mm×125mm组模具参考,其厚度为6mm。
2)卸料螺钉的选用
卸料板上设置4个卸料螺钉,公称直径为d=M8,公称长度为L=20mm的开槽沉头螺钉。
6.3垫板的结构设计
考虑推件装置在上模内挖窝,采用垫板加固,上垫板厚度取8mm,垫板轮廓尺寸与落料凹模轮廓尺寸相同。
6.4导料板的结构设计
导料板是级进模中最通用的一种倒料装置,安装在凹模上平面的两侧。
基本形式为平行的两块长条板,导板的结构形式和尺寸规格查《冲压模设计指导》[5]表3-23选200×36×6mmJB/T7648.5
6.5承料板的结构设计
安装在导料板大出凹模的部分的底下,以支承条料引入模具。
承料板的结构形式和尺寸规格查《冲压模设计指导》表3-24选125×40mmJB/T7648.6
6.6模柄
由压力机的型号J21-40.可查得模柄孔的直径d=Φ50mm,深度L=75mm,由装配要求,模柄与模柄孔配合为H7/m6并加销钉防转,模柄长度比模柄孔深度小5~10mm,由于采用固定卸料,上模座回程时受力较大,因此选用压入式模柄较合理,查《冲压模设计指导》表3-40选GB/T7646.1-1995
6.7标准模架和导向零件
标准模架中,应用最广泛常的是用的导柱导套式模架,是由上、下模座和导向零件组成。
模架是整副模具的骨架,模具的全部零件都固定在它的上面,并承受冲压过程的全部载荷。
模具上模座和下模座分别与冲压设备的滑块和工作台固定。
上、下模间的精确位置,由导柱、导套的导向来实现。
按导柱在模架上的固定位置不同,导柱模架的基本型式有如图5所示的四种。
a)后侧导柱模架b)中间导柱模架
c)对角导柱模架d)四导柱模架
图5模架
图a)为后侧导柱模架。
由于前面和左、右不受限制,送料和操作比较方便。
因导柱安装在后侧,工作时,偏心距会造成导柱导套单边磨损,并且不能使用浮动模柄结构。
图b)为中间导柱模架。
导柱安装在模具的对称线上,导向平稳、准确。
但只能一个方向送料。
图c)为对角导柱模架。
由于导柱安装在模具中心对称的对角线上,所以上模座在导柱上滑动平稳。
常用于横向送料级进模或纵向送料的落料模、复合模。
图d)为四导柱模架。
具有滑动平稳、导向准确可靠、刚性好等优点。
常用于冲压尺寸较大或精度要求较高的冲压零件,以及大量生产用的自动冲压模架。
根据以上特点选用a较为适合。
6.8模座的选择
查《冲压模具标准选用与设计指南》表2-3选用GB/T2855.6-81后侧带导柱形式模板。
根据凹模轮廓尺寸L×B=160mm×125mm,上模座板厚为35mm.下模座板厚为40mm。
如图6所示:
a)上模座
b)下模座
图6
6.9选择导柱和导套
导柱和导套的结构和尺寸都可以由标准中选取,查《冲压模具标准选用与设计指南》表3-2选用A型导柱和导套,根据模座闭合高度H=174.5mm,以及导柱上端面与上模座的的顶面的距离等参数,选择导柱Φ25×160mm;导套Φ38×95mm。
6.10凸模尺寸计算
零件外形相对简单,根据实际情况并考虑加工,为了满足凸模强度和刚性,将凸模设计成阶梯式,使装配修磨方便。
采用成形铣、成形磨削加工。
凸模总长计算公式
L=H1+H2+H3+Y 公式(14)
式中H1-凸模固定板厚度;H1=36mm
H2-卸料板厚度;H2=6mm
H3-导料板厚度;H3=6mm
Y-附加长度;包括凸模刃口修模量,凸模进入凹模的深度(0.5~1)mm,凸模固定板与卸料板的安全距离,其中Y取15~20mm
L=H1+H2+H3+Y
=36+6+6+19.5
=67.5mm
7冲压力与压力中心计算
7.1冲压计算
通过冲压力计算能合理地选择冲压设备和设计模具。
冲压力的大小主要与材料的力学性能、厚度及冲裁件分离的轮廓长度有关。
用平刃口冲裁时,冲裁力F(N)可按下式进行计算:
F=KLτt公式(15)
式中F—冲裁力;
L—冲裁件周边长度;
t—材料厚度;
τ—材料抗剪强度(MPa);查《冷冲模设计》表2-3得τ=480MPa
K—系数;考虑到模具刃口的磨损。
模具间隙的波动,材料力学性能的变化及材料厚度偏差等因素,一般取K=1.3。
F推=nK推F公式(16)
式中F—冲裁力
K推—推件力系数
n—梗塞在凹模内的冲件数(n=h/t)
1)落料力
F落=1.3Ltτ
=1.3×π×50×1.5×480
=147KN
2)冲孔力
F冲=1.3Ltτ
=1.3×2π×14×1.5×480
=82.3KN
其中:
d为冲孔直径,2πd为两个孔圆周长之和。
3)推件力
查《冷冲模设计》表3-8得K推=0.05;
该模具凹模刃口形式,凹模洞口主要参数查《冷冲模设计》表4-2;取h=6mm则n=h/t=6/1.5=4个。
F推=nK推F
=nK推(F落+F冲)
=4×0.05×229.3
=45.9kN
该套模具采用钢性卸料,下出件的卸料装置。
4)总冲压力F=F落+F冲+F推公式(17)
代入数据
F=F落+F冲+F推=275.2KN
7.2压力中心
模具压力中心是指冲压时诸冲压力合力的作用点位置。
为了确保压力机和模具正常工作,应使模具的压力中心与压力机滑块的中心相重合,否则,会使冲模和力机滑块产生偏心载荷,使滑块和导轨之间产生过大的摩擦,模具导向零件加速磨损,降低模具和压力机的使用寿命。
冲模的压力中心,可以按下述原则来确定:
1)对称形状的单个冲裁件,冲模的压力中心就是冲裁件的几何中心。
2)工件形状相同且分布位置对称时,冲模的压力中心与零件的对称中心相重合。
3)形状复杂的零件、多孔冲模、级进模的压力中心可以用解析计算法求出冲模压力中心。
图7凹模图
1)选定坐标轴x和y
如图7以凹模左下角为原点,横向为x轴,纵向为y轴建立直角坐标系
2)根据公式
x0=
y0=
公式(18)
式中x0,y0—为压力中心
l—凸模直径
代入数据
x0=
=
=81.82mm
而y方向的压力中心在凹模对称中心上,即y0=62.5mm
8压力机的选择与校核
8.1压力机的选择
1压力机的选择原则
冲压设备的选择直接关系到设备的安全及生产效率,产品质量,模具寿命和生产成本等一系列重要问题。
重压设备的选择主要包括设备的类型规格参数两方面的问题。
冲压设备类型的选择主要根据所要完成冲压工序的性质,生产批量的大小,冲压件的几何尺寸和精度要求等来选择冲压设备类型。
1)对于中小型冲裁件,弯曲件或浅拉深件的常采用开式曲柄压力机。
2)对于大中型对于大和精度要求高的冲压件,多采用闭式曲柄压力机。
3)对于大型或较复杂的拉深件,常采用上传动的闭式双动拉深压力机。
4)对于大批量生产或形状复杂,批量很大的中小形冲压件应优先选用自动高速压力机或者多工位自动压力机。
5)对于批量小,材料厚的冲压件,常采用液压机。
6)对于精冲零件最好选择专用的精冲压力机。
2冲压设备规格的选择
在选择冲压设备的类型后,应进一步根据冲压加工中所需的冲压力(包括卸料力,压料力等)变形功以及模具的结构形式或闭合高度,外形轮廓尺寸等选择冲压设备的规格。
1)公称压力
压力机的公称压力是指压力机滑块离下止点前某一特定距离,既压力机的曲轴旋转侄离下止点前某一角度时滑快上所容需的最大工作压力。
2)滑快行程
压力机的滑快行程是指滑快从上止点到下止点所经过的距离压力机的行程的小应能保证毛胚或半成品的放入及成型零件的取出。
3)闭合高度
压力机的闭合高度是指滑快在下止点时,滑快底平面到工作台面之间的高度模具的闭合高度必须适合于压力机闭合高度范围的要求。
3压力机的其它参数
1)压力机工作台的尺寸压力机工作台上垫板的平面尺寸应大于模具下模座的平面尺寸,并留有固定模具的充分余地,一般每边留50-70mm。
2)压力机工作台孔的尺寸,模具底设置的漏料孔或弹顶装置尺寸必须小于压力机工作台孔的尺寸。
3)压力机模柄孔尺寸模柄直径必须和压力机滑快内模柄安装用孔的直径相一致,模柄的高度应小于模柄安装用孔的深度。
综上所述选择开式曲柄压力机,压力机型号为J21-40。
参数如下表1
表1
公称压力
400KN
滑快行程
80mm
行程次数
80次/min
连杆调节长度
70mm
模柄孔尺寸
直径×深度
Φ50×70
mm
工作台尺寸
前后×左右
460×700
(mm×mm)
最大装模高度
330mm
电动机功率
5.5KW
8.2校核
8.2.1模具闭合高度的校核
1)闭合高度
模具闭合高度应为上模座板、垫板、固定板、固定卸料板、导料板、凹模板、下模座板等厚度以及安全距离的总和。
即
H=H上模座+H垫板+H固定板+H卸料板+H导料板+H凹模板+H下模座+A公式(19)
式中H上模座—上模座厚度;H上模座=35mm
H垫板—垫板厚度;H垫板=8mm
H固定板—固定板厚度;H固定板=36mm
H卸料板—卸料板厚度;H卸料板=6mm
H导料板—导料板厚度;H导料板=6mm
H凹模板—凹模板厚度;H凹模板=25mm
H下模座—下模座厚度;H下模座=40mm
A—安全距离;A取18.5
考虑凸模进入凹模的深度。
根据生产现场调整,可稍有增减,以制件完全分离为准。
H=H上模座+H垫板+H固定板+H卸料板+H导料板+H凹模板+H下模座+A
=35+8+36+6+6+25+40+18.5
=174.5mm
2)模具闭合高度H应该满足
Hmin-H1+10≤H≤Hmax-H1-5公式(20)
式中Hmax—压力机最大闭合高度;
Hmin—压力机最小闭合高度;
H1—垫板厚度。
根据选压力机J21—40,查《冷冲模设计》表1-2开式压力机参数表得:
Hmax=330mm,Hmin=260mm,H1=80mm.
将以上数据带入公式10-1,得160<H<250
经计算该模具闭合高度H=174.5mm,在160mm~250mm内,且开式压力机J21—40最大装模高度330mm,大于模具闭合高度174.5mm, 可以使用。
8.2.2校核导柱导套行程配合
导柱和导套配合应该满足当压力机滑块运动到上止点时,导柱和导套不会脱离开来且能够安全工作。
H-h>s公式(21)
式中H—导套长度
h—导柱上端面与上模座的的顶面的距离
s—滑块行程
H-h=95-8.5=86.5mm>80mm满足要求
参考文献
[1]丁松聚.冷冲模设计.机械工业出版社,2001.
[2]陈炎翤.多工位级进模设计与制造.机械工业出版社,2006.
[3]吴忠泽.机械设计课程设计手册.高等教育出版社,2012.
[4]高军,李熹平,修大鹏.冲压模具标准件选用与设计指南.化学工业出版社2007.
[5]王立人,张辉.冲压模设计指导.北京理工大学出版社,2009.